Studi Kasus Pemeliharaan Prediktif
Studi kasus yang disajikan dalam artikel ini adalah data aktual yang dianalisis oleh penulis. Studi kasus perawatan prediktif yang mewakili analisis getaran akan menyajikan contoh dan perbandingan kesalahan bantalan, kondisi tidak seimbang, dan pengujian dampak untuk frekuensi alami.
Setiap contoh akan direpresentasikan sebagai spektrum dan, dalam beberapa kasus, bentuk gelombang waktu yang akan memberikan bukti kesalahan yang ada di segmen data tertentu.
Laporan oli juga disajikan untuk memberikan bukti konklusif tentang kondisi oli kotor, dengan target tingkat kebersihan ISO yang diidentifikasi untuk referensi.
Kebersihan oli sangat penting dalam menghilangkan kegagalan komponen dini dan memperpanjang umur peralatan. Ini memungkinkan departemen pemeliharaan bekerja untuk meningkatkan waktu kerja dan ketersediaan alat berat.
Termografi inframerah diwakili oleh gambar termal komponen peralatan dengan variasi suhu. Bahkan sedikit variasi suhu dapat menunjukkan potensi masalah pada komponen mesin. Personil terlatih yang mampu menafsirkan gambar termal adalah komoditas berharga di arena pemeliharaan keandalan.
Motor listrik sangat penting untuk pengoperasian fasilitas manufaktur industri. Ada dua mode kegagalan potensial yang mempengaruhi motor listrik, kegagalan bantalan atau kegagalan belitan listrik. Setiap jenis mode kegagalan dapat dideteksi dan diprediksi, memungkinkan perawatan merencanakan dan menjadwalkan pemindahan motor untuk menghindari waktu henti yang tidak diinginkan.
Kerusakan isolasi belitan listrik dapat dideteksi dengan analisis arus motor yang memungkinkan personel pemeliharaan prediktif untuk memprediksi kegagalan dini dari suatu masalah potensial.
Studi Kasus Data Getaran (Gear Mesh)
Semua set roda gigi membuat komponen frekuensi yang disebut sebagai jaring roda gigi. Frekuensi dasar gir-mesh sama dengan jumlah gigi gir dikalikan kecepatan lari poros. Selain itu, semua set roda gigi membuat serangkaian pita samping atau modulasi yang terlihat di kedua sisi frekuensi jaring roda gigi utama.
Data yang ditunjukkan pada Gambar 1 di bawah ini mewakili blok data yang dikumpulkan pada gearbox planet dalam operasi kayu dimensional. Frekuensi yang diinginkan terlihat pada 37.915.8 cycles per minute (CPM) dengan harmonik frekuensi tersebut terlihat lagi pada 75.831.6 CPM. Pita samping terlihat jelas di kedua sisi frekuensi yang bersangkutan. Diagnostik masalah ini agak sulit untuk didiagnosis karena keterlibatan konfigurasi unit roda gigi. Unit khusus ini adalah satu set roda gigi planetary, yang berarti bahwa poros input (gigi matahari) memiliki tiga roda gigi yang berputar atau mengorbit di sekitar roda gigi matahari, yang pada gilirannya menyatu dengan roda gigi lingkar luar.
Dengan semua penyatuan roda gigi di dalam kotak roda gigi, mengidentifikasi frekuensi jala roda gigi bisa jadi sulit. Pada Gambar 1, frekuensi diidentifikasi dan dicocokkan dengan frekuensi dalam spektrum. Perhatikan dampak dalam bentuk gelombang waktu di bagian bawah contoh. Ini adalah indikasi yang baik untuk menghubungkan gigi dengan cacat pada gigi.
Jenis pitting dan spalling pada gigi gir ini disebabkan oleh kontaminasi pada oli di dalam unit. Tekanan di antara gigi saat menyatu satu sama lain bisa mencapai 300.000 pon per inci persegi (psi). Pasir dan kotoran jauh lebih keras daripada logam; ketika ditekan di antara gigi roda gigi, mereka menyebabkan lekukan pada gigi, yang menyebabkan spalling dan pitting. Setelah masalah didiagnosis, laporan dibuat dan unit tidak dapat digunakan. Itu dikirim ke bengkel, dan setelah dibongkar, ditemukan bahwa ketiga unit roda gigi planetary memiliki cacat yang terlihat pada giginya.
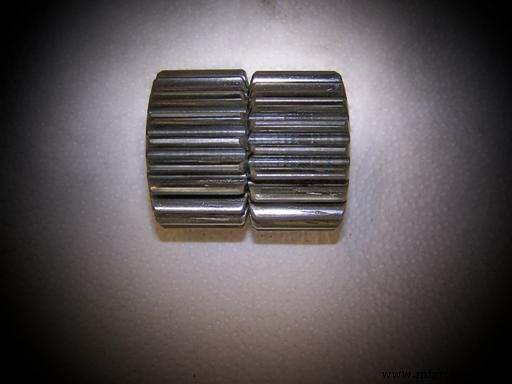
Gambar 1. Data Gear Mesh
Ini hanyalah salah satu contoh manfaat dari teknologi pemeliharaan prediktif, dalam hal ini analisis getaran. Jika masalah ini tidak terdeteksi oleh analisis getaran, itu akan terus berkembang ke titik kegagalan bencana. Saat cacat terbentuk, gigi gir terus menggerus permukaan logam, memasukkan logam ke dalam girboks dan menciptakan efek domino.
Masalah ini juga dapat dideteksi dengan analisis oli. Dengan mengambil sampel oli, seseorang akan dapat mendeteksi logam aus di gearbox melalui analisis.
Prosedur pemeliharaan prediktif korektif dapat mengurangi kepastian kegagalan katastropik. Gambar 2 menunjukkan data getaran blower yang perlu diseimbangkan. Gambar 3 menunjukkan pengurangan getaran setelah pekerjaan keseimbangan selesai. Ini hanyalah contoh lain bagaimana perawatan prediktif dapat mengubah kondisi mesin.
Pada Gambar 2, perhatikan amplitudo tinggi pada kecepatan berjalan 1X dari blower. Ini merupakan indikasi ketidakseimbangan dalam elemen berputar dari blower.
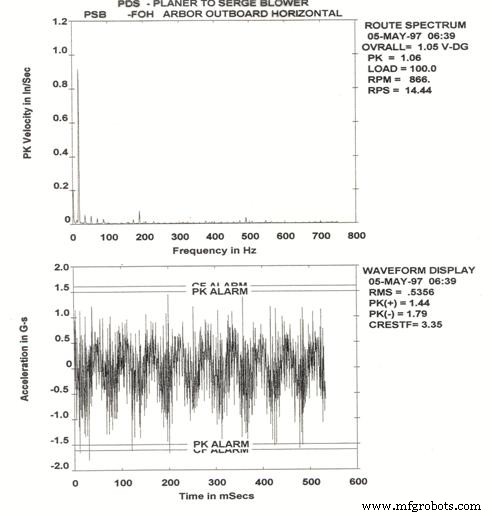
Gambar 2. Data Getaran dari Kipas
Setelah menyelesaikan pekerjaan penyeimbangan yang ditunjukkan pada Gambar 3, terjadi perubahan amplitudo yang drastis. Pengurangan getaran akan memperpanjang masa pakai peralatan dan memungkinkan pengoperasian bebas masalah.
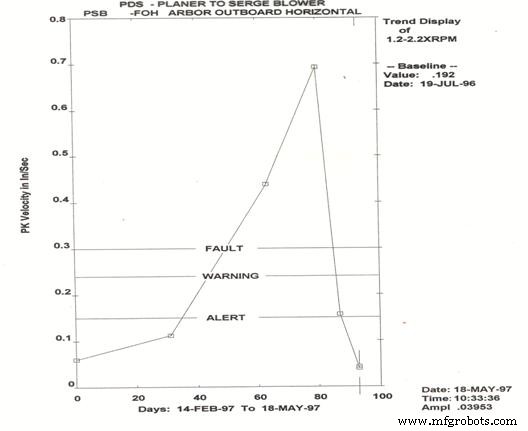
Gambar 3. Data Tren Getaran
Perhatikan tren data pada Gambar 3. Setelah menyeimbangkan getaran kipas, amplitudo turun jauh di bawah tingkat alarm yang disetel untuk mesin.
Mendiagnosis masalah hanyalah permulaan dalam proses pemeliharaan prediktif. Setelah masalah terdeteksi, memastikan bahwa masalah tidak terulang lagi dalam beberapa bulan atau bahkan beberapa tahun adalah tujuannya. Salah satu tujuan analis yang baik seharusnya tidak hanya mendeteksi mode kegagalan tetapi juga menemukan akar penyebab masalah dan mencegahnya terjadi lagi.
Gambar 1-3 memeriksa masalah penyambungan roda gigi dan data yang terkait dengannya, serta kondisi ketidakseimbangan pada blower. Gambar 4 merupakan masalah bantalan dengan cacat ras luar. Perhatikan pita samping di sekitar frekuensi kesalahan ras luar? Hal ini disebabkan oleh modulasi dalam bentuk gelombang waktu. Jika Anda melihat bentuk gelombang waktu di bawah spektrum, Anda dapat melihat modulasi amplitudo yang ada.
Umumnya, jenis modulasi ini akan mewakili frekuensi operasi dari elemen berputar dari mesin yang bersangkutan.
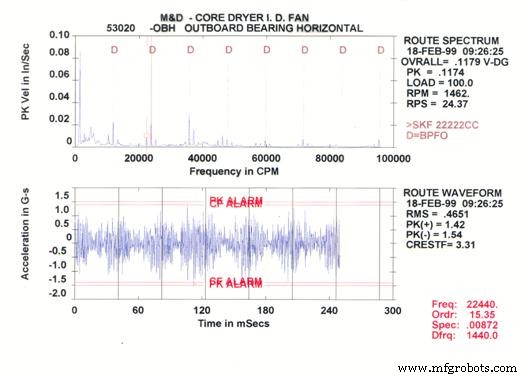
Gambar 4. Data Getaran dari Bearing Rusak
Informasi lain yang ada pada data yang disajikan adalah jenis bantalan SKF 22222CC. Informasi ini dimasukkan ke dalam perangkat lunak untuk memungkinkan perangkat lunak memberi label frekuensi kesalahan dalam spektrum. Perangkat lunak ini memiliki database yang memiliki lebih dari 10.000 frekuensi kesalahan bantalan yang dihitung. Ini membantu mengurangi waktu yang berharga dan membuat pekerjaan analis menjadi lebih mudah.
Analisis getaran dapat menjadi alat diagnostik yang kuat. Mengidentifikasi kegagalan bantalan, masalah roda gigi, dan kondisi ketidakseimbangan dan ketidaksejajaran bukan satu-satunya hal positif yang disediakan oleh teknologi ini. Menentukan parameter pengoperasian seperti kondisi resonansi potensial memberikan keuntungan besar saat merancang dan menentukan kecepatan pengoperasian.
Tekanan untuk terus mempercepat atau mengubah kondisi operasi hanya akan meningkat dengan fasilitas manufaktur yang sangat kompetitif yang kami kerjakan setiap hari. Masalah dengan perubahan kecepatan mesin berputar adalah bahwa pada titik tertentu kita menjelajah ke frekuensi alami dari struktur atau elemen berputar. Ketika kecepatan operasi mesin yang berputar dan frekuensi alami menjadi terlalu dekat, suatu kondisi yang disebut resonansi tereksitasi. Ini akan meningkatkan amplitudo mesin sebanyak 20 kali dan dapat menyebabkannya berguncang sendiri. Untuk menentukan frekuensi yang harus dihindari saat memodifikasi atau merancang mesin, pengujian seperti uji tumbukan harus dilakukan. Pada Gambar 5, contoh hasil uji dampak disediakan.
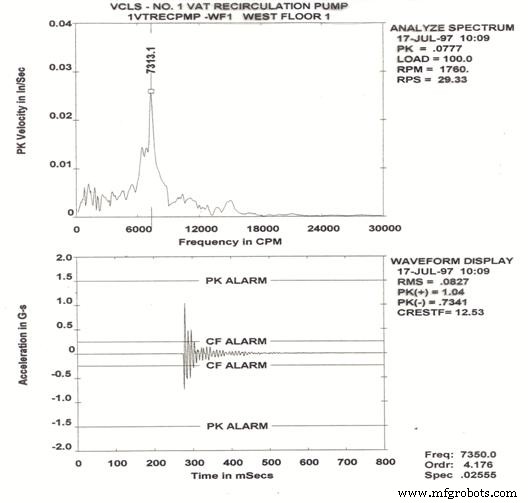
Gambar 5. Data Mengidentifikasi Frekuensi Alami Struktur
Data pada Gambar 5 merupakan uji dampak yang valid. Mencoba mengoperasikan mesin yang berputar dalam 20 persen dari 7.313,1 CPM akan menyebabkan kondisi pengoperasian yang buruk dan mesin tidak dapat diandalkan sepanjang masa pakai mesin.
Studi Kasus Termografi Inframerah
Termografi inframerah adalah teknologi populer untuk pemeliharaan prediktif karena alasan yang jelas. Sangat mudah untuk melihat di mana letak masalahnya, dan masalah yang terdeteksi agak lebih mudah untuk didiagnosis oleh teknisi. Pelatihan dan sertifikasi nasional masih sangat dianjurkan untuk menjadi kompeten dalam menganalisis data termografi. Sangat penting untuk mempertimbangkan suhu sekitar saat menganalisis dan tren data yang dikumpulkan.
Data pada Gambar 6 menunjukkan starter kontrol motor dengan sambungan longgar pada kabel terminal “B”.
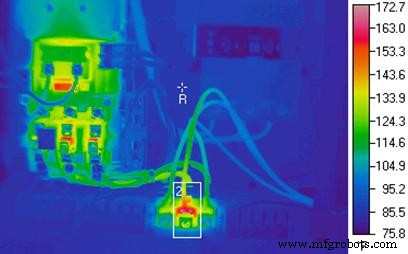
Gambar 6. Data Inframerah Starter Motor, Diambil oleh Penulis
Suhu dalam persegi panjang pada gambar inframerah yang mengidentifikasi terminal "B" memiliki suhu maksimum 172,8 derajat Fahrenheit. Ketika koneksi menjadi longgar, mereka menghasilkan panas yang berlebihan. Ketika kondisi ini terjadi, kawat akan terbakar menjadi dua, menyebabkan motor yang dikendalikan menjadi satu fasa. Kondisi ini akan menyebabkan motor listrik mati sebelum waktunya.
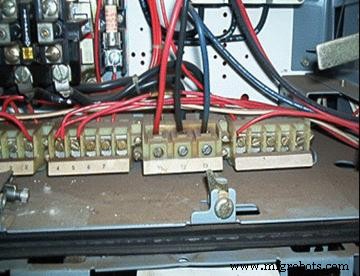
Gambar 7. Gambar Area Masalah
Gambar 7 adalah foto kontrol yang diambil untuk membantu teknisi listrik dalam mengidentifikasi area masalah. Bagian dari proses pemeliharaan prediktif adalah mengembangkan laporan yang akan membuat pekerjaan teknisi perbaikan semudah mungkin. Teknisi yang mendiagnosis masalah biasanya bukan yang melakukan perbaikan.
Aplikasi untuk termografi inframerah masih ditemukan dan digunakan dengan setiap studi kasus pemeliharaan prediktif baru. Manfaat inframerah sebagai alat PdM sejauh ini paling bermanfaat dari sudut pandang keuangan untuk fasilitas manufaktur di seluruh dunia. Gambar 6 adalah contoh aplikasi tegangan rendah. Inframerah tidak memiliki batasan dalam mendeteksi perubahan suhu yang sangat kecil.
Gambar 8 mewakili data yang diambil pada saluran listrik tegangan tinggi. Kegagalan pada aplikasi ini akan mematikan seluruh pabrik, yang menelan biaya jutaan dolar. Untungnya, itu ditangkap oleh teknisi inframerah pada rute inspeksi bulanan yang dijadwalkan.
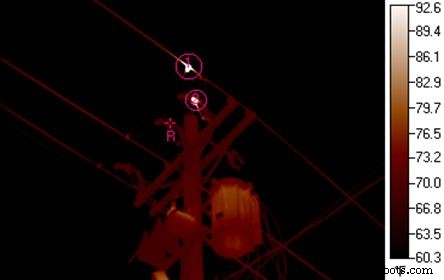
Gambar 8. Data Inframerah dari Koneksi Lepas
Suhu pada soket saluran tercatat pada 160,2 derajat Fahrenheit, lebih dari dua kali suhu sekitar.
Seperti yang Anda lihat dari studi kasus pemeliharaan prediktif dari data yang dianalisis, termografi inframerah adalah alat yang efektif untuk memprediksi dan mencegah kegagalan dini. Ketika digunakan secara maksimal dan dikombinasikan dengan teknologi PdM lainnya, termografi inframerah adalah teknologi yang sangat bermanfaat untuk proses perawatan dasar kondisi.
Analisis Minyak
Dalam Gambar 9 di bawah ini, tingkat kontaminan ISO adalah 22/21/17. Ini jauh melebihi standar yang ditetapkan untuk semua peralatan operasi di sebagian besar aplikasi industri.
Untuk setiap peningkatan numerik tingkat kontaminan ISO, jumlah kontaminan dalam oli berlipat ganda. Jika standarnya adalah 16/14/11, maka peningkatan kontaminan dalam oli untuk 22/21/17 adalah 64 kali lebih kotor dari standar.
Analisis oli adalah alat perawatan prediktif yang andal dan sangat efektif dalam mendeteksi kontaminan dalam oli yang diakibatkan oleh kotoran yang masuk atau serpihan keausan internal yang dihasilkan oleh efek degradasi dan keausan mesin. Peningkatan kadar kontaminan mempercepat proses keausan semua komponen dalam aplikasi mesin industri.
Kontaminan dalam minyak dapat dicegah. Filtrasi yang baik di sisi belakang unit daya hidraulik akan membantu menghilangkan kotoran dan partikel masuk lainnya. Biasanya filtrasi 3 mikron dengan rasio 200 beta adalah standar yang ditetapkan untuk sebagian besar mesin.
Menghilangkan kebocoran dan memastikan bahwa oli bersih digunakan untuk mengisi ulang oli yang mungkin perlu diganti adalah praktik terbaik lainnya yang dapat membantu menjaga kebersihan oli.
Gambar 9. Data Analisis Minyak
Studi Kasus Analisis Arus Motor
Analisis arus motor adalah alat PdM lain yang telah membayar dividen besar untuk proses manufaktur di seluruh dunia. Memprediksi kerusakan insulasi dini pada belitan motor listrik memungkinkan teknisi untuk mendiagnosis masalah kelistrikan sebelum kegagalan besar.
Jika Anda menggabungkan analisis arus motor dengan analisis inframerah atau getaran, Anda dapat mendeteksi kegagalan listrik dan mekanis motor listrik, yang secara drastis mengurangi risiko waktu henti yang tidak terjadwal. Dengan menerapkan analisis akar penyebab kegagalan, seseorang kemudian dapat meningkatkan keandalan mesin dalam proses pabrik.
Pada Gambar 9, data yang diberikan mewakili motor kipas resirkulasi pelembab udara tempat analis melakukan analisis data rutin bulanan.
Nama Tes
Standar AC
Nama Motor
1677
ID Aset
T/A
ID Sirkuit
T/A
Kondisi Motor
Bagus
Tanggal Tes
07/09/2005
27/07/2006
Waktu Tes
10:23:15
07/09/2005
Frekuensi
1200
1200
Mohm Ph 1 ke Gnd
Waktu Pengisian Daya
30
30
Tegangan
500
500
Suhu Motor
32
32
Mohm Terukur
1700.0
303.0
Mohm dikoreksi
980.0
174.0
pF Ph 1 ke Gnd
16250
16500
ohm Ph 1 sampai 2
0.86900
0.88250
ohm Ph 1 sampai 3
0,87000
0.88250
ohm Ph 2 sampai 3
0.80650
0.80450
mH Ph 1 hingga 2
22.940
23.110
mH Ph 1 hingga 3
21.450
23.730
mH Ph 2 hingga 3
21.740
21.950
Rta. Induktansi
22,043
22.930
% Res. Ketidakseimbangan
4,95
6.07
% Ketidakseimbangan Ind.
4.07
4.27
$ Kehilangan Daya
21,85
26,84
Lokasi Pengujian
T-Leads
T-Leads
MCE #
030535
030535
Pengguna
Catatan
Tidak
Tidak
Gambar 10. Data yang Diambil oleh Penulis
Data yang diberikan di atas menunjukkan perbandingan dari dua bacaan; satu adalah baseline yang diambil pada 7 September 2005, dan yang lainnya diambil pada 27 Juli 2006, menunjukkan kerusakan pada isolasi mulai terjadi. Perhatikan peningkatan persentase ketidakseimbangan resistensi. Ini adalah penyebab alarm, dan tindakan harus diambil untuk menjadwalkan motor dikeluarkan dari servis dan dikirim untuk direkondisi. Ini hanyalah salah satu contoh manfaat analisis arus motor di arena PdM.
Kontribusi lain, seperti analisis getaran, adalah kemampuan untuk mendeteksi anomali celah udara. Jika tidak dicentang, masalah celah udara antara rotor dan stator dapat menyebabkan gesekan rotor dan stator yang dapat menyebabkan kegagalan fatal pada motor. Ini dapat terjadi bahkan jika semua indikasi lain menunjukkan bahwa ada rotor dan stator yang sehat. Celah udara sebagai zona gangguan menggambarkan jarak terukur antara rotor dan stator di dalam motor.
Manfaat teknologi prediktif terlihat jelas dalam setiap contoh data yang disediakan dalam artikel ini. Tidak masalah jika departemen pemeliharaan memulai dengan analisis getaran, termografi inframerah, analisis oli, atau analisis arus motor. Masing-masing akan memberikan keuntungan moneter ke garis bawah jika dilaksanakan dengan komitmen dan personel yang terlatih.
Data yang diberikan menggambarkan bagaimana analisis getaran dapat mendeteksi cacat penyambungan roda gigi pada unit transmisi daya, cacat bantalan pada peralatan yang berputar, kondisi ketidakseimbangan pada kipas, dan pendeteksian frekuensi alami struktur yang mendukung peralatan berputar. Setiap masalah yang diwakili dan didiagnosis telah terbukti menghemat ribuan dolar dalam biaya perbaikan dan waktu henti.
Data yang disediakan oleh pencitraan termal menunjukkan bagaimana perubahan kecil dalam suhu dapat dideteksi, memungkinkan analis untuk mengatasi masalah yang akan memastikan kegagalan besar.
Data analisis oli yang disediakan telah menunjukkan untuk mengidentifikasi kontaminan dalam oli yang dapat menyebabkan suku cadang aus sebelum waktunya dan mengurangi masa pakai peralatan. Mengidentifikasi partikel keausan dalam oli mesin dapat mendeteksi masalah bantalan dan masalah roda gigi yang jika tidak demikian dapat tidak terdeteksi.
Analisis arus motor memberi analis kemampuan untuk mendiagnosis kerusakan isolasi dan memprediksi kegagalan yang tidak dapat dideteksi dengan peralatan prediksi lainnya.
Jika departemen pemeliharaan mampu menggunakan dua atau lebih dari teknologi ini, keandalan proses meningkat secara drastis. Analisis data yang tumpang tindih dengan menggabungkan teknologi ini akan membantu dalam membangun program pemeliharaan prediktif yang efektif.
Gary Fore, CMRP
Spesialis Keandalan I &E
Eagle Rock Energy
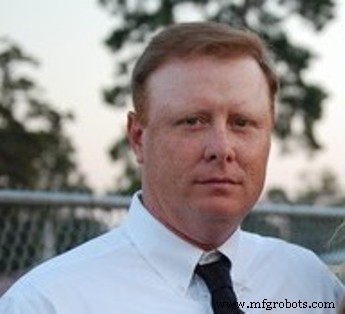
Tentang penulis:
Gary Fore, CMRP, adalah spesialis keandalan I&E di Eagle Rock Energy. Dia telah menghabiskan 22 tahun di industri energi dan produk bangunan, yang mengkhususkan diri dalam rekayasa keandalan dengan penekanan berat pada pemantauan kondisi. Dia memiliki gelar sarjana sains di bidang teknik mesin dan gelar associate sains terapan dalam teknologi elektro-mekanik. Sertifikasinya meliputi:Certified Maintenance and Reliability Professional (melalui Society for Maintenance and Reliability Professionals), analis getaran Kategori III (Vibration Institute), termografer inframerah Level II, Spesialis Pelumasan Bersertifikat, dan Analis Pelumas Mesin Level I (Dewan Internasional untuk Pelumasan Mesin). ).