Sejarah Pemeliharaan Prediktif | Senseye
“Anda tidak dapat memperbaiki sesuatu yang tidak rusak” dulunya adalah filosofi Pemeliharaan Reaktif tradisional, bertahun-tahun yang lalu. Bantuan hanya dipanggil sekali mesin benar-benar gagal.
Menyelesaikan laporan, mencari atau memesan suku cadang pengganti dan merakit keahlian perawatan yang dibutuhkan, sering kali menimbulkan penundaan dan waktu henti yang tidak perlu, serta biaya lembur.
Lead time dan, akibatnya, jadwal pengiriman keluar dari jendela.
Merencanakan kegagalan
Pemikiran diperbarui pada 1980-an, dengan popularitas teknik manufaktur Jepang termasuk Just in Time (JIT), di mana ide barunya adalah melakukan Pemeliharaan Pencegahan Terjadwal, atau Terrencana. Konsep ini disempurnakan lebih lanjut dengan diperkenalkannya Total Productive Maintenance, yang digunakan dalam Lean Manufacturing, di mana pemeliharaan direncanakan untuk menjaga peralatan dalam keadaan bekerja setiap saat.
Implementasi yang berhasil berarti lebih sedikit kerusakan dan mengurangi waktu henti, menghasilkan penggunaan tenaga kerja yang lebih efektif, masa pakai alat berat yang lebih lama, dan keselamatan tempat kerja yang lebih baik.
Manfaat nyata ini meningkatkan produktivitas secara keseluruhan – tetapi perencanaan pemeliharaan melibatkan asimilasi informasi dari produsen peralatan, insinyur dan operator berpengalaman, dalam jangka waktu yang lama.
Unduh sumber daya gratis kami untuk mempelajari peran tim TI Anda agar dapat memberikan nilai dan praktik terbaik untuk pengumpulan dan transfer data." align="middle">
Bagaimana orang bisa yakin bahwa pemeliharaan dijadwalkan pada waktu yang optimal?
Memprediksi Kegagalan
Optimalisasi waktu perawatan telah dicapai melalui Predictive Maintenance, dengan diperkenalkannya Condition Monitoring.
Dengan metodologi ini, data dari indikator kritis tertentu digunakan untuk menunjukkan ketika peralatan menunjukkan penurunan kinerja, atau karena gagal. Ini berfungsi sebagai sistem peringatan dini, memberikan waktu untuk merencanakan kontinjensi, mengurangi kerugian karena penundaan pemeliharaan.
Keberhasilan Pemantauan Kondisi tergantung pada perolehan informasi yang berkualitas dan relevan dari komponen-komponen penting ini dalam waktu yang tepat, menganalisis dan mengevaluasinya dengan cepat, sebelum bertindak cepat untuk mengimplementasikan temuan.
Di pabrik tradisional, informasi terbatas tersedia dari sistem kontrol industri, seringkali membutuhkan pemrosesan dan formulasi lebih lanjut ke dalam laporan sebelum para ahli dapat menginterpretasikan hasilnya.
Sekarang di Ujung Jari Anda
Dengan hadirnya Industri 4.0 dan Pabrik Cerdas, setiap kemungkinan data yang diperlukan untuk mengotomatisasi analisis kondisi peralatan dapat tersedia. Digitalisasi berarti bahwa data waktu nyata dapat dikumpulkan dari berbagai sumber di seluruh lantai pabrik dan disimpan dengan cara yang mudah diakses.
Hal ini memungkinkan analitik tingkat lanjut untuk diterapkan, dengan cepat dan mudah, memberikan penilaian situasi yang hampir instan dan menyoroti anomali apa pun. Pemrosesan di cloud membuat informasi ini tersedia di seluruh organisasi, memungkinkan mereka mengumpulkan praktik terbaik dan merespons dengan cepat.
Kemampuan untuk mendiagnosis kegagalan secara otomatis semakin diperluas dengan penambahan Prognostik. Data yang dikumpulkan dari mesin dan aset membangun model operasi yang, ketika dianalisis, memberikan indikasi awal kapan mesin akan gagal, mengidentifikasi Sisa Masa Pakainya (RUL).
Antisipasi kebutuhan pemeliharaan ini memungkinkan operasi yang lebih gesit, dengan cakrawala waktu yang dipahami dengan baik, memungkinkan pengambilan keputusan dan tindakan yang akan diambil yang akan mencegah atau membatasi kerugian karena waktu henti yang tidak direncanakan.
Ceritakan lebih banyak
Senseye mengotomatiskan teknik pemantauan dan prognostik kondisi terbaru dan menampilkan berbagai hal dengan cara yang sangat sederhana untuk membantu Anda menghindari waktu henti yang tidak direncanakan.
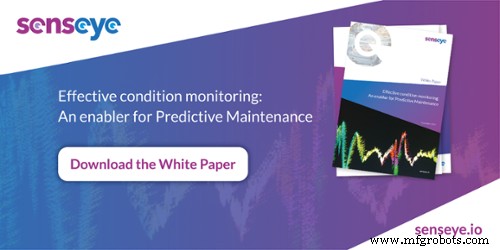