Teknik Pengujian Non-Destruktif
Teknik Pengujian yang Tidak Merusak
Mungkin ada cacat mikroskopis yang melekat pada bahan karena ketidaksempurnaan kisi kristal. Juga, proses manufaktur seperti pengelasan, pengecoran, penempaan, dan perawatan permukaan, dll. dapat menyebabkan cacat atau cacat lebih lanjut. Selanjutnya, bahan digunakan dalam berbagai kondisi stres, kelelahan, dan korosi, yang dapat membuat cacat tambahan atau memperburuk yang ada. Kegagalan material biasanya terjadi ketika ketidaksempurnaan ini mencapai proporsi yang berbahaya sehingga bagian material yang tersisa tidak dapat menahan tekanan yang dialaminya, sehingga menjadi ulet atau rapuh. Oleh karena itu, ada kebutuhan untuk mendeteksi ketidaksempurnaan ini dalam bahan dan mengevaluasinya dalam hal sifat, ukuran, dan lokasinya. Langkah-langkah lebih lanjut diperlukan untuk menilai tingkat keparahan ketidaksempurnaan untuk memutuskan apakah bahan tersebut diterima, diterima setelah diperbaiki, atau harus ditolak dan dibuang.
Pengujian non-destruktif (NDT) adalah teknik memeriksa, menguji, atau mengevaluasi bahan, komponen, atau rakitan untuk ketidaksempurnaan yang juga dikenal sebagai diskontinuitas, atau perbedaan karakteristik tanpa merusak kemampuan servis bagian atau sistem. Dengan kata lain, ketika pemeriksaan atau pengujian selesai bagian tersebut masih dapat digunakan. Teknik ini dapat diterapkan atas dasar pengambilan sampel untuk penyelidikan individu atau dapat digunakan untuk pemeriksaan 100% bahan dalam sistem kendali mutu produksi. Anda dapat memeriksa dan/atau mengukur bahan atau struktur tanpa merusak tekstur permukaan, integritas produk, dan kegunaannya di masa mendatang.
Meskipun NDT adalah konsep teknologi tinggi, evolusi peralatan telah membuatnya cukup kuat untuk aplikasi di lingkungan industri apa pun pada setiap tahap pembuatan. Aplikasinya berkisar dari produksi baja hingga inspeksi lokasi komponen yang sudah beroperasi. Tingkat keterampilan tertentu diperlukan untuk menerapkan teknik NDT dengan benar untuk mencapai jumlah maksimum informasi mengenai produk, dengan umpan balik konsekuen ke fasilitas produksi. NDT bukan hanya sebuah metode untuk menolak material di bawah standar tetapi juga merupakan jaminan yang menentukan material yang dianggap baik itu baik. Teknik ini menggunakan berbagai prinsip. Tidak ada metode tunggal di mana kotak hitam dapat dibangun untuk memenuhi semua persyaratan dalam semua keadaan
Bidang NDT sangat luas dan interdisipliner yang memainkan peran penting dalam pemeriksaan komponen dan sistem struktural sehingga mereka menjalankan fungsinya secara andal. Standar tertentu juga telah dibuat untuk menjamin keandalan pengujian NDT dan mencegah kesalahan tertentu baik karena kesalahan pada peralatan yang digunakan, kesalahan penerapan metode atau keterampilan dan pengetahuan para pemeriksa. Tes NDT yang berhasil memungkinkan untuk menemukan dan mengkarakterisasi kondisi dan kekurangan material. Teknik NDT biasanya membutuhkan keterampilan operator yang cukup besar dan interpretasi hasil tes secara akurat bisa jadi sulit karena hasilnya bisa subjektif.
Nama teknik NDT sering mengacu pada jenis media penetrasi atau peralatan yang digunakan untuk melakukan pengujian. Teknik NDT dapat diklasifikasikan sebagai teknik konvensional dan sebagai teknik non-konvensional. Teknik NDT konvensional meliputi (i) inspeksi visual atau optik, (ii) pengujian penetran cair, (iii) pengujian partikel magnetik, (iv) pengujian arus eddy, (v) pengujian radiografi, dan (vi) pengujian ultrasonik. Teknik NDT non-konvensional hanya digunakan untuk aplikasi khusus dan mencakup radiografi neutron, emisi akustik, pengujian inframerah, teknik gelombang mikro, pengujian kebocoran, holografi, pengujian gelombang terpandu, radar penembus tanah, dan pengujian laser, dll.
Elemen penting yang umum untuk sebagian besar teknik NDT adalah (i) media penyelidik, (ii) sampel uji yang sesuai untuk media yang digunakan sehingga diskontinuitas dapat dideteksi, (iii) detektor yang mampu mengukur distribusi atau perubahan media, (iv) teknik untuk merekam atau menampilkan informasi yang diterima dari detektor yang sesuai untuk evaluasi, dan (v) operator yang dilatih untuk menginterpretasikan umpan balik detektor untuk mengevaluasi hasil.
Teknik NDA memberikan indikasi selama pengujian. Definisi istilah 'indikasi' yang berlaku untuk NDT adalah 'tanggapan atau bukti tanggapan yang diungkapkan melalui NDT yang memerlukan evaluasi lebih lanjut untuk menentukan signifikansi sebenarnya'. Ketika teknik NDT tertentu diterapkan pada suatu bagian maka ada respon. Respon ini merupakan indikasi. Istilah 'respons' dimaksudkan untuk berarti (i) 'bleed out' saat melakukan pengujian penetran cair, (ii) penumpukan partikel saat melakukan pengujian partikel magnetik, (iii) perubahan densitas pada film radiografi jika terjadi pengujian radiografi, (iv) sinyal saat melakukan pengujian ultrasonik, dan (v) defleksi meter, sinyal, atau perubahan digital saat melakukan pengujian arus eddy. Setelah respons diamati, operator yang melakukan pengujian diharuskan untuk menafsirkannya, dan kemudian mengkategorikannya ke dalam salah satu kelompok indikasi yaitu (i) salah, (ii) tidak relevan, atau (iii) diskontinuitas relevan atau benar.
Tak satu pun dari teknik NDT memberikan solusi untuk semua masalah yang mungkin, yaitu mereka bukan alternatif opsional melainkan saling melengkapi. Prinsip dasar, aplikasi tipikal, kelebihan dan keterbatasan teknik konvensional dijelaskan di bawah ini.
Pemeriksaan visual atau optik
Teknik inspeksi visual dan optik (Gbr 1) digunakan untuk memeriksa kondisi permukaan suatu komponen. Pengujian visual secara luas digunakan untuk hampir setiap kondisi permukaan yang mungkin. Pada dasarnya, pengujian visual dan optik dapat menjadi sederhana dan mudah. Paling sederhana, komponen yang bersih dapat diperiksa oleh operator dalam cahaya yang memadai tanpa peralatan, bisa semudah itu. Sering kali, operator mengharuskan penggunaan peralatan optik untuk membantu pemeriksaan, yang dapat berkisar dari lensa pembesar genggam hingga fiber-scope fleksibel, atau sistem video jarak jauh.
Operator berpengalaman, dalam kondisi optimal, dapat mendeteksi retakan kecil sekalipun. Pengulangan adalah, bagaimanapun, masalah. Jika kondisi tidak dioptimalkan, operator yang sama dapat melewatkan retakan yang sama pada komponen yang sama pada pemeriksaan ulang. Inilah sebabnya mengapa, alat bantu optik sering digunakan untuk memberi operator kesempatan terbaik untuk menemukan kondisi gangguan sesering mungkin. Pemeriksaan harus dilakukan di lingkungan yang bersih dan nyaman dengan pencahayaan yang memadai.
Perhatian harus diberikan pada keselamatan, posisi kerja dan kondisi atmosfer. Inspeksi membutuhkan konsentrasi yang cukup besar oleh operator. Pencahayaan sangat penting dan dapat sangat mempengaruhi hasil. Cahaya alami adalah jenis cahaya terbaik untuk melakukan inspeksi visual. Cahaya buatan juga dapat digunakan untuk inspeksi visual, namun operator harus memastikan bahwa tingkat cahaya yang benar dinyatakan dalam spesifikasi atau prosedur yang digunakan.
Komponen harus bersih dan bebas dari lapisan pelindung, misalnya kotoran atau cat dapat mengaburkan kondisi permukaan yang dicari. Sangat penting bagi operator untuk memiliki pelatihan dan pengalaman yang memadai sebelum melakukan inspeksi visual. Operator juga harus memiliki penglihatan yang baik. Seperti diketahui, mata adalah instrumen yang sangat canggih tetapi tidak melihat segalanya. Ini dirancang untuk memfokuskan cahaya ke retina, mengubah cahaya menjadi impuls saraf dan mengirimkannya ke otak. Otak kemudian memproses informasi ini dan membentuk gambar yang terlihat. Ini membawa kita pada persepsi, yang merupakan perbedaan antara realitas fisik dan pandangan yang menurut para inspektur mereka lihat. Inspektur yang berbeda menafsirkan informasi yang masuk dari mata secara berbeda, sehingga mereka semua melihat pemandangan fisik yang sama dengan sedikit berbeda.
Ilusi Muller-Lyer (Gambar 1) menunjukkan perbedaan antara persepsi dan kenyataan. Poros kedua anak panah itu sama panjang tetapi tampak berbeda. Perbedaan persepsi antara dua inspektur tergantung pada pelatihan dan pengalaman dan keadaan mental dan fisik pengamat pada saat pengamatan dilakukan. Persepsi dapat dipengaruhi oleh kelelahan dan kesehatan. Kelelahan mengurangi efisiensi dan kemampuan visual pengamat. Masalah-masalah ini menyebabkan interpretasi data fisik yang tidak akurat. Inspeksi yang ideal adalah inspeksi yang semua faktornya yaitu pelatihan, pengalaman, pencahayaan, dan kondisi lingkungan dioptimalkan.
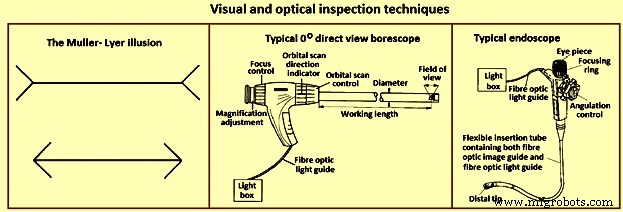
Gbr 1 Teknik inspeksi visual dan optik
Secara garis besar, inspeksi visual dibagi menjadi dua jenis teknik melihat. Teknik pertama adalah melihat langsung. Dalam jenis tampilan objek ini, objek berada di hadapan operator secara langsung. Ini dapat dilakukan tanpa bantuan atau dengan menggunakan peralatan. Yang kedua adalah melihat jarak jauh. Dalam hal ini, melihat objek tidak dilakukan di hadapan operator secara langsung. Ini dilakukan dengan menggunakan peralatan khusus.
Inspeksi visual dapat diterapkan dengan sukses ke hampir semua hal. Ini dapat digunakan untuk menemukan berbagai jenis kondisi permukaan, dari diskontinuitas, seperti korosi atau retakan, hingga efek belang pada permukaan yang dicat. Operator perlakuan panas yang berpengalaman bahkan dapat memperkirakan suhu suatu komponen dari tampilan visualnya setelah dipanaskan hingga pijar, seperti baja merah ceri kusam berada pada sekitar 550 derajat C.
Operator sering diminta untuk menemukan diskontinuitas kecil. Ini bisa sangat sulit dengan mata telanjang, jadi alat bantu optik diperlukan. Beberapa alat bantu optik yang paling umum adalah (i) lensa pembesar genggam (biasanya dari perbesaran 1,5x hingga perbesaran 10x), (ii) pembesar pengukur yang menggabungkan skala pengukuran untuk memungkinkan kondisi permukaan diukur seperti anglepoise kaca pembesar yang memiliki perbesaran hingga 10x dan sering kali memiliki tabung fluoresen melingkar yang terpasang untuk memberikan penerangan yang seragam, (iii) mikroskop yang memiliki berbagai jenis dan tersedia dalam berbagai rentang perbesaran, (iv) borescopes kaku yang merupakan bagian yang sangat baik dari peralatan untuk memeriksa bagian dalam tabung atau pipa (Gbr1), (v) perangkat serupa yang disebut endoskop (Gbr 1) yang lebih fleksibel daripada borescopes karena penggunaan serat optik untuk pemandu cahaya dan pemandu gambar, dan ( vi) untuk meningkatkan kualitas gambar, sistem optik borescopes dapat diganti dengan kamera video mini, yang dapat berisi tabung gambar, yang menggunakan berkas elektron untuk memindai target fotokonduktif, yang dikenal sebagai cahaya se nsor, atau sebagai alternatif yang dapat berisi perangkat pencitraan solid-state, seperti perangkat yang dipasangkan dengan daya atau perangkat yang diisi daya.
Pengujian penetran cair
Prinsip dasar pengujian penetran cair (Gbr 2) adalah ketika cairan (penetran) dengan viskositas sangat rendah (sangat cair) diterapkan ke permukaan suatu bagian, ia menembus ke dalam celah dan rongga yang terbuka ke permukaan. Setelah penetran berlebih dihilangkan, penetran yang terperangkap dalam rongga tersebut mengalir kembali, menciptakan indikasi. Pengujian penetran dapat dilakukan pada bahan magnetik dan non-magnetik, tetapi tidak bekerja dengan baik pada bahan berpori.
Dalam rangka penurunan sensitivitas dan penurunan biaya, proses penetran cair dapat didaftar sebagai (i) penetran pewarna fluoresen pasca emulsi, (ii) penetran pewarna fluoresen yang dapat dilepas pelarut, (iii) penetran pewarna fluoresen yang dapat dicuci dengan air, (iv) terlihat pasca emulsi penetran pewarna, (v) penetran pewarna tampak yang dapat dilepas dengan pelarut, dan (vi) penetran pewarna tampak yang dapat dicuci dengan air.
Keuntungan dari pengujian penetran cair adalah (i) biaya yang relatif rendah, (ii) teknik NDT yang sangat portabel, (iii) sangat sensitif terhadap diskontinuitas yang halus dan rapat, (iv) dapat diterapkan pada berbagai bahan, dan (v) inspeksi area yang luas . Keterbatasan teknik penetran cair adalah (i) permukaan uji harus bebas dari semua kotoran, minyak, lemak, cat, dan karat, dll., (ii) hanya mendeteksi diskontinuitas permukaan, (iii) tidak dapat digunakan pada pori-pori dan sangat permukaan kasar, (iv) penghilangan semua bahan penetran, setelah pengujian, sering diperlukan, dan (v) tidak ada metode yang mudah untuk menghasilkan rekaman permanen.
Dalam teknik ini, penetran dapat 'terlihat', artinya dapat dilihat dalam cahaya sekitar, atau berpendar, yang membutuhkan penggunaan cahaya 'hitam'. Proses penetran zat warna tampak ditunjukkan pada Gambar 2. Saat melakukan pengujian penetran cair, permukaan yang diuji harus bersih dan bebas dari bahan atau cairan asing yang dapat menghalangi penetran memasuki rongga atau celah yang terbuka ke permukaan bagian. Setelah menerapkan penetrant, dibiarkan tetap di permukaan untuk jangka waktu tertentu (penetrant dwell time), kemudian bagian tersebut dibersihkan dengan hati-hati untuk menghilangkan kelebihan penetrant dari permukaan. Saat melepas penetrant, operator harus berhati-hati untuk tidak menghilangkan penetrant yang mengalir ke dalam rongga. Lapisan ringan pengembang kemudian diterapkan ke permukaan dan waktu disediakan (waktu tinggal pengembang) untuk memungkinkan penetran dari rongga atau celah meresap ke dalam pengembang, menciptakan indikasi yang terlihat. Mengikuti waktu tinggal pengembang yang ditentukan, bagian tersebut diperiksa secara visual atau dengan bantuan lampu hitam untuk penetran fluoresen. Sebagian besar pengembang adalah bubuk halus seperti bedak putih yang memberikan kontras warna dengan penetran yang digunakan.
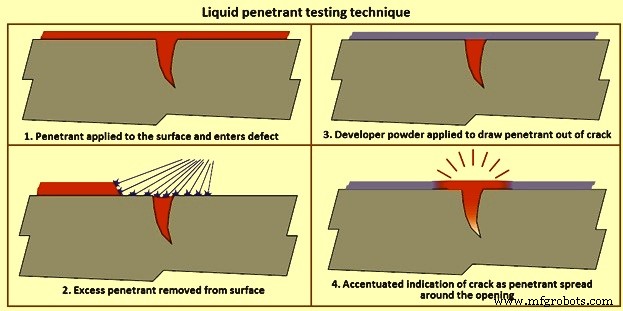
Gbr 2 Teknik pengujian penetran cair
Pelarut lepas penetran adalah penetran yang membutuhkan pelarut selain air untuk menghilangkan kelebihan penetran. Penetran ini biasanya terlihat di alam, biasanya diwarnai dengan warna merah cerah yang sangat kontras dengan pengembang putih. Penetrant biasanya disemprotkan atau disikat ke bagian, dan kemudian setelah waktu tinggal penetran selesai, bagian dibersihkan dengan kain yang dibasahi dengan pembersih penetran setelah itu pengembang diterapkan. Setelah waktu tunggu pengembang, bagian tersebut diperiksa untuk mendeteksi kebocoran penetran yang muncul melalui pengembang.
Penetran yang dapat dicuci dengan air memiliki pengemulsi yang termasuk dalam penetran yang memungkinkan penetran dihilangkan dengan menggunakan semprotan air. Mereka paling sering diterapkan dengan mencelupkan bagian dalam tangki penetran, tetapi penetran dapat diterapkan ke bagian besar dengan penyemprotan atau menyikat. Setelah bagian sepenuhnya tertutup dengan penetrant, bagian ditempatkan pada papan pembuangan untuk waktu tinggal penetran, dan kemudian dibawa ke stasiun bilas di mana itu dicuci dengan semprotan air saja untuk menghilangkan kelebihan penetran. Setelah kelebihan penetrant telah dihapus, bagian tersebut dapat ditempatkan di pengering udara hangat atau di depan kipas angin lembut sampai air telah dihapus. Bagian tersebut kemudian dapat ditempatkan di tangki pengembang kering dan dilapisi dengan pengembang, atau dibiarkan selama sisa waktu tinggal kemudian diperiksa.
Penetran pasca-emulsi adalah penetran yang tidak memiliki pengemulsi yang termasuk dalam susunan kimianya seperti penetran yang dapat dicuci dengan air. Penetran pasca-emulsi diterapkan dengan cara yang sama, tetapi sebelum langkah pencucian air, pengemulsi diterapkan ke permukaan untuk jangka waktu yang ditentukan (waktu tinggal pengemulsi) untuk menghilangkan kelebihan penetran. Ketika waktu tinggal pengemulsi telah berlalu, bagian tersebut mengalami pencucian air yang sama dan proses pengembangan yang digunakan untuk penetran yang dapat dicuci dengan air. Pengemulsi dapat bersifat lipofilik (berbasis minyak) atau hidrofilik (berbasis air).
Pengujian partikel magnetik
Pengujian partikel magnetik menggunakan satu atau lebih medan magnet untuk menemukan diskontinuitas permukaan dan dekat permukaan dalam bahan ferro-magnetik. Hal ini digunakan untuk menemukan diskontinuitas permukaan dan sub-permukaan sedikit atau cacat pada bahan ferro-magnetik. Cacat seperti itu ada di bagian yang dimagnetisasi menyebabkan medan magnet, yaitu fluks, meninggalkan bagian itu. Jika partikel magnetik diterapkan pada permukaan ini, partikel tersebut ditahan oleh kebocoran fluks untuk memberikan indikasi visual. Sementara beberapa metode yang berbeda dari uji partikel magnetik dapat digunakan, semuanya bergantung pada prinsip umum yang sama ini. Oleh karena itu, setiap pengujian partikel magnetik dilakukan dengan menciptakan medan magnet di suatu bagian dan menerapkan partikel magnetik ke permukaan pengujian.
Medan magnet dapat diterapkan dengan magnet permanen atau elektro-magnet. Saat menggunakan elektro-magnet, medan hanya ada ketika arus diterapkan. Ketika medan magnet menghadapi diskontinuitas yang melintang terhadap arah medan magnet, garis fluks menghasilkan medan kebocoran fluks magnetnya sendiri seperti yang ditunjukkan pada Gambar 3. Hal ini dapat dilihat, ketika partikel feromagnetik berwarna sangat halus (partikel magnetik ) diterapkan pada permukaan bagian, partikel ditarik ke dalam diskontinuitas, mengurangi celah udara dan menghasilkan indikasi yang terlihat pada permukaan bagian. Partikel magnetik dapat berupa bubuk kering atau tersuspensi dalam larutan cair, dan dapat diwarnai dengan pewarna yang terlihat atau pewarna fluoresen yang berpendar di bawah sinar ultraviolet (hitam).
Arus bolak-balik (AC) atau arus searah (DC) dapat digunakan untuk menginduksi medan magnet. Medan magnet yang diciptakan oleh AC karena 'efek kulit' paling kuat di permukaan benda uji. AC juga memberikan mobilitas partikel yang lebih besar pada permukaan bagian yang memungkinkan mereka bergerak bebas untuk menemukan area kebocoran fluks, meskipun permukaan bagian dapat tidak beraturan. DC menginduksi medan magnet yang memiliki daya tembus lebih besar dan dapat digunakan untuk mendeteksi diskontinuitas dekat permukaan.
Sebagian besar inspeksi lapangan dilakukan dengan menggunakan yoke (Gbr 3). Kumparan listrik dililitkan di sekitar inti pusat, dan ketika arus diterapkan, medan magnet dihasilkan yang memanjang dari inti ke bawah melalui kaki yang diartikulasikan ke bagian tersebut. Ini dikenal sebagai magnetisasi longitudinal karena garis fluks magnet berjalan dari satu kaki ke kaki lainnya. Ketika kaki ditempatkan pada bagian fero-magnetik dan kuk diberi energi, medan magnet dimasukkan ke bagian tersebut. Karena garis fluks berjalan dari satu kaki ke kaki lainnya, diskontinuitas berorientasi tegak lurus terhadap garis yang ditarik antara kaki dapat ditemukan. Untuk memastikan tidak ada indikasi yang terlewatkan, yoke digunakan sekali pada posisi seperti yang ditunjukkan pada gambar dan kemudian digunakan lagi dengan yoke diputar 90 derajat sehingga tidak ada indikasi yang terlewat. Karena semua arus listrik terkandung dalam yoke dan hanya medan magnet yang menembus bagian tersebut, jenis aplikasi ini juga dikenal sebagai induksi tidak langsung.
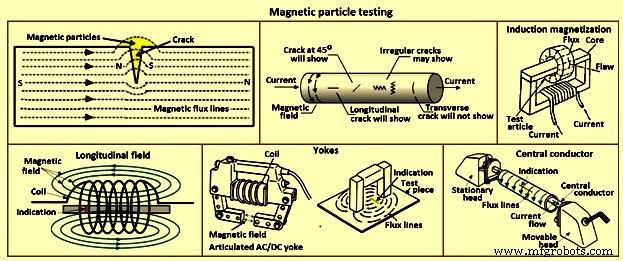
Gbr 3 Pengujian partikel magnetik
Unit poke menggunakan induksi langsung, di mana arus mengalir melalui bagian dan medan magnet melingkar dihasilkan di sekitar kaki seperti yang ditunjukkan pada Gambar 3. Karena medan magnet antara poke berjalan tegak lurus terhadap garis yang ditarik di antara poke, indikasi berorientasi paralel untuk garis ditarik antara pokes dapat ditemukan. Seperti pada yoke, dua inspeksi dilakukan, yang kedua dengan poke yang berorientasi 90 derajat ke aplikasi pertama.
Kumparan listrik digunakan untuk menghasilkan medan magnet memanjang. Ketika diberi energi, arus menciptakan medan magnet di sekitar kabel yang membentuk koil sehingga garis fluks yang dihasilkan berorientasi melalui koil. Karena adanya medan longitudinal, indikasi pada bagian-bagian yang ditempatkan dalam sebuah kumparan diorientasikan melintang terhadap medan longitudinal.
Sebagian besar mesin mandi basah horizontal (unit bangku) memiliki kumparan dan satu set kepala yang dapat dilalui arus listrik, menghasilkan medan magnet. Mesin ini menggunakan partikel magnetik fluoresen dalam larutan cair, oleh karena itu dinamakan 'mandi basah'. Saat menguji bagian di antara kepala, bagian ditempatkan di antara kepala, kepala yang dapat digerakkan dipindahkan ke atas sehingga bagian yang diuji dipegang erat di antara kepala, bagian dibasahi dengan larutan mandi yang mengandung partikel magnetik dan arus diterapkan saat partikel mengalir di atas bagian tersebut. Karena aliran arus dari kepala ke kepala dan medan magnet berorientasi 90 derajat ke arus, indikasi berorientasi sejajar dengan garis antara kepala terlihat. Jenis pemeriksaan ini biasanya disebut 'tembak di kepala'.
Saat menguji bagian berongga seperti pipa, tabung dan alat kelengkapan, batang melingkar konduktif dapat ditempatkan di antara kepala dengan bagian yang tergantung pada batang (konduktor pusat) seperti yang ditunjukkan pada Gambar 3. Bagian tersebut kemudian dibasahi dengan larutan rendaman dan arus diterapkan, berjalan melalui konduktor pusat daripada melalui bagian. ID dan OD bagian tersebut kemudian dapat diperiksa. Seperti dalam kasus head shot, medan magnet tegak lurus terhadap aliran arus, membungkus di sekitar benda uji, sehingga indikasi berjalan secara aksial sepanjang bagian dapat ditemukan dengan menggunakan teknik ini.
Keuntungan dari pengujian partikel magnetik adalah (i) ekonomis, (ii) membantu pengujian visual, (iii) dapat diperbaiki atau peralatan portabel, (iv) memberikan hasil yang dapat diulang secara instan, (v) teknik inspeksi yang efektif, dan ( vi) bahan habis pakai kontras atau fluoresen. Keterbatasan pengujian partikel magnetik adalah (i) bagian yang diperiksa harus fero-magnetik, (ii) diperlukan arus tinggi, (iii) hanya dapat mendeteksi cacat permukaan dan sedikit di bawah permukaan, (iv) bagian perlu terdemagnetisasi, (v) bagian harus bersih dan relatif halus, (vi) peralatan dapat menjadi besar dan berat, (vi) catu daya biasanya diperlukan, (vii) pelapis dapat menutupi indikasi, dan (viii) permeabilitas bahan atau bagian dapat mempengaruhi hasil.
Pengujian arus Eddy
Arus eddy dibuat melalui proses yang disebut induksi elektromagnetik. Ketika AC diterapkan pada konduktor, seperti kawat tembaga, medan magnet berkembang di dalam dan di sekitar konduktor. Medan magnet ini mengembang saat AC naik ke maksimum dan runtuh saat arus dikurangi menjadi nol. Jika konduktor listrik lain dibawa ke dekat medan magnet yang berubah ini, arus diinduksi dalam konduktor kedua ini. Arus ini dipengaruhi oleh sifat material seperti rongga, retak, perubahan ukuran butir, serta jarak fisik antara kumparan dan material. Arus ini membentuk impedansi pada kumparan kedua yang digunakan sebagai sensor. Dalam prakteknya sebuah probe ditempatkan pada permukaan bagian yang akan diperiksa, dan peralatan elektronik memonitor arus eddy pada benda kerja melalui probe yang sama. Sirkuit penginderaan adalah bagian dari koil pengirim.
Aplikasi utama dari teknik arus eddy adalah untuk mendeteksi cacat permukaan atau bawah permukaan. Teknik ini sensitif terhadap konduktivitas material, permeabilitas dan dimensi produk. Arus eddy dapat dihasilkan dalam bahan penghantar listrik apa pun yang dikenai medan magnet bolak-balik (biasanya 10 Hz hingga 10 MHz). Medan magnet bolak-balik biasanya dihasilkan dengan melewatkan arus bolak-balik melalui sebuah kumparan. Kumparan dapat memiliki banyak bentuk dan dapat memiliki antara 10 putaran hingga 500 putaran kawat. Besarnya arus eddy yang dihasilkan dalam produk tergantung pada konduktivitas, permeabilitas dan geometri set up. Setiap perubahan material atau geometri dapat dideteksi oleh kumparan eksitasi sebagai perubahan pada impedansi kumparan.
Kumparan paling sederhana terdiri dari batang ferit dengan beberapa lilitan lilitan kawat di salah satu ujungnya dan yang diposisikan dekat dengan permukaan produk yang akan diuji. Ketika retak, misalnya, terjadi pada permukaan produk, arus eddy bergerak lebih jauh di sekitar retakan dan ini dideteksi oleh perubahan impedansi (Gbr 4). Kumparan juga dapat digunakan berpasangan, umumnya disebut pasangan yang digerakkan, dan pengaturan ini dapat digunakan dengan kumparan yang dihubungkan secara berbeda. Dengan cara ini sinyal 'angkat' (jarak probe dari permukaan) dapat ditingkatkan. Kumparan juga dapat digunakan dalam konfigurasi jenis transformator di mana satu gulungan kumparan adalah primer dan satu (atau dua) gulungan digunakan untuk sekunder. .
Sinyal arus eddy yang terdeteksi mengandung informasi amplitudo dan fasa yang dapat ditampilkan pada layar tipe CRT (tabung sinar katoda) yang biasanya non digital. Sinyal dapat ditampilkan sebagai sinyal aktual, yaitu sinyal absolut, atau dengan elektronik yang sesuai, hanya perubahan sinyal yang ditampilkan. Hasil terbaik dicapai jika hanya satu parameter produk yang berubah, mis. adanya retakan. Dalam prakteknya perubahan sinyal arus eddy disebabkan oleh perbedaan komposisi, kekerasan, tekstur, bentuk, konduktivitas, permeabilitas dan geometri. Dalam beberapa kasus, efek retakan dapat disembunyikan dengan perubahan parameter lain dan penolakan yang tidak perlu dapat terjadi. Namun, kumparan dapat dipilih untuk konfigurasi, ukuran, dan frekuensi pengujian untuk meningkatkan deteksi retak, konduktivitas, kehilangan logam, dll. sesuai kebutuhan.
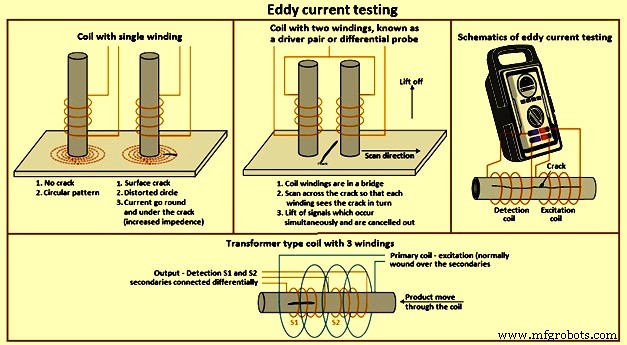
Gbr 4 Pengujian arus Eddy
Kedalaman penetrasi arus eddy material dapat diubah dengan menyesuaikan frekuensi uji, yaitu semakin tinggi frekuensi semakin rendah penetrasi. Namun, semakin rendah frekuensinya, semakin rendah sensitivitasnya terhadap cacat kecil. Kumparan yang lebih besar kurang sensitif terhadap kekasaran permukaan dan sebaliknya. Unit elektronik terbaru mampu mengoperasikan berbagai konfigurasi koil dalam mode absolut atau diferensial dan pada rentang frekuensi yang luas. Untuk pengujian permukaan retakan pada komponen berbentuk tunggal atau kompleks, biasanya digunakan kumparan dengan belitan inti ferit tunggal. Probe ditempatkan pada komponen dan 'seimbang' dengan menggunakan kontrol unit elektronik. Saat probe dipindai di seluruh permukaan komponen, retakan dapat dideteksi.
Di mana permukaan harus dipindai secara otomatis, belitan kumparan tunggal hanya cocok jika jarak pengangkatan dipertahankan secara akurat. Biasanya konfigurasi koil diferensial digunakan dengan sistem pemindaian kecepatan tinggi di mana efek lepas landas, efek getaran, dll. dapat dibatalkan sampai batas yang dapat diterima. Tabung, batang dan kawat dapat diperiksa menggunakan kumparan melingkar dan ini biasanya memiliki konfigurasi kumparan dengan satu primer dan dua sekunder dihubungkan secara berbeda.
Mayoritas elektronik arus eddy memiliki tampilan fase dan ini memberikan operator kemampuan untuk mengidentifikasi kondisi cacat. Dalam banyak kasus, sinyal dari retakan, lepas landas, dan parameter lainnya dapat diidentifikasi dengan jelas. Unit juga tersedia yang dapat memeriksa produk secara bersamaan pada dua atau lebih frekuensi pengujian yang berbeda. Unit ini memungkinkan efek tertentu yang tidak diinginkan dibatalkan secara elektronik untuk memberikan deteksi cacat yang lebih baik.
Tes arus eddy murni listrik. Unit koil tidak perlu menyentuh permukaan produk dan dengan demikian teknik ini dapat dengan mudah diotomatisasi. Sebagian besar sistem otomatis adalah untuk komponen geometri sederhana di mana penanganan mekanis disederhanakan.
Keuntungan dari pengujian arus eddy adalah (i) cocok untuk penentuan berbagai kondisi bahan penghantar, seperti deteksi cacat, komposisi, kekerasan, konduktivitas, permeabilitas, dll. dalam berbagai macam logam teknik, (ii) informasi dapat disediakan dalam istilah sederhana sesering pergi / tidak pergi dengan tampilan fase unit elektronik dapat digunakan untuk mencapai informasi produk yang jauh lebih besar, (iii) unit yang sangat ringkas dan portabel tersedia, (iv) tidak ada bahan habis pakai (kecuali probe yang terkadang dapat diperbaiki), (v) fleksibilitas dalam pemilihan probe dan frekuensi pengujian agar sesuai dengan aplikasi yang berbeda, dan (vi) cocok untuk otomatisasi total. Kerugian dari pengujian arus eddy adalah (i) berbagai parameter yang mempengaruhi tanggapan arus eddy berarti bahwa sinyal dari karakteristik material yang diinginkan, mis. retak, dapat ditutupi oleh parameter yang tidak diinginkan, mis. perubahan kekerasan, maka pemilihan probe dan elektronik yang cermat diperlukan dalam beberapa aplikasi, dan (ii) biasanya pengujian dibatasi
Pengujian radiografi
Metode pengujian radiografi digunakan untuk mendeteksi cacat internal pada banyak bahan dan konfigurasi yang berbeda. Sinar-X, yang dihasilkan secara elektrik, dan sinar gamma yang dipancarkan dari isotop radioaktif, menembus radiasi yang diserap secara berbeda oleh bahan yang dilaluinya. Semakin besar ketebalannya, semakin besar penyerapannya. Selanjutnya, semakin padat material, semakin besar penyerapannya. Sinar-X dan sinar gamma juga memiliki sifat, seperti cahaya, mengubah sebagian kristal perak halida dalam film fotografi menjadi perak metalik, sebanding dengan intensitas radiasi yang mencapai film, dan karenanya membentuk gambar laten. Ini dapat dikembangkan dan diperbaiki dengan cara yang mirip dengan film fotografi normal (Gbr 5).
Bahan dengan rongga internal diuji dengan menempatkan subjek di antara sumber radiasi dan film. Kekosongan terlihat sebagai area gelap, di mana lebih banyak radiasi telah mencapai film, dengan latar belakang yang jelas. Prinsipnya sama untuk radiografi sinar-x dan sinar gamma.
Dalam radiografi sinar-x, daya tembus ditentukan oleh jumlah volt yang diterapkan pada tabung sinar-x. Untuk baja, ketebalannya sekitar 1.000 volt per inci. Dalam radiografi sinar gamma, isotop mengatur daya tembus dan tidak dapat diubah di setiap isotop. Jadi iridium 192 digunakan untuk baja dengan tebal 15 mm sampai 25 mm, dan cesium 134 digunakan untuk baja dengan tebal 20 mm sampai 265 mm. Dalam radiografi sinar-x intensitas, dan karenanya waktu pemaparan, diatur oleh arus listrik katoda dalam tabung. Waktu pemaparan biasanya dinyatakan dalam mili-ampere menit. Dengan sinar gamma intensitas radiasi diatur pada saat pasokan isotop. Intensitas radiasi dari isotop diukur dalam Becquerel dan berkurang selama periode waktu tertentu. Waktu yang dibutuhkan untuk meluruh menjadi setengah jumlah curie adalah waktu paruh dan merupakan karakteristik dari masing-masing isotop. Misalnya, waktu paruh iridium 192 adalah 74 hari, dan sesium 134 adalah 2,1 tahun.
Faktor eksposur adalah produk dari jumlah curie dan waktu, biasanya dinyatakan dalam jam curie. The time of exposure is to be increased as the isotope decays. When the exposure period becomes uneconomical the isotope is to be renewed. As the isotope is continuously emitting radiation it is to be housed in a container of depleted uranium or similar dense shielding material, whilst not exposed for protecting the environment and personnel.
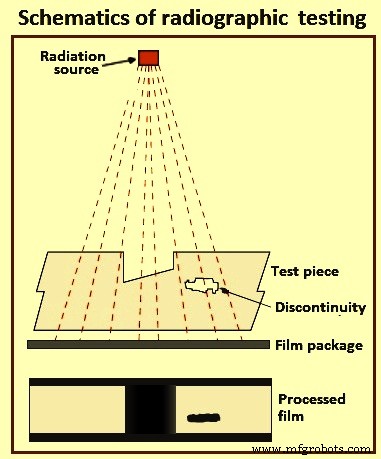
Fig 5 Schematics of radiographic testing
To produce an x-ray or gamma ray radiograph, the film package ((enclosed in a light tight cassette and comprising film and intensifying screens, the latter being required to reduce the exposure time) is placed close to the surface of the subject. The source of radiation is positioned on the other side of the subject some distance away, so that the radiation passes through the subject and on to the film. After the exposure period the film is removed, processed, dried, and then viewed by transmitted light on a special viewer. Different radiographic and photographic accessories are necessary, including such items as radiation monitors, film markers, image quality indicators, dark-room equipment, etc. As far as the last is concerned there are many degrees of sophistication, including fully automatic processing units. These accessories are the same for both x-ray and gamma radiography systems. Also needed are such consumable items as radiographic film and processing chemicals
Recent developments in radiography permit ‘real time’ diagnosis. Such techniques as computerized tomography yield much important information, though these methods can be suitable for only investigative purposes and not generally employed in production quality control.
Industrial radiography involves exposing a test object to penetrating radiation so that the radiation passes through the object being inspected and a recording medium placed against the opposite side of that object. For thinner or less dense materials such as aluminum, electrically generated x-radiations (x-rays) are normally used, and for thicker or denser materials, gamma radiation is generally used. Gamma radiation is given off by decaying radioactive materials, with the two most commonly used sources of gamma radiation being Iridium-192 (Ir-192) and Cobalt-60 (Co-60). Ir-192 is normally used for steel upto 15 mm to 25 mm, depending on the Curie strength of the source, and Co-60 is normally used for thicker materials due to its greater penetrating ability. The recording media can be industrial x-ray film or one of several types of digital radiation detectors. With both, the radiation passing through the test object exposes the media, causing an end effect of having darker areas where more radiation has passed through the part and lighter areas where less radiation has penetrated. If there is a void or defect in the part, more radiation passes through, causing a darker image on the film or detector.
Film radiography uses a film made up of a thin transparent plastic coated with a fine layer of silver bromide on one or both sides of the plastic. When exposed to radiation these crystals undergo a reaction which allows them, when developed, to convert to black metallic silver. This silver is then ‘fixed’ to the plastic during the developing process, and when dried, becomes a finished radiographic film. To be a usable film, the area of interest on the film is to be within a certain density (darkness) range and is to show enough contrast and sensitivity so that discontinuities of interest can be seen. These items are a function of the strength of the radiation, the distance of the source from the film and the thickness of the part being inspected. If any of these parameters are not met, another exposure (is to be made for that area of the part.
Computed radiography is a transitional technology between film and direct digital radiography. This technique uses a reusable, flexible, photo-stimulated phosphor plate which is loaded into a cassette and is exposed in a manner similar to traditional film radiography. The cassette is then placed in a laser reader where it is scanned and translated into a digital image, which take from one to five minutes. The image can then be uploaded to a computer or other electronic media for interpretation and storage. Computed tomography uses a computer to reconstruct an image of a cross sectional plane of an object as opposed to a conventional radiograph. The computed tomography image is developed from multiple views taken at different viewing angles which are reconstructed using a computer. With traditional radiography, the position of internal discontinuities cannot be accurately determined without making exposures from several angles to locate the item by triangulation. With computed tomography, the computer triangulates using every point in the plane as viewed from many different directions.
Digital radiography digitizes the radiation which passes through an object directly into an image which can be displayed on a computer monitor. The three principle technologies used in direct digital imaging are amorphous silicon, charge coupled devices, and complementary metal oxide semi-conductors. These images are available for viewing and analysis in seconds compared to the time needed to scan in computed radiography images. The increased processing speed is a result of the unique construction of the pixels; an arrangement which also allows a superior resolution than is found in computed radiography and most film applications.
The advantages of radiographic testing include (i) is useful on wide variety of materials, (ii) can be used for checking internal mal-structure, misassembly or misalignment, (iii) provides permanent record, and (iv) devices for checking the quality of radiograph are available. Some of the limitations of this method are (i) access to both sides of the object is needed, (ii) cannot detect planar defects readily, (iii) thickness range which can be inspected is limited, (iv) sensitivity of inspection decreases with thickness of the test object, (v) considerable skill is needed for interpretation of the radiographs, (vi) depth of defect is not indicated readily, and (vii) x-rays and gamma rays are hazardous to human health.
Ultrasonic testing
Ultrasonic technique is used for the detection of internal and surface (particularly distant surface) defects in sound conducting materials. The principle is in some respects similar to echo sounding. A short pulse of ultrasound is generated by means of an electric charge applied to a piezo electric crystal, which vibrates for a very short period at a frequency related to the thickness of the crystal. In flaw detection, this frequency is normally in the range of one million to six million times per second (1 MHz to 6 MHz). Vibrations or sound waves at this frequency have the ability to travel a considerable distance in homogeneous elastic material, such as many metals with little reduction. The velocity at which these waves propagate is related to the Young’s Modulus for the material and is characteristic of the material. For example the velocity in steel is 5,900 metres per second, and in water 1,400 metres per second.
Ultrasonic energy is considerably reduced in air, and a beam propagated through a solid, on reaching an interface (e.g. a defect, or intended hole, or the back wall) between that material and air reflects a considerable amount of energy in the direction equal to the angle of incidence. For contact testing the oscillating crystal is incorporated in a hand held probe, which is applied to the surface of the material to be tested. To facilitate the transfer of energy across the small air gap between the crystal and the test piece, a layer of liquid (referred to as ‘couplant’), usually oil, water or grease, is applied to the surface. The crystal does not oscillate continuously but in short pulses, between each of which it is quiescent.
Piezo electric materials not only convert electrical pulses to mechanical oscillations, but also transduce mechanical oscillations into electrical pulses. Hence, there is not only a generator of sound waves but also a detector of returned pulses. The crystal is in a state to detect returned pulses when it is quiescent. The pulse takes a finite time to travel through the material to the interface and to be reflected back to the probe.
The standard method of presenting information in ultrasonic testing is by means of a cathode ray tube, in which horizontal movement of the spot from left to right represents time elapsed. The principle is not greatly different in digitized instruments that have a LCD (liquid crystal display) flat screen. The rate at which the spot moves is such that it gives the appearance of a horizontal line on the screen. The system is synchronized electronically so that at the instant the probe receives its electrical pulse the spot begins to traverse the screen. An upward deflection (peak) of the line on the screen is an indication of this occurrence. This peak is normally termed the initial pulse.
Whilst the base line is perfectly level the crystal is quiescent. Any peaks to the right of the initial pulse indicate that the crystal has received an incoming pulse reflected from one or more interfaces in the material. Since the spot moves at a very even speed across the tube face, and the pulse of ultrasonic waves moves at a very even velocity through the material, it is possible to calibrate the horizontal line on the screen in terms of absolute measurement. The use of a calibration block, which produces a reflection from the back wall a known distance away from the crystal together with variable controls on the flaw detector, allows the screen to be calibrated in units of distance, and hence determination of origins of returned pulses obtained from a test piece.
It is hence possible not only to discover a defect between the surface and the back wall, but also to measure its distance below the surface. It is important that the equipment is properly calibrated and, since it is in itself not able to discriminate between intended boundaries of the object under test and unintended discontinuities, the operator is required to identify the origin of each peak. Further as the pulses form a beam it is also possible to determine the plan position of a flaw. The height of the peak (echo) is roughly proportional to the area of the reflector, though there is on all instruments a control, which can reduce or increase the size of an indication – variable sensitivity in fact. Not only is part of the beam reflected at a material / air interface but also at any junction where there is a velocity change, for example steel / slag interface in a weld.
Probing all faces of a test piece not only discovers the three-dimensional defect and measures its depth, but can also determine its size. Two-dimensional (planar) defects can also be found but, unlike radiography, it is best that the incident beam impinges on the defect as near to right angles to the plane as possible. To achieve this some probes introduce the beam at an angle to the surface. In this manner longitudinal defects in tubes (inner or outer surface) are detected.
Interpretation of the indications on the screen requires a certain amount of skill, particularly when testing with hand held probes. The technique is, however, admirably suited to automatic testing of regular shapes by means of a monitor – an electronic device which fits into the main equipment to provide an electrical signal when an echo occurs in a particular position on the trace. The trigger level of this signal is variable and it can be made to operate a variety of mechanical gates and flaw warnings. Furthermore, improvements in computer technology allow test data and results to be displayed and out-putted in a wide variety of formats.
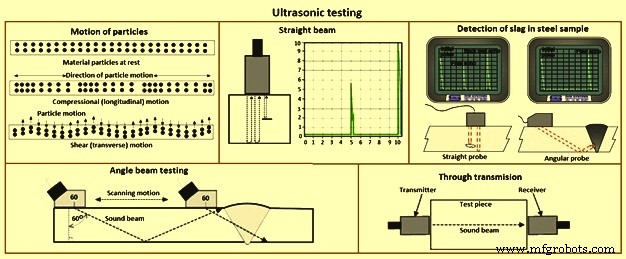
Fig 6 Ultrasonic testing
Modern ultrasonic flaw detectors are fully solid state and can be battery powered, and are robustly built to withstand site conditions. Since the velocity of sound in any material is characteristic of that material, it follows that some materials can be identified by the determination of the velocity. This can be applied, for example in spheroidal graphite cast irons to determine the percentage of graphite nodularity.
When the velocity is constant, as it is in a wide range of steels, the time taken for the pulse to travel through the material is proportional to its thickness. Hence, with a properly calibrated instrument, it is possible to measure thickness from one side with accuracy in hundredths of a millimeter. This technique is now in very common use. A development of the standard flaw detector is the digital wall thickness gauge. This operates on similar principles but gives an indication, in LED (light emitting diode) or LCD 9liquid crystal display) numerics, of thickness in absolute terms of millimetres. These equipments are easy to use but need prudence in their application.
The two most commonly used types of sound waves used in industrial inspections are the compression (longitudinal) wave and the shear (transverse) wave (Fig 6). Compression waves cause the atoms in a part to vibrate back and forth parallel to the sound direction and shear waves cause the atoms to vibrate perpendicularly (from side to side) to the direction of the sound. Shear waves travel at around half the speed of longitudinal waves. Sound is introduced into the part using an ultrasonic transducer (probe) which converts electrical impulses from the ultrasonic testing machine into sound waves, then converts returning sound back into electric impulses which can be displayed as a visual representation on a digital or LCD screen. If the machine is properly calibrated, the operator can determine the distance from the transducer to the reflector, and in many cases, an experienced operator can determine the type of discontinuity which caused the reflector. Because ultrasound does not travel through air (the atoms in air molecules are too far apart to transmit ultrasound), a liquid or gel called ‘couplant’ is used between the face of the transducer and the surface of the part to allow the sound to be transmitted into the part.
Straight beam inspection uses longitudinal waves to interrogate the test piece as shown at the right. If the sound hits an internal reflector, the sound from that reflector reflects to the transducer faster than the sound coming back from the back-wall of the part due to the shorter distance from the transducer. This results in a screen display. Digital thickness testers use the same process, but the output is shown as a digital numeric readout rather than a screen presentation.
Angle beam inspection uses the same type of transducer but it is mounted on an angled wedge (also called a probe) that is designed to transmit the sound beam into the part at a known angle. The most commonly used inspection angles are 45 degrees, 60 degrees, and 70 degrees, with the angle being calculated up from a line drawn through the thickness of the part (not the part surface). A 60 degree probe is shown in Fig 6. If the frequency and wedge angle is not specified by the governing code or specification, it is upto the operator to select a combination which adequately inspects the part being tested. In angle beam inspections, the transducer and wedge combination (also referred to as a probe) is moved back and forth towards the weld so that the sound beam passes through the full volume of the weld. As with straight beam inspections, reflectors aligned more or less perpendicular to the sound beam sends sound back to the transducer and are displayed on the screen.
Immersion Testing is a technique where the part is immersed in a tank of water with the water being used as the coupling medium to allow the sound beam to travel between the transducer and the part. The ultrasonic testing machine is mounted on a movable platform (a bridge) on the side of the tank so it can travel down the length of the tank. The transducer is swivel-mounted on at the bottom of a waterproof tube which can be raised, lowered and moved across the tank. The bridge and tube movement permits the transducer to be moved on the X-, Y- and Z-axes. All directions of travel are gear driven so the transducer can be moved in accurate increments in all directions, and the swivel allows the transducer to be oriented so the sound beam enters the part at the required angle. Round test parts are frequently mounted on powered rollers so that the part can be rotated as the transducer travels down its length, allowing the full circumference to be tested. Multiple transducers can be used at the same time so that multiple scans can be performed.
Through transmission inspections are performed using two transducers, one on each side of the part (Fig 6). The transmitting transducer sends sound through the part and the receiving transducer receives the sound. Reflectors in the part cause a reduction in the amount of sound reaching the receiver so that the screen presentation shows a signal with lower amplitude (screen height).
Phased array inspections are done using a probe with multiple elements which can be individually activated. By varying the time when each element is activated, the resulting sound beam can be steered, and the resulting data can be combined to form a visual image representing a slice through the part being inspected.
Time of flight diffraction uses two transducers located on opposite sides of a weld with the transducers set at a specified distance from each other. One transducer transmits sound waves and the other transducer acting as a receiver. Unlike other angle beam inspections, the transducers are not manipulated back and forth towards the weld, but travel along the length of the weld with the transducers remaining at the same distance from the weld. Two sound waves are generated, one travelling along the part surface between the transducers, and the other travelling down through the weld at an angle then back up to the receiver. When a crack is encountered, some of the sound is diffracted from the tips of the crack, generating a low strength sound wave which can be picked up by the receiving unit. By amplifying and running these signals through a computer, defect size and location can be determined with much greater accuracy than by conventional ultrasonic testing methods.
The advantages of ultrasonic flaw detection include (i) thickness and lengths upto 10 meter can be tested, (ii) position, size and type of defect can be determined, (iii) instant test results, (iv) portable, (v) extremely sensitive if required, (vi) capable of being fully automated, (vi) access to only one side necessary, and (vii) no consumables needed. The disadvantages of ultrasonic flaw detection include (i) no permanent record available unless one of the more sophisticated test results and data collection systems is used, (ii) the operator can decide whether the test piece is defective or not whilst the test is in progress, (iii) indications need interpretation, (iv) considerable degree of skill