Proses Peleburan Bijih Besi Langsung untuk Pembuatan Besi
Proses Peleburan Bijih Besi Langsung untuk Pembuatan Besi
Proses peleburan bijih besi langsung (DIOS) adalah proses reduksi peleburan untuk produksi logam panas (besi cair). Ini adalah proses dua tahap yang telah dikembangkan di Jepang. Ini menggunakan batubara non-coking dalam bentuk bubuk atau butiran untuk melebur bijih besi halus menjadi besi cair (logam panas) dan karenanya, tidak diperlukan pabrik oven kokas dan pabrik sintering. Denda bijih direduksi sebelumnya dalam tungku unggun terfluidisasi dan diisikan dalam tungku reduksi peleburan bersama dengan batubara dan fluks non-coking. Oksigen ditiupkan ke tungku reduksi peleburan.
Dua tahap proses DIOS terdiri dari (i) pra reduksi bijih besi di tungku reduksi awal (PRF), dan (ii) reduksi akhir dan peleburan di tungku reduksi peleburan (SRF). Pra reduksi bijih dilakukan dalam dua langkah dengan memanfaatkan gas buang dari SRF. Setiap langkah menggunakan reaktor fluidized bed yang dirancang sebagai tungku vertikal.
Pengembangan proses DIOS dimulai pada tahun 1988 di Jepang sebagai proyek penelitian bersama di antara delapan perusahaan manufaktur besi yang, sebelum tahun 1988, telah mempelajari proses peleburan-reduksi secara individual. Proyek ini disponsori oleh MITI, Kementerian Perdagangan dan Industri Internasional Jepang. Perusahaan Jepang dan Japan Iron and Steel Federation (JISF) secara aktif mendukung pengembangan proses selama periode 1988 hingga 1996.
Studi teknologi inti yang diperlukan untuk pembangunan pabrik percontohan dilakukan selama periode 1988 hingga 1990. Selama periode ini teknologi inti didirikan. Teknologi inti ini mencakup (i) peningkatan efisiensi termal SRF, (ii) teknologi yang akan diintegrasikan dengan PRF, (iii) teknologi untuk pembuangan terak cair, dan (iv) peningkatan skala SRF. Pabrik percontohan dengan kapasitas 500 ton per hari berdasarkan konsep proses dibangun dan ditugaskan selama tahun 1993 di Keihin works of NKK Corporation (sekarang bagian dari holding JFE). Untuk uji pabrik percontohan, SRF yang digunakan adalah tungku oksigen dasar 250 ton yang dimodifikasi.
Uji coba pabrik dilakukan selama periode 1993 hingga 1995. Kemungkinan penggunaan langsung debu bijih besi, bijih granular, dan batu bara dikonfirmasi selama uji pabrik percontohan. Namun, selama dua tahun ujian, banyak pengalaman berharga yang didapat, sebagian besar positif dan ada juga yang negatif. Pengalaman negatif yang disaksikan selama uji coba pabrik adalah sebagai berikut.
- Ada tingkat pra-reduksi yang rendah, biasanya di bawah 30%. Ini membawa tekanan berat pada SRF.
- Pergerakan bijih besi di fluidized bed tidak mulus dan masalah lengket diamati di fluidized bed PRF.
Selama uji coba pabrik, spesifikasi peralatan yang diperlukan ditentukan. Dengan berbagai bahan baku, peralatan dan spesifikasi operasi untuk mencapai efisiensi termal yang tinggi, sebagai alternatif dari tanur sembur, telah ditentukan. Selain itu, teknologi untuk pendinginan air pada badan tungku telah ditetapkan. Sebuah desain konseptual dan evaluasi ekonomi (studi kelayakan) untuk fasilitas komersial dilakukan. Kondisi fasilitas dan operasi untuk membuktikan keunggulan dibandingkan tanur sembur, seperti yang ditunjukkan dalam hasil penelitian, diperjelas.
Berdasarkan data pilot plane, studi kelayakan telah dilakukan di Jepang dengan parameter kinerja untuk pabrik komersial 6000 ton per hari (kapasitas tahunan 2 juta ton). Flow sheet untuk pabrik ini adalah pada Gambar 1. Jika dibandingkan dengan produksi logam panas 2 juta ton melalui proses tanur sembur, diketahui bahwa (i) biaya investasi berkurang sebesar 35%, (ii) biaya produksi logam panas berkurang sebesar 19 %, (iii) konsumsi batubara berkisar antara 730 kg/tHM hingga 750 kg/tHM (ton logam panas) yang setara dengan proses blast furnace, (iv) konsumsi energi bersih berkurang 3 % hingga 4%, dan (v) emisi CO2 dalam proses pembuatan besi berkurang sebesar 4% hingga 5%.
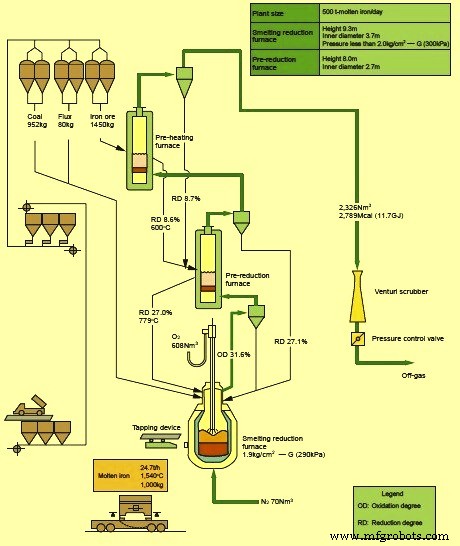
Gbr 1 Lembar aliran pembangkit DIOS 6000 ton per hari
Deskripsi proses
Proses DIOS memiliki karakteristik (i) bijih besi dan batu bara halus dapat langsung digunakan, (ii) tidak memerlukan kokas sehingga tidak ada pembatasan jenis batu bara yang digunakan dalam proses, (iii) proses dapat dihentikan dan dihidupkan kembali dengan mudah sehingga fleksibilitas yang baik dan (iv) intensitas pengadukan bak dapat dioptimalkan untuk tingkat pasca-pembakaran yang lebih tinggi dan untuk efisiensi perpindahan panas yang lebih baik.
Denda bijih besi (ukuran 0-8 mm) tanpa sintering dipanaskan terlebih dahulu hingga sekitar 500 derajat C pada langkah pertama pra-reduksi dan dikurangi sekitar 5% pada reaktor pertama dari dua reaktor fluidized bed yang beroperasi secara seri dan selanjutnya direduksi. menjadi sekitar 15% sampai 25% di reaktor kedua. Untuk pra-reduksi ini, digunakan gas buang yang sudah dibersihkan dari SRF. Suhu bijih besi mencapai sekitar 800 derajat C selama langkah kedua pra-reduksi. Bijih yang telah direduksi dipindahkan ke SRF untuk reduksi dan peleburan akhir.
Sebagian besar batubara non-coking (ukuran kurang dari 25 mm) yang dibutuhkan untuk proses tersebut dibebankan oleh gravitasi di SRF. Oksigen disuntikkan ke dalam SRF dari atas untuk pembakaran batubara primer serta untuk pasca-pembakaran. Tombak oksigen dirancang untuk memberikan oksigen kecepatan tinggi untuk oksidasi karbon (pukulan keras) dan oksigen kecepatan rendah untuk pasca-pembakaran di freeboard (pukulan lunak) secara bersamaan. Karbon monoksida (CO) yang dihasilkan digunakan untuk pra-reduksi bijih besi di PRF. Suhu di SRF adalah sekitar 1500 derajat C. Nitrogen ditiupkan ke bagian bawah SRF untuk pengadukan rendaman.
Pengurangan oksida besi cair di SRF dipromosikan oleh batubara berkarbonisasi yaitu arang, dan mengandung karbon dalam besi. Tiga lapisan material ada di dalam SRF. Lapisan-lapisan tersebut adalah (i) lapisan atas yang terdiri dari campuran batubara dan bijih tereduksi sebagian, (ii) lapisan tengah yang terdiri dari terak cair yang mengandung arang batubara dan bijih cair, dan (iii) lapisan bawah terdiri dari logam panas. Debu yang dihilangkan dari gas buang SRF dan butiran halus yang dikeluarkan dari gas yang meninggalkan reaktor fluidized bed (keduanya PRF) disuntikkan kembali ke SRF. Selain itu, sejumlah kecil batu bara halus, dari urutan 50 kg per ton produksi logam panas, disuntikkan ke dalam gas buang SRF untuk mendinginkan gas buang. Karbon batubara ini bereaksi dengan CO2 dari gas buang untuk menghasilkan CO sedangkan disosiasi bahan volatil batubara menghasilkan CO dan H2. Jumlah tambahan CO dan H2 ini membantu dalam pra-reduksi bijih di PRF.
Tujuan dari proses ini adalah untuk mencapai pasca-pembakaran sekitar 40%, dan pra-reduksi sekitar 20% hingga 30%. Dengan kondisi tersebut konsumsi batubara diperkirakan sekitar 700 kg/tHM hingga 800 kg/tHM tergantung pada jenis batubara non-coking. Biasanya konsumsi batubara lebih tinggi dengan batubara yang memiliki bahan mudah menguap yang tinggi.
Proses DIOS beroperasi pada tekanan 1 kg/sq cm sampai 2 kg/sq cm dan menggunakan top feed batubara dan bijih. Ini menggunakan tombak atas untuk injeksi oksigen dan memiliki sistem fluidized bed untuk pra-reduksi bijih besi. Dalam SRF, sebagian besar reduksi terjadi pada lapisan terak berbusa. Nilai kalor gas ekspor sekitar 1000 -1100 kkal/N cum. Gas ini dapat digunakan untuk pembangkit listrik.
Agar proses DIOS berhasil, ada enam elemen dasar dari proses yang harus dikontrol. Juga, ada kebutuhan untuk mengontrol interaksi antara enam elemen ini. Enam elemen dasar dari proses DIOS diberikan di bawah ini.
- Tingkat pra-pengurangan – Semakin tinggi tingkat pra-pengurangan, semakin rendah beban pada SRF.
- Rasio pasca-pembakaran – Rasio pasca-pembakaran menentukan tingkat pasca-pembakaran gas yang berkembang di SRF. Ini digunakan untuk evaluasi potensi pembangkitan panas SRF, dan juga berarti potensi pengurangan gas buang pada tahap pra-reduksi. Secara praktis ditentukan oleh analisis gas buang. Jika rasio pasca pembakaran tinggi, maka gas buang yang keluar dari SRF memiliki lebih banyak CO2 dan H2O, sehingga menurunkan potensinya sebagai gas pereduksi. Diamati bahwa dengan sekitar 50% pasca-pembakaran dan tingkat pra-reduksi 25% hingga 30%, efisiensi SRF yang baik dapat dicapai. Nilai pasca pembakaran yang tinggi menyebabkan pemanfaatan bahan bakar dengan nilai CO dan H2 lebih banyak di dalam reaktor peleburan itu sendiri. Oleh karena itu, ini menurunkan konsumsi batu bara.
- Kinetika reaksi – Karena hembusan oksigen di SRF, waktu untuk menyelesaikan proses agak singkat dan kinetika reaksi penting. Laju produksi dalam SRF bergantung pada kinetika reaksi.
- Efisiensi perpindahan panas atau efisiensi energi – Efisiensi perpindahan panas didefinisikan sebagai rasio panas yang digunakan secara efektif untuk peleburan dengan total panas yang dihasilkan di SRF. Untuk efisiensi bahan bakar yang lebih baik, panas yang dihasilkan pasca-pembakaran perlu ditransfer secara efektif ke terak dan logam panas untuk mempertahankan reaksi endotermik yang terjadi di sana dan juga untuk melawan kehilangan panas.
- Biaya produksi – Agar proses menjadi kompetitif, biaya produksi harus dikendalikan agar lebih rendah dari biaya produksi logam panas yang dihasilkan oleh proses blast furnace.
- Aspek lingkungan – Emisi dari proses harus dikontrol sehingga menawarkan keunggulan dibandingkan rute tanur sembur.
Parameter proses dan konsumsi spesifik
Nilai khas untuk parameter proses dan konsumsi spesifik diberikan di Tab 1.
Tab 1 Nilai umum untuk parameter proses dan konsumsi spesifik |
No. Sl. | Parameter | Satuan | Nilai |
1 | Analisis tipikal batubara non-coking | | |
| Materi yang mudah menguap | % | <40 |
| Karbon tetap | % | 60-88 |
| Kelembaban | % | 4-6 |
| Abu | % | 8-12 |
| Belerang | % | <0.6 |
| Ukuran partikel | % | <30 |
2 | Pra-reduksi bijih | % | 20-30 |
3 | Konsumsi oksigen | N cum/tHM | Sekitar 500 |
4 | Konsumsi batubara | kg/tHM | 700-800 |
5 | Konsumsi listrik | kWh/tHM | Sekitar 75 |
6 | Konsumsi uap bertekanan rendah | kg/tHM | Sekitar 80 |
7 | Gas buang | | |
| Kuantitas | N cum/tHM | Sekitar 1800 |
| Nilai kalori | kkal/N cum | 1000-1100 |
8 | Keluaran energi | J kal/tHM | Sekitar tahun 1850 |
9 | Pembangkitan uap bertekanan rendah | kg/tHM | Sekitar 700 |
10 | Pembangkitan listrik | kWh/tHM | Sekitar 30 |
11 | Komposisi Khas gas buang | | |
| H2 | % | 15 |
| CO | % | 30 |
| CO2 | % | 20 |
| N2 | % | 15 |
| H2O | % | 20 |
Kualitas tipikal logam panas yang dihasilkan oleh proses DIOS terdiri dari C- sekitar 3,5%, Si – kurang dari 0,05%, S – kurang dari 0,05%, dan P – 0,10 %. Logam panas dan terak diketuk melalui lubang keran.
Perbandingan proses DIOS dan proses BF sehubungan dengan keseimbangan energi dan emisi CO2 ditunjukkan pada Gambar 2.
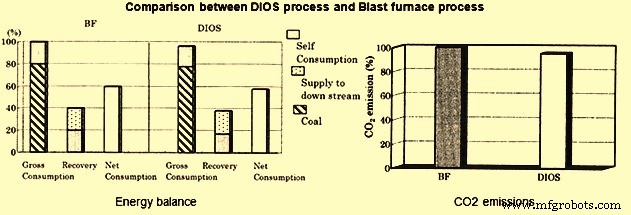
Gbr 2 Perbandingan antara proses DIOS dan proses BF
Keuntungan dan keterbatasan proses
DIOS memiliki keuntungan sebagai berikut.
- Ini menggunakan bahan baku dan bahan bakar yang murah (batubara non-coking, debu internal, dll.).
- Proses menghilangkan kebutuhan pabrik sintering dan pabrik oven kokas.
- Biaya operasi rendah.
- Konsumsi langsung daya listrik rendah.
- Ini memiliki konsumsi energi bersih yang lebih rendah.
- Ini fleksibel sehubungan dengan penggunaan bahan baku dan variasi dalam tingkat produksi serta sehubungan dengan penghentian dan permulaan pabrik.
- Ringkas dan hanya membutuhkan sedikit investasi tambahan.
- Biaya investasi diperkirakan sekitar 65% dari produksi logam panas setara dengan proses tanur tinggi.
- Ini stabil dan menghasilkan pasokan logam panas berkualitas tinggi.
- Ini berkontribusi pada penggunaan energi batubara yang efektif.
- Co-produksi energi (pembangkitan bersama) dengan mudah dapat dilakukan.
- Memiliki beban lingkungan yang rendah (SOx, NOx, CO2 rendah, pembentukan debu, tidak ada kebocoran gas oven kokas).
Proses DIOS memiliki batasan sebagai berikut.
- Suhu penyadapan tinggi. Suhunya berkisar antara 1750 derajat C hingga 1800 derajat C.
- Keausan refraktori tinggi karena suhu tinggi. Karena itu, ada konsumsi refraktori yang tinggi dan waktu henti proses yang tinggi yang diperlukan untuk pelapisan ulang.
- Karena penggunaan tiga reaktor (2 angka PRF dan satu angka SRF) dalam prosesnya, kontrol prosesnya sedikit rumit.
- Karena tingkat pra reduksi rendah (kurang dari 30%) maka beban pada SRF tinggi, sehingga pengoperasian SRF sangat penting untuk keberhasilan proses.
- Pengalaman dalam mengoperasikan pabrik scale-up kurang karena tidak adanya investasi di pabrik scale-up.