Proses Pembuatan Besi HIsmelt
Proses Peleburan Pembuatan Besi
Proses HIsmelt merupakan teknologi peleburan langsung berbasis udara yang sederhana namun inovatif. Proses ini untuk produksi besi cair (logam panas) menggunakan bijih besi halus atau bahan pakan besi lain yang sesuai. Peleburan dilakukan dalam penangas besi cair dengan menggunakan batubara sebagai reduktor dan bahan sumber energi. Bahan baku utama yang dibutuhkan untuk proses ini adalah bijih besi halus, batu bara dan fluks (batu kapur dan dolomit).
HIsmelt adalah kependekan dari 'peleburan intensitas tinggi'. Ini adalah proses peleburan langsung untuk membuat besi cair langsung dari bijih besi. Proses telah dikembangkan untuk mengolah butiran bijih besi dengan minimal pra-perlakuan, membuat proses lebih fleksibel dalam hal kualitas bijih besi yang dapat diolah. Proses ini memungkinkan penggunaan batu bara non kokas dan bijih besi halus dengan pengotor yang signifikan. Produk utama dari proses ini adalah besi cair atau logam panas yang dapat digunakan di bengkel peleburan baja atau dapat dicor di mesin pig casting untuk menghasilkan pig iron. Produk sampingan dari proses ini adalah terak dan gas buang.
Kekuatan pendorong untuk pembuatan besi alternatif ini adalah (i) kemampuan untuk memanfaatkan bahan baku yang lebih murah dan lebih melimpah seperti batubara non-coking dan bijih yang tidak diaglomerasi, (ii) ukuran pabrik ekonomi yang lebih kecil, (iii) modal dan biaya operasi yang kompetitif, (iv) mengurangi masalah lingkungan melalui penghapusan oven kokas dan pabrik sinter / pelet, dan (v) fleksibilitas operasi. Proses HIsmelt sangat fleksibel karena dapat menggunakan berbagai macam umpan besi, termasuk limbah pabrik baja dan bijih fosfor tinggi. Proses tersebut dapat menggunakan bijih yang berukuran minus 6 mm, yang merupakan pakan pabrik sinter biasa, dan juga dapat memproses bijih yang merupakan pakan pelet khas, yaitu 80% lebih halus dari 40 mikrometer tanpa ada perubahan dalam hasil besi dalam proses tersebut. . Batubara mulai dari angin kokas hingga batubara non-coking yang mudah menguap 38% dapat digunakan.
Fitur utama proses
Proses HIsmelt sederhana dan telah menunjukkan tingkat keandalan yang tinggi. Mekanisme dasar dari proses HIsmelt adalah reduksi dan peleburan bijih yang mengandung besi dengan karbon terlarut dalam penangas logam. Hal ini dicapai dengan injeksi dan pembakaran parsial batubara secara langsung ke dalam bak dan dengan mentransfer panas yang dihasilkan oleh pasca pembakaran gas yang berkembang dari bak dengan semburan udara panas yang diperkaya oksigen kembali ke bak. Pengayaan oksigen dari semburan udara panas (kandungan oksigen hingga 30%) telah berhasil digunakan untuk meningkatkan intensitas operasi kapal, menghasilkan peningkatan produktivitas yang diharapkan. Keseluruhan reaksi dan mekanisme perpindahan panas menyediakan energi yang cukup untuk mempertahankan reaksi reduksi dan panas untuk peleburan besi dan terak.
Proses ini terjadi dalam Smelt Reduction Vessel (SRV) vertikal di bawah tekanan yang merupakan inti dari proses HIsmelt (Gbr 1). SRV memiliki perapian berlapis tahan api dan cangkang atas berpendingin air. Prosesnya dilakukan di kapal ini. Perapian tahan api berisi rendaman besi cair dan terak cair. Lapisan terak tebal terletak di atas rendaman logam. Denda bijih besi, batubara dan fluks disuntikkan langsung ke dalam lelehan di SRV. Setelah kontak dengan penangas besi, pelarutan karbon dalam batubara terjadi, yang bereaksi dengan oksida dalam umpan bantalan besi, membentuk karbon monoksida (CO). Pemanasan batubara yang cepat juga mengakibatkan retaknya volatil batubara yang melepaskan hidrogen.
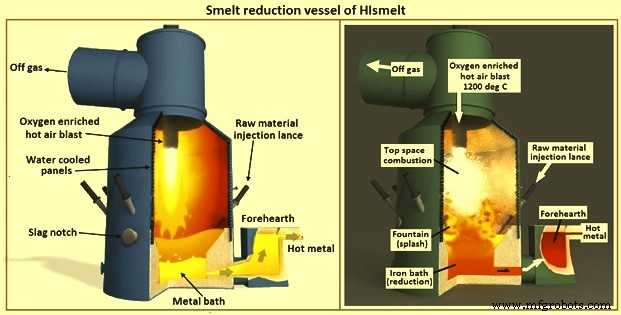
Gbr 1 Bejana reduksi bau HIsmelt
Sebuah air mancur dari bahan cair, yang sebagian besar terdiri dari terak, meletus ke ruang atas oleh pengusiran cepat gas pembawa CO, hidrogen dan nitrogen dari bak cair. Udara panas pada 1.200 derajat C dihembuskan ke ruang atas melalui tombak berpendingin air. CO dan hidrogen pasca dibakar dengan oksigen dari ledakan udara panas. Logam dan terak yang dipanaskan jatuh kembali ke dalam bak yang menyediakan energi untuk peleburan langsung bijih besi. Terak yang dikeluarkan melapisi panel berpendingin air, yang mengurangi kehilangan energi.
Gas lepas dari proses didinginkan sebagian dalam tudung tabung membran. Energi sensibel dan kimia dalam gas lepas kemudian dapat digunakan untuk mempengaruhi beberapa pemanasan awal, pra-reduksi dan / atau kalsinasi umpan dan fluks logam. Gas yang hilang kemudian dibersihkan dalam scrubber dan digunakan sebagai bahan bakar untuk kompor sembur panas atau di pembangkit listrik bersama.
Kapal dilengkapi dengan perapian untuk penyadapan terus menerus dari logam panas. Ini mempertahankan tingkat rendaman yang optimal di dalam SRV dan menyediakan aliran produk yang bersih tanpa perlu pemisahan terak dan logam eksternal. Terak diketuk secara berkala melalui takik berpendingin air.
Proses peleburan HI memiliki sejumlah fitur unik yang membedakannya dari proses peleburan langsung lainnya. Fitur-fitur ini diberikan di bawah ini.
- Proses ini menggunakan rendaman logam sebagai media reaksi utama. Proses peleburan langsung lainnya biasanya memberi makan atas bijih dan batubara, dengan peleburan melalui arang (ditambah sedikit logam) di lapisan terak. Karbon terlarut dalam logam adalah reduktor yang lebih mudah tersedia daripada arang dalam terak, karena yang terakhir membutuhkan fase gas antara (CO). Dengan kata lain, proses HIsmelt mencapai tingkat peleburan yang jauh lebih cepat dengan menggunakan karbon dalam bentuk yang lebih aktif (yaitu terlarut).
- Faktor pembeda lainnya adalah tingkat pencampuran dalam lelehan. Menyuntikkan bahan umpan langsung ke logam menghasilkan volume besar gas 'dalam'. Ini menciptakan gumpalan ke atas yang didorong oleh daya apung yang pada gilirannya menyebabkan pergantian cairan yang cepat. Telah dihitung bahwa omset ini adalah urutan ton per detik. Di bawah kondisi ini, ada potensi yang sangat kecil untuk membentuk gradien suhu yang signifikan (lebih besar dari 20 derajat C hingga 30 derajat C) dalam fase cair dan sistem beroperasi dengan (pada dasarnya) lelehan isotermal. Pergantian massa yang cepat mendorong perpindahan panas yang baik dari ruang atas ke bak mandi tanpa pemanasan berlebih yang signifikan dari tetesan cairan individu. Implikasinya signifikan untuk refraktori perapian di wilayah garis terak, karena pencampuran yang baik menyebabkan batu bata terkena FeO rendah dan suhu seragam (rendah).
- Metode injeksi padat menggunakan tombak berkecepatan tinggi memastikan efisiensi penangkapan dalam lelehan tinggi dan bahkan ultra halus dapat digunakan secara langsung.
- Tingkat FeO 'alami' 5% hingga 6% dalam terak bersama dengan karbon logam pada 4% menciptakan kondisi untuk partisi fosfor yang kuat dari logam menjadi terak. Biasanya sekitar 80% sampai 90% fosfor masuk ke dalam slag (Gbr 2).
- Kinerja batubara hampir tidak bergantung pada morfologi partikel, karena batubara digiling halus untuk injeksi.
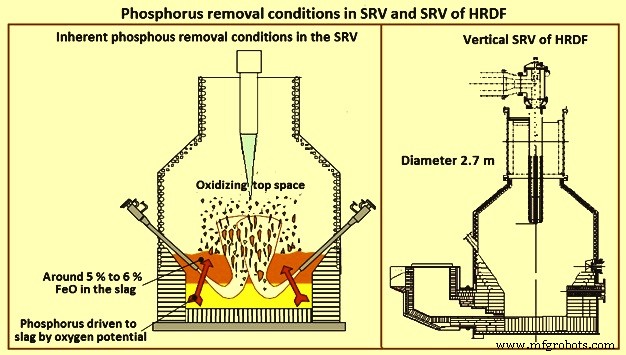
Gbr 2 Kondisi penyisihan fosfor di SRV dan SRV HRDF
Pengembangan proses historis
Asal usul proses HIsmelt ditelusuri kembali ke proses pengubah oksigen tiup bawah (OBM) dan evolusi proses pembuatan baja tiup gabungan yang dikembangkan oleh Klöckner Werke di pabrik baja Maxhütte mereka. CRA (sekarang Rio Tinto) membentuk usaha patungan pada tahun 1981 dengan Klöckner Werke untuk mengejar teknologi pengurangan peleburan dan pembuatan baja. Uji coba dilakukan pada konverter OBM 60 ton untuk mendemonstrasikan dasar-dasar proses reduksi smelt. Keberhasilan pengujian konsep pengurangan peleburan menghasilkan pabrik percontohan skala kecil (SSPP) dengan kapasitas sekitar 12.000 ton per tahun yang berlokasi di pabrik baja Maxhütte. Desain SSPP didasarkan pada SRV berputar horizontal yang menggunakan tuyer bawah untuk injeksi batubara, fluks dan bijih besi. SSPP beroperasi dari 1984 hingga 1990 dan membuktikan kelayakan teknologinya.
Tahap pengembangan proses selanjutnya adalah Fasilitas Penelitian dan Pengembangan HIsmelt (HRDF) yang dibangun di Kwinana, Australia Barat. Pembangunan HRDF dimulai pada tahun 1991. HRDF memiliki kapasitas desain 100.000 ton per tahun. Tujuan utama dari HRDF adalah untuk mendemonstrasikan proses dan skala rekayasa dari pabrik inti dan untuk menyediakan data operasi untuk evaluasi komersial. Konfigurasi SRV asli untuk Kwinana adalah peningkatan langsung dari SRV SSPP dan didasarkan pada kapal berbentuk horizontal yang mampu berputar hingga 90 derajat. Kapal horizontal dioperasikan dari Oktober 1993 hingga Agustus 1996. Sementara peningkatan proses berhasil ditunjukkan, kompleksitas rekayasa kapal horizontal membatasi kelangsungan komersialnya.
Untuk mengatasi kekurangan ini, sebuah desain dikembangkan untuk bejana vertikal berpendingin air. Desain dan rekayasa untuk SRV vertikal (Gbr 2) diselesaikan pada tahun 1996. Perbaikan utama yang dimasukkan ke dalam desain termasuk bejana vertikal stasioner, injeksi atas bahan baku padat, tombak ledakan udara panas yang disederhanakan, perapian untuk penyadapan terus menerus dari panas. panel berpendingin air dan logam untuk mengatasi masalah keausan tahan api.
Bejana pengurang smelt vertikal HRDF ditugaskan pada paruh pertama tahun 1997 dan dioperasikan hingga Mei 1999. Bejana vertikal menunjukkan peningkatan besar dalam hal keausan tahan api, keandalan, ketersediaan, produktivitas, dan kesederhanaan dalam desain. Kapal ini memenuhi semua persyaratan utama untuk keberhasilan teknologi pembuatan besi peleburan langsung – menggabungkan pencapaian teknis tingkat tinggi dengan konsep rekayasa sederhana dan teknologi pabrik. Tahap operasi ini menegaskan bahwa proses telah siap untuk ditingkatkan ke tingkat pabrik komersial.
Sebuah usaha patungan dibentuk pada tahun 2002 antara Rio Tinto (60 %), Nucor Corporation (25 %), Mitsubishi Corporation (10 %), dan Shougang Corporation (5%) untuk tujuan membangun dan mengoperasikan 800.000 ton per tahun HIsmelt tanaman. Terletak di Kwinana, Australia Barat, fasilitas pig iron merchant dirancang dan direkayasa dengan SRV diameter perapian 6 meter. Konstruksi pabrik dimulai pada Januari 2003. Komisioning dingin dimulai pada paruh kedua tahun 2004 sedangkan komisioning panas dilakukan pada kuartal kedua 2005. Pabrik telah mencapai tingkat produksi 80 ton logam panas per jam pada awal 2008 dengan tingkat batubara 810 kg per ton logam panas.
Karena kondisi ekonomi pada tahun 2008, pabrik Kwinana ditutup dan pada tahun 2014 sebagian peralatan Kwinana dipindahkan dari Australia ke China. Pabrik HIsmelt baru terletak di dekat Pelabuhan Shouguang di Provinsi Shandong, dan dimiliki dan dioperasikan oleh Molong Petroleum Machinery Limited, sebuah perusahaan baja swasta. Pabrik Molong HIsmelt dimulai pada tahun 2016 dan telah menghasilkan logam panas dengan biaya lebih rendah daripada tanur sembur mini lokal yang sebelumnya digunakan oleh Molong. Sendok logam panas dikirim oleh kendaraan jalan ke pabrik pembuatan baja oksigen dasar Molong yang terletak 40 km selatan pabrik HIsmelt. Pada tahun 2017, Molong membeli kekayaan intelektual HIsmelt dari Rio Tinto untuk melisensikan teknologi tersebut kepada pengguna lain di China dan luar negeri.
Proses
Proses HIsmelt, digambarkan pada Gambar 1, melibatkan injeksi bahan padat berkecepatan tinggi (batubara, bijih besi dan fluks) ke dalam penangas besi cair pada suhu sekitar 1450 derajat C. Mekanisme dasar dari proses ini adalah reduksi dan peleburan besi bantalan bijih dengan karbon terlarut di bak mandi. Proses ini menggunakan injeksi batubara dan bijih berkecepatan tinggi ke dalam lelehan melalui tombak injeksi berpendingin air yang miring ke bawah. Batubara yang disuntikkan setelah pemanasan dan devolatilisasi larut untuk mempertahankan sekitar 4% karbon dalam logam cair dan mengisi kembali karbon yang digunakan dalam reaksi reduksi. Denda bijih besi yang disuntikkan disuntikkan jauh ke dalam bak di mana mereka langsung berkurang saat kontak dengan karbon terlarut dalam bak untuk peleburan berlangsung. Reaksi reduksi ini menghasilkan besi dan CO. Bagian bawah SRV dipertahankan pada potensial oksigen rendah untuk memungkinkan reaksi reduksi ini terjadi dan kinetika reaksi seimbang pada sekitar 5% sampai 6% FeO (oksida besi) dalam terak.
Gas reaksi (CO) dan produk devolatilisasi batubara yang dihasilkan dari jauh di dalam bak membentuk air mancur (percikan) yang sebagian besar terak dan beberapa logam. Pasokan panas untuk menjaga keseimbangan termal yang diperlukan berasal dari pembakaran gas reaksi (kebanyakan CO) di bagian atas SRV. Ledakan panas yang diperkaya oksigen (biasanya 35%) pada 1.200 derajat C dimasukkan melalui tombak atas dan secara efisien membakar gas yang dihasilkan di dalam bak dan melepaskan energi dalam jumlah besar. Pembakaran ini terjadi di daerah yang relatif mengoksidasi di bagian atas SRV. Perpindahan panas antara daerah atas (pengoksidasi) ke daerah bawah (pereduksi) dicapai sedemikian rupa sehingga gradien potensial oksigen dipertahankan. Ini dilakukan melalui sejumlah besar percikan cairan yang bergerak di antara dua wilayah. Terak cair dan percikan logam bertindak sebagai pembawa panas.
Injeksi bahan diatur sedemikian rupa sehingga penetrasi padatan yang signifikan ke dalam penangas besi dicapai yang mengarah pada pelarutan karbon ke dalam logam dan reduksi bijih besi melalui reaksi keseluruhan yang diberikan oleh persamaan 3[C]besi + Fe2O3 =2 [Fe] besi + 3CO. Reaksi ini sangat endotermik dan, jika prosesnya dipertahankan, diperlukan suplai panas dari luar. CO ditambah hidrogen yang dilepaskan dari bak menyediakan bahan bakar untuk menghasilkan panas ini. Ledakan panas (udara yang diperkaya oksigen pada 1.200 derajat C) disuntikkan ke ruang atas melalui pusaran pusaran pusat dan pembakaran terjadi untuk membakar gas mandi menjadi karbon dioksida dan air sesuai persamaan 2CO + O2 =2CO2 dan 2H2 + O2 =2H2O.
Secara teoritis diinginkan untuk mencapai pembakaran total gas mandi ini tetapi, dalam prakteknya, pasca-pembakaran sekitar 50% sampai 60% biasanya dicapai. Pasca-pembakaran (PC) didefinisikan sebagai rasio konsentrasi volumetrik spesies yang terbakar seperti yang diberikan oleh persamaan PC (%) =100(CO2 =H2O) / (CO + CO2 + H2 + H2O).
Peleburan terjadi di leburan di mana potensi oksigen rendah, sedangkan pembangkitan panas terjadi di ruang atas di mana potensi oksigen relatif tinggi. Kunci dari proses ini adalah memindahkan panas dari daerah pembakaran ke daerah peleburan tanpa mengurangi potensi oksigen di kedua zona tersebut.
Ketika CO dan H2 dilepaskan dari peleburan di dalam bak, laju pelepasannya sedemikian rupa sehingga dihasilkan erupsi cairan yang hebat. Logam dan terak dilemparkan ke atas membentuk air mancur yang dapat menyerap gas (percikan) dengan luas permukaan yang tinggi untuk perpindahan panas. Gas pembakaran panas melewati air mancur ini dan, dengan demikian, mentransfer panas ke tetesan terak dan logam yang pada gilirannya mengirimkan panas ini ke bak mandi. Logam meninggalkan bejana secara terus menerus melalui lubang depan yang meluap (yang secara efektif merupakan segel manometer logam cair), sedangkan terak diketuk secara berkala melalui dinding samping bejana melalui takik terak berpendingin air.
Produk utama dari proses ini adalah logam panas. Logam panas disadap terus menerus melalui perapian terbuka dan bebas dari terak. Suhu tipikal logam panas adalah sekitar 1.420 derajat C hingga 1.450 derajat C dan komposisi khas logam panas adalah karbon – 4,4% +/- 0,15 %, silikon – kurang dari 0,01%, mangan – kurang dari 0,02 %, fosfor – kurang dari 0,02 % +/- 0,01 %, dan belerang – 0,1 % +/- 0,05 %
Atmosfer pengoksidasi relatif dan terak suhu rendah di SRV menghasilkan sebanyak 90% sampai 95% dari fosfor dalam bahan pakan partisi ke terak (Gbr2). Oleh karena itu proses ini memiliki fleksibilitas untuk menggunakan bijih yang mengandung fosfor tinggi.
Karena terak disadap melalui takik terak, logam panas bebas terak. Logam panas dapat diperlakukan di pabrik desulfurisasi logam panas untuk menurunkan tingkat belerang dari logam panas menjadi kurang dari 0,05%. Lembar aliran khas dari proses HIsmelt ditunjukkan pada Gambar 3.
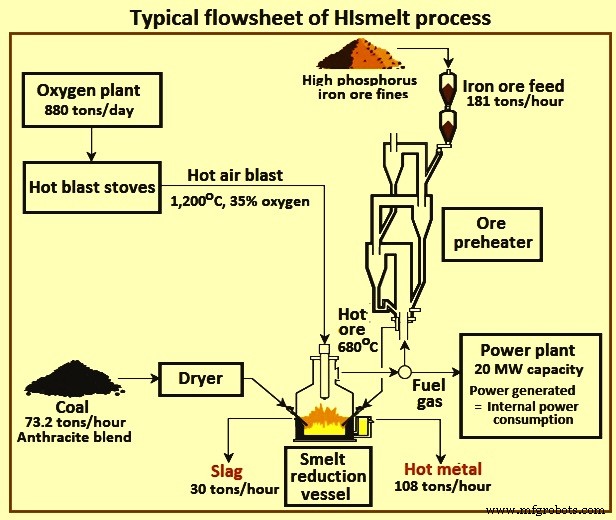
Gbr 3 Flow sheet khas dari proses HIsmelt
Gas lepas dari SRV didinginkan dari 1500 derajat C hingga 800 derajat C oleh tudung ketel radiasi, sebagian dibersihkan dalam siklon panas dan kemudian didinginkan lebih lanjut hingga 200 derajat C melalui sistem ketel konvektif. Ketel radiatif dan konvektif menghasilkan uap jenuh yang mengalir ke drum uap yang terletak di ketel uap.
Gas lepas SRV yang keluar dari boiler konvektif didinginkan, digosok dan didinginkan melalui semprotan air dan disirkulasikan melalui saluran untuk digunakan sebagai bahan bakar untuk kompor sembur panas dan boiler gas mati. Dalam boiler off gas, kelebihan gas off SRV dibakar dan memanaskan uap jenuh dari boiler radiatif, konvektif, dan off gas. Uap super panas ini mengalir ke turbin uap yang menghasilkan daya yang cukup untuk mengoperasikan pabrik HIsmelt, ancillary, dan mengirim kelebihan daya ke jaringan lokal. Gas buang dari boiler gas dan kompor digosok dengan bubur kapur untuk menghilangkan belerang dalam gas sebelum dibuang ke atmosfer.
Produk sampingan dari proses ini adalah slag dan off gas. Terak dibentuk dengan memfluks gangue dalam bijih besi dan abu dalam batubara dengan kapur dan dolomit. Terak dapat digranulasi atau diarahkan ke lubang untuk diproses lebih lanjut. Kemudian dapat digunakan sebagai bahan baku untuk berbagai keperluan seperti pembuatan semen, dasar jalan, atau pengkondisian tanah. Gas keluar dari proses biasanya memiliki derajat pasca pembakaran 50% sampai 60%. Gas-gas ini keluar dari bagian atas SRV pada suhu tinggi dan memiliki nilai energi yang mirip dengan gas tanur sembur. Itu dibersihkan, didinginkan dan digunakan sebagai bahan bakar dan untuk pembangkit listrik.
Proses HIsmelt sangat fleksibel. Sifat proses yang sangat responsif berarti mengubah bijih besi, batu bara, dan fluks menjadi logam, terak, dan energi hampir secara instan. Kemampuan proses memungkinkan laju umpan bahan baku diubah dengan sangat efisien tanpa mempengaruhi kualitas produk. Fleksibilitas pengoperasian ini memaksimalkan produktivitas, karena mudah untuk mempertahankan jendela pengoperasian kondisi stabil. Tidak seperti tanur sembur, proses HIsmelt dapat dimulai, dihentikan atau dihentikan dengan mudah. Gambar 4 menunjukkan tata letak pabrik HIsmelt.
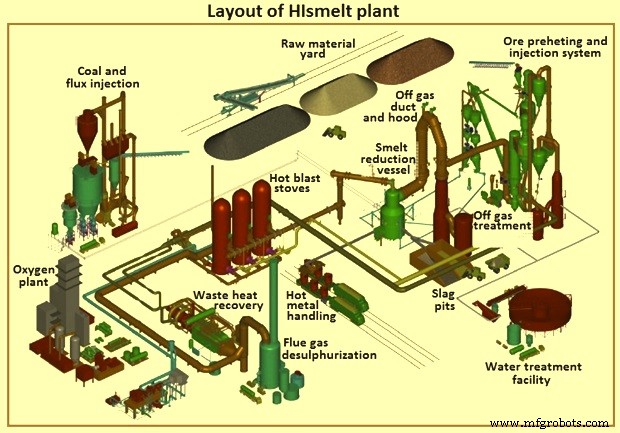
Gbr 4 Tata letak pabrik HIsmelt
Manfaat lingkungan
Manfaat lingkungan dari proses HIsmelt cukup besar. Dengan mengurangi permintaan akan kokas, sinter, dan pelet, serta meningkatkan efisiensi energi dari proses pembuatan besi, ini mengurangi emisi gas rumah kaca dan polutan lingkungan yang merusak lainnya seperti SOx, NOx, dan dioksin. Perbaikan dari proses tersebut adalah (i) pengurangan emisi CO2 sebesar 20%, (ii) pengurangan emisi SOx sebesar 90%, (iii) pengurangan emisi NOx sebesar 40%, dan (iv) tidak ada emisi beracun dengan emisi gas buang. dioksin dan furan pada tingkat nol. Kondisi operasi dalam SRV menghalangi pembentukan dioksin. Selanjutnya ada pengurangan besar dalam emisi debu dan konsumsi air tertentu. Proses dengan mendaur ulang limbah pabrik lebih lanjut membantu dalam perlindungan lingkungan.
Keuntungan
Keuntungan yang diproyeksikan dari proses ini adalah (i) bahan baku berbiaya rendah karena aglomerasi umpan besi dan proses pembuatan kokas dihilangkan, (ii) stok umpan fleksibel karena proses beroperasi pada berbagai butiran bijih besi dan bahan oksida limbah, bersama dengan batubara volatil tinggi dan rendah, (iii) fleksibilitas produksi, (iv) kualitas produk yang lebih baik, (v) konsumsi energi total yang diminimalkan, (vi) konfigurasi rekayasa dan proses yang disederhanakan, (vii) emisi lingkungan jauh di bawah industri, (viii) lebih rendah biaya modal, dan (ix) biaya operasional yang lebih rendah.