Injeksi Batubara Bubuk dalam Tungku Ledakan
Injeksi Batubara Bubuk dalam Tungku Ledakan
Injeksi batubara bubuk (PCI) adalah proses yang melibatkan penyuntikan partikel batubara halus dalam jumlah besar ke dalam jalur tanur sembur (BF). Batubara bubuk merupakan bahan bakar tambahan penting yang digunakan dalam pembuatan besi BF. PCI menyediakan bahan bakar tambahan untuk penggantian kokas parsial dan telah terbukti baik secara ekonomi dan lingkungan. Ini dapat menghasilkan peningkatan substansial dalam efisiensi BF dan dengan demikian berkontribusi pada pengurangan konsumsi energi dan emisi lingkungan.
Ketika pulverized coal diinjeksikan ke dalam BF melalui blowpipes dan tuyeres, batubara tersebut merupakan sumber panas dan reduktor, karena reaksi devolatilisasi, gasifikasi, dan pembakaran serta pembentukan unburned char. Di lingkungan saat ini, batu bara bubuk banyak digunakan dalam BF sebagai pengganti sebagian kokas metalurgi. PCI adalah teknologi mapan saat ini untuk produksi logam panas (HM) di BF. Ini dipraktikkan di sebagian besar BF dan semua BF baru biasanya dibuat dengan kemampuan PCI. Komposisi dan sifat batubara yang digunakan untuk injeksi dapat mempengaruhi operasi, stabilitas dan produktivitas BF, kualitas HM, dan komposisi gas BF.
Dalam skenario ini, ada banyak kriteria yang digunakan untuk mengukur kinerja PCI. Yang pertama adalah penghancuran dan kemudahan penanganan. Biaya operasi utama di PCI, selain biaya batubara, terkait dengan penghancuran dan distribusi batubara ke BF. Yang kedua berkaitan dengan pengoperasian BF. Kualitas batubara yang diinjeksi dapat mempengaruhi kualitas HM, stabilitas BF, dan komposisi gas atas. Abu dari batubara yang diinjeksi (i) dapat bertindak sebagai penghambat proses oksidasi, (ii) merupakan penghantar utama alkali yang tidak diinginkan, dan (iii) mengkonsumsi energi leleh. Yang ketiga berkaitan dengan manfaat ekonomi. Manfaat biaya utama adalah penggantian batu bara kokas berbiaya tinggi ditambah biaya operasi pembuatan kokas, meskipun manfaat lain seperti peningkatan produktivitas juga telah diamati, peningkatan ini tergantung pada kualitas kokas. Manfaat ekonomi dan operasional yang penting dari penggunaan PCI di BF adalah sebagai berikut.
- Konsumsi batubara kokas yang mahal lebih rendah. Mengganti kokas BF dengan kokas lunak atau batubara termal yang lebih murah mengurangi biaya pereduksi.
- Masa pakai oven kokas diperpanjang karena lebih sedikit kokas yang dibutuhkan untuk diproduksi. Hal ini penting karena banyak oven kokas yang mencapai akhir masa pakainya dan diperlukan investasi yang signifikan untuk mengganti atau memeliharanya.
- Sistem PCI lebih murah daripada biaya baterai oven kokas tambahan. Biaya modal yang lebih rendah berarti depresiasi dan bunga yang lebih rendah untuk dibebankan pada HM.
- Produktivitas BF yang lebih tinggi, yaitu jumlah produksi HM yang lebih tinggi per hari (bersamaan dengan perubahan operasional lainnya).
- Fleksibilitas yang lebih besar dalam pengoperasian BF. Misalnya, PCI memungkinkan pengaturan suhu nyala api, dan kondisi termal di BF dapat diubah lebih cepat daripada yang dimungkinkan dengan menyesuaikan muatan beban di bagian atas tungku.
- Meningkatkan konsistensi dalam kualitas HM dan kandungan silikonnya.
- Mengurangi emisi keseluruhan dari pabrik baja, khususnya, menurunkan emisi dari pembuatan kokas karena persyaratan kokas yang berkurang.
Sejarah
Injeksi batubara bubuk dikembangkan pada abad ke-19, tetapi tidak diterapkan untuk keperluan industri. Pada awal 1960-an, PCI berhasil diimplementasikan di AK Steel USA dan Shougang di China. Meskipun uji coba di beberapa negara pada waktu itu telah membuktikan bahwa teknologi untuk transportasi pneumatik dan injeksi batubara telah tersedia, tetapi keekonomisan dan relatif mudahnya prosesnya, injeksi minyak dan gas alam menjadi lebih populer. Pada 1980-an, minat terhadap PCI meningkat, terutama didorong oleh kenaikan dramatis dalam harga bahan bakar minyak pada tahun 1973 dan lagi pada tahun 1979, dan potensinya sebagai pengganti kokas mulai disadari. Pada awal 1980-an, fasilitas injeksi batubara dipasang di seluruh Eropa dan Jepang, dengan laju injeksi normal antara 40 kg/tHM dan 90 kg/tHM dan dengan tingkat penggantian kokas sekitar 0,9 kg kokas/kg batubara. Proses ini berkembang sangat cepat sejak saat itu dan pada paruh kedua tahun 1980-an ada praktik injeksi batubara yang berhasil dengan kecepatan mulai dari 180 kg/tHM hingga 200 kg/tHM. Pada tahun sembilan puluhan teknologi PCI menjadi matang. Namun pergeseran nyata ke PCI hanya terjadi ketika biaya kokas metalurgi mulai meningkat karena meningkatnya permintaan global.
Batubara untuk PCI
Kepentingan relatif dari berbagai aspek kualitas batubara untuk PCI telah bervariasi, karena teknologi injeksi telah meningkat dan laju injeksi meningkat. Pada akhir 1970-an, dipicu oleh krisis minyak, minat terhadap PCI diperbarui dan batu bara dianggap sebagai bahan bakar pengganti minyak yang ekonomis. Karena sifat mudah terbakar dianggap penting, batubara yang digunakan untuk PCI sebagian besar adalah batubara termal. Pada saat itu, batubara termal sudah tersedia dan memiliki biaya yang jauh lebih rendah daripada batubara kokas keras dan kokas semi lunak.
Setelah fokus awal pada pembakaran batubara yang disuntikkan, fokus kemudian diarahkan pada pemahaman tentang dampak kualitas batubara pada penggantian kokas. Selama periode ini, terlihat bahwa batubara volatil rendah (LV) memberikan rasio penggantian yang lebih baik daripada batubara volatil tinggi (HV).
Mengenai penghancuran batubara, empat parameter operasi utama untuk pulverizer adalah (i) laju umpan, (ii) laju aliran udara, (iii) pengaturan pengklasifikasi yang terdiri dari siklon dan bag filter, dan (iv) tekanan penggilingan (beban pada rol/bola). Laju umpan, tekanan penggilingan dan pengaturan pengklasifikasi memiliki pengaruh langsung pada beban pulverizer dan karenanya daya yang dibutuhkan. Laju aliran udara secara tidak langsung mempengaruhi daya pulverizer karena berdampak pada efisiensi pengklasifikasi.
Karakteristik penggilingan batubara biasanya dijelaskan oleh hasil sejumlah kecil tes analitik standar. Berdasarkan hasil ini, prediksi dibuat untuk mengantisipasi perilaku penggilingan batubara. Ada kecenderungan umum untuk mengurangi penilaian perilaku penggilingan batubara ke HGI (Hardgrove Grindability Index), yang merupakan ukuran untuk grindability batubara. Grindability adalah indeks dan karenanya tidak memiliki unit. Semakin kecil HGI, semakin sulit tekstur batubara dan semakin sulit untuk digiling batubara tersebut. Grindability merupakan faktor penting untuk penghancuran batubara di pulverizer. Ini memengaruhi kehalusan produk, konsumsi daya, dan throughput.
Kadar air batubara memiliki pengaruh pada penghancuran batubara. Hal ini diperlukan untuk mengurangi kadar air total yang terkandung dalam batubara ke sekitar tingkat kelembapan keseimbangan untuk mengurangi masalah penanganan di dalam pabrik penghancur serta di dalam bunker. Kadar air batubara yang meninggalkan pulverizer adalah dua pertiga dari tingkat kelembaban keseimbangan. Kuantitas kelembaban yang harus dihilangkan dalam pulverizer diberikan oleh persamaan 'kelembaban yang dihilangkan dalam pulverizer =(sebagai kelembaban yang diterima) – 2/3 (kelembaban keseimbangan)', di mana kelembaban keseimbangan untuk sub-bituminus dan lebih tinggi peringkat batubara kira-kira diberikan oleh persamaan 'keseimbangan kelembaban =0,69 + 0,84 x (kelembaban udara mati) + 0,18 x kuadrat (kelembaban udara mati). Kadar air keseimbangan bervariasi menurut peringkat batubara, komposisi maseral, dan kadar abu.
Jenis batubara dan kelembaban permukaannya mengatur persyaratan pengeringan penghancuran. Kemampuan pengeringan dari desain pulverizer yang diberikan tergantung pada tingkat beban sirkulasi di dalam pulverizer, kemampuan untuk secara cepat mencampur pengembalian pengklasifikasi kering dengan umpan batubara basah yang masuk, dan rasio udara dan suhu saluran masuk udara yang dapat ditoleransi oleh desain pulverizer tertentu. .
Sistem proses PCI
Sistem proses PCI terdiri dari beberapa sub-sistem dari penerimaan batubara hingga injeksi batubara bubuk di setiap tuyere untuk memenuhi persyaratan PCI. Ini terdiri dari enam sub-sistem yaitu (i) penyimpanan dan pembuangan batubara mentah, (ii) penghancuran dan pengeringan batubara mentah, (iii) transportasi, penyimpanan dan pasokan batubara bubuk ke sistem injeksi, (v ) distribusi batu bara bubuk yang merata ke setiap tuyere, (v) pembakaran batu bara bubuk, dan (vi) fasilitas pencegahan ledakan. Karakteristik penting dari sistem proses PCI dijelaskan di bawah ini.
Tangki reservoir dirancang untuk memiliki kapasitas tinggi sehingga bahkan jika salah satu jalur penghancur berhenti beroperasi, injeksi batubara dapat dilanjutkan sampai kondisi operasional yang sesuai, seperti pengurangan jumlah bijih yang dimasukkan ke dalam tungku atau persiapan. untuk meniup diambil.
Ada tiga tangki pengumpan, satu tangki tempat batubara dikeluarkan, tangki kedua dalam keadaan siaga untuk pemakaian, dan tangki ketiga dalam tahap pengurangan tekanan, pengisian batu bara bubuk, dan pemberian tekanan setelah selesai pengisian.
Pipa transportasi, yang terdiri dari pipa fase padat dan pipa fase encer, memastikan transportasi batubara yang lancar dengan kehilangan tekanan yang kecil. Pipa bertekanan tinggi antara tangki reservoir dan tuyeres tidak memiliki bagian yang dapat dipindahkan, kecuali katup penutup, yang memastikan ketersediaan tinggi dan memfasilitasi kontrol dan pemeliharaan.
Untuk proses penghancuran dan penyimpanan, sistem yang andal untuk mencegah ledakan dibuat dengan memasang peredam ledakan, dan alat pemadam kebakaran, dll.
Untuk keberhasilan pengoperasian sistem PCI, perhatian harus diberikan pada berbagai fenomena yang terjadi di BF. Yang penting di antara fenomena ini adalah (i) derajat pembakaran batubara yang diinjeksikan atau perilaku butiran halus batubara yang tidak terbakar di dasar kokas yang mempengaruhi distribusi aliran gas di daerah beban, (ii) perilaku abu batubara yang menyatu atau kemungkinan pengendapannya di pipa sembur zona -tuyere, (iii) permeabilitas atau distribusi aliran gas di zona beban yang dipengaruhi oleh rasio bijih/kokas yang meningkat dengan meningkatnya laju injeksi batubara, dan (iv) sifat termal yang diwakili oleh suhu gas bosh atau rasio aliran panas yang mempengaruhi reaksi berlangsung di bagian bawah BF.
Penempatan tombak injeksi dalam pipa tiup adalah penting dan harus sedemikian rupa untuk memastikan pembakaran sempurna dari batubara yang disuntikkan di dalam zona raceway dan secara bersamaan menghindari deposit abu batubara di ujung pipa sembur. Lembar aliran khas proses PCI ditunjukkan pada Gambar 1.
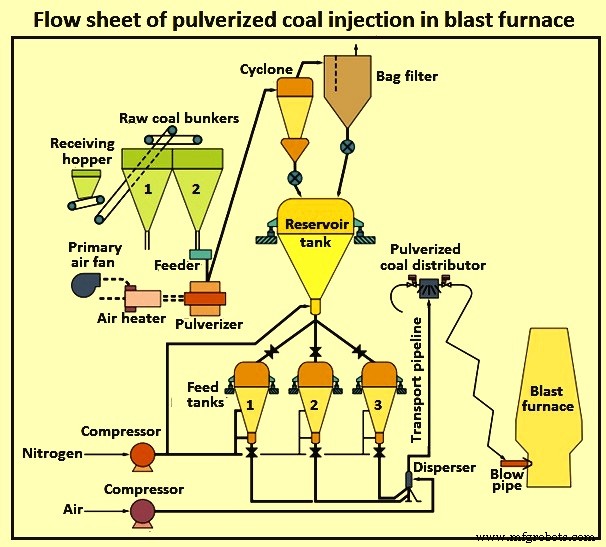
Gbr 1 Lembar aliran tipikal injeksi batu bara bubuk dalam tanur tinggi
Proses injeksi batubara
Proses PCI didasarkan pada konsep sederhana membawa batubara kering yang digiling halus (dihaluskan) dengan gas pembawa (biasanya nitrogen) ke BF di mana ia didistribusikan ke tuyer yang berbeda dan disuntikkan melalui tombak di pipa tiup. Dalam pipa tiup, dicampur dengan udara ledakan panas yang diperkaya oksigen dan kemudian dipasok ke BF di raceway.
Batubara mentah diterima di hopper penerima. Ini disaring dan diproses untuk menghilangkan bahan gelandangan dan disimpan di bunker batubara mentah. Batubara mentah dihancurkan, dikeringkan dan kemudian dikirim secara pneumatik ke pengklasifikasi dalam sistem sekali pakai. Batubara dikeringkan secara menyeluruh untuk mencegah pendangkalan dan pemadatan. Batubara bubuk disimpan dalam tangki reservoir tunggal di mana ia disimpan dalam kondisi inert.
Batubara bubuk adalah diumpankan gravitasi dari tangki reservoir ke tangki umpan yang kemudian diberi tekanan dengan gas inert sebagai bagian dari proses batch di mana tangki umpan mengisi, memberi makan, mengeluarkan atau menahan untuk memberikan aliran bubuk batubara yang terus menerus ke dalam BF. Laju aliran batubara bubuk diatur oleh tekanan gas inert sebagai fungsi dari perubahan berat tangki umpan. Aliran tunggal batubara fase padat dari tangki umpan digabungkan dengan gas transpor (nitrogen) di tee pencampuran.
Sebuah pipa transportasi tunggal membawa campuran batubara/gas ke distributor batubara yang terletak di BF (Gbr 2). Di distributor, aliran tunggal campuran batubara/gas dibagi secara otomatis menjadi beberapa aliran yang sama dan disalurkan melalui pipa ke setiap tuyere untuk diinjeksikan ke BF. Sistem pendeteksi blok melindungi dari penyumbatan tuyere.
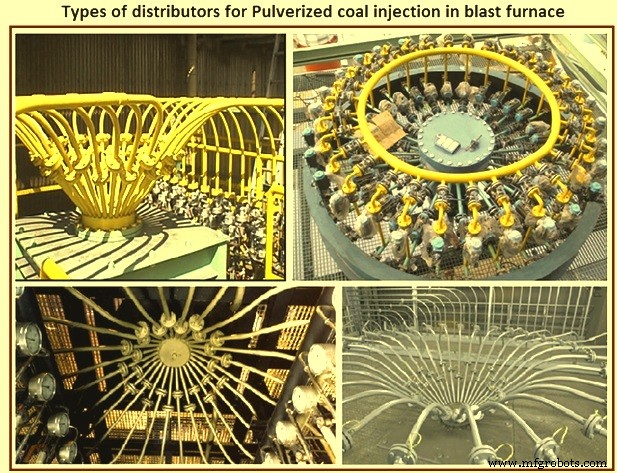
Gbr 2 Jenis distributor
Ada beberapa karakteristik penting dari proses PCI. Dalam sistem loop tertutup, gas yang dipancarkan dari filter sebagian disirkulasikan kembali ke saluran masuk pulverizer. Hal ini menciptakan kondisi inert yang meminimalkan kandungan oksigen dalam sistem dan mengurangi kemungkinan ledakan debu batubara.
Gas limbah kompor BF beserta gas BF (bila diperlukan) digunakan sebagai sumber energi untuk pengeringan batubara sehingga mengurangi konsumsi energi primer. Kelembaban batubara dapat dihilangkan dari sistem dengan sangat efektif tanpa menggunakan pendingin gas atau kondensor. Penggunaan gas inert selama pengoperasian tangki reservoir mengurangi risiko kebakaran dan ledakan.
Berat total batubara yang diinjeksi dikontrol secara tepat oleh sistem sel beban yang menyesuaikan terus menerus untuk memenuhi set point. Susunan tangki umpan yang paralel memastikan aliran batubara yang terus menerus ke dalam BF. Sistem distribusi batubara sederhana dan efektif tanpa bagian yang bergerak.
Laju injeksi biasanya dikontrol dengan memodulasi posisi katup pengukur yang dipasang pada pelepasan tangki umpan. Sistem ini memastikan pemerataan batubara yang disuntikkan di antara jumlah total tuyer dan memiliki kemampuan bawaan untuk mendistribusikan ulang secara otomatis total batubara yang disuntikkan ke dalam BF jika injeksi dihentikan dalam satu atau lebih tuyer karena alasan apa pun.
Nitrogen bertekanan digunakan untuk injeksi batubara bubuk dari tangki umpan ke dalam pipa transportasi. Dengan sejumlah kecil gas transpor tambahan, batubara yang dihaluskan diangkut dan diinjeksikan ke dalam BF dalam kondisi fase padat. Dalam kondisi seperti itu, pemuatan sekitar 40 kg hingga 50 kg batubara per kg gas dicapai dalam pipa pengangkutan batubara.
Batubara diangkut melalui pipa dengan kecepatan hanya beberapa meter per detik. Kecepatan pengangkutan batubara yang rendah mengurangi keausan pada pipa sehingga meningkatkan masa pakainya. Sistem konveyor padat sangat kuat dan dapat mengangkut batu bara yang dihaluskan ke jarak jauh.
Distribusi seragam batubara bubuk ke tuyeres sangat penting. Untuk mengoperasikan BF dengan efisiensi tinggi, distribusi beban dan aliran gas yang seragam dalam arah melingkar sangat penting. Dalam hal ini, laju bubuk batubara yang akan disuntikkan melalui setiap tuyere harus seragam mungkin. Akurasi distribusi yang tinggi diinginkan sekitar 1,5% (akurasi distribusi normal udara ledakan panas adalah sekitar 2,5%) yang diperoleh dengan menggunakan distributor (Gbr 2). Skema injeksi batubara di tuyere dan raceway ditunjukkan pada Gambar 3.
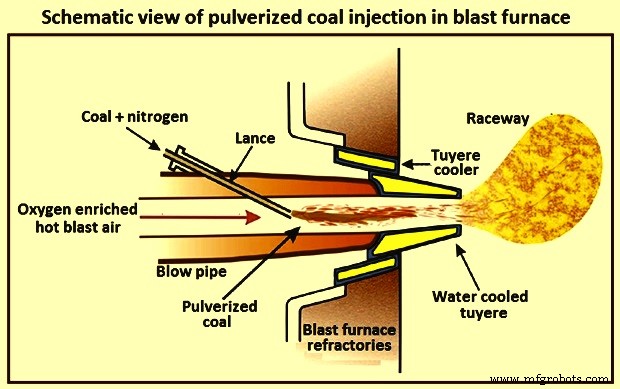
Gbr 3 Skema injeksi batu bara bubuk di tuyere dan raceway
Operasi BF dan PCI
Telah diamati bahwa pada tingkat PCI, lebih tinggi dari 140 kg/tHM, perubahan terjadi dalam operasi BF. Beberapa perubahan tersebut antara lain (i) pengurangan rasio kokas/bijih, (ii) ukuran raceway, (iii) pengurangan permeabilitas kokas di sekitar raceway, (iv) perubahan distribusi suhu di raceway, (v ) degradasi mekanis kokas di raceway, dan (vi) penurunan suhu deadman. Semua perubahan ini saling bergantung dan dipengaruhi oleh sifat dan jumlah batubara yang disuntikkan, kualitas kokas, dan kondisi ledakan.
Permeabilitas – Aliran gas, aliran cairan, dan penurunan beban di dalam BF bersifat dinamis yang mengarah pada munculnya dan hilangnya zona non-aktif di bosh, deadman, atau stack. Untuk produktivitas tinggi dan operasi BF yang stabil dengan tingkat PCI yang tinggi, persyaratan penting adalah aliran batubara yang konsisten dan sifat batubara melalui masing-masing tuyer. Kualitas batubara yang konsisten dapat dikontrol dengan memadukan batubara PCI dan aliran batubara dengan kontrol individual pada setiap tuyere. Sifat batubara dapat berdampak pada aliran gas, cair dan padat yang kompleks di zona bawah BF (Gambar 4), tetapi dampak ini tidak signifikan jika aliran stabil dan kualitas batubara tercapai. Batubara yang disuntikkan dapat mempengaruhi permeabilitas di zona bawah melalui alasan berikut.
- Pembakaran yang mempengaruhi jumlah bahan yang tidak terbakar (arang dan jelaga) yang keluar dari raceway.
- Pembentukan butiran halus coke dalam raceway disebabkan oleh energi yang diberikan ke coke oleh momentum ledakan. Jumlah denda yang dihasilkan tergantung pada kualitas kokas. Momentum ledakan dipengaruhi oleh derajat pembakaran yang terjadi di dalam tuyere.
- Viskositas terak mempengaruhi aliran terak dan HM melalui zona deadman dan penetrasi gas panas dari raceway ke zona deadman yang selanjutnya mengurangi viskositas terak di dalam zona deadman.
Perubahan operasional dapat dilakukan untuk mengatasi permeabilitas yang berkurang pada laju injeksi yang tinggi. Misalnya, pengisian kokas sentral meningkatkan permeabilitas poros BF dan meningkatkan kedalaman raceway meningkatkan permeabilitas dan mengurangi kehilangan beban panas. Beberapa pengaruh PCI pada operasi BF ditunjukkan pada Gambar 4.
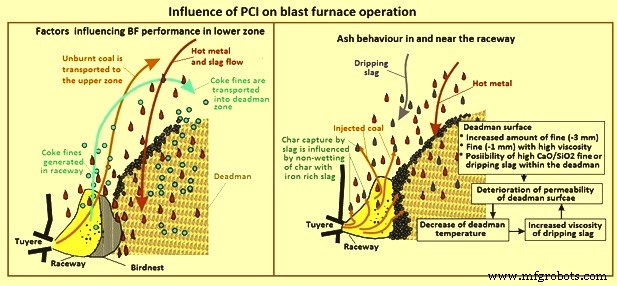
Gbr 4 Pengaruh PCI pada operasi BF
Dampak arang yang tidak terbakar – Pada laju PCI rendah, butiran halus kokas yang dihasilkan di jalur balap dikonsumsi oleh pembakaran, kehilangan larutan, dan reaksi lain di zona BF yang lebih rendah. Pada peningkatan tingkat PCI, telah diamati bahwa ada peningkatan sisa denda dari bagian atas BF serta peningkatan kedalaman raceway fisik dan ketidakstabilan BF. Namun, peningkatan karbon yang terbawa adalah kokas halus dengan sejumlah kecil jelaga dan arang yang tidak terbakar dapat diabaikan. Arang yang tidak terbakar dapat bermanfaat karena dengan adanya arang, ketahanan aus dari kokas meningkat. Perilaku ini tampaknya terbatas pada reaktivitas rendah dan kokas berkekuatan tinggi.
Arang mudah terbakar – Dapat diamati bahwa pembakaran batubara yang diinjeksi pada tingkat tuyere menurun dengan peningkatan laju injeksi atau penurunan bahan volatil batubara. Namun, pembakaran batubara pada 700 mm di atas tuyere adalah lebih dari 95% untuk semua batubara karena reaksi kehilangan larutan dari arang yang tidak terbakar. Arang yang tidak terbakar tidak dikonsumsi oleh reaksi kehilangan larutan terperangkap di BF atau keluar sebagai debu. Diperkirakan laju injeksi maksimum yang dapat diperoleh adalah 230 kg/tHM pada efisiensi pembakaran 75%.
Kondisi pembakaran yang intens di dalam tuyere dan raceway menyebabkan pelepasan volatil yang lebih tinggi. Saat mengevaluasi karakteristik batubara volatil rendah, telah ditemukan rasio volatil yang dilepaskan ke proksimat volatil matter (VM) batubara meningkat secara signifikan dengan peringkat (kandungan karbon) batubara pada tingkat pemanasan tinggi. Ada bukti yang jelas dari fragmentasi partikel yang terbakar. Aliran arang yang tidak terbakar dari raceway berdampak pada permeabilitas zona bawah dan zona deadman BF.
Fragmentasi partikel batubara dapat terjadi selama devolatilisasi (fragmentasi primer) dan selama pembakaran arang (fragmentasi sekunder). Fragmentasi primer dipengaruhi oleh VM batubara. Partikel char yang besar menghasilkan partikel fly ash yang jauh lebih banyak daripada partikel char yang kecil. Peringkat batubara juga memiliki pengaruh besar. Tingkat fragmentasi cenderung meningkat dengan meningkatnya peringkat batubara dan cenderung menurun dengan meningkatnya pemuatan abu.
Di BF, laju pemanasan yang cepat, suhu tinggi, oksigen yang diperkaya, dan umumnya batubara peringkat lebih tinggi yang digunakan untuk PCI, semuanya berkontribusi pada fragmentasi primer dalam tuyere. Di bawah kondisi ini, permukaan luar partikel dapat mengeras karena reaksi dengan oksigen atau anil termal sebelum devolatilisasi lengkap inti bagian dalam partikel. Hal ini menyebabkan fragmentasi ledakan partikel.
Reaktivitas arang meningkat dengan kandungan VM batubara karena perubahan morfologi arang, namun pada suhu tinggi yang berkaitan dengan pembakaran arang di raceway, reaktivitas kimia memiliki signifikansi yang sangat kecil karena laju pembakaran dibatasi oleh laju difusi oksigen ke partikel, dan waktu burnout lebih bergantung pada ukuran partikel dan konsentrasi oksigen. Kandungan abu yang tinggi dalam arang mempengaruhi perilaku pembakaran secara negatif. Sifat mudah terbakar batubara LV dapat ditingkatkan dengan mencampurnya dengan batubara HV, karena batubara HV mengurangi waktu penyalaan dan meningkatkan suhu di dalam tuyere.
Komposisi abu dari arang yang tidak terbakar dapat mempengaruhi efek katalitik abu terhadap reaksi kehilangan larutan. Tergantung pada komposisinya, abu juga dapat memperlambat konversi karbon karena penyumbatan pori-pori arang sebagai akibat dari peningkatan proporsi pembentukan terak dalam partikel arang. Meskipun sebagian besar arang dikonsumsi oleh reaksi dalam tungku karena reaktivitas arang yang secara signifikan lebih tinggi dibandingkan dengan kokas, biasanya diyakini bahwa arang yang tidak terbakar memainkan peran penting dalam penonaktifan orang mati dengan mengurangi permeabilitas arang. deadman untuk aliran gas dan cairan. Penurunan permeabilitas dianggap meningkat dengan peningkatan laju injeksi karena daya bakar batubara menurun karena penurunan rasio udara berlebih. Beberapa arang yang tidak terbakar dapat ditangkap oleh terak yang menetes, meskipun jumlah arang yang ditangkap ini dipengaruhi oleh perilaku non-pembasahan arang dengan terak kaya besi.
Fragmentasi batubara/arang dan pembakaran yang dikendalikan oleh difusi adalah alasan utama mengapa VM memiliki sedikit efek pada pembakaran batubara PCI.
Deposisi arang yang tidak terbakar di BF – Pengendapan arang yang tidak terbakar dan denda kokas di zona bawah Bf adalah fenomena kompleks yang terdiri dari beberapa mekanisme pembangkitan seperti reaksi, aliran multi-fase, akumulasi, dan re-entrainment. Telah ditunjukkan baik dengan pengukuran dalam BF dan secara numerik bahwa bentuk dan ukuran raceway berubah secara dinamis dengan akumulasi dan re-entrainment bubuk di zona yang lebih rendah. Perubahan ini memiliki kira-kira dua periode, periode yang lebih pendek adalah fluktuasi biasa dalam raceway dan periode yang lebih lama sesuai dengan perubahan besar dengan aliran karena akumulasi bubuk. Ini adalah perubahan besar dalam aliran gas yang dapat menyebabkan kecepatan gas tinggi di dekat dinding BF yang mengakibatkan hilangnya panas dan keausan dinding BF yang lebih tinggi.
Akumulasi bubuk di tempat tidur yang dikemas telah diperiksa, secara eksperimental dan numerik. Pekerjaan eksperimental di unggun kemasan 2 dimensi menggunakan partikel 3 mm dan bubuk 0,075 mm telah menunjukkan pengaruh pemuatan bubuk dan kecepatan gas superfisial terhadap akumulasi bubuk di wilayah yang sesuai dengan lantai dan sarang burung dari raceway. Pengaruh bentuk zona kohesif yang berbeda pada akumulasi partikel juga telah ditunjukkan secara eksperimental. Analisis numerik mampu menunjukkan banyak perilaku akumulasi yang sama seperti data uji eksperimental. Analisis numerik ini juga menunjukkan pengaruh signifikan ukuran bubuk terhadap akumulasi bubuk di zona deadman.
Analisis numerik pengaruh serbuk halus (unburnt char dan fine coke) yang telah dilakukan menunjukkan bahwa unburnt char dan fine coke yang memiliki diameter dan densitas berbeda memiliki pola aliran, area akumulasi, dan zona reaksi yang berbeda. Kepadatan serbuk yang dihasilkan memiliki pengaruh yang signifikan terhadap pola aliran serbuk terutama untuk partikel yang lebih besar. Ketika partikel serbuk menjadi lebih besar dari 1 mm, kecenderungannya adalah mengendap dari gas yang mengalir ke atas dan turun ke dalam deadman yang menurunkan permeabilitasnya. Setiap arang yang tidak terbakar lebih disukai dibawa dengan aliran gas ke daerah atas BF di mana ia bereaksi dengan HM dan / atau gas yang menetes. Ada beberapa bukti keberadaan sarang burung walet dengan kandungan denda yang sangat tinggi. Jumlah denda tergantung pada kualitas kokas dan pada tingkat PCI. Denda kokas yang besar dan lebih berat cenderung meninggalkan aliran gas dan terakumulasi di zona deadman yang memiliki efek buruk pada permeabilitas zona yang lebih rendah.
Analisis numerik dan sampel fisik baru-baru ini telah mengkonfirmasi bahwa jumlah arang yang tidak terbakar yang terakumulasi di zona deadman relatif kecil dan tidak meningkat dengan peningkatan laju PCI. Dengan demikian, arang yang tidak terbakar memiliki pengaruh kecil di bagian bawah tungku dan peningkatan resistensi permeabilitas. Kemungkinan besar pengendapan fine coke memiliki pengaruh yang lebih signifikan terhadap permeabilitas BF daripada arang yang tidak terbakar.
Pengaruh sifat kokas – Sering dinyatakan bahwa kebutuhan akan sinter dan coke berkualitas tinggi sangat penting untuk mencapai tingkat PCI yang tinggi dan untuk mempertahankan produktivitas yang tinggi. Sangat penting untuk meningkatkan permeabilitas BF secara keseluruhan untuk mencapai produktivitas tinggi pada kecepatan PCI yang tinggi. Biasanya BF dengan operasi PCI tinggi menggunakan kokas kekuatan tinggi (dalam hal indeks drum) dan SiO2 rendah dan sinter AL2O3 rendah dengan sifat pengurang suhu tinggi yang sangat baik. Beberapa BF Asia mencapai produktivitas tinggi dengan tingkat PCI melebihi 200 kg/tHM dengan menggunakan bahan baku berkualitas tinggi.
Berdasarkan pengalaman industri, terlihat bahwa ukuran kokas bosh meningkat dengan kekuatan dingin (I40), meningkat dengan kekuatan panas (CSR), meningkat dengan ukuran kokas kasar, dan menurun dengan laju PCI. Hasil dari penggarukan tuyere di 'Corus Ijmuiden BF' telah menunjukkan bahwa satu poin I40 menghasilkan 1,5% lebih banyak coke bosh di atas 40 mm persegi. Telah ditemukan bahwa tidak ada hubungan antara laju injeksi batubara dan jumlah kokas halus pada tingkat tuyere. Data untuk injeksi dan I40 menunjukkan bahwa ada degradasi kokas maksimum di sekitar laju PCI 120 kg/tHM.
Sebuah studi yang meneliti perilaku kokas di zona BF yang lebih rendah di bawah tingkat PCI yang tinggi menemukan bahwa arang lebih disukai dikonsumsi. Ini menurunkan konsentrasi CO2 di sekitar partikel kokas dan memperluas lapisan reaksi kokas di sekitar permukaan dan ke bagian dalam partikel. Dengan adanya arang yang disuntikkan, ketahanan aus kokas meningkat dan volume pori total dalam kokas meningkat. Peningkatan ketahanan abrasi dengan peningkatan kecepatan PCI ini dapat menjadi alasan peningkatan ukuran coke bosh pada kecepatan PCI yang tinggi.
Analisis sampel kokas yang diambil pada tingkat tuyere telah menunjukkan bahwa, pada tingkat PCI yang tinggi, sifat suhu tinggi (CSR dan CRI) memiliki efek positif yang lebih besar pada permeabilitas daripada sifat kekuatan dingin. Tampaknya permeabilitas tidak membaik setelah nilai CSR sekitar 65% hingga 70%.
Dalam sebuah penelitian dengan data beberapa BF dengan tingkat PCI di atas 170 kg/tHM, BF memiliki indeks perapian (HI =CRI – 2,5 x CSR + 100 %) di atas 97%, meskipun tidak ada hubungan yang jelas antara HI dan tingkat injeksi. ditemukan. Juga telah diamati bahwa produktivitas meningkat dengan HI. Juga telah disarankan bahwa pada tingkat PCI yang tinggi, kokas harus menahan abrasi (I10 rendah) dan memiliki CSR yang tinggi.
Dalam sebuah penelitian yang meneliti pengaruh kualitas kokas pada produktivitas BF, indeks kualitas kokas global telah dikembangkan. Indeks ini memberikan indikasi variasi panas di bagian bawah BF dan karenanya merupakan gambaran permeabilitas perapian dan poros BF. Indeks kualitas kokas global ini telah ditentukan oleh persamaan Iglobal.coke =0,5 x [(I40 – 3,42 x I10 + 100) + (CSR – 2,6 x CRI + 100)]. Variasi variasi panas di bagian bawah BF dapat dijelaskan oleh variasi di Iglobal.coke. Indeks ini digunakan di beberapa pabrik untuk menentukan strategi operasi BF, jika Iglobal.coke rendah, laju injeksi batubara dan produksi menurun. Telah dipertimbangkan bahwa penambahan batubara yang tidak terbakar ke butiran halus kokas yang ada menyebabkan permeabilitas yang lebih rendah di zona deadman yang mengakibatkan penurunan stabilitas lapisan kokas.
Namun, permeabilitas ditemukan menurun dengan meningkatnya kandungan VM dan kisaran ukuran yang lebih halus dari batubara bubuk. Penjelasan untuk hal ini adalah bahwa dengan meningkatnya daya bakar batubara (peningkatan kandungan volatil dan/atau penggilingan yang lebih halus), pembakaran yang lebih besar di dalam tuyere memberikan volume gas yang lebih besar yang disuntikkan ke raceway, yang mengarah ke momentum ledakan yang lebih besar. Momentum ledakan yang lebih besar ini menyebabkan peningkatan kedalaman raceway dan peningkatan degradasi coke raceway, yang mengarah pada peningkatan carry-over denda coke.
Dalam sebuah penelitian yang meneliti pengaruh energi ledakan pada pembentukan raceway, hubungan linier antara energi ledakan dan kedalaman raceway telah terlihat. Model raceway 2 dimensi menunjukkan hubungan linier antara kecepatan ledakan dan kedalaman raceway untuk ukuran kokas konstan dan dimensi BF. Peningkatan ketidakstabilan deadman dan degradasi kokas karena peningkatan momentum ledakan telah dimodelkan oleh dalam penelitian lain. Model ini menunjukkan bahwa kedalaman raceway meningkat secara linier dengan kecepatan ledakan untuk kekuatan kokas yang konstan.
Dengan menggunakan data dari berbagai penelitian, variasi momentum ledakan dengan kandungan karbon dari batubara yang diinjeksi diperkirakan. Hal ini dapat menunjukkan bagaimana peringkat batubara yang diinjeksi mempengaruhi pembentukan halus kokas. Batubara VM tinggi pada umumnya menghasilkan hingga dua kali lebih banyak kokas halus dibandingkan batubara PCI VM rendah karena peningkatan momentum ledakan yang dihasilkan dari pembakaran volatil di dalam tuyere. Data operasional menunjukkan bahwa, pada laju injeksi sekitar 170 kg/tHM, permeabilitas dan produktivitas meningkat ketika kedalaman raceway ditingkatkan (momentum ledakan lebih tinggi). Memperluas raceway mengurangi area deadman dan karenanya meningkatkan area di mana HM dan slag bisa turun dan di mana aliran gas bisa naik.
Di Eropa, kekuatan kokas dingin dan di Jepang, kekuatan kokas panas digunakan sebagai parameter kokas untuk memantau kualitas kokas oleh banyak pabrik yang beroperasi dengan laju PCI tinggi. There is evidence that coke strength alone is not sufficient to predict the degradation of coke due to physical and chemical mechanisms.
Influence of coal ash chemistry on slag viscosity – The viscosity of the slag can influence the BF productivity since the productivity is related to the flooding phenomenon which can occur in the lower zone of the BF. The slag viscosity can adversely influence the permeability and the liquid flooding factor. Tuyere samples from a Japanese BF has given a valuable insight into the influence of the ash from injected coal on the physical properties of the dripping slag and the permeability of the region surrounding the raceway for a high productivity and operations with high PCI rates.
In recent years, there have been several studies into to the prediction of slag viscosities due to its importance to the flow behaviour of slag in the BFs. In one of the study, a quasi-chemical viscosity model has been developed for fully liquid slags in the Al2O2-CaO-FeO-MgO-SiO2 system, which has shown good agreement between experimental data and predictions over the whole compositional range. The composition of the slag influences the liquidus temperature in SiO2-CaO-MgO-Al2O3 systems. A slag critical temperature at which the viscosity of the slag abruptly changes has been described. At a basicity of less than 1.3, the critical temperature is around 1340 deg C and at a basicity of over 1.3, the critical temperature is around 1380 deg C. Lowering the MgO content of the slag decreases the slag viscosity but the temperature of the slag is the major factor.
A laboratory study has shown that mixing of pulverized fluxes with ash from coke and coal reduces the melting point of the tuyere slag by more than 200 deg C. At the same time slag viscosity is highly improved. In another study the reactions at the interface of unburnt char and iron have been examined. It has been found that the dissolution of carbon into the liquid iron is influenced more by the chemistry of the ash layer that formed at the interface than other factors. An increase in silica content slows the carbon dissolution. Silicon vaporization can occur in some coals. Further, it has been shown that the formation of ferritic iron at the surface can also slow the carbon dissolution.
The alkalis from coke or PCI which are of the most interest to BF operators are Na2O and K2O. Within the BF there is a re-circulation of the alkalis as the alkali vapours produced in the lower section of the furnace are condensed in the upper region of the furnace. High alkali load can lead to the formations of scabs (skulls) on the BF wall leading to BF irregularities like hanging and slipping. The chlorine content of the injected coal can increase the recirculation of alkalis within the BF. The level of re-circulating load can be controlled by adjusting slag volume and the chemistry.
The results of a study into the influence of alkalis in BFs indicate that decreased slag basicity, decreased hearth temperature, increased top gas temperatures, use of low alkali-burden are important factors in the control of alkalis in the BF. The most effective control is to limit alkali input to 2.0 kg/tHM to 2.5 kg/tHM. The main interaction of alkalis with coke occurs as the coke passes through the re-circulating zone becoming enriched in alkalis. This weakens the coke and makes it more susceptible to breakage. The extent of this effect probably depends on the type of carbon texture. The coke loses its alkalis as it proceeds down the furnace through the high temperature zone near the raceway.
With PCI the alkalis from the injected coal evaporate in the raceway and then due to the temperature drop condense in the deadman zone. The peak values of alkalis contents are around 2 m from the tuyere nose. The build-up of alkalis within deadman zone can lead to permeability problems associated with the HM flow to the hearth. In one of the studies on the effect of chlorine and alkali on BF operation, it has been found that a reduction of chlorine and alkali inputs improved BF permeability.