Lapisan tahan api dari tanur tinggi
Lapisan tahan api tanur tinggi
Sebuah tanur sembur (BF) modern dilapisi tahan api untuk melindungi cangkang tungku dari suhu tinggi dan bahan abrasif di dalam tungku. Lapisan tahan api didinginkan untuk lebih meningkatkan perlindungan terhadap pengiriman panas berlebih yang dapat merusak lapisan tahan api. BF memiliki sistem refraktori yang kompleks untuk memberikan masa pakai yang lama dan aman yang diperlukan untuk ketersediaan tanur sembur dan untuk memungkinkan pengoperasian dan pengecoran tungku yang hampir berkesinambungan.
Kondisi dalam tanur sembur sangat bervariasi menurut wilayah dan refraktori dikenakan berbagai mekanisme keausan. Detailnya diberikan pada Tab 1. Kondisi aplikasi berbagai daerah tanur sembur tidak sama karena sifat geometrinya dan juga karena proses pirometalurgi yang terjadi pada tahap yang berbeda. Ada beragam mekanisme keausan fisik dan kimia di berbagai wilayah tanur sembur dan sifatnya kompleks. Misalnya keausan mekanis atau abrasi terjadi terutama di daerah tumpukan atas dan disebabkan oleh bahan pengisi yang layak dan oleh gas sarat debu. Beban termal yang tinggi merupakan faktor utama dalam tumpukan bawah dan daerah perut. Di daerah perapian, aliran horizontal dan vertikal dari logam panas dikombinasikan dengan tekanan termal sering membentuk kavitasi berbentuk kaki gajah yang tidak diinginkan. Bahan tahan api di daerah ini harus menjaga mekanisme keausan ini untuk menghindari kerusakan karena mereka. Oleh karena itu, tumpukan BF (menengah atas dan bawah), perut, bosh, raceway dan wilayah tuyere, perapian, dan taphole semuanya memerlukan kualitas refraktori yang berbeda bergantung pada kondisi aplikasi masing-masing.
Tab 1 Mekanisme serangan di berbagai wilayah tanur tinggi |
| | |
Wilayah | Mekanisme serangan | Mengakibatkan kerusakan |
| | |
Tumpukan atas | Abrasi | Keausan abrasif |
| Fluktuasi suhu sedang | Spalling |
| Dampak | Hilangnya batu bata |
| | |
Stack tengah | Fluktuasi suhu sedang hingga berat | Spalling |
| Erosi gas | Pakai |
| Oksidasi dan serangan alkali | Kerusakan |
| | |
Tumpukan bawah | Fluktuasi suhu yang tinggi | Spalling parah |
| Erosi oleh pancaran gas dan abrasi | Pakai |
| Oksidasi dan serangan alkali | Kerusakan |
| Kelelahan termal | Kerusakan cangkang dan retak |
| | |
Perut | Fluktuasi suhu sedang | Spalling |
| Oksidasi dan serangan alkali | Kerusakan |
| Abrasi, erosi gas, dan suhu tinggi | Pakai |
| | |
Boss | Suhu tinggi | Serangan stres |
| Serangan terak dan alkali | Kerusakan dan keausan |
| Fluktuasi suhu sedang | Spalling |
| Abrasi | Pakai |
| | |
Balapan dan | Suhu sangat tinggi | Tekan retak dan aus |
Wilayah Tuyere | Fluktuasi suhu | Spalling |
| Oksidasi (air dan oksigen) | Kerusakan |
| Serangan dan erosi terak | Pakai |
| Kerusakan akibat koreng | Hilangnya elemen pendingin dan tuyeres |
| | |
Perapian | Oksidasi (air) | Pakai |
| Serangan seng, terak, dan alkali | Kerusakan |
| Suhu tinggi | Peningkatan stres dan retak |
| Erosi dari cairan panas | Tembus risiko |
| | |
Takik besi | Fluktuasi suhu yang tinggi | Spalling |
(lubang ketuk) | Erosi (terak dan besi) | Keausan lubang keran |
| Serangan seng dan alkali | Kerusakan |
| Serangan gas dan oksidasi (air) | Keausan dan kerusakan |
Pemilihan kombinasi tahan api yang sesuai bergantung pada mekanisme keausan sangat penting. Pemilihan refraktori yang tidak tepat sering kali menyebabkan kegagalan refraktori yang kemudian menjadi masalah yang kompleks untuk dipecahkan. Jenis lapisan tahan api yang diperlukan di wilayah tanur tinggi serta tren pola lapisan tahan api diberikan pada Gambar 1.
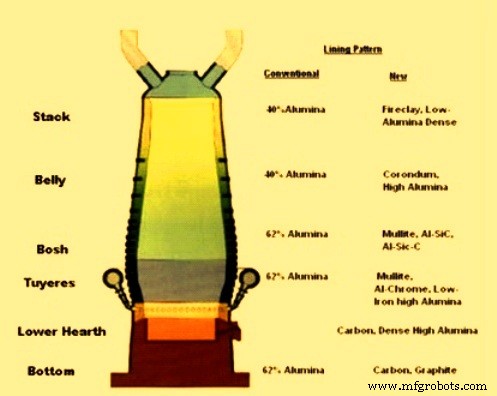
Gbr 1 Lapisan tahan api di berbagai wilayah tanur tinggi
Saat ini masa kampanye seorang BF diperkirakan sekitar 15 tahun atau lebih. Selanjutnya ada kecenderungan BF berkapasitas besar, yang mengalami kondisi operasi yang ketat. Untuk mencapai tujuan umur lapisan yang panjang di bawah kondisi operasi yang ketat, perlu memiliki kombinasi yang baik dari refraktori bermutu tinggi yang dikombinasikan dengan sistem pendinginan yang sangat efisien dan kontrol yang ketat pada operasi tungku untuk memastikan produktivitas tinggi tanpa pengerjaan dinding yang berlebihan dan dengan meminimalkan 'tergelincir' di BF yang dapat menyebabkan kerusakan dini berlebihan pada lapisan refraksi.
Diketahui bahwa bagian bawah dan sebagian perapian terkorosi terutama oleh besi kasar, terak, dan alkali. Batu bata tahan api di area ini mengalami beban dan suhu tinggi. Sehingga diperlukan lapisan tahan api yang harus memiliki kekuatan tinggi, nilai mulur yang lebih rendah dalam nilai kompresi dan nilai RUL (refractoriness under load) dan PCE (pyrometric cone equivalent) yang lebih tinggi. Beberapa BF menggunakan besi rendah, alumina 42% -62 % padat, bata tahan api mullite, blok karbon konvensional, dll. di perapian bawah dan bawah sementara tren saat ini adalah menggantinya dengan blok grafit berpori super mikro. Kehidupan perapian BF sangat bergantung pada faktor-faktor berikut.
- Faktor operasional seperti (i) produktivitas tinggi yang menyebabkan beban panas tinggi, (ii) kecepatan fluida tinggi yang menyebabkan lebih banyak erosi dan (iii) injeksi batubara yang tinggi berarti permeabilitas yang lebih rendah. Tak satu pun dari faktor ini berada di bawah kendali operator BF dan karenanya, satu-satunya solusi untuk ini adalah lapisan tahan api yang kuat.
- Desain sistem pelapis tahan api – Seluruh lapisan tahan api juga mengalami tekanan termal yang juga memainkan peran dominan terutama jika desainnya tidak memadai. Sistem atau desain pelapis tahan api harus (i) mengoptimalkan ketahanan termal, (ii) memberikan bantuan ekspansi, (iii) mencegah keretakan, dan (iv) menghilangkan penghalang bawaan.
- Sifat tahan api – Ini mencakup (i) Konduktivitas termal yang tinggi, (ii) ketahanan alkali, (iii) permeabilitas rendah, (iv) ekspansi termal rendah, dan (v) elastisitas rendah.
Perkembangan terbaru batu bata karbon berpori mikro dan peningkatan kualitas blok grafit dan semi grafit telah menyebabkan ketahanan infiltrasi yang lebih tinggi terhadap besi dan terak, dan konduktivitas termal. Masalah pembentukan lapisan rapuh sekitar 800 derajat C isotermal oleh kondensasi alkali dan tekanan termal telah diatasi dengan menggunakan blok yang lebih kecil, kelonggaran ekspansi optimal, dll. Refraktori karbon ditutupi oleh batu bata fireclay atau mullite untuk melindunginya dari oksidasi. Desain 'cangkir keramik' ini penting, karena isotermnya berubah bergantung pada kualitas dan ketebalan bahan cangkir.
Tumpukan batu bata sangat rentan terhadap abrasi dan erosi tinggi oleh bahan pengisi dari atas serta partikel asap dan debu berkecepatan tinggi yang keluar karena tekanan ledakan tinggi di lingkungan CO (karbon mono oksida). Oleh karena itu, kondisi aplikasi menuntut bahan tahan api yang harus memiliki kekuatan tinggi, permeabilitas rendah, ketahanan abrasi yang tinggi, dan ketahanan terhadap disintegrasi CO. Bata tahan api fireclay tugas super atau bata alumina padat yang memiliki Al2O3 sekitar 39% – 42% dapat memberikan karakteristik ini yang diperlukan untuk aplikasi tumpukan.
Tuyere dan bosh diserang oleh perubahan suhu, abrasi dan alkali; dan perut dan poros bawah oleh kejutan termal, abrasi dan serangan CO dll. Di area kritis BF, yaitu tuyere, bosh, perut dan tumpukan bawah, silikon karbida, SiC-Si3N4 dan refraktori korundum telah menggantikan karbon dan 62 % Al 2 O3 atau batu bata mullite. Ini memanfaatkan konduktivitas termal yang tinggi dari SiC dalam kombinasi dengan pendingin stave. Namun karena masalah kebocoran air di sekitar taphole dan area tuyere, banyak tanur sembur dilapisi dengan refraktori korundum alumina tinggi atau alumina-krom. Saat ini dan tren di refraktori Bf diberikan di Tab 2.
Tab 2 Blast furnace refraktori |
|
Area | Hadir | Tren |
| | |
Tumpukan | 39 % – 42 %% Al2O3 | Tembakan api super tugas |
Perut | 39 % – 42 % Al2O3 | Korundum, SiC-Si3N4 |
Bos | 62 % Al2O3, Mullite | SiC-Si3N4 |
Tuyere | 62 % Al2O3, Mullite | SiC terikat sendiri, Alumina-chrome (Corundum) |
Perapian bawah | 42 % -62 % Al2O3, Mullite, Blok karbon konvensional | Blok Karbon/Grafit dengan pori-pori super mikro |
Ketuk lubang | Ikatan tar Fireclay, Ikatan alumina tinggi / tar SiC | Ikatan tar Fireclay, Ikatan alumina / tar SiC tinggi |
Lembah utama | Massa ramming berikat pitch / air / Grog / Tar, Castables | Ultra low cement castables (ULCC), campuran SiC / Alumina, teknik perbaikan Gunning |
Memiringkan cerat | Massa ramming alumina / SiC tinggi / castable semen rendah | Alumina tinggi / SiC / Karbon / ULCC |
Berbagai jenis refraktori BF
Berbagai jenis refraktori yang digunakan dalam lapisan tanur tinggi dijelaskan di bawah ini.
- Blok karbon panggang – Blok karbon berpori mikro, blok karbon semi grafit, dan blok silikon karbon berpori mikro dibuat dengan antrasit yang dikalsinasi secara elektrik, grafit sintetis, dan silikon karbida suhu tinggi sebagai bahan baku utama. Mereka memiliki konduktivitas termal yang lebih tinggi, permeabilitas yang lebih rendah, logam panas yang baik dan ketahanan alkali. Blok karbon semi grafit digunakan sebagai lapisan bawah bawah. Blok karbon berpori mikro digunakan sebagai pelapis bagian bawah atas dan perapian bawah tanur sembur dengan peleburan intensif. Blok silikon karbon berpori mikro digunakan untuk meletakkan perapian, lubang keran, dan lubang terak tanur sembur.
- Batu karbon panggang berukuran kecil – Batu bata karbon berpori mikro yang dicetak dan batu bata silikon karbida karbon diproduksi melalui pembentukan panas, pemanggangan suhu tinggi dan penggilingan akhir dengan antrasit yang dikalsinasi secara elektrik suhu tinggi, grafit sintetis dan silikon karbida sebagai bahan baku utama dan minyak yang berasal dari batubara atau resin fenolik formaldehida sebagai pengikat serta aditif bubuk ultra mikro. Batu bata silikon karbida karbon berpori mikro yang dicetak dapat digunakan untuk pembuatan bata tuyere, lubang terak, lubang keran, perapian, dan zona pembentukan terak dari tanur tinggi.
- Bata cangkir keramik – Ini adalah bata korundum komposit fase terikat plastik. Bata terdiri dari mullite berkualitas tinggi dan korundum leburan kemurnian tinggi sebagai bahan baku dengan penambahan pengikat tertentu dengan membentuk pada tekanan tinggi dan sintering pada suhu tinggi. Dengan fitur refraktori tinggi di bawah beban (RUL), struktur kompak, porositas rendah dan ketahanan tinggi terhadap korosi, batu bata digunakan untuk bagian bawah BF, lapisan bawah cangkir keramik dan batu bata gabungan tuyere, lubang keran dan lubang terak dari ledakan besar tungku.
- Bata korundum – Bata korundum terbuat dari korundum leburan coklat dan silikon karbida sebagai bahan awal, dikombinasikan dengan aditif khusus, melalui proses pencetakan cetakan dan sintering sebelum pemesinan halus. Batu bata dicirikan oleh ketahanan alkali yang baik dan ketahanan korosi terak, yang cocok untuk melapisi bagian bawah, cangkir keramik perapian, tuyere, lubang keran dan lubang terak.
- Bata SiC- Si3N4 – Ada banyak jenis bata SiC dengan sistem ikatan yang berbeda dan kandungan SiC yang bervariasi. Secara umum, SiC terikat langsung memiliki ketahanan yang tinggi terhadap alkali dan seng. Juga, mereka memiliki konduktivitas termal yang tinggi, ketahanan erosi yang sangat baik, sifat kejutan termal yang sangat baik, dan tahan terhadap korosi dan serangan CO. Umumnya, SiC terikat nitrida digunakan dalam aplikasi, seperti perut BF.
- Bata karbon alumina berpori mikro – Batu bata ini dibuat dengan mengadopsi klinker bauksit kelas khusus, korundum, grafit dan alumina tengah sebagai bahan baku utama, dikombinasikan dengan beberapa jenis aditif bubuk super halus. Ini fitur pori mikro, ketahanan alkali yang baik dan konduktivitas termal yang tinggi. Digunakan untuk melapisi bosh, stack, dan cooling wall BF.
- Batu bata kelas alumina 50% – Biasanya refraktori di kelas ini adalah bata api tugas super yang ditingkatkan. Mereka umumnya terdiri dari campuran bauksit, tanah liat batu api/chamotte dan tanah liat plastik. Batu bata alumina 50% biasanya memiliki porositas rendah, mengembang saat dipanaskan kembali hingga 1600 derajat C dan memiliki ketahanan yang baik terhadap siklus termal. Batu bata di kelas ini yang mengandung bahan dengan kemurnian lebih tinggi menunjukkan kualitas bantalan beban yang baik dan memiliki ketahanan yang sangat baik terhadap serangan alkali.
- Bata kelas alumina 60% – Batu bata di kelas ini terdiri dari berbagai macam bahan. Batu bata mid alumina yang paling umum dan sangat dihargai terdiri dari mineral dari kelompok sillimanite (biasanya dikombinasikan dengan sejumlah kecil alumina terkalsinasi dan tanah liat plastik). Kualitas alumina 60% lainnya di kelas ini terdiri dari campuran chamotte sintetis, bauksit, alumina terkalsinasi dan tanah liat plastik. Pembentukan mullite tingkat tinggi memungkinkan batu bata di kelas ini (terutama refraktori yang mengandung sillimanite) untuk menunjukkan ketahanan mulur yang sangat baik. Batu bata silimanit sering kali dapat diikat dengan fosfat/kimiawi dan diawetkan sebagai cara untuk meningkatkan ketahanan sengatan panas.
- Batu bata kelas alumina 70% – Batu bata kelas ini dibuat dari bahan baku utama bauksit atau chamotte alumina tinggi yang ditambahkan dengan fireclay. Batu bata ini dibakar hingga sekitar 1400 derajat C untuk mencegah ekspansi berlebihan selama pembakaran (disebabkan oleh reaksi bahan silika dengan bauksit, membentuk mullite). 70% batu bata alumina menunjukkan nilai ekspansi yang tinggi dalam pelayanan sehingga mengurangi ukuran sambungan.
- 80 % batu bata kelas alumina – Ini didasarkan pada bauksit dengan penambahan bahan alumina dan tanah liat yang dikalsinasi. Mereka ditembakkan ke sekitar 1420 – 1480 derajat C untuk mempertahankan ukuran bata yang konsisten. Produk yang dibakar di kelas ini memiliki porositas sekitar 20%, kekuatan dan ketahanan yang baik terhadap siklus termal. Produk ini terkait dengan ikatan fosfat/kimia (baik yang diawetkan dan dibakar) sebagai sarana untuk memberikan ketahanan yang lebih besar terhadap abrasi dan mengurangi porositas.
- Fireclay batu bata – Batu bata Fireclay terdiri dari campuran biasanya dua atau lebih tanah liat. Penggunaan lempung batu api dan kaolin memberikan sifat tahan api, lempung terkalsinasi (chamottes) mengontrol penyusutan pengeringan dan pembakaran, dan lempung plastik memfasilitasi pembentukan dan kekuatan ikatan. Bata fireclay biasanya dikelompokkan menjadi (i) bata super duty (PCE> 33) yang memiliki tipikal kandungan alumina 40% sampai 45% dan memiliki refraktori yang baik, tahan terhadap goncangan termal dan stabilitas volume pada suhu yang lebih tinggi, (ii) tinggi bata tahan api tugas (PCE 31 hingga 33) yang mirip dengan setara tugas super tetapi biasanya dibuat dari lempung batu api/chamotte berkualitas rendah dan lempung plastik (khas Al2O3 40 % hingga 45%) dan biasanya digunakan sebagai pengganti batu bata tahan api menengah di mana siklus termal merupakan masalah potensial, (iii) bata tahan api tugas menengah (PCE 29 hingga 31) (al2O3 tipikal 38% hingga 42%) digunakan dalam aplikasi yang tidak terlalu berat dan ketahanan kejut termalnya lebih rendah daripada bata api super dan tugas tinggi, (iv) bata tahan api tugas rendah (PCE 15 hingga 29) (al2O3 tipikal 35% hingga 38%) digunakan sebagai pelapis penahan dan aplikasi lain di mana suhu sedang lazim, dan (v) bata tahan api semi silika yang memiliki kandungan alumina tipikal 18 % hingga 25% dengan nilai silika s mulai 72% hingga 80% dan memiliki kekuatan bantalan beban yang sangat baik dan stabilitas volume pada suhu yang relatif lebih tinggi.
- Massa tap hole – Karakteristik utama yang dibutuhkan dari massa tap hole termasuk viskositas yang baik dan sifat sintering yang baik dikombinasikan dengan ketahanan korosi dan erosi.