Busa Terak di Tungku Busur Listrik
Pembusaan Terak di Tungku Busur Listrik
Pembusaan terak telah menjadi praktik penting dan kritis untuk tungku busur listrik modern (EAF) karena terak berbusa yang baik memberikan kontribusi efisiensi yang cukup besar dan manfaat lain untuk proses tersebut. Kualitas pembusaan terak merupakan faktor penting dalam proses pembuatan baja EAF karena memastikan bahwa panas dari penangas cairan tidak hilang melalui dinding EAF. Busa terak bermanfaat untuk proses pembuatan baja EAF dalam hal luas permukaan yang besar yang terbentuk dan perlindungan yang diberikan terhadap kontak langsung lelehan dengan atmosfer.
Pembusaan terak adalah teknik yang berguna sekaligus ekonomis. Ini adalah teknik yang banyak digunakan, tidak hanya karena memungkinkan penghematan energi, tetapi karena beberapa keuntungan yang ditawarkannya yang meliputi (i) peningkatan efisiensi energi, karena panas dari busur ditangkap oleh terak, (ii) perlindungan panel air dan atap dari radiasi, (iii) penurunan getaran dan polusi suara, dan (iv) penurunan penggabungan nitrogen oleh bak mandi.
Pembentukan terak berbusa dapat dibagi menjadi 3 langkah. Ini adalah (i) langkah 1 yaitu injeksi oksigen dalam fase baja cair, (ii) langkah 2 yaitu injeksi karbon ke terak, dan (iii) langkah 3 yaitu saat oksigen disuntikkan ke terak. Awalnya, oksigen disuntikkan ke dalam logam cair (langkah 1). Oksigen ini bereaksi dengan karbon yang ada membentuk gelembung CO (karbon monoksida). Oksigen juga bereaksi dengan zat besi yang ada di bak mandi. Saat besi hilang dalam bentuk oksida besi, karbon disuntikkan ke terak (langkah 2), melakukan reaksi reduksi oksida besi. Langkah ini menghasilkan gas CO, dan juga menyebabkan besi kembali ke bak, meningkatkan kinerja tungku. Pada langkah 3, oksigen disuntikkan ke terak, untuk menyebabkan oksidasi karbon yang ada di terak. Pada langkah ini, karbon dan oksigen juga dapat disuntikkan secara bersamaan, memungkinkan pembentukan CO yang lebih baik dan pembusaan yang lebih baik.
Biasanya ada lapisan terak padat di bawah busa. Namun, ada kemungkinan bahwa semua terak yang ada diperlukan untuk menghasilkan busa dan tidak ada lapisan padat. Dalam kasus seperti itu, jumlah terak yang ada tidak cukup untuk menghasilkan semua busa yang dapat dibentuk oleh terak dan gas.
Juga telah dilaporkan bahwa proses pembusaan terak dapat menghemat 3% hingga 10% dan 25% hingga 63% konsumsi energi dan refraktori. Pada dasarnya ada dua persyaratan untuk berbusa yaitu (i) reaksi atau proses yang menghasilkan gelembung gas kecil, dan (ii) sifat terak yang sesuai untuk menjaga gelembung sebagai busa yang stabil. Biasanya, gas yang dihasilkan dari reaksi kimia cenderung membuat terak berbusa dengan gelembung yang lebih kecil, sedangkan injeksi fase gas (oksigen, argon, dll.) menghasilkan gelembung yang lebih besar dan busa yang kurang stabil.
Kemampuan berbusa tertentu dari terak yang digunakan untuk proses EAF diinginkan, karena sejumlah alasan. Selama proses, terak berbusa melindungi elektroda grafit dari keausan dan menutupi busur. Hal ini memungkinkan produktivitas yang lebih tinggi di tungku, karena meningkatkan perpindahan panas antara elektroda dan logam cair. Ini juga mengurangi kehilangan radiasi, karena terak mengisolasi berkas cahaya. Hal ini pada gilirannya melindungi refraktori dari keausan, yang mengurangi jumlah waktu henti untuk pekerjaan pemeliharaan. Terak berbusa juga berkontribusi pada stabilisasi busur, memastikan efisiensi yang lebih tinggi. Selain itu, busa membantu mengurangi kebisingan dari EAF, yang memberikan lingkungan kerja yang lebih baik. Keuntungan lain dengan terak berbusa adalah pengurangan fluktuasi daya dan tegangan.
Akibat dari foaming slag yang baik pada EAF dan pengendaliannya yang baik antara lain (i) penurunan harmonisa akibat pencelupan elektroda pada slag dapat meningkatkan daya pada setting transformator yang sama sebesar 6% sampai 9%, (ii) peningkatan daya sebesar 15% ketika ujung elektroda sedalam 300 mm hingga 600 mm di dalam terak karena plasma busur yang lebih panas di sekitar ujung elektroda, dan (iii) terak berbusa yang baik memungkinkan pembakar bahan bakar oksigen (bila digunakan) meledak ke dalam terak, meningkatkan efisiensi energi pembakar dari 40% menjadi 70%. Namun, untuk mendapatkan manfaat maksimal dari terak berbusa, terak harus dibuat lebih awal di panas dan kimia terak harus dikontrol secara ketat dengan membatasi pembilasan terak dan dengan meletakkan kapur atau kerak penggilingan di bagian bawah pengisian pertama. keranjang. Manfaat termal dari terak berbusa yang baik adalah karena pergeseran jalur perpindahan panas ke bak mandi dan menjauh dari dinding samping. Sesuai penelitian, variasi kualitas terak berbusa dapat menjelaskan +/- 0 kWh/t dalam permintaan energi listrik
Hal ini berguna untuk mengetahui apa yang dimaksud dengan slag foaming. Pembangkitan gas sangat diperlukan agar berhasil dengan praktik terak berbusa. Gas terutama dihasilkan oleh reduksi oksida besi (FeO) dengan karbon membentuk gas CO. Gas menyebabkan gelembung busa terbentuk di atas lapisan terak yang padat. Busanya bisa berupa gelembung busa yang relatif kecil seperti busa pada bir atau gelembung yang lebih besar seperti busa gelembung sabun di atas air. Gelembung kecil hasil dari reaksi kimia dan busa yang dihasilkan cukup stabil. Injeksi gas, bagaimanapun, menghasilkan gelembung yang lebih besar dan busa yang kurang stabil. Pembusaan yang sebenarnya tidak sama dengan penimbunan gas sederhana dari gelembung-gelembung dalam cairan. Dalam kasus gas hold-up, gelembung gas didistribusikan ke seluruh cairan dan ekspansi terak disebabkan oleh gelembung gas dalam cairan. Untuk gas hold-up, ekspansi meluruh dengan cepat setelah gas berhenti. Busa sejati bisa cukup stabil dan tetap demikian selama beberapa menit setelah pembangkitan gas berhenti.
Reaksi pembentukan gelembung gas, reduksi FeO dalam terak dengan menambahkan karbon dan karbon terlarut dalam logam. Dalam proses pembusaan terak, karbon disuntikkan ke dalam terak, bereaksi dengan oksida besi dalam terak untuk menghasilkan gas CO, yang membuat terak berbusa. Reaksi diberikan oleh C (disuntikkan) + (FeO) =Fe + CO. Gas CO untuk pembusaan juga dihasilkan oleh dekarburisasi logam yang diberikan oleh reaksi C (dalam logam) + 1/2 O2 =CO. FeO adalah dihasilkan in situ sebagai produk oksidasi utama dari hembusan oksigen dan karenanya merupakan komponen utama dalam terak (lebih tinggi dari 20%). Jika konsistensi terak cocok untuk menopang busa, injeksi sederhana karbon ke terak menyebabkan terak berbusa. Laju reduksi yang relatif tinggi memberikan FeO potensi menghasilkan sejumlah besar gas di dalam busa. Laju reduksi FeO oleh karbon cukup cepat. Selain itu, reaksi reduksi juga mengkonsumsi panas, yang menghasilkan peningkatan lokal pada viskositas terak.
Variabel proses yang mempengaruhi pembentukan buih adalah komposisi terak, kecepatan superfisial gas, temperatur bak, ukuran gelembung, kebasaan terak, densitas terak, viskositas terak, dan tegangan permukaan terak. Kecepatan gas superfisial biasanya diukur dalam meter per detik (m/s) dan merupakan kecepatan gas sebenarnya dikalikan dengan fraksi volume gas.
Indeks pembusaan (FI) merupakan parameter penting untuk pembusaan terak. Ini dapat dilihat sebagai waktu untuk gas melewati terak. Ini merupakan indikasi sejauh mana pembusaan dan merupakan rasio antara tinggi busa dan kecepatan gas superfisial. Oleh karena itu, satuan FI adalah waktu yang biasanya dalam detik. Dengan demikian, FI dapat diartikan sebagai ukuran waktu yang diperlukan untuk gas proses untuk melewati busa secara vertikal. FI terkait dengan sifat terak seperti viskositas. Semakin tinggi viskositas, semakin tinggi FI. Konsekuensi yang jelas adalah bahwa peningkatan viskositas secara otomatis menyebabkan peningkatan tinggi busa.
FI menurun dengan meningkatnya ukuran gelembung. Secara umum terlihat bahwa gelembung-gelembung kecil terbentuk oleh reaksi pertama yang diberikan di atas dan hasil busa yang relatif stabil. Dalam pembuatan baja EAF, telah ditemukan bahwa, menjelang akhir proses, busa menjadi kurang stabil dan tinggi busa berkurang. Ini terjadi karena awalnya dengan meningkatnya kandungan FeO, laju reaksi pertama dan pembentukan CO meningkat dan, karenanya, pembusaan meningkat. Namun, dengan meningkatnya kandungan FeO, viskositas terak menurun dan densitas meningkat menyebabkan gelembung busa mengalir lebih cepat, berkurang dan busa membusuk. Oleh karena itu, ada kandungan FeO kritis di bawah yang berbusa meningkat dengan kandungan FeO dan di atasnya busa kurang stabil. Ini terjadi pada sekitar 20% sampai 40% FeO tergantung pada kondisi lain.
Pembusaan terak saat diperkenalkan dibantu dengan injeksi bubuk grafit yang dibuat dari elektroda (80 % ukuran -200 mesh) ke antarmuka terak logam menggunakan peralatan injeksi yang sesuai dengan udara sebagai gas pembawa. Melalui perhitungan sebelumnya dan prosedur trial and error, ditemukan bahwa laju aliran massa grafit sebesar 25 kg/menit cukup baik untuk menghasilkan busa yang stabil. Nilai yang lebih tinggi dari ini, pada awal pemanasan, menyebabkan slag slag berat yang memengaruhi operasi di lantai kerja dan membuat busur listrik yang tidak stabil menghambat operasi dengan busur panjang bertegangan tinggi dan arus rendah.
Dalam proses pembuatan baja EAF, operasi busur panjang terjadi bersamaan dengan praktik terak berbusa. Dengan pembusaan terak melalui injeksi karbon, ketinggian lapisan terak dapat dinaikkan sampai menutupi busur sepenuhnya, mencegat radiasi busur dan suar, mentransfer panas ke bak mandi dan mengurangi beban panas di dinding samping. Jika terak berbusa yang baik tidak dapat dipertahankan, bagaimanapun, lebih baik untuk mengurangi tegangan sekunder dan dengan demikian panjang busur untuk menghindari risiko kerusakan pada struktur tungku.
Fenomena pembusaan terak tergantung pada sifat terak dan laju evolusi gas, karena reaksi dalam terak. Dengan demikian, untuk mendapatkan busa dalam terak, diperlukan aliran gas. Aliran gas dihasilkan ketika karbon (C) dan gas oksigen (O2) masing-masing ditambahkan ke terak dan rendaman logam. Kontrol ketinggian buih diperlukan untuk mempertahankan operasi yang stabil.
Tergantung pada sifat fisik terak (yang dipengaruhi oleh komposisi dan suhu), pembusaan kemudian terjadi pada tingkat yang berbeda-beda. Dalam pembuatan baja EAF, cukup umum untuk menambahkan karbon (dalam bentuk kokas atau batu bara) ke lapisan terak. Konsumsi karbon terjadi melalui reaksi Boudouard, dan dengan demikian laju pembentukan CO sebanding dengan laju penambahan karbon ke terak EAF, setelah reaksi mencapai keadaan tunak.
Pembusaan terak secara signifikan dipengaruhi oleh aliran gas ke dalam tungku, tetapi juga dipengaruhi oleh sifat terak, yang terakhir dikendalikan oleh viskositas, densitas dan tegangan permukaan. Sifat fisik ini, pada gilirannya, bergantung pada suhu sistem dan komposisi terak.
Untuk proses EAF, komposisi slag tergantung pada grade baja serta metode pemurnian yang digunakan. Ketika memilih komposisi untuk terak, beberapa hal harus dipertimbangkan. Terak terdiri dari berbagai oksida, yang dapat dibagi menjadi tiga kategori, yaitu (i) oksida basa (seperti CaO, MgO dan FeO), oksida asam (seperti SiO2) dan oksida amfoter (seperti Al2O3). Untuk terak dasar, kandungan FeO umumnya dianggap pada tingkat optimum berkisar antara 15% sampai 25%. Untuk membangun busa dalam terak, viskositas harus cukup tinggi untuk menghalangi naiknya gelembung. Untuk mendapatkan viskositas yang sesuai, penting untuk memiliki kebasaan terak yang sesuai. Kebasaan umumnya disebut sebagai rasio komponen dasar dalam terak dengan komponen asam. Komponen dasar memberikan ion O2 ke lelehan dan komponen asam mengikatnya. Viskositas dapat diubah melalui perubahan komposisi, yang menyebabkan perubahan rasio CaO/SiO2, sehingga menurunkan atau meningkatkan kebasaan terak.
Perubahan viskositas juga dapat dicapai melalui perubahan kandungan FeO. Ketika meningkatkan jumlah FeO, viskositas berkurang. Cara lain untuk memodifikasi kekentalan terak adalah dengan meningkatkan jumlah partikel padat dalam terak, misalnya dengan penambahan kapur. Telah diamati bahwa viskositas terak menurun dengan peningkatan kebasaan, tetapi ketika melewati nilai kritis dan fase padat diendapkan, itu meningkat sekali lagi. Dengan demikian, keberadaan partikel padat berkontribusi pada peningkatan viskositas yang tampak. Partikel padat juga bertindak sebagai situs nukleasi untuk gelembung. Namun, jumlah partikel padat yang berlebihan mencegah gelembung naik melalui terak.
Dalam sistem cairan, gradien tegangan permukaan atau antarmuka dapat menyebabkan gerakan. Ini disebut efek Marangoni. Dalam antarmuka antara terak dan logam cair umumnya ada gradien besar dalam tegangan antarmuka. Konsentrasi FeO dianggap lebih rendah daripada di sisa terak pada antarmuka antara terak dan logam, di mana reaksi yang membentuk CO terjadi. Hal ini memungkinkan terbentuknya gelembung, karena kandungan FeO yang lebih sedikit menghasilkan tegangan permukaan yang lebih rendah, yang menimbulkan efek Marangoni. Dengan demikian, kemampuan untuk membuat permukaan baru, yang terjadi ketika gelembung terbentuk di terak, difasilitasi ketika tegangan permukaan rendah.
Tegangan permukaan juga mempengaruhi degradasi busa, mengacu pada stabilitas gelembung. Berbagai penelitian telah menunjukkan bahwa stabilitas dapat ditingkatkan dengan penambahan komponen aktif permukaan. Juga telah diamati dalam proses pembuatan baja bahwa keberadaan komponen aktif permukaan mendorong pembusaan. Namun, aliran Marangoni, yang membantu menghilangkan gelembung CO dari antarmuka, dapat dihasilkan tanpa elemen aktif permukaan. Kepadatan terak mempengaruhi tinggi busa. Kepadatan yang rendah berarti bobot yang harus dipikul lebih sedikit, yang memungkinkan busa lebih tinggi, dibandingkan dengan terak dengan kepadatan tinggi. Untuk menahan beban, permukaan harus memiliki sifat elastis. Hal ini dapat dicapai melalui penambahan elemen aktif permukaan yang menghasilkan tegangan permukaan variabel.
Terak berbusa dalam operasi pembuatan baja dihasilkan dari pembentukan gelembung CO, melalui reaksi reduksi, (i) CO2 + C(s) =2CO (reaksi Boudouard), (ii) CO + Fe2O3 =CO2 + 2FeO, (iii) CO + FeO =CO2 + Fe, dan (iv) C(s) + FeO =CO + Fe. Reaksi Boudouard dan reduksi FeO oleh karbon padat adalah reaksi yang sangat endotermik, sedangkan reduksi Fe2O3 oleh CO adalah energi-netral dan reduksi FeO oleh CO hanya sedikit eksotermik. Penting untuk dicatat bahwa oksida besi adalah sumber komponen oksigen yang diperlukan untuk pembakaran karbon, bukan oksigen gas, dan dengan demikian beberapa oksidasi rendaman baja diperlukan untuk pembusaan terak.
Kekuatan pendorong untuk pembusaan terak adalah energi pneumatik yang disediakan oleh pembangkitan CO selama proses peleburan-pemurnian di EAF. Dalam proses pembusaan terak, karbon disuntikkan ke dalam terak, bereaksi dengan oksida besi (FeO) di dalam terak untuk menghasilkan karbon monoksida (CO), yang membentuk busa pada terak. Reaksi diberikan oleh C (disuntikkan) + (FeO) =Fe + CO. CO untuk berbusa juga dihasilkan oleh dekarburisasi logam yang diberikan oleh reaksi C (dalam logam) + 1/2 O2 =CO. Reaksi ini bertanggung jawab untuk pembentukan CO Reaksi kedua merupakan reaksi langsung antara gas oksigen dan karbon dalam bak, sedangkan reaksi pertama adalah reaksi reduksi oksida besi langsung oleh karbon dalam terak. Semua reaksi ini adalah pembentuk CO yang memberikan energi pengadukan untuk perpindahan massa antara terak logam, karbon, dan fase gas dan mereka dapat dianggap sebagai kondisi yang diperlukan untuk pembusaan terak. Beberapa reaksi adalah konsumen CO seperti (i) CO + Fe2O3 =CO2 + 2FeO, dan (ii) CO + FeO =CO2 + Fe, yang dapat dikontrol dengan reaksi Boudouard CO2 + C(s) =2CO.
Situs reaksi ini dapat ditemukan sebagai (i) pada antarmuka terak-logam, (ii) pada antarmuka gas-logam, (iii) pada antarmuka terak karbon, dan (iv) pada antarmuka terak-gas dan karbon-gas. . Gambar 1 menunjukkan diagram skematis reaksi kimia untuk pembusaan terak di EAF. Diagram menunjukkan situs reaksi selama injeksi karbon selama proses peleburan-pemurnian baja di EAF. Dapat dilihat dari diagram bahwa pembentukan CO merupakan fungsi yang sangat kompleks dari beberapa variabel proses yang terdiri dari ukuran, jenis dan laju aliran massa bahan karbon, laju aliran gas pembawa, kandungan karbon dalam bak, kimia terak, dan terak-logam. area antarmuka dll.
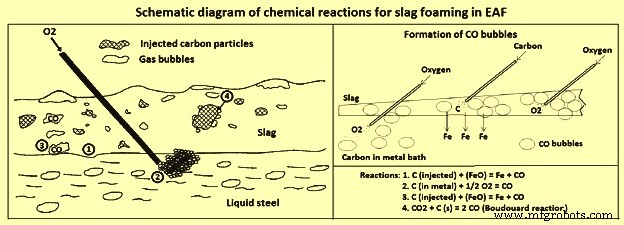
Gbr 1 Diagram skematis reaksi kimia untuk pembusaan terak di EAF
Di sisi lain, kondisi lain untuk pembusaan terak harus dipenuhi. Kondisi ini secara langsung berkaitan dengan sifat transportasi (yang mempengaruhi stabilitas busa) terak pembuatan baja pada suhu pemurnian. FI terak menentukan sifat-sifat ini. FI diukur dalam satuan waktu yaitu detik dan merupakan fungsi kimia terak. Kurva stabilitas untuk FI terak ditunjukkan pada Gambar 2. Kesimpulan dari kurva diberikan di bawah ini.
- Terak asam memiliki kemampuan pembentukan indeks pembusaan tertinggi yang dapat disebut sebagai pembusaan homogen.
- Terak dengan kandungan oksida besi yang rendah (kurang dari 10%) membentuk busa yang lebih stabil daripada terak yang sangat teroksidasi (lebih dari 40% FeO pada semua basa) yang, oleh karena itu, dapat disebut terak tidak berbusa.
- Pada kandungan oksida besi yang rendah, kebasaan terak sangat mempengaruhi stabilitas pembusaan. Pada kebasaan yang lebih tinggi, di bawah kandungan oksida besi tertentu, FI menurun. Pada kandungan oksida besi yang tinggi, kebasaan terak tidak berperan.
- Terak dengan kandungan oksida besi menengah dan kebasaan tinggi di dekat zona saturasi kapur juga memiliki FI menengah dan keberadaan partikel padat larutan kapur dapat membantu menstabilkan pembentukan busa. Karena alasan ini, zona ini dapat disebut sebagai pembusaan heterogen.
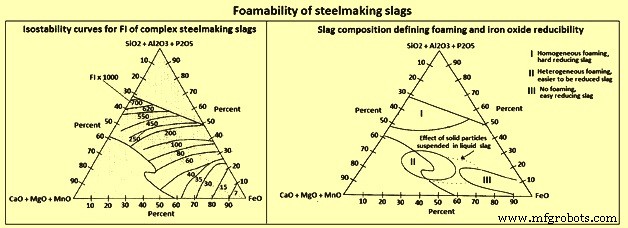
Gbr 2 Kemampuan berbusa terak pembuatan baja
Gambar 2 juga menunjukkan komposisi terak dan pembusaan. Partikel padat yang tersuspensi dalam terak cair mempengaruhi viskositasnya. Biasanya terlihat bahwa dengan hanya 20% fraksi volume partikel padat dalam terak cair, ada peningkatan dua kali lipat dalam viskositas terak dan zona untuk pembusaan heterogen dapat sangat diperbesar, sebagian mencakup zona tidak berbusa, seperti yang ditunjukkan dengan garis putus-putus pada Gambar 2.
Untuk mendapatkan gambaran yang lebih lengkap tentang pembusaan terak selama injeksi karbon, aktivitas oksida besi dalam terak kompleks telah menjadi subjek beberapa penelitian. Studi-studi ini telah menunjukkan hal berikut.
- Zona pembusaan homogen dengan aktivitas oksida besi rendah (kurang dari 10%) menunjukkan ketahanan yang kuat terhadap reduksi besi oleh karbon bukan hanya karena aktivitas oksida besi yang rendah tetapi terutama karena sifat aktif permukaan silika dalam terak. Reduksi besi di zona ini dikendalikan oleh perpindahan massa dan mekanisme reaksi kimia.
- Terak yang sangat teroksidasi mudah direduksi oleh karbon karena aktivitas oksida besi cukup tinggi tetapi tidak membentuk busa yang stabil.
- Komposisi normal dari slag pembuatan baja menunjukkan perilaku antara. Meskipun, terak akhir cenderung sangat teroksidasi.
Penting untuk mempertahankan terak berbusa adalah pemantauan kondisinya. Ketika pembusaan terak pertama kali diperkenalkan, itu dipantau secara manual, operator tungku menggunakan mata dan telinga mereka, ditambah dengan pengalaman mereka, untuk menilai apakah terak itu benar atau tidak, dan langkah-langkah yang diperlukan untuk memperbaikinya. Dimulai pada pertengahan 1980-an, pemantauan elektronik dan kontrol komputer dari pembusaan terak diperkenalkan, dengan beberapa sinyal yang mungkin dipelajari seperti distorsi busur, kebisingan busur, dan emisi cahaya. Saat ini, distorsi busur tampaknya menjadi sinyal yang paling banyak digunakan dalam operasi tungku AC untuk memantau kondisi busa, karena sensor dan program yang diperlukan sering terintegrasi dengan regulator elektroda yang canggih. Banyak EAF menggunakan harmonik yang dihasilkan dalam suplai listrik oleh busur sebagai monitor terak berbusa, karena terak berbusa yang lebih baik menghasilkan busur yang lebih stabil dan harmonik yang lebih sedikit. Pemantauan melalui emisi suara dan cahaya dari EAF juga telah dicoba sebagai metode pemantauan busa.
Busa di EAF, bagaimanapun, telah menjadi bagian integral dari proses pembuatan baja, terutama selama tahap pemurnian panas. Proses busur panjang saat ini memaksimalkan transfer energi ke skrap yang mengelilingi elektroda dan busur. Dengan demikian, potongan memotong sebagian besar radiasi busur dan sedikit melewati ke dinding samping.
Namun, begitu skrap meleleh, semua radiasi busur dapat menimpa dinding samping. Dengan menutupi sebanyak mungkin busur yang terbuka, terak berbusa memotong energi ini, mencegahnya mencapai dinding, dan meneruskannya ke bak baja. Terak berbusa dapat terbentuk secara perlahan saat skrap meleleh dan dinding samping tungku dan atap menjadi semakin terpapar panas yang memancar dari busur, mencapai ketinggian maksimum selama tahap pemurnian panas. Karbon dan CO yang disuntikkan juga membantu mengurangi oksida besi di terak kembali menjadi besi metalik.