Analisis Kekritisan:Apa Itu dan Mengapa Penting
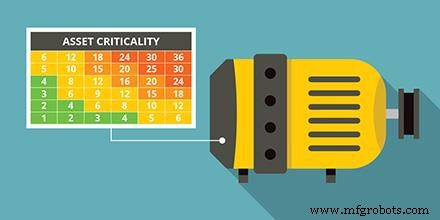
Analisis kritik didefinisikan sebagai proses pemberian peringkat kekritisan aset berdasarkan potensi risiko kegagalannya.
Apa itu Analisis Kekritisan?
Analisis kekritisan didefinisikan sebagai proses pemberian peringkat kekritisan aset berdasarkan potensi risikonya. Risiko didefinisikan sebagai "efek ketidakpastian pada tujuan," menurut ISO 31000:2009 – Manajemen Risiko – Prinsip dan Pedoman . Karena tidak dapat benar-benar diukur, risiko, dalam hal ini, dianggap sebagai semua kemungkinan cara aset dapat gagal dan efek kegagalan pada sistem dan operasi secara keseluruhan. Mengingat hal ini, analisis kekritisan terkait erat dengan mode kegagalan dan analisis efek (FMEA) dan mode kegagalan, efek dan analisis kekritisan (FMECA), yang akan dibahas nanti. Setelah analisis kekritisan dilakukan, FMEA biasanya dilakukan pada 20 persen teratas dari aset paling penting.
Apa Tujuan Analisis Kekritisan?
Jadi, mengapa analisis kekritisan itu penting? Anda terus-menerus mendengar tentang kekritisan — melakukan analisis kekritisan untuk memprioritaskan aset untuk rencana pemeliharaan produktif total (TPM), program pemantauan berbasis kondisi, atau analisis akar masalah pada peralatan prioritas tinggi. Kekritisan memainkan peran dalam hampir semua jenis pemeliharaan. Itu bermuara pada risiko dan apa yang membuat setiap peralatan menjadi penting. Analisis kekritisan memungkinkan Anda memahami potensi risiko aset yang dapat memengaruhi operasi Anda. Ini memastikan keandalan dilihat dari kaca pembesar berbasis risiko daripada pendapat setiap orang.
Menurut Life Cycle Institute, model analisis kekritisan harus mencakup beberapa area organisasi Anda termasuk:
- Dampak pelanggan
- Dampak terhadap keselamatan dan lingkungan
- Kemampuan untuk mengisolasi kegagalan titik tunggal
- Riwayat pemeliharaan preventif (PM)
- Riwayat pemeliharaan korektif
- Rata-rata waktu antar kegagalan (MTBF)
- Waktu tunggu suku cadang
- Probabilitas kegagalan
Karena model kekritisan berhubungan dengan banyak area organisasi, analisis kekritisan harus menjadi upaya di seluruh perusahaan. Termasuk departemen yang berhubungan dengan operasi, teknik, pemeliharaan, pengadaan, dan kesehatan dan keselamatan memastikan analisis mempertimbangkan semua fungsi operasi secara keseluruhan. Anda harus memahami bahwa risiko dapat didefinisikan secara berbeda di berbagai tim. Memiliki tim yang beragam yang memberikan masukan membantu subjektivitas dalam menetapkan risiko.
Analisis kekritisan juga penting karena dapat digunakan di berbagai skenario dalam suatu organisasi. Beberapa skenario ini mungkin terlihat seperti ini:
- Skor kekritisan dapat digunakan sebagai masukan untuk membantu menentukan peringkat prioritas akhir untuk tugas pemeliharaan, yang pada gilirannya dapat digunakan bersama dengan prioritas perintah kerja.
- Ini dapat membantu mengidentifikasi strategi mitigasi risiko tingkat tinggi untuk peralatan tertentu. Misalnya, ini dapat melibatkan penerapan teknik pemantauan kondisi pada aset yang sangat kritis.
- Ini dapat membantu menentukan jumlah suku cadang yang optimal untuk setiap peralatan.
- Ini dapat memberikan masukan yang berharga untuk diskusi penganggaran, sehingga peralatan dengan tingkat kritis tinggi diberikan prioritas yang lebih tinggi untuk peningkatan atau penggantian.
- Analisis kekritisan membantu teknisi keandalan memfokuskan upaya dan energi mereka pada aset yang paling penting.
Cara Melakukan Analisis Kekritisan
Penting untuk dicatat bahwa tidak ada satu pendekatan definitif untuk melakukan analisis kekritisan. Berikut adalah dua metode yang banyak digunakan, satu pendekatan sederhana untuk memulai dan metode mendalam lainnya.
Jadi, di mana Anda harus mulai? Banyak organisasi hanya ingin tahu aset mana yang harus dimasukkan dalam penilaian kekritisan. Alih-alih menganggap semua aset Anda penting, buatlah daftar aset utama yang menurut tim Anda penting dan hitung biaya waktu henti dan perbaikan. Anda mungkin akan terkejut dengan hasilnya. Misalnya, Anda mungkin memiliki ratusan motor yang bergerak konstan, yang cukup kritis, tetapi aset yang paling penting adalah boiler yang menghasilkan uap untuk menjaga motor tersebut tetap bergerak.
Karena inti dari pendekatan ini adalah untuk menemukan titik awal yang baik, mari kita lihat beberapa langkah tindakan yang dapat Anda ambil untuk memulai rencana kritis.
- Kumpulkan daftar aset untuk dipotong yang tidak akan melebihi 20 persen dari semua aset. Praktik terbaik untuk ini adalah rasio 5-ke-1 atau lebih besar.
- Kumpulkan tim personel dari sisi operasi, pemeliharaan, teknik, dan pengadaan organisasi untuk melakukan survei peralatan pabrik. Operator peralatan juga harus disertakan dalam tim ini.
- Selanjutnya, beri peringkat kekritisan aset menggunakan rumus yang telah ditetapkan. Solusi Keandalan Seumur Hidup menggunakan rumus berikut untuk menentukan dampak keuangan suatu aset:Kekritisan Peralatan =Frekuensi Kegagalan (per tahun) x Konsekuensi Biaya ($) =Risiko ($ per tahun) . Konsekuensi biaya dalam rumus ini adalah biaya produksi yang hilang ditambah biaya perbaikan. Misalnya, jika Anda memiliki banyak mesin yang identik, waktu henti mesin mungkin $400 per jam, per mesin.
Sekarang setelah Anda memiliki ide dasar tentang cara memulai, mari kita lihat pendekatan analisis kekritisan yang lebih mendalam dan efisien. Metode ini mencakup tiga langkah:menyetujui matriks risiko yang akan digunakan, menyusun hierarki peralatan Anda, dan menilai risiko kegagalan untuk setiap aset.
- Setuju dengan matriks risiko. Ini terutama mengacu pada matriks risiko perusahaan yang ada dan bagaimana sebagian besar matriks ini mungkin perlu disesuaikan untuk memasukkan penilaian kekritisan peralatan. Dua bidang utama di mana modifikasi mungkin diperlukan adalah menyepakati tingkat risiko dari tingkat perusahaan dan peralatan, dan menggabungkan kategori risiko yang tumpang tindih.
Pada tingkat perusahaan, kegagalan yang menyebabkan hilangnya pendapatan $1 juta mungkin dianggap kecil atau sedang , tetapi pada tingkat operasional peralatan atau pabrik, ini mungkin terlihat sebagai yang utama.
Kedua, matriks risiko yang mencakup kategori terpisah untuk hal-hal seperti kesehatan, keselamatan, lingkungan dan masyarakat dapat digabungkan, karena jika salah satu dari kategori ini terkena dampak kegagalan, yang lain juga akan terpengaruh. Menggabungkan kategori akan mempercepat analisis kekritisan.
- Kumpulkan hierarki aset Anda. Direkomendasikan agar peralatan atau hierarki aset Anda diletakkan di sepanjang garis fungsional, yang berarti lantai pabrik Anda memiliki sejumlah unit proses tertentu, unit proses tersebut terdiri dari sistem peralatan mereka sendiri, dan masing-masing sistem tersebut terdiri dari individu peralatan. Ini memungkinkan Anda melakukan analisis kekritisan jauh lebih cepat daripada jika hierarki aset Anda diatur oleh garis kelas peralatan. Meskipun aset Anda sudah diatur menurut lini fungsional, aset tersebut tetap harus ditinjau untuk memastikan tidak ada yang keluar jalur. Memiliki hierarki yang tersusun dengan benar di awal akan mempercepat analisis kekritisan nanti.
- Nilai risiko kegagalan setiap aset. Saat menilai risiko kegagalan untuk membantu menentukan kekritisan peralatan, pertimbangkan poin-poin berikut:
- memahami risiko yang berkaitan dengan peristiwa, bukan peralatan;
- pilih hanya satu peristiwa – peristiwa hasil yang wajar maksimum (MRO);
- lihat hanya dimensi dengan tingkat risiko tertinggi; dan
- mulai dari atas hierarki dan turun ke bawah.
Kedua, setiap peralatan dapat memiliki segudang kemungkinan peristiwa kegagalan, dan risiko yang terkait dengan masing-masing peristiwa tersebut berbeda. Akan sangat memakan waktu untuk mencoba dan mengidentifikasi semua kemungkinan peristiwa ini. Beberapa konsultan dan pakar keandalan merekomendasikan untuk memilih hanya satu peristiwa – peristiwa yang paling menggambarkan hasil wajar maksimum (MRO) dalam hal risiko untuk peralatan tertentu. Ini berarti Anda harus mencari peristiwa yang paling mungkin terjadi dan peristiwa di mana risiko keseluruhan ditentukan sebagai yang tertinggi.
Penentuan ini harus dilakukan di lingkungan tipe bengkel, karena individu dari departemen yang berbeda akan memiliki pendapat yang berbeda tentang acara MRO. Termasuk dalam diskusi ini adalah orang-orang yang paling mengetahui peralatan dan mereka yang memahami konsekuensi kegagalan dari perspektif bisnis.
Ketiga, pertimbangkan untuk menilai hanya satu dimensi risiko – dimensi dengan tingkat risiko tertinggi – untuk menghindari pemborosan waktu. Seperti disebutkan sebelumnya, melihat setiap peristiwa secara individual biasanya berakhir dengan membuang-buang waktu, karena banyak yang secara langsung mempengaruhi yang lain. Seringkali, cukup jelas dimensi risiko mana yang memiliki tingkat risiko tertinggi. Misalnya, jika Anda mengevaluasi kekritisan katup pelepas tekanan di pabrik gas alam, risiko yang terkait dengan keselamatan adalah apa yang akan Anda lihat (termasuk dampak lingkungan dan masyarakat). Jika Anda menilai komponen yang menyediakan listrik untuk mengoperasikan peralatan pabrik, kemungkinan besar Anda akan mempertimbangkan dampak ekonomi dari kegagalan tersebut.
Terakhir, untuk memastikan pendekatan analisis kekritisan Anda efisien dan efisien, mulailah dari atas hierarki peralatan dan turunkan. Hal terbaik tentang pendekatan ini adalah, secara logika, aset atau peralatan apa pun di tingkat hierarki yang lebih rendah tidak dapat memiliki peringkat kekritisan yang lebih tinggi daripada aset di atasnya. Dengan kata lain, segera setelah Anda mengidentifikasi peralatan di salah satu kategori yang lebih rendah dalam hierarki Anda di mana peringkat kekritisan rendah, item apa pun di bawah peralatan ini juga harus termasuk dalam kategori yang sama, menghilangkan kebutuhan untuk menganalisis kekritisannya. Seperti yang dapat Anda bayangkan, ini menekankan pentingnya membangun hierarki Anda dengan benar sejak awal.
Memvisualisasikan Analisis Kekritisan
Ketika berbicara tentang menyusun peringkat kekritisan secara visual, Anda akan menemukan banyak teori tentang cara terbaik untuk melakukan ini. Salah satu pendekatan yang paling umum adalah dengan menggunakan kisi 6x6, yang memplot probabilitas kegagalan terhadap tingkat keparahan kegagalan, yang menghasilkan nomor prioritas risiko (RPN).
Mungkin pendekatan yang lebih umum adalah mengevaluasi semua kategori utama (operasional, kesehatan, keselamatan dan lingkungan, keandalan, dll.) secara individual untuk mencari tahu kasus terburuk kegagalan. Jenis analisis ini akan meminta anggota tim menetapkan setiap konsekuensi nomor risiko, yang kemudian ditambahkan atau dikalikan dengan masing-masing konsekuensi, memberikan RPN akhir. Sebagian besar organisasi menggunakan skor kekritisan yang diturunkan dari peringkat 0-6 hingga 0-10 yang ditentukan untuk setiap kategori, dengan 0 tidak berdampak dan 6 (atau 10) memiliki dampak paling besar. Misalnya, jika Anda menilai risiko dampak keselamatan, kesehatan, dan lingkungan dari suatu aset, Anda dapat menentukan dampak kegagalan berdasarkan hal berikut:
Cara melakukan dan memvisualisasikan analisis kekritisan ini harus dilakukan dalam dua tahap. Fase pertama adalah analisis awal dari tim lintas fungsi dengan masukan dari operasi; pemeliharaan; pengadaan teknik; dan lingkungan, kesehatan dan keselamatan (EH&S). Fase kedua adalah menjaga proses analisis selalu hijau atau mempertahankan proses analisis kekritisan sepanjang siklus hidup aset. Ini membantu Anda mengetahui kapan risiko telah dikurangi atau jika ada perubahan signifikan pada setiap aset.
Membuat visual untuk proses Anda melakukan analisis kekritisan dan menentukan peringkat kekritisan akhir dapat dilakukan dalam 10 langkah:
- Langkah 1: Pilih karakteristik yang ingin Anda gunakan untuk mengevaluasi setiap aset. Karakteristik ini harus mencakup berbagai aspek bisnis, seperti dampak pada pelanggan, dampak EH&S, kemampuan untuk mengisolasi dan memulihkan dari kegagalan titik tunggal, riwayat pemeliharaan preventif, riwayat pemeliharaan korektif, dll.
- Langkah 2: Timbang setiap karakteristik menggunakan skala 0 hingga 10 untuk menggambarkan signifikansinya bagi bisnis. Anda juga dapat menggunakan skala yang lebih besar (semakin besar skalanya, semakin mudah untuk mengidentifikasi aset penting), tetapi skalanya tidak boleh melebihi 100.
- Langkah 3: Tentukan deskripsi setiap karakteristik pada skala untuk akurasi.
- Langkah 4: Buat daftar (atau impor) hierarki aset Anda.
- Langkah 5: Tentukan fungsi utama setiap aset untuk mengidentifikasi kegagalan satu titik.
- Langkah 6: Analisis efek kegagalan satu titik untuk setiap aset di semua karakteristik.
- Langkah 7: Hitung peringkat kekritisan untuk setiap aset dengan membagi skor mentah (jumlah semua karakteristik) dengan total poin tertimbang yang mungkin, dikalikan dengan 100.
- Langkah 8: Identifikasi 10-20 persen teratas dari aset penting.
- Langkah 9: Tinjau analisis Anda dan temukan karakteristik yang membuat setiap aset penting.
- Langkah 10: Terakhir, identifikasi aset yang paling signifikan untuk area bisnis yang penting, seperti keandalan, biaya, nilai penggantian, pengembangan rencana pemeliharaan, dll.
Analisis Kekritisan:Pendekatan FMECA
Mode kegagalan, efek dan analisis kekritisan (FMECA) dikembangkan pada akhir 1940-an oleh militer Amerika Serikat untuk transisi dari pendekatan "mengidentifikasi kegagalan dan memperbaikinya" ke pendekatan "mengantisipasi kegagalan dan mencegahnya". Metodologi ini kemudian distandarisasi dan diterbitkan sebagai standar militer:MIL-STD_ 1629A. FMECA melibatkan analisis kegagalan kuantitatif, artinya menggunakan kuantitas dan angka untuk menilai risiko dan potensi kegagalan.
FMECA dan FMEA adalah alat yang terkait erat yang digunakan untuk melakukan analisis kekritisan; satu adalah alat kualitatif (FMEA) yang melihat skenario "bagaimana-jika", sementara yang lain (FMECA) adalah alat kuantitatif yang mempertimbangkan RPN. Memanfaatkan FMEA dengan FMECA, Anda dapat melakukan analisis kekritisan untuk memastikan area bisnis tertentu seperti desain, operasi, dan biaya dioptimalkan.
Porsi FMEA pendekatan kekritisan ini melibatkan pendefinisian sistem, membangun batas sistem dan diagram parameter, mengidentifikasi mode kegagalan, menganalisis efek kegagalan, menentukan akar penyebab mode kegagalan, dan memberikan hasil kepada tim desain. Porsi FMECA termasuk mentransfer semua yang dipelajari dari FMEA ke FMECA, mengklasifikasikan efek kegagalan berdasarkan tingkat keparahan, melakukan perhitungan kekritisan, memeringkat kekritisan mode kegagalan dan menentukan item risiko tertinggi, mengambil tindakan untuk mengurangi kegagalan dan mendokumentasikan risiko yang tersisa, dan menindaklanjuti efektivitas tindakan koreksi .
Melakukan analisis kekritisan menggunakan metodologi FMECA memberikan nilai di departemen desain dan pengembangan, operasi, dan manfaat biaya, termasuk:
- Manfaat desain dan pengembangan mencakup peningkatan keandalan aset, kualitas peralatan yang lebih baik, margin keamanan yang lebih tinggi, dan penurunan waktu pengembangan dan desain ulang.
- Manfaat operasi menyertakan cara yang lebih efektif untuk mengurangi biaya, program pemeliharaan preventif dan prediktif (PdM) yang dioptimalkan, analisis pertumbuhan keandalan selama pengembangan produk, dan pengurangan pemborosan dan operasi yang tidak bernilai tambah atau meningkatkan prinsip lean manufacturing.
- Manfaat biaya termasuk kemampuan untuk mengurangi atau mengenali kegagalan sebelum terjadi ketika kesalahan tersebut lebih murah untuk diperbaiki, meminimalkan biaya garansi, dan meningkatkan penjualan karena kepuasan pelanggan.
Karena cukup memakan waktu untuk dipraktikkan, pendekatan FMECA umumnya bukan metode "masuk" untuk melakukan analisis kekritisan; namun, beberapa grup konsultan keandalan memiliki sumber daya untuk membantu Anda jika organisasi Anda memilih metode ini.
Analisis Kekritisan:Intinya
Analisis kekritisan adalah alat yang hebat untuk mengidentifikasi prioritas tugas pemeliharaan. Cara yang baik untuk melihatnya adalah bahwa prioritas tugas pemeliharaan harus ditetapkan oleh tingkat risiko yang datang dengan tidak melakukan tugas itu. Secara kebetulan, tingkat risiko yang terkait dengan tidak melakukan tugas pemeliharaan tertentu ditentukan oleh konsekuensi dari potensi kegagalan yang dapat terjadi jika tugas tidak diselesaikan dan kemungkinan kegagalan tersebut terjadi jika tugas tidak dilakukan pada waktu yang telah ditentukan. waktu.
Setelah Anda memiliki peringkat kekritisan Anda, analisis kekritisan dapat membantu Anda memilih strategi mitigasi risiko yang tepat yang dapat Anda terapkan untuk setiap aset. Misalnya: