Prepreg baru untuk pencetakan kompresi di RAPM
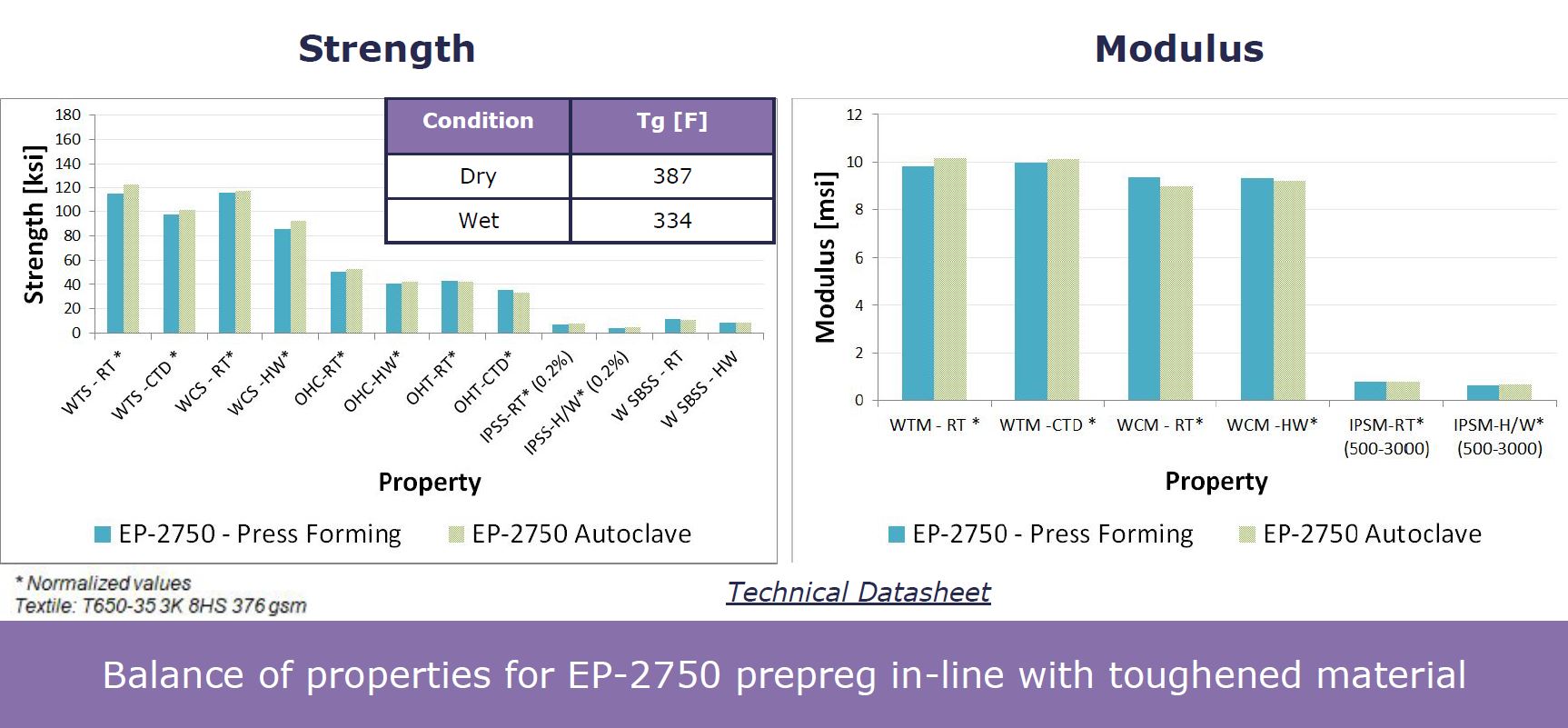
Prepreg serat karbon/epoksi telah menjadi bahan dasar untuk komposit kedirgantaraan selama beberapa dekade karena memberikan sifat mekanik yang tinggi dan kandungan resin/serat yang presisi, serta kemudahan penanganan untuk layup dan perawatan autoklaf. Namun, karena produsen pesawat terbang dan mobilitas udara perkotaan (UAM) mengeksplorasi tingkat produksi yang lebih tinggi dan biaya yang lebih rendah, pencetakan kompresi menjadi menarik, memangkas waktu siklus dan meningkatkan efisiensi dibandingkan autoklaf. Paling sederhana, cetakan kompresi terdiri dari pemanasan awal bahan cetakan, menempatkannya ke dalam rongga pahat terbuka dan konsolidasi dengan tekanan hidrolik pada suhu, di mana bahan termoset cair diubah menjadi padat. Bagian yang diawetkan kemudian dikeluarkan untuk setiap langkah pemangkasan dan penyelesaian yang diperlukan.
Menggabungkan press moulding dan prepreg tidak hanya memberikan proses yang efisien dan berkecepatan tinggi dengan kinerja dan penanganan prepreg yang mudah, tetapi juga menghindari beberapa dinamika proses yang kompleks dalam pengisian bala bantuan kering dengan resin cair selama proses seperti infus resin dan pencetakan transfer resin (RTM). Khususnya untuk aerostruktur yang lebih kecil, prepreg press moulding menawarkan potensi waktu takt <30 menit sambil tetap mencapai bagian geometri kompleks berkualitas tinggi.
Solvay Composite Materials (Alpharetta, Ga., A.S.) adalah mitra utama dalam program RApid High-Performance Manufacturing (RAPM) yang dipimpin oleh The Boeing Co. (Chicago, Ill., U.S.). RAPM adalah bagian "pembentukan" dari program The Tailorable Feedstock and Forming (TFF) yang diluncurkan oleh Defense Advanced Research Projects Agency (DARPA, Arlington, Va., US) pada tahun 2015. Tujuannya adalah untuk memungkinkan cepat, berbiaya rendah, dan gesit pembuatan komponen komposit kecil berbentuk kompleks dan meningkatkan kemampuan komposit untuk bersaing dengan aluminium mesin dalam aplikasi pertahanan.
Sebagai pemasok lama bagi Boeing untuk aplikasi pertahanan, Solvay juga telah menjadi pemimpin dalam solusi baru untuk kedirgantaraan komersial, seperti prepreg epoksi out-of-autoclave (OOA) CYCOM 5320-1, dan juga untuk otomotif, seperti waktu takt 1 menit, prepreg vinyl hybrid SolvaLite 730.
RAPM adalah kesempatan sempurna bagi Solvay untuk menguji dan menyempurnakan sistem eksperimentalnya XEP-2750, yang sekarang dikomersialkan sebagai CYCOM EP2750, yang dikembangkan untuk menjembatani produksi komposit dirgantara dan otomotif. Blog ini — bilah sisi online untuk fitur Mei 2020 “Merevolusi paradigma biaya komposit, Bagian 2:Pembentukan” — mengulas pengembangan tersebut serta proses pencetakan kompresi yang digunakan dan apa yang ditawarkan CYCOM EP2750 kepada produsen komposit dirgantara dan otomotif.
Referensi untuk blog ini antara lain:
- “Fabrikasi Spring Frame Press dari Komponen Produksi Aerospace” oleh Timothy J. Luchini
1
, Alejandro J. Rodriguez
2
, Scott A. Rogers
2
, Aurele Bras
3
, Adam Whysall
3
, Richard Russell
3
, Scott Lucas
2
, Gail L. Hahn
1
. Prosiding Konferensi SAMPE. Charlotte, NC, 20-23 Mei 2019.
- “Tantangan Geometri Bagian Struktural Dirgantara untuk Cetakan Kompresi Tingkat Tinggi” oleh Aurele Bras
1
, Alejandro J. Rodriguez
2
, Richard Russell
1
, Timothy J. Luchini
3
, Travis Adams
3
, Adam Whysall
1
, Scott A. Rogers
2
, Scott Lucas
2
, Gail L. Hahn
3
. Masyarakat untuk Kemajuan Material dan Rekayasa Proses – Amerika Utara.Prosiding Konferensi SAMPE. Seattle, WA, 4-7 Mei 2020. Masyarakat untuk Kemajuan Teknik Material dan Proses – Amerika Utara.
- “Pembentukan Cepat Kinerja Tinggi dari Prepreg xEP-2750 Struktural untuk Pencetakan Kompresi” oleh Timothy J. Luchini
1
, Alejandro J. Rodriguez
2
, Scott A. Rogers
2
, Bra Aurele
2
, Adam Whysall
2
, Richard Russell
2
, Scott Lucas
2
, Gail L. Hahn
1
. SAMPE 2019.
1
Perusahaan Boeing, Saint Louis, MO 63134,
2
Bahan Komposit Solvay, Anaheim, California, AS dan
3
Bahan Komposit Solvay, Heanor, Inggris
- Webinar CompositesWorld:“Proses Otomotif untuk Manufaktur Komposit Aerospace Tingkat Tinggi” oleh Alejandro Rodriguez, Solvay Composite Materials, Anaheim, California, AS
Target bahan dan proses
CYCOM EP2750 dikembangkan untuk memenuhi target kinerja yang ditetapkan oleh Boeing untuk epoksi yang diperkeras kedirgantaraan, menunjukkan keseimbangan suhu transisi kaca (Tg) hingga 350 °F, sifat berlekuk yang baik — misalnya kompresi lubang terbuka (OHC) dan tegangan lubang terbuka (OHT) — dan ketahanan pelarut. Kelas prepreg baru ini berlaku untuk aerostruktur primer dan sekunder dan kompatibel dengan berbagai penguat (misalnya, serat karbon dan kaca).
CYCOM EP2750 juga dikembangkan dengan kemampuan untuk meningkatkan produksi menggunakan penanganan otomatis dan pencetakan kompresi. Ini termasuk waktu penyembuhan pada alat 15-30 menit pada 330-370 °F, dengan 1 jam pasca-penyembuhan pada 350 °F. Waktu takt 30 menit atau kurang ini memungkinkan volume produksi tahunan 10.000 suku cadang per alat.
Solvay menggunakan dua variasi cetakan kompresi selama program RAPM:cetakan bingkai pegas dan pembentukan diafragma ganda (DDF). Keduanya menggunakan prinsip memegang blanko datar dan membawanya melalui tahap pemanasan awal inframerah (IR) sebelum memasukkannya ke dalam rongga alat logam yang cocok. Pers kemudian menutup cetakan baja mengikuti program otomatis dan menerapkan tekanan penuh ke prepreg untuk sisa waktu pada alat.
Baik cetakan rangka pegas dan DDF menggunakan alat logam yang cocok dan menawarkan pendekatan panas-masuk, panas-keluar, menghilangkan panas dan dingin alat, untuk produksi tingkat tinggi. Keduanya digunakan untuk berhasil mencetak beberapa jenis bagian geometri kompleks dengan pad-up, flensa vertikal, dan variasi ketebalan dari 3,8 hingga 8,9 milimeter. Suku cadang ini dibuat di Pusat Aplikasi Solvay di Heanor, Inggris Meskipun tidak tersedia selama RAPM, Heanor sekarang memiliki fitur jalur pencetakan kompresi otomatis dari gulungan prepreg ke bagian cetakan, mencapai waktu takt 15 hingga 60 menit untuk suku cadang ruang angkasa yang dibuat dengan EP2750 dan takt kali 3 menit atau kurang untuk bagian kecil hingga menengah menggunakan prepreg otomotif. Solvay melihat banyak manfaat dalam proses DDF termasuk:
- Penghapusan langkah preforming – blanko 2D menjadi bagian 3D
- Tidak diperlukan pelepasan atau pembersihan jamur
- Pengurangan bahan tambahan (mis., breather, bleeder, bagging, tape) vs. autoclave
- Peningkatan buy-to-fly vs. cetakan rangka pegas karena lebih sedikit bahan berlebih yang dibutuhkan untuk memasang klem pegas.
Impregnasi penuh vs. sebagian mempertahankan tekanan
Karakteristik EP2750 yang memfasilitasi pencetakan kompresi mencakup tack rendah untuk penanganan pengambilan dan penempatan otomatis dan sifatnya yang sepenuhnya diresapi versus CYCOM 5320-1, yang sebagian diresapi untuk memfasilitasi pernapasan tepi, yang diperlukan untuk laminasi bebas-kosong menggunakan pemrosesan OOA. Namun, pencetakan kompresi memanfaatkan aliran resin paksa yang sangat cepat karena tekanan yang lebih tinggi yang diterapkan — misalnya, hingga 350 psi (maksimum tipikal untuk EP2750) dibandingkan dengan 35 psi yang umum dalam pemrosesan autoklaf dan 14,7 psi dalam pemrosesan OOA khusus vakum.
Memiliki prepreg yang lebih sepenuhnya diresapi, meskipun kandungan resin hanya sedikit lebih tinggi — 40% di CYCOM EP2750 dibandingkan dengan 36% di CYCOM 5320-1 — mempertahankan tekanan hidrostatik selama pemadatan dan pengawetan di rongga alat logam yang cocok, sehingga mengurangi risiko area kering, curing part thickness (CPT) yang tidak konsisten, kerutan, dan cacat lainnya sambil memastikan kualitas permukaan yang baik.
Khususnya, Solvay mengembangkan Film Transformer yang dipatenkan untuk meningkatkan tekanan hidrostatik saat menggunakan kandungan resin yang lebih rendah CYCOM 5320-1 prepreg. Diterapkan pada tata letak bagian sebelum pencetakan kompresi, Film Transformer meningkatkan kandungan resin dan membantu memenuhi persyaratan CPT dalam uji coba pencetakan bagian RAPM.
Uji coba pencetakan suku cadang RAPM
Seperti yang dijelaskan dalam artikel fitur CW Mei 2020, CYCOM EP2750 adalah salah satu bahan utama yang diuji coba di trek prepreg termoset RAPM. Bagian-bagian Pathfinder yang diujicobakan dalam fase Manufaktur &Pengembangan awal disertakan
Panel akses manik-manik TS-RAPM-001 dan -009, rusuk TS-RAPM-002 dan saluran C melengkung TS-RAPM-003. Suku cadang dirancang di Boeing (beberapa lokasi secara global), perkakas dibuat di C-Con GmbH (Munich, Jerman), suku cadang diproduksi di Pusat Aplikasi Solvay di Heanor, Inggris dan kemudian diuji di Solvay Anaheim, California, AS dan Boeing St. Louis, Mo., AS
Kualitas permukaan dievaluasi menggunakan inspeksi non-destruktif (NDI) dan panel yang dipilih dipotong melintang untuk porositas, geser balok pendek, fraksi volume serat, kandungan resin, derajat pengerasan, dan suhu transisi gelas.
Tingkat porositas di bawah 0,5% dengan mudah dicapai, dikaitkan dengan tekanan konsolidasi yang tinggi dari cetakan kompresi. Meskipun parameter proses harus dioptimalkan untuk setiap bagian yang berbeda, setelah dikunci, proses tersebut terbukti dapat diulang.
panel manik-manik TS-RAPM-009
Bagian datar sepanjang 600 milimeter ini menampilkan manik-manik paralel dari berbagai geometri. Ketebalan meningkat dari 3 menjadi 6 milimeter di satu sudut (pad-up) sedangkan sudut yang berlawanan menampilkan joggle ketebalan yang konstan. Tepi yang berlawanan terdiri dari flens vertikal dengan sudut draf yang bervariasi secara linier dari 0° hingga 20°.
Slippage pad-up
Uji coba awal dijalankan dengan pad-up yang ditumpuk di permukaan layup. Namun, karena lapisan pad-up terletak di dekat tepi bagian, mungkin saja mereka terjepit keluar dari bagian, menghasilkan daerah bertekanan rendah selama penyembuhan dan porositas. Solusinya adalah menyisipkan lapisan pad-up di dalam tumpukan laminasi. Risiko selip dan porositas tidak terlihat di bagian selanjutnya di mana bantalan ditempatkan jauh dari tepi dan secara efektif dikunci oleh material di sekitarnya.
Porositas dengan waktu tinggal
Peningkatan porositas juga terlihat jika waktu tinggal terlalu lama. Panel manik-manik yang dibuat dengan waktu diam 8 menit memiliki kandungan rongga yang lebih rendah daripada yang dibuat dengan waktu diam 10 menit. Hal ini terutama berlaku di area pad-up, di mana kandungan rongga adalah 5,5% untuk 10 menit dan 0,4% untuk 8 menit. Tempat tinggal yang lebih pendek mempertahankan aliran resin yang tinggi, membasahi serat secara efektif, dan mempertahankan tekanan dalam rongga pahat melalui proses curing.
Tempat tinggal yang lebih lama memungkinkan aliran dan tekanan resin berkurang, terutama di area pad-up, karena kedekatannya dengan tepi rongga pahat, yang tidak memiliki tepi geser atau pengurangan penampang. Dengan demikian, tekanan di rongga pahat menurun di tepi bagian, terutama di daerah yang lebih tebal di mana penampang lebih besar. Tidak adanya tekanan di sini juga memperburuk risiko selip pad-up plies. “Saat merancang perkakas, pengurangan bagian di sekitar rongga pahat akan membantu membangun dan mempertahankan tekanan, terutama untuk suku cadang dengan ketebalan yang bervariasi,” jelas Gail Hahn, rekan peneliti Boeing dan penyelidik utama untuk proyek RAPM. “Anda perlu menunjukkan beberapa bentuk penjepit atau penyegelan untuk mendorong keadaan tekanan hidrostatik di rongga.”
tulang rusuk TS-RAPM-002
Setelah parameter pemrosesan ditetapkan untuk panel manik-manik TS-RAPM-009, proses diulangi untuk rusuk TS-RAPM-002, yang berukuran 540 milimeter pada tepi terpanjangnya. Tulang rusuk membangun ketebalan di tengah dari 3,3 hingga 5,2 milimeter dan kedalaman penarikan adalah 42 milimeter pada bagian akhir yang dipangkas. Keempat tepi menampilkan flensa vertikal. Perhatikan bahwa sudut kompensasi pegas ditentukan selama uji coba panel manik-manik dan kemudian diterapkan pada geometri pahat rib. Uji coba panel manik-manik juga menghasilkan kemampuan tegangan yang lebih tinggi dan modularitas lokasi pegas pada rangka pegas.
Kelebihan bahan untuk klem
Iga dibuat menggunakan cetakan rangka pegas dan DDF. Karena tarikan tulang rusuk yang dalam, material berlebih diperlukan untuk memasang klem rangka pegas, tetapi hal ini dapat dikurangi saat menggunakan DDF. Masalah lainnya adalah bahwa desain pahat membatasi ruang untuk klem pegas berada di sekitar rongga pahat.
Variasi dalam CPT
Ketebalan lapisan yang diawetkan (CPT) lebih tinggi di bagian datar dari rusuk daripada di tepi vertikal. Itu beralasan bahwa geometri bagian menyimpan resin di dalam area datar tengah, mencatat bahwa flensa vertikal bertindak sebagai segel resin. Ini membantu pemadatan dan penyelesaian bagian di area datar tengah. Namun, sayap vertikal mengalami geser yang kuat selama penutupan pahat, yang menyebabkan kekasaran permukaan tetapi bukan porositas (lihat data porositas di bawah). CYCOM EP2750, material curah yang lebih rendah, membantu mengurangi efek ini — ketebalannya yang lebih rendah mengurangi geser.
Variasi ketebalan web dengan kandungan resin prepreg
Penyelidikan kualitas menunjukkan tulang rusuk berulang dengan porositas <0,1% dan kerutan/gelombang serat minimal. Namun, sementara diasumsikan variasi ketebalan bagian akan diminimalkan dengan pemrosesan cetakan yang sesuai, tinjauan parameter pemrosesan material dan CPT bagian akhir menunjukkan bahwa sementara celah perkakas di flensa vertikal rusuk tetap dan konsisten, ketebalan web dapat bervariasi sebagai fungsi kandungan resin prepreg (kurang dari +/-2%) dan proses — CPT dapat bervariasi antara flensa dan jaring karena resin dibiarkan bermigrasi di dalam rongga.
TS-RAPM-003 saluran-C melengkung
Bagian ini memiliki panjang 640 milimeter dengan bagian U sedalam 40 milimeter pada bagian akhir yang dipangkas. Jari-jari bagian dalam lebih besar dari jari-jari luar, dan ketebalannya meningkat dari 6,6 milimeter di bagian sempit menjadi 8,8 milimeter di ujung lebar. Karena ketebalannya, bagian saluran-C secara substansial lebih berat daripada bagian sebelumnya yang dibahas. Oleh karena itu, bingkai pegas membutuhkan lebih banyak titik pemasangan dibandingkan dengan bagian sebelumnya.
Double dwell untuk mempertahankan tekanan di bagian yang tebal
Pemindaian-C dari bagian yang dicetak menyoroti kerutan yang merambat dari jari-jari dalam ke jari-jari luar untuk bagian-bagian yang menggunakan blanko prakonsolidasi. Skala abu-abu menunjukkan kerutan juga membawa porositas.
Kerutan dan porositas ini dihilangkan untuk bagian prepreg CYCOM EP2750 dengan menggunakan “double dwell” proses. Ini terdiri dari menerapkan sejumlah tekanan selama tinggal segera setelah peningkatan viskositas material. "Ini ditentukan dengan menggunakan data yang disediakan oleh pers dan alat-alat selama pengembangan proses," jelas Hahn. “Pada dasarnya, ada dua langkah peningkatan tekanan progresif sebelum aplikasi tekanan penuh. Akibatnya, profil tekanan-vs-waktu memiliki bentuk yang mirip dengan profil viskositas resin. Tempat tinggal awal pada ketebalan massal digunakan untuk mendorong viskositas resin ke atas untuk mencegah penipisan muatan material [kosong atau bentuk awal]. Jika muatan memiliki ketebalan yang signifikan, dua tempat tinggal digunakan untuk mencegah hilangnya tekanan karena penyusutan resin. Tempat tinggal pertama berada di celah X, dan yang kedua di celah Y, dengan Y
Gambar 18 di atas menunjukkan pengaruh tinggal ganda pada ketebalan bagian saluran-C. Menyesuaikan tekanan dengan viskositas resin memungkinkan lebih banyak resin untuk dipertahankan di dalam bagian, yang membasahi serat untuk porositas rendah dan ketebalan yang dibangun untuk mencapai distorsi serat rendah nominal yang diperlukan namun dipertahankan. Namun, tim RAPM menekankan bahwa proses tinggal ganda ini hanya disukai untuk bagian yang lebih tebal, karena dapat menyebabkan ketidakrataan CPT di bagian dengan ketebalan yang bervariasi.
Pelajaran RAPM dan uji coba bagian lebih lanjut
Uji coba bagian RAPM yang dibahas di sini telah memberikan kontribusi pengetahuan terhadap pembuatan suku cadang struktural kedirgantaraan tingkat tinggi menggunakan cetakan kompresi prepreg. Pelajaran yang dipetik meliputi:
- Bukti rendah bermanfaat untuk kualitas suku cadang, khususnya untuk menahan tingkat porositas dan meningkatkan penyelesaian permukaan pada tepi vertikal. Prepreg konten resin yang lebih tinggi, seperti CYCOM EP2750, memungkinkan jendela manufaktur yang lebih luas, serta peningkatan pengulangan proses
- Idealnya, peralatan press harus mencakup stasiun pemanasan awal inframerah (IR), rangka pembawa otomatis untuk memindahkan blanko/bentuk awal ke cetakan, toleransi paralelisme yang ketat antara pelat tekan atas dan bawah, kemampuan untuk mengontrol dan memantau posisi pelat untuk toleransi yang ketat dan kemampuan untuk menekan menggunakan kekuatan rendah maupun tinggi.
- Prakonsolidasi blanko/bentuk awal memungkinkan pengurangan gangguan serat pada dinding vertikal dan berkontribusi pada pengurangan tingkat porositas keseluruhan pada bagian yang dicetak. CATATAN ini debulking, BUKAN preforming pada alat berbentuk
RAPM telah menunjukkan bahwa cetakan kompresi prepreg dapat menghasilkan struktur kelas kedirgantaraan berkualitas tinggi sekaligus mengurangi waktu siklus dan tenaga kerja. Hal ini memungkinkan komposit untuk bersaing lebih baik dalam studi perdagangan untuk aplikasi luar angkasa sambil memberikan peningkatan penghematan berat dan kinerja komponen (misalnya, ketahanan terhadap korosi, retak dan kelelahan, dll.).
Solvay dan Boeing telah bekerja sama untuk menyempurnakan sistem prepreg EP2750 yang baru, menunjukkan waktu takt hingga 20 menit, berkat kombinasi kimia material, pengetahuan prepreg dan proses serta otomatisasi.
Selain bagian Pengembangan Manufaktur yang dibahas di atas, RAPM juga telah memproduksi beberapa bagian Tantangan dan Transisi, yang dimaksudkan untuk menantang perkembangan awal dan transisi kandidat dengan potensi untuk menang melawan aluminium mesin dalam aplikasi pertahanan. Ini termasuk:
- Bagian tantangan TS-RAPM-007 Solvay
- Panel akses kulit TS-RAPM-008
- TS-RAPM-012 Boeing "gelombang"
- Lengan motor TS-RAPM-014
- TS-RAPM-015 sirip
Hasil dan pembelajaran dari uji coba bagian ini dan studi fitur manufaktur RAPM lainnya akan dipublikasikan pada 2020/2021.
Solvay uji coba suku cadang otomotif
Solvay juga telah mengilustrasikan bagaimana kinerja EP2750 di suku cadang otomotif, seperti pilar B berukuran 36 kali 16 kali 2 inci dengan ketebalan .0725 inci, yang terdiri dari 5 lapis Solvay THORNEL T650-35 standar modulus 3K serat karbon derek dalam 376 gram/meter persegi 8-harness kain satin. Part ini dibuat di Solvay Heanor, UK menggunakan DDF. Jika dibandingkan dengan prepreg standar yang diautoklaf, kombinasi CYCOM EP2750 dan DDF menawarkan pengurangan 60% dalam waktu siklus dan 85% dalam waktu takt (waktu antara memulai satu bagian dan bagian berikutnya pada jalur produksi — yaitu, waktu denyut jalur) .