Pengembangan Proses Pengurangan Peleburan untuk Pembuatan Besi
Pengembangan Proses Reduksi Peleburan untuk Pembuatan Besi
Proses peleburan reduksi (SR) merupakan perkembangan terbaru dalam teknologi produksi logam panas (besi cair). Proses ini menggabungkan gasifikasi batubara non-coking dengan reduksi lelehan bijih besi. Intensitas energi proses SR lebih rendah dibandingkan dengan blast furnace (BF), karena produksi kokas tidak diperlukan dan kebutuhan untuk preparasi bijih besi juga berkurang.
Proses pembuatan besi SR dikandung pada akhir 1930-an. Sejarah perkembangan proses SR kembali ke tahun 1950-an. Studi fundamental skala laboratorium tentang SR bijih besi dimulai pertama kali oleh Dancy pada tahun 1951. Namun, upaya serius dimulai dari tahun 1980 dan seterusnya.
Ada dua jalur perkembangan yang terpisah dari teknologi pembuatan besi utama selama paruh kedua abad kedua puluh.
Lini pengembangan pertama dipusatkan pada BF yang tetap menjadi unit proses utama untuk produksi logam panas. Secara umum, garis pengembangan ini tidak mencakup perubahan proses radikal dalam tungku itu sendiri. Ini berlangsung melalui evolusi bertahap yang melibatkan (i) peningkatan ukuran tungku, (ii) peningkatan persiapan beban, (iii) peningkatan tekanan atas, (iv) peningkatan suhu ledakan panas, (v) tanpa lonceng pengisian dan perbaikan distribusi beban, (vi) perbaikan refraktori dan sistem pendingin, (vii) injeksi bahan bakar tambahan (bahan bakar gas, bahan bakar cair, atau batu bara bubuk) dan pengayaan semburan udara panas dengan oksigen (O2), dan (viii ) penerapan otomatisasi serta penyempurnaan teknologi instrumentasi dan kontrol. Keberhasilan pembuatan besi yang berkelanjutan di BF mencerminkan tingkat efisiensi termal dan kimia yang sangat tinggi yang dapat dicapai selama produksi logam panas dan keuntungan biaya yang diakibatkannya. Bahkan, dalam kasus BF besar, ini dilengkapi dengan skala ekonomi.
Teknologi produksi logam panas di BFs, bagaimanapun, sekarang telah berkembang ke tahap di mana produksi yang efisien secara teknis dan ekonomis berlangsung pada skala besar operasi biasanya dari urutan 2 juta ton (Mt) per tahun sampai 3 Mt per tahun. Juga, pembuatan besi di BF membutuhkan infrastruktur dan unit produksi terkait yang cukup besar yang mencakup pembuatan kokas dan fasilitas untuk sintering halus bijih besi. Hal ini menghasilkan intensitas modal yang tinggi dari kompleks BF modern yang tidak hanya membutuhkan periode waktu yang sangat lama untuk konstruksinya tetapi juga perlu dioperasikan hingga mendekati tingkat kapasitas agar layak secara ekonomi.
Pengembangan lini kedua yang paralel dengan pengembangan di BF terdiri dari upaya yang cukup besar yang dilakukan menuju pengembangan rute manufaktur yang lebih kecil dan lebih fleksibel dengan biaya investasi yang lebih rendah. Hal ini menyebabkan pengembangan teknologi pembuatan besi alternatif utama yang muncul selama akhir 1960-an dan awal 1970-an. Ini adalah teknologi reduksi langsung (DR) di mana stok umpan oksida besi direduksi menjadi besi metalik dengan mereduksi gas pada suhu di bawah titik leleh besi. Produk dari proses DR, besi tereduksi langsung (DRI), secara fisik mirip dengan bahan baku dalam bentuk (biasanya bijih besi bongkahan dan/atau pelet) dan mengandung mineral gangue yang ada dalam bijih asli. DRI juga dikenal sebagai besi spons. Sangat cocok untuk digunakan sebagai pengganti skrap selama operasi pembuatan baja dan memiliki keunggulan kualitas dibandingkan skrap, terutama dalam kandungan residunya yang rendah dan kemudahan penanganan dan pengumpanannya.
Proses DR mampu beroperasi secara ekonomis pada tingkat output yang jauh lebih rendah daripada BF, biasanya kurang dari 0,6 Mt per tahun. Mereka membutuhkan sedikit infrastruktur pendukung, dan jauh lebih sedikit padat modal daripada BF. Beberapa dari proses DR ini menggunakan gas alam sebagai bahan baku untuk produksi gas pereduksi. Ketersediaan gas alam tidak tersebar luas di seluruh dunia. Proses DR berbasis batubara pada prinsipnya adalah proses berbasis rotary kiln dan hanya populer di beberapa negara karena berbagai alasan teknis dan ekonomi.
Proses DR juga menderita fakta bahwa mereka menghasilkan produk antara yang bersaing langsung dengan skrap karena membutuhkan peleburan dan pemurnian sangat sering dalam tungku induksi atau tungku busur listrik. Mahalnya biaya listrik membuat pencairan listrik kurang diminati. Juga di lingkungan yang tertekan, penurunan harga barang bekas menyebabkan penurunan harga DRI. Hal ini mengakibatkan popularitas proses DR yang lebih rendah di sebagian besar negara di seluruh dunia.
Popularitas yang lebih rendah dari proses DR memberikan insentif terhadap pengembangan rute proses pembuatan besi SR. Hasilnya adalah konsentrasi upaya pengembangan pada proses yang dapat bersaing dengan proses BF tetapi kurang rentan terhadap masalah yang dihadapinya.
Tujuan pengembangan proses pembuatan besi SR
Tujuan pengembangan proses pembuatan besi SR adalah sebagai berikut.
- Pengurangan biaya – Karena BF adalah proses yang efisien secara termal dan kimia, hanya ada sedikit ruang untuk proses pesaing untuk mengurangi biaya yang dikeluarkan untuk bahan baku dan energi. Tetapi ada peluang yang tersedia untuk mengurangi biaya tinggi yang terkait dengan pembuatan besi BF dengan menghindari pabrik dan peralatan terkait serta unit produksi yang padat modal. Jadi tujuan yang jelas untuk proses pembuatan besi SR adalah penggunaan batubara non-kokas secara langsung sebagai bahan bakar proses dan reduktor untuk menghindari kebutuhan akan unit pembuatan kokas. Kemampuan untuk menggunakan butiran bijih besi juga merupakan tujuan lain yang menawarkan kesempatan untuk memotong biaya unit aglomerasi seperti pabrik sintering/pelet. Penggunaan O2 curah, yang telah tersedia secara luas, menawarkan metode untuk mencapai suhu proses yang tinggi tanpa memerlukan kompor sembur panas, dan karena O2 biasanya tersedia pada tekanan tinggi, maka tidak diperlukan blower udara yang besar.
- Operasi skala kecil – Tujuan kedua dari pengembangan proses pembuatan besi SR adalah memiliki ukuran proses yang ekonomis. Jika ketergantungan proses pembuatan besi SR pada unit terkait dapat dihindari, maka biaya investasi keseluruhan dapat dikurangi sehingga memungkinkan untuk mengoperasikan proses tersebut secara ekonomis pada kapasitas yang jauh lebih kecil (katakanlah sekitar 0,5 Mt per tahun). Proses SR berkapasitas kecil juga dapat memberikan peluang untuk pabrik yang tidak terlalu kompleks yang membutuhkan waktu konstruksi yang jauh lebih singkat untuk commissioningnya dan yang jauh lebih sederhana untuk dioperasikan. Juga teknologi pembuatan besi SR semacam itu dapat menjadi menarik di negara-negara di mana terdapat kesulitan dalam mengatur keuangan skala besar dan di mana ada masalah sehubungan dengan ketersediaan batubara metalurgi.
- Peningkatan fleksibilitas – Proses pembuatan besi SR dengan biaya modal rendah dan dengan penggunaan batubara non-coking dapat memiliki fleksibilitas yang lebih tinggi selama operasi. Unit proses kecil dan cukup mandiri dari proses SR juga dapat secara logistik dan manajerial lebih fleksibel daripada kompleks terintegrasi yang besar (terdiri dari proses kokas, sintering dan BF) di mana perubahan atau penundaan produksi di satu area berdampak pada semua area lainnya . Fleksibilitas dalam sumber bahan bakar menguntungkan, dan proses yang dapat menggunakan berbagai macam batubara dari berbagai pemasok memberikan fleksibilitas tambahan.
- Kemampuan untuk berintegrasi dengan teknologi yang tersedia di area lain – Ini adalah tujuan lain untuk pengembangan proses pembuatan besi SR. Proses tersebut harus menghasilkan besi yang dapat digunakan oleh proses pembuatan baja yang ada. Selanjutnya proses SR tidak mengganggu proses pembuatan besi yang sudah beroperasi di dalam pabrik. Dalam konteks ini, produk yang dibutuhkan harus serupa dengan logam panas BF sehubungan dengan suhu dan komposisi kimia.
- Unggul dalam hal dampak lingkungan – Karena ada kesadaran yang berkembang tentang dampak lingkungan di seluruh dunia, proses dengan dampak yang lebih rendah terhadap lingkungan memiliki penerimaan yang lebih tinggi di industri. Oleh karena itu, tujuan pengembangan proses SR adalah memiliki emisi dan pembuangan limbah yang lebih rendah jika dibandingkan dengan proses pembuatan besi BF.
Konsep proses
Untuk proses pembuatan besi SR untuk melengkapi dan/atau bersaing dengan proses BF, generasi baru proses SR sedang dikembangkan. Proses ini didasarkan pada batubara non-coking sebagai bahan bakar utama dan reduktor dan bertujuan untuk produk besi cair. Beberapa dari proses ini mengusulkan untuk menggunakan tonase O2 sebagai oksidan untuk memungkinkan kebutuhan panas proses dipenuhi dengan pembakaran bahan bakar batubara. Beberapa orang membayangkan penggunaan pemanas listrik dalam skala besar sebagai sumber panas proses.
Reduksi peleburan bijih besi untuk menghasilkan produk besi cair dalam proses selain BF telah lama dikenal sebagai rute proses yang layak secara teknis dan menarik dan sejumlah konsep proses telah diusulkan. Banyak dari konsep proses ini tidak pernah menemukan aplikasi komersial dan sekarang tampaknya tidak mungkin untuk dikembangkan.
Untuk mengetahui, bagaimana proses pembuatan besi SR telah berkembang ke tingkat perkembangan saat ini, perlu dipahami posisi awal dari mana konsep proses pembuatan besi SR telah dikembangkan.
- Konsep proses dasar pembuatan baja oksigen (BOS) – Selama akhir 1970-an dan awal 1980-an, ada minat yang cukup besar dalam metode pengurangan biaya rute produksi BOS dengan meningkatkan kemampuan proses peleburan sisa. Hal ini didorong oleh rendahnya tingkat harga barang bekas pada saat itu. Metode penambahan bahan bakar (biasanya batu bara) ke konverter dan kemudian membebaskan panas untuk melelehkan sisa-sisa tambahan dengan meniupkan O2 ekstra dikembangkan, tetapi pemulihan energi di bejana cenderung relatif tidak efisien dan sebagian besar energi bahan bakar hilang di gas buang tungku. Dengan cepat disadari bahwa gas-gas ini sangat cocok untuk digunakan sebagai gas pereduksi dalam reduksi langsung, yang merupakan teknologi yang dipahami dengan baik. Kemudian menjadi jelas bahwa besi tereduksi yang dihasilkan dapat diumpankan ke konverter sebagai bahan baku logam untuk mempertahankan proses peleburan dan reduksi mandiri. Awalnya pengumpanan DRI panas dari unit reduksi ke reaktor pembuatan baja dipandang sebagai masalah rekayasa yang sulit, dan proses diusulkan di mana DRI didinginkan sebelum dibuang dari unit reduksi. Namun, sekarang telah diterima bahwa peningkatan efisiensi energi yang diperoleh dengan transfer panas DRI melebihi masalah teknik, dan konsep proses saat ini didasarkan pada transfer panas. Meskipun ada fitur khusus proses dari berbagai proses berbasis BOS, yang mencerminkan perbedaan dalam rekayasa dan penekanan proses di pihak pengembang, konsep dasar dan desain termokimia dari proses secara praktis identik.
- Konsep proses berbasis reduksi langsung – Sejak proses reduksi DR berbasis gas alam menjadi semakin kurang menarik di sebagian besar lokasi karena ketersediaan dan harga gas alam yang tinggi, upaya diarahkan untuk menggunakan batubara non-coklat sebagai sumber gas pereduksi untuk pengoperasian pabrik DR. Proses DR yang terkait dengan gasifikasi batubara dianggap layak secara teknis tetapi tidak layak karena biaya modal yang tinggi untuk gasifikasi batubara. Namun, konsep ini dibawa ke depan, dan peleburan-gasifier dari desain inovatif diusulkan yang terkait dengan poros reduksi dari jenis yang cukup konvensional. Melter-gasifier memiliki unggun terfluidisasi, diumpankan dengan batubara dan DRI dari poros reduksi, dengan tombak O2 terendam di unggun terfluidisasi. Batubara yang memasuki unggun didevolatilisasi dan arang yang tersisa membentuk konstituen utama unggun terfluidisasi, dan bahan bakar untuk peleburan DRI.
- Konsep proses berdasarkan perapian BF – Beberapa desain proses diusulkan di mana peleburan dan gasifikasi berlangsung di tempat tidur kokas, dengan cara yang sama seperti tahap peleburan akhir di BF. Dalam desain ini O2 dan batubara disuntikkan ke dalam reaktor yang dikemas dengan kokas yang juga diumpankan dengan DRI. Besi yang meleleh dan terak meresap melalui kokas untuk terkumpul di dasar reaktor, dan gas panas meninggalkan zona leleh melalui unggun kokas. Kokas hadir untuk memberikan tempat terbuka di mana pelelehan terjadi dan dari mana gas dapat keluar, tetapi bahan bakar utamanya adalah batu bara non-kokas yang dibakar dengan O2. Dalam konsep proses ini, tujuannya adalah untuk meminimalkan konsumsi kokas. Dalam konsep proses ini, DRI juga dapat disuntikkan ke dasar reaktor bersama dengan batubara dan O2 atau secara alternatif dimasukkan dari atas zona reaksi dengan kokas yang diperlukan untuk menggantikan kokas yang dikonsumsi dalam reaktor. Pengembangan lebih lanjut dari konsep tersebut telah mengarah pada pembuatan tahap reduksi di bagian atas reaktor peleburan daripada unit proses yang terpisah, memberikan proses reduksi peleburan oksi/batubara arus berlawanan secara kontinu. Proses tersebut berusaha mendekati tingkat efisiensi termal dan kimia yang sangat tinggi, yang mampu dilakukan oleh BF.
- Konsep proses dengan input energi listrik – Konsep ini telah menjadi dasar untuk beberapa proses. Konsep-konsep ini menggunakan listrik sebagai sumber panas dan batubara atau hidrokarbon lainnya hanya sebagai agen pereduksi. Asumsi dasar dalam konsep ini adalah bahwa seiring waktu, pembangkit listrik tenaga nuklir akan menyediakan energi listrik yang melimpah dengan biaya yang sangat rendah, dan bahan bakar fosil akan menjadi semakin mahal seiring dengan menipisnya sumber daya. Biasanya, konsep ini menggunakan pemanas listrik untuk desain reaktor yang dalam hal lain mirip dengan yang digunakan dalam berbagai proses oksi/batubara. Konsep-konsep ini mengakui bahwa batasan termokimia yang dikenakan oleh sistem kimia karbon/hidrogen/oksigen/besi berlaku baik sumber panasnya adalah pembakaran atau listrik.
- Konsep proses yang menggunakan tungku peleburan listrik dengan bahan bakar fosil sebagai energi primer – Ada beberapa proses yang menggunakan tungku listrik untuk peleburan dan reduksi akhir, dan penggunaan bahan bakar fosil, biasanya batubara non-coklat, sebagai sumber energi utama. Di bawah konsep ini, biasanya bahan bakar dimasukkan pada tahap reduksi dan gas buang dari reduksi, bersama dengan panas buangan lain yang timbul digunakan untuk menghasilkan energi listrik yang digunakan dalam operasi peleburan. Jenis desain ini memungkinkan tingkat pemisahan operasi reduksi dan peleburan, yang tidak perlu dicocokkan, karena proses selalu dapat diseimbangkan dengan impor atau ekspor listrik dari atau ke jaringan distribusi. Secara umum proses ini mentransfer sebagian material yang direduksi ditambah beberapa bahan bakar (char) dari unit reduksi ke peleburan yang juga melakukan reduksi akhir.
Berdasarkan tujuan dan konsep di atas, pekerjaan pengembangan dilakukan untuk beberapa proses. Beberapa dari proses ini adalah BSC, CIG, Hoogovens, Kobe, Krupp, Korf, BSC Oxy/Coal BF, Kawasaki, Pirogas, Plasmasmelt, Sumitomo, DSS, Combismelt, Elred, dan Inred dll. Beberapa dari proses ini tidak bertahan setelah awal bekerja pada skala laboratorium. Beberapa mencapai tahap pilot plant dan kemudian ditinggalkan. Beberapa dari upaya pengembangan ini digabung karena kegiatan 'penggabungan dan akuisisi' skala besar terjadi selama periode tersebut dan pekerjaan pengembangan dilanjutkan dengan nama baru untuk proses tersebut. Namun, pengetahuan yang diperoleh selama pekerjaan pengembangan ini membantu pengembangan lebih lanjut dari proses SR untuk pembuatan besi.
Dalam beberapa tahun terakhir, sekitar dua puluh proses SR telah dikembangkan di seluruh dunia. Prinsip dasar dari proses SR adalah melebur bijih besi/sinter/pelet yang telah direduksi dengan batu bara non-coking dan O2 atau ledakan panas di dalam reaktor. Tujuan dari semua proses SR adalah untuk mengkonsumsi batubara non-coking dan O2 dalam jumlah paling sedikit untuk membuat proses tersebut menjadi efisien bahan bakar.
Proses SR untuk pembuatan besi secara garis besar dapat dibagi menjadi dua kategori yaitu (i) proses yang menggunakan batubara dan listrik, dan (ii) proses yang menggunakan O2 dan batubara non-coking.
Proses yang menggunakan batu bara dan listrik
Proses SR ini memanfaatkan listrik sebagai sumber energi dan non-coking coal sebagai reduktor. Berdasarkan jumlah tahapan yang terlibat, proses ini dapat dibagi terutama menjadi dua jenis yaitu (i) proses satu tahap, dan (ii) proses dua tahap.
Dalam proses satu tahap, bejana reaktor diumpankan dengan bijih besi dingin tanpa pra-reduksi dan batubara non-coking digunakan sebagai pereduksi. Dalam proses ini, reduksi dan peleburan berlangsung di peleburan listrik. Gas buang dari smelter digunakan untuk pembangkit listrik internal. Proses ini menawarkan fleksibilitas yang lebih besar dibandingkan dengan proses oxy-coal lainnya.
Dalam hal proses dua tahap, DRI yang dihasilkan di unit reduksi dilebur di peleburan listrik. Gas buang dari unit reduksi digunakan untuk pembangkitan listrik internal. Proses ini menawarkan fleksibilitas yang lebih besar dibandingkan dengan proses oxy-coal lainnya.
Konsep proses satu tahap dan dua tahap yang memanfaatkan batubara dan listrik ditunjukkan pada Gambar 1.
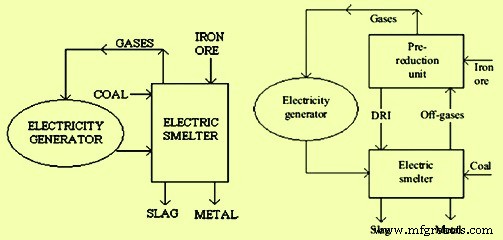
Gbr 1 Konsep proses satu tahap dan dua tahap yang memanfaatkan batubara dan listrik
Proses yang memanfaatkan oksigen dan batu bara
Proses SR ini memanfaatkan pembakaran oxy-coal sebagai sumber energi dan juga untuk tujuan reduksi. Berdasarkan jumlah tahapan yang terlibat (sesuai dengan desain termokimianya), proses ini dapat dibagi menjadi tiga jenis yaitu (i) proses satu tahap, (ii) proses dua tahap, dan (iii) proses tiga tahap.
Proses satu tahap adalah yang paling sederhana dari semua proses mandi besi dan secara teoritis mewakili desain ideal di mana logam panas diproduksi dalam reaktor tunggal di mana reduksi dan peleburan terjadi. Dalam proses ini, semua reaksi metalurgi dilakukan dalam reaktor tunggal di mana bijih besi, batu bara, dan O2 diumpankan dan gas yang dihasilkan dari penangas cairan dipasok ke tingkat yang sangat tinggi (sekitar 75%) dan sebagian besar panas dipindahkan kembali ke penangas cairan. Reaktor diumpankan dengan batubara basah dan bijih besi basah tanpa pra-reduksi dan karenanya prosesnya membutuhkan energi yang tinggi. Energi total disuplai oleh pembakaran batubara dengan O2. Persyaratan O2 dan batubara tinggi karena kemungkinan terbatas yang tersedia untuk pemanfaatan gas pereduksi. Proses SR ini umumnya tidak efisien dan tidak menarik secara ekonomi, kecuali jika kredit yang memadai diberikan untuk sejumlah besar gas buang bernilai tinggi (suhu tinggi dan potensi reduksi tinggi). Kontrol yang tepat dari terak berbusa dengan potensi pengoksidasi dan karakteristik didih tinggi dan erosi tahan api adalah dua masalah lain yang terkait dengan proses ini. Keuntungannya termasuk biaya modal yang rendah, penggunaan bijih besi yang tidak siap dan batubara non-coking, dan kemampuan untuk menerima bijih dan batubara kadar rendah. Proses Romelt dan Ausmelt adalah contoh untuk proses SR ini. Konsep proses single stage SR yang memanfaatkan O2 dan batubara tanpa dan dengan pasca pembakaran ditunjukkan pada Gambar 2.
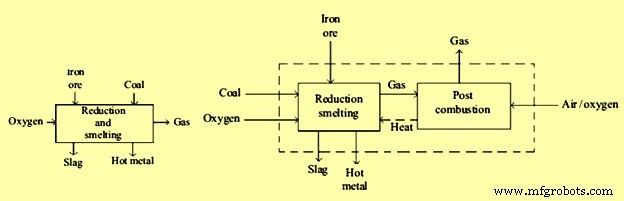
Gbr 2 Konsep proses SR satu tahap menggunakan O2 dan batubara tanpa dan dengan pasca pembakaran
Dalam proses dua tahap, dua reaktor terpisah untuk pra-reduksi dan reduksi peleburan digunakan. Gas buang dari tahap peleburan digunakan untuk pra-reduksi yang pada gilirannya mengurangi kebutuhan energi untuk reduksi akhir dan peleburan. Tergantung pada tingkat pra-reduksi dan pasca-pembakaran, proses ini dapat dibagi lagi menjadi dua kelompok. Pada kelompok pertama, terdapat proses-proses yang memiliki tingkat pra-reduksi yang tinggi dan tingkat pasca-pembakaran yang sangat rendah. Hal ini memerlukan kontrol yang ketat dari proses peleburan dimana komposisi dan jumlah gas buang yang dihasilkan cukup untuk menghasilkan DRI yang sangat metalisasi. Proses Corex termasuk dalam kategori ini. Pada kelompok kedua, proses-proses tersebut ada yang memiliki tingkat pra-reduksi rendah dan tingkat pasca-pembakaran tinggi. Oksida besi pra-reduksi panas umumnya dimasukkan ke dalam reaktor peleburan bersama dengan batubara non-coking dan O2/udara yang dipanaskan sebelumnya. Gas-gas yang berevolusi dari penangas cairan dibakar oleh O2/udara yang dipanaskan sebelumnya di dalam peleburan. Panas pasca pembakaran dipindahkan secara efisien dari fase gas ke penangas cair. Proses seperti HIsmelt, DIOS, AISI-DOE, dll., termasuk dalam grup ini. Efisiensi proses dua tahap dapat ditingkatkan dengan memisahkan zona reaksi gas dari zona peleburan. Kehilangan panas terjadi karena gas buang melter harus didinginkan dari 1600 derajat C menjadi 800 derajat C sebelum dapat digunakan untuk reduksi. Namun, jika karbon hadir di zona reaksi gas, itu dapat membantu mengurangi suhu off gas karena reaksi endotermik C+ CO2=2 CO, dan C + H2O =CO + H2. Konsep proses SR dua tahap memanfaatkan O2 dan batubara tanpa dan dengan pasca pembakaran ditunjukkan pada Gambar 3.
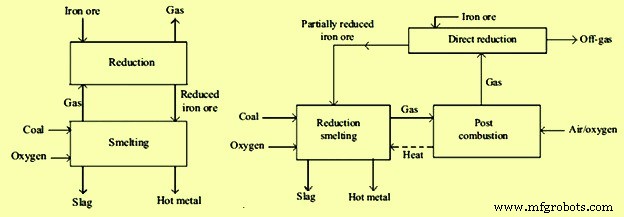
Gbr 3 Konsep proses SR dua tahap yang memanfaatkan O2 dan batubara tanpa dan dengan pasca pembakaran
Dalam proses tiga tahap, gasifier terpisah digabungkan dengan unit peleburan dan unit pra-reduksi untuk gasifikasi batubara yang menghasilkan CO, H2, CH4, dll. Proses ini membutuhkan langkah tambahan gasifikasi/reformasi gas antara reaktor peleburan dan pra -reaktor reduksi Kehadiran karbon di zona gasifikasi membantu dalam mengurangi suhu gas peleburan tanpa kehilangan energi. Konsep proses SR tiga tahap yang memanfaatkan O2 dan batubara ditunjukkan pada Gambar 4.
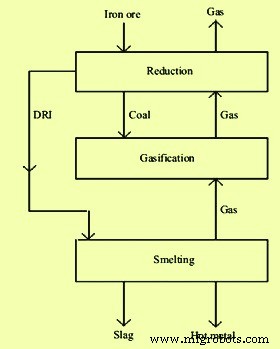
Gbr 4 Konsep proses SR tiga tahap menggunakan O2 dan batubara
Keuntungan dari proses SR
Proses SR memiliki banyak keunggulan dalam hal bahan baku, biaya energi, biaya modal, skala ekonomi, dan kompatibilitas lingkungan. Keuntungan tersebut antara lain sebagai berikut.
- Biaya investasi yang lebih rendah karena skala operasi ekonomi yang lebih rendah dibandingkan dengan BF.
- Biaya operasional yang lebih rendah terutama karena penggunaan batubara non-coking.
- Intensitas peleburan tinggi dengan produktivitas tinggi karena kinetika reaksi yang lebih cepat dan peningkatan laju transpor karena konveksi. Kapasitas leleh spesifik sangat tinggi, setidaknya dua kali lipat dari kapasitas leleh spesifik dalam BF. Pemanfaatan langsung bijih besi halus dan halus batu bara dimungkinkan.
- Tidak ada persyaratan batu bara kokas yang mahal.
- Proses berkontribusi pada penghapusan sintering/peletisasi dan pembuatan kokas. Karena penghapusan ini, terjadi penurunan kebutuhan tenaga kerja dan pengurangan biaya operasional.
- Prosesnya ramah lingkungan karena emisinya lebih rendah.
- Proses mempertahankan kualitas logam panas yang sama seperti yang diperoleh di BF.
- Kontrol yang ditingkatkan atas parameter proses dimungkinkan.
- Fleksibilitas tersedia dalam pemilihan desain termokimia.
- Proses reduksi lebih cepat dari BF.
- Sedapat mungkin mendaur ulang timbunan stok yang ada, debu di pabrik, lumpur, dan revert lainnya.
- Proses ini memberikan peningkatan ekonomi energi dengan memanfaatkan gas buang untuk pembangkit listrik. Proses SR menghasilkan banyak gas, yang dapat digunakan untuk pembangkit listrik.
Keterbatasan proses SR antara lain sebagai berikut.
- Proses mengkonsumsi O2 dalam jumlah besar, yang pembangkitannya membutuhkan daya yang tinggi (sekitar 0,6 kWh per N cum O2).
- Proses tersebut menghasilkan sejumlah besar gas ekspor dengan nilai kalori tinggi (sekitar 2000 kkal/N cum) dan kelayakan ekonomis dari proses tersebut bergantung pada pemanfaatannya yang efisien.
- Ukuran modul maksimum unit proses SR terbatas dan mungkin bukan alternatif terbaik jika kapasitas pembuatan besi besar diperlukan di pabrik.
- Pra-reduksi bijih besi adalah kebutuhan untuk proses tersebut.
- Proses membutuhkan pasca-pembakaran yang sangat efisien untuk memenuhi kebutuhan energi proses peleburan.