Pengujian Baja Non Destruktif
Pengujian Baja Tak Merusak
Pengujian non-destruktif (NDT) baja adalah sekelompok teknik analisis yang digunakan untuk mengevaluasi sifat-sifat bahan baja, komponen, atau lasan tanpa menyebabkan kerusakan pada mereka. Teknik NDT digunakan untuk mendeteksi dan mengevaluasi cacat internal dan permukaan (seperti ketidaksempurnaan, diskontinuitas, dan cacat dll.) yang dapat menyebabkan kegagalan di bawah kondisi operasi yang dirancang. Cacat internal dan permukaan ini mungkin merupakan area dengan integritas yang lebih rendah dibandingkan dengan bagian lain dari material baja atau mungkin terdiri dari adanya retakan, rongga dan ketidaksempurnaan lainnya. NDT memberikan hasil tidak langsung namun valid dan, menurut definisi, membiarkan objek uji sesuai dengan tujuan penggunaannya.
Istilah pemeriksaan tidak merusak (NDE), pemeriksaan tidak merusak (NDI), dan evaluasi tidak merusak (NDE) juga digunakan untuk teknik pengujian ini. Karena tidak ada perubahan permanen pada material baja yang diuji dengan teknik NDT, teknik NDT dianggap sangat penting untuk inspeksi material. NDT menghemat uang dan waktu dalam evaluasi produk, pemecahan masalah, dan penelitian.
Teknik NDT merupakan jenis pekerjaan yang sangat khusus yang memainkan fungsi kritis. Teknik ini memerlukan layanan teknisi yang sangat terspesialisasi dan berkualifikasi yang menggunakan peralatan dan metode canggih untuk mengevaluasi area komponen baja yang sulit atau tidak mungkin diperiksa dengan mata telanjang.
Teknik NDT digunakan untuk mendeteksi cacat selama pembuatan dan fabrikasi serta cacat yang terjadi selama servis komponen baja. Namun, tidak mungkin untuk mendeteksi semua kemungkinan cacat dengan memeriksa komponen dengan NDT. Lebih lanjut di NDT, bukan cacat yang terdeteksi tetapi efek yang dihasilkan pada material seperti modifikasi sifat fisik (pelemahan terhadap suara ultra atau konduktivitas listrik, dll.). Teknik NDT tidak memberikan informasi langsung tetapi informasi tidak langsung yang perlu diinterpretasikan. Beberapa teknik NDT lebih langsung dan akurat daripada yang lain.
Ada berbagai teknik NDT yang dapat digunakan untuk mengevaluasi material baja, komponen, atau lasan. Semua teknik NDT memiliki beberapa elemen umum yang meliputi berikut ini.
- Ada beberapa sumber energi penyelidik atau beberapa jenis media penyelidik.
- Ada diskontinuitas yang harus menyebabkan perubahan atau pengubahan media probing.
- Ada beberapa cara untuk mendeteksi perubahan.
- Ada beberapa cara untuk menunjukkan perubahan.
- Ada beberapa cara untuk mengamati dan/atau merekam indikasi ini sehingga dapat dilakukan interpretasi.
Kesesuaian teknik NDT untuk aplikasi tertentu ditentukan dengan mempertimbangkan elemen di atas. Sumber energi penyelidik atau media penyelidik harus sesuai untuk benda uji dan untuk mendeteksi cacat atau diskontinuitas yang dicari. Jika ada, cacat atau diskontinuitas harus mampu memodifikasi atau mengubah media penyelidik. Setelah diubah, ada beberapa cara untuk mendeteksi perubahan ini. Perubahan pada media penyelidik ini dengan diskontinuitas adalah untuk membentuk beberapa indikasi atau direkam. Terakhir, indikasi ini perlu ditinjau ulang agar dapat diinterpretasikan dan untuk mengklasifikasikan diskontinuitas.
Sejumlah teknik NDT telah dikembangkan, masing-masing memiliki kelebihan dan keterbatasan sehingga kurang lebih sesuai untuk aplikasi tertentu. Dengan berbagai teknik NDT yang tersedia, penting untuk memilih teknik yang memberikan hasil yang diperlukan. Kombinasi teknik NDT yang berbeda juga dapat diterapkan untuk memberikan jaminan bahwa bahan atau komponen layak untuk digunakan.
Ada banyak metode NDT bahan dan komponen baja yang berbeda. Metode NDT yang lebih umum digunakan untuk evaluasi bahan baja, komponen, atau lasan adalah (i) inspeksi visual, (ii) inspeksi penetran pewarna, (iii) pengujian partikel magnetik, (iv) inspeksi radiografi, (v) pengujian ultrasonik, dan (vi) pengujian arus eddy.
Pemeriksaan visual
Inspeksi visual adalah bentuk pemeriksaan NDT yang paling umum, primer, murah, dan tertua. Itu bergantung pada deteksi ketidaksempurnaan permukaan menggunakan mata, tidak memerlukan peralatan pengujian khusus (kecuali alat bantu sederhana seperti kaca pembesar), dan dapat diselesaikan lebih cepat dan ekonomis. Namun, karena sifat subjektif dari inspeksi visual, variabilitas hasil inspeksi sering terjadi. Cacat tersebut juga tidak dapat dideteksi dengan inspeksi visual yang tidak terlihat oleh mata. Tiga persyaratan dasar untuk inspeksi visual adalah (i) penglihatan yang baik sehingga dapat melihat diskontinuitas yang dicari, (ii) pencahayaan yang baik, jenis cahaya yang tepat adalah penting, dan (iii) pengalaman, harus mampu mengenali diskontinuitas.
Pemeriksaan penetran pewarna
Dalam metode inspeksi penetran pewarna, penetran pewarna digunakan untuk mendeteksi cacat permukaan dengan 'keluarnya' media penetrasi dengan latar belakang yang kontras. Pewarna penetrasi diterapkan pada permukaan yang telah dibersihkan sebelumnya dari bahan baja yang akan diuji dan dibiarkan selama periode yang ditentukan (waktu tinggal) karena aksi kapiler menariknya ke cacat permukaan apa pun. Penetran berlebih kemudian dihilangkan dan pengembang diterapkan. Pengembang membalikkan aksi kapiler dan menarik penetran dari cacat. Indikasi yang dihasilkan mengungkapkan adanya cacat sehingga dapat dilihat secara visual dan cacat dapat diamati dan dievaluasi oleh teknisi. Metode pemeriksaan penetran pewarna ditunjukkan pada Gambar 1.
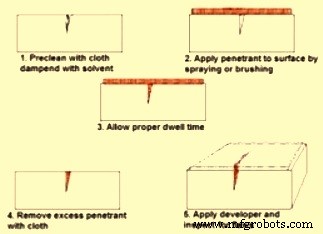
Gbr 1 Pemeriksaan penetran pewarna
Ada dua metode penetran pewarna diklasifikasikan yaitu (i) berdasarkan jenis indikasi yang dihasilkan, dan (ii) metode penghilangan. Hasil pengujian penetran pewarna juga ditampilkan dalam dua cara, terlihat dan berpendar. Jenis penetran yang terlihat menghasilkan garis merah tebal atau indikasi regangan dengan latar belakang pengembang putih bila dilihat dalam kondisi cahaya putih yang baik. Penetran fluoresen menghasilkan indikasi fluoresen hijau ketika diamati di bawah sinar ultraviolet. Karena mata manusia dapat lebih mudah melihat indikasi fluoresen daripada indikasi yang terlihat, penggunaan inspeksi penetran fluoresen dalam pengujian yang lebih sensitif.
Metode kedua klasifikasi penetran didasarkan pada cara dimana kelebihan penetran dihilangkan dari permukaan uji. Penetran dapat dicuci dengan air, dapat dilepas dengan pelarut, atau dapat diemulsikan kembali. Penetran yang dapat dicuci dengan air mengandung pengemulsi yang memungkinkan penetran dibilas menggunakan semprotan air bertekanan rendah. Penetran penghilang pelarut membutuhkan pelarut untuk menghilangkan kelebihan penetran dari permukaan uji. Penetran pasca-emulsi dihilangkan dengan menambahkan pengemulsi setelah waktu tunggu penetran.
Proses ini sederhana, serbaguna dan hemat biaya dan dapat ditingkatkan lebih lanjut dengan menggunakan pewarna berwarna cerah atau fluoresen. Satu-satunya kelemahan adalah hanya dapat mendeteksi cacat permukaan.
Pengujian partikel magnetik
Pengujian partikel magnetik digunakan untuk menemukan diskontinuitas permukaan dan sedikit di bawah permukaan atau cacat pada bahan feromagnetik seperti baja. Cacat seperti itu ada di bagian yang dimagnetisasi menyebabkan medan magnet (fluks) meninggalkan bagian itu. Jika partikel magnetik diterapkan ke permukaan ini, mereka akan ditahan di tempatnya oleh kebocoran fluks untuk memberikan indikasi visual. Sementara beberapa metode yang berbeda dari uji partikel magnetik dapat digunakan, semuanya bergantung pada prinsip umum yang sama ini. Ini adalah proses yang sangat sederhana dan hemat biaya.
Pengujian partikel magnetik dilakukan dengan cara menciptakan medan magnet pada bagian yang akan diuji dengan cara menempelkan partikel magnetik pada permukaan uji. Prosesnya dilakukan baik di lapangan, menggunakan kuk magnet portabel, atau di toko menggunakan bangku magnet. Bangku lebih efisien untuk volume pekerjaan yang besar.
Pengujian partikel magnetik baja umumnya dilakukan dengan menggunakan jenis elektromagnet tertentu. Elektromagnet bergantung pada prinsip bahwa ada medan magnet yang terkait dengan konduktor listrik apa pun. Arus bolak-balik (AC) atau arus searah (DC) dapat digunakan untuk menginduksi medan magnet. Medan magnet yang diciptakan oleh AC karena 'efek kulit' paling kuat di permukaan benda uji. AC juga memberikan mobilitas partikel yang lebih besar pada permukaan objek yang memungkinkannya bergerak bebas untuk menemukan area kebocoran fluks, meskipun permukaan objek mungkin tidak beraturan. DC menginduksi medan magnet yang memiliki daya tembus lebih besar dan dapat digunakan untuk mendeteksi diskontinuitas dekat permukaan.
Pemeriksaan radiografi
Inspeksi radiografi adalah teknik yang didasarkan pada penggunaan radiasi elektromagnetik panjang gelombang pendek yang melewati material baja. Metode radiografi tradisional adalah proses pembuatan rekaman permanen pada film radiografi benda uji untuk mendeteksi cacat. Hal ini dilakukan dengan memaparkan objek uji ke sinar-x yang dihasilkan secara elektrik atau sinar gamma dari sumber radiasi. Radiasi dari sumber melewati objek dan direkam pada film radiografi. Film diproses dan film yang diproses (radiograf) dilihat oleh teknisi berkualifikasi yang mampu mendeteksi cacat dan anomali sesuai dengan kode dan standar yang berlaku.
Prinsip yang digunakan dalam teknik ini adalah bahwa benda baja dengan area dengan ketebalan yang dikurangi atau kepadatan material yang lebih rendah memungkinkan lebih banyak lewatnya radiasi, dan oleh karena itu menyerap lebih sedikit radiasi. Radiasi yang mencapai film setelah melewati material membentuk bayangan bayangan pada radiografi. Area dengan penyerapan rendah (slag, void, dan porositas) muncul sebagai area gelap pada radiografi sedangkan area dengan penyerapan tinggi (inklusi padat) muncul sebagai area terang pada radiografi.
Diskontinuitas bawah permukaan yang mudah dideteksi dengan metode ini adalah rongga, cacat, inklusi logam dan non-logam, dan retakan.
Kemajuan terbaru dalam pemeriksaan radiografi adalah radiografi digital, yang tidak memerlukan penggunaan film yang mahal dan peralatan yang sedang berkembang.
Pengujian ultrasonik
Pengujian ultrasonik (UT) adalah metode pemeriksaan yang menggunakan gelombang suara frekuensi tinggi (ultrasound) yang berada di atas jangkauan pendengaran manusia, untuk mengukur sifat geometris dan fisik pada material baja. Metode ini menggunakan gelombang suara yang dihasilkan secara elektrik untuk menembus objek baja untuk mendeteksi cacat. Refleksi sonik, refraksi dan penyerapan kemudian ditampilkan dan direkam pada layar CRT (tabung sinar katoda) untuk interpretasi. Proses ini membutuhkan lebih banyak keterampilan dan pengalaman untuk memberikan interpretasi yang akurat.
Salah satu manfaat utama UT adalah dianggap sebagai tes volumetrik yang sesungguhnya. Ini mampu menentukan tidak hanya panjang dan lokasi cacat, tetapi juga memberikan informasi kepada operator tentang jenis cacat yang ditemukan. Keuntungan utama UT adalah hanya membutuhkan akses ke satu sisi material yang diuji. Keuntungan penting lainnya adalah bahwa UT mendeteksi diskontinuitas planar kritis seperti retak dan fusi yang tidak sempurna. UT paling sensitif terhadap diskontinuitas yang terletak tegak lurus terhadap berkas suara. Karena berbagai sudut pancaran dapat digunakan, UT dapat mendeteksi laminasi, fusi yang tidak sempurna dan retakan yang diorientasikan sedemikian rupa sehingga deteksi dengan pengujian radiografi tidak mungkin dilakukan. UT memiliki kemampuan penetrasi yang dalam.
Kemajuan dalam peralatan UT termasuk array bertahap dan teknologi tiga dimensi (3D) telah sangat meningkatkan fleksibilitas dan kemampuan beradaptasi UT untuk semua jenis pekerjaan NDT.
Pengujian arus Eddy
Dalam pengujian arus eddy (ET), sebuah kumparan yang membawa arus AC ditempatkan dekat dengan permukaan spesimen, atau di sekitar spesimen. Arus dalam koil menghasilkan arus eddy yang bersirkulasi dalam spesimen yang dekat dengan permukaan dan ini pada gilirannya mempengaruhi arus dalam koil dengan induksi timbal balik. Cacat dan variasi material pada spesimen mempengaruhi kekuatan arus eddy. Oleh karena itu, keberadaan cacat diukur dengan perubahan listrik pada kumparan yang menarik. Perubahan tegangan dan fasa dapat diukur, tetapi beberapa instrumen yang lebih sederhana hanya mengukur perubahan tegangan.
Kuatnya arus eddy yang dihasilkan bergantung pada daya hantar listrik benda uji, permeabilitas magnetik benda uji, jarak stand-off antara benda uji dan kumparan, frekuensi AC yang digunakan pada kumparan eksitasi, dimensi kumparan dan benda uji, dan keberadaan. dari kekurangan. Sebagian besar keberhasilan pengujian ET bergantung pada pemisahan efek dari variabel-variabel ini. Sebagian besar instrumen arus pusaran memerlukan kalibrasi pada satu set spesimen uji dan sensitivitas cacat bisa sangat tinggi.
Teknik pengujian arus eddy digunakan untuk deteksi retak, pengukuran ketebalan material, pengukuran ketebalan lapisan dan pengukuran konduktivitas untuk identifikasi material, deteksi kerusakan panas, penentuan kedalaman case, keausan sadel, pitting, retak melintang, tonjolan beku, split, penyok, perlakuan panas pemantauan, penyortiran cepat komponen kecil baik untuk cacat, variasi ukuran, atau variasi material.
Arus Eddy merupakan alat yang berguna untuk mendeteksi kerusakan korosi dan kerusakan lain yang menyebabkan penipisan material pada dinding tubing seperti heat exchanger dan tube boiler. Metode arus eddy sangat baik untuk cacat permukaan dan dekat permukaan, sensitif terhadap retakan kecil dan cacat lainnya dan membutuhkan persiapan bagian yang sangat sedikit. Ini terbatas untuk digunakan pada bahan konduktif, dengan permukaan yang dapat diakses oleh probe.