Proses Sintering Bijih Besi Denda
Proses Sintering Bijih Besi Halus
Pabrik sintering biasanya diasosiasikan dengan produksi logam panas di tanur sembur di celana baja terintegrasi. Proses sintering pada dasarnya adalah langkah proses pra-perawatan selama pembuatan besi untuk produksi bahan pengisi yang disebut sinter untuk tanur sembur dari butiran bijih besi dan juga dari limbah metalurgi (debu yang terkumpul, lumpur dan skala pabrik dll.).
Teknologi sintering pada awalnya dikembangkan untuk tujuan pemanfaatan dalam tanur tinggi bijih besi halus dan besi yang ada dalam limbah metalurgi pabrik baja. Namun saat ini fokusnya telah berubah. Sekarang proses sintering bertujuan untuk menghasilkan beban berkualitas tinggi untuk tanur sembur. Saat ini sinter adalah beban logam utama untuk tanur sembur besar.
Proses sintering digunakan untuk menggumpalkan campuran bijih besi (blend), return fine, fluks dan kokas dengan ukuran partikel kurang dari 10 mm, sehingga sinter yang dihasilkan dengan ukuran saring 10 mm sampai 30 mm, dapat menahan kondisi tekanan dan suhu di tanur tinggi.
Prinsip sintering
Sintering adalah proses termal (dilakukan pada 1300 derajat C hingga 1400 derajat C) di mana campuran bijih besi, butiran halus, produk daur ulang dari industri pabrik baja (seperti skala pabrik, debu tanur tinggi, dll.), terak elemen pembentuk, fluks dan butiran kokas diaglomerasi di pabrik sinter dengan tujuan membuat produk sinter dengan komposisi kimia, kualitas (fisik) dan granulometri yang sesuai untuk dimasukkan ke dalam tanur sembur, sehingga memastikan operasi yang homogen dan stabil dari tungku ledakan. Sebelum sintering, ada proses penting yang disebut granulasi. Granulasi adalah homogenisasi campuran bijih besi dalam drum berputar dengan 7% sampai 8% air dengan tujuan memperoleh produk pra-diaglomerasi, yang kemudian disampaikan sebagai lapisan di atas jeruji atau untai yang terus bergerak untuk mendapatkan produk yang disinter. Proses ini memiliki peran mendasar karena memastikan permeabilitas sinter bed yang memadai dan karenanya produktivitas mesin sintering yang baik.
Fleksibilitas proses sintering memungkinkan konversi berbagai bahan, termasuk butiran halus bijih besi, debu yang ditangkap, konsentrat bijih, dan bahan bantalan besi lainnya dengan ukuran partikel kecil (misalnya, skala pabrik) menjadi aglomerat seperti klinker.
Proses sintering melibatkan pemanasan produk pra-diaglomerasi untuk menghasilkan massa semi-cair yang mengeras menjadi potongan-potongan sinter berpori dengan karakteristik ukuran dan kekuatan yang diperlukan untuk dimasukkan ke dalam tanur tinggi.
Sinter produk
Produk dari proses sintering disebut sinter dan karakteristik kualitas sinter yang baik meliputi (i) analisis kimia, (ii) distribusi ukuran butir, (iii) reducibility, dan (iv) kekuatan sinter. Sifat khas sinter diberikan di Tab 1
Tab 1 Sifat khas sinter |
Nomor Sl. | Barang | Satuan | Nilai |
1 | Komposisi kimia | | |
| Fe | % | 56,5 hingga 57,5 |
| FeO | % | 6.0 hingga 8.0 |
| SiO2 | % | 4,0 hingga 5,0 |
| Al2O3 | % | 1,0 hingga 2,5 |
| CaO | % | 7,5 hingga 8,5 |
| MgO | % | 1,6 hingga 2,0 |
2 | Kebasaan (CaO/SiO2) | | 1,7 hingga 2,9 |
3 | Kekuatan ISO (+ 6,3 mm) | % | Lebih dari 75 |
4 | Indeks degradasi pengurangan (RDI) | (-3 mm) % | 27 hingga 31 |
5 | Indeks reduksi (RI) | (R60) % | 55-75 |
6 | Indeks Tumbler | (-6.3 mm) % | 65-75 |
Produk sinter bijih besi ditunjukkan pada Gambar 1.
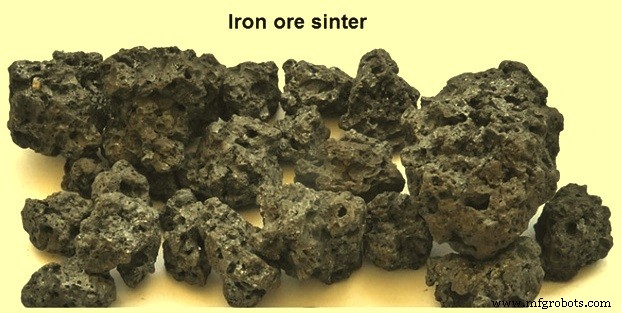
Gbr 1 Sinter bijih besi
Jenis sinter
Sinter diklasifikasikan menjadi sinter asam, sinter fluks sendiri, dan sinter super fluks. Sinter self-fluxing memiliki kandungan CaO (kapur) yang cukup untuk memfluks komponen asamnya (SiO2, dan Al2O3). Sinter super-fluks memiliki kandungan CaO tambahan untuk fluks komponen asam yang dimasukkan ke dalam tanur tinggi melalui bahan beban lainnya. Dalam kasus self-fluxing dan super-fluxed sinter, kapur mengurangi suhu leleh campuran sinter dan pada suhu yang relatif rendah (1100 derajat C hingga 1300 derajat C) ikatan kuat terbentuk dengan adanya FeO. Berikut ini adalah keuntungan menambahkan fluks ke sinter.
- Ini menghasilkan terak dengan kotoran yang ada dalam bijih besi dan bahan bakar padat yang menghasilkan matriks yang cocok untuk kohesi partikel.
- Ini meningkatkan sifat fisik dan metalurgi sinter
- Ini mengurangi suhu leleh campuran sinter.
- Mengurangi/menghilangkan penambahan batu kapur pada tanur tinggi sehingga menghemat bahan bakar yang dibutuhkan untuk reaksi kalsinasi batu kapur (CaCO3 =CaO + CO2) di tanur tinggi sehingga mengurangi laju kokas di tanur tinggi.
Proses sintering
Proses sintering dimulai dengan persiapan bahan baku yang terdiri dari bijih besi halus, fluks, bahan limbah metalurgi in-plant, bahan bakar dan denda kembali dari pabrik sinter. Bahan-bahan ini dicampur dalam drum pelet berputar dan air ditambahkan untuk mencapai aglomerasi yang tepat dari campuran bahan baku. Aglomerasi ini berbentuk mikro pelet. Pelet mikro ini membantu mendapatkan permeabilitas optimal selama proses sintering. Pelet mikro ini kemudian dibawa ke mesin sintering dan membentuk lapisan atas campuran muatan.
Proses sintering adalah proses berkelanjutan yang didasarkan pada perlakuan campuran muatan (halus bijih, butiran halus kembali, dan fluks, dll.) lapisan dengan adanya angin kokas ke aksi pembakar yang ditempatkan di permukaan lapisan. Dengan cara ini, pemanasan terjadi dari bagian atas ke bagian bawah. Lapisan campuran muatan terletak di atas sistem untai dan sistem pembuangan memungkinkan seluruh ketebalan untuk mencapai suhu yang sesuai untuk pencairan sebagian campuran, dan aglomerasi berikutnya.
Dalam mesin sintering Dwight-Lloyd, jeruji sintering adalah rantai kontinu dengan panjang dan lebar yang besar, dibentuk oleh penyatuan serangkaian mobil palet yang membuat untaian sintering (Gbr 2). Setiap mobil palet lewat di bawah hopper pengisian di mana ia diisi terlebih dahulu oleh bahan granulometri kasar (10 mm hingga 20 mm) dalam lapisan yang memiliki ketebalan 30 mm hingga 60 mm yang membentuk lapisan perapian yang sebagian besar terdiri dari sinter balik. Lapisan perapian melindungi kisi baja dari panas berlebih selama proses sintering.
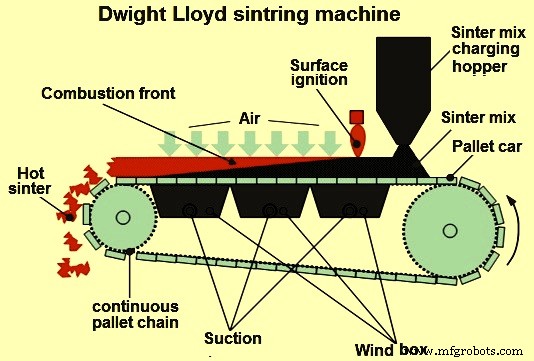
Gambar 2 Mesin Dwight Lloyd
Lapisan kedua pelet mikro dibebankan di atas lapisan perapian dan diratakan. Kemudian, mobil palet lewat di bawah tungku inisialisasi, di mana pengapian yang mudah terbakar terjadi di permukaan campuran muatan. Pada saat yang sama, campuran mengalami pengisapan down draft melalui muatan sinter. Karena hisapan down draft, udara ditarik melalui dasar yang bergerak menyebabkan bahan bakar terbakar.
Mobil palet melanjutkan proses dan pembakaran berlangsung ke arah aliran gas. Dengan cara ini, proses sintering berlangsung. Proses pembakaran tidak terjadi secara bersamaan di seluruh ketebalan bed. Sebaliknya, pembakaran terjadi sebagai lapisan horizontal yang bergerak secara vertikal melalui tempat tidur. Ketebalan lapisan ini adalah sebagian kecil dari tempat tidur. Permeabilitas unggun merupakan persyaratan kualitas untuk campuran muatan, dan karenanya, proses granulasi campuran muatan merupakan langkah penting untuk proses sintering (permeabilitas unggun ditingkatkan karena granulasi).
Di wilayah di atas zona pembakaran, produk sinter yang sangat panas memanaskan udara yang melewati lapisan ini. Dengan cara ini, udara yang telah dipanaskan sebelumnya tiba ke area pembakaran. Panas dari udara/gas yang sebelumnya dipanaskan diserap di bagian dingin ini, menyebabkan pemanasan awal beban dan penguapan uap air dari campuran muatan. Dalam konteks ini, suhu tinggi yang menyebabkan pencairan sebagian tercapai, dan proses sintering berlangsung.
Efisiensi termal yang tinggi disebabkan oleh akumulasi panas di sebagian lapisan campuran muatan yang disebut zona sintering atau front api. Bagian depan nyala berkembang dengan kecepatan mulai dari 10 mm hingga 30 mm/menit menuju kisi sintering. Pada ketinggian tempat tidur sekitar 500 mm, prosesnya biasanya memakan waktu sekitar 25 menit. Setelah ujung untai tercapai, bahan yang disinter dibuang dan mengalami pendinginan, penghancuran, dan penyaringan.
Proses sintering dikendalikan oleh 'burn-through point' (BTP) yang didefinisikan sebagai titik di mana suhu limbah gas mencapai nilai tertinggi. Ini adalah titik di mana bagian depan api mencapai dasar dasar sinter bed. Kecepatan mesin sinter dan aliran gas dikontrol untuk memastikan bahwa titik bakar terjadi sesaat sebelum sinter dibuang. Penentuan titik burn-through sangat penting untuk menstabilkan proses serta meningkatkan kualitas dan produktivitas.
Pada bagian akhir mesin, material hasil sinter berupa cake dibuang ke dalam hot sinter crusher. Di sini kue sinter panas dihancurkan hingga ukuran partikel maksimum yang telah ditentukan sebelumnya. Dari sini sinter dibuang ke pendingin sinter yang dapat berupa pendingin garis lurus atau melingkar. Setelah dingin, sinter dipindahkan ke bagian penyaringan yang biasanya dibagi menjadi tiga fraksi granulometri. Fraksi pertama terdiri dari 0 mm sampai 5 mm yang disebut denda kembali dan dikirim ke gerbong makan. Fraksi sinter dengan kisaran granulometri dalam 5 mm sampai 15 mm digunakan sebagai lapisan perapian di untai sinter. Jumlah sisa fraksi 5 mm sampai 15 mm yang tidak digunakan untuk lapisan perapian dicampur dengan fraksi granulometri ketiga yang memiliki kisaran ukuran 15 mm sampai dengan 50 mm dikirim ke tanur sembur.
Denda pengembalian tidak dapat dihindari dihasilkan selama proses sintering, dan didaur ulang kembali ke dalam proses sintering. Denda pengembalian umumnya terdiri dari sekitar 30% sampai 40% dari bahan bantalan besi. Denda yang dikembalikan dari pengayakan sintering sedikit mudah diasimilasi dibandingkan dengan pengayakan tanur tinggi karena kandungan ferit kalsium tinggi yang lebih rendah.
Ada empat zona yang teridentifikasi pada ketinggian sinter bed. Ini diberikan di bawah ini.
- Zona dingin dan basah – Ini termasuk zona dasar sinter dengan suhu kurang dari 100 derajat C. Daerah ini dibentuk oleh campuran muatan yang akan disinter, dengan batas atas jenuh dalam air/uap air.
- Zona pengeringan – Ini mencakup area lapisan sinter dengan suhu berkisar antara 100 derajat C dan 500 derajat C. Penguapan kelembaban campuran sinter dan dehidrasi hidroksida berikutnya terjadi di zona ini.
- Zona reaksi – Ini termasuk zona sinter bed dengan suhu berkisar antara 500 derajat C (mulai penyalaan kokas) dan 900 derajat C (mulai periode pendinginan). Suhu maksimum yang dicapai pada zona ini berkisar antara 1300 derajat C sampai dengan 1400 derajat C. Proses utama yang terjadi di zona ini adalah (i) pembakaran kokas (eksotermik), (ii) dekomposisi karbonat (endotermik), (iii ) reaksi fase padat, (iv) reduksi dan reoksidasi oksida besi, dan (v) reaksi pembentukan massa sinter.
- Zona pendinginan – Zona ini ditemukan segera setelah zona reaksi. Di zona ini, pendinginan dan rekristalisasi produk sinter berlangsung. Ada zona superfisial di mana lapisan sinter lebih rapuh daripada di tempat tidur sinter lainnya.
Penyebab fluktuasi proses sinter telah dipelajari untuk menurunkan konsumsi karbon, sehingga menurunkan emisi karbon dioksida. Analisis frekuensi data pabrik (suhu gas buang pada satu kotak angin, tingkat pengisian campuran dan kadar air campuran) telah menunjukkan bahwa variasi kelembaban campuran umpan terkait dengan fluktuasi suhu gas buang pada kotak angin tertentu. Peningkatan kontrol proses dengan mengontrol kadar air campuran umpan dalam rentang nilai yang sempit memungkinkan penurunan konsumsi karbon dan menghasilkan emisi karbon dioksida yang lebih rendah.
Sirkuit gas buang harus sepenuhnya anti bocor, tidak memungkinkan udara dari atmosfer dihisap oleh sistem. Ini menghasilkan penghematan daya di sirkuit gas buang. Gas limbah diolah untuk menghilangkan debu dalam siklon, presipitator elektrostatik, scrubber basah atau filter kain. Flowsheet dari pabrik sinter ditunjukkan pada Gambar 3.
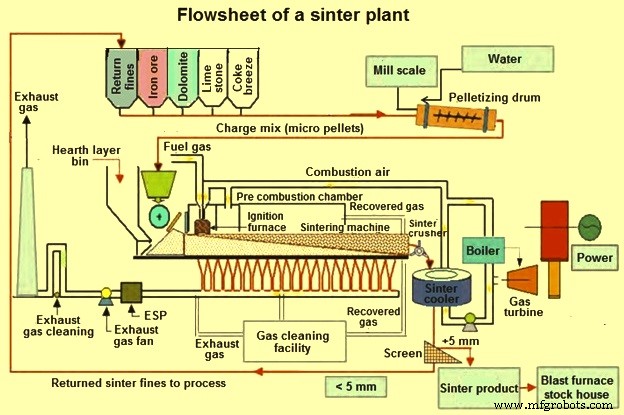
Gbr 3 Flowsheet dari pabrik sinter
Mesin sinter
Mesin sinter terdiri dari dua jenis yaitu (i) mesin melingkar, dan ii) mesin garis lurus. Mesin garis lurus juga dikenal sebagai mesin Dwight Lloyd. Dwight dan Lloyd membangun pabrik sinter kontinu pertama pada tahun 1906.
Mesin sinter melingkar biasanya cocok untuk tanur sembur yang memiliki volume berguna 650 Cu m dan kurang. Parameter man dari beberapa mesin melingkar diberikan di Tab 2.
Tab 2 Parameter utama mesin sinter sirkular |
Subjek | Satuan | Mesin 12 meter persegi | Mesin 17 meter persegi | Mesin 25 meter persegi | Mesin 33 meter persegi |
Produksi tahunan | 1000 tpa | 172 | 253 | 404,5 | 556 |
Total kebutuhan daya | kW | 700 | 1500 | 1750 | 2400 |
Lahan yang dibutuhkan untuk pabrik | m persegi | 8000 | 9000 | 10000 | 12000 |
Dibutuhkan tanah untuk bangunan | m persegi | 800 | 3400 | 35000 | 3600 |
Berbagai fitur dari mesin melingkar adalah sebagai berikut.
- Jika dibandingkan dengan mesin garis lurus, biaya investasi modalnya rendah dan masa konstruksinya singkat.
- Penyegelan lebih baik dan kebocoran udara lebih sedikit di mesin ini karena kotak angin bergerak secara serempak dengan kisi dan karena penyegelan air diadopsi.
- Sistem pengosongan membuat ukuran sinter dingin sedemikian rupa sehingga tidak memerlukan penghancur tambahan.
- Mesin melingkar memiliki fleksibilitas operasional yang tinggi.
Sebuah mesin sinter melingkar ditunjukkan pada Gambar 4.
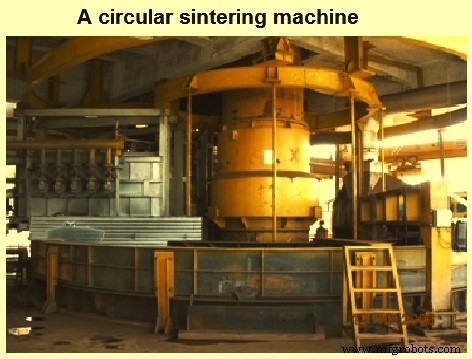
Gambar 4 Mesin sintering melingkar
Mesin garis lurus biasanya digunakan untuk pabrik sinter berkapasitas tinggi. Area sintering dari mesin tersebut umumnya 50 meter persegi ke atas. Mesin garis lurus saat ini dipasang dengan lebar mulai dari 2 m hingga 5 m dan dengan area sintering efektif mulai dari 200 meter persegi hingga 600 meter persegi. Produktivitas mesin tersebut biasanya dalam kisaran 30 t/sqm/hari sampai 46 t/sqm/hari. Kapasitas mesin tersebut berkisar dari 190.000 ton per tahun hingga 6,5 Mtpa. Sebuah mesin lurus ditunjukkan pada Gambar 5.
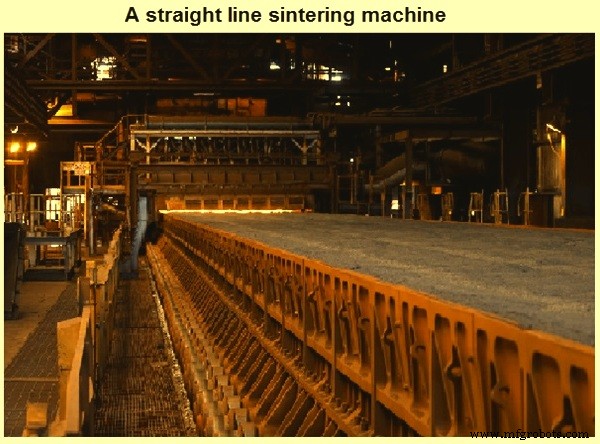
Gbr 5 Mesin sintering garis lurus
Masalah penting terkait dengan sinter dan pabrik sinter
Berikut ini adalah isu-isu penting terkait dengan sinter dan tanaman sinter.
- Penggunaan sinter mengurangi laju kokas dan meningkatkan produktivitas dalam tanur tinggi.
- Proses sintering membantu pemanfaatan butiran bijih besi (0-10 mm) yang dihasilkan selama operasi penambangan bijih besi.
- Proses sintering membantu mendaur ulang semua bahan limbah besi, bahan bakar, dan bantalan fluks di pabrik baja.
- Proses sintering memanfaatkan gas produk dari pabrik baja.
- Sinter tidak dapat disimpan dalam waktu lama karena menghasilkan butiran halus yang berlebihan selama penyimpanan yang lama.
- Sinter menghasilkan butiran halus/debu yang berlebihan selama beberapa kali penanganan di pabrik sinter.