Pembentukan Scaffold di Blast Furnace Shaft
Pembentukan Scaffold di Blast Furnace Shaft
Istilah scaffold digunakan bila terjadi akresi atau pembentukan keropeng pada dinding blast furnace (BF) yang menyebabkan penurunan luas penampang poros BF. Scaffold dapat terjadi relatif pada tingkat yang lebih tinggi dari poros BF atau relatif rendah pada poros BF (dekat bagian atas bosh). Sulit untuk menggeneralisasi jenis perancah karena sangat sedikit kesamaan antara struktur dan lokasi perancah dari BF yang berbeda. Namun, perancah umumnya dapat diatur dalam dua kelompok. Kelompok-kelompok ini adalah (i) perancah laminasi, dan (ii) perancah non-laminasi. Perancah dengan struktur laminasi terdiri dari lapisan alternatif besi logam (Fe) dan beban kaya alkali. Formasi khas dari perancah besar di BF ditunjukkan pada Gambar 1.
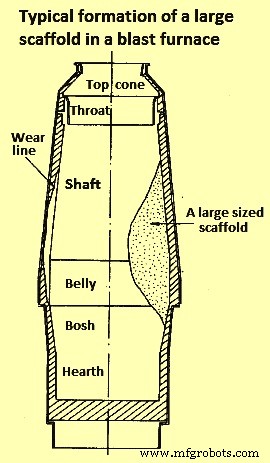
Gbr 1 Formasi tipikal perancah besar di BF
Perancah dapat menyebabkan gantung di BF. Menggantung terjadi ketika beban dalam perjalanannya bertemu dengan hambatan yang sangat tinggi yang mengakibatkan terhentinya pergerakan beban. Gantungan tersebut dapat pecah, kemudian material tersebut jatuh karena adanya celah yang telah dibuat di bawah gantung tersebut. Setelah pecah, saat terjadi slip, biasanya material dalam jumlah besar jatuh dan mengakibatkan kerja BF yang tidak teratur yang mengakibatkan distribusi gas tidak seragam dengan implikasinya pada parameter BF.
Prasyarat untuk pembentukan perancah yang stabil dan berbahaya adalah (i) adanya bahan yang sesuai dalam beban BF untuk membangun perancah (misalnya butiran halus, beban yang disaring dengan buruk, sinter dengan karakteristik degradasi reduksi suhu rendah yang rendah, penggunaan penyimpanan lama, sinter basah dan dingin , atau kokas ukuran kecil dll.), (ii) adanya bahan aglomerasi (penyemenan) untuk aglomerasi bahan beban, (iii) adanya mekanisme pengikat (anchoring) untuk membangun perancah pada dinding poros BF yang dapat berupa ikatan kimia dengan bahan pelapis, penahan fisik di sekitar pelat pendingin, bangunan lengkung ke arah dinding bosh, atau hanya kondensasi dari bahan yang menggumpal di dinding, (iv) pasokan kontinu yang terjadi pada komponen yang menempel, dan (v ) perancah yang dibentuk cukup kuat untuk menahan gaya aus material yang turun.
Tempat di mana perancah berada tergantung pada bahan aglomerasi, bahan perekat, bahan beban, operasi tungku, dan fitur konstruksi tungku seperti elemen pendingin dan bahan pelapis. Itu dapat ditemukan di berbagai level di BF seperti poros, bosh, atau perutmu. Gambar 2 memberikan beberapa tampilan perancah dalam BF.
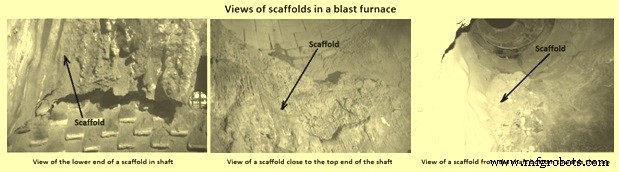
Gbr 2 Tampilan perancah dalam BF
Komposisi kimia khas dari akar dan kerak keras sampel perancah dari beberapa BF Eropa diberikan di Tab 1.
Tab1 Analisis tipikal perancah sampel dari BF Eropa |
Nomor Sl. | Komposisi | Akar perancah | Kerak keras dari perancah |
Contoh 1 | Contoh 2 | |
% | % | % |
1 | C | 4,24 | 1,59 | 8.4 |
2 | Fe (total) | 56 | 33 | 42,6 |
3 | SiO2 | 5.4 | 21 | 5.9 |
4 | Al2O3 | 9.51 | 5.16 | 1,26 |
5 | CaO | 11.9 | 20.6 | 5.35 |
6 | MgO | 4,95 | 6.08 | 1,91 |
7 | ZnO | 0,002 | TID | 23.3 |
8 | PbO | 0 | TID | 0,26 |
9 | K2O | 0,86 | 1,57 | 3.1 |
10 | Na2O | 0,36 | 0,76 | 1,3 |
11 | S | 4.2 | 0,05 | 0,20 |
Perancah di bagian dada dan perut
Dalam BF yang ideal, penumpukan dan pengelupasan perancah terjadi terus menerus sehingga tidak ada variasi besar dalam kerugian pendinginan atau kimia terak yang diamati. Pada BF yang lebih tua dengan pelat pendingin dan lapisan keramik, keseimbangan ini sulit dicapai terutama ketika lapisan telah terkikis. Dalam BF baru-baru ini dengan lapisan grafit plat stave atau tembaga, ada urutan perancah yang menumpuk dan terkelupas secara bergantian. Pengupasan perancah biasanya dilakukan dua kali atau lebih dalam seminggu.
Perancah terdiri dari angin kokas, komponen bijih tereduksi, terak, komponen debu seperti jelaga, dan alkali terkondensasi dll. Perancah jenis ini rapuh dan mudah terkelupas. Jika perancah jenis ini bertahan lebih lama di dinding bosh, terutama saat menutupi keliling bosh, perancah tersebut stabil secara mekanis dan bertambah kuat seiring waktu. Oksida besi direduksi menjadi logam Fe, disinter bersama dan dikarbonisasi. Karbon kokas (C) digasifikasi dengan reaksi kehilangan larutan yang meninggalkan ruang untuk debu dan bahan yang mengembun, mis. kalium oksida (K2O). Ketika perancah telah tinggal untuk waktu yang lebih lama pada suhu yang lebih tinggi di bosh perancah itu kompak dan sebagian besar mengandung Fe dan terak. Semakin lama perancah tetap, semakin besar dimensinya dan risiko gangguan serius meningkat.
Pembentukan perancah yang khas terjadi karena alasan dan langkah-langkah yang terdiri dari (i) ada banyak butiran halus dan sinter yang disaring dengan buruk dengan karakteristik degradasi penurunan suhu rendah yang rendah, (ii) Bahan halus dipisahkan ke dinding sisi di mana aliran gas lemah, suhu rendah dan laju reduksi lambat, (iii) akar zona kohesif terletak rendah di bosh dan dapat juga beban campuran, (iv) penurunan normal beban berhenti karena untuk penghentian gantung atau pemeliharaan, (v) penyusutan sinter berlanjut karena pengurangannya, (vi) bahan yang melunak atau setengah cair menempel pada elemen pendingin dan mengeras, (vii) ketika beban mulai turun lagi (penggantungan slip atau tungku dinyalakan kembali setelah berhenti), bahan yang menempel ini tetap pada tempatnya, (viii) senyawa seng (Zn) dan alkali mengembun dari gas dalam bahan yang tergenang menggumpal halus bersama-sama, (ix) pembentukan akar dari perancah lipatan, (x) pada permukaan lapisan material yang tergenang, ke arah beban, kondensasi senyawa aglomerasi dan debu terus membangun kerak keras dari komponen Fe, ZnO (seng oksida), K2O, dan terak, (xi) lanjutan pertumbuhan ke atas dan sedikit ke arah pusat tungku. Jika perancah semacam ini dibiarkan tumbuh, ia dapat tumbuh selama beberapa waktu tanpa menimbulkan masalah yang berarti, tetapi setelah itu menyebabkan gangguan serius dalam pengoperasian BF, mis. perapian dingin, kerusakan tuyere, dll.
Perancah di poros tengah dan bawah
Secara tradisional alkali dianggap sebagai alasan pembentukan perancah di poros BF. Pada suhu di atas 1100 derajat C, alkali berkurang dan menguap dari terak cair dan naik dengan gas. Sianida alkali terbentuk pada suhu mulai dari 900 derajat C hingga 1000 derajat C dan pada kisaran suhu kurang dari 750 derajat C hingga 880 derajat C, uap ini dikondensasi dan dioksidasi oleh CO2 menjadi karbonat. Alkali juga dapat bereaksi dengan bahan beban, partikel debu dan lapisan jika suhunya cukup tinggi. Dalam sistem Na2O-K2O-MgO-CaO Al2O3-SiO2, terdapat banyak komposisi dengan titik leleh rendah dengan beberapa di antaranya memiliki titik leleh serendah 700 derajat C. Pada suhu yang berfluktuasi, lelehan ini dapat melarutkan lebih banyak bahan padat ketika suhunya berubah-ubah. naik dan menggumpal partikel bersama-sama ketika suhu turun lagi. Campuran dengan titik leleh rendah ini terurai menjadi fase yang lebih stabil selama pemadatan dan sulit untuk menetapkan komposisi lelehan tertentu sebagai fase penggumpalan. Fase mengkristal biasanya memiliki titik leleh yang lebih tinggi daripada fase cair awal. Itu sebabnya mis. KAlSiO4 (kalsilit) sering ditemukan di scaffolds, meskipun memiliki titik leleh yang sangat tinggi (lebih besar dari 1700 derajat C). Pengaruh K pada formasi scaffold ditunjukkan pada Gambar 3.
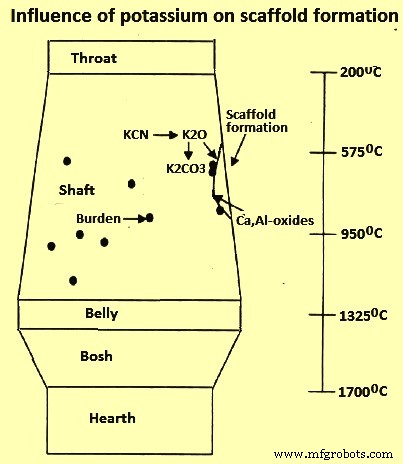
Gbr 3 Pengaruh K pada formasi scaffold
Seng berkurang pada sekitar 800 derajat C dan diuapkan pada 907 derajat C. Seng dioksidasi kembali menjadi ZnO di bagian beban yang lebih dingin di mana suhu turun di bawah 800 derajat C dan di mana rasio CO2 / (CO2+CO) lebih tinggi dari 0,2.
Scaffold dapat tumbuh sangat cepat jika tidak ada mekanisme keausan seperti pergerakan beban yang turun. Selama pergerakan beban turun, gumpalan kokas dengan tepi keras bertindak sebagai bahan penggilingan. Pertumbuhan perancah adalah keseimbangan antara mengikuti dan memakai fenomena. Ada banyak faktor pendukung yang dijelaskan sebelumnya. Umumnya sulit untuk menunjukkan hanya satu faktor. Biasanya sejumlah faktor memicu pertumbuhan perancah.
Perancah di poros atas
Perancah di poros atas sangat umum ketika bahan beban tidak disaring secara menyeluruh atau nilai sifat kerusakan suhu rendahnya buruk. Denda dalam beban dipisahkan ke arah dinding atau dibentuk oleh penyusutan sinter. Jumlah denda yang berlebihan menimbulkan penurunan tekanan tinggi dan dapat menyebabkan apa yang disebut 'gantungan debu'. Bahan halus yang tertahan membentuk dasar untuk menggumpalkan senyawa seperti ZnO dan K2CO3. Terkadang kelembapan pada beban basah dan dingin juga dapat mengembun pada material halus di sisi dinding.
Akar perancah terletak di tengah poros, sebaiknya ditambatkan di sekitar pelat pendingin yang luar biasa. Karena akar perancah terletak sangat tinggi di poros, sulit untuk menghancurkannya dengan melelehkan terak. Selain itu, perancah di poros atas membuat sulit atau bahkan tidak mungkin untuk mengontrol distribusi bijih / kokas di sepanjang radius tungku.
Penyebab terbentuknya perancah
Ada beberapa teori tentang bagaimana perancah pembentukan dimulai, tetapi semua teori menerima bahwa alkali dan / atau Zn terlibat dalam proses pembentukan perancah. Perbedaan mendasar antara teori-teori tersebut adalah apakah alkali dan Zn hanya bertindak sebagai inisiator untuk pembentukan scaffold, atau apakah mereka bertanggung jawab atas keseluruhan proses. Namun, tidak terlalu pasti apakah keberadaan alkali dan Zn merupakan prasyarat untuk pembentukan perancah, atau apakah mereka hanya memperburuk keseluruhan proses pembentukan perancah.
Berdasarkan studi kimia dan mineralogi yang dilakukan pada sampel yang dikumpulkan untuk perancah beberapa BF, terbukti bahwa pembentukan perancah di The BF dapat terjadi baik karena satu penyebab atau karena banyak penyebab. Berbagai penyebab dirangkum di bawah ini.
Seng – Senyawa yang mengandung Zn dan Zn ditemukan di beberapa sampel. Penumpukan Zn terjadi karena siklus Zn di BF. Senyawa yang mengandung Zn seperti ZnO masuk ke BF dengan beban besi. Sementara Zn mencair pada suhu 419,7 derajat C dan menguap pada 906 derajat C, titik leleh ZnO adalah 1975 derajat C. Tergantung pada tekanan parsial Zn dan kandungan CO / CO2 dan H2 / H2O, ZnO berkurang pada suhu tinggi dan dalam kondisi yang ditemukan pada tingkat tuyere sesuai dengan reaksi reversibel ZnO + C =Zn + CO, ZnO + CO =Zn + CO2, dan ZnO + H2 =Zn + H2O. Gas, logam Zn naik ke poros, di mana kondisi berubah dan Zn teroksidasi lagi dan mengembun pada bahan beban. Curah hujan membentuk lapisan putih-kehijauan di atas material beban. Karena suhu leleh yang tinggi, ZnO tetap menempel dan bergerak ke bawah dengan beban. Bersama dengan Zn baru, masuk bersama beban, Zn terakumulasi dalam BF asalkan tidak dibawa keluar.
Oksidasi dan reaksi lebih lanjut menghasilkan berbagai senyawa Zn yang telah terbentuk selama studi mineralogi sampel. ZnO paling sering ditemukan. Beberapa senyawa lain yang ditemukan adalah zinc silikat (Zn2SiO4), gahnit (ZnAl2O4), hardystonite (Ca2ZnSi2O7), dan franklinite (ZnO.Fe2O3). ZnO dapat menggumpal berbagai beban halus dan debu, membentuk perancah di poros. Perancah seperti itu tidak perlu dipasang langsung ke seluruh dinding yang ditutupinya.
Dalam kasus khas operasi BF di mana bahan beban memiliki beban Zn yang sangat tinggi hingga 45 kg per ton logam panas (kg/tHM), jumlah Zn dalam BF terakumulasi lebih cepat daripada BF dengan konsentrasi Zn yang lebih rendah dari beban. Namun, perancah yang disebabkan oleh Zn bukanlah masalah khusus dari BF tertentu. Konsentrasi Zn dapat mencapai jumlah yang tinggi di setiap BF, jika Zn tidak dibawa keluar dari proses dengan tindakan tertentu seperti suhu gas atas yang tinggi.
Sintering – Jika bagian dari beban besi disimpan dalam keadaan terakumulasi dalam jangka waktu yang lama maka dapat dikurangi bahkan pada suhu dan atmosfer yang ada di poros. Akumulasi ini menjadi kaya akan butiran Fe logam, yang ditemukan dekat dengan fase terak. Karena tekanan beban dan suhu di atas 900 derajat C, butiran Fe logam dapat disinter bersama. Pembentukan padat Fe tebal terjadi. Karena stabilitasnya, hanya perlu ditempelkan ke dinding di bagian bawah akumulasi di poros menyebabkan pembentukan perancah.
Alkali – Alkali biasanya masuk ke BF dengan bahan besi dan dengan kokas dalam bentuk silikat. Penumpukan alkali dapat terjadi serupa dengan pembentukan Zn di BF. Dikurangi pada tingkat tuyere, alkali naik di poros dan mengembun pada suhu 882 derajat C (natrium, Na) dan 779 derajat C (kalium, K).
Uap alkali yang naik dengan gas sekitarnya mengembun di bagian atas BF di mana sebagian meninggalkan dengan gas atas, sedangkan sisanya mengembun di dinding bagian dalam atau pada bahan umpan. Karena volatilisasi dan kondensasi alkali di zona termal yang berbeda, alkali cenderung berputar di dalam BF, yang mengarah ke akumulasi dan interaksi dengan bahan umpan lainnya. Ini dapat memiliki dampak yang signifikan pada proses, bahkan ketika alkali dibebankan dalam jumlah kecil, umumnya kurang dari 5 kg/tHM. Tampilan sederhana dari sirkulasi alkali di BF ditunjukkan pada Gambar 4. Studi BF yang digali telah menunjukkan bahwa tingkat alkali tertinggi di mana suhu di atas 1000 derajat C, yang berarti bahwa ada peningkatan konsentrasi alkali di bagian bawah. BF.

Gbr 4 Tampilan sederhana dari sirkulasi alkali di BF
Beberapa reaksi yang terjadi untuk membentuk oksida alkali yang memiliki titik leleh di atas tingkat suhu poros. Alkali juga dapat menggumpal beban dan debu. Jika diendapkan di dinding poros, alkali dapat menyatukan bagian beban dan membentuk perancah.
Tidak penting bahwa perancah yang sebagian besar terbuat dari alkali dibentuk di setiap BF. Namun, pada BFs, terdapat lapisan tipis yang mengandung kalsilit (KAlSiO4) dan senyawa K2O lainnya. Mereka terbentuk langsung di dinding. Perilaku KAlSiO4 penting. Itu bisa menyatukan bagian beban dan membentuk perancah. Bagian besi kemudian direduksi dan disinter bersama, membentuk perancah yang solid. Karena KAlSiO4 bukanlah komposisi yang stabil, ia dapat bereaksi sehingga tidak ada atau sangat sedikit alkali yang kemudian ditemukan dalam sampel scaffold.
Zona lembek – Pada suhu sekitar 1100 derajat C, material beban besi mulai melunak. Struktur lunak di dalam zona lembek ini dipaksa oleh berat beban untuk saling menempel. Selama penghentian tungku atau setelah dinding yang lebih dingin di dekat daerah tercapai, zona lembek ini mengeras, menempel pada dinding dan membentuk lapisan depan perancah. Perancah mengganggu aliran gas melalui poros dan memaksa aliran ke arah lain. Jika karena aliran gas yang berubah, suhu tetap di bawah level aslinya, perancah hampir tidak bisa meleleh. Proses reduksi dan sinter kemudian menghasilkan lapisan butiran Fe logam dalam fase terak yang bahkan lebih sulit untuk dihilangkan. Perancah yang sangat besar dapat ditemukan di BF di mana suhu telah mencapai lebih dari 1100 derajat C. Perancah ini terdiri dari fase terak dan butiran Fe logam yang disinter bersama. Sejumlah kecil Zn atau alkali hadir. Oleh karena itu, di daerah ini diperkirakan bukan unsur-unsur ini, tetapi proses pemadatan bahan lembek yang bertanggung jawab atas pelekatan awal. Indikator lebih lanjut untuk proses pembentukan ini adalah rendahnya karburisasi Fe dan partikel kokas yang tertutup rapat.
Air – Air memasuki BF dengan cara yang berbeda. Yang terpenting adalah (i) wet sinter dan coke, terutama sinter yang diterima dari open storage yang tidak atap terlindung dari kondisi lingkungan seperti hujan, (ii) injeksi uap air pada level tuyere, dan (iii) injeksi air cair di atas beban, jika suhu gas atas melebihi nilai tertentu. Juga, di dekat bagian atas beban, di dinding dingin dekat daerah, uap air bisa mengembun. Sepanjang dinding poros, air cair dapat mengalir ke bawah dan mencapai tingkat poros yang lebih dalam. Air menumpuk debu dan partikel halus dari beban dan dapat menempelkan aglomerat ini ke dinding. Selama periode waktu yang lama, proses sinter dan reduksi membentuk perancah bangunan yang kokoh.
Air yang mengalir ke bawah di dinding poros, mengurangi suhu di dinding dekat daerah. Karena penurunan suhu ini, Zn dan alkali mengembun lebih cepat dan proses pembentukan perancah yang sesuai dipercepat. Begitu air mencapai daerah yang lebih panas, ia menguap, sementara fase air cair mengalir lebih jauh ke bawah di poros BF. Uap air mengurangi kandungan H2/H2O di daerah tersebut. Akibatnya, kesetimbangan reaksi reversibel dalam persamaan ZnO + H2 =Zn + H2O berubah ke arah atau lebih jauh ke arah ZnO.
Dalam diagram area dominasi untuk sistem Zn-O-H2 (Gbr 5), tiga fase berbeda ditampilkan sebagai fungsi dari kandungan H2 / H2O dan suhu. Fase-fasenya adalah (i) Zn cair, Zn(l), (ii) Zn uap, Zn(v), dan (iii) ZnO padat, ZnO(s). Diagram telah dihitung dari data termokimia untuk zat murni. Garis-garis padat dengan tikungan pada titik didih adalah garis koeksistensi di mana Zn dan ZnO berada dalam kesetimbangan bersama. Zn stabil di atas garis tersebut dan ZnO stabil di bawah. Garis koeksistensi merupakan fungsi dari aktivitas Zn, a(Zn). Untuk gas ideal, aktivitas uap Zn, a(Zn) sama dengan tekanan parsial Zn(v). Dalam kondisi yang biasanya ditemukan di BF, nilai aktivitas antara 0,1 dan 0,01 diharapkan untuk uap Zn. Semakin jauh kondisi dari garis koeksistensi, semakin banyak produk yang dibuat sebelum reaksi mencapai kesetimbangan lagi. Jika lebih banyak ZnO terbentuk, peluang untuk membawa Zn keluar dari proses dengan penurunan suhu gas atas yang tinggi.
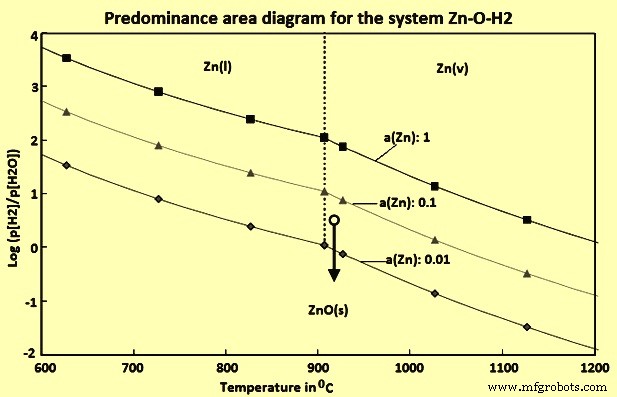
Gbr 5 Diagram area dominasi untuk sistem Zn-O-H2
Lingkaran hitam pada diagram mencirikan jumlah H2 yang tiga kali jumlah uap air pada suhu sedikit di atas titik didih Zn. Bergantung pada tekanan parsial Zn, kesetimbangan termo-mekanis mendekati, bahkan mungkin mendukung Zn(v). Jika ditambahkan air akan menguap dan kandungan H2/H2O menurun ke arah panah. Kondisi sekarang semakin jauh dari garis koeksistensi. Akibatnya, jumlah ZnO yang terbentuk meningkat. Setelah presipitasi, scaffold terbentuk lebih cepat seiring dengan percepatan proses pembentukan scaffold.
Kapur dicampur dengan air – Jika terlalu banyak kapur bakar yang ditambahkan ke proses sintering, dapat memaksa sinter untuk pecah dan pecah, jika terkena air dan bereaksi. Akibatnya, jumlah bagian beban halus meningkat di BF. Secara umum, bagian beban yang halus jauh lebih mudah untuk menggumpal dan mendukung pembentukan perancah. Di dalam BF, kapur yang terbakar dan air dapat bereaksi membentuk semen. Semen menggumpal beban dan membentuk perancah bangunan yang sangat stabil dan kokoh. Jika bagian beban besi dikurangi dan disinter bersama, perancah yang lebih stabil akan terbentuk.
Proses pembentukan perancah
Scaffolds biasanya terbuat dari cangkang padat di sisi dalam BF dan lapisan material beban lepas di antara cangkang ini dan dinding BF. Penelitian telah menunjukkan bahwa cangkang padat berkembang sepanjang isoterm. Selama pembentukan, isoterm ini terletak pada posisi cangkang padat. Ada dua struktur berbeda yang membentuk cangkang padat pada sisi dalam yang memungkinkan yaitu (i) butiran logam Fe dalam fase terak, dan (ii) beban yang direkatkan oleh ZnO. Dua proses pembentukan tampaknya mungkin.
Pada proses pertama, beban besi yang lunak akan mengeras sepanjang isoterm, jika suhu di dalam BF turun. Alasan penurunan suhu bisa menjadi penghentian atau fluktuasi dalam proses. Selama interval waktu yang cukup lama, beban yang mengandung Fe berkurang dan selanjutnya disinter bersama pada suhu dan atmosfer poros. Pada akhir proses telah terbentuk butiran Fe logam dalam fase terak.
Pada proses kedua, Zn, alkali dan senyawanya mengendap dan terbentuk setelah suhu turun di bawah titik tertentu. Hanya pada suhu tertentu, proses reaksi dan pengendapan menghasilkan cukup Zn atau senyawa alkali untuk mengikat beban bersama-sama. Struktur kokas dan sinter yang diikat bersama oleh ZnO adalah produknya. Selama proses reduksi dan sinter lebih lanjut dari beban bantalan Fe, Zn dapat bereaksi dan menjadi gas. Dalam hal ini, butiran Fe logam dalam fase terak adalah produk akhir dari perancah, yang pada proses pertama terdiri dari struktur kokas dan sinter yang diikat bersama oleh ZnO.
Perancah yang dibentuk oleh salah satu proses di atas menjelaskan bentuk cangkang padat, lapisan material beban lepas dan mengapa perancah terbentuk dalam beberapa hari. Setelah cangkang padat ada, itu mengganggu aliran gas melalui poros dan memaksa aliran ke arah lain. Sebagai hasil dari aliran gas yang berubah, suhu dapat tetap di bawah tingkat aslinya. Dalam hal ini, perancah hampir tidak bisa meleleh. Kondensasi dan presipitasi pada lapisan material beban lepas kemudian mengakumulasi senyawa Zn dan alkali. Proses akumulasi ini juga dapat menyebabkan pembentukan lapisan baru di depan cangkang yang sudah ada. Cangkang yang ada merupakan penopang struktural untuk pertumbuhan lebih lanjut dari lapisan baru dan melindunginya dari abrasi.
Scaffolds biasanya terus menerus dibentuk. Kandungan alkali dan Zn dari gas naik diendapkan pada beban atau refraktori saat suhu menurun di poros. Fenomena ini menciptakan perancah yang tumbuh perlahan. Kecepatan pertumbuhan lapisan perancah pada refraktori umumnya dalam urutan beberapa milimeter per minggu. Jenis pembentukan perancah ini terutama dipengaruhi oleh beban alkali dan Zn beban dan distribusi suhu di poros.
Gangguan atau interupsi pada proses di BF dapat menyebabkan beban untuk memulai sintering. Jika ini terjadi di bagian bawah tungku, beban yang menurun dapat menghilangkan sebagian atau seluruh material yang diaglomerasi. Jika aglomerasi terjadi di bagian paling atas dari poros, sebagian beban yang diaglomerasi dapat menjadi stagnan. Material di bawah zona ini juga akan stagnan. Semua bahan ini tereduksi perlahan seiring waktu dan menjadi Fe tereduksi. Selama waktu reduksi dan tergantung pada distribusi temperatur dalam BF, asap alkali dan Zn dapat mengendap pada permukaan partikel oksida Fe dan membentuk senyawa dengan silikat alumina dan magnesia. Kecepatan pertumbuhan fenomena ini dapat jauh lebih besar dibandingkan dengan pembentukan perancah karena pengendapan alkali dan Zn pada refraktori. Kecepatan pertumbuhan tergantung pada parameter seperti perluasan zona beban aglomerasi awal, distribusi suhu, dan jumlah partikel halus dalam gas naik.
Langkah-langkah untuk menghindari pembentukan perancah
Jika perancah tumbuh sangat besar mereka mengganggu proses di BF dan mengurangi efisiensi BF. Perancah solid-build terkadang hanya dapat dilepas dengan peledakan. Tindakan kontra radikal semacam itu terkadang tidak dapat dicegah. Namun, tampaknya mungkin untuk melakukan intervensi dengan tindakan yang tidak terlalu ekstrem untuk menghindari pembentukan perancah. Ketika perancah masih relatif kecil dalam ukuran, terutama selama proses pembentukan, langkah-langkah melawan pembentukannya efektif. Beberapa dari langkah-langkah ini diberikan di bawah ini.
Kapasitas pendinginan – Untuk memulai proses peleburan material beban yang dipadatkan pada dinding poros dan untuk mencegah pemadatan zona lembek di daerah dingin, dekat dinding, kapasitas sistem pendingin poros dapat dikurangi. Jumlah kotak pendingin di bagian atas poros dapat diminimalkan. Kapasitas pendinginan yang lebih sedikit membuat suhu di dalam cukup tinggi, untuk mencegah kemungkinan zona lembek dari pemadatan selama penghentian BF. Sebagai alternatif tampaknya mungkin, untuk mengisi coke dalam jumlah tinggi di dekat dinding, sebelum penghentian. Kokas harus ditempatkan sedemikian rupa, sehingga selama penghentian, itu tetap di daerah, di mana bagian bawah perancah biasanya menempel ke dinding. Dengan cara itu pemadatan dan pelekatan dinding material beban lunak dapat dicegah, karena kokas tidak menjadi lunak pada suhu poros.
Dekat dengan dinding pengisian coke – Coke dalam jumlah tinggi, lebih disukai dibebankan ke dinding dekat daerah meningkatkan suhu dan dapat melelehkan perancah. Kenaikan suhu juga mencegah atau mengurangi kondensasi Zn dan alkali dan sebagai hasilnya, pengembangan perancah baru. Hasil pertama dari pengisian kokas di dekat dinding umumnya terlihat dua atau tiga hari setelah inisiasi. Kerugian dari tindakan balasan ini tentu saja adalah proses keausan yang lebih tinggi dari refraktori dinding poros dan penggunaan gas yang berkurang.
Silika – Silika dapat bereaksi dengan bahan perancah dan dapat membentuk senyawa silika eutektik dengan titik leleh rendah. Oleh karena itu silika dapat ditambahkan ke dinding dekat daerah, untuk melelehkan perancah dari dinding poros.
Menempatkan bagian tengah beban yang halus – Bagian halus dari beban jauh lebih mudah untuk menggumpal dan harus dikurangi. Jika sama sekali dibebankan ke BF, ini untuk memasukkan BF ke wilayah tengah. Dengan cara ini kemungkinan menempelnya aglomerat beban halus ke dinding poros diminimalkan.
Menyeimbangkan alkali dan terak asam – Keseimbangan input dan output memberikan informasi berharga tentang jumlah alkali yang sebenarnya dalam proses BF. Alkali kemudian dapat dibawa keluar dari BF dengan terak asam. Terak asam juga meningkatkan jumlah belerang dalam logam panas (HM). Oleh karena itu, penyeimbangan penting untuk mengoperasikan BF dengan terak asam untuk jangka waktu terbatas dan karenanya kerugiannya seminimal mungkin.
Tergelincir paksa – Tergelincir paksa terjadi ketika ada penghentian tekanan ledakan selama beberapa menit. Ini memaksa beban untuk turun tiba-tiba di poros dan bagian atas beban tenggelam. Karena gaya tiba-tiba yang diprakarsai oleh berat beban, perancah dapat putus. Geser paksa harus diberikan hanya pada akhir sadapan, untuk mencegah penurunan kualitas dan kontaminasi HM oleh material geser ke bawah.
Optimasi fitur konstruksi BF – Terutama di bagian atas yang dingin, kotak pendingin bertindak seperti jangkar untuk perancah di masa depan. Berbeda dengan stave, kotak pendingin menghasilkan titik dingin yang tersebar di dinding poros. Titik dingin ini merupakan titik awal yang ideal untuk kondensasi dan pemadatan. Tongkat dengan efek pendinginan yang sama dengan kotak pendingin menghasilkan medan suhu yang stabil, tanpa suhu minimum yang ekstrem. Oleh karena itu, tongkat kurang rentan untuk menghasilkan perancah.
Suhu gas atas yang tinggi – Zn dapat dikeluarkan dari proses BF dengan suhu gas tertinggi, tidak memberikan uap Zn cukup waktu untuk mengembun atau bereaksi. Untuk mencapai tujuan ini, suhu gas puncak optimal yang dibutuhkan adalah sekitar 350 derajat C. Bersama dengan jumlah kokas yang tinggi, yang dibebankan ke area dinding, jumlah Zn sebesar 45 kg/tHM dapat ditangani di BF.