Injeksi Limbah Plastik di Blast Furnace
Injeksi Sampah Plastik di Blast Furnace
Daur ulang limbah plastik (WP) dengan menyuntikkannya ke dalam tanur tinggi (BF) sedang dipraktekkan di beberapa BF terutama di Jepang dan Eropa. Penggunaan plastik di BF juga memulihkan energi dari WP sehingga terkadang dianggap sebagai pemulihan energi. Proses pembuatan besi berbasis BF dapat memanfaatkan WP dengan salah satu metode berikut.
- Karbonisasi dengan batubara untuk menghasilkan kokas.
- Pengisian atas ke dalam BF, meskipun ini menghasilkan tar yang tidak diinginkan dari penguraian plastik di poros.
- Menggasifikasi plastik di luar BF. Gas sintesis yang dihasilkan kemudian disuntikkan melalui tuyeres.
- Injeksi sebagai padatan melalui tuyer dengan cara yang mirip dengan bubuk batubara (PC). Biasanya dilakukan sebagai injeksi bersama WP dan batubara ke dalam BF.
Upaya pertama untuk injeksi plastik limbah (WPI) di BF dilakukan di Bremen Steel Works pada tahun 1994, dengan injeksi komersial dimulai setahun kemudian. Sistem terintegrasi pertama untuk menyuntikkan sampah plastik ada di Keihin Works milik NKK (sekarang JFE Steel) di Jepang.
Menyuntikkan WP ke BF memiliki beberapa keuntungan lingkungan, operasional dan ekonomi. Ini termasuk yang berikut.
- Pengurangan jumlah sampah plastik yang dibuang atau dibakar.
- Konsumsi coke dan PC lebih rendah, sehingga menghemat sumber daya batubara. Namun, baik WP maupun PC tidak dapat sepenuhnya menggantikan coke. Jumlah kokas yang diganti dalam BF sebagian tergantung pada kualitas WP.
- Ada penghematan sumber daya energi. Manfaat sumber daya yang dihemat dari campuran WPI adalah sekitar 11 giga kalori per ton (Gcal/t).
- Ada penurunan emisi karbon dioksida (CO2) karena energi pembakaran WP umumnya setidaknya setinggi PC yang diinjeksi secara normal, dan rasio hidrogen (H2) terhadap karbon (C) yang lebih tinggi berarti lebih sedikit CO2 diproduksi di dalam BF dari proses pembakaran dan reduksi bijih besi.
- Konsumsi energi lebih rendah karena H2 adalah zat pereduksi yang lebih disukai daripada C. Regenerasi H2 lebih cepat dan kurang endotermik daripada regenerasi karbon monoksida (CO). Dengan demikian WPI dapat menurunkan konsumsi energi, yang juga berarti menurunkan emisi CO2.
- Ada efisiensi energi yang tinggi yaitu setidaknya 80%. Sekitar 60% dari plastik yang disuntikkan dikonsumsi untuk mereduksi bijih besi, dan sekitar 20% energi di sisa 40% gas digunakan sebagai bahan bakar di dalam pabrik baja. Dengan demikian, pemanfaatan WP adalah proses yang efisien dalam BF.
- WP memiliki kandungan sulfur (S) dan alkali yang lebih rendah dibandingkan batubara. Injeksi dengan kandungan S rendah diinginkan karena efek S pada kualitas logam panas (HM). Alkali dapat berkontribusi pada degradasi kokas, disintegrasi sinter, dan kerusakan lapisan tungku tahan api.
- Emisi dioksin dan furan lebih rendah. Emisi dioksin di Bremen Steel Works adalah 0,0001–0,0005 nano gram per meter kubik (ng/cum) gas buang, nilai yang jauh di bawah norma. Biasanya, tidak ada kontaminasi gas tambahan yang muncul sehingga gas BF teratas dapat digunakan di pabrik baja.
Kerugian utama WPI adalah biaya pengumpulan dan perawatan material. WP berasal dari berbagai sumber termasuk rumah tangga, industri dan pertanian, sehingga tersebar luas. Oleh karena itu, pengumpulan dan perawatannya mahal. Sampah sangat heterogen, terdiri dari campuran berbagai jenis plastik. Sampah plastik yang berbeda membutuhkan pengolahan yang berbeda. Plastik dengan kandungan klorin (Cl) tinggi, seperti polivinilklorida (PVC), perlu dideklorinasi, sehingga menambah biaya persiapan. Senyawa Cl dapat menimbulkan korosi pada lapisan refraktori BF dan saluran pipa di pabrik pembersihan gas (GCP) BF teratas. Kinerja BF sebagian besar ditentukan oleh kualitas dan konsistensi WP, kokas, dan bijih besi.
Kualitas WP seperti PC mempengaruhi kualitas HM, stabilitas dan produktivitas BF, dan komposisi gas BF teratas. Setelah disuntikkan, kinerja pembakaran plastik menjadi penting karena dapat mempengaruhi operasi BF.
Jenis plastik
Plastik biasanya terbuat dari molekul hidrokarbon sederhana (monomer) yang berasal dari minyak atau gas. Ini menjalani polimerisasi untuk membentuk polimer yang lebih kompleks dari mana produk diproduksi. Aditif, seperti antioksidan, pewarna, dan penstabil lainnya, ditambahkan untuk memberikan sifat khusus pada plastik.
Plastik adalah istilah umum yang menggambarkan berbagai bahan dan senyawa. Ada lebih dari 20 kelompok plastik yang berbeda dengan ratusan varietas. Ini dapat diklasifikasikan menjadi dua jenis utama, yaitu (i) termoplastik, dan (ii) termoset. Jenis kedua terdiri dari plastik yang telah dikeraskan dengan proses curing. Setelah diatur, mereka tidak dapat dilunakkan dengan pemanasan dan karenanya tidak cocok untuk injeksi BF. Ini termasuk resin poliuretan, epoksi, dan fenolik.
Jenis utama plastik yang cocok untuk injeksi di BF adalah termoplastik, yang melunak saat dipanaskan dan mengeras saat didinginkan. Ini terdiri dari lima keluarga utama adalah (i) polietilen (PE), yang meliputi polietilen densitas rendah (LDPE) dan polietilen densitas tinggi (HDPE), (ii) polipropilen (PP), (iii) polietilen tereftalat (PET), (iv ) polivinilklorida (PVC), dan (v) polistirena (PS), dalam bentuk PS padat dan polistiren diperluas (EPS).
BF tempat WPI pertama kali dilakukan memanfaatkan plastik dari kemasan dan wadah. BF menyuntikkan WP campuran tetapi ini tidak selalu ditentukan. Salah satu definisi yang umum digunakan adalah WP campuran mencakup semua kemasan plastik non-botol.
WP adalah bahan yang sangat heterogen. Ini sebagian besar terdiri dari polimer hidrokarbon yang mudah terbakar dan aditif. Diperkirakan hanya 3% dari total C yang digunakan sebagai zat pereduksi tetap tidak teroksidasi. Polimer memiliki sifat fisik dan kimia yang berbeda. Komposisi kimia dari gugus polimer utama diberikan pada Tab 1. Injeksi terdiri dari campuran gugus polimer ini (dan, sebagai tambahan, dapat mengandung PVC). Oleh karena itu, tabel tersebut mencakup komposisi khas WP. Untuk tujuan perbandingan, komposisi kimia PC dan injeksi bahan bakar minyak diberikan.
Tab 1 Komposisi kimia umum dari limbah plastik, PC, dan bahan bakar minyak |
Elemen | Satuan | PE | PP | PS | PEliharaan | PVC | Campuran sampah plastik | PC | Bahan bakar minyak |
Karbon | % | 85,60 | 85,75 | 92.16 | 64,71 | 41,40 | 77,80 | 79,60 | 85,90 |
Hidrogen | % | 14,21 | 14.15 | 7.63 | 3,89 | 5.30 | 12.00 | 4,32 | 10,50 |
Belerang | % | | | | | 0,03 | 0,90 | 0,97 | 2.23 |
Abu | % | 0,19 | 0,10 | 0,21 | 0,17 | 0,40 | 4,90 | 9.03 | 0,05 |
Klorin | % | | | | | 47,70 | 1,40 | 0,20 | 0,04 |
Kalium | % | | | | | | 0,05 | 0,27 | 0,001 |
Natrium | % | | | | | | 0,09 | 0,08 | 0,001 |
WP campuran harus memenuhi persyaratan spesifikasi tertentu. Nilai tipikal untuk ini adalah 3% atau kurang kelembaban, 0,4% atau kurang klorida, dan ukuran partikel 8 mm atau kurang. Ada batasan jumlah logam berat dan logam sisa dalam campuran WP, karena ini dapat mempengaruhi kualitas HM. Spesifikasi umum diberikan di Tab 2.
Tab 2 Spesifikasi umum untuk logam berat dan elemen jejak dalam limbah plastik |
Elemen | Satuan | Nilai |
Klorin | % | Kurang dari 2 |
Belerang | % | Kurang dari 0,5 |
Merkurius | gram/ton | Kurang dari 0,5 |
Kadmium | gram/ton | Kurang dari 9 |
Prospek | gram/ton | Kurang dari 250 |
Seng | gram/ton | Kurang dari 1000 |
Tembaga | gram/ton | Kurang dari 1000 |
Arsenik | gram/ton | Kurang dari 5 |
Kromium | gram/ton | Kurang dari 500 |
Nikel | gram/ton | Kurang dari 500 |
Secara keseluruhan, plastik yang digunakan untuk WPI di BF memiliki sifat sebagai berikut.
- WP memiliki rasio H2/C yang tinggi (biasanya lebih tinggi dari batubara). Menyuntikkan plastik meningkatkan jumlah H2 di dalam BF dan di atas gas BF. Peningkatan kandungan H2 gas bosh menurunkan kepadatan gas bosh, dan karenanya mengurangi penurunan tekanan atau memungkinkan aliran gas yang lebih besar untuk tekanan yang sama. Karena reduksi oleh H2 kurang endotermik daripada reduksi langsung, ada penurunan kebutuhan energi. Kemampuan H2 dan uap air (H2O) untuk berdifusi masuk dan keluar dari partikel beban bijih individu secara signifikan lebih tinggi daripada CO dan CO2. Difusibilitas yang lebih tinggi mendorong laju reduksi yang lebih cepat, terutama pada suhu yang lebih rendah. Suhu api adiabatik raceway yang optimal (RAFT) juga lebih rendah karena kandungan H2 yang lebih tinggi di raceway. Namun, konsentrasi H2 yang lebih tinggi di poros BF dapat menyebabkan peningkatan jumlah butiran halus kokas di poros sehingga menurunkan permeabilitas.
- WP memiliki nilai kalori tinggi (CV), dalam banyak kasus lebih besar dari PC. CV khas PE adalah sekitar 11 juta kalori per kilogram (Mcal/kg), PS sekitar 9,7 Mcal/kg, PET sekitar 5,6 Mcal/kg, dan PVC sekitar 4,5 Mcal/kg (walaupun ada banyak variasi antara kaku dan PVC fleksibel). Semakin tinggi CV, semakin besar jumlah panas yang disuplai oleh material, dan karenanya semakin besar pengurangan konsumsi kokas.
- WP memiliki kandungan S dan alkali yang rendah (seringkali lebih rendah dari batubara).
- WP memiliki kadar abu yang rendah jika tidak ada bahan pengisi plastik (biasanya lebih rendah dari batubara tetapi lebih tinggi dari bahan bakar minyak). , sedikit tambahan terak yang dihasilkan. Tapi menyuntikkan WP telah menyebabkan peningkatan penurunan tekanan (penurunan permeabilitas tungku), yang telah dikaitkan dengan komponen abu yang berasal dari WP. Titik leleh yang tinggi (sekitar 1750 derajat C) dari abu berarti tidak mudah membentuk terak.
- WP memiliki kandungan Cl yang tinggi jika ada PVC. Hampir semua klorin meninggalkan BF sebagai asam klorida (HCl), yang dapat menimbulkan korosi pada saluran pipa tempat gas BF bagian atas mengalir. PVC biasanya dihapus dari WP meskipun proses de-klorinasi telah dikembangkan. Kandungan klorin dari campuran WP biasanya dibatasi kurang dari 2%, yaitu sekitar 3% PVC. Kekhawatiran telah diungkapkan tentang kemungkinan pembentukan dioksin dan furan melalui HCl yang dihasilkan, tetapi pengukuran di atas gas BF menunjukkan kandungan yang rendah.
Kekuatan dan kekerasan WP bisa menjadi masalah. Plastik yang diaglomerasi dengan kekuatan rendah mudah pecah selama pengangkutan (yang dapat menyebabkan masalah penyumbatan dan pembakaran dan dengan demikian menurunkan efisiensi pembakaran (CE). Penggunaan WP dalam BF memungkinkan pemulihan tambahan bahan besi yang ada dalam aliran limbah yang kaya plastik. Injeksi 1 kg WP biasanya menggantikan sekitar 1,3 kg PC, dan sekitar 1 kg minyak berat dalam BF. Penggantian kokas oleh WPI dibatasi hingga sekitar 30%, meskipun nilai 40% telah disebutkan. BF membutuhkan injektan yang konsisten kualitas untuk operasi yang stabil. Oleh karena itu, persiapan WP merupakan langkah penting.
Persiapan WP untuk injeksi
Kualitas injektor WP penting tidak hanya dalam hal penggunaannya di BF itu sendiri, tetapi juga dalam persiapan, penanganan dan distribusi bahan ke tungku. Injeksi WP disiapkan dan dikirim ke hopper penyimpanan. Kemudian diangkut secara pneumatik melalui pipa individu atau melalui distributor ke tuyer individu.
Dua persyaratan paling penting untuk keberhasilan penggunaan WP di BF adalah ketersediaan dan biaya pemrosesannya. Limbah seringkali sangat heterogen dan sering bercampur dengan bahan lain. Oleh karena itu, pengumpulan dan pemilahan sampah yang mengandung residu plastik menjadi mahal. Tujuan dari pabrik pengolahan adalah untuk menyediakan bahan baku dengan kualitas yang konsisten dengan ukuran partikel yang diperlukan dan dalam jumlah yang cukup. Tingkat pemrosesan yang diperlukan tergantung pada kondisi di mana limbah tersebut diterima.
Bahan asing seperti logam dan pasir perlu dihilangkan karena dapat menyebabkan masalah, termasuk abrasi pada sistem injeksi dan elemen penggilingan di pabrik, dan kualitas HM yang lebih rendah. Aditif yang ditambahkan ke produk plastik tertentu selama fabrikasi juga dapat menyebabkan masalah abrasi. Sejumlah kecil kertas, batu, dan pasir yang disertakan dengan plastik tidak menimbulkan masalah karena dibuang ke terak BF.
Bahan limbah mengandung berbagai jenis plastik yang memerlukan pemilahan untuk pengolahan terpisah. Ini menambah biaya persiapan. Selain itu, biaya dipengaruhi oleh ukuran partikel yang dibutuhkan, yang mempengaruhi efisiensi pembakaran dan gasifikasi WP. Otomatisasi, jika memungkinkan, dapat membantu menurunkan biaya ini. Sampah yang terkumpul biasanya dipisahkan menjadi dua aliran yaitu (i) plastik padat, yang diparut, kontaminan logam dihilangkan secara magnetis, kemudian dihancurkan menjadi potongan-potongan berukuran 6 mm hingga 10 mm, dan (ii) plastik film yang dipotong-potong. , PVC dihilangkan dengan pemisahan sentrifugal, kemudian dilebur dan diaglomerasi dengan menggunakan panas gesekan untuk membentuk pelet dengan ukuran partikel 6 mm hingga 10 mm.
Dalam hal, WPI termasuk limbah kota maka limbah tersebut diperlakukan dengan cara yang sama (seperti aliran plastik padat dan film). Mungkin diperlukan langkah de-klorinasi. Pelet PVC yang dipisahkan dipanaskan dengan kokas dalam tungku putar di bawah atmosfer nitrogen (N2) hingga sekitar 300 derajat C hingga 350 derajat C, memecahnya menjadi hidrokarbon dan asam HCl. Hidrokarbon dipisahkan dari kokas dan disuntikkan ke dalam BF. Asam HCl yang diperoleh kembali dapat digunakan di dalam pabrik baja atau dijual. Kekuatan plastik yang diaglomerasi, dan sifat mudah terbakarnya, dapat ditingkatkan dengan penambahan kalsium karbonat (CaCO3).
Di Eropa, sebuah proses yang disebut Redop (Pengurangan bijih besi dalam BF oleh plastik dari limbah kota) telah dikembangkan. Bubur dari fraksi plastik campuran (dipisahkan dari limbah kota) dipanaskan dalam reaktor berpengaduk pada suhu 230 derajat C sampai 300 derajat C. Asam HCl yang dilepaskan dinetralkan dengan penambahan basa larut dalam air yang diencerkan. Plastik yang dideklorinasi meleleh menjadi tetesan, yang ukurannya ditentukan oleh pengadukan dan oleh sisa-sisa selulosa yang masih ada. Setelah pendinginan, tetesan plastik memadat menjadi butiran yang memiliki Cl lebih dari 0,15% yang cocok untuk injeksi ke dalam BF.
Sistem injeksi
Sistem injeksi secara pneumatik mengangkut dan mengukur WP dari tempat penyimpanan melalui bejana injeksi, di mana ia diberi tekanan hingga atau di atas tekanan BF, ke tombak injeksi tuyere. Tombak menyuntikkan WP dalam jumlah yang sama melalui tuyeres, yang disusun secara simetris di sekitar keliling BF. Faktor penting dalam desain sistem distribusi adalah untuk memastikan umpan reduktor yang seragam ke setiap tuyere tanpa fluktuasi dalam rute pengiriman WP. Setiap gangguan dalam pasokan WP dapat dengan cepat menyebabkan masalah serius. Semakin tinggi tingkat injeksi, semakin serius konsekuensi dari gangguan yang tidak direncanakan.
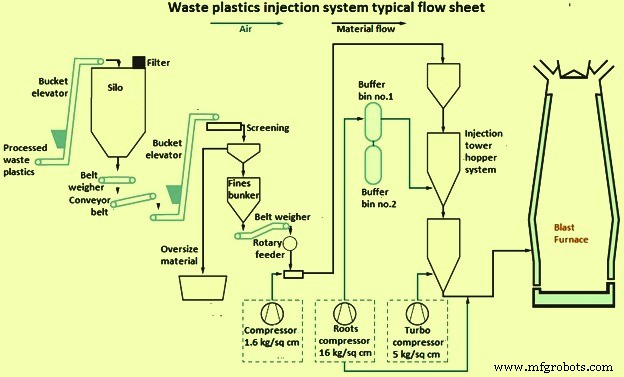
Gbr 1 Flow sheet tipikal untuk sistem injeksi WP
Jika WP disuntikkan bersama dengan PC maka dapat diangkut (i) melalui sistem injeksi dan tombak yang benar-benar terpisah, (ii) melalui sistem injeksi terpisah ke tombak biasa, dan (iii) sebagai campuran. Dalam kebanyakan kasus, batubara dan WP diangkut secara terpisah karena ukuran partikelnya yang berbeda (batubara dihaluskan sementara WP berada dalam kisaran ukuran 1 mm hingga 10 mm) dan densitasnya.
Setidaknya dua kapal injeksi diperlukan untuk memberikan aliran WP terus menerus ke BF. Pada dasarnya, ada dua pengaturan berikut dari kapal-kapal ini.
- Pengaturan serial di mana bejana atas secara berkala mengisi kembali bejana bawah, yang selalu dijaga di bawah tekanan, dan yang menyuntikkan WP terus menerus ke dalam BF. Oleh karena itu, bejana injeksi terus ditimbang dan laju aliran WP dikontrol dengan hati-hati. Pengotoran tempat sampah oleh bulu plastik dapat terjadi.
- Pengaturan di mana kedua pembuluh disuntikkan secara bergantian. Operasi yang tumpang tindih diperlukan untuk mempertahankan injeksi WP selama periode pergantian.
WP dari kapal injeksi dapat diangkut (i) dengan pipa individu ke setiap tuyere dengan jumlah WP dikontrol secara independen, dan diisi di setiap pipa, dan (ii) oleh pipa umum ke distributor yang berdekatan dengan BF yang kemudian membagi WP secara merata ke dalam pipa individu yang mengarah ke setiap tuyere. Keuntungan dari metode kedua adalah jarak antara instalasi preparasi dan BF dapat lebih panjang dibandingkan dengan sistem pipa individu. Perbedaan dalam perutean pipa ke tuyere dan pemisahan WP yang tidak merata yang tak terhindarkan pada titik pemisahan dapat mengakibatkan pengumpanan yang tidak merata ke tuyer. Ketidakseimbangan juga dapat menyebabkan keausan yang tidak merata pada pipa dan distributor.
Tergantung pada rasio WP untuk menyampaikan gas, WP diangkut secara pneumatik dari bejana injeksi ke tuyeres baik dalam (i) fase encer, atau (ii) fase padat. Gas pembawa untuk WP biasanya udara terkompresi. Kecepatan gas untuk WP dalam sistem fase padat adalah 3 meter per detik (m/s) hingga 8 m/s. Beberapa pabrik menggunakan pengangkutan fase encer untuk pelet plastik (hingga 10 mm).
Kecepatan gas pembawa selalu lebih tinggi dari kecepatan transportasi minimum untuk mencegah penyumbatan. Kecepatan minimum ini tergantung pada sejumlah parameter termasuk tekanan sistem dan diameter pipa, dan variabel-variabel ini berinteraksi satu sama lain. Kecepatan rendah dalam sistem fase padat berarti pipa rendah dan keausan komponen, sedangkan kecepatan tinggi sistem fase encer dapat menyebabkan keausan, terutama pada tikungan pipa. Tingkat keausan ditentukan oleh kekerasan, bentuk dan kecepatan partikel. Aglomerat plastik memiliki bentuk partikel yang tidak beraturan yang dapat menyebabkan erosi, sedangkan butiran plastik yang diekstrusi memiliki bentuk yang teratur. Partikel plastik yang dihancurkan lebih keras daripada pelet yang diaglomerasi. Melapisi bagian pipa yang rentan terhadap erosi dengan, misalnya, bahan elastomer uretan akan memberikan ketahanan abrasi, serta memperlambat penumpukan butiran halus yang dapat menyebabkan penyumbatan.
Sifat WP yang terkait dengan penyumbatan saluran transfer meliputi (i) kadar air yang perlu dikontrol untuk mencegah penyumbatan, dan (ii) keberadaan partikel ultrafine. Distribusi ukuran partikel dari plastik campuran yang diaglomerasi adalah penting. Proporsi partikel berukuran kurang dari 250 mikro meter (mikron) harus dibatasi hingga 1% bila spesifikasi ukuran partikel adalah 0 mm sampai 10 mm dan butiran diangkut dalam fase encer. Juga, untuk injeksi yang stabil, penting bahwa sekitar 50% dari plastik yang disuntikkan memiliki ukuran partikel atas 6 mm. Penggunaan partikel plastik berserat sulit dilakukan karena serat menggumpal membentuk partikel yang lebih besar yang menghalangi pipa. Bulu plastik juga bisa membuat pipa macet. Partikel plastik dapat menjadi bermuatan listrik statis selama pengangkutannya melalui pipa yang menyebabkannya menempel pada dinding. Dalam kasus yang parah, pipa mungkin tersumbat, terutama di tikungan. Penambahan bahan berbutir halus yang mengalir bebas dapat mempengaruhi efeknya.
Penyumbatan dapat dikurangi dengan perbaikan tata letak pipa dan sistem distribusi. Sistem injeksi memiliki metode untuk mendeteksi dan membersihkan penyumbatan. Jalur transfer termasuk port pembersihan di mana penyumbatan dibersihkan, biasanya dengan udara bertekanan tinggi. Sebuah tes sederhana dan praktis diperlukan untuk menilai flowability dan handleability WP. Hal ini memungkinkan materi yang bermasalah untuk diidentifikasi sebelum digunakan.
Tombak injeksi menyuntikkan WP ke dalam sumpitan yang mengarah ke tuyere. Partikel segera dipanaskan oleh ledakan panas, dinyalakan, digasifikasi dan dibakar. Desain dan penempatan tombak mempengaruhi CE dari WP. Masalah penyumbatan tombak dan tuyere serta pencairan ujung tombak dapat terjadi. Penyumbatan sebagian besar disebabkan oleh WP yang dipanaskan hingga suhu di mana mereka menjadi lengket dan menempel pada permukaan tombak dan tuyer injeksi. Ada prosedur yang ditetapkan untuk mendeteksi dan membersihkan penyumbatan ini sebelum dapat menyebabkan masalah.
Pembakaran
Raceways adalah daerah vital dari BF meskipun volume totalnya biasanya tidak melebihi 1% dari volume bagian dalam BF. Mereka memasok proses dengan panas dan zat pereduksi. Injeksi WP mempengaruhi kondisi raceway yang, pada gilirannya, memiliki konsekuensi di luar raceway. Partikel yang tidak terbakar meninggalkan raceway dapat menyebabkan masalah operasional seperti penurunan permeabilitas, distribusi gas dan suhu yang tidak diinginkan, erosi kokas yang berlebihan, dan peningkatan sisa arang. Jumlah arang yang tidak terbakar meningkat dengan meningkatnya laju injeksi. Jadi, perilaku pembakaran dan gasifikasi dari plastik yang diinjeksi di raceway merupakan faktor penting untuk operasi tungku yang stabil. Perilaku pembakaran sampah plastik ditunjukkan pada Gambar 2.
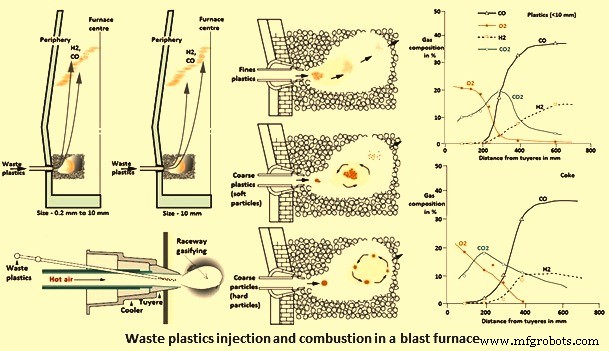
Gbr 2 Perilaku pembakaran WP di BF
Jelas bahwa BF dapat mengkonsumsi lebih banyak WP yang disuntikkan daripada yang dibakar di dalam raceway karena bahan yang tidak terbakar dikonsumsi di tempat lain di BF. Pembakaran plastik mengikuti jalur yang mirip dengan PC kecuali bahwa beberapa jenis plastik terurai secara termal menjadi cairan yang mudah terbakar dan gas yang mudah menguap. Lebih sedikit arang yang terbentuk dari plastik yang memiliki kadar abu lebih rendah daripada batu bara. Oleh karena itu, pembakaran gas bisa lebih penting daripada pembakaran arang. Partikel plastik memiliki konduktivitas termal yang rendah dan karenanya perpindahan panas di raceway tinggi. Perilaku pembakaran tergantung pada jenis plastik, sifat-sifatnya (seperti kekerasan/kepadatan) dan ukurannya. Partikel yang lebih besar memiliki waktu tinggal yang lebih lama di raceway misalnya sekitar 4 detik hingga 6 detik untuk partikel berukuran 7 mm.
Ini adalah karakteristik pembakaran WP daripada pembakaran kokas yang mengatur komposisi gas dan distribusi suhu di raceway karena mereka lebih disukai dibakar. Gambar 2 menunjukkan bagaimana komposisi gas (termasuk H2) bervariasi dalam simulasi (model panas) raceway ketika limbah plastik disuntikkan. Sebagai perbandingan, Gambar 2 mencakup komposisi gas untuk semua operasi kokas ketika hanya meniupkan udara panas melalui tuyere.
Tingkat pembakaran (CE), dan karenanya jumlah bahan yang tidak terbakar diangkut keluar dari raceway, tergantung pada beberapa faktor yang meliputi (i) sifat WP, seperti konten volatile matter (VM), ukuran partikel, dan densitas, dan (ii) kondisi operasi, misalnya, komposisi dan suhu gas BF, serta posisi dan desain lance. Perilaku pembakaran dan gasifikasi sampah plastik di raceway dipengaruhi oleh sifatnya.
Jenis plastik bervariasi dalam komposisi, struktur dan derajat keteraturan (kristalinitas). Misalnya, struktur PP, PS dan PVC berbeda dari PE karena masing-masing mengandung metil (CH3), benzena dan Cl, sebagai unit berulang. PE terdiri dari rantai panjang hidrokarbon alifatik yang terbuat dari monomer etilen. Baik HDPE dan LDPE pada dasarnya memiliki struktur molekul yang sama kecuali percabangan rantai yang bertanggung jawab atas perbedaan densitas. Dengan demikian, perilaku dekomposisi termal dari berbagai konstituen WP berbeda. Dekomposisi termal PE, sebagai contoh, menghasilkan pelepasan H2 yang lebih besar dibandingkan dengan CO.
Menyuntikkan plastik menurunkan RAFT karena mendorong reaksi endotermik. WPI memiliki efek pendinginan yang lebih kuat daripada PCI, dan efeknya tergantung pada jenis plastiknya. Poly butylene terephthalate (PBT) memiliki efek pendinginan yang lebih tinggi dari PE yang, pada gilirannya, lebih besar dari PS. Laju injeksi 100 kg untuk plastik kelas rendah dan hingga 170 kg untuk PS secara teoritis dimungkinkan di bawah kondisi tuyere konstan tanpa menimbulkan penurunan suhu nyala hingga di bawah 2000 derajat C (Gbr 3). Peningkatan suhu ledakan dan/atau pengayaan O2, dan/atau penurunan kelembaban ledakan dapat mengimbangi efek pendinginan WP.
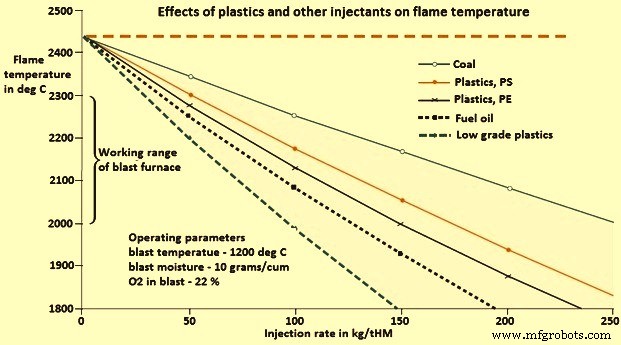
Gbr 3 Efek plastik dan injektor lain pada suhu nyala
Studi analisis gravimetri termal (TGA) telah menunjukkan bahwa perilaku pirolisis PS, PP, PBT, LDPE dan HDPE serupa, dengan kehilangan berat hidrokarbon yang cepat terjadi dalam kisaran suhu yang sempit sekitar 80 derajat C hingga 100 derajat C. pirolisis PS dimulai dan berakhir sebelum PP yang, pada gilirannya, dimulai dan diakhiri sebelum PE. Perilaku degradasi termal PVC lebih kompleks. Pertama benzena (C6H6) dan kemudian Cl dilepaskan, diikuti oleh degradasi sisa hidrokarbon yang terjadi pada suhu yang sama dengan plastik lainnya. Selain itu, PVC menghasilkan fraksi arang, tidak seperti plastik lainnya. Ini memiliki struktur yang lebih kompleks. Secara umum, PE (dan beberapa jenis plastik lainnya) terurai secara termal menjadi cairan yang mudah terbakar dan gas yang mudah menguap.
Beberapa penelitian menunjukkan bahwa PVC menghasilkan arang tidak seperti LDPE, HDPE, PP dan PS (tanpa zat pewarna). Yang tidak berwarna tidak menghasilkan residu padat setelah pirolisis, menghasilkan jelaga dalam jumlah besar. Selain itu, PVC juga menghasilkan jelaga yang banyak diikuti oleh PS, PP, dan PE. PVC juga menunjukkan pengapian yang lebih cepat dan waktu pirolisis dan pembakaran yang lebih pendek daripada PE, PP, dan PS yang berukuran sama. Pengapian yang lebih cepat dikaitkan dengan 'energi aktivasi untuk degradasi termal' PVC yang lebih rendah (20 kkal/mol hingga 33,5 kkal/mol untuk PVC dibandingkan dengan 48 kkal/mol hingga 72 kkal/mol untuk plastik lainnya). Perbedaan perilaku pirolisis antara berbagai plastik juga disebabkan oleh perbedaan struktur kimianya yang dapat mengubah reaktivitasnya. Reaktivitas PS lebih besar daripada reaktivitas PP yang selanjutnya lebih tinggi dari LDPE dan HDPE.
Performa pembakaran WP dipengaruhi oleh ukuran partikelnya. Untuk konversi lengkap, dan dengan demikian pemanfaatan WP yang efektif, pemanasan, devolatilisasi, pirolisis, dan pembakaran partikel dilakukan antara masuknya partikel ke ledakan panas dan batas raceway.
Perilaku pembakaran WP yang berbeda bervariasi. PE secara teratur digunakan sebagai bahan pengganti untuk menyelidiki WPI di BF karena kelimpahan turunannya di WP. Temperatur penyalaan PE meningkat dengan bertambahnya ukuran partikel (360 derajat C dengan 3 mm hingga 5 mm dibandingkan dengan 380 derajat C dengan ukuran partikel 6 mm hingga 10 mm) saat dibakar di udara. Hal ini dikaitkan dengan luas permukaan kontak yang lebih besar dari partikel halus ke O2. Oleh karena itu, partikel plastik yang lebih halus diharapkan memiliki CE yang lebih tinggi daripada yang lebih kasar.
Analisis konsentrasi CO2 dalam gas yang dihasilkan (sering digunakan sebagai ukuran CE) menunjukkan bahwa partikel PE yang lebih besar mengalami pembakaran lebih jauh dari tuyer, dan karenanya membutuhkan waktu lebih lama untuk terbakar dalam BF daripada yang lebih halus. Ini adalah karena konduktivitas termal yang rendah dari plastik. Analisis juga menunjukkan bahwa selain memiliki temperatur penyalaan yang lebih rendah, PE memiliki waktu pembakaran yang lebih singkat dan laju pembakaran yang lebih tinggi dibandingkan dengan batubara dengan ukuran partikel 0,6 mm sampai 0,7 mm. Ini karena PE terurai menjadi gas yang mudah terbakar pada suhu tinggi. Pembakaran gas pirolisis dengan O2 merupakan reaksi gas-gas yang merupakan reaksi yang lebih cepat.
Sebuah studi dengan pembakaran PE dan campuran WP dalam tungku listrik di bawah aliran udara panas dan pengukuran kandungan CO dan CO2 dari gas yang dihasilkan, telah menunjukkan bahwa laju pembakaran partikel yang lebih kecil dari kedua bahan lebih cepat daripada partikel yang lebih besar pada 1200 derajat C, tetapi pada 1250 derajat C, ukuran partikel memiliki pengaruh yang kecil pada proses pembakaran. Seperti yang diharapkan, CE (disebut rasio pembakaran dan didefinisikan sebagai rasio kandungan C dengan kandungan C asli) dari partikel dengan ukuran yang sama lebih baik pada suhu yang lebih tinggi. Partikel yang lebih kecil memiliki CE yang lebih tinggi selama 200 detik awal hingga 600 detik, tetapi setelah periode ini CE terbalik di mana partikel yang lebih besar memiliki CE yang lebih tinggi.
Penambahan CaCO3 meningkatkan kekuatan plastik yang diaglomerasi, memungkinkan partikel bersirkulasi lebih lama di dalam raceway. Ini juga menurunkan titik leleh terak yang terbentuk, sehingga mengurangi penurunan tekanan di tungku yang disebabkan oleh penurunan permeabilitas.
Sebuah studi dilakukan di Jerman untuk perilaku pembakaran WP dengan komposisi yang sama (76% C, 10% H2, 8% O2, dan 5% abu) dan ukuran partikel (3 mm hingga 6 mm) tetapi disiapkan dengan cara yang berbeda. . Tiga jenis plastik dipelajari. Mereka adalah aglomerat (fraksi setelah penghancuran dan penghilangan zat yang tidak diinginkan), granulasi (setelah peleburan pada 100 derajat C) dan granulasi ulang (setelah pengepresan tambahan, memiliki kepadatan tertinggi). Plastik yang diaglomerasi (dihancurkan) memiliki CE tertinggi karena luas permukaannya yang lebih besar dan kepadatan terendah, diikuti oleh granulasi dan kemudian granulasi ulang. CE dari ketiga jenis plastik rendah karena partikel besar tidak dapat terbakar sepenuhnya dalam waktu tinggal yang tersedia.
Penggunaan WP yang efektif memerlukan perubahan operasional untuk mengkompensasi perubahan parameter raceway dan efeknya di tempat lain di BF (seperti keadaan termal, rezim terak, dan dinamika gas). Penyuntikan WP hingga 10 kg/tHM diperkirakan tidak akan mengganggu operasi BF. Measures to intensify the combustion of WP in the tuyere/raceway region, and hence increase injectant rates, include (i) increase of the amount of O2 in the tuyeres, and (ii) adjustment of the blast temperature and moisture.
Oxygen can be added to the tuyere by (i) enrichment of the hot air blast, (ii) injection through the WP lances, and (iii) separate O2 lances. The addition of O2 means more O2 is available for the participation in the combustion of WP in the raceway. Thus the CE increases. However, the influence of O2 enrichment on the CE is limited.
Oxygen enrichment of the hot air blast produces both a reduction in bosh gas flow and a rise in flame temperature. The former effect can help counteract the increase in burden resistance (lower permeability) and the pressure drop associated with high injection rates. The latter effect can help compensate for the cooling effect of the decomposition of the WP volatiles. The CO and H2 contents also increase with O2 enrichment, resulting in improved reduction of the iron ores in the central shaft. The CV of the top BF gas normally improves with the O2 enrichment. The lower limit of O2 enrichment is generally determined by the amount needed to maintain the required RAFT, with more O2 required as the volatile content of the WP increases. If the flame temperature becomes too high, then burden descent can become erratic. Too low a flame temperature hinders WP combustion and melting of the ore burden. The upper limit is dependent on maintaining a sufficient top gas temperature. As O2 is increased, the gas mass flow within the BF decreases, which decreases the heat flow to the upper region of the BF for drying the burden. The upper limit of the top gas temperature may also be governed by the need to protect the top gas equipment. Other limitations to O2 enrichment include its cost and availability.
The key measure for combustion at high injectant rates is a high blast temperature. O2 enrichment plays a more important role as a means of controlling gas flow in the BF rather than controlling the WP combustion. Generally, a higher hot blast temperature is an inexpensive measure than O2 enrichment since it allows a lower O2 consumption. Increased blast temperatures also reduce coke consumption. WP has a stronger cooling effect on flame temperature than coal.
Although increasing the blast temperature raises the RAFT with waste PE injection, it has been found in a study that regardless of the blast temperature (900 deg C, 1000 deg C, and 1100 deg C) and O2 enrichment (0.7 % and 1.2 %), the maximum RAFT which can be achieved is around 1950 deg C. This suggests that blast temperature and O2 enrichment only affect the combustion kinetics (rates), and not the thermodynamics, as long as the plastic particles start burning, the maximum temperature related to the enthalpy of combustion remains constant.
Lowering blast moisture can help to compensate for the cooling effects of WPI. If the RAFT becomes excessive, then blast moisture can be increased. Raising hot blast moisture means more H2 in the bosh gas for iron ore reduction. The optimum RAFT in the BFs operating with higher H2 contents can be lower than those operating with lower H2. In addition, the blast velocity can be adjusted to not only improve waste plastics combustion, but to maintain the required length of the raceway zone which is critical for obtaining good conditions in the hearth.
Unburnt char
With the increase of the injection rate, the combustibility of WP has a tendency to decrease resulting in unburnt material (char, fines and fly ash) leaving the raceway. Some of this material, along with coke debris, accumulates at the back of the raceway, in the bird’s nest, hampering the rising gas flow and entrained solids in this area. The majority are swept upwards where they can accumulate under the cohesive zone, decreasing permeability and hence BF productivity. Changes in the lower BF zone permeability can also affect the HM quality and slag viscosity.
The unburnt material tends to accumulate at positions where large changes in gas flow occur. Finally it is entrained into the gas flow, passing through the cohesive zone coke slits, and up the BF shaft, where it can influence burden permeability, and is finally released with the top BF gas. Higher WP injection rates also increase the volume of combustion gases, and hence the gas flow, and change the heat load in the lower part of the BF. In addition, more slag is produced.
The deposition of unburnt fine material is a complex phenomenon consisting of several generation mechanisms, reactions, multiphase flow, accumulation and re-entrainment. Different gas flow models have been developed to understand and predict the behaviour of fine material within the BF. With suitable burden charging patterns (such as central coke charging) and the use of stronger coke many of the problems relating to gas flow have been solved.
The experience has shown that most of the unburnt char is consumed within the BF. The three mechanisms for this are (i) gasification with CO2 and H2O, (ii) reaction with liquid iron (carburization), and (iii) reaction with slag. It is advantageous if the unburnt char participates in the ore reduction reactions, thus replacing more of the coke and lowering the amount of unburnt solids in the top BF gas.
The reaction of chars with CO2 and H2O begins in the raceway, but since the residence time for fine particles is very short for appreciable reaction, gasification mainly occurs in the BF shaft. The reactions of char C with CO2 (Boudouard reaction) and H2O are slower than char combustion. The chars resulting from WP and coke compete with each other for CO2 and H2O. Chars from WP are more reactive than those from coke and thus are preferentially gasified. Thus coke degradation by the Boudouard reaction decreases with increasing WPI rates.
It has been reported that the CO2 gasification rate of char from agglomerated WP (particle diameter 400 micron to 500 micron) is around 10 times higher compared to the PC char (50 micron), despite its larger size. The rates have been determined using a thermo-balance. The CO2 gasification rate of PVC char is also slightly higher than PC char. It has also been reported that the reaction rate of unburnt char from WP (300 micron to 400 micron) is around half that of PC char (50 microns). Though WP char has a longer residence time in the packed coke bed due to its larger size, it has a small gasification rate due to its fairly small specific surface area. Hence, it can accumulate in the lower part of the BF, decreasing permeability, unless CE in the raceway is high.
The reactivity of C in the unburnt char to CO2 and H2O is dependent not only on its surface area (particle size) but also on its structure and composition, as well as operating conditions. Also, since the residence time for particles at high temperatures is too short in a BF, char gasification mainly occurs at decreasing temperatures in the furnace shaft. The properties of char change as it moves up the BF, and hence its reactivity to CO2 and H2O. The reacting atmosphere is not uniform, for example, the concentrations of CO, CO2, H2 and H2O vary at different locations within the BF. Normally higher H2 and CO concentrations are found at the periphery compared to the centre of the BF for waste plastics with a particle size of 0.2 mm to 1 mm but the reverse takes place with the injection of larger particles size (less than 10 mm).
Injection of WP increases the bosh gas H2 concentration. Since the chemical reaction rate of H2 reduction is higher than that of CO, the extent of Boudouard reaction reduces as bosh gas H2 increases. CO2 and H2O are present in the upper part of the BF due to the reduction of iron oxides. Under the conditions here, char gasification by CO2 is likely to be controlled by the rate of the chemical reactions. In the lower part of the BF, char gasification is partly diffusion controlled. Hence the overall reaction rate of char gasification is likely to be influenced by the chemical reactivity of char to CO2 in this region. Char reactivity towards CO2 is influenced by its chemical structure, with less ordered structures being more reactive. The char structure from agglomerated WP has an isotropic texture with high CO2 reactivity.
The presence of certain minerals in the char ash, such as Fe and alkalis, can catalyze the CO2 gasification reaction, whereas other minerals, such as silica (SiO2) and alumina (Al2O3), can slow down the reaction. Depending on its composition, ash can also retard the C conversion due to the blockage of char particles as a result of increased proportion of slag formation in the char particle. In the lower part of the BF, condensed alkalis from the recirculating gases can have a catalytic effect. The loss of C by gasification increases the char ash content. In general, WP has a lower ash (mineral) content than PC and thus are more likely to be consumed within the BF.
Carburization of the HM begins in the solid phase within the cohesive zone of the BF, and continues during descent of the metal droplets through the active coke, deadman and hearth zones. Unburnt char and fine material leaving the raceway can contact the dripping liquid metal in the bosh and hearth zones. C and other elements, such as Fe, Si and S, dissolve from the char into the liquid Fe influencing the composition of the HM. The dissolution of C contributes to the carburization of liquid Fe, and commands the level of char consumption by the HM. It is critical where CE is low. If the HM is close to saturation when it reaches the areas of deadman and hearth, the unburnt material cannot be consumed, thus diminishing permeability in these regions. The C comes from unburnt WP materials, as well as coke.
Carbon dissolution from unburnt char into liquid metal is influenced by the operating conditions and the following factors.
- Char particle size – Unburnt chars which maintain their original form react very little with the liquid Fe and slag as they cannot penetrate into the liquids. However, if they are agglomerated into larger particles or captured by the larger pieces of coke, then they behave like bosh coke and carburize the metal up to saturation.
- Char structure – Generally, the rate of dissolution improves as the C structure becomes more ordered.
- Char mineral matter – In general, SiO2, Al2O3, and magnesia (MgO) slow the C dissolution kinetics, while calcium fluoride (CaF2) and Fe oxides enhance the rate. The effect of lime (CaO) is less clear. The reaction of calcium (Ca) with S in the metal produces a CaS (calcium sulphide) layer which hinder C transfer. The ash fusion temperature (AFT) is also one of the controlling mechanisms which limit C dissolution. The formation of an ash layer on the carbonaceous material reduces the surface area available for dissolution, hence retarding C dissolution rates. Low AFT allows easy removal of the ash, in the form of liquid slag. This results in constant exposure of fresh C surface to the HM, permitting the mass transfer of C to the liquid iron.
- Liquid metal composition – It changes over time. The C dissolution rate typically decreases as the C content of the liquid metal increases. Higher S content also retards C dissolution. Combustion of WP and coke releases sulphur oxides (SOx) which can react with the descending liquid metal and slag. This is less of a problem with WP since they typically have a lower S content than coal and coke.
Unburnt char, ash, fines, and coke can interact with the dripping liquid slag. The slag composition changes as it moves down the BF, with the Fe oxide concentration being continuously lowered as it is reduced. The reactions at the interface between the solid char and liquid slag play a major role in char consumption since they influence the kinetics of the reduction reactions and the contact area between the slag and char available for reaction.
Factors influencing unburnt char interactions with the slag include the slag composition, char C content, and char ash content and composition, as well as the operating conditions. Basically, char consumption by slags occurs through the following.
- Reduction of the Fe oxides in slags by C in the char – The wetting characteristics have a significant effect on the dominant reduction mechanism taking place. The wetting characteristics of slags vary with slag composition, temperature, time, and carbonaceous material. Wetting varies as a function of time since the reduction of Fe oxide in the slag by char, and the dissolution of the char ash components into the slag, results in continuous variations in the slag and char compositions. An increase in temperature normally results in improved wettability at the slag/C interface. Reduction rate usually increases with increasing slag FeO (2 % to 10 %) content and with increasing reaction temperature (1300 deg C to 1600 deg C).
- Reduction of SiO2 in slag by C of char – This is a function of temperature. At temperatures less than 1500 deg C, only reduction of Fe oxide occurs. At higher temperatures, both SiO2 and Fe oxides in the slag are reduced, resulting in increased consumption of the char. SiO2 is reduced by C, via gaseous SiO, to Si or silicon carbide (SiC). Self-reduction of SiO2 in the char ash by C can also occur, resulting in further consumption of the char. The reduction kinetics of SiO2 is influenced by the wettability of chars by the slags. Wetting behaviour improves with an increase in slag SiO2 content, and with an increase in temperature (1500 deg C to 1700 deg C). Higher amounts of SiO2 and Fe oxides in the char ash facilitate the slag/C interactions, leading to improved consumption of these oxides through reduction reactions.
- Interaction between components in the slag and char – This interaction leads to the assimilation of char ash components such as S.
In addition, the reduction of MgO in slag by char C can lead to further consumption. Self-reduction of the oxides in the char ash by C can also contribute to char consumption.
The presence of unburnt char in the slag can interfere with tapping by increasing slag viscosity, while assimilation of char normally increases the fluidity of the bosh slag. Changes in slag mobility can affect the position and shape of the fluid and cohesive zones. A high viscosity slag around the tuyeres also leads to serious gas flow problems. Slag viscosity is a complex function of slag composition, temperature and O2 partial pressure. As well as unburnt char and coke, unburnt ash from WP can interact with the slag. All of these carbonaceous materials contribute oxides to the slag. In general, higher amounts of SiO2 or Al2O3 (acidic components) increase slag viscosity, whereas a higher basicity (higher CaO or MgO) lowers slag viscosity because of de-polymerization of the silicate network. Slag viscosity decreases with increasing FeO (0 % to 20 %) content at a fixed basicity. Basicity is generally determined by the CaO/SiO2 ratio. Since the slags do not fully assimilate the char and ash in the bosh region, bosh slag normally has a higher basicity than tapped slag. The addition of fluxes can help solve slag formation problems.