Apakah Pemicu Upaya RCA Anda Senang?
Sebagian besar lingkungan kerja bersifat reaktif. Selalu ada lebih banyak pekerjaan yang harus dilakukan dalam sehari maka ada waktu untuk melakukan pekerjaan. Ini karena perubahan lingkungan kerja yang tidak terduga yang menyebabkan tenaga kerja segera merespon dan tanpa persiapan untuk mengembalikan lingkungan mereka kembali ke status quo.
Karena itu, beberapa perusahaan telah memilih untuk melakukan analisis akar masalah atas kejadian tak terduga ini. Ketika berhadapan dari sudut pandang reaktif, manajemen akan memulai pemicu yang akan menjalankan kinerja analisis akar penyebab berdasarkan tingkat getaran, jam henti, dampak keuangan, dll. Penempatan pemicu adalah langkah pertama yang BAIK dan perlu.
Alasan langkah pertama yang baik adalah karena perkembangan alami adalah untuk pertama-tama menyadari bahwa fasilitas tersebut reaktif ke tingkat yang berlebihan. Penemuan ini biasanya melalui pelaporan downtime harian atau mingguan. Setelah ditentukan ada masalah, langkah-langkah untuk mengendalikan situasi diimplementasikan. Pemicu hampir selalu merupakan respons pertama.
Beberapa perusahaan mengukur kinerja pemecahan masalah karyawan berdasarkan sistem pembobotan jenis masalah. Semakin sering masalah muncul kembali, semakin banyak poin yang dikumpulkan karyawan dan kemudian diberi skor pada akhir tahun. Perusahaan lain mengukur kinerja pemecahan masalah karyawan dengan menugaskan 10 atau 12 investigasi kegagalan untuk diselesaikan pada akhir setiap tahun.
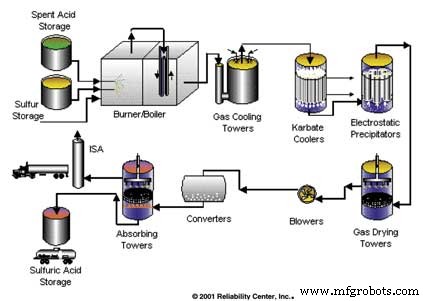
Gambar 1. Diagram alir proses untuk pabrik asam sulfat.
Semua upaya ini didasarkan pada aktivasi beberapa peristiwa yang tidak diinginkan. Kejadiannya dapat berkisar dari gangguan listrik yang mematikan seluruh bagian fasilitas hingga poros pemecah pompa yang kritis setiap dua bulan. Mengapa menunggu pemicu trip dan menimbulkan downtime dan kerusakan aset? Jauh lebih sulit untuk melakukan analisis akar penyebab ketika terjadi kerusakan sekunder yang parah. Faktanya adalah bahwa pemicu adalah cara reaktif untuk mengontrol peristiwa yang tidak terjadwal.
Perkembangan alami dari pengetahuan baru ini adalah berhenti menunggu pemicu diaktifkan dan menjadi proaktif. Ketika langkah ini tercapai, fasilitas dapat pindah ke tingkat berikutnya, HEBAT. Ini juga akan menghilangkan tekanan karyawan untuk memberikan skor untuk penilaian kinerja yang mungkin dilakukan dengan tergesa-gesa untuk memenuhi persyaratan.
Melakukan analisis mode dan efek kegagalan (FMEA) adalah cara untuk mengganti pemicu dan memberi tahu manajemen bahwa upaya analisis akar masalah didasarkan pada hasil moneter yang baik. Setiap analisis akar penyebab yang diselesaikan akan memiliki nilai yang telah ditentukan yang telah diidentifikasi menggunakan FMEA. Ini berubah dari BAIK menjadi HEBAT.
Proaction adalah wawasan untuk melihat area operasi dengan pendekatan terstruktur yang dirancang untuk mengungkap kejadian potensial yang akan menyebabkan pemicu aktif. Ini dapat dicapai dengan menggunakan FMEA. Ini adalah istilah yang sering digunakan, tetapi artinya berbeda bagi orang yang berbeda. Benang merahnya adalah ini:FMEA memberikan fokus dan poin pada peluang yang akan memberikan peningkatan yang terukur pada fasilitas.
FMEA adalah pendekatan proaktif untuk mengungkap apa yang tidak Anda ketahui tentang operasi Anda. Hal ini penting karena ada anggapan bahwa kita sudah mengetahui identitas masalah manufaktur kita. Ini sebagian besar tidak benar.
Beberapa mungkin tahu apa masalah terburuknya, tetapi kemungkinan besar fasilitas tidak tahu apa masalah terburuk kedua atau ketiga, keempat dan seterusnya. Dalam banyak kasus, kita tidak tahu masalah apa yang sebenarnya merugikan kita karena masalah tersebut tidak terdeteksi dan telah menjadi bagian dari berbisnis.
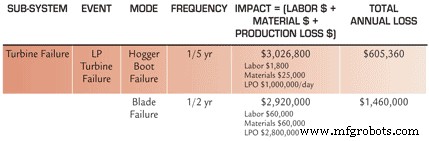
Gambar 2. Contoh lembar kerja pengumpulan data.
Contohnya adalah peralatan yang membuat barang berwujud, seperti mesin pembuat rokok atau mesin pengubah kertas. Jenis peralatan ini dapat dinyalakan dan dimatikan berkali-kali selama shift karena berbagai alasan.
Operator terkadang mematikan peralatan karena cacat kualitas atau beroperasi dengan kecepatan rendah karena tingkat kapasitas penuh menyebabkan startup dan penghentian yang berlebihan, yang pada gilirannya menyebabkan operator bekerja lebih keras daripada jika peralatan dijalankan dengan kecepatan rendah.
Mari kita ambil contoh dari industri rokok. Contoh ini dapat dengan mudah diterapkan untuk membuat permen, baut atau klip kertas. Dalam industri rokok, ada downtime yang dihasilkan secara elektronik yang disebut rod break. Saat kondisi ini terjadi, operator merespon dengan mengumpulkan bagian kertas dari batang rokok dan membuangnya ke tempat sampah.
Operator kemudian mengembalikan tembakau yang hilang dari batang ke dalam wadah pengerjaan ulang, memasang kembali kertas rokok dan menekan tombol mulai untuk mengembalikan peralatan ke mode produksi. Proses ini membutuhkan waktu tiga hingga empat menit bagi operator.
Respons operator adalah tindakan tugas yang dipelajari selama siklus pelatihannya. Respons ini dapat berlangsung 40 hingga 50 kali shift, yang mengurangi produktivitas mesin di akhir tahun hingga lebih dari 20 juta batang rokok. Ini tidak ada di layar radar karena itu adalah tugas yang dilakukan secara teratur; itu dianggap sebagai bagian dari melakukan pekerjaan.
Ada banyak kejadian kecil kerugian yang terjadi setiap hari di fasilitas dan dianggap sebagai "cara kita melakukan bisnis." Ketika kejadian ini diekspos dan dihitung untuk kerugian tahunan dalam jam dan dolar, dampak finansial terhadap fasilitas menjadi jelas.
Di mana Anda mendapatkan data untuk melakukan FMEA? Manajer dan lainnya sering mengatakan bahwa karyawan adalah aset terbesar. Namun, karena teknologi, analis lebih memilih informasi dari sistem manajemen pemeliharaan. Ini adalah cara cepat untuk mendapatkan data waktu henti, data penggunaan suku cadang, dll.
Paling sering, data yang disediakan oleh sistem manajemen pemeliharaan adalah apa yang ada di layar radar atau apa yang sudah kita ketahui. Saat data di bawah radar dicari, data tersebut dikumpulkan dari sumber informasi yang paling mungkin tidak terdeteksi atau di bawah radar - karyawan.
Tidak berlebihan untuk mengatakan bahwa orang yang mengoperasikan dan memelihara fasilitas mengetahui hal-hal tentang lingkungan mereka yang tidak akan pernah diketahui kecuali diminta. Sebagian besar karyawan menemukan cara mengatasi masalah yang menyebabkan mereka kesakitan atau tenaga ekstra untuk melakukan pekerjaan.
Ini mungkin termasuk mengabaikan alarm yang berbunyi tanpa alasan yang jelas, bekerja dengan kecepatan rendah, mengganti filter sebelum waktunya, menambahkan set-sekrup ke kopling yang kendor, menjepit bantalan agar tidak bergerak, tack-welding impeller retak. Daftarnya bisa terus dan terus. Jenis aktivitas ini memengaruhi produktivitas dan kemungkinan besar tidak akan pernah muncul dalam sistem manajemen pemeliharaan.

Gambar 3. Contoh lembar kerja pengumpulan data elektronik.
Manajemen dapat membuka pintu ini dan belajar dari karyawan dengan mengikuti metode tiga langkah untuk melakukan FMEA yang sukses.
- Buat diagram alur proses untuk sistem yang ingin Anda analisis.
- Buat definisi kegagalan untuk dikomunikasikan dari manajemen tingkat atas ke tangan di tingkat kerja.
- Buat lembar kerja pengumpulan data FMEA yang mencerminkan masalah yang menjadi perhatian, seperti limbah material, tingkat kerusakan, waktu henti, insiden keselamatan, dll.
Buat diagram alur proses: Diagram alir proses mencerminkan perutean proses. Ini biasanya dari input bahan mentah ke titik penyimpanan atau pengiriman (lihat Gambar 1).
Alasan melakukan ini adalah untuk memberikan gambaran visual kepada fasilitator FMEA dan karyawan selama proses wawancara.
Buat definisi kegagalan: Definisi kegagalan yang jelas dan ringkas diperlukan untuk memastikan karyawan dan manajemen memiliki pemahaman yang sama tentang apa yang dianggap sebagai kegagalan. Tanpa pemahaman ini, hasil kebingungan dan analisis Anda terganggu. Definisi kegagalan biasanya dinodai oleh iklim bisnis, kondisi yang terjual habis atau siklus penjualan yang lambat. Definisi kegagalan juga dapat melingkupi masalah saat ini yang dialami suatu area, seperti tingkat pengerjaan ulang yang tinggi, tingkat cacat yang tinggi, tingkat cedera tangan yang tinggi, dll.
Beberapa contoh definisi kegagalan adalah:
-
Kegagalan adalah ketika terjadi cacat sekunder.
-
Kegagalan adalah setiap kejadian buruk yang memiliki akar manusia.
-
Kegagalan adalah ketika aset menjadi tidak dapat dioperasikan.
-
Kegagalan adalah saat aset tidak dapat lagi menjalankan fungsinya.
-
Kegagalan adalah setiap peristiwa atau kondisi yang mengganggu produksi.
-
Kegagalan adalah setiap peristiwa atau kondisi yang menyebabkan pengeluaran uang anggaran yang tidak terduga.
Ketika konsensus diperoleh pada definisi kegagalan, Anda siap untuk menyusun lembar kerja pengumpulan data FMEA.
Membuat lembar kerja pengumpulan data: Peran lembar kerja pengumpulan data adalah untuk menciptakan kapasitas untuk menangkap data yang diperlukan untuk mengidentifikasi beberapa kegagalan yang signifikan dari yang lainnya. Untuk melakukan ini, aturan yang sangat sederhana digunakan:frekuensi dikalikan dengan dampak. Konfigurasi lembar kerja pengumpulan data melakukan beberapa hal untuk analisis. Ini mengidentifikasi kejadian, mode yang menyebabkan kejadian, frekuensi mode dan dampak kombinasi mode kejadian pada sistem yang dianalisis (gambar 2 dan 3).
Temuan ini memungkinkan Anda untuk mengungkap apa
Anda tidak tahu. Ini memungkinkan Anda untuk mengubah
hasilnya karena Anda mengetahui biaya bisnis Anda saat ini.
Ini menempatkan Anda di kursi catbird. Anda dapat melihat apa yang orang lain tidak bisa karena Anda meluangkan waktu untuk melihat. Sekarang Anda dapat membuat keputusan berdasarkan informasi yang solid, yang memberi Anda keuntungan bisnis.
Dengan keuntungan ini, Anda dapat memilih proyek yang ingin Anda lakukan akar penyebabnya dengan kerugian yang terjadi pada fasilitas selama satu tahun. Ini tidak akan terjadi ketika bereaksi terhadap proyek analisis akar penyebab yang dipicu. Proyek yang dipicu dalam beberapa kasus dapat mengikat aset manusia yang berharga yang dapat dimanfaatkan dengan lebih baik pada proyek yang memberikan keuntungan lebih besar bagi organisasi.
Mark Latino adalah wakil presiden operasi untuk Reliability Center Inc. Dia datang ke RCI setelah menghabiskan 19 tahun di perusahaan Amerika (Weyerhaeuser, Allied Chemical, Philip Morris). Untuk informasi lebih lanjut, kunjungi www.reliability.com atau hubungi 804-458-0645.