Rear wall reboot:One-stop, tow to tape to CFRP part
Pada permulaan kemajuan komposit serat karbon saat ini ke dalam aplikasi otomotif, pabrikan BMW Group (Munich, Jerman) tampaknya berdiri terpisah. Pekerjaan awal untuk mempercepat pencetakan transfer resin (RTM) untuk produksi M .-nya atap model sport mengarah pada pembentukan rantai pasokan lengkap untuk suku cadang plastik yang diperkuat serat karbon (CFRP) pada i3 dan i8 kendaraan dan kemudian ke sel kerja fabrikasi dan perakitan yang semuanya baru untuk body-in-white (BIW) Carbon Core multi-material pada Seri 7 .
BMW berkomitmen pada i3 pada tahun 2009 sangat meriah, tetapi pada tahun yang sama, Audi AG (Ingolstadt, Jerman) mendirikan pusat teknis yang dikhususkan untuk plastik yang diperkuat serat. Pada tahun 2011, Audi mengumumkan kemitraan dengan Voith Composites (Garching, Jerman) untuk mengembangkan dan memproduksi suku cadang CFRP dengan volume tinggi. Tahun berikutnya, ia mempublikasikan pengembangan pilar B baja yang diperkuat CFRP, dibuat menggunakan resin transfer moulding (RTM), dan kemitraannya dengan SOGEFI (Guyancourt, Prancis) untuk mengkomersialkan pegas suspensi koil komposit. Pada tahun 2012, Audi juga menjabat sebagai mitra pendiri klaster terdepan MAI Carbon, yang mencakup BMW, Voith Composites, SGL Group (Wiesbaden, Jerman) dan lainnya.
Terutama, narasi Audi tentang pengembangan CFRP dimulai dengan R8 generasi pertama. mobil sport, dirilis pada tahun 2006. Ini menampilkan penutup kompartemen untuk bagian atas yang dapat dikonversi serta bilah samping yang dibuat oleh resin transfer moulding (RTM). Perusahaan berkembang dari eksterior estetika dan struktur yang lebih kecil ke Modular Sportscar System (MSS) di Audi R8 e-tron . Meskipun struktur utama supercar listrik itu terdiri dari balok aluminium ekstrusi yang digabungkan dengan coran aluminium, semua panel dan pengisinya adalah CFRP, termasuk sisipan bagasi dengan struktur tabrakan bergelombang yang memungkinkan modul belakang menyerap energi lima kali lebih banyak daripada rangka logam. .
Tulang punggung MSS adalah dinding belakang , yang berkembang dari konsep awal pada tahun 2011 menjadi modul yang saat ini diproduksi untuk R8 non-listrik oleh SGL Technologies (sebelumnya BENTELER-SGL, Ort im Innkreis, Austria; lihat “Tur Pabrik:BENTELER SGL”). Tapi Audi sudah merencanakan langkah selanjutnya:mengulangi dinding belakang untuk digunakan dalam volume yang lebih tinggi A8 sedan mewah, dengan Voith Composites sebagai mitra manufakturnya.
Voith Composites adalah anak perusahaan berusia 10 tahun dari multinasional Voith GmbH &Co. KGaA, didirikan pada tahun 1867. Perusahaan induk sekarang mempekerjakan 19.000 karyawan, memiliki pendapatan tahunan sebesar €4,2 miliar (US$5,2 miliar) dan menyediakan peralatan dan teknologi manufaktur melalui empat divisi:Voith Digital Solutions, Voith Hydro, Voith Paper dan Voith Turbo. Komposit Voith berkembang dari produksi gulungan CFRP yang digunakan dalam pembuatan kertas menjadi manufaktur poros penggerak/poros cardan otomotif dan industri dan laminasi datar.
Pada tahun 2011, Voith Composites mulai mengerjakan rantai proses CFRP yang sangat otomatis, yang bertujuan untuk memproduksi A8 dinding belakang. Pada intinya adalah Voith Roving Applicator (VRA), yang, dalam satu baris, menyebarkan derek serat karbon 35K dari Zoltek (St. Louis, MO, US) ke pita pengikat searah (UD), yang kemudian dipotong dan ditumpuk ke membentuk blank yang disesuaikan. VRA diakui dengan Penghargaan Inovasi JEC pada tahun 2017. VRA juga membangun dasar yang kuat untuk operasi pembentukan dan pencetakan berikutnya. Penghargaan tertinggi kategori otomatis diraih lagi untuk Voith Composites dan Audi di JEC World 2018 untuk lini produksi digital 4.0 berbasis VRA yang telah selesai digunakan untuk memproduksi Audi A8 modul dinding belakang. Bekerja sama dengan pemasok resin Dow Automotive (Auburn Hills, MI, US) dan Zoltek, mitra ini tidak hanya mengembangkan bahan, proses, dan sistem inspeksi inline terintegrasi yang diperlukan untuk memproduksi suku cadang CFRP berkinerja tinggi dengan laju volume tinggi, tetapi juga menciptakan suku cadang CFRP yang lengkap. rangkaian desain/manufaktur berbantuan komputer (CAD/CAM) dan alat simulasi yang penting yang telah diterapkan untuk mengembangkan bagian masa depan.
Evolusi desain yang didorong oleh efisiensi
“Kami mulai bekerja dengan Audi sejak awal,” kata Dr. Jaromir Ufer, kepala pengembangan bisnis Voith Composites. Prioritas pertama adalah mengembangkan A8 baru desain dinding belakang, yang akan mengarahkan bagaimana bagian tersebut harus dibuat.
“Ketika kami memulai rekayasa untuk produksi ini, kami tidak dapat menemukan produk [perangkat lunak] siap pakai yang memiliki semua yang kami butuhkan,” jelas Ufer. “Jadi kami menyatukan alat desain seperti ABAQUS, tetapi membuat kartu material kami sendiri dan mengembangkan metode simulasi kami sendiri.” Audi telah mengidentifikasi pengurangan bobot BIW dan peningkatan kekakuan torsi sebagai tujuan utama R8 desain dinding belakang (lihat “Dinding kursi Audi R8:Awal produksi”). Untuk A8 modul, desain integral diajukan untuk mengurangi MSS multi multi-komponen perakitan ke panel CFRP tunggal berbentuk dengan sejumlah kecil attachment yang terikat dan terpaku. Desain ini mendorong pengembangan laminasi yang sangat anisotropik dengan jalur beban lokal, yang memungkinkan bagian yang telah selesai menghasilkan 33% kekakuan torsi sel penggerak pada 50% berat vs. perakitan tiga hingga lima bagian aluminium yang dilas.
“Preform komposit untuk Audi A8 panel dinding belakang bervariasi dari dasar 6 lapisan hingga 19 lapisan di mana tulangan lokal ditambahkan — misalnya, di mana ada pemutus atau beban titik, seperti lampiran pengaman gendongan anak,” jelas Ufer (Gbr 2).
Aplikator Voith Roving
Ufer mencatat bahwa pengembangan desain ini dan VRA berjalan beriringan. “Hanya dengan memiliki kebebasan desain yang ditawarkan VRA adalah kinerja A8 baru dinding belakang mungkin.” Yang juga penting adalah fakta bahwa pemasok serat Zoltek membuat komitmen harga selama 7 tahun untuk program tersebut.
Proses VRA dimulai dengan lapisan serat karbon PX 35 Zoltek. Beberapa kumparan penarik 50K dimasukkan ke setiap saluran VRA dan disebarkan untuk menghasilkan pita lebar 50 mm. Selanjutnya, pengikat berbasis epoksi diterapkan yang nantinya akan bereaksi dengan resin matriks epoksi snap-cure Dow VORAFORCE selama pencetakan transfer resin (RTM) dari bagian komposit. Sejumlah kecil panas inframerah (IR) diterapkan untuk melelehkan pengikat yang cukup untuk menahan pita bersama-sama melalui langkah-langkah konsolidasi, pemotongan, dan penumpukan berikutnya (Langkah 1).
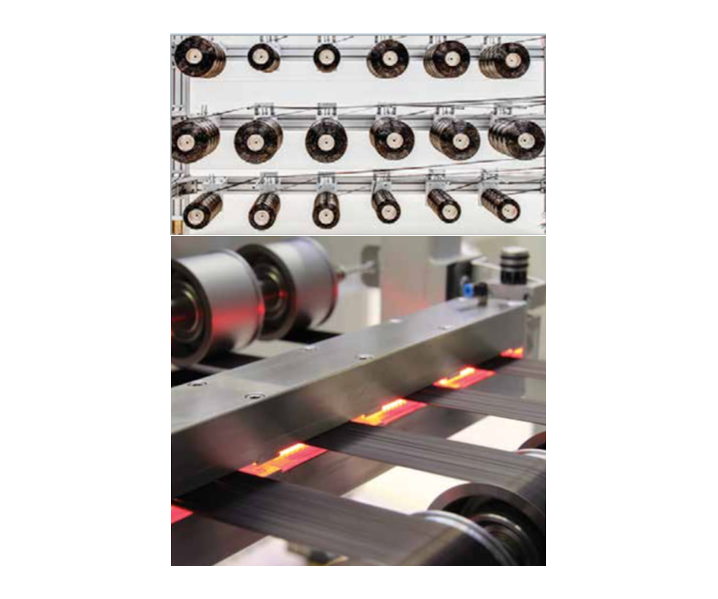
Langkah 1: Derek serat karbon Zoltek 50K dimasukkan ke dalam Voith Roving Applicator (VRA), di mana ia pertama kali disebarkan, kemudian dilapisi dengan pengikat berbasis epoksi dan kemudian dipanaskan dengan IR untuk melelehkan sebagian pengikat.
“Ini adalah proses berkelanjutan yang sepenuhnya otomatis,” kata Ufer. “Jika karena alasan tertentu perlu untuk menghentikan saluran, peralatan akan bereaksi secara otomatis. Misalnya, pemanas IR segera dimatikan dan ditarik kembali untuk mencegah kerusakan pita karena panas berlebih. Ada ratusan detail seperti itu dalam peralatan, dan kontrol digital memungkinkan teknologi ini.”

Langkah 2: Pita penarik sebar kemudian dikonsolidasikan saat berjalan melalui beberapa rol di bawah tekanan.
Setelah aplikasi pengikat, konsolidasi pita dicapai saat melewati beberapa rol di bawah tekanan (Langkah 2). Ufer menjelaskan ini juga membangun buffer untuk saluran. “Kami memiliki unit yang mengganggu aliran tarikan terus menerus dari serat, menyediakan transisi ke format pulsa mekanisme pita potong-dan-tempat.” Mekanisme berbasis gantry ini memotong pita dengan panjang yang disesuaikan dan menempatkannya pada sudut tertentu dari 0-360 ° ke meja putar (Langkah 3). Setiap tumpukan yang disesuaikan, terdiri dari 6 hingga 19 lapisan pita, dengan ketebalan masing-masing berkisar antara 1,5 hingga 3,7 mm.
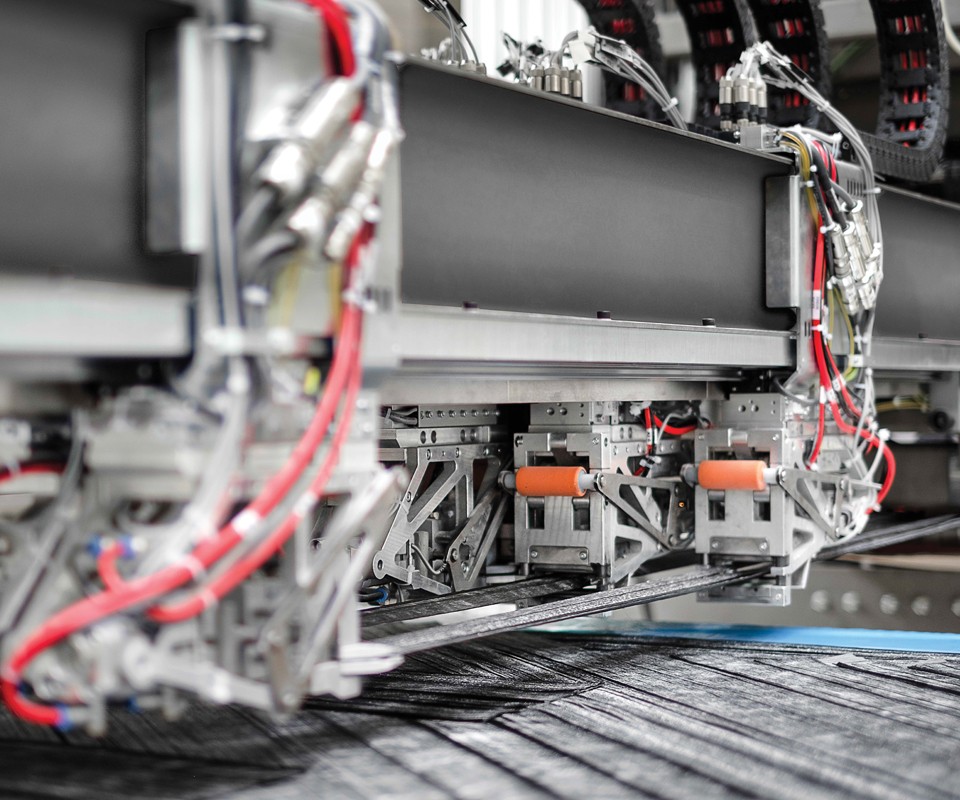
Langkah 3: VRA kemudian memotong pita dan menempatkan hingga empat bagian sekaligus ke meja putar, menyesuaikan panjang pita dan sudut orientasi di dalam tumpukan laminasi (mis., 45°/90°/30°).
Voith telah memasang empat jalur VRA (lihat foto pembuka), dan meskipun masing-masing menerapkan hingga empat pita lebar 50 mm sekaligus, Ufer menunjukkan, “garis memiliki pendekatan modular, sehingga mereka dapat menerapkan 10 atau lebih pita pada satu waktu. waktu. Itu tergantung pada ukuran bagian dan tingkat produksi. ”
Otomatisasi termasuk pemeriksaan kualitas. Pemindaian kaset dan bentuk awal dibandingkan dengan algoritma penolakan. “Pemindaian pita 100% oleh VRA memastikan distribusi serat yang tepat untuk seluruh lini produksi,” jelas Ufer. “Kami juga menggunakan sensor termografi dan laser untuk memeriksa bentuk awal di area yang ditentukan.” VRA kemudian dapat bereaksi terhadap masalah apa pun yang terdeteksi. “Jika satu pita tidak benar,” dia menunjukkan, “VRA akan memotong panjang yang kurang dan menghasilkan yang lain untuk menggantikannya.” Kode QR ditempatkan pada bentuk awal yang sudah jadi untuk keterlacakan. (Kode QR lebih disukai daripada tag identifikasi frekuensi radio (RFID) karena dilaporkan lebih tahan terhadap proses injeksi resin.)
Pembentukan, pencetakan, dan perakitan
Tumpukan 2D keluar dari VRA dan dipindahkan ke bagian pembentukan, pencetakan, dan perakitan jalur produksi. Mesin press pertama di mana ia ditempatkan, dipasok oleh spesialis otomasi komposit FILL (Gurten, Austria), menggunakan panas dan tekanan untuk membentuk tumpukan pita 2D menjadi bentuk awal 3D (Langkah 4). Ufer menjelaskan bahwa karena preform bervariasi dalam ketebalan dan bentuk, press dapat menyesuaikan tekanan yang diterapkan saat membentuk bagian yang terpisah dari preform yang dijepit di alat pembentuk. ALPEX Technologies (Mils bei Hall, Austria) membuat cetakan RTM baja yang cocok, berdasarkan desain yang disediakan oleh Voith Composites. “Kami mengembangkan proses perkakas dan pers secara virtual,” kata Ufer. “Meskipun tidak ada pengujian loop yang sebenarnya diperlukan, kami memvalidasi dan memverifikasi model simulasi pada bentuk dan bagian lain sebelum pemesinan A8 alat produksi dinding belakang. Simulasi proses pencetakan ini langsung menuju produksi nyata, dan membantu mempercepat pengoptimalan.”
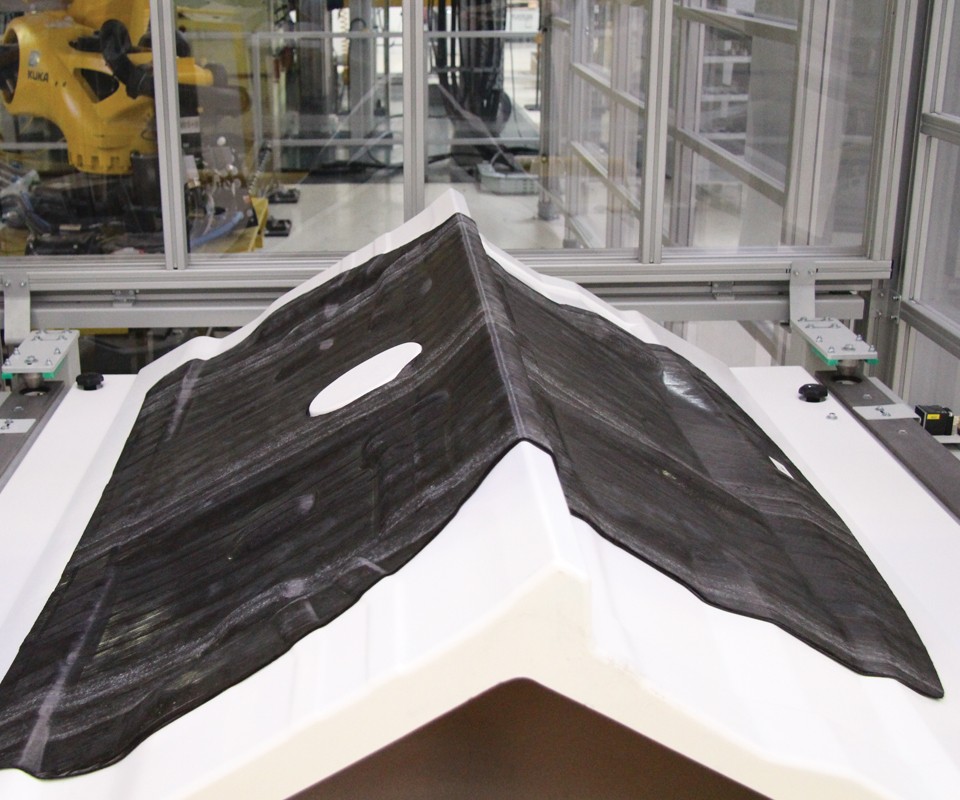
Langkah 4 :Tumpukan pita dipindahkan ke mesin press, di mana ia dibentuk menjadi bentuk bagian 3D akhir.
Pers menahan selama beberapa detik untuk mereaksikan pengikat bubuk dan mengatur bentuknya, menghasilkan bentuk awal yang stabil yang dapat menahan pencucian serat selama injeksi resin. “Partikel pengikat juga berfungsi untuk menahan serat untuk meningkatkan aliran resin selama RTM,” catat Ufer. “Ini berguna karena tidak ada jahitan pada bentuk awal untuk membantu aliran resin, sehingga partikel pengikat ini bertindak sebagai saluran aliran mikro.”
Bentuk awal selanjutnya ditransfer oleh robot ke sel CNC EiMa Maschinenbau GmbH (Frickenhausen, Jerman), tempat pisau ultrasonik memotong kontur akhir luar. Kemudian ditempatkan secara robotik ke dalam pers RTM (Langkah 5) yang dipasok oleh ENGEL (Schwertberg, Austria). Semua robot dalam barisan dipasok oleh KUKA Robotics (Augsburg, Jerman).
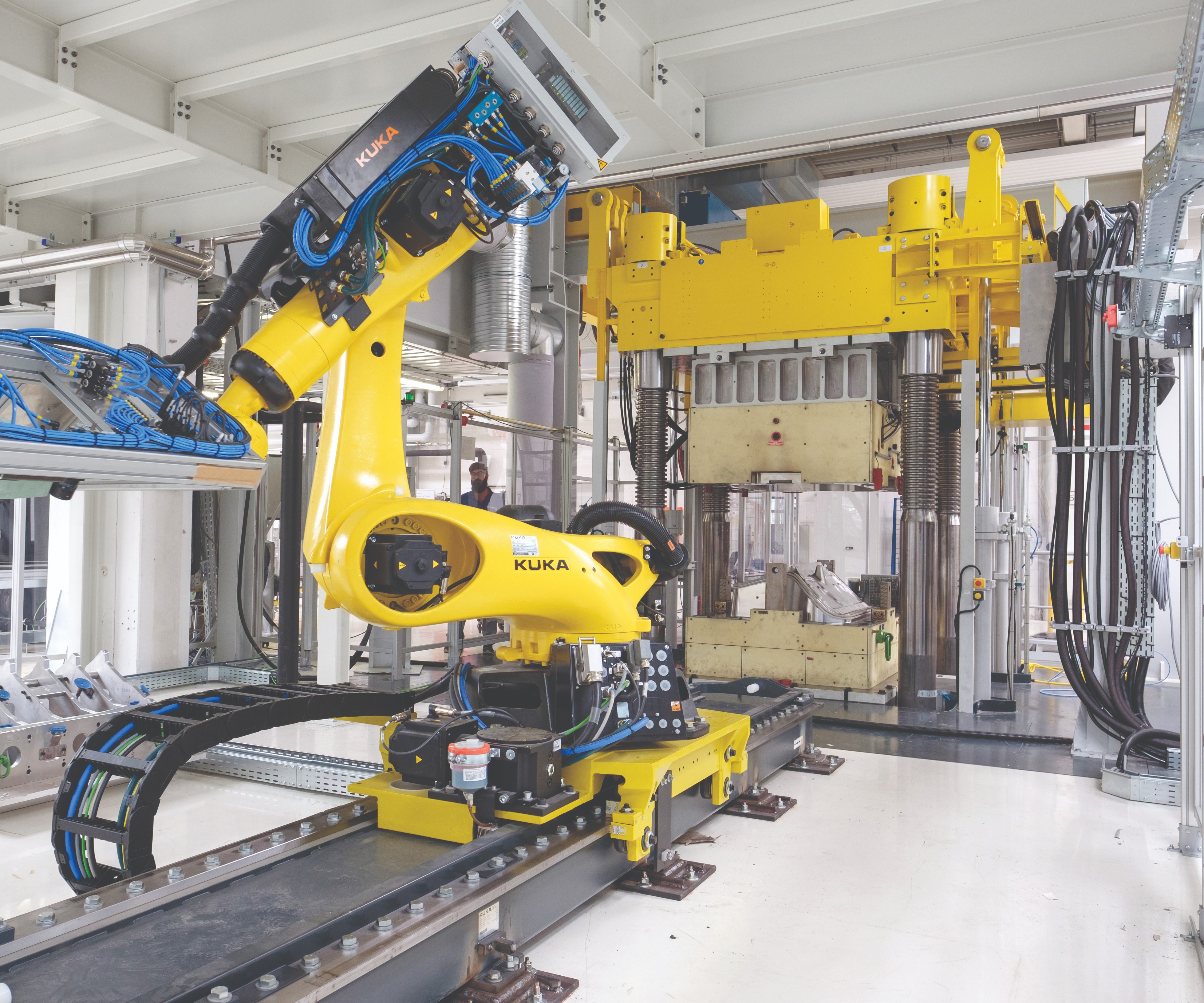
Langkah 5: Bentuk awal ditempatkan ke dalam pers 350-kN dan dicetak, menggunakan ultra-RTM.
Proses RTM digunakan untuk mencetak A8 dinding belakang sama dengan yang dikembangkan di Audi Lightweight Center untuk R8 sebelumnya dinding belakang, disebut sebagai ultra-RTM. Ini memungkinkan pencetakan bagian besar menggunakan injeksi cepat tetapi tekanan rendah. Dibandingkan dengan 140 bar khas HP-RTM, tekanan injeksi resin dalam cetakan selama ultra-RTM Audi A8 dinding belakang <15 bar, bahkan kurang dari itu untuk R8 . Akibatnya, alih-alih 2.500 kN gaya tekan, hanya diperlukan 350 kN. Oleh karena itu, mesin press yang lebih kecil dan lebih murah dapat digunakan untuk menghasilkan suku cadang bervolume tinggi dan berkualitas tinggi.
Resin epoksi VORAFORCE 5300, sistem tiga komponen yang mencakup pelepasan cetakan, mengering dalam 90-120 detik pada 120 °C dan memiliki viskositas pemrosesan 20 cps. Untuk A8 dinding belakang, tembakan resin 1,3 kg disuntikkan ke dalam bentuk awal, diikuti dengan penyembuhan 120 detik.
Bagian yang diawetkan secara robotik dibongkar dan dimuat ke dalam sel penggilingan CNC tertutup untuk pemesinan potongan. Selanjutnya, bagian yang digiling ditempatkan ke dalam mesin cuci otomatis untuk membersihkan sisa debu CFRP.
Dinding belakang yang dicuci dipindahkan ke sel perakitan yang dilengkapi dengan dua robot. Robot pertama menempatkan bagian cetakan ke dalam mesin paku keling otomatis, yang mendokumentasikan gaya yang diterapkan selama pemasangan paku keling. Ini adalah bagian dari kecerdasan manufaktur yang dibangun ke dalam keseluruhan proses dan ditambahkan ke catatan pemrosesan digital setiap bagian (yaitu, utas digital). Bagian tersebut kemudian dipindahkan ke area bonding dan robot kedua menyiapkan area untuk bonding, menggunakan pembersih pelarut otomatis. Robot yang sama kemudian menerapkan perekat struktural poliuretan Dow BETAFORCE 9050M dua komponen yang cepat sembuh (Langkah 6), yang kompatibel dengan epoksi tiga bagian. Bagian selanjutnya ditempatkan dalam oven untuk siklus penyembuhan perekat pendek.
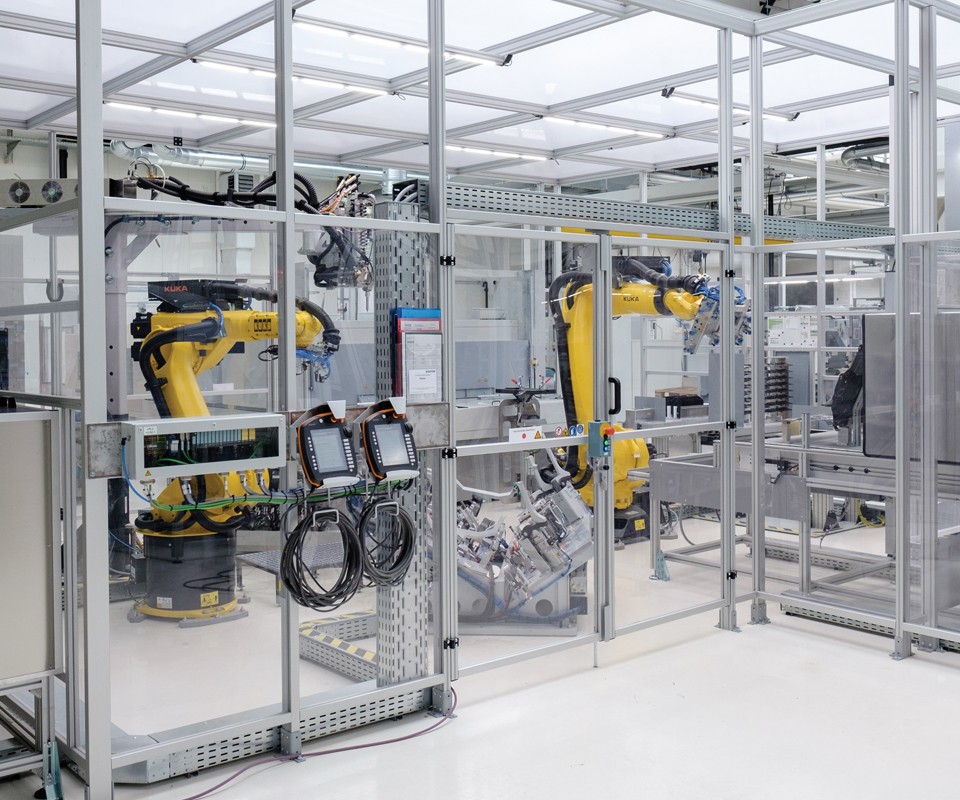
Langkah 6: Perekat poliuretan BETAFORCE diterapkan secara robotik untuk perekat yang direkatkan dan kemudian diawetkan dalam siklus oven yang singkat.
Lini produksi ini mempertahankan waktu siklus 5 menit untuk suku cadang yang telah selesai dan permintaan suku cadang saat ini dapat dipenuhi dalam satu atau dua shift 8 jam. Perangkat pemindaian laser 3D digunakan secara berkala untuk memeriksa bentuk dan pengukuran 3D bagian tersebut. Bagian yang sudah jadi kemudian disiapkan untuk pengiriman ke Audi A8 jalur perakitan akhir di Neckersalm, Jerman, sekitar 3 jam perjalanan darat (Langkah 7).
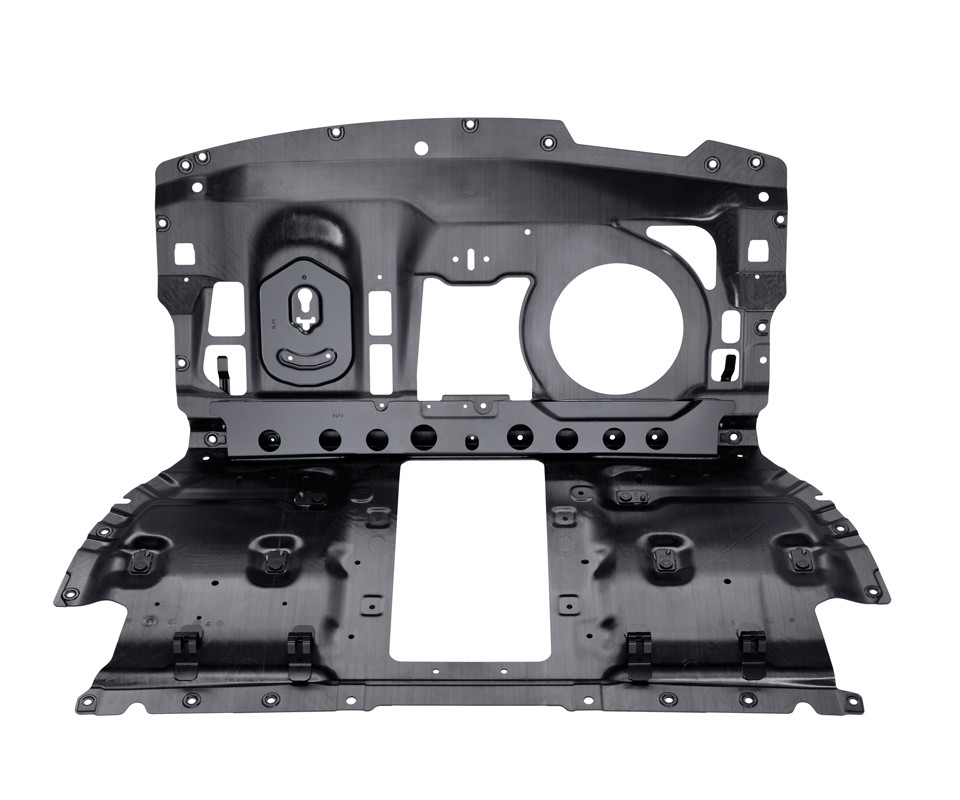
Langkah 7 Bagian yang telah selesai kemudian disiapkan untuk pengiriman ke jalur perakitan akhir Audi A8.
Penempatan serat langsung =fleksibilitas masa depan
Dengan semua investasi yang telah dilakukan, mengejutkan untuk mengetahui bahwa Voith Composites tidak yakin dengan bisnis ini, tetapi memang perusahaan menyelesaikan pengembangan dan kemudian berpartisipasi dalam proses penawaran yang kompetitif untuk memenangkan produksi. “Kami mampu memenuhi target biaya suku cadang yang ditentukan oleh Audi, serta persyaratan kualitas dan kinerja suku cadang,” kata Ufer. Ini bukan prestasi kecil, mengingat beberapa perusahaan bersaing untuk program tersebut.
Voith Composites telah mematenkan beberapa bagian dari prosesnya. “VRA telah menunjukkan industrialisasi menggunakan penempatan serat langsung [DFP] dari kaset, yang mengurangi skrap serta bahan yang digunakan melalui layup yang sangat dioptimalkan,” kata Ufer. Ini juga menggunakan bahan yang paling hemat biaya — serat derek berat dan pengikat bubuk yang tidak diolah. Proses generasi kedua menggantikan pengikat bubuk dengan aplikasi langsung resin, menghilangkan lebih banyak langkah proses. Namun, perusahaan telah mengembangkan proses DFP lainnya, termasuk Voith Longfiber Preformer dan Voith Prepreg Winding.
“Kami menetapkan standar baru untuk suku cadang serat karbon untuk produksi serial otomotif volume tinggi,” kata direktur pelaksana Voith Composites Dr. Lars Herbeck. “Pabrik pintar yang kami dirikan membawa produksi otomatis komponen CFRP ke tingkat efisiensi dan fleksibilitas baru, termasuk hampir semua bentuk serta ukuran lot individual.” Ini, memang, di mana industri ini menuju.