Memahami Pembuatan Besi dalam Studi Blast Furnace dan Dissection di Jepang
Memahami pembuatan Besi dalam studi Blast Furnace dan Dissection di Jepang
Pembuatan besi tanur sembur (BF) adalah cara yang paling layak untuk memproduksi logam panas (HM) terutama karena kinerjanya yang mapan dan terbukti, penggunaan bahan baku yang fleksibel, dan kemampuan konservasi energi panas yang tinggi. Tidak ada tanggal pasti yang tersedia untuk dimulainya pembuatan besi BF. Namun, desain proses dan rekayasa ulang yang penting mulai diterapkan di tungku pembuatan besi di Eropa sejak abad ke-14. Sejak itu, rute BF telah mendominasi sebagai proses preferensi atas metode produksi besi alternatif lainnya.
Sejak awal, proses pembuatan besi BF, untuk mempertahankan dan tetap bertahan, telah mengalami perkembangan evolusioner yang bertahan lama untuk menjadi proses yang sangat efisien. Perkembangan paling penting hingga saat ini meliputi (i) modernisasi fasilitas, (ii) peningkatan produktivitas tungku, (iii) penurunan tingkat kokas, (iv) perpanjangan masa pakai tungku, dan (v) fleksibilitas dan peningkatan material. Kemajuan teknologi yang telah dilakukan untuk meningkatkan ekonomi, efisiensi, dan membuat proses ramah lingkungan antara lain (i) berbagai praktik manajemen dan pengendalian proses, (ii) pengisian kokas pusat, (iii) operasi tekanan atas tungku tinggi, (iv ) pengoperasian tungku dengan pengayaan oksigen (O2), (v) penggantian kokas yang mahal dengan alternatif sumber karbon tambahan yaitu batu bara bubuk, gas alam, minyak bumi, dan plastik, dan (vi) masih banyak lagi. Perkembangan teknologi proses pembuatan besi BF telah membawanya dari unit produksi kecil, mengkonsumsi bahan bakar dalam jumlah besar ke kondisi sekarang di mana tungku yang dirancang untuk menghasilkan 10.000 ton HM per hari cukup umum di beberapa negara. Bahkan dengan peningkatan dramatis dalam ukuran dan keluaran BF, banyak reaksi yang terjadi di dalam tungku masih belum diketahui.
BF modern beroperasi terutama pada beban sinter, pelet, sinter/bijih besi, atau sinter/pelet. Jenis dan kualitas bahan-bahan ini bergantung pada filosofi pengoperasian masing-masing pabrik, sehingga karakteristik produksi dan pengurangan bahan-bahan ini sangat penting bagi proses BF.
Pengembangan proses BF
Perkembangan yang terjadi dalam proses BF telah diperkenalkan secara bertahap, akhirnya menjadi praktik operasi standar. Dimungkinkan untuk membuat daftar perkembangan utama dalam urutan kronologis perkiraan yang terdiri dari (i) penggunaan beban yang disiapkan secara efektif, (ii) injektor ledakan, (ii) tekanan atas yang tinggi, (iv) suhu ledakan yang tinggi, dan (v) peningkatan kontrol dari distribusi beban. Bersamaan dengan perkembangan ini, telah terjadi peningkatan ukuran fisik BF secara bertahap.
Penggunaan beban yang disiapkan
Persiapan pertama bahan beban hanyalah ukuran bijih besi yang dibebankan ke tungku. Ukuran beban yang lebih dekat meningkatkan permeabilitas tungku, memungkinkan lebih banyak angin yang dihembuskan, sehingga meningkatkan output BF. Selain itu, efisiensi reaksi reduksi juga meningkat karena penghilangan gumpalan bijih yang lebih besar, sehingga menurunkan laju kokas.
Sintering bijih besi sebelum pengisian adalah langkah penting kedua dalam persiapan beban, tetapi sintering pada awalnya dikembangkan untuk membuat limbah bahan bantalan besi seperti debu cerobong BF, kerak pabrik dan bijih halus menjadi umpan BF yang dapat digunakan. Namun, konsep ini berubah dengan cepat setelah keberhasilan yang dicapai dengan sinter self-fluxing pada pertengahan 1950-an, memungkinkan fluks dihilangkan dari beban muatan BF dan dimasukkan melalui sinter. Hal ini juga menyebabkan penurunan tingkat kokas sambil meningkatkan produktivitas BF. Situasi saat ini adalah bahwa sinter sekarang menjadi komponen beban yang mapan di pabrik BF modern dan masih dalam penyelidikan berkelanjutan untuk lebih meningkatkan sifat-sifatnya.
Menipisnya bijih besi bermutu tinggi yang tersedia membuat pemasok perlu meningkatkan produk mereka dengan cara benefisiasi diikuti dengan produksi pelet bijih besi bermutu tinggi dari konsentrat. Proses ini diterima secara luas yang mengakibatkan beban yang dibebankan ke tungku BF yang memiliki kandungan besi tinggi dan kandungan gangue rendah, yang pada gilirannya menyebabkan peningkatan lebih lanjut dalam produksi ditambah dengan penurunan tingkat kokas. Peningkatan lain yang diklaim dengan pelet adalah bahwa permeabilitas beban meningkat karena ukuran yang lebih dekat. Namun, penggunaan pelet tidak universal dan di beberapa negara BF dioperasikan terutama pada beban sinter dengan pelet dan/atau bijih besi berukuran menyumbang sebagian kecil dari keseluruhan muatan. Memang ada beberapa pandangan bahwa rasio sinter yang tinggi sangat penting untuk operasi yang stabil dari BF besar karena sinter memiliki suhu tinggi yang unggul dan sifat distribusi yang lebih baik, karena pelet mudah digulung, membuat kontrol distribusi menjadi sulit. Juga karena penggunaan sinter di BF, angin kokas yang dihasilkan di pabrik oven kokas dikonsumsi di dalam pabrik baja.
Injeksi ledakan
Ada tiga injectants yang biasanya digunakan di BF. Ini adalah (i) uap, (ii) O2, dan (iii) bahan bakar tambahan. Injeksi mempengaruhi suhu nyala, yaitu suhu nyala di zona pembakaran tuyere. Uap dan bahan bakar tambahan menurunkan suhu nyala sementara O2 meningkatkannya. Suhu nyala teoritis dapat dihitung dan sangat penting untuk menjaga kelancaran operasi dan meningkatkan produktivitas dengan sejumlah besar O2 dan bahan bakar tambahan. Suhu nyala api yang rendah mencegah reaksi dalam tungku dan menyebabkan pendinginan tungku. Temperatur nyala yang tinggi dapat merusak permeabilitas sebagai akibat dari perluasan zona lebur dan penguapan alkali dan silika (SiO2) pada beban. Untuk memastikan operasi yang lancar, perlu untuk mengontrol suhu nyala api teoritis dengan memvariasikan jumlah injektan.
Melihat ketiga injektor secara terpisah, uap bereaksi dengan kokas untuk menghasilkan hidrogen (H2) yang meningkatkan tingkat pengurangan bahan beban, sehingga menurunkan laju bahan bakar. Bahan bakar tambahan adalah injektor utama. Jenis bahan bakar tambahan yang digunakan tergantung pada kondisi setempat. Injeksi bahan bakar tambahan memberikan jumlah tambahan H2 dan karbon monoksida (CO) di BF, meningkatkan tingkat pengurangan beban, yang pada gilirannya memberikan penurunan tingkat kokas. Sangat penting untuk memastikan pembakaran sempurna bahan bakar tambahan di tuyere karena pembakaran tidak sempurna dapat merusak permeabilitas tungku, menyebabkan efek buruk pada operasi tungku. Pembakaran yang tidak memadai dapat dikendalikan dengan memberikan O2 berlebih yang cukup dalam ledakan.
Injeksi oksigen meningkatkan jumlah kelebihan O2 dan meningkatkan suhu nyala, yang melawan penurunan suhu nyala yang disebabkan oleh injeksi uap dan bahan bakar tambahan. Ini juga berguna untuk mengurangi jumlah gas bosh, sehingga meminimalkan tingkat penyaluran gas di BF dan tingkat banjir dan pemuatan. Banjir menyebabkan operasi tungku tidak teratur. Pembebanan adalah situasi ketika terak cair dicegah turun karena kecepatan gas ke atas. Pada akhirnya berat terak menjadi cukup untuk mengatasi aliran gas agar terak turun. Ketika rasio O2 dalam ledakan meningkat secara bertahap, volume gas yang dihasilkan per ton HM menurun, menyebabkan penurunan jumlah perpindahan panas dari gas ke padatan di poros, yang mengakibatkan penurunan suhu poros. Juga, peningkatan produktivitas melalui pengayaan O2 mempercepat laju penurunan beban, menghasilkan lebih sedikit waktu untuk perpindahan panas. Akibatnya, material beban memasuki zona suhu tinggi tanpa dipanaskan terlebih dahulu, sehingga mendinginkan tungku dan menyebabkan beban tergelincir dan menggantung.
Praktik penggunaan injektor memerlukan kontrol yang cermat dengan memperhatikan tiga batasan yaitu (i) batas perpindahan panas antara gas dan padatan, (ii) batas suhu nyala teoritis, dan (iii) batas pembakaran sempurna bahan bakar tambahan. Kontrol dalam batas ini menghasilkan tingkat bahan bakar yang rendah dan produktivitas yang tinggi.
Tekanan atas yang tinggi
Manfaat dari tekanan atas yang tinggi adalah mengurangi kecepatan gas di tungku sehingga memungkinkan lebih banyak waktu untuk pengurangan gas yang mengakibatkan penurunan laju bahan bakar. Kehilangan debu juga berkurang karena kecepatan gas yang lebih rendah tidak cukup untuk membawa partikel debu yang lebih kasar. Sebagai alternatif, lebih banyak angin dapat dihembuskan dan dengan demikian produksi dapat ditingkatkan sambil mempertahankan kecepatan gas yang sama di tungku, sehingga mencegah penyaluran, penggenangan, dan pemuatan. Kerugian utama adalah bahwa untuk mengakomodasi peningkatan tekanan gas, diperlukan konstruksi yang kokoh di seluruh peralatan BF dari kompor, melalui pipa hiruk pikuk, dinding tungku, tungku atas, dan pabrik pembersih gas dll, yang jelas mahal. Tentu saja bagian atas BF saja memerlukan desain khusus untuk menyamakan tekanan gas dalam sistem pengisian dan mencegah keausan pada peralatan pengisian bagian atas tungku. Kerugian lain adalah hilangnya energi dalam gas atas bertekanan tinggi, meskipun turbin pemulihan gas atas dapat memulihkan sebagian energi ini.
Meskipun ada masalah dengan penerapan tekanan atas yang tinggi dari aspek teknik, pengoperasian tanur sembur yang besar mengharuskan penggunaannya untuk (i) menurunkan laju bahan bakar, dan (ii) memungkinkan produktivitas tungku yang lebih tinggi.
Suhu ledakan tinggi
Udara yang memasuki BF melalui tuyere dipanaskan oleh pembakaran kokas, dan karenanya, semakin panas udara yang masuk, semakin sedikit kokas yang dikonsumsi dalam pemanasan lebih lanjut di dalam wilayah tuyere. Pemanasan awal udara bukanlah hal baru. Memang lebih dari seabad yang lalu kompor BF sudah ada. Namun, hanya relatif baru-baru ini bahwa suhu lebih dari 1300 derajat C telah dicapai. Pencapaian suhu yang lebih tinggi ini karena adanya modifikasi desain tungku. Modifikasi tersebut adalah (i) meningkatkan luas permukaan panas dari pekerjaan checker dengan mengubah bentuk batu bata, (ii) menggunakan refraktori berkualitas lebih tinggi yang mampu menahan suhu yang lebih tinggi, dan (iii) menyediakan ruang bakar eksternal yang juga meningkatkan luas permukaan yang dipanaskan.
Peningkatan dalam distribusi beban
Pengendalian distribusi bahan beban penting untuk meningkatkan pemanfaatan gas dan menurunkan tarif bahan bakar. Distribusi yang benar juga diperlukan untuk mengontrol bentuk zona kohesif BF, sehingga memaksimalkan produksi dan meminimalkan aliran gas di dinding BF, yang terakhir memperpanjang umur tungku.
Dengan bertambahnya ukuran tungku, distribusi material beban yang diperlukan untuk menyediakan distribusi gas yang stabil di dalam BF tidak dapat dipertahankan dengan peralatan pengisian konvensional karena perbedaan sudut kompilasi, kepadatan dan bentuk. Masalah ini sebagian telah diatasi dengan pemasangan pelindung bergerak untuk mengontrol distribusi material saat meninggalkan bel pengisian. Pengembangan sistem pengisian atas tanpa lonceng dan atas Gimble, yang memiliki saluran berputar yang mampu mendistribusikan muatan secara akurat ke posisi mana pun pada lini stok tungku, sangat membantu dalam memecahkan masalah tersebut.
Sinter bijih besi
Di banyak BF, sinter adalah komponen utama dari beban BF. Komposisi kimia sinter tergantung pada komponen lain yang membentuk beban tungku. Biasanya sinter berkisar dari fluks (CaO/SiO2 sekitar 1,2) hingga superfluks (CaO/SiO2 sekitar 1,7 hingga 2,2). Sinter fluks umumnya digunakan ketika sebagian besar beban tungku adalah sinter. Sinter super-fluks digunakan ketika sisa beban bersifat asam, sehingga menyeimbangkan kimia terak untuk memberikan komposisi terak yang dapat diterima. Sinter sangat heterogen karena sifat dari proses sintering.
Struktur sinter – Fluks, yang dicampur dengan bijih besi, bereaksi selama sintering, meleleh dan menyerang partikel bijih. Aglomerasi lengkap partikel bijih kecil dapat terjadi, tetapi umumnya partikel yang lebih besar hanya mengalami serangan permukaan. Selama pendinginan, pengendapan fase yang berbeda terjadi dalam matriks terak, hasil keseluruhan menjadi campuran fase yang jauh dari keadaan setimbang dan bahan heterogen yang fasenya bergantung pada pemisahan komponen dalam pencampuran awal, mis. di mana partikel kapur ada sebelum sintering, daerah kaya kapur terbentuk. Secara keseluruhan fase yang ada tergantung pada jumlah agen fluks yang ditambahkan. Sinter self-fluxing terutama hematit dan magnetit dengan sejumlah kecil kalsium ferit, yang dihasilkan oleh reaksi antara bijih besi dan kapur. Di sini istilah 'ferit' mengacu pada jumlah gabungan dari berbagai spesies ferit yang dapat diproduksi, tergantung pada kebasaan dan partikel bijih di zona reaksi. Saat kebasaan meningkat, ada peningkatan proporsi ferit.
Dalam sinter, biasanya, ferit terkontaminasi dengan SiO2 dan Al2O3 (alumina) dan produk tersebut dikenal sebagai SFCA (silico-ferit kalsium dan alumina). SFCA biasanya sesuai dengan rumus umum 'n1(Fe2O3).n2(SiO2).n3(Al2O3).5CaO', di mana jumlah n1,n2, dan n3 adalah sekitar 12. Kandungan kalsium cukup konstan sekitar 15 %. Dalam prakteknya biasanya pada sinter ferit yang biasa ditemukan adalah 7 Fe2O3.2SiO2.3AI2O3.5CaO, dan 9Fe2O3.2SiO2.0.5AI2O3.5CaO.
Pengurangan sinter – Jenis dan jumlah ferit yang ada dalam sinter memainkan peran penting dalam sifat reduksi. Reduksibilitas ferit tidak konstan, tetapi bervariasi dari satu jenis ke jenis lainnya. Terlihat bahwa proporsi ferit meningkat dengan meningkatnya kebasaan sinter. Namun, reducibility tidak mengikuti tren yang sama. Di antara rentang kebasaan 1,0 sampai 1,5, reducibility meningkat karena peningkatan ferit jenis CaO.2Fe2O3 dan CaO.FeO.Fe203. Pada kisaran kebasaan 1,4 hingga 1,5 reduksibilitas menurun karena penurunan proporsi hematit yang ada dalam sinter dan hilangnya CaO.2Fe203 ditambah dengan munculnya 2CaO.Fe2O3 yang relatif tidak dapat direduksi. Peningkatan kebasaan di atas 1,5 kembali menunjukkan tren yang meningkat karena munculnya CaO.Fe2O3 dan CaO.FeO.Fe2O3.
Perilaku reduksi ferit adalah kompleks karena mereka terurai agar terjadi reduksi oksida besi. Selama proses reduksi, pertama-tama oksida besi dan ferit yang lebih tinggi, yang kaya akan besi oksida, direduksi hingga hanya tersisa di-kalsium ferit dan wustit. Gas kemudian menyerang di-kalsium ferit sesuai dengan reaksi reversibel 2CaO.Fe2O3 + 3H2 =2CaO + 2Fe + 3H2O. CaO yang dibebaskan kemudian segera bereaksi dengan wustit sebagai reaksi reversibel 2CaO + 3FeO =2CaO.Fe2O3 + Fe. Reaksi kemudian berjalan sesuai persamaan sebelumnya dan seterusnya. Namun, mikro-foto menunjukkan bahwa wustit tidak hadir pada batas gas dan karenanya proses difusi antara kedua reaksi berlangsung. Studi telah menunjukkan bahwa pada permukaan oksida, ferit di-kalsium pertama-tama direduksi. Besi yang dibebaskan terpisah dalam fase oksida dan kalsium berdifusi masuk dan bereaksi dengan wustit dan sekali lagi besi memisahkan atau berdifusi ke dalam Fe3O4.
Pelet bijih besi
Selama proses produksi pelet bijih besi, bijih besi diuntungkan dengan menghancurkan dan menghilangkan bahan gangue yang dibebaskan. Umumnya beberapa kuarsa ditambahkan dalam produksi pelet asam untuk meningkatkan sifat pelet. Mayoritas pelet yang dihasilkan adalah dari jenis asam, yaitu tanpa penambahan fluks substansial yang disengaja. Selama produksi pelet asam, pelet hijau ditembakkan pada sekitar 1300 derajat C dalam atmosfer pengoksidasi. Hal ini mendorong ikatan partikel dengan (i) sintering butir hematit, (ii) oksidasi dan sintering berikutnya butir magnetit, dan (iii) ikatan terak. Yang terakhir ini disebabkan oleh peleburan sisa kecil gangue dan bentonit, yang digunakan dalam proses pelet untuk memastikan kekuatan pelet hijau yang cukup. Fase terak ini pada dasarnya terdiri dari kapur, silika, oksida besi dan sedikit alkali, magnesia, alumina, dll.
Indikasi komposisi kimia fasa terak dapat diperoleh dengan mengacu pada diagram fasa CaO-SiO2-Fe2O3. Hal yang perlu diperhatikan adalah bahwa diagram kesetimbangan harus digunakan dengan hati-hati karena di sebagian besar proses reaksi jarang terjadi pada kesetimbangan, namun diagram tersebut adalah alat yang berguna. Sangat sedikit reaksi, jika ada, yang terjadi antara butiran kuarsa dan hematit selama pembakaran dan dengan demikian pelet asam terdiri dari hematit, kuarsa, fase terak, dan dalam beberapa kasus, jika pembakaran yang cukup belum terjadi, magnetit, yang berasal dari bijih magnetit dalam campuran pelet.
Pelet asam digunakan di beberapa BF dalam beban tungku. Jumlah yang digunakan dalam beban tergantung pada praktik operasi yang diadopsi. Dalam kasus BFs beroperasi seluruhnya pada pelet asam sebagai sumber unit besi, fluks (batu kapur dan dolomit) yang dibutuhkan untuk proses pembentukan terak dibebankan dalam BF sebagai bagian dari beban.
Pelet fluks – Saat ini penggunaan pelet terfluks lebih disukai. Dalam pelet terfluks, fluks digabungkan ke dalam pelet, sehingga menghindari kebutuhan pengisian mereka secara terpisah ke dalam tungku. Pelet fluks dapat diproduksi dengan penambahan kapur, sebagai fluks, atau dolomit. Ketika kebasaan pelet meningkat dengan penambahan fluks, terjadi perubahan struktur mikro. Mengingat pelet fluks kapur, penambahan kapur memiliki pengaruh pada komposisi dan kuantitas terak, juga jumlah hematit. Penambahan kapur memungkinkan terjadinya reaksi antara hematit dan kapur untuk menghasilkan kalsium ferit CaO.Fe2O3 atau 2CaO.Fe2O3 tergantung pada konsentrasi kapur. Dengan pelet fluks, suhu pembakaran lebih rendah dari pelet asam untuk menghindari pembentukan terak yang berlebihan.
Dalam kasus pelet fluks, diharapkan untuk menemukan butir hematit dikelilingi oleh ferit kalsium yang disebabkan oleh reaksi kimia kapur. Dalam beberapa kasus, butir hematit asli dapat sepenuhnya diubah menjadi ferit kalsium, yang jelas tergantung pada ukuran butir hematit asli. Pengaruh kapur pada fase terak adalah dua kali lipat. Pertama ada peningkatan umum dalam jumlah terak dan kedua perubahan kebasaan. Komposisi yang tepat secara alami tergantung pada jumlah fase yang bereaksi, tetapi kemungkinannya dapat diduga dari diagram fase CaO-Fe2O3-SiO2. Salah satu masalah dengan pelet fluks adalah sifat reduksinya yang relatif buruk. Kekurangan pelet yang difluks kapur ini telah menyebabkan produksi pelet yang difluks dengan dolomit, bukan kapur.
Penambahan magnesium ke oksida besi menghasilkan reaksi keadaan padat antara keduanya dan peningkatan suhu leleh. Oleh karena itu dalam pelet fluks dolomit magnesio-ferit MgO.Fe2O3 atau (Mg.Fe)O.Fe2O3 diproduksi. Kuarsa tidak dapat sepenuhnya diserap dalam pelet fluks dolomit karena pelelehan antara magnesium dan silika tidak terjadi pada suhu pembakaran dan hanya reaksi yang terjadi dalam keadaan padat yang dapat berlangsung.
Mekanisme reduksi yang terkait dengan pelet asam dapat dijelaskan dengan reduksi gas, kinetika reaksi, dan reduksi langsung. Dalam kasus reduksi gas, saat O2 dihilangkan dari oksida besi, pelet asam mengikuti jalur reduksi hematit menjadi magnetit menjadi wustit (pada suhu lebih tinggi dari 560 derajat C) menjadi besi logam. Perubahan fase ini diwakili oleh reaksi gas reversibel, menggunakan CO sebagai agen pereduksi. Persamaannya adalah 3Fe2O3 + CO =2Fe3O4 + CO2, Fe3O4 + CO =3FeO + CO2, Fe3O4 + 4CO =3Fe + 4CO2, dan FeO + CO =Fe + CO2.
Mekanisme reduksi hematit telah dipelajari secara ekstensif dan telah dicatat bahwa reduksi hematit tidak terjadi dalam langkah-langkah diskrit, yaitu menjadi magnetit, kemudian menjadi wustit, dll., tetapi reduksi menghasilkan struktur kimia dari atas ke bawah, asalkan reduksi Potensi gasnya cukup tinggi, yaitu strukturnya terdiri dari partikel hematit, dikelilingi oleh lapisan magnetit, kemudian wustit dan akhirnya lapisan luar besi metalik. Wustite adalah non-stoikiometrik, yaitu kekurangan ion besi. Kekosongan ini adalah cacat penting dalam perilaku reduksi oksida besi karena memungkinkan difusi besi melalui kisi oksida besi. Penghilangan O2 dari wustite menghasilkan pengisian kekosongan ion besi pada permukaan oksida.
Pengurangan permukaan menggerakkan difusi kekosongan dan cacat elektron dari bagian dalam oksida menuju antarmuka reaksi. Dengan reduksi wustite, aliran masuk ion logam bereaksi dengan lapisan magnetit, sehingga mengurangi magnetit. Reaksi kemudian terjadi dan siklus berulang secara bertahap mengurangi magnetit.
Kinetika reduksi oksida besi telah dipelajari secara ekstensif tetapi ada beberapa pandangan yang bertentangan sehubungan dengan langkah pengendalian laju. Proses reduksi gas oksida besi memerlukan banyak langkah seperti (i) difusi gas yang bereaksi dari fase gas curah melalui lapisan batas, (ii) difusi gas melalui lapisan produk ke antarmuka reaksi, (iii) adsorpsi gas ke antarmuka reaksi, (iv) reaksi kimia pada antarmuka, (v) desorpsi gas produk dari antarmuka reaksi, (vi) difusi produk reaksi gas menjauh dari antarmuka reaksi ke permukaan partikel, dan (vii) difusi gas produk melalui lapisan batas ke dalam fase gas curah.
Meskipun terdapat konflik besar mengenai langkah atau langkah pembatas laju, umumnya reduksi oksida besi sesuai dengan persamaan yang diturunkan oleh McKewan K1 =Kw/do =ro[1 – (1- R1/3)]/t di mana K1 adalah laju kemajuan antarmuka hematit/magnetit dalam mm/menit, Kw adalah konstanta laju dalam g / sq mm / menit, do =kerapatan bola oksida besi murni dalam g/cu mm, ro adalah jari-jari bola oksida besi dalam mm, R adalah konversi pecahan hematit menjadi magnetit, dan t adalah waktu reaksi dalam menit. Dinyatakan bahwa karena laju reduksi oksida besi sesuai dengan persamaan ini, langkah pembatasan laju adalah reaksi kimia.
Hills menggunakan prinsip transpor massa untuk menunjukkan bahwa reaksi yang dikendalikan oleh perpindahan massa dan difusi saja dapat memiliki karakteristik spesifik yang sering digunakan untuk mengidentifikasi reaksi yang dikendalikan secara kimia, terutama linearitas [1 – (1 – R)1/3)] terhadap waktu . Hills mendalilkan bahwa reaksi dikendalikan oleh kedua proses (i) difusi gas melalui lapisan produk dan (ii) transportasi melalui lapisan batas di luar partikel. Bentuk persamaan laju Hills dapat dinyatakan sebagai 3[1 – (1 – R)2/3]- 2R(1- Bm) =C2.t di mana R adalah reduksi pecahan, t adalah waktu reduksi dalam detik, Bm =DE/Kg.ro, Bm adalah modulus untuk perpindahan massa, yaitu rasio resistansi difusi di dalam lapisan produk dan resistansi perpindahan massa di luar partikel, DE adalah koefisien difusi pada lapisan produk dalam sq mm/s, Kg adalah koefisien perpindahan massa ke permukaan bola yang bereaksi dalam mm/s dan ro adalah jari-jari bola dalam mm. C2 adalah konstanta untuk reaksi reduksi dan bergantung pada sifat bola oksida besi dan kondisi lingkungan.
Dalam kasus reduksi pada suhu 800 derajat C dan lebih tinggi, peningkatan suhu reduksi gas menyebabkan kenaikan laju reaksi, asalkan pelelehan partikel tidak terjadi. Peningkatan porositas juga menghasilkan peningkatan tingkat reduksi.
Mekanisme reduksi langsung oksida besi dengan karbon (C) sangat penting dalam BF dan telah ditemukan bahwa reduksi langsung hanya terjadi dalam jumlah yang cukup besar pada suhu lebih dari 900 derajat C. Reaksi reduksi langsung sebenarnya dapat dibagi menjadi persamaan FexOy + C =FexO(y-1) + CO Reduksi oleh gas adalah CO + FexOy =FexO(y-1) + CO2. Dalam reaksi ini x =1, 2 atau 3 dan y =1, 3 atau 4. Reaksi kehilangan larutan (Boudouard) CO2 + C =2CO menghasilkan CO untuk reaksi gas. Karena, reaksi reduksi langsung sebenarnya terjadi melalui reaksi reduksi tidak langsung, menunjukkan bahwa reduksi langsung oksida padat dalam proses BF tidak penting sehubungan dengan kemajuan reaksi.
Situasi dengan oksida besi cair yang bereaksi dengan C tentu saja sangat berbeda di mana area kontak antara oksida cair dan C padat jauh lebih besar daripada oksida padat dan C padat. Juga, difusi spesi yang bereaksi dan produk dalam cairan adalah jauh lebih cepat daripada dalam keadaan padat. Efek ini menyebabkan laju reaksi yang jauh lebih tinggi dalam sistem oksida cair / C padat daripada dalam sistem oksida padat / C padat. Semakin tinggi suhu reaksi semakin besar derajat reduksinya. Telah ditemukan bahwa langkah pembatas laju untuk reduksi terak kaya FeO berubah dengan tingkat reduksi. Nukleasi besi tereduksi dan reaksi kimia pada antarmuka C/cair tampaknya merupakan tahap pembatas laju sampai tercapai tingkat reduksi yang tinggi. Pada tingkat reduksi yang lebih tinggi, langkah paling lambat adalah difusi O2 melalui lapisan batas terak.
Pengaruh alkali terhadap reduksi
Alkali kembali bersirkulasi di dalam BF dengan penguapan di zona suhu tinggi dan pengendapan berikutnya pada beban dan kokas di daerah yang lebih dingin. Alkali yang diendapkan kemudian turun bersama beban dan kokas untuk akhirnya diuapkan. Sifat dari efek re-sirkulasi ini sedemikian rupa sehingga tingkat alkali yang cukup tinggi dapat terakumulasi di dalam BF yang dapat mempengaruhi pengurangan bahan beban. Penambahan alkali ditemukan untuk meningkatkan laju reduksi pelet asam dan basa. Telah diperhatikan bahwa ada tingkat optimum penambahan alkali, di atas mana laju reduksi menurun karena pembentukan terak yang ekstensif. Juga, pelet fluks dolomit menunjukkan penurunan laju reduksi ketika ada uap alkali dalam gas pereduksi. Lebih lanjut, jenis jenis alkali penting, yaitu natrium hidroksida (NaOH) adalah promotor yang lebih baik dari reaksi reduksi daripada natrium klorida (NaCl) untuk konsentrasi yang sama dari kation natrium.
Peningkatan laju reduksi yang terjadi ketika alkali ditambahkan ke oksida besi disebabkan oleh peningkatan pembengkakan yang memaparkan area permukaan yang lebih besar ke gas pereduksi. Selain itu, alkali menyebabkan reduksi kimia terkait non-permukaan yang berarti bahwa permukaan wustit terus-menerus terkena gas pereduksi alih-alih dilindungi oleh lapisan besi logam. Reduksi kimia yang tidak berhubungan dengan permukaan disebabkan oleh penggabungan kation alkali ke dalam kisi wustit yang menyebabkan homogenisasi dalam aktivitas wustit, memodifikasi perilaku nukleasi besi, sehingga mengarah pada reduksi kimia yang tidak terkait permukaan. Pembengkakan pelet tampaknya umumnya dianggap sebagai gejala kandungan alkali yang berlebihan.
Membebani perilaku di BF
Dalam masa hidup proses BF, banyak pengetahuan tentang karakteristik reduksi oksida besi, pelet dan sinter telah terakumulasi, hingga suhu reaksi sekitar 1000 derajat C. Pada suhu di luar ini, sangat sedikit yang diketahui tentang reaksi yang terjadi atau efeknya pada sifat-sifat bahan beban BF. Bahkan dengan banyaknya informasi yang tersedia tentang perilaku material beban pada suhu hingga 1000 derajat C, tidak mudah untuk menerapkannya karena alasan sederhana bahwa pemeriksaan internal BF selama operasi sangat sulit. 'Alat' utama untuk mendapatkan sampel dari pengoperasian BF adalah probe gas, probe suhu, dan probe beban, dll. meskipun cakupannya yang berguna hanya volume BF yang sangat kecil.
Hal ini adil untuk menyatakan, bagaimanapun, bahwa korelasi antara perilaku material selama reduksi dan proses BF telah cukup mapan. Sebagai contoh, diketahui bahwa bahan yang menunjukkan derajat kerusakan besar ukuran fisik selama penurunan suhu rendah menyebabkan penurunan permeabilitas tungku dalam praktek dan bahan beban yang sangat dapat direduksi menurunkan laju bahan bakar. Juga pelet yang membengkak secara ekstensif selama reduksi menyebabkan hilangnya permeabilitas tungku.
Studi diseksi
Sebuah terobosan besar mengenai perilaku bahan dalam BF datang dengan pendinginan air dari beberapa tungku operasi dan pembedahan metodis dan studi isinya. Distribusi beban di dalam BF tergantung pada urutan pengisian, bobot muatan, komponen beban, dan operasi tungku dan hasil di setiap tungku beroperasi dengan cara yang berbeda. Gambar 1 menunjukkan struktur internal di Kukioka BF no.4. Lapisan bijih dan kokas dipertahankan sampai zona leleh-pelunakan atau zona kohesif tercapai. Awal dari zona kohesif selama prosedur diseksi telah dipastikan dengan peningkatan ketahanan fisik untuk menghilangkan material dengan cara mekanis. Zona kohesif adalah tempat bahan mulai melunak dan akhirnya meleleh. Penemuan bahwa zona kohesif tidak dalam satu wilayah tungku, tetapi didistribusikan dalam bentuk geometris yang wajar adalah salah satu wawasan utama reaksi yang terjadi dalam BF selama operasinya.
Ditemukan bahwa struktur zona kohesif bervariasi tergantung pada operasi tungku. Sebagai contoh, Gambar 1 juga menunjukkan struktur yang ditemukan di tiga tungku yang berbeda. Hirohata BF no. Gambar 1 menunjukkan lapisan lunak berbentuk 'donat' yang tersusun dalam struktur 'V' terbalik, sedangkan Kukioka BF no.4 memiliki zona kohesif berbentuk 'W'. Higashida BF no.5 mengungkapkan 'V' terbalik yang terdistorsi yang disebabkan oleh operasi tungku yang tidak teratur sebelum operasi pendinginan.
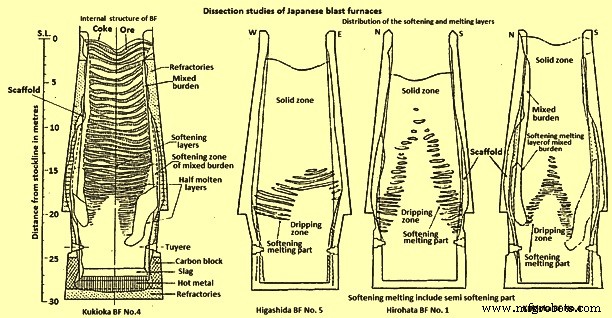
Gbr 1 Studi diseksi tanur tinggi Jepang
Tingkat pengurangan – Kajian tingkat pengurangan pada setiap lapisan beban Hirohata BF no. 1 dan Kukioka BF no.4 telah menghadirkan fitur-fitur menarik. One of the interesting features is the fact that very little reduction occurs until the burden reaches the cohesive zone, wherein reduction proceeds rapidly. One of the major problems with water quenching is the possible reoxidation of the burden material during the cooling period and laboratory tests were conducted to determine the extent of reoxidation which might be taking place. One study was made to measure the reoxidation of sinter, in the laboratory, under the same cooling conditions existing during quenching of a BF, using a series of different initial reduction levels. The another study used another technique employing burden materials of various reduction degrees cooled from three different temperatures (400 deg C, 800 deg C and 1000 deg C) at a cooling rate of 200 deg C per hour in a nitrogen (N2) atmosphere. In this study it has been found that although the reduction temperatures and reduction degrees were different, the final reoxidation degree was around constant at 20 % to 25 %, i.e. the reoxidation increased in proportion to the initial reduction degree. At temperatures below 300 deg C, no reoxidation occurred. The result of these experiments is that the reduction levels were required to be increased, for example, from 10 % to 30 % to 15 % to 40 %. These corrected levels were in agreement with the reduction levels found in Russian dissection studies on a N2 quenched furnace.
Temperature profiles – The temperature isotherms within the furnaces were estimated by a combination of several methods. In one method, ‘Tempil’ pellets encased in numerous graphite holders were charged prior to blowing out the furnaces. This technique allowed the estimation of the temperature within the range 200 deg C to 1800 deg C, but one of the problems with this technique was that there was no method of controlling the distribution of the graphite holders within the BF. The other methods employed were measurement of the extent of coke graphitization, thus estimating the temperature between 1200 deg C and 1700 deg C. Measurement of the coke electrical resistance, which allowed temperature estimation between 1100 deg C and 1700 deg C and finally the degree of iron ore fusion was measured to estimate temperatures within the range of 900 deg C to 1400 deg C.
Comparing the isotherms with the distribution of the softening-melting burden layers (Fig 1 and Fig 2), it was found that the cohesive zone exists over a temperature range of around 1100 deg C to 1500 deg C for BFs operating mainly on sinter burdens.
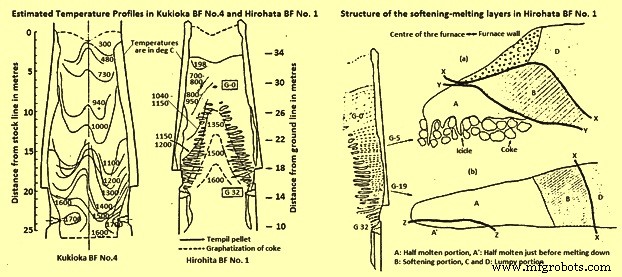
Fig 2 Estimated temperature profiles in Kukioka BF no. 4 and Hirohata BF no. 1 and structural of the softening-melting layers in Hirohata BF no. 1.
Burden layer structure within the cohesive zone – The type of structure of an individual burden layer in the cohesive zone depends upon the position of the layer within the BF. Two layers from Hirohato BF no.1 are shown in Fig 2. Layer G-5 is near the apex of the cohesive zone, while layer G-19 is situated near the base of the cohesive zone. Layer G-5 has four distinct zones, two of which are lumpy or granular portions (C and D). Layer G-19, on the other hand, contains only one lumpy portion, D. Apart from the obvious shape differences between the layers, the other main difference is the replacement of the icicles’ in layer G-5 by a half-molten portion just prior to melting down, A in layer G-19.
As seen earlier a substantial amount of reduction takes place in the cohesive zone and this has been proved by the reduction data obtained for each portion as given in Tab 1, and Tab 2. The figures are on the low side, as reoxidation, caused by the act of water quenching, certainly have taken place. The reason for the high reduction level of portion C is attributed to the slightly lower reduction temperature while in contact with the coke.
Tab 1 Degree of reduction of the burden materials in the softening-melting layers of Hirohata BF no. 1 |
Softening-melting layer | Portion* | Reduction degree % |
| | Sinter | Ore lump | Pellet |
G-5 | A | 65.6 | 65 | 79.3 |
C | 72.8 | 68.2 | 81.2 |
D | 11.5 | 12.3 | 14.6 |
G 19 | D | 35.4 | 36.6 | 41.3 |
* B:Softening portion, C and D:Lumpy portion |
Tab 2 Degree of reduction of the pellets in the lumpy portion |
Softening-melting layer | Sampling position (distance from the boundary*) (m) | Mean value of the reduction of the sample pellets (%) |
G3 | 2 | 12.7 |
0.2-around 0.3 | 23.1 |
G10 | 1 | 14.1 |
0.2-around 0.3 | (55)** |
G12 | 1.3 | 13.9 |
0.9 | 14.3 |
0.5 | 12.3 |
* Between the lumpy and softening portions |
** The value of the reduced pellet being not reoxidized |
The thickness of the softening-melting layers in Hirohata BF no. 1 ranged from 400 mm to 500 mm, in the case of the upper layers, to 70 mm – 100 mm for the layers near the base of the cohesive zone. The diminishing thickness is due to compaction, caused by the pressure exerted by the weight of material above the layer and also because of a natural thinning of material due to the increase in furnace diameter as the material descends. In the softening portions iron ore granules were combined in contact with each other. Sinter particles in the layers deformed very little, unlike pellets, which showed signs of deformation.
The process of pellet metallization can take place in one of three modes namely (i) the metallic iron is uniformly distributed within a pellet, (ii) a metallic shell is formed, leaving a wustite core, and (iii) wustite within the pellet reacts to form a slag and moves towards the metallic iron shell, leaving a central cavity. The reason for these three possible modes is not connected with the distribution within the softening-melting layer, but can be due to differences between the pellets or uneven gas flow in the softening-melting layer.
It has been found that the half molten portion consisted of highly compacted metallic iron and a small quantity of slag. Any limestone or olivine present remained unslagged. The icicles extend into the coke voids and consist of a metallic shell with a hollow interior, with small droplets of slag adhering to the iron. The higher the softening-melting layer within the furnace, the greater the length of the icicles, e.g. level G-1 produced some icicles of several hundreds of millimeters in length, while the lower layers produced icicles only 10 to 20 millimeters long.
The structure of the softening-melting layers in Kukioka BF no.4 was basically identical to those described for Hirohata BF no.1, except the thinner burden layers made the structure less distinct and the icicles smaller.
Slag composition changes – The major chemical change of the slag phase in the softening-melting layers is a decrease in the FeO content as the slag trickles down from the melting portion. Although large differences were detected by x-ray microanalyses of slags in portion A, ranging from 2 % to 20 % FeO, depending upon the location, the FeO content of the slag immediately prior to separation from the softening-melting layer was only 2 % to 3 %. The type of slag was not significantly different to that found in the normal sinter product, but in the ore granules a considerable quantity of fayalite was produced. Descent of the slag results in a gradual change in composition. The gradual increase in the CaO/SiO2 ratio is attributed to fluxing with limestone and a drop in the SiO2 content, caused by SiO2 reduction. The rise in Al2O3 is created by the incorporation of coke ash into the descending slag.
Metal composition changes – Considering the changes in metal composition as it descends the furnace; the carbon content of the metal in the half-molten portion of the softening-melting layer is around 0.2 % in the upper part and 0.35 % to 0.57 % in the lower part. The source of C in these half-molten layers is attributed to the carburizing action of the CO, except for the metal in contact with coke. Similar trends are visible in the layers found in Kukioka BF no.4. The rise in the C content of the icicles is attributed to the metal being in direct contact with particles of coke. Two distinct processes have been identified which are operating for the separation of metallic iron from the layers. The first mechanism is via the icicles which form at 1350 deg C to 1400 deg C and drip into the coke bed. Reduction of the iron oxides present in the icicles occurs rapidly to produce metallic iron. The second process occurs in layers in which no icicles form. In this situation, the metallic iron is carburized by the underlying coke until it reaches a C level such that melting can occur at the pertaining temperature. In this case the temperature of meltdown is around 1500 deg C.
The question of the mechanism of silicon pick-up by the metal within the furnace has been the subject of considerable discussion. Studies carried out in the experimental BF at Liege, Belgium fitted with sampling probes have found that the silicon level rise gradually from the melting zone to the hearth, such that 75 % of the final HM silicon is achieved by the time the metal reached the tuyere level. The Japanese dissection studies on the other hand reveal that the silicon level of the metal at the tuyere level is far in excess of that of the tapped HM. An explanation for this discrepancy between the two groups of studies can be that silicon pick-up had occurred during the process of water quenching the Japanese furnaces. During the experiments conducted to determine the probability of silicon pick-up during quenching, it was found that silicon pick-up from any slag present could be a possibility. Hence, this is to be borne in mind when analyzing the Japanese dissection data.
The sulphur (S) level of the metal within the softening-melting region is much higher than the concentration in the tapped HM. In the granular zones very little increase in S level occurs, which can be due to the materials in the softening-melting zone absorbing the S from the ascending gases, rather than a lack of absorption capacity by the burden in the granular zones. The lack of substantial quantities of S in the gas in the stack of the furnace can explain the horizontal profile at temperatures below 800 deg C. Further, as the temperature and slag basicity rise, the distribution of S between the slag and metal increases accordingly. Some idea of how S recirculates within the BF can be seen in Fig 3 in which the circulation of S within Hirohata BF no. 1 is shown.

Fig 3 Circulation of sulphur within Hirohata BF no. 1
Size distribution – The change in physical size of the burden components during their descent was determined from the quenched furnace data and one of the major problems with this part of the study was that breakdown of material occurs during the quenching operation. Degradation of sinter reaches a maximum at temperatures of 400 deg C to 600 deg C and increases with the retention time. At levels of reduction in excess of 30 %, very little degradation occurs. Estimation of the cooling pattern of Kokura BF no.2 shows that the burden materials are exposed for a lengthy period of time to conditions which lead to considerable breakdown. The effect of the water quenching operation on the degradation of sinter was calculated. This calculation indicates that the sinter degradation increases with time after blow out and considerable degradation occurs in the region around the middle of the shaft.
Applying this to a centre working furnace (centre working means that the majority of the gas flows up the central axis of the furnace), it has been noticed that the degradation of sinter in the central zone of the furnace, where the reduction degree is high, is mainly caused by the reduction processes during operation. The situation in the peripheral zone is that the reduction degree is low and in this situation the breakdown is mainly caused by the long residence time of materials around 500 deg C during blowing out of the furnace. This was illustrated with the dissection results for the centre working Hirohata BF no.1. Another factor in maintaining the size of the burden materials is that in the central region of Hirohata BF no. 1, cracks if generated fused immediately because of the high temperatures and the rapid reduction taking place. Degradation is generally a problem having maximum concerns with sinters. Examination of the size distribution of pellets revealed that they were hardly pulverized and maintained their original shape.
Influence of gas flow – To further prove that the determination of the shape of the cohesive zone is by the gas flow within the furnace, core samples were taken from the Hirohata BF no.1 and Kukioka BF no.4 and their permeability was determined. Then their permeability was related to gas flow and gas velocity distribution profiles were prepared. These profiles can be directly related to the softening-melting layer distribution. The gas flow in the lower part of the BF is fast, 7 m/sec to 9 m/sec but slows considerably in the softening-melting layers to 2 m/sec to 4 m/sec thus indicating the poor permeability of the softening-melting layers. As the gas ascends the shaft its velocity naturally decreases due to the drop in gas temperature.
Cohesive zone control
It has been shown that the shape of the cohesive zone varies from BF to BF and much attention needs to be given for its control. The control of the cohesive zone is very dependent upon burden distribution. For maximum production, at the expense of fuel rate, a strong centre working profile is to be adopted, but if the fuel rate is to be minimized, then a less centre working practice is to be followed. Indeed, this is very much visible when comparing a strong centre working furnace, like Hirohata BF no.1 with moderate centre working furnace, like Kukioka BF no. 4. This point can be well explained by relating productivity to the height of the cohesive zone above the tuyeres (Fig 4). The higher the position of cohesive zone in the furnace, the greater is the productivity, although at the expense of an increase in fuel rate.
Another point concerning control of the cohesive zone is its effect on the refractory lining. If the wall temperature of the furnace is too high, then refractory wear is appreciable and one can expect a reduced life of the BF. Thus, for maintaining the refractory thickness, it is necessary to control the cohesive zone so that the wall temperatures are maintained at minimum levels.
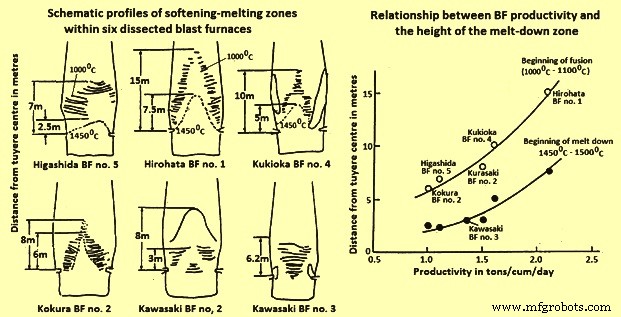
Fig 4 Schematic profiles of softening-melting zones and relationship BF productivity and height of the melt-down zone
Melting processes
The role of S in the melting process is governed by the Fe-S-O phase diagram. There is a necessity of a reaction between solid metallic iron and wustite in the burden with gaseous S, in the ascending gases. These phases react to form a eutectic of chemical composition 24 % S, 9 % O2, and 67 % Fe, having a melting point of 915 deg C. Once formed this liquid gains temperature as it descends the furnace, dissolving solid metallic iron and wustite which cause a change in liquid composition along a path until at certain point, the liquid splits into two conjugate liquid phases. Further increases in the temperature cause first part of the liquid to dissolve more solid iron, moving its composition along a path while the second part of the liquid dissolves more iron oxide and moves along the another composition path. Thus there are two phases (i) a liquid metal phase, and (ii) a liquid slag phase. The presence of silica in the system does not appreciably alter this mechanism. Indeed it moves the miscibility gap. Hence the separation of the nascent liquid into liquid metal and liquid slag phases occur at lower temperatures.
Once formed the two liquids go their own separate ways. The liquid metal dissolving solid iron, C and S become the final metal phase. The slag during its descent dissolves alumina, silica and lime from the coke ash, burden gangue and fluxes to form the final slag phase. A study has also shown that that the presence of hydrogen sulphide, in a CO / N2 gas mixture, lowered the melting point of iron ore sinters and pellets due to the formation of the liquid Fe-S-0 phase.
Alkalis are also thought to be closely associated with the initial melting process in the BF. Study with regards to the distribution of alkali, shows that the alkali is concentrated in the softening-melting layers. The reason for this is that alkali compounds, inherent within the burden and coke charged into the furnace are reduced and at temperatures in excess of 800 deg C to 900 deg C, the alkalis vapourize, as a metallic element or as a cyanide, and are swept into the softening-melting layers where they concentrate . As the softening-melting layers descend the alkali evaporates and continues the cycle.