Pengantar proses Pelet dan Pelet bijih besi
Pengantar Proses Pelet dan Pelet Bijih Besi
Pelletizing adalah proses yang melibatkan pencampuran partikel halus bijih besi halus berukuran kurang dari 200 mesh (0,074 mm) dengan aditif seperti bentonit dan kemudian membentuknya menjadi bola dekat oval/spherical dengan ukuran berkisar 8 mm hingga 16 mm dengan pelet dan mengeraskan bola dengan menembakkan bahan bakar. Ini adalah proses aglomerasi untuk mengubah butiran halus bijih besi menjadi 'pelet bijih besi berukuran seragam' yang dapat diisi langsung ke dalam tanur sembur (BF) atau ke dalam tanur vertikal atau tanur putar yang biasanya digunakan untuk produksi besi tereduksi langsung (DRI) . Pelet bijih besi ditunjukkan pada Gambar 1.
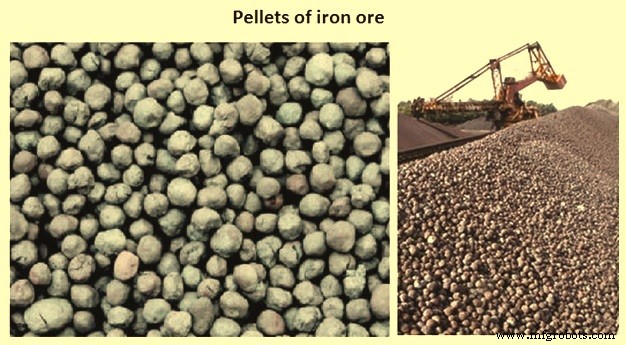
Gbr 1 Pelet bijih besi
Sifat khas pelet bijih besi diberikan di Tab 1
Tab 1 Sifat khas pelet bijih besi |
Analisis kimia (berdasarkan kering) | Satuan | Nilai | Toleransi |
Fe | % | 65 | Minimum |
FeO | % | 0,3 | Maksimum |
SiO2 + Al2O3 | % | 5 | Maksimum |
CaO | % | 0,03 | ± 0,01 |
MgO | % | 0,06 | ± 0,01 |
Dasar | % | 65 | Maksimum |
Fosfor | % | 0,05 | Maksimum |
Sifat fisik | | | |
Kepadatan massal | t/cum | 2.2 | ± 0,2 |
Indeks Tumbler | % | 93 | Minimum |
Indeks abrasi | % | 3 | Min ± 0,5 % |
Kekuatan penghancur dingin (Rata-rata) | kg/p | 250 | Minimum |
Analisis ukuran | | | |
8 mm – 16 mm | % | 94 | Minimum |
-5 mm | % | 2 | Maksimum |
+16 mm | % | 4 | Maksimum |
Sifat metalurgi | | | |
Porositas | % | 18 | Minimum |
Reduksibilitas | % | 62 | Minimum |
Teknologi proses
Ada empat tahap yang terlibat dalam produksi pelet bijih besi. Tahapan tersebut terdiri dari (i) persiapan bahan baku, (ii) pembentukan bola atau pelet hijau, (iii) indurasi pelet, dan (iv) pendinginan, penyimpanan dan pengangkutan pelet.
Persiapan bahan baku – Selama proses peletisasi konsentrat bijih besi dari pabrik benefisiasi bijih besi dikeringkan dan dipanaskan sampai sekitar 120 derajat C. Bahan kering diumpankan ke ball mill untuk digiling. Konsentrat/bijih besi giling dengan ukuran khas 80% kurang dari 45 mikron (0,045 mm) dengan kadar air sekitar 9% diperlukan untuk produksi pelet. Pengikat yang sesuai (biasanya bentonit) ditambahkan ke konsentrat yang dicampur secara menyeluruh dalam mixer intensitas tinggi.
Pembentukan bola atau pelet hijau – Pelet hijau dengan kisaran ukuran 8 mm hingga 16 mm disiapkan dalam drum bola atau dalam pelet cakram. Pelet cakram lebih disukai untuk produksi pelet hijau berkualitas karena dalam pelet cakram mudah untuk mengontrol operasi dengan ruang kaki minimum. Pelletizer cakram adalah panci miring dengan diameter sekitar 5 meter (m) hingga 7,5 m. Berputar pada sekitar 6 rpm (rotasi per menit) hingga 8 rpm. Kemiringan disk sekitar 45 derajat dan dapat disesuaikan pada posisi off-line antara 45 derajat hingga 49 derajat.
Campuran yang telah dibasahi sebelumnya diumpankan ke dalam disk dengan laju yang terkendali. Di dalam piringan, bahan tersebut terkoagulasi dan karena gerakan putar yang terus menerus terbentuk menjadi bintil/pelet. Butiran bijih diangkat ke atas sampai gesekan diatasi oleh gravitasi dan material menggelinding ke dasar piringan. Gerak menggelinding ini pertama-tama membentuk butiran-butiran kecil yang disebut biji. Pertumbuhan terjadi pada putaran piringan berikutnya dengan penambahan lebih banyak umpan segar dan tumbukan antara pelet kecil. Saat pelet tumbuh dalam ukuran, mereka bermigrasi ke pinggiran dan ke atas tempat tidur di cakram, sampai meluap ke tepi. Pertumbuhan pelet dikendalikan oleh sedikitnya air yang disemprotkan ke dalam piringan dan penyesuaian kecepatan putaran piringan. Pelet ini disebut pelet hijau karena tidak memiliki kekuatan yang dibutuhkan. Pelet hijau kemudian disaring di layar rol dan bahan ukuran yang dibutuhkan diumpankan ke parut perjalanan dari mesin pelletizing.
Tegangan permukaan air, aksi kapiler air, dan gaya gravitasi di dalam piringan bola adalah gaya-gaya yang bekerja pada partikel bijih. Oleh karena itu, mereka bergabung bersama dan membentuk inti yang tumbuh dalam ukuran dan menjadi bentuk bola. Gaya-gaya ini bertanggung jawab atas aglomerasi butiran halus bijih besi yang dihasilkan dalam balling disc karena gerakan rotasi pada balling disc. Ketika partikel padat bersentuhan dengan air, permukaan bijih dibasahi dan dilapisi dengan film air. Karena tegangan permukaan film air, jembatan cair terbentuk. Sebagai hasil dari pergerakan partikel di dalam piringan bola dan karena kombinasi dari tetesan air individu yang mengandung butiran bijih, partikel pertama menggumpal. Aglomerasi awal partikel menyebabkan pembentukan biji. Jembatan cair di bagian dalam biji ini menahan partikel bersama-sama seolah-olah partikel berada dalam jaringan. Dengan pasokan air lebih lanjut, aglomerat mengembun dan menjadi lebih padat. Gaya kapiler jembatan cair lebih aktif pada tahap pembentukan bola hijau ini. Optimal dari fase pembentukan bola ini terjadi ketika semua lubang di dalam bola diisi dengan cairan. Ketika partikel padat sepenuhnya dilapisi dengan air, tegangan permukaan tetesan air menjadi aktif sepenuhnya mendominasi gaya kapiler. Selain efek ini, gerakan bergulir butir dan gerakan atau pergeseran partikel relatif satu sama lain juga memainkan peran penting.
Indurasi – Selama indurasi, pengerasan panas pelet hijau dilakukan. Indurasi pelet hijau terdiri dari tiga langkah utama yaitu (i) pengeringan pelet hijau, (ii) pembakaran pelet pada suhu sekitar 1300 derajat C untuk mensinter partikel oksida besi, dan (iii) pendinginan pelet panas sebelum dibuang.
Selama pengeringan (kisaran suhu 180 derajat C hingga 350 derajat C), kadar air pelet hijau diuapkan. Kelembaban permukaan dan interstisial menguap pada suhu yang lebih rendah di mana air yang digabungkan secara kimiawi (seperti goetit atau limonit) atau kombinasi hidrat atau hidroksida apa pun kehilangan airnya pada suhu yang sedikit lebih tinggi. Selama tahap pra-pemanasan (kisaran suhu 500 derajat C sampai 1.100 derajat C), dekomposisi karbonat dan hidrat terjadi. Gasifikasi bahan bakar padat seperti batu bara atau kokas dan konversi oksida besi seperti goetit, siderit, dan magnetit menjadi hematit tingkat oksida yang lebih tinggi, juga berlangsung selama tahap ini. Dimulainya ikatan oksida padat dan pertumbuhan butir adalah langkah penting dari tahap ini. Selama tahap pembakaran (kisaran suhu 1250 derajat C hingga 1340 derajat C), suhu berada di bawah suhu leleh fase oksida utama tetapi dalam kisaran reaktivitas komponen gangue dan aditif. Pembentukan oksida dan ikatan terak sangat menentukan tahap ini.
Ikatan butiran mineral yang berkembang selama indurasi pelet dipengaruhi oleh tiga faktor yang terdiri dari (i) ikatan oksida padat, (ii) kristalisasi ulang oksida besi, dan (iii) ikatan terak. Ikatan oksida padat adalah karena oksidasi oksida besi besi menjadi oksida besi besi yang menghasilkan ikatan dan jembatan, tetapi hanya dengan jumlah terbatas. Rekristalisasi oksida besi pada dasarnya adalah proses fisik di mana partikel yang lebih kecil berkonsolidasi menjadi partikel yang lebih besar dengan hilangnya energi permukaan. Selama kristalisasi ulang oksida besi, pertumbuhan kristal oksida besi yang berkelanjutan memberikan kekuatan yang cukup. Selama proses tersebut, pertumbuhan butir untuk hematit dimulai pada sekitar 1100 derajat C. Dalam kasus ikatan terak, gangue dengan membentuk media transportasi lelehan untuk oksida besi atau besi, memfasilitasi pertumbuhan butir dan kristalisasi butir oksida. Ini juga memungkinkan mekanisme untuk bekerja pada suhu yang lebih rendah daripada yang dibutuhkan jika tidak ada.
Perlakuan indurasi menyebabkan reaksi kimia tertentu terjadi yang mengubah sifat metalurgi spesifik pelet. Reaksi-reaksi ini dapat mencakup oksidasi magnetit dan dehidrasi hematit tanah. Untuk kelas BF, pelet fluks diproduksi dengan penambahan batu kapur, dolomit, silika, dll. ke umpan balling. Penambahan ini bereaksi dengan gangue dalam bijih besi untuk meningkatkan kinerja pelet dalam langkah-langkah pemrosesan hilir tertentu.
Pendinginan dan penanganan pelet – Pelet didinginkan dan disaring setelah indurasi. Pelet yang berukuran lebih besar dihancurkan dan dikirim bersama dengan yang berukuran lebih kecil ke tempat penyimpanan stok tempat mereka diproses ulang. Pelet yang didinginkan dikirim ke penyimpanan untuk diangkut ke pabrik hilir untuk diproses lebih lanjut.
Proses peletisasi
Ada beberapa proses/teknologi pelet bijih besi yang tersedia untuk produksi pelet. Beberapa di antaranya adalah (i) proses shaft furnace, (ii) proses straight traveling grate, (iii) proses grate kiln, (iv) proses cement bonded (proses Grangcold, Proses MIS Grangcold, dan proses char dll), dan (v ) proses hidro-termal, (proses COBO, proses MTU, dan proses INDESCO dll.). Namun, saat ini, hanya proses straight traveling grate (STG) dan proses grate kiln (GK) yang lebih populer.
Proses parut perjalanan lurus
Proses ini dikembangkan oleh mantan Lurgi Metallurgie dan memperhitungkan kapasitas terpasang utama global. Dalam proses ini, skrin rol dek ganda memastikan ukuran pelet hijau yang tepat (berukuran 8 mm hingga 16 mm) didistribusikan secara merata di seluruh lebar jeruji jalan. Grate membawa pelet hijau di tempat tidur yang memiliki ketinggian dalam kisaran 300 mm sampai 550 mm melalui tungku yang memiliki beberapa zona. Zona ini dengan updrafting, downdraft pengeringan, pemanasan awal, pembakaran, setelah pembakaran dan pemanasan zona. Sebuah flowsheet dari proses diberikan pada Gambar 2.
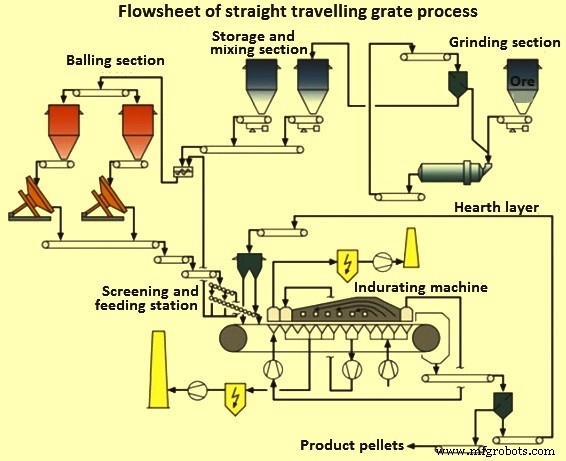
Gbr 2 Flowsheet proses straight traveling grate
Proses kiln parut
Proses grate kiln dikembangkan oleh mantan Allis Chalmer dan pabrik pertama dengan teknologi ini dibangun pada tahun 1960. Dalam proses grate kiln (Gbr 3) traveling grate digunakan untuk mengeringkan dan memanaskan pelet. Material bergerak di atas grate berjalan lurus hingga mencapai suhu dalam kisaran 800 derajat C hingga 1000 derajat C. Setelah itu, bahan dipindahkan ke tanur putar berlapis refraktori untuk indurasi di mana suhu dinaikkan lebih lanjut dalam kisaran 1250 derajat C hingga 1300 derajat C. Pada 800 derajat C, FeO dari bijih besi magnetit diubah menjadi Fe2O3 dalam reaksi eksotermik. Panas yang dibebaskan mengeraskan bola hijau yang berguna untuk menahan dampak jatuh karena rotasi tanur putar. Sebuah pendingin melingkar digunakan untuk pendinginan pelet dipecat. Flowsheet dari proses grate kiln diberikan pada Gambar 3.
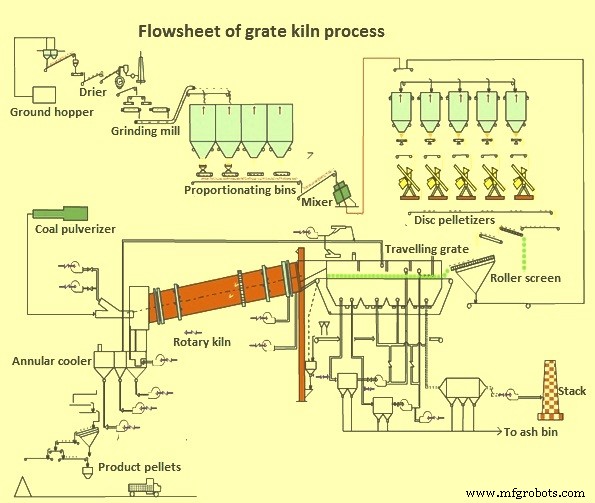
Gbr 3 Flowsheet proses grate kiln
Perbandingan kedua proses diberikan di Tab 2.
Tab 2 Perbandingan antara proses straight traveling grate dan grate kiln process |
Nomor Sl. | Proses parutan jalan lurus | Proses kiln parut |
1 | Siklus pengeringan, pemanasan awal, indurasi, dan pendinginan dilakukan dalam satu unit | Siklus pengeringan, pemanasan awal, indurasi, dan pendinginan dilakukan di unit yang berbeda |
2 | Pelet hijau tetap tidak terganggu selama proses | Seluruh proses berlangsung di tiga peralatan yaitu travelling grate, rotary kiln dan circular cooler sehingga terjadi transfer pellet. |
3 | Mobil parut bergerak dengan kecepatan yang sama di zona pengeringan, indurasi, dan pendinginan. Setiap gangguan di satu zona memengaruhi zona lainnya | Kontrol independen dari tiga zona sehingga proses memiliki fleksibilitas operasional yang lebih baik |
4 | Penghasilan denda dapat diabaikan karena tidak ada transfer material | Karena pemindahan material terjadi di beberapa tempat, maka timbul denda yang lebih tinggi |
5 | Tidak ada persyaratan kekuatan untuk produk antara | Sebelum dipindahkan ke kiln, pelet hijau harus dikeraskan secukupnya |
6 | Ketersediaan proses lebih tinggi | Ketersediaan proses lebih rendah |
7 | Konsumsi energi spesifik lebih tinggi | Konsumsi energi spesifik lebih rendah |
8 | Lebih sedikit perawatan | Perawatan lebih tinggi |
9 | Penghasilan debu yang lebih rendah | Penghasilan debu yang lebih tinggi |
10 | Biaya investasi lebih tinggi | Biaya investasi lebih rendah |
11 | Cocok untuk bijih hematit dan magnetit | Proses lebih cocok untuk bijih magnetit.. |
Perbandingan distribusi suhu selama dua proses ditunjukkan pada Gambar. 4
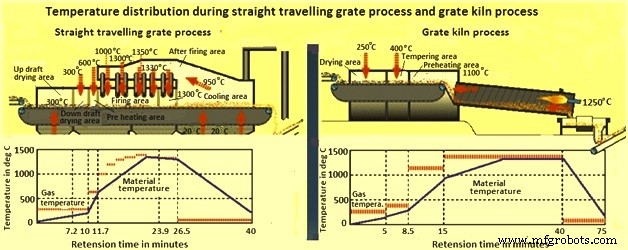
Gbr 4 Perbandingan distribusi temperatur selama dua proses
Keuntungan pelet
Berbagai keuntungan pelet bijih besi diberikan di bawah ini.
- Pelet bijih besi merupakan jenis butiran halus yang teraglomerasi yang memiliki indeks jatuh yang lebih baik jika dibandingkan dengan bijih besi dan dapat digunakan sebagai pengganti bongkahan bijih besi baik dalam produksi BF maupun untuk produksi DRI.
- Pelet memiliki reducibility yang baik karena memiliki porositas yang tinggi (25% sampai 30%). Biasanya pelet berkurang jauh lebih cepat daripada sinter serta gumpalan bijih besi. Porositas tinggi juga membantu metalisasi yang lebih baik dalam produksi DRI.
- Pelet memiliki ukuran yang seragam pada umumnya berkisar antara 8 mm -16 mm.
- Pelet memiliki bentuk bulat dan pori-pori terbuka yang memberikan permeabilitas lapisan yang baik.
- Pelet memiliki sudut istirahat yang rendah yang merupakan kelemahan karena menciptakan distribusi pengikat yang tidak merata.
- Analisis kimianya seragam karena dikontrol selama proses benefisiasi. Kandungan Fe bervariasi dalam kisaran 63% hingga 68% tergantung pada kandungan Fe dari butiran halus bijih. Tidak adanya LOI (loss on ignition) adalah keuntungan lain dari pelet.
- Pelet memiliki kekuatan mekanik yang tinggi dan seragam serta dapat diangkut ke jarak jauh tanpa menimbulkan butiran halus. Selanjutnya, ia telah mendapat perlawanan terhadap disintegrasi. Kekuatan mekanik dan seragam yang tinggi dari pelet bahkan di bawah tekanan termal dalam mengurangi atmosfer.