Gulungan filamen 3D memungkinkan konsep tempat duduk kendaraan
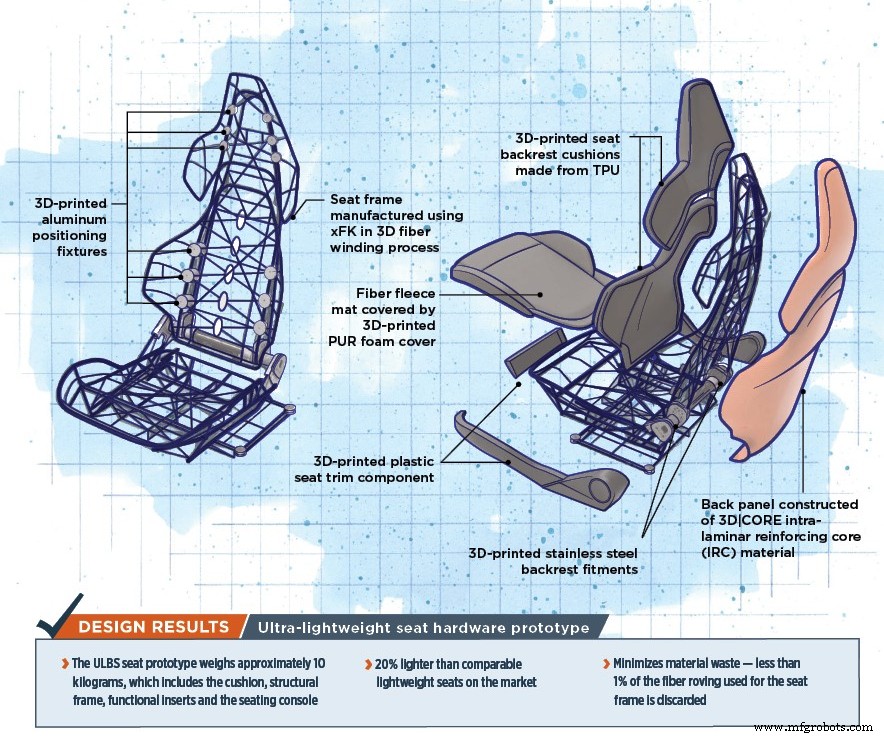
Keberlanjutan dan tanggung jawab lingkungan menjadi pendorong tren teknologi yang semakin lazim di industri otomotif. Kendaraan berenergi rendah dan rendah emisi telah menjadi prioritas bagi sektor otomotif internasional, dan tren menuju teknologi transportasi alternatif seperti elektromobilitas dan mobilitas udara perkotaan (UAM) mendapatkan momentum. OEM mencari bahan dan proses yang muncul sebagai penggerak untuk moda perjalanan prospektif ini, tetapi perubahan di sektor otomotif sering kali berjalan lambat. Agar bahan dan proses baru dapat diadopsi sepenuhnya, bahan dan proses tersebut tidak hanya harus memenuhi syarat, tetapi juga harus hemat biaya dan harus memungkinkan produksi volume tinggi.
Kursi yang sangat ringan. Konsep tempat duduk Ultra Leichtbausitz (ULBS) dikembangkan melalui kolaborasi antara beberapa perusahaan menggunakan kombinasi teknologi. Sumber | csi entwicklungstechnik
Baru-baru ini, sebuah proyek inovatif dengan potensi sektor otomotif — serta pasar negara berkembang seperti hypercars dan taksi udara — menunjukkan bagaimana bahan, proses, dan teknologi baru, serta kolaborasi erat antar perusahaan, dapat memungkinkan moda transportasi generasi mendatang. Tujuan proyek ini adalah untuk sepenuhnya memikirkan kembali kursi mobil menggunakan teknologi generatif mutakhir, dan melakukannya hanya dengan menggunakan bahan yang tepat sebanyak yang diperlukan di tempat yang tepat — dan untuk menghasilkan hasil dengan cepat. Prototipe kursi kendaraan hibrida logam-komposit ultra-ringan yang dihasilkan dikembangkan, mulai dari desain hingga manufaktur, hanya dalam tujuh bulan, melalui pendekatan desain yang digerakkan oleh simulasi, metode manajemen proyek yang gesit, dan kerja sama yang erat serta integrasi sistem antara perusahaan yang terlibat.
Membuat tempat duduk yang lebih baik
Studi kelayakan kursi ultra-ringan Ultraleichtbausitz (ULBS) dikembangkan melalui kolaborasi antara beberapa perusahaan menggunakan kombinasi teknologi. Visi proyek ini, dalam kata-kata grup, "untuk menciptakan konsep tempat duduk yang sangat ringan, yang luar biasa di pasar dalam hal pengoptimalan bobotnya." Perusahaan pemrakarsa csi entwicklungstechnik GmbH (csi, Neckarsulm, Jerman), Alba Tooling &Engineering (Forstau, Austria) dan Konsultasi Manajemen Otomotif (AMC, Penzberg, Jerman) mengembangkan konsep tempat duduk prototipe bekerja sama dengan Covestro (Leverkusen, Jerman), LBK Fertigung (Friedberg, Jerman), Robert Hofmann (Lichtenfels, Jerman) dan 3D|CORE (Herford, Jerman).
Proyek kolaboratif menghasilkan prototipe kursi dengan berat sedikit di atas 10 kilogram, yang mencakup bantalan, rangka struktural, sisipan fungsional, dan konsol tempat duduk yang memungkinkannya dipasang ke kendaraan. Kursinya 20% lebih ringan dari kursi ringan yang sebanding di pasaran, banyak di antaranya adalah kursi aftermarket. Menurut pemimpin proyek ULBS Stefan Herrmann, yang bertanggung jawab untuk desain ringan di CSI, saat ini tidak ada kursi pesaing di pasar yang beratnya kurang dari 12 kilogram.
“Namun, perbandingan langsung seringkali bukan apple-to-apples, karena kursi aftermarket sering kali tidak menyertakan konsol tempat duduk dalam definisi beratnya,” kata Herrmann, “Juga kenyamanan tempat duduk ULBS jauh lebih tinggi dibandingkan dengan kursi dengan berat yang serupa. Kursi yang ada sering kali merupakan kursi bucket, yang bobotnya bahkan lebih rendah tetapi tidak senyaman itu, atau kursi supersports tradisional, yang bobotnya jauh lebih tinggi.”
ULBS menampilkan beberapa teknologi inovatif, di antaranya struktur kerangka keliling serat berdasarkan teknologi proses xFK dalam 3D memainkan peran yang paling menonjol. (Lihat “Filament winding, reinvented” untuk informasi lebih lanjut tentang xFK dalam 3D dan teknologi penggulungan filamen lainnya.) Pentingnya mendasar dari teknologi pemenang penghargaan untuk deposisi roving serat tak berujung terletak pada kebebasan desainnya, dalam simulasi-driven dan material- penempatan serat yang dioptimalkan tepat pada arah beban serta dalam aplikasi bahan serat yang sederhana, hemat biaya, dan bebas limbah. Untuk transfer beban dalam struktur kerangka ini, bagian cetak 3D telah digunakan. Di area dengan beban tertinggi, seperti perlengkapan sandaran, kursi menggunakan struktur cetak 3D yang terbuat dari baja tahan karat dengan kekuatan tinggi dan modulus tinggi. Di area dengan beban lebih sedikit, pencetakan 3D aluminium digunakan.
csi entwicklungstechnik, sebuah perusahaan teknik yang mengkhususkan diri dalam struktur body-in-white (BIW) kendaraan, serta interior dan eksterior otomotif dengan area bisnis termasuk polimer yang diperkuat serat karbon (CFRP) dan manufaktur aditif, mengawasi dan mengoordinasikan proyek berdasarkan ide yang digagas oleh AMC. csi menyediakan gaya, permukaan, konsep, simulasi, teknik desain, dan manajemen proyek untuk proyek tersebut.
Herrmann menjelaskan:“csi bertanggung jawab atas paket kerja dalam domain rantai proses digital — penataan gaya, desain teknik, desain permukaan, simulasi CAE, simulasi topologi, simulasi validasi, dan konfirmasi virtual proyek.”
Dia menekankan bahwa apa yang membuat proyek ULBS penting bukan hanya penggunaan bahan inovatif dan metode manufaktur, tetapi pengembangan bagian kompleks yang terdiri dari desain komponen baru dalam jangka waktu tujuh bulan yang singkat menggunakan kolaborasi erat di antara para mitra.
Rangka dudukan luka filamen. Sebagian besar pengurangan berat dalam proyek ULBS dihasilkan dari teknologi proses penggulungan serat AMC xFK dalam 3D. Sumber | csi entwicklungstechnik
Menggulung bingkai
Sebagian besar pengurangan bobot dalam proyek ULBS dihasilkan dari xFK AMC dalam 3D, teknologi komposit serat yang sangat fleksibel, dapat dikonfigurasi, hemat biaya, dan berkelanjutan untuk komponen penggulungan..
xFK dalam 3D telah digunakan untuk berbagai produk dan aplikasi untuk berbagai industri dan segmen pasar. SGL Group Wiesbaden, Jerman) menampilkan beberapa suku cadang otomotif dan sepeda yang diproduksi melalui teknologi ini di pameran komposit internasional JEC World 2018. Salah satu suku cadang yang dipamerkan, cincin rantai sepeda serat karbon yang dikembangkan oleh AMC, dikatakan mampu memangkas bobot hingga 70% dibandingkan dengan versi aluminium.
Bushing berliku. Keliling serat termoset yang diresapi resin dililitkan di sekitar perlengkapan pemosisian, memungkinkan serat diatur agar sesuai dengan beban setiap bagian dan fungsi yang diinginkan. Sumber | csi entwicklungstechnik
xFK dalam proses 3D memutar struktur penahan beban dengan cara yang bebas limbah menggunakan serat kontinu termoset yang diresapi resin. Keliling serat yang jenuh dengan resin epoksi dililitkan di sekitar perlengkapan pemosisian, atau busing belitan, sehingga serat dapat diatur secara khusus agar sesuai dengan beban setiap bagian dan fungsi yang diinginkan.
“Salah satu manfaat utama xFK dalam 3D adalah menghilangkan titik lemah terkait transfer beban dan pengenalan beban dalam struktur,” kata Herrmann. Dia menjelaskan bahwa titik lemah sering kali tidak berada dalam kontinum struktur, tetapi di area di mana beban dimasukkan ke dalam struktur, terutama di mana komponen tetangga terhubung ke struktur. Teknologi xFK dalam 3D memungkinkan transfer beban di seluruh koneksi dan memungkinkan serat disejajarkan sesuai dengan fungsi komponen dan kasus beban yang diinginkan, dan diproduksi dalam tiga dimensi.
Proses penggulungan filamen juga menghasilkan manfaat tambahan. Proses ini membantu meminimalkan limbah material — kurang dari 1% serat keliling yang terbuang.
csi mengenali xFK dalam kekuatan 3D dan merancang rangka kursi ULBS untuk dibangun di bawah konsultasi Dr. Clause Georg Bayreuther, kepala teknologi AMC.
“Bekerja dengan insinyur csi, konsultan AMC, dan ahli perkakas Alba mengembangkan konsep dan struktur rangka kursi ini untuk diproduksi menggunakan xFK dalam proses 3D,” kata Peter Fassbaender, konsultan teknologi dan penggagas xFK dalam teknologi 3D.
Alba memproduksi perkakas untuk rangka kursi CFRP dan menyediakan dukungan teknis. Selain itu, meskipun rangka kursi dililit dari serat karbon, serat alami atau serat basal juga merupakan kandidat yang baik.
Teknologi baru. Prototipe ULBS menggunakan kombinasi teknologi baru termasuk cangkang panel belakang yang terbuat dari bahan inti penguat intralaminar (IRC), dan bantal sandaran kursi cetak 3D yang terbuat dari poliuretan termoplastik (TPU). Sumber | csi entwicklungstechnik
Struktur material hybrid
Selain rangka, prototipe ULBS menyertakan beberapa inovasi baru lainnya. Alba, yang memasok perkakas, juga memasok perkakas, teknik, dan manufaktur untuk badan busa kursi dan menjalankan perakitan kursi. Sebuah tikar bulu serat menutupi bingkai CFRP kursi yang kemudian ditutupi oleh penutup busa PUR yang dicetak 3D. Area bantalan kursi terbuat dari busa tradisional.
Pengurangan berat lebih lanjut dicapai melalui penggunaan 3D|CORE, bahan inti penguat intralaminar (IRC), di struktur cangkang panel belakang sandaran kursi. Bahannya adalah bahan inti penguat intra-laminar (IRC) — inti sandwich struktural yang terdiri dari badan inti busa polystyrene (XPS) dan polyethylene terephthalate (PET) yang diekstrusi dalam pola sarang lebah terintegrasi. Selama produksi komponen komposit, struktur sarang lebah diisi dengan resin, menghasilkan kekuatan intra-laminar yang tinggi. 3D|Core dirakit di antara dua lapisan serat kaca untuk membuat bentuk awal, yang diresapi dengan resin epoksi termoplastik menggunakan cetakan transfer resin bantuan vakum (VA-RTM).
Covestro menyediakan perekat Dispercoll sebagai pengikat untuk alas bulu domba serat, serta bantalan sandaran yang dicetak 3D. Menurut Herrmann, sifat mekanik Dispercoll memberikan ketahanan abrasi yang baik, yang penting karena kontak permukaan antara bantalan dan bingkai dapat membuat bulu domba aus seiring waktu.
“Jika Anda memiliki roving serat tunggal, ketika Anda memasukkannya ke dalam tekstil, Anda mendapatkan gerakan mikro antara bagian CFRP yang keras dan alas bulu domba. Komponen rangka tempat duduk dapat bergesekan dengan tekstil dan merusaknya,” jelas Herrmann.
Kursi tradisional biasanya memiliki area permukaan yang lebih besar yang menopang bantalan, dan tidak memiliki masalah ini. Namun, dengan xFK dalam 3D, ada area permukaan kontak yang lebih kecil karena struktur rangka.
“Saat xFK dalam struktur 3D mendorong kain bulu domba, Anda harus memiliki pengikat yang spesifik dan tahan lama; inilah yang disediakan Dispercoll dalam konteks ini,” tambah Herrmann.
Covestro juga memasok apa yang dikatakan sebagai bantal cetak 3D pertama di dunia. Sementara busa intensif konvensional dan perkakas biasanya digunakan di sandaran kursi, penggunaan bantal sandaran kursi cetak 3D, yang terbuat dari TPU (poliuretan termoplastik), semakin meningkatkan fleksibilitas dan kemampuan beradaptasi kursi ULBS sehubungan dengan estetikanya, pilihan dan kenyamanan integrasi fungsional.
Kursi untuk masa depan
Proyek ULBS mencapai beberapa tujuan. Konsep yang dihasilkan, meskipun belum dipasarkan, memiliki potensi untuk melayani banyak pasar khusus seperti hypercar, taksi udara, kendaraan ultra-ringan, mikromobilitas, helikopter, multicopter dan penerbangan. Meskipun diakui lebih mahal daripada kursi mobil produksi, ULBS menunjukkan beberapa teknologi yang meminimalkan limbah, sehingga menurunkan biaya material. Dibandingkan dengan teknologi serat karbon lainnya, xFK dalam 3D menghasilkan jumlah limbah yang sangat rendah. Faktanya, seluruh proyek ditujukan untuk menggunakan sumber daya minimal dan hanya bahan minimum yang diperlukan. ULBS juga menawarkan kemungkinan penggunaan sumber daya terbarukan dan berkelanjutan seperti serat alami dalam struktur rangka, bantalan, dan tekstil.
Namun yang lebih penting, proyek ini menunjukkan bagaimana perusahaan dapat meminimalkan waktu ke pasar dengan bekerja sama melalui prosedur koordinasi yang singkat dan gesit. Ini juga merupakan contoh yang baik dalam menggunakan pemikiran desain untuk berhasil membawa produk dari ide ke prototipe perangkat keras dengan berfokus pada persyaratan fungsional dan melihat ke depan untuk aplikasi masa depan dan tujuan keberlanjutan.