Pembuatan Besi di Rotary Hearth Furnace
Pembuatan Besi di Rotary Hearth Furnace
Pembuatan besi di tungku perapian putar (RHF) adalah proses reduksi langsung yang memanfaatkan batubara non-coking untuk reduksi bijih besi. RHF adalah reaktor proses yang terdiri dari perapian datar dan tahan api yang berputar di dalam tanur terowongan melingkar yang stasioner. Di dalam RHF, terjadi reduksi langsung bijih besi atau bahan limbah yang mengandung besi, dengan menggunakan batu bara sebagai reduktor.
RHF bukanlah teknologi baru. Ini telah berhasil digunakan dalam berbagai aplikasi industri yang mencakup perlakuan panas, kalsinasi kokas minyak bumi, pengolahan limbah, dan pemulihan logam suhu tinggi non-ferro.
Sejarah pembuatan besi di RHF kembali ke pertengahan 1960-an dengan pengembangan proses 'Heat Fast' oleh Midrex. Sejak itu beberapa proses pembuatan besi berdasarkan RHF telah dikembangkan. Ini termasuk proses 'Fastmet'/proses 'Fastmelt', dan proses ITmk3 yang dibawa ke operasi komersial. Proses ini telah dijelaskan dalam artikel terpisah yang memiliki tautan http://www.ispatguru.com/fastmet-and-fastmelt-processes-of-ironmaking/, dan http://www.ispatguru.com/itmk-3-process- pembuatan-besi-nugget/. Proses RHF lainnya adalah proses 'Redsmelt', proses 'Inmetco', proses 'Iron Dynamics', proses 'DRyIron', proses 'Comet' dan 'SidComet' dan proses Hi-QIP.
Proses peleburan merah
Teknologi proses Redsmelt telah dikembangkan untuk memenuhi permintaan yang terus meningkat akan alternatif pembuatan besi ramah lingkungan berbiaya rendah untuk rute tanur sembur tradisional. Pabrik dengan proses ini dapat dirancang untuk kapasitas produksi 0,3 juta ton per tahun menjadi 1,0 juta ton logam panas per tahun. Proses ini dapat mengolah berbagai macam bijih besi halus dan bahan limbah dari pabrik baja.
Proses Redsmelt didasarkan pada RHF yang mengurangi pelet hijau yang terbuat dari bijih besi, denda reduktor, dan pengikat untuk menghasilkan besi tereduksi langsung (DRI) panas dan logam yang dibebankan ke tungku busur terendam (SAF). Proses ini beroperasi pada suhu tinggi dan tekanan atmosfer.
Umpan oksida besi ke tungku Redsmelt dalam bentuk pelet hijau yang terbuat dari bijih besi halus, reduktor dan pengikat. Pengikat harus memberi pelet hijau kekuatan mekanik yang cukup untuk mendukung penanganan guncangan di hilir. Pelet disaring pada layar tipe roller dengan ukuran antara 8 mm hingga 16 mm. Bahan di bawah dan di atas ukuran disirkulasi ulang untuk memberi makan disk pelet. Pelet kemudian didistribusikan ke RHF dalam lapisan hingga 30 kg/m2. Selama perjalanan melalui tungku dalam 12 menit hingga 18 menit, pelet dipanaskan hingga 1370 derajat C. Pengeringan pelet, devolatilisasi batubara dan reduksi oksida besi terjadi selama proses pemanasan. Kontak erat antara oksida besi dan karbon pada suhu yang sangat tinggi menghasilkan laju reaksi yang sangat cepat. Untuk mencegah reoksidasi besi metalisasi, zona akhir tungku dioperasikan dalam atmosfer sub-stoikiometri. Produk DRI panas kemudian diumpankan ke SAF untuk dilebur menjadi logam panas dan terak.
Lembar aliran proses ditunjukkan secara skematis pada Gambar 1.
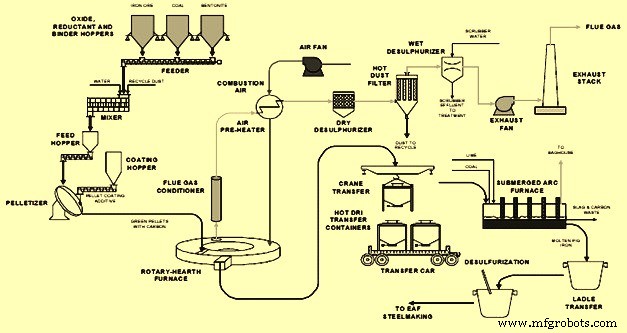
Gbr 1 Flow sheet proses Redsmelt
Proses Inmetco
Proses ini dikembangkan oleh International Nickel Corporation (INCO), Kanada pada tahun 1978. INCO mengembangkan proses ini dan menamakannya 'Inmetco' (Inco + met) karena dikembangkan untuk daur ulang limbah metalurgi. Proses tersebut juga dapat digunakan untuk mereduksi butiran halus bijih besi dan kombinasi butiran halus bijih besi dan bahan limbah metalurgi.
Proses Inmetco didasarkan pada RHF yang mereduksi briket yang terbuat dari butiran halus bijih besi, limbah material bantalan besi, dan batu bara bubuk untuk menghasilkan DRI logam panas yang dapat langsung diisikan ke dalam tungku induksi atau tungku busur listrik. Proses ini beroperasi pada suhu tinggi dan pada tekanan yang sedikit negatif.
Umpan besi ke tungku Inmetco dalam bentuk pelet disk yang terbuat dari bijih besi halus berukuran di bawah 250 mikro meter dan batubara halus atau kokas atau arang dengan bahan volatil kurang dari 25%. Mereka didistribusikan ke RHF di lapisan yang sekitar 3 pelet dalam melalui ban berjalan berputar. Proses ini menggunakan pengikat kerja cepat yang memungkinkan pelet diangkut ke perapian tanpa degradasi yang signifikan. Perapian berputar terus menerus dan pelet dipanaskan oleh pembakar yang terletak di sekitar pinggiran perapian hingga 1250 derajat C hingga 1300 derajat C selama periode 10 menit hingga 15 menit. Pembakar diatur dalam kelompok, dan membentuk zona pemanasan dan pengurangan. Zona pemanasan membuat sekitar sepertiga dari area perapian dan zona reduksi sekitar dua pertiga dari perapian. Pembakar terletak di lingkar dalam dan luar. Produk DRI panas dapat dikumpulkan dalam kaleng transfer bersih N2, atau langsung diumpankan ke tungku listrik untuk dilebur. RHF beroperasi di bawah sedikit tekanan negatif, dan disegel oleh bak segel air.
Lembar aliran proses ditunjukkan secara skematis pada Gambar 2.
Gambar 2 Flow sheet proses Inmetco
Proses Dinamika Besi
Proses pembuatan besi Iron Dynamics (IDI) didasarkan pada RHF yang mereduksi muatan oksida besi berkarbon menjadi padatan besi metalik yang dibebankan ke SAF untuk menyelesaikan reduksi dan untuk melelehkan serta mendesulfurisasi besi tereduksi. Mencairnya DRI juga memungkinkan pemisahan fase dari terak cair dan besi yang dihasilkan.
Proses IDI terdiri dari lima area proses yaitu (i) penerimaan bahan baku, (ii) penggilingan dan persiapan bijih dan reduktor (batubara), (iii) pelet, (iv) reduksi tungku putar, dan (v) peleburan SAF. Setelah bijih diterima, bijih dikeringkan sampai kadar airnya kurang dari 0,5% menggunakan off gas dari RHF. Bijih juga dimanfaatkan dengan menggunakan pemisah magnetik dan saringan untuk mengurangi jumlah material gangue. Kemudian digiling hingga 50% dikurangi ukuran 200 mesh. Batubara diangkut ke penghancur batu bara/fluks untuk ukuran hingga 80% dikurangi ukuran 200 mesh. Bijih tanah dan batu bara dicampur secara intensif dengan pengikat dan air dalam mixer dan dimasukkan ke dalam pelet disk. Pelet basah dikeringkan hingga kurang dari 1% kelembaban dan dipanaskan hingga 150 derajat C dalam pengering parut melingkar. Pengisi pelet menerima bola hijau kering dan melapisinya ke perapian tungku dalam lapisan setebal 25 mm hingga 40 mm. RHF berbahan bakar gas alam memiliki delapan zona reaksi. Suhu, aliran gas, dan komposisi gas dikontrol untuk menyediakan kondisi yang diperlukan di setiap zona untuk memanaskan, mengurangi, dan melindungi pelet dengan benar. DRI pada pelepasan tungku memiliki sekitar 85% metalisasi. Fasilitas aditif memasukkan fluks, kokas, silika, atau bahan lain ke sendok pengangkut DRI untuk mengontrol kimia terak di SAF. Sistem gas buang menghilangkan panas, debu, belerang dioksida, dan dinitrogen oksida dari gas buang. Sebuah afterburner melakukan pembakaran sisa CO (karbon monoksida) di saluran gas buang berpendingin air. Gas didinginkan dan NOx dikeluarkan di pendingin primer. Gas buang digunakan untuk memanaskan udara pembakaran dan memasok panas ke bijih, batu bara, dan pengering pelet. Setelah pengering pelet, gas disaring dan SOx (sulfur oksida) dihilangkan sebelum dibuang dari tumpukan. DRI dan aditif jatuh ke dalam lapisan terak SAF oleh gravitasi di mana peleburan berlangsung. Metalisasi rata-rata di sini adalah sekitar 95,8%. Terak disadap dari tungku ke dalam pot terak dan dipindahkan ke fasilitas pemrosesan terak.
Lembar aliran proses ditunjukkan secara skematis pada Gambar 3.
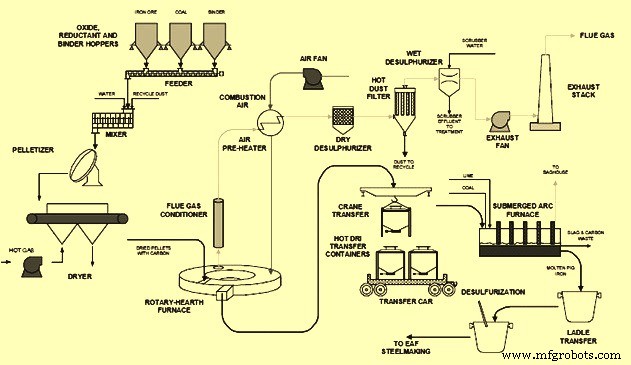
Gbr 3 Flow sheet proses Dinamika Besi
Proses DryIron
Proses DRyIron dikembangkan oleh Maumee Research and Engineering Inc. (MR&E). Proses ini didasarkan pada RHF yang mengurangi pelet hijau yang terbuat dari limbah bahan oksida besi dan bubuk batubara non-metalurgi untuk menghasilkan DRI logam panas (lebih besar dari 90%). Proses ini beroperasi pada suhu tinggi dan tekanan atmosfer, memiliki waktu tinggal yang singkat dan juga dapat digunakan untuk mendaur ulang limbah material bantalan besi.
Umpan oksida besi ke tungku DRyIron dalam bentuk pelet/briket hijau yang terbuat dari oksida besi halus dan batu bara atau kokas yang menghilangkan pra-pengeringan pelet. Di bawah kondisi teoritis suhu tinggi yang ideal (sekitar 1300 derajat C), oksida besi bereaksi dengan karbon tetap untuk membentuk besi logam dalam briket dengan pelepasan CO2. Rasio teoritis karbon tetap terhadap oksida besi adalah 1,5:1.
Proses DRyIron telah diformulasikan untuk menghasilkan besi metalik menggunakan rasio karbon-ke-oksida 6:1, yang menghasilkan evolusi CO dan CO2 dan meninggalkan tingkat karbon sisa sekitar 4%. Kunci dari proses ini adalah mengontrol rasio CO terhadap CO2 untuk meminimalkan reoksidasi, konsumsi karbon, dan waktu tinggal tungku. Selama perjalanan di seluruh tungku, pelet dipanaskan hingga 1300 derajat C. Pengeringan pelet, devolatilisasi batubara dan reduksi oksida besi terjadi selama proses pemanasan. Kontak erat antara oksida besi dan karbon pada suhu yang sangat tinggi menghasilkan laju reaksi yang sangat cepat. Produk DRI panas kemudian dapat dipasok ke toko peleburan baja dengan sejumlah opsi berbeda.
Lembar aliran proses ditunjukkan secara skematis pada Gambar 4.
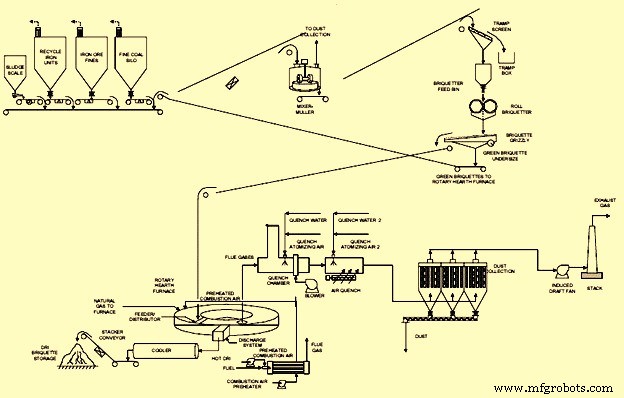
Gbr 4 Flow sheet proses DRyIron
Proses Komet dan SidComet
Proses Comet, yang dikembangkan oleh Centre de Recherches Metallurgiques (CRM), Belgia adalah sistem berbasis batubara yang menghasilkan besi spons dari bijih halus dan batu kapur dalam tungku perapian putar. Proses reduksi langsung komet menghasilkan gangue rendah dan DRI sulfur rendah dari bijih besi dan fine batubara. Serangkaian uji laboratorium yang diperpanjang telah menunjukkan kelayakan dan fleksibilitas proses, yang terutama dapat dioperasikan dengan segala jenis batubara, atau reduktor padat lainnya (termasuk angin lignit dan kokas) dan yang juga sangat cocok untuk mendaur ulang bantalan besi limbah metalurgi untuk diganti (atau dicampur dengan) bijih besi. Sebuah laboratorium, instalasi 100 kg/jam mulai beroperasi pada November 1996. Berdasarkan hasil yang berhasil diperoleh, pabrik percontohan 1,5 ton/jam telah dibangun di Sidmar, Ghent, Belgia. Hasil metalisasi mengkonfirmasi yang diperoleh dari unit laboratorium. Produktivitas, biaya, harga, konsumsi energi, dan dampak lingkungan telah ditetapkan.
Dalam proses Comet, butiran bijih besi dan batu bara tidak tercampur dan menjadi pelet tidak seperti proses lain yang disebutkan sebelumnya. Sebaliknya, mereka dibebankan dalam bentuk lapisan alternatif di perapian. Batu kapur biasanya ditambahkan untuk mengontrol kandungan sulfur dalam batubara. Suhu di zona reduksi adalah sekitar 1300 derajat C. Gas alam, gas oven kokas, dan batu bara bubuk, dll., dibakar untuk menghasilkan panas. Pasca-pembakaran volatil dan CO yang dilepaskan selama reaksi juga memberikan sejumlah panas. Lapisan DRI mengalami sintering karena suhu tinggi. Namun, kelebihan arang tetap berbentuk tepung dan karena itu dapat dengan mudah dipisahkan menggunakan saringan. Gas buang mengalami pasca pembakaran lebih lanjut di luar tungku dan panas digunakan untuk memanaskan udara proses dan bahan pengisi. Karena beban yang lebih tinggi pada tungku dalam proses ini, waktu pemrosesan dalam proses ini biasanya jauh lebih besar daripada rekan-rekannya yang menggunakan pelet komposit.
Lembar aliran proses ditunjukkan secara skematis pada Gambar 5.
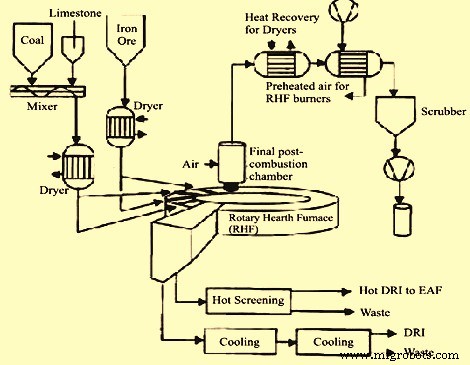
Gbr 5 Lembar Alur Proses Komet
Proses SidComet mirip dengan proses Comet. Satu-satunya perbedaan adalah bahwa bijih besi dan batu bara halus diumpankan sebagai campuran dalam kasus ini. Waktu tinggal mirip dengan proses Komet. Karena waktu tinggal yang lebih tinggi, produktivitas proses ini biasanya tetap lebih rendah daripada proses berbasis pelet.
Proses Hi-QIP
Berdasarkan konsep yaitu (i) proses tidak memerlukan gas alam atau batu bara kokas sebagai reduktor, (ii) produk besi dari proses bebas dari komponen gangue, (iii) peralatan sesederhana mungkin, dan (iv) sistem pemulihan energi minimal, dan hasil eksperimen, proses pembuatan besi baru yang disebut proses Hi-QIP (Kerikil Besi Berkualitas Tinggi) dikembangkan. Proses tersebut merupakan proses baru berbasis batubara untuk menghasilkan besi berkualitas tinggi. Prosesnya mirip dengan proses ITmk3 karena memungkinkan peleburan besi tereduksi di tungku perapian putar. Proses ini memungkinkan fluktuasi pencampuran bahan baku. Pengembangan saat ini telah mencapai tahap pilot plant.
Proses Hi-QIP memiliki dua fitur khusus dibandingkan dengan proses serupa. Ini adalah (i) penggunaan lapisan bahan karbon pada tungku putar, dan (ii) peleburan besi tereduksi dalam tungku. Reaktor utama dalam proses Hi-QIP adalah tungku perapian putar. Bijih besi berbutir kasar atau halus, batu bara dan batu kapur digunakan sebagai bahan baku. Penggunaan bahan yang kental tidak dipertimbangkan untuk proses tersebut. Bahan berkarbon, seperti batu bara, diletakkan di perapian, dan lubang kecil berbentuk cangkir dibentuk di lapisan ini oleh roller. Bijih besi digunakan sebagai sumber besi, batubara sebagai agen pereduksi, dan batu kapur sebagai agen fluks. Bahan-bahan ini dicampur dan diisi ke lapisan bahan berkarbon, dan kemudian dipanaskan dengan pembakar. Dalam proses ini, bijih besi direduksi dan dilebur, dan batu bara yang tercampur dalam lapisan bahan baku digasifikasi dan bertindak sebagai zat pereduksi. Batugamping meleleh dan membentuk terak dengan komponen gangue dan abu dalam campuran. Besi cair dan terak cair mengalir ke lubang, di mana mereka dipadatkan oleh chiller, membentuk kerikil. Kerikil besi dan kerikil terak dikeluarkan dari tungku dengan perangkat sekrup.
Fitur umum utama pembuatan besi di RHF
Aliran proses umum selama pembuatan besi oleh RHF diberikan pada Gambar 6.
Gbr 6 Alur proses umum selama pembuatan besi di RHF
Pengurangan aglomerat bijih besi/batubara dalam RHF adalah proses pembuatan besi yang bebas kokas dan ramah lingkungan. Namun, produktivitas dan efisiensi energi dari proses ini rendah karena ketinggian lapisan yang dangkal, suhu reaksi yang rendah, dan aditif karbon yang tidak mencukupi dalam pelet. Kinetika reduksi oksida besi dalam aglomerat bijih besi/batubara sangat sensitif terhadap suhu karena melibatkan reaksi endotermik yang kuat. Di sisi lain, suhu yang lebih tinggi mendorong reoksidasi DRI yang baru diproduksi oleh CO2 dan/atau O2. Dalam praktik RHF saat ini, kedalaman lapisan aglomerat adalah dangkal, tingginya hanya 2-3 pelet, dan reduktor padatnya rendah bahan volatil. Oleh karena itu, aliran gas yang dapat melindungi pellet dari reoksidasi menjadi lemah dan tidak stabil. Praktik mempertahankan rasio CO/CO2 lebih besar dari 2 menghasilkan efisiensi bahan bakar yang sangat buruk sementara suhu proses yang rendah membatasi produktivitas proses.
Keberhasilan penggunaan teknologi RHF untuk reduksi langsung bahan bantalan besi tergantung pada cara teknologi proses diterapkan melalui rekayasa proses yang tepat. Jika RHF diintegrasikan dengan benar ke dalam proses global dan teknologi reduksi langsung diterapkan dengan benar, hasilnya adalah sistem ekonomi yang hemat energi, ramah lingkungan, untuk memproduksi besi alternatif yang berkualitas.
Konsep reduksi langsung berbasis batubara yang memanfaatkan RHF adalah konsep yang sederhana. Namun, implementasi komersial dari konsep tersebut tidak mudah dicapai.
Konsep proses pembuatan besi di RHF dan perbandingan pengisian lapisan tunggal dengan pengisian multi-lapisan ditunjukkan pada Gambar 7.
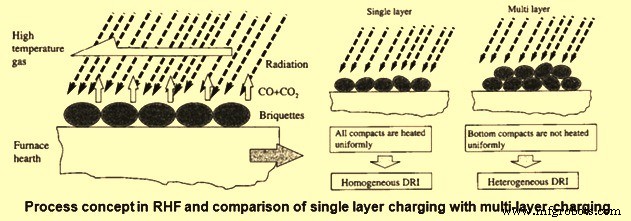
Gbr 7 Konsep proses dalam RHF dan perbandingan pengisian satu lapisan dengan pengisian multi-lapisan
Reaksi berikut terjadi selama pembuatan besi di RHF.
FexOy + y C =x Fe + y CO
FexOy + y CO =x Fe + y CO2
C + O2 =CO2
C + CO2 =2 CO
Ada tiga sampai empat zona utama di dalam RHF yaitu (i) zona pemanasan awal (b) zona reduksi utama (c) zona reduksi akhir dan (d) zona pendinginan. Atmosfer tungku dikendalikan untuk memenuhi persyaratan termal dan metalurgi dari proses dengan kontrol yang tepat dari rasio bahan bakar dan oksigen. Potensi oksigen yang lebih tinggi diperlukan di zona pemanasan awal untuk mengekstraksi energi kimia maksimum yang tersimpan dalam bahan bakar yang dibakar di zona ini. Penghapusan kelembaban yang terperangkap dan hal-hal yang mudah menguap juga terjadi di zona ini. Kedua zona reduksi memiliki potensi oksigen yang jauh lebih rendah yang mencegah oksidasi ulang pelet tereduksi. Di zona reduksi, oksida besi dan beberapa oksida logam pengotor lainnya direduksi menjadi bentuk logamnya. Di zona pendinginan, DRI didinginkan di bawah 300 derajat C sebelum digunakan.
Selain bahan bakar yang terbakar, ada sumber panas lain di dalam RHF. Pasca pembakaran gas CO yang dihasilkan selama reduksi membantu mengurangi kebutuhan energi proses. Kadang-kadang, udara sekunder juga disuntikkan untuk memfasilitasi pasca pembakaran gas buang. Pembakaran zat yang mudah menguap juga melepaskan beberapa panas. Sejumlah kecil panas juga dihasilkan selama pembakaran karbon yang ada dalam pelet/briket.
Batubara non kokas dan terkadang bahan berkarbon rendah termasuk limbah plastik dapat digunakan di RHF sebagai reduktor. Pemanfaatan reduktor karbon tingkat rendah ini memungkinkan proses RHF untuk menghasilkan besi metalik dengan mereduksi oksida besi. Namun, persentase kandungan bahan volatil dalam reduktor karbon sangat penting untuk digunakan dalam RHF. Evolusi gas yang cepat meningkatkan tekanan internal yang dapat mengakibatkan pemecahan pelet/briket. Ini dapat dihindari untuk menjaga persentase gumpalan yang tinggi dalam DRI produk.
Kecepatan rotasi perapian harus dikontrol secara eksternal. Kecepatan tergantung pada reaktivitas bahan baku. Praktik normalnya adalah memastikan waktu tinggal yang cukup lama bagi pelet / briket untuk mencapai tingkat metalisasi yang tinggi.
RHF biasanya dioperasikan pada tekanan negatif kecil untuk menghindari kebocoran gas tungku ke lingkungan eksternal dan disegel menggunakan bak segel air.
Secara umum menguntungkan untuk memanfaatkan panas sensibel dari DRI panas dengan pengisian panas ke dalam peleburan. Jika peleburan tertunda, praktik yang biasa dilakukan adalah mengubah DRI menjadi besi briket panas (HBI) untuk meminimalkan tingkat oksidasi ulang dengan mengurangi luas permukaan yang tersedia.
Perpindahan panas ke lapisan bawah adalah salah satu kelemahan serius dari RHF, terutama ketika lapisan pelet multilayer digunakan sebagai pengganti lapisan tunggal untuk meningkatkan produktivitas. Penyusutan komposit pellet/briket diharapkan dapat mempermudah perpindahan panas dari lapisan atas ke lapisan bawah. Penyusutan pelet/briket terjadi karena efek gabungan dari reaksi kimia dan sintering oksida besi. Ini meningkatkan kinetika reaksi lapisan bawah. Itu tergantung pada suhu dan waktu. Beberapa penelitian tentang fenomena penyusutan mengungkapkan bahwa pellet/briket komposit arang kayu memiliki perilaku penyusutan yang lebih baik dibandingkan dengan arang batubara bituminus dan pellet/briket komposit grafit.
Gas buang dari RHF biasanya mengalami pasca pembakaran lengkap dengan memanfaatkan udara tambahan. Energi yang diperoleh dari ini digunakan yaitu (i) untuk memanaskan awal udara pembakaran, (ii) mengeringkan bahan umpan, atau (iii) menghasilkan uap di boiler pemulihan panas limbah.
Debu dari gas buang dikumpulkan di bag filter. Debu ini mengandung persentase tinggi logam yang mudah menguap seperti seng dan kadmium terutama karena daur ulang bahan limbah.