Busa Terak di Tungku Oksigen Dasar
Pembusaan Terak di Tungku Oksigen Dasar
Dalam pembuatan baja tungku oksigen dasar (BOF), aliran oksigen supersonik (O2) disuntikkan ke permukaan penangas logam panas. Unsur-unsur pengotor dalam bak seperti karbon (C), silikon (Si), mangan (Mn), dan fosfor (P) dioksidasi dan dikeluarkan dari bak dalam bentuk CO (karbon mono-oksida), CO2 (karbon di-oksida), SiO2 (silika), MnO (mangan oksida), P2O5 (fosfor pentoksida), dan oksida besi oleh O2 yang disuntikkan. Oksida gas, yang mengandung 90% CO dan 10% CO2, keluar dari tungku dari atas dengan sejumlah kecil debu besi oksida (FeO) dan kapur (CaO). Oksida cair lainnya larut dengan fluks tambahan yang membentuk terak cair yang selanjutnya memfasilitasi pemurnian bak.
Busa adalah fenomena penting yang biasa ditemui ketika gas dihembuskan melalui cairan kental. Ini bermanfaat dalam pembuatan baja BOF karena membantu proses pemurnian dengan cara yang berbeda. Ini memberikan peningkatan luas permukaan untuk reaksi pemurnian dan melindungi rendaman logam cair dari kontak langsung dengan atmosfer. Ini meningkatkan kinetika reaksi, perpindahan panas, dan efisiensi energi proses. Ini membentuk media untuk pasca-pembakaran dan perpindahan panas. Ini melindungi lapisan refraktori dari efek pembakaran ekstrim dengan menyediakan perisai untuk refraktori dan karenanya memperpanjang umur lapisan refraktori. Bertindak sebagai penampung oksida pengotor seperti Mn, Si, dan P, yang telah teroksidasi dari penangas cairan. Selain itu, pembusaan terak mencegah rendaman cairan dari oksidasi dan memungkinkan kontrol komposisinya. Ini juga bertindak sebagai isolator termal antara pemandian air panas dan sekitarnya dan dengan demikian mencegah kehilangan energi yang besar. Namun, pembusaan terak dalam pembuatan baja BOF dianggap sebagai fenomena yang perlu dikontrol hingga volume terbatas untuk mendapatkan manfaatnya.
Pada dasarnya ada dua persyaratan untuk pembusaan terak. Ini adalah (i) reaksi atau proses yang menghasilkan gelembung gas kecil, dan (ii) sifat terak yang sesuai untuk menjaga gelembung sebagai busa yang stabil. Biasanya, gas yang dihasilkan dari reaksi kimia cenderung membuat terak berbusa dengan gelembung yang lebih kecil, sedangkan injeksi fase gas seperti O2 dan Ar (argon) dll. menghasilkan gelembung yang lebih besar dan busa yang kurang stabil.
Busa adalah kejadian umum di BOF yang dihasilkan dengan menjebak gas di lapisan terak. Dengan perkembangan pukulan, jumlah terak serta gas yang dihasilkan meningkat, dan akibatnya, pembusaan terak juga meningkat. Pembusaan terak dapat menjadi tidak menguntungkan dan berbahaya bila terbentuk dalam jumlah besar, dan meluap dari mulut konverter, yang disebut slopping of the bath. Oleh karena itu, pembusaan terak harus dikontrol dengan baik untuk proses produksi yang berkelanjutan dan efisien. Oleh karena itu, pemahaman menyeluruh tentang busa dan proses pembusaan diperlukan untuk mengoptimalkan proses dengan meminimalkan pembusaan terak.
Terak adalah material non-logam yang dihasilkan dari produk reaksi oksidasi (SiO2, MnO, P2O5, dan FeO) dan fluks pelarut (kapur dan dolomit terkalsinasi) selama proses pembuatan baja. Terak juga dapat mengandung senyawa oksida, gas terlarut, lapisan refraktori terlarut, dan partikel padat dari fluks tak terlarut atau senyawa oksida/oksida yang diendapkan.
Terak memiliki kerapatan yang rendah dan karenanya mengapung di atas logam cair. Persyaratan utama terak dalam pembuatan baja BOF adalah berfungsi sebagai kolam oksida dari pengotor yang teroksidasi dan dihilangkan untuk dikumpulkan. Selanjutnya, komposisi dan suhu dari kolam terak ini membantu kemajuan reaksi pemurnian dalam konverter. Keuntungan lain dari memiliki lapisan terak dalam konverter operasi terdiri dari melindungi wadah logam dari udara sekitar, memperlambat pembubaran lapisan tahan api konverter, dan mengendalikan suhu wadah.
Komposisi terak (biasanya dalam sistem CaO–MgO–SiO2–FeO–Al2O3) secara langsung mempengaruhi viskositas, konduktivitas termal, densitas, dan sifat lainnya, sehingga berdampak pada kemampuan terak untuk menghilangkan kotoran dari penangas cairan. Terak umumnya memiliki viskositas tinggi dan kepadatan rendah, menyebabkan terak mengapung di bak logam curah. Karena sifat fisiknya, terak memiliki kemampuan untuk menjebak gelembung gas yang dihasilkan oleh reaksi kimia dan menyuntikkan O2, dan menghasilkan busa terak.
Busa terak (Gbr 1) dihasilkan saat gas CO dihasilkan dan terperangkap dalam terak. De-karburisasi baja adalah sumber untuk menghasilkan busa. Saat pancaran O2 menyentuh permukaan bak, tetesan logam terkoyak karena momentum tinggi dan berakhir di busa menciptakan emulsi terak, gas, dan tetesan logam. Dalam emulsi, terak memiliki banyak permukaan tetesan logam untuk bereaksi, yang meningkatkan kinetika reaksi. Prosesnya diperkirakan akan lebih lama jika belum ada emulsi. Emulsi sangat penting untuk proses dan penting untuk memiliki komposisi terak yang tepat untuk menjaga pembusaan tetap terkendali, dengan tingkat pembusaan yang tidak terlalu tinggi atau terlalu rendah. Waktu tinggal menentukan kemungkinan waktu reaksi antara terak dan tetesan yang bergerak dalam fase emulsi.
Laju pembentukan gas memainkan peran penting dalam pembentukan dan pertumbuhan busa. Gas tersebut merupakan produk dari proses dekarburisasi. Ini berlangsung (i) dengan oksidasi langsung pada permukaan logam di titik panas sesuai persamaan [C] + 1/2O2(g) =CO(g), (ii) dalam busa, secara tidak langsung oleh oksida besi yang bereaksi dengan logam tetesan sesuai persamaan [C] + (FeO) =CO(g) + {Fe} di mana (FeO) adalah produk oksidasi besi (Fe) oleh O2 murni sesuai persamaan {Fe} + 1/2 O2 (g) =(FeO), dan (iii) dalam lelehan, melalui reaksi antara O2 terlarut dan C sesuai persamaan [C] + [O] =CO(g)..
Dekarburisasi sesuai reaksi di bawah (i), dan juga oksidasi Fe sesuai reaksi kedua di bawah (ii), dimulai segera dan berlanjut sepanjang pukulan, meskipun dalam kasus pertama dengan kecepatan yang berkurang, karena penurunan terus menerus dalam kandungan C pada permukaan logam. Laju oksidasi Fe lebih konstan, tetapi kandungan FeO yang dihasilkan dari terak akhirnya menurun karena peningkatan konsumsi sesuai dengan reaksi pertama di bawah (ii). Pada akhir periode penghembusan, kandungan FeO dalam terak mulai meningkat lagi karena partisipasi FeO dalam proses dekarburisasi berkurang karena rendahnya kandungan C dari lelehan. Pada akhir pukulan, reaksi pengontrolan de-karburisasi adalah reaksi di dalam lelehan antara C dan O2 terlarut sesuai dengan reaksi di bawah (iii). Oleh karena itu, laju dekarburisasi pada akhir pukulan bergantung pada perpindahan massa C dari bagian bawah ke bagian atas lelehan dan O2 terlarut dalam arah yang berlawanan. Reaksi prinsip yang terlibat dalam dekarburisasi lelehan dalam konverter BOF ditunjukkan pada Gambar 1.
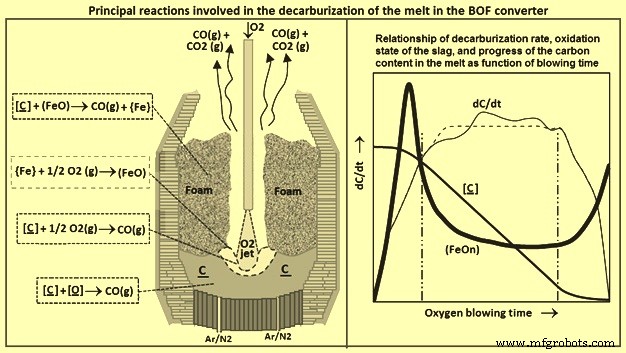
Gbr 1 Reaksi prinsip yang terlibat dalam dekarburisasi lelehan dalam konverter BOF
Seperti ditunjukkan di sebelah kanan Gambar 1, laju de-karburisasi maksimum, dan karenanya laju pembangkitan gas maksimum, mencapai 25% hingga 30% ke dalam pukulan, dan berlanjut hingga sebagian besar di dalam busa sesuai dengan reaksi pertama. di bawah (ii). Lajunya cukup konstan dengan tingkat tergantung pada ketersediaan FeO dan pasokan tetesan logam yang dikeluarkan dari zona pelampiasan O2. Pada sekitar 80% pukulan, laju pembangkitan gas dengan cepat turun karena kandungan C yang rendah dalam lelehan.
Busa terak bermanfaat untuk proses pembuatan baja dalam hal luas permukaan yang besar yang terbentuk dan perlindungan yang diberikan terhadap kontak langsung lelehan dengan atmosfer. Biasanya, sifat fisik terak berkembang dalam mendukung pembusaan selama pukulan, dan ketika bertepatan dengan tingkat produksi gas yang tinggi dari reaksi kimia, pembusaan terak dapat menjadi tidak terkendali dan meluap konverter menciptakan insiden slopping. Tergelincir adalah kejadian yang merugikan, dan konsekuensinya meliputi kehilangan hasil, biaya kesehatan dan keselamatan, kerusakan peralatan, dan pencemaran lingkungan.
Variabel proses yang mempengaruhi pembentukan buih pada BOF adalah komposisi slag, kecepatan superfisial gas, temperatur bath, ukuran gelembung, kebasaan slag, densitas slag, viskositas slag, dan tegangan permukaan slag. Kecepatan gas superfisial biasanya diukur dalam meter per detik (m/s) dan merupakan kecepatan gas sebenarnya dikalikan dengan fraksi volume gas.
Komposisi terak adalah salah satu variabel proses terpenting yang mempengaruhi pembusaannya, yang berkembang sepanjang pukulan, umumnya, mendukung pembusaan. Hal ini disebabkan oleh fakta bahwa sifat fisiko-kimia terak seperti densitas, viskositas, tegangan permukaan, dan kebasaan, bervariasi dengan komposisi terak. Pembusaan pada kecepatan gas superfisial yang tinggi seperti yang ditemui dalam pembuatan baja BOF (yaitu lebih besar dari 1 m/s), cairan tertahan oleh aliran gas. Dikatakan bahwa dalam situasi ini fraksi hampa (VF) sangat bergantung pada kecepatan superfisial gas, sementara sangat bergantung pada sifat fisik terak dan cairan. Selanjutnya, pembentukan dan keberadaan penahan gas ini diatur oleh gravitasi dan gaya hambat pada cairan yang diberikan oleh gas.
Busa terak terbentuk ketika gas yang disuntikkan dan dihasilkan oleh reaksi pemurnian terperangkap oleh terak selama proses. Untuk busa terak, jumlah gas yang terperangkap oleh terak diukur dengan VF atau fraksi gas, dan VF umumnya bervariasi dalam kisaran 0,7 hingga 0,9. Gambar 2 menunjukkan kolom busa yang khas dengan lapisan busa yang berbeda menurut VF. Efek gabungan dari sifat fisik terak yang berkembang selama pukulan adalah untuk mendukung stabilisasi busa, dan ketika bertepatan dengan tingkat de-karburisasi yang tinggi pada paruh pertama pukulan, volume busa terak meningkat dengan cepat.
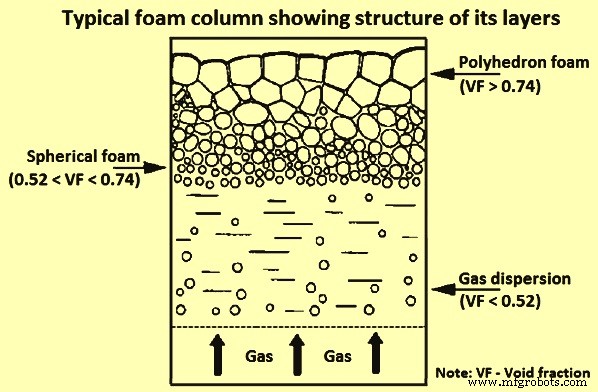
Gbr 2 Kolom busa tipikal menunjukkan struktur lapisannya
Indeks pembusaan (FI) merupakan indikasi tingkat pembusaan dan merupakan rasio antara tinggi busa dan kecepatan gas superfisial. Oleh karena itu, satuan FI adalah waktu yang biasanya berkisar antara 0,6 detik (s) hingga 1,3 detik. Dengan demikian, FI dapat diartikan sebagai ukuran waktu yang diperlukan untuk gas proses untuk melewati busa secara vertikal. Dengan laju suplai O2 yang konstan, kecepatan gas dapat diasumsikan cukup konstan selama periode dekarburisasi utama dari pukulan, yaitu tinggi pembusaan berbanding lurus dengan FI.
Sifat yang sangat penting dalam kaitannya dengan FI adalah viskositas yang tampak dari emulsi. Semakin tinggi viskositas semu, semakin tinggi FI. Konsekuensi yang jelas adalah bahwa peningkatan viskositas nyata secara otomatis menyebabkan peningkatan tinggi busa, dan dengan viskositas nyata yang cukup tinggi, busa akhirnya mulai mengalir di atas konverter, yaitu terjadi slopping. Salah satu parameter yang sangat mempengaruhi viskositas semu adalah adanya partikel padat. Sesuai penelitian, peningkatan fraksi partikel padat hanya sebesar 10%, ada peningkatan 50% dalam viskositas nyata dan setidaknya peningkatan yang setara pada tinggi busa.
Pengaruh komposisi terak terhadap pembusaannya menjadi subjek studi eksperimental, menggunakan terak CaO-SiO2-FeO pada kisaran suhu 1.250 derajat C sampai 1.400 derajat C. Terak tersebut terkandung dalam wadah alumina, dan argon (Ar ) gas disuntikkan ke busa terak. Hasil yang diamati pada pengaruh parameter yang berbeda pada pembusaan terak diekspresikan menggunakan FI, yang pertama kali digunakan untuk sistem berair. FI memiliki arti waktu tempuh rata-rata gas melalui lapisan busa dan dapat dinyatakan dengan persamaan FI =delta h/delta Vg, dan Vg =Qg/A. Di sini delta h adalah perubahan ketinggian terak, dan Vg adalah kecepatan superfisial gas, Qg adalah laju aliran gas, dan A adalah luas penampang wadah. FI diamati berubah antara 0,3 detik hingga 56 detik untuk terak metalurgi dengan komposisi berbeda. Hubungan di atas dianggap sah bila VF busa tidak tergantung pada tinggi busa. Tingkat pembusaan terak telah sering ditentukan dengan menggunakan FI.
Metode lain untuk menghitung FI dapat dinyatakan sebagai 'laju perubahan volume busa =laju pembentukan atau injeksi gas - laju perubahan volume karena pecahnya gelembung'. Oleh karena itu, FI juga dapat dinyatakan dalam bentuk persamaan FI =1/k.e, di mana, 'k' adalah konstanta laju untuk peluruhan gelembung, dan 'e' adalah VF rata-rata. Namun, definisi FI ini adalah untuk sistem keadaan tunak, yang memiliki laju aliran gas dan komposisi kimia yang hampir konstan. Namun, untuk menjelaskan kebusukan terak BOF, diperlukan FI dinamis yang memperhitungkan sifat dinamis dari pembangkitan gas dan komposisi terak yang diwakili oleh FI(d) =f(r).FI di mana f (r) =(laju pembangkitan gas + laju perubahan volume terak)/ laju perubahan volume terak. FI adalah properti dari terak yang berubah seiring waktu selama pukulan dan yang melewati maksimum.
Dalam studi lain, telah ditunjukkan bahwa FI terkait dengan sifat fisik terak. Hubungan ini menunjukkan bahwa FI meningkat dengan meningkatnya viskositas terak, sedangkan FI menurun dengan meningkatnya kepadatan dan tegangan permukaan terak.
Pengaruh kecepatan gas superfisial pada pembusaan terak
Pengaruh kecepatan superfisial gas terhadap pembusaan terak CaO-SiO2-FeO, dimana busa dihasilkan dengan menginjeksikan gas Ar telah dipelajari. Telah diamati bahwa tinggi busa meningkat secara linier dengan meningkatnya kecepatan gas superfisial.
Dalam proses reduksi peleburan, konverter beroperasi pada kecepatan gas superfisial sekitar 0,3 m/s hingga 3,0 m/s. Busa yang diamati pada kecepatan gas superfisial rendah berbeda dengan yang diamati pada kecepatan gas tinggi. Busa pada kecepatan gas superfisial tinggi (yaitu lebih tinggi dari 1 m/s) adalah terak yang diperluas, di mana seluruh volume cairan diekspansi secara seragam dalam metode turbulen dan pengadukan. Ketinggian campuran dan VF dari terak yang diperluas ini meningkat dengan meningkatnya kecepatan gas superfisial, dan itu segera runtuh dengan penghentian aliran gas. Di sisi lain, busa yang dihasilkan pada kecepatan gas superfisial rendah (yaitu 0,01 m/s sampai 0,1 m/s) seperti busa sabun, dan busa ini runtuh secara bertahap dengan penghentian aliran gas. Pengamatan ini ditemukan valid untuk kecepatan gas superfisial yang lebih tinggi yang khas untuk proses reduksi peleburan, ketika tidak ada oksida yang tidak larut yang mengubah viskositas terak.
Di sisi lain, dalam salah satu penelitian, disarankan bahwa pembusaan pada kecepatan gas superfisial yang lebih tinggi seperti yang ditemui dalam pembuatan baja BOF (yaitu lebih tinggi dari 1 m/s), cairan tertahan oleh aliran gas. Dikatakan bahwa dalam situasi ini VF sangat bergantung pada kecepatan superfisial gas, sementara sangat bergantung pada sifat fisik terak dan cairan. Selanjutnya, pembentukan dan keberadaan penahan gas ini diatur oleh gravitasi dan gaya hambat pada cairan yang diberikan oleh gas.
Pengaruh komposisi terak terhadap pembusaan terak
Komposisi terak adalah salah satu faktor terpenting yang mempengaruhi pembusaannya, yang berkembang sepanjang pukulan, umumnya, mendukung pembusaan. Hal ini disebabkan oleh fakta bahwa sifat fisiko-kimia terak seperti densitas, viskositas, tegangan permukaan, dan kebasaan, berbeda dengan komposisi terak.
Dalam salah satu penelitian, diketahui bahwa penambahan P2O5 sedikit menurunkan FI, sedangkan penambahan S sedikit menurunkan FI. FI ditemukan menurun dengan penambahan CaF2 (kalsium fluorida) secara signifikan, sementara itu meningkat terutama dengan penambahan MgO. Pengamatan ini dilakukan dalam studi untuk terak CaO-SiO2-FeO pada 1.400 derajat C, di mana injeksi gas Ar telah menghasilkan busa. Dalam studi ini, juga telah diamati bahwa FI meningkat dengan meningkatnya konsentrasi partikel.
Pengaruh penambahan FeO dan MgO pada FI terak CaO-SiO2-FeO-MgO telah menjadi subjek dari satu penelitian lain. FI telah diamati menurun dengan meningkatnya kandungan FeO hingga sekitar 20% massa FeO dalam terak dan kemudian tetap konstan hingga konsentrasi massa sekitar 32% FeO dalam terak. Penambahan MgO (magnesium oksida) juga menunjukkan kecenderungan yang sama dengan FeO dengan menurunkan indeks pembusaan dengan penambahannya pada terak 35%CaO-35 %SiO2-30 %FeO.
Saat menganalisis evolusi FI dengan komposisi terak, pengaruh penambahan MnO dan P2O5 pada FI juga patut dipertimbangkan. Pengaruh penambahan MnO dan P2O5 pada terak jenuh CaO-SiO2-30FeO-MgO masing-masing telah menjadi subjek dari satu penelitian. Telah diamati bahwa FI sedikit menurun dengan meningkatnya MnO dalam terak, sementara itu meningkat dengan penambahan P2O5 hingga 3% dan kemudian menurun dengan penambahan P2O5 lebih lanjut.
Pengaruh suhu pada pembusaan terak
Peningkatan suhu terak telah diamati untuk menurunkan indeks busa dari 35%CaO-35 %SiO2-30 %FeO-10 %MgO terak selama penelitian yang dilakukan pada kisaran suhu 1.400 derajat C hingga 1.550 derajat C. Pengamatan ini dapat dikaitkan dengan koefisien temperatur positif dari tegangan permukaan dan koefisien temperatur negatif dari viskositas. Pengaruh tegangan permukaan dan viskositas pada pembusaan terak sedemikian rupa sehingga peningkatan tegangan permukaan mendestabilisasi busa sedangkan peningkatan viskositas menstabilkan busa. Oleh karena itu, efek gabungan dari dua sifat di atas mengurangi FI dengan peningkatan suhu.
Pengaruh ukuran gelembung pada pembusaan terak
Pengamatan umum adalah bahwa terak berbusa berbanding terbalik dengan ukuran gelembung. Dengan kata lain, busa yang terdiri dari gelembung-gelembung yang lebih besar akan runtuh lebih awal dibandingkan dengan yang terdiri dari gelembung-gelembung yang lebih kecil. Pengamatan ini telah diselidiki dalam sebuah penelitian dengan menginjeksikan gas Ar melalui nozzle multi-orifice ke dalam slag tipe bath smelting. Pembusaan terak yang sama oleh gelembung yang dihasilkan dari reaksi antar muka telah dipelajari. Rata-rata diameter gelembung gelembung yang dihasilkan dari single orifice nozzle adalah 13,5 mm, sedangkan dari multi-orifice nozzle sekitar 7,5 mm. Telah diamati bahwa tinggi busa yang diukur ketika injeksi gas telah melalui nosel multi-lubang adalah sekitar 70% lebih besar daripada yang diukur ketika injeksi gas melalui nosel lubang tunggal. Gelembung yang lebih besar yang dihasilkan dari injeksi gas Ar melalui single orifice nozzle berbentuk polihedral. Di sisi lain, ketika gelembung telah dihasilkan dari CO yang dihasilkan oleh reaksi antarmuka, gelembung diamati gelembung gas bulat halus, dan busa yang dihasilkan relatif lebih stabil. Namun, dalam kedua kasus, ukuran gelembung berbanding terbalik dengan FI (Gbr 3).
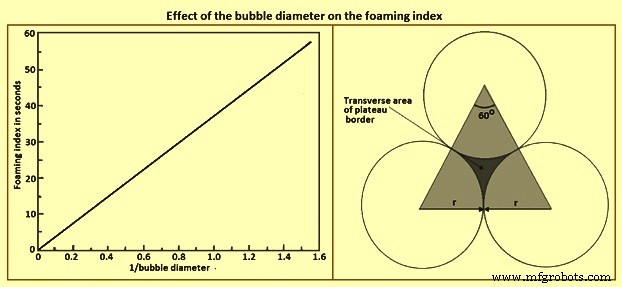
Gbr 3 Pengaruh diameter gelembung pada FI
Pengamatan ini telah dijelaskan oleh fakta bahwa peningkatan ukuran gelembung meningkatkan drainase. Terlihat bahwa daerah transversal dari perbatasan dataran tinggi seperti yang ditunjukkan pada Gambar 3 mempengaruhi kecepatan drainase. Dengan kata lain, area transversal lebih besar untuk gelembung yang lebih besar meningkatkan drainase dibandingkan dengan gelembung yang lebih kecil. Pengaruh diameter gelembung pada FI ini menunjukkan proporsionalitas terbalik antara ukuran gelembung dan FI, meskipun tingkat pengaruhnya berbeda. Namun, dalam pembuatan baja BOF, busa terak terutama diproduksi dengan menjebak gas CO di lapisan terak, dan dalam hal ini, laju dan kuantitas produksi CO, aliran fluida turbulen, dan tegangan permukaan adalah efek utama pada ukuran baja. gelembung.
Pengaruh kebasaan terak terhadap pembusaan terak
Dalam studi yang dilakukan pada terak CaO-SiO2-FeO untuk menyelidiki faktor-faktor yang mempengaruhi pembusaan, pengaruh kebasaan terak terhadap pembusaannya dipelajari. Pengamatan yang dilakukan dalam studi adalah bahwa FI melewati minimum dengan meningkatnya kebasaan. Ada penurunan awal FI dengan meningkatnya kebasaan yang disebabkan oleh penurunan viskositas dan peningkatan tegangan permukaan, karena mereka memiliki efek negatif pada FI. Komposisi CaO pada FI minimum mengacu pada komposisi liquidus, yang mengendap jika terlampaui. Oleh karena itu, setelah komposisi liquidus, penambahan CaO lebih lanjut mengendap sebagai partikel padat 2CaO.SiO2, meningkatkan viskositas dan dengan demikian menstabilkan busa.
Pengaruh kepadatan terak pada pembusaan terak
Kepadatan adalah sifat fisik penting lainnya, yang memiliki efek yang cukup besar pada pembusaan terak. Seperti ditunjukkan pada Gambar 4, kepadatan terak meningkat dengan akumulasi komponen terak seperti FeO, MnO, dan MgO, dan menurun dengan meningkatnya SiO2 dan suhu.
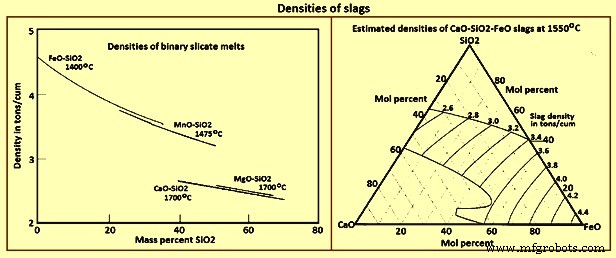
Gbr 4 Kepadatan terak
Oleh karena itu, FI menurun dengan akumulasi FeO, MnO, dan MgO, dan meningkat dengan meningkatnya kandungan SiO2 dalam terak. Lebih lanjut, FeO juga dianggap mampu menurunkan viskositas dengan meningkatnya kandungannya dalam terak. Proporsionalitas terbalik antara FI dan kepadatan terak ini ditunjukkan dalam beberapa penelitian dan terbukti bahwa indeks pembusaan berkurang dengan meningkatnya kepadatan terak, meskipun tingkat pengaruh yang berbeda ditemukan dalam penelitian yang berbeda.
Pengaruh viskositas terak pada pembusaan terak
Viskositas terak dan evolusinya selama pukulan juga memainkan peran penting dalam pembusaan terak. Viskositas terak terutama diatur oleh pembentuk jaringan seperti SiO2, dan penambahan oksida logam, seperti FeO, MgO, MnO, dan CaO, merusak struktur jaringan dan mengurangi viskositas terak.
Ini adalah pengamatan umum bahwa slopping terjadi pada beberapa menit pertama pukulan selama proses pembuatan baja BOF. Hal ini karena meningkatnya viskositas terak karena suhu yang lebih rendah dan adanya partikel kapur yang tidak larut pada awal proses, bersamaan dengan tingginya laju dekarburisasi. Selanjutnya, jika jalur terak, berada di bawah suhu cair terak, partikel fase kedua mengendap. Partikel fase kedua ini, yang ukurannya lebih kecil dibandingkan dengan gelembung busa, meningkatkan viskositas terak cair yang menstabilkan busa. Namun, volume busa meningkat dengan peningkatan viskositas hanya sampai nilai viskositas kritis, setelah itu gas mulai mengalir melalui terak tanpa berbusa. Telah ditunjukkan dalam beberapa penelitian bahwa FI meningkat dengan meningkatnya viskositas terak.
Pada dasarnya, efek viskositas adalah pada drainase dan pecahnya film gelembung di busa. Peningkatan viskositas menstabilkan busa dengan meningkatkan ketebalan film gelembung untuk memperlambat koalesensi gelembung dan dengan mengurangi aliran ke bawah cairan (yaitu drainase cair) dari film melalui perbatasan dataran tinggi.
Pengaruh tegangan permukaan terak pada pembusaan terak
Tegangan permukaan cairan ada karena gaya kohesif yang diberikan pada molekul pada permukaan cairan oleh molekul lain dalam cairan. Akibatnya, tegangan permukaan bertanggung jawab untuk pembentukan tetesan dan untuk memperlambat molekul cairan agar tidak keluar dari cairan. Dalam kasus pembuatan baja BOF, pembentukan emulsi terak/logam dan busa dipengaruhi oleh tegangan permukaan terak. Selanjutnya, perpindahan massa antara terak dan logam juga dipengaruhi oleh tegangan permukaan terak sampai batas tertentu. Tegangan permukaan besi cair murni adalah sekitar 1,8 N/m pada 1.550 derajat C, yaitu sekitar 25 kali lebih tinggi daripada air. Sebaliknya, tegangan permukaan oksida cair murni dan terak sangat rendah, berkisar antara 0,20 N/m dan 0,70 N/m.
Tegangan permukaan terak cenderung bervariasi dengan suhu dan komposisi terak. Non-logam seperti S, P, O2, dan N2 (nitrogen) adalah aktif permukaan dengan kekuatan yang berbeda dalam besi cair. Di sisi lain, oksida termasuk SiO2, P2O5, dan MnO, menurunkan tegangan permukaan terak, sedangkan Al2O3 (alumina) sedikit meningkatkan tegangan permukaan.
Tegangan antar muka antara logam dan terak juga merupakan faktor penting dalam proses pembuatan baja BOF, mirip dengan tegangan permukaan. Oleh karena itu, tegangan antar muka mempengaruhi pembentukan emulsi logam / terak dan perpindahan massa antara logam dan terak mirip dengan perilaku tegangan permukaan. Ketika tegangan antar muka pada antarmuka terak / logam rendah, proses pemurnian didorong melalui bantuan perpindahan massa antar muka dan pembentukan busa / emulsi, yang menguntungkan. Namun, tegangan antar muka yang rendah juga dapat mendorong jebakan tetesan terak oleh logam cair, dan adhesi yang kuat antara terak dan logam, yang membuat pemisahan fisik terak dari logam lebih sulit pada tahap penyadapan.
Berbagai elemen yang ditambahkan ke besi cair memberikan tingkat pengaruh yang berbeda pada tegangan antarmuka antara logam cair dan terak. Pada umumnya hampir semua unsur yang ditambahkan menurunkan tegangan antar muka besi cair. Dalam pembuatan baja BOF, O2 dan S dianggap sebagai elemen aktif permukaan terkuat dalam logam, yang sangat menurunkan tegangan antar muka. Selanjutnya, FeO dan MnO dianggap sebagai komponen oksida aktif permukaan dalam terak yang mengurangi tegangan antarmuka antara logam dan terak.
Agar bak peleburan terak menjadi busa, keberadaan komponen aktif permukaan seperti P2O5, CaF2, Fe2O3 (oksida besi), V2O5 (vanadium pentoksida) , dan Na2O (natrium oksida) sangat penting. Senyawa aktif permukaan seperti itu memiliki kemampuan untuk mengurangi viskositas, dan yang paling penting dapat mengurangi tegangan permukaan terak, memungkinkan terak untuk menjebak gas dan menghasilkan busa.
Salah satu aspek pengaruh tegangan permukaan / antar muka adalah kemampuannya untuk menentukan ukuran gelembung yang dihasilkan pada antarmuka terak / logam. Oleh karena itu, peningkatan tegangan permukaan terak dan tegangan antar muka terak/logam meningkatkan diameter gelembung, yang membuat busa tidak stabil. Di sisi lain, busa distabilkan oleh gelembung-gelembung kecil yang dihasilkan ketika tegangan permukaan logam meningkat. Selanjutnya, gelembung dari busa yang sudah diproduksi mengalami peningkatan drainase filmnya dengan peningkatan tegangan permukaan. Hal ini disebabkan oleh peningkatan hisapan cairan dalam film menuju batas dataran tinggi karena kelengkungan film gelembung meningkat dengan meningkatnya tegangan permukaan.