5 Cara Untuk Memahami Gambar Pemesinan yang Kompleks
1. Metode dimensi struktur umum
Metode dimensi lubang umum:
Lubang Buta
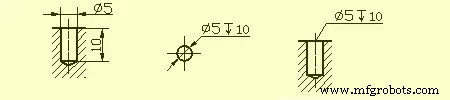
Lubang Berulir
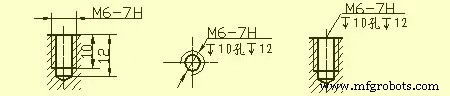
Penghitung lubang
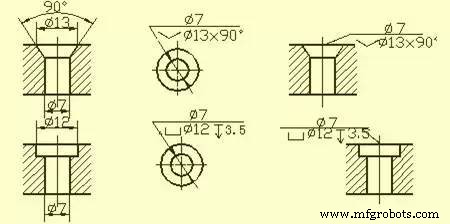
Lubang Countersink
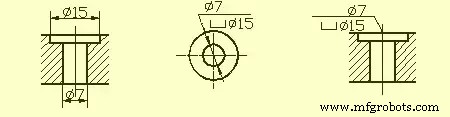
Metode pengukuran talang
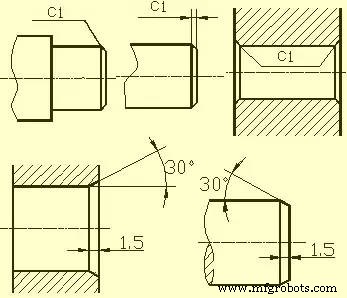
2. Struktur Pemesinan Pada Bagian
Alur overtravel undercut dan grinding wheel
Ketika bagian dipotong, untuk memfasilitasi penarikan pahat dan memastikan bahwa permukaan kontak dari bagian yang relevan dekat selama perakitan, alur undercut atau alur overtravel roda gerinda harus pra-pemesinan pada langkah permukaan yang diproses. .
Ukuran undercut saat memutar lingkaran luar umumnya dapat ditandai dengan cara "lebar alur × diameter" atau "lebar alur × kedalaman alur". Alur roda gerinda overtravel saat menggiling lingkaran luar atau menggiling lingkaran luar dan permukaan ujung.
Struktur Pengeboran
Lubang buta yang dibor dengan mata bor memiliki sudut kerucut 120° di bagian bawah. Kedalaman pengeboran mengacu pada kedalaman bagian silinder, tidak termasuk lubang kerucut. Pada transisi pengeboran bertahap, ada juga sudut kerucut meja bundar 120 °, gambar dan notasi ukurannya.
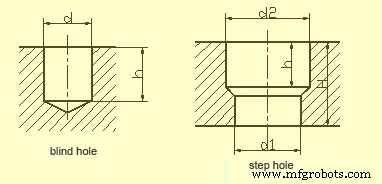
Saat mengebor dengan bor, sumbu bor harus tegak lurus dengan permukaan ujung lubang bor untuk memastikan akurasi pengeboran dan menghindari bor pecah. Struktur yang benar dari tiga permukaan ujung pengeboran.
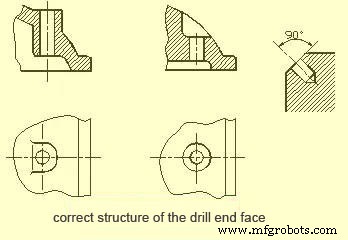
Bos dan Pit
Permukaan kontak suatu bagian dengan bagian lain umumnya diproses. Untuk mengurangi area pemrosesan dan memastikan kontak yang baik antara permukaan bagian, bos dan lubang sering dirancang pada coran. Bos permukaan penyangga yang dibaut atau bentuk tersembunyi permukaan penyangga. untuk mengurangi area pemrosesan, dibuat struktur alur.
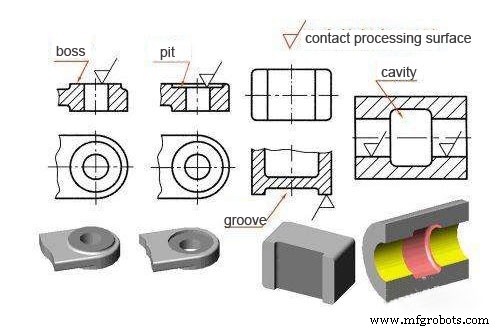
3 Struktur Bagian Umum
Bagian Poros
Bagian tersebut umumnya termasuk poros, busing dan bagian lainnya. Saat mengekspresikan tampilan, selama Anda menggambar tampilan dasar dan menambahkan tampilan dan dimensi penampang yang sesuai, Anda dapat mengekspresikan fitur bentuk utama dan struktur lokalnya. Untuk memfasilitasi tampilan gambar selama pemrosesan, sumbu umumnya ditempatkan secara horizontal untuk proyeksi, dan yang terbaik adalah memilih posisi di mana sumbu adalah garis vertikal lateral.
Saat menandai ukuran bagian bushing, sumbunya sering digunakan sebagai patokan ukuran radial. Dari sini, 14 dan 11 yang ditunjukkan pada gambar (lihat bagian A-A), dll dicatat. Dengan cara ini, persyaratan desain dan referensi proses selama pemrosesan (ketika bagian poros diproses pada mesin bubut, lubang tengah poros dipegang oleh bidal di kedua ujungnya) disatukan. Datum arah panjang sering kali memilih permukaan akhir yang penting, permukaan kontak (bahu) atau permukaan mesin.
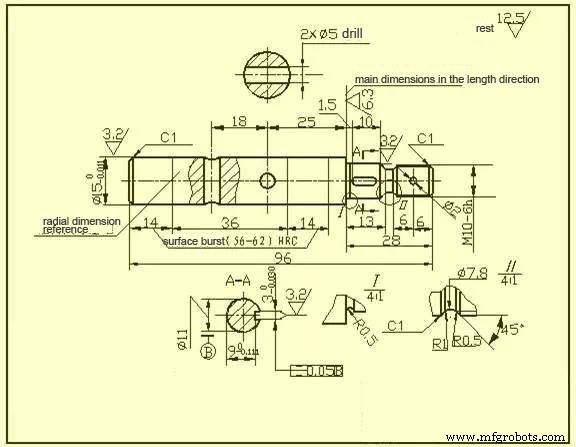
Bahu kanan dengan kekasaran permukaan Ra6.3 seperti yang ditunjukkan pada gambar dipilih sebagai referensi dimensi utama dalam arah panjang, dan dimensi seperti 13, 28, 1,5 dan 26,5 disuntikkan.
Kemudian ambil ujung poros kanan sebagai alas bantu dalam arah panjang untuk menandai total panjang poros 96.
Bagian Penutup Disk
Bentuk dasar dari suku cadang ini adalah piringan datar, umumnya termasuk tutup ujung, tutup katup, roda gigi dan bagian lainnya. Struktur utama mereka pada dasarnya adalah tubuh yang berputar, biasanya dengan berbagai bentuk flensa dan lubang melingkar yang terdistribusi secara merata. Dan tulang rusuk dan struktur lokal lainnya. Saat memilih tampilan, umumnya pilih tampilan penampang bidang simetri atau sumbu rotasi sebagai tampilan depan, dan juga perlu menambahkan tampilan lain yang sesuai (seperti tampilan kiri, tampilan kanan, atau tampilan atas) untuk mengekspresikan bentuk dan struktur bagian yang seragam. Seperti yang ditunjukkan pada gambar, tampilan kiri ditambahkan untuk mengekspresikan flensa persegi dengan sudut membulat dan empat didistribusikan secara merata melalui lubang.
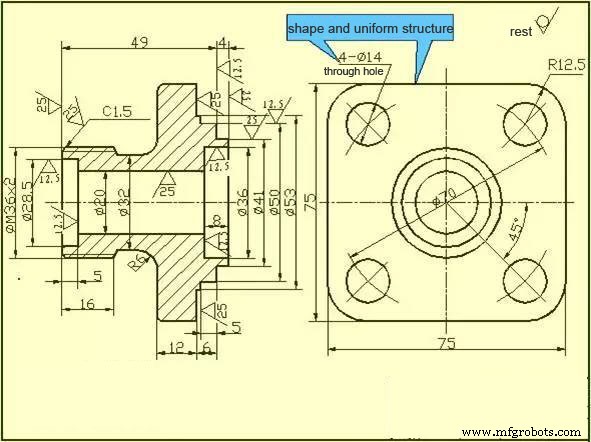
Saat menandai ukuran bagian penutup cakram, sumbu melalui lubang poros biasanya dipilih sebagai referensi dimensi radial, dan referensi dimensi utama dalam arah panjang sering kali merupakan permukaan akhir yang penting.
Bagian rangka garpu
Bagian tersebut umumnya termasuk garpu, batang penghubung, bantalan dan bagian lainnya. Karena posisi pemrosesan yang bervariasi, saat memilih tampilan utama, pertimbangan utama adalah posisi kerja dan karakteristik bentuk. Untuk pemilihan tampilan lain, dua atau lebih tampilan dasar sering kali diperlukan, dan tampilan lokal yang sesuai, tampilan penampang, dll. harus digunakan untuk mengekspresikan struktur lokal bagian tersebut. Tampilan yang ditunjukkan pada gambar bagian pijakan kaki sangat halus dan jelas. Pandangan kanan tidak diperlukan untuk menyatakan lebar bantalan dan rusuk. Untuk rusuk berbentuk T, penampang lebih tepat.
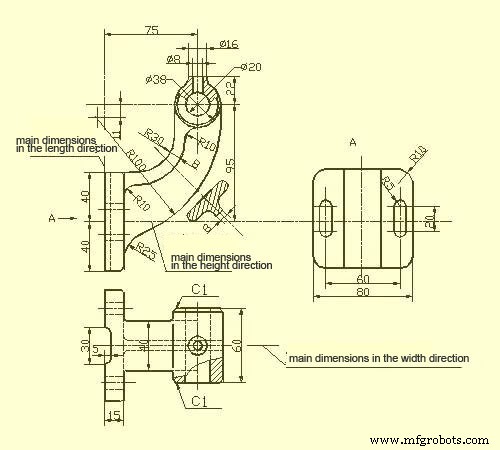
Saat menandai dimensi bagian braket garpu, permukaan dasar pemasangan atau bidang simetri bagian biasanya dipilih sebagai referensi dimensi. Lihat gambar untuk metode dimensi.
Bagian kotak
Secara umum, bentuk dan struktur bagian jenis ini lebih kompleks daripada tiga jenis bagian sebelumnya, dan posisi pemrosesan lebih banyak berubah. Bagian tersebut umumnya termasuk badan katup, badan pompa, kotak peredam dan bagian lainnya. Saat memilih tampilan utama, posisi kerja dan karakteristik bentuk terutama dipertimbangkan. Saat memilih tampilan lain, tampilan bagian yang sesuai, penampang, pandangan parsial, dan pandangan miring harus diadopsi sesuai dengan situasi aktual untuk secara jelas mengekspresikan struktur internal dan eksternal dari bagian tersebut.
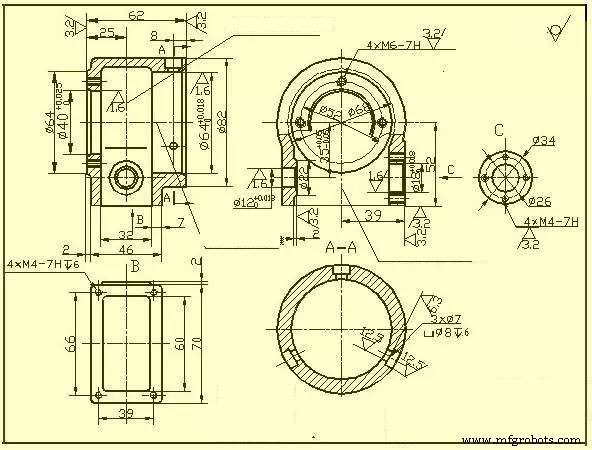
Dalam hal dimensi, sumbu, permukaan instalasi penting, permukaan kontak (atau permukaan pemrosesan), dan permukaan simetri (lebar, panjang) dari beberapa struktur utama kotak biasanya dipilih sebagai referensi dimensi. Untuk bagian-bagian pada kotak yang perlu dipotong, dimensinya harus ditandai sejauh mungkin untuk memudahkan pemrosesan dan pemeriksaan.
4 Kekasaran Permukaan
Karakteristik mikro-geometris puncak dan lembah dengan spasi kecil di permukaan bagian disebut kekasaran permukaan. Hal ini terutama disebabkan oleh bekas pahat yang ditinggalkan pahat pada permukaan bagian dan deformasi plastis pada permukaan logam selama pemotongan.
Kekasaran permukaan bagian juga merupakan indeks teknis untuk mengevaluasi kualitas permukaan bagian. Ini berdampak pada sifat perkawinan, akurasi kerja, ketahanan aus, ketahanan korosi, kedap udara, dan penampilan suku cadang.
Kode, simbol dan tanda kekasaran permukaan
GB/T 131-1993 menentukan kode kekasaran permukaan dan notasinya. Simbol pada gambar yang menunjukkan kekasaran permukaan bagian ditunjukkan pada tabel di bawah ini.
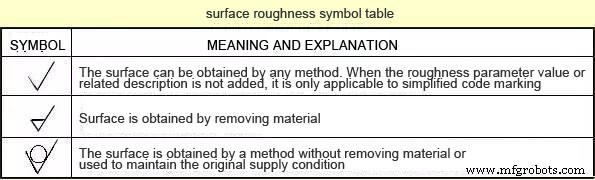
Parameter evaluasi utama kekasaran permukaan bagian
1) Deviasi rata-rata aritmatika kontur (Ra)
Dalam panjang sampling, rata-rata aritmatika dari nilai absolut dari offset kontur.
2) Tinggi profil maksimum (Rz)
Jarak antara garis atas puncak kontur dan garis bawah puncak kontur dalam panjang sampling.
Catatan:Parameter Ra lebih disukai saat menggunakannya.
Metode penandaan simbol kekasaran permukaan pada gambar
1) Kode kekasaran permukaan (simbol) umumnya harus dicatat pada garis kontur yang terlihat, garis batas atau perpanjangannya, dan ujung simbol harus menunjuk dari luar material ke permukaan.
2) Arah angka dan simbol dalam kode kekasaran permukaan harus ditandai sesuai kebutuhan.
Pada gambar yang sama, setiap permukaan umumnya ditandai dengan kode (simbol) hanya sekali, dan sedekat mungkin dengan garis dimensi yang relevan. Ketika ruang sempit atau tidak nyaman untuk diberi label, itu bisa mengarah ke label. Ketika semua permukaan bagian memiliki persyaratan kekasaran permukaan yang sama, mereka dapat ditandai secara seragam di sudut kanan atas gambar. Ketika sebagian besar bagian memiliki persyaratan kekasaran permukaan yang sama, kode (simbol) yang paling banyak digunakan dapat digunakan. Catat pada saat yang sama di sudut kanan atas gambar, dan tambahkan kata-kata "sisanya". Ketinggian kode (simbol) kekasaran permukaan yang ditandai secara seragam dan teks penjelasan harus 1,4 kali lipat dari tanda gambar.
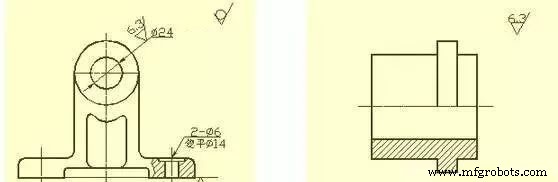
Nomor kode (simbol) kekasaran permukaan dari permukaan kontinu pada bagian tersebut, permukaan elemen berulang (seperti lubang, gigi, alur, dll.) dan permukaan terputus yang dihubungkan oleh garis padat tipis hanya dicatat satu kali.
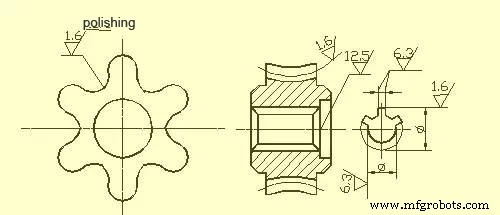
Jika ada persyaratan kekasaran permukaan yang berbeda pada permukaan yang sama, gunakan garis tipis tipis untuk menggambar garis pemisah, dan catat kode dan ukuran kekasaran permukaan yang sesuai.
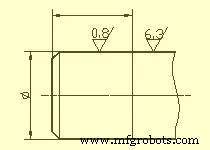
Bila bentuk gigi (gigi) tidak tergambar pada permukaan kerja roda gigi, ulir, dll., metode notasi kode kekasaran permukaan (simbol) ditunjukkan pada gambar.
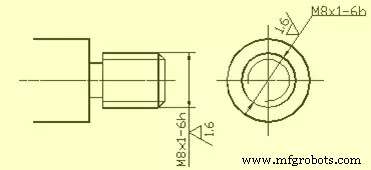
Permukaan kerja lubang tengah, permukaan kerja alur pasak, kode kekasaran permukaan talang, dan sudut membulat dapat disederhanakan dan ditandai.
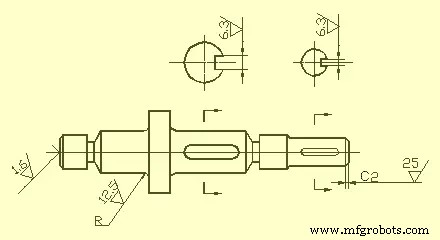
Ketika bagian-bagian perlu dipanaskan sebagian atau dilapisi sebagian (dilapisi), garis putus-putus tebal harus digunakan untuk menggambar rentang dan menandai dimensi yang sesuai. Persyaratan juga dapat ditulis pada garis horizontal sisi panjang simbol kekasaran permukaan.
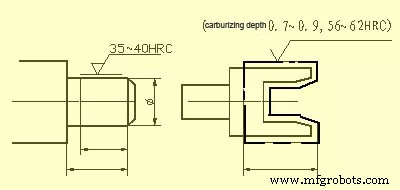
5 Toleransi Standar Dan Deviasi Dasar
Untuk memfasilitasi produksi, mewujudkan pertukaran suku cadang dan memenuhi persyaratan penggunaan yang berbeda, standar nasional "Batas dan Kesesuaian" menetapkan bahwa zona toleransi terdiri dari dua elemen:toleransi standar dan deviasi dasar. Toleransi standar menentukan ukuran zona toleransi, dan deviasi dasar menentukan lokasi zona toleransi.
1) Toleransi Standar (TI)
Nilai toleransi standar ditentukan oleh ukuran dasar dan kelas toleransi. Tingkat toleransi adalah tanda untuk menentukan keakuratan ukuran. Toleransi standar dibagi menjadi 20 level, yaitu IT01, IT0, IT1,…, IT18. Akurasi ukurannya menurun dari IT01 menjadi IT18. Nilai spesifik dari toleransi standar dapat ditemukan dalam standar yang relevan.
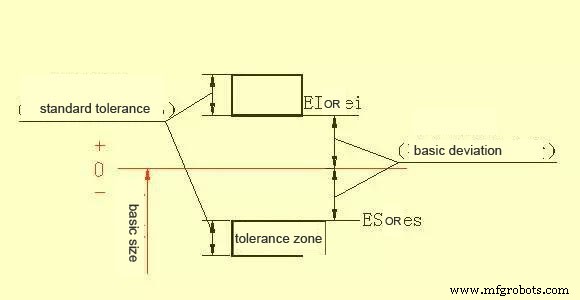
2) Penyimpangan dasar
Deviasi dasar mengacu pada deviasi atas atau bawah dari zona toleransi relatif terhadap posisi garis nol dalam batas standar dan fit, umumnya mengacu pada penyimpangan yang mendekati garis nol. Ketika zona toleransi berada di atas garis nol, deviasi dasar adalah deviasi yang lebih rendah; jika tidak, itu adalah deviasi atas. Ada 28 penyimpangan dasar secara total, dan kode dinyatakan dalam huruf Latin, dengan huruf besar sebagai lubang dan huruf kecil sebagai poros.
Deviasi dasar dan toleransi standar memiliki rumus perhitungan berikut sesuai dengan definisi toleransi dimensi:
ES=EI+IT atau EI=ES-IT