Produksi Ferro-Mangan
Produksi Ferro-Mangan
Ferro-mangan (Fe-Mn) adalah aditif penting yang digunakan sebagai deoxidizer dalam produksi baja. Merupakan paduan utama besi (Fe) dan mangan (Mn) dengan kandungan Mn minimal 65%, dan kandungan Mn maksimal 95%. Ini diproduksi dengan memanaskan campuran oksida Mn (MnO2) dan besi (Fe2O3) dengan karbon (C) biasanya sebagai kokas atau batubara.
Fe-Mn dalam tanur tinggi (BF) dengan kandungan Mn jauh lebih tinggi daripada yang mungkin sebelumnya diproduksi pertama kali pada tahun 1872 oleh Lambert Von Pantz. Fe-Mn yang dihasilkan memiliki 37% Mn, bukan 12% yang diperoleh sebelumnya. Bijih Mn tingkat metalurgi yang memiliki kandungan Mn lebih tinggi dari 40% biasanya diproses menjadi bentuk logam ferro-alloy yang sesuai dengan proses piro-metalurgi, yang sangat mirip dengan proses piro-metalurgi besi. Dalam proses produksinya, campuran bijih Mn, reduktor (bentuk C) dan fluks (CaO) dilebur pada suhu yang lebih tinggi dari 1200 derajat C untuk memungkinkan reaksi reduksi dan pembentukan paduan. Nilai standar Fe-Mn dapat diproduksi baik dalam BF atau dalam tanur busur listrik terendam (SAF).
Proses SAF listrik, bagaimanapun, jauh lebih fleksibel daripada proses BF, di mana terak dapat diproses lebih lanjut menjadi Si-Mn dan Fe-Mn yang dimurnikan. Pilihan proses juga tergantung pada harga relatif tenaga listrik dan kokas. Dalam SAF tiga fase, elektroda dikubur dalam bahan muatan. Bahan baku dipanaskan dan Mn oksida direduksi oleh gas karbon mono oksida (CO) panas membentuk zona reaksi yang lebih dalam di tungku. Reaksi eksotermik memberikan kontribusi yang baik terhadap panas yang dibutuhkan. Produksi HC Fe-Mn yang efisien tergantung pada tingkat pra-reduksi yang terjadi di bagian atas tungku.
Ada beberapa kadar Fe-Mn yang dibagi menjadi banyak kelompok. Tiga kelompok utama adalah C Fe-Mn tinggi, C Fe-Mn sedang, dan C Fe-Mn rendah. Fe-Mn C tinggi dapat dibuat dalam BF dan SAF. Pada SAF dibuat dengan dua praktek yang berbeda yaitu (i) praktek terak Mn tinggi, dan (ii) praktek membuang terak. Medium C Fe-Mn dapat diproduksi dengan proses de-karbonasi atau melalui reaksi redoks (reduksi-oksidasi) antara silikon (Si) dalam paduan silico-mangan (Si-Mn) dan bijih Mn. Fe-Mn C rendah dihasilkan dari reaksi bijih Mn dan Si-Mn C rendah.
Bahan baku yang dibutuhkan untuk produksi Fe-Mn
Bahan baku yang dibutuhkan untuk produksi Fe-Mn adalah bijih Mn, kokas dan fluks seperti batugamping, dolomit dan kuarsit. Bahan baku sering disimpan di luar ruangan, dan kandungan air, termasuk air yang terikat secara kimiawi dalam bijih Mn, mungkin tinggi, hingga 10%.
Bijih Mn merupakan bahan baku penting yang digunakan dalam produksi Fe-Mn. Bijih Mn diklasifikasikan menurut kandungan Mn. Secara umum, bijih yang mengandung setidaknya 35% Mn diklasifikasikan sebagai bijih Mn. Biasanya, ada tiga nilai bijih Mn berdasarkan kandungan Mn-nya. Yaitu (i) bijih Mn kadar tinggi dengan kadar Mn 44% sampai 48%, (ii) bijih Mn kadar sedang dengan kadar Mn 35% sampai 44%, dan bijih Mn kadar rendah dengan kadar Mn 25% sampai 35 %.
Bijih dengan kandungan Mn 10% sampai 35% disebut bijih besi mengandung Mn sedangkan bijih dengan kandungan Mn 5% sampai 10% disebut bijih besi mangan. Bijih yang mengandung kurang dari 5% Mn dengan keseimbangan sebagian besar Fe diklasifikasikan sebagai bijih besi.
Kokas yang dibutuhkan untuk produksi Fe-Mn di SAF harus lebih reaktif daripada yang biasanya digunakan dalam besi BF. Kokas yang sangat reaktif ketika digunakan dalam SAF menghasilkan pengoperasian tungku yang stabil yang memberikan produktivitas yang baik.
Produksi Fe-Mn C tinggi dalam BF
Tungku sembur banyak digunakan di negara maju untuk produksi Fe-Mn, hingga akhir Perang Dunia II. Biasanya, pabrik baja terintegrasi menetapkan BF mereka yang lebih kecil untuk produksi Fe-Mn C tinggi. Bijih Mn kadar rendah dengan kandungan Mn minimal 28% dapat digunakan untuk peleburan di BF.
Fe-Mn C tinggi diproduksi di BF dalam proses yang mirip dengan proses menghasilkan logam panas (HM) di BF. Namun ada beberapa perbedaan penting antara kedua proses tersebut. Oksida besi direduksi oleh CO di daerah poros tungku sesuai dengan reaksi berikut.
3Fe2O3 + CO =2Fe3O4 + CO2
Fe3O4 + CO =3FeO + CO2
FeO + CO =Fe + CO2
Di sisi lain, Mn oksida direduksi oleh C padat di daerah bosh dan perapian BF karena suhu yang lebih tinggi disebabkan oleh reaksi berikut.
Mn3O4+ 4C =3Mn + 4CO
MnO + C =Mn + CO
Oleh karena itu, produksi Fe-Mn di BF membutuhkan jumlah kokas yang lebih besar daripada yang dibutuhkan untuk produksi HM di BF. Pemanasan awal ledakan dan pengayaan oksigen (O2) biasanya digunakan untuk mengurangi kebutuhan kokas. Dolomit atau batugamping yang ditambahkan ke muatan meningkatkan aktivitas MnO untuk reduksi. Volume terak kecil, terak dasar dan suhu ledakan tinggi diperlukan untuk pemulihan Mn yang lebih tinggi. Dengan kontrol yang cermat dan campuran muatan yang lebih seragam di poros BF, perolehan kembali Mn lebih dari 90% dan laju kokas 1530 kg/t telah dicapai.
Gas teratas di BF yang menghasilkan Fe-Mn mengandung butiran halus yang berlebihan. SAF telah menggantikan BF karena laju kokas yang lebih kecil, umur refraktori yang lebih lama, tidak memerlukan ledakan panas, dan penggunaan kembali terak yang kaya MnO untuk produksi paduan besi Si-Mn.
Produksi Fe-Mn C tinggi dalam SAF
Dalam kasus produksi C Fe-Mn tinggi dalam BF, energi panas yang dibutuhkan untuk proses peleburan disuplai oleh pembakaran kokas tambahan, sedangkan dalam kasus produksi C Fe-Mn tinggi dalam SAF, termal energi yang dibutuhkan untuk proses peleburan disuplai oleh tenaga listrik. Belanja modal yang dibutuhkan untuk fasilitas baru juga lebih rendah dalam kasus SAF.
Parameter desain penting dari SAF untuk produksi Fe-Mn C tinggi adalah (i) diameter dan jarak elektroda, (ii) diameter tungku perapian, (iii) kedalaman wadah, (iv) rentang tegangan, dan (v) MVA kapasitas transformator. Karena resistivitas beban yang rendah dalam produksi Fe-Mn, tegangan rendah antara elektroda diperlukan untuk mempertahankan penetrasi elektroda yang memuaskan dalam muatan. Oleh karena itu, untuk mendapatkan pembebanan daya yang tepat untuk tungku, diperlukan arus yang lebih tinggi. Jadi, untuk beroperasi dalam kapasitas pembawa arus elektroda C, diameter elektroda untuk SAF yang memproduksi Fe-Mn lebih tinggi daripada SAF yang memproduksi ferroalloy lainnya. Energi listrik disuplai untuk reaksi peleburan melalui tiga elektroda karbon, yang biasanya tipe self-baking. Wadah terdiri dari cangkang baja dilapisi dengan batu bata tahan api dan lapisan dalam blok C. Perapiannya mirip dengan BF, tetapi memiliki lapisan C yang lebih tebal.
Ketinggian poros SAF jauh lebih sedikit daripada besi BF dan waktu tinggal beban di poros secara proporsional lebih sedikit. Biasanya, reduksi oksida menjadi logam dilakukan dalam beberapa jam dibandingkan dengan 6 sampai 8 jam dalam BF besi. Penggunaan kokas reaktif dalam produksi SAF Fe-Mn memungkinkan oksida besi direduksi menjadi logam, oksida Mn yang lebih tinggi direduksi menjadi MnO dan sejumlah kecil MnO direduksi menjadi Mn yang terlarut dalam besi pada saat beban mencapai lapisan terak-kokas campuran di bawah elektroda. Ketinggian poros yang lebih rendah relatif terhadap BF juga berarti bahwa kekuatan kokas adalah sifat yang kurang kritis dalam peleburan SAF Fe-Mn daripada di peleburan BF besi.
SAF yang memproduksi Fe-Mn dapat memiliki bagian atas terbuka atau bagian atas tertutup. Tungku atas terbuka memiliki tudung pengumpul asap setidaknya 1 meter di atas bagian atas cangkang tungku. Panel atau layar yang dapat dipindahkan terkadang digunakan untuk mengurangi area terbuka antara tungku dan kap mesin, dan untuk meningkatkan efisiensi penangkapan emisi. Gas CO yang naik melalui muatan tungku terbakar di area antara permukaan muatan dan tudung penangkap. Ini secara substansial meningkatkan volume gas yang harus ditangani oleh sistem penahanan. Selain itu, proses pembakaran terbuka yang kuat membawa material yang lebih halus ke dalam muatan. Filter kantong kain biasanya digunakan untuk mengontrol emisi dari tungku terbuka.
SAF atas tertutup (Gbr 1) biasanya memiliki penutup baja berpendingin air yang pas dengan cangkang tungku. Tujuan dari tungku atas tertutup adalah untuk mengurangi infiltrasi udara ke dalam gas tungku, yang mengurangi pembakaran gas. Ini mengurangi volume gas yang membutuhkan pengumpulan dan perawatan. Penutup memiliki lubang untuk bahan muatan dan elektroda untuk dilewati. Tungku atas tertutup yang menutup sebagian bukaan kap ini disebut sebagai 'tungku tertutup campuran' atau 'tungku setengah tertutup'. Meskipun jenis tungku tertutup ini secara signifikan mengurangi infiltrasi udara, beberapa pembakaran masih terjadi di bawah penutup tungku. SAF atas tertutup yang memiliki segel mekanis di sekitar elektroda dan senyawa penyegel di sekitar tepi luar disebut sebagai 'tertutup' atau 'tertutup total'. Tungku ini memiliki sedikit, jika ada, infiltrasi udara dan pembakaran terselubung. Kebocoran air dari penutup ke dalam tungku harus diminimalkan karena hal ini menyebabkan produksi gas yang berlebihan dan operasi tungku yang tidak stabil. Produk yang rentan terhadap pelepasan gas proses yang sangat bervariasi biasanya tidak dibuat di tungku dekat atas untuk alasan keamanan. Dengan meningkatnya derajat selungkup, lebih sedikit gas yang dihasilkan untuk ditangkap oleh sistem tudung dan konsentrasi CO dalam gas tungku meningkat. Scrubber basah digunakan untuk mengontrol emisi dari SAF atas tertutup. Gas kandungan CO tinggi yang digosok dapat digunakan di dalam pabrik sebagai bahan bakar atau dibakar.
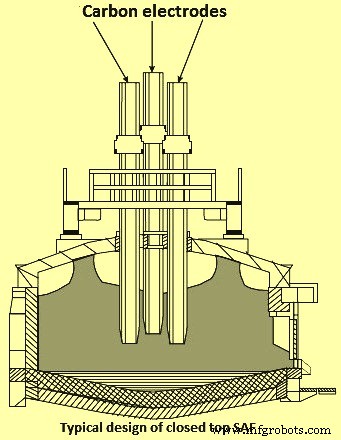
Gbr 1 Desain tipikal tungku busur terendam atas tertutup
SAF atas tertutup memungkinkan kontrol asap yang lebih baik dengan biaya modal yang lebih rendah dan menurunkan kebutuhan energi. Di sisi lain, persyaratan untuk bijih yang digunakan dalam tungku atas tertutup lebih terbatas, mis. O2 bebas harus kurang dari 10% dan bijih kurang gembur. Jika tidak, kerak dapat terbentuk yang menyebabkan terjadinya ledakan. Kinerja ekonomi untuk produksi Fe-Mn ditingkatkan dengan memilih bahan baku yang tepat yang cocok untuk SAF atas tertutup, menerapkan keseimbangan bahan terbaik untuk bahan baku dan meningkatkan kondisi peleburan. Ini menghasilkan konsumsi bahan baku yang lebih rendah, konsumsi energi spesifik yang berkurang, operasi tungku yang baik, kualitas paduan yang lebih tinggi, dan biaya produksi yang lebih rendah.
Reaksi dan perubahan bahan beban selama produksi C Fe-Mn tinggi dalam SAF telah lebih baik dipahami dengan mempelajari secara ekstensif tungku beku yang digali di pabrik Meyerton Fe-Mn di Afrika Selatan pada tahun 1977. Studi ini memberikan cukup banyak pemahaman tentang perubahan bahan beban dan sifat zona reaksi. Penggalian mengungkapkan bahwa interior tungku dapat dibagi menjadi sembilan zona yang tiga tampaknya paling penting untuk reduksi dan pemrosesan metalurgi. Ini adalah (i) kerucut beban turun cepat di sekitar masing-masing elektroda, (ii) unggun kokas langsung di bawah elektroda, dan (iii) lapisan campuran kokas-terak di bawah unggun kokas. Pengungkapan utama dari penggalian adalah bahwa antara suhu dalam kisaran 1300 derajat C dan 1600 derajat C, reduksi terjadi dalam tiga tahap utama, yaitu (i) reduksi cepat oksida Mn yang lebih tinggi menjadi MnO dan hematit menjadi logam Fe (dalam padatan oleh gas CO dan pembentukan terak primer yang sebagian besar terdiri dari CaO dan SiO2, (ii) pelarutan MnO ke dalam terak dan reduksi pada permukaan gumpalan bijih untuk membentuk manik-manik logam, dan (iii) reduksi oleh gumpalan C dalam kontak dengan terak cair.
Reduksi karbotermik MnO dan FeO adalah reaksi endotermik tetapi reduksi MnO membutuhkan lebih banyak panas daripada reduksi FeO seperti yang diberikan dalam reaksi berikut.
MnO (s) + C (s) =Mn (l) + CO (g) Delta H =276 KJ (pada 1200 derajat C)
FeO (l) + C (s) =Fe (s) + CO (g) Delta H =149 KJ (pada 1200 derajat C)
Reduksi MnO juga membutuhkan suhu minimum yang lebih tinggi. Suhu reduksi untuk MnO adalah 1400 derajat C dan untuk FeO adalah 720 derajat C. Dalam praktiknya, aktivitas termodinamika Mn dan Fe kurang dari satu karena pembentukan paduan sehingga suhu minimum yang sebenarnya sedikit lebih rendah. Dalam produksi Fe-Mn, dengan demikian, secara termodinamika mungkin bijih besi direduksi menjadi Fe, oksida Mn yang lebih tinggi direduksi menjadi MnO, dan sebagian MnO direduksi menjadi Mn yang dilarutkan dalam logam Fe ( pada aktivitas termodinamika rendah) dalam keadaan padat di bawah kondisi di poros menggunakan panas yang masuk akal dan mengurangi kapasitas gas yang dihasilkan di zona terak-kokas. Ini hanya menyisakan pengurangan sisa MnO yang terjadi di zona campuran terak-kokas bersuhu tinggi. Laju reduksi oksida Fe menjadi logam dan reduksi oksida Mn yang lebih tinggi menjadi MnO sangat dikendalikan oleh reaksi Boudouard (C+ CO2 =2CO) dalam kondisi yang ada di poros SAF pada suhu hingga sekitar 1300 derajat C. Laju reduksi MnO menjadi paduan jauh lebih sedikit dikendalikan oleh reaksi Boudouard karena, pada suhu (lebih besar dari 1300 derajat C) di mana sebagian besar MnO berkurang, reaktivitas kokas, terlepas dari nilai awal cenderung konvergen ke nilai yang sama secara luas.
Reduksi Mn oksida (MnO2) tertinggi terjadi dalam empat tahap. Tahap reduksi pertama dari MnO2 menjadi Mn2O3 (4MnO2 =2Mn2O3 + O2) dicapai pada suhu lebih besar dari 450 derajat C hingga 500 derajat C dan tahap kedua Mn2O3 menjadi Mn3O4 (6Mn2O3 =4Mn3O4 + O2) pada suhu lebih besar dari 900 derajat C hingga 950 derajat C dan keduanya dapat diwujudkan tanpa zat pereduksi dan hanya dengan dekomposisi termal. Kedua langkah dalam dekomposisi termal menunjukkan kisaran stabilitas Mn oksida. Reduksi Mn3O4 menjadi MnO (Mn3O4 + CO =3 MnO + CO2, dan Mn3O4 + C =3 MnO + CO) hanya dimungkinkan oleh gas CO atau padatan C. Reduksi MnO oleh karbon pada tekanan atmosfer hanya dapat dilakukan pada suhu lebih besar dari 1410 derajat C. Untuk mencapai reduksi penuh, suhu harus lebih tinggi lagi. Masalahnya di sini adalah tekanan uap Mn yang tinggi dan penguapan yang kuat. Dalam kasus proses produksi Mn dengan berbagai langkah reduksi, MnO pertama larut dalam fase terak dari mana Mn direduksi oleh C padat dan bergerak ke fase logam. Di sini solusi terak dan paduan yang tidak ideal sangat penting. Metode termodinamika terkini digunakan untuk menentukan fase dan neraca energi berdasarkan neraca massa.
Kokas yang lebih reaktif yang digunakan untuk produksi Fe-Mn dalam SAF memungkinkan reaksi yang dikendalikan Boudouard diselesaikan lebih tinggi di poros, sehingga lebih efektif memanfaatkan panas yang masuk akal dan mengurangi kapasitas gas dari tungku yang lebih rendah, dan memungkinkan reduksi permintaan panas akhir dari MnO menjadi Mn menjadi reaksi utama di zona campuran terak-kokas bersuhu tinggi. Sebaliknya, kokas yang kurang reaktif dapat menyebabkan kondisi reduksi yang buruk dan lapisan kokas yang lebih besar di tungku, menghasilkan kontrol tungku yang buruk, komposisi paduan dan terak yang tidak stabil, dan konsumsi daya yang lebih tinggi.
Pertimbangan penting untuk keberhasilan operasi peleburan adalah komposisi terak, karena memiliki efek yang berbeda pada resistivitas tungku, suhu peleburan, pemulihan Mn, dan jumlah Si dalam Fe-Mn. Pencampuran bijih atau penambahan pereaksi fluks seringkali diperlukan untuk menghasilkan komposisi terak yang diinginkan. Dua jenis praktik terak biasanya digunakan untuk produksi Fe-Mn dalam SAF. Ini adalah (i) praktik terak Mn tinggi, dan (ii) praktik terak Mn rendah juga dikenal sebagai praktik 'buang terak'.
Praktek terak Mn tinggi umumnya lebih disukai oleh pabrik-pabrik di mana bijih Mn kadar tinggi dilebur dan Si-Mn juga diproduksi. Kandungan Mn terak ini berkisar antara 28% sampai 40%. Kisaran % khas dari senyawa lain dalam terak adalah (i) MgO -3% hingga 8%, (ii) Al2O3 – 10% hingga 30%, (iii) CaO – sekitar 15%, dan (iv) SiO2 – 25% menjadi 28%. Terak ini umumnya digunakan dalam produksi Si-Mn, sehingga meningkatkan perolehan Mn secara keseluruhan. Sejumlah kecil fluks seperti dolomit atau batu kapur juga digunakan tergantung pada konsentrasi Mn yang diinginkan dalam terak.
Praktek membuang terak diikuti ketika kualitas bijih Mn sangat rendah. Karena kualitas bijih Mn yang rendah, ekstraksi Mn tingkat tinggi diperlukan untuk mencapai kandungan Mn yang diinginkan dalam paduan Fe-Mn. Juga ketika bijih Mn mengandung oksida dasar seperti CaO dan MgO, dan jika bijih tersebut dilebur sendiri, maka secara alami akan menghasilkan terak Mn yang rendah. Kandungan Mn terak dari praktik ini umumnya berkisar antara 10% hingga 20% dan perolehan kembali Mn dalam paduan Fe-Mn berkisar antara 80% hingga 90%. Kisaran % khas dari senyawa lain dalam terak adalah (i) MgO -3% hingga 8%, (ii) Al2O3 – 4% hingga 10%, (iii) CaO – sekitar 35%, dan (iv) SiO2 – 28% menjadi 32%. Jika bijih Mn hanya mengandung sejumlah kecil CaO atau MgO, muatan tungku kemudian terdiri dari bijih Mn, kokas, dan fluks dasar seperti batu kapur atau dolomit. Hasil yang lebih baik diperoleh ketika oksida dasar yang dibutuhkan (CaO atau MgO) terkandung dalam bijih Mn. Kebutuhan daya pada praktik slag slag lebih tinggi daripada yang dibutuhkan untuk praktik slag Mn yang tinggi karena adanya energi tambahan yang dibutuhkan untuk kalsinasi dolomit atau batugamping dalam muatan dan semakin banyak jumlah Mn yang terekstraksi dari slag yang menghasilkan kandungan CO yang lebih tinggi di dalam off-gas dibandingkan dengan praktik Mn tinggi.
Produksi Fe-Mn medium C
Medium C Fe-Mn mengandung 1% hingga 1,5% C dan memiliki kandungan Mn berkisar antara 75% hingga 85%. Medium C Fe-Mn dapat diproduksi baik dengan pemurnian C Fe-Mn tinggi dengan O2 atau dengan rute silico-termik, di mana Si dalam Si-Mn digunakan untuk mengurangi tambahan MnO yang ditambahkan sebagai bijih atau terak.
Pemurnian Fe-Mn C tinggi dengan O2 – Proses ini juga dikenal sebagai proses pemurnian oksigen mangan (MOR) dan dipatenkan oleh Union Carbide. Dalam proses ini, Fe-Mn C tinggi didekarburasi dengan cara yang sama seperti yang dilakukan dalam proses pembuatan baja di tungku oksigen dasar (BOF). Namun, ada beberapa perbedaan yang jelas dalam hal pemurnian Fe-Mn. Perbedaan ini adalah (i) suhu akhir 1750 derajat C diperlukan dibandingkan dengan 1650 derajat C yang dibutuhkan dalam pembuatan baja, (ii) serangan yang lebih parah pada refraktori, (iii) pengecoran paduan akhir yang sulit, (iv) tekanan uap yang lebih tinggi Mn, dan (v) volume dan suhu off-gas yang lebih tinggi.
Pada proses MOR, O2 ditiupkan ke dalam leburan C Fe-Mn yang tinggi dan suhu dinaikkan dari nilai sadapannya 1300 derajat C menjadi 1750 derajat C. Panas yang dibutuhkan disuplai oleh oksidasi Mn menjadi Mn oksida dan C ke CO. Pada bagian awal proses peniupan, sebagian besar O2 dikonsumsi oleh oksidasi Mn, dan suhu lelehan meningkat dari 1300 derajat C menjadi 1550 derajat C. Selanjutnya, C teroksidasi dengan cepat dan suhu naik menjadi 1650 derajat C. Di atas suhu ini, laju penyisihan C menurun dan Mn sekali lagi teroksidasi. Proses dihentikan pada 1750 derajat C, yang sesuai dengan kandungan C 1,3%. Pengurangan lebih lanjut dalam kandungan C menghasilkan kehilangan Mn yang sangat tinggi. Pada proses MOR, perolehan kembali Mn sekitar 80% dan distribusi Mn dapat diuraikan sebagai (i) paduan MC Fe-Mn 80%, (ii) fume yang terbentuk dari penguapan 13%, (iii) slag yang dibentuk oleh oksidasi Mn 5%, dan (iv) kehilangan lainnya, percikan dll. 2%.
Keberhasilan operasi proses ini tergantung pada desain bejana peniup dan tombak O2 serta perhatian yang cermat terhadap prosedur operasional. Proses MOR memiliki banyak keunggulan dibandingkan proses silico-termik yang meliputi konsumsi energi yang lebih rendah, investasi modal yang lebih rendah, biaya produksi yang lebih rendah, dan fleksibilitas yang lebih besar. Kerugian utama dari proses ini adalah penggunaannya terbatas pada produksi medium C Fe-Mn karena kandungan C tidak dapat diturunkan di bawah 1,3%.
Rute silika-termik – Dalam rute silika-termik untuk produksi medium C Fe-Mn, terak bermutu tinggi atau lelehan yang mengandung bijih Mn dan kapur (CaO) dikontakkan dengan Si-Mn yang mengandung Si dalam kisaran 16% hingga 30%. Si dalam paduan bertindak sebagai zat pereduksi dalam proses, yang mereduksi oksida Mn dalam lelehan menurut reaksi Si + 2MnO =SiO2 + 2Mn. Tujuan kapur adalah untuk mengurangi aktivitas SiO2 dalam lelehan, sehingga memaksa reaksi di atas sejauh mungkin ke kanan. Rasio kebasaan (CaO/SiO2) dalam terak harus lebih besar dari 1,4 untuk pengurangan yang cukup dalam aktivitas SiO2.
C yang memasuki proses dalam Si-Mn tetap seluruhnya dalam fasa logam dan karena itu ditemukan dalam produk. Jadi, untuk menghasilkan medium C Fe-Mn yang mengandung 1% C, diperlukan Si-Mn yang mengandung 20% Si. Panas yang dihasilkan oleh reduksi silico-termik tidak cukup untuk mempertahankan proses. Oleh karena itu biasanya dilakukan dalam tungku busur listrik (EAF). EAF ini dilapisi dengan batu bata magnesit, yang cukup tahan terhadap terak yang sangat mendasar. EAF dapat dimiringkan sehingga terak dapat dipisahkan dari logam.
Meskipun proses reduksi silico-termik lebih intensif energi daripada dekarburisasi C Fe-Mn tinggi, ia memiliki keuntungan bahwa kandungan C akhir hanya dibatasi oleh kandungan C dari Si-Mn awal. Oleh karena itu, proses silika-termik dapat digunakan untuk memproduksi logam C Fe-Mn dan Mn industri yang rendah.
Produksi Fe-Mn C rendah
Rendah C Fe-Mn mengandung Mn dalam kisaran 76% hingga 92% dan C dalam kisaran 0,5% hingga 0,75. Produksi Fe-Mn C rendah tidak mungkin dilakukan dengan dekarburisasi Fe-Mn C tinggi tanpa kehilangan Mn yang sangat tinggi. Oleh karena itu harus dibuat dari proses reduksi siliko-termik. Prosesnya mirip dengan yang digunakan dalam produksi silika-termik medium C Fe-Mn. Bijih dengan kemurnian tinggi digunakan dan khususnya bijih yang mengandung Fe dan P harus dihindari. Bijih Mn buatan yang diproduksi sebagai bijih kadar tinggi sangat cocok karena tingkat pengotornya yang rendah dan karena semua Mn ada sebagai MnO. Oleh karena itu, reduksi oksida Mn yang lebih tinggi tidak diperlukan. Angka konsumsi khas per ton ferromanganese C Fe-Mn rendah yang memiliki komposisi Mn – 85 % hingga 92%, C – sekitar 0,1 %, dan Si sekitar 1 % dengan perolehan kembali mangan 75 % adalah bijih Mn terkalsinasi – 1250 kg hingga 1350 kg, Si-Mn (mengandung 32% hingga 33% Si) – 800 kg hingga 850 kg, kapur tohor – 1000 kg hingga 1100 kg, elektroda – 10 kg hingga 12 kg dan daya listrik – 1800 kWh hingga 2500 kWh.