Pengekstrusi pelet:Apakah mungkin pencampuran langsung pelet dengan aditif?
Pencetakan pelet , juga dikenal sebagai fabrikasi granulat leburan (FGF ), sebagian besar terkait dengan pencetakan injeksi, tetapi juga banyak digunakan dalam pencetakan 3D FDM, terutama dalam kondisi profesional atau industri. Ini memungkinkan pengguna untuk membuat campuran khusus berdasarkan polimer basa dan aditif yang dipilih , semua dalam bentuk pelet. FGF adalah metodologi ideal untuk pencetakan format besar dan pembuatan prototipe , dan pembuatan filamen itu sendiri . Pencetakan 3D dengan pelet memerlukan printer 3D yang dilengkapi dengan pelet hopper dan ekstruder pelet , seperti Dyze Pulsar Pellet Extruder aliran tinggi , yang kompatibel dengan sebagian besar printer 3D berskala besar atau dipasang di lengan robot.
Pencetakan 3D dengan pelet menawarkan banyak keuntungan . Biaya produksi jauh lebih rendah (sebesar 60 - 90 %) dibandingkan dengan pencetakan 3D filamen karena pelet lebih banyak tersedia dan lebih sedikit diproses daripada filamen, sehingga mengurangi biaya dan waktu produksinya . Selain itu, FGF mengizinkan penggunaan bahan daur ulang , dan cocok untuk pencetakan format besar, seperti pekerjaan konstruksi. Contoh bagus dari ekstruder pelet yang tergabung dalam peralatan AM skala besar adalah robot ekstruder pelet yang merupakan bagian dari Sistem CEAD Flexbot .

Gambar 1. Pencetakan pelet 3D format besar dengan CEAD AM Flexbot. Sumber:CEAD.
Penggabungan plastik
Praktik yang sangat umum dalam industri plastik adalah penggabungan plastik . Ini terdiri dari pencampuran polimer cair dengan berbagai aditif untuk mencapai sifat termomekanis yang lebih baik atau lebih maju. Campuran tersebut kemudian dibentuk menjadi ekstrudat (untaian plastik), didinginkan , dan diteruskan ke granulator yang memotong ekstrudat menjadi pelet . Penggabungan plastik adalah cara yang bagus untuk meningkatkan sifat bahan cetak 3D.
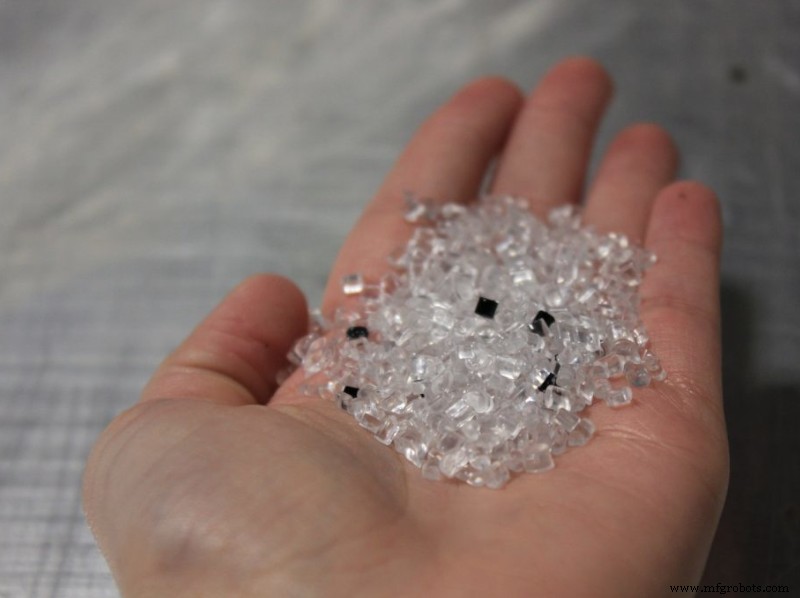
Gambar 2. Contoh campuran masterbatch PETG. Sumber:Desain Dyze.
Ini dilakukan dengan menambahkan masterbatch warna untuk mengubah warna polimer, atau masterbatch aditif untuk meningkatkan kinerja termomekanis plastik (kemampuan cetak lebih baik, laju aliran lebih tinggi, atau kekakuan lebih tinggi) atau memberikan sifat khusus . Beberapa sifat yang dapat dicapai dengan pencampuran pelet adalah:
- Kekuatan dan fleksibilitas :polimer dapat dicampur dengan serat karbon atau serat kaca untuk meningkatkan sifat termomekanis.
- Toleransi UV :degradasi plastik dapat diperlambat dengan menambahkan senyawa yang melindungi dari radiasi UV ke dalam campuran.
- Aditif keamanan pangan :harus dipastikan bahwa plastik yang dirancang untuk bersentuhan dengan makanan aman untuk tujuan tersebut.
- Fitur antimikroba :peracikan plastik juga digunakan untuk membuat campuran yang menghambat pertumbuhan kuman di permukaan plastik, fitur yang sangat penting dalam pengobatan .
- Retardasi api :beberapa polimer diperkaya dengan zat yang mencegah atau menghambat penyebaran api, kualitas yang sangat berguna dalam industri otomotif atau luar angkasa.
- Deteksi magnetik :pelet polimer dapat dicampur dengan pelet yang dapat dideteksi secara magnetis untuk mencapai filamen yang dapat dideteksi secara magnetis.
- perlindungan ESD :mencampur pelet aman ESD dengan basis polimer akan menghasilkan bahan yang aman untuk ESD.
- Warna :peracikan plastik memungkinkan pencampuran warna yang praktis tidak terbatas.
Peracikan dilakukan oleh perusahaan profesional dengan bantuan peralatan khusus seperti pengaduk bersama, sekrup kembar (co-rotating dan counter-rotating) dan mixer internal untuk memastikan pencampuran yang tepat dari polimer dan aditif. Hasilnya dari proses ini adalah pelet yang siap digunakan dalam printer 3D yang dilengkapi dengan pellet extruder .
Pencampuran pelet
Pencampuran pelet dilakukan dengan sekrup pencampur disebutkan sebelumnya. Sekrup pencampur memiliki tiga zona berbeda, masing-masing memiliki peran dalam proses pencampuran:
- Zona makan , di mana pelet diangkut ke ekstruder.
- Zona transisi (kompresi) , di mana udara dikeluarkan dari campuran pelet saat sedang dipanaskan dan dilelehkan.
- Zona pengukuran , yang tugasnya membangun tekanan dan menstabilkan aliran output.
Ada variasi model di atas, dengan sekrup dengan bagian meteran yang diubah , seperti sekrup Maddock, untuk lebih menyempurnakan pencampuran dan homogenisasi lelehan.
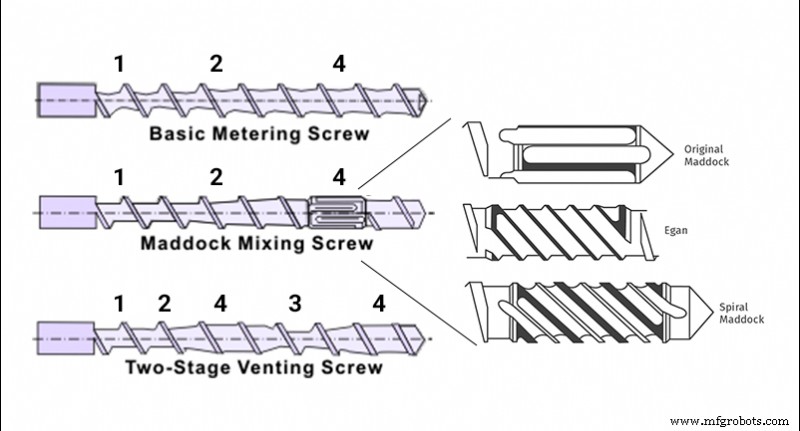
Gambar 3. Jenis sekrup pencampur, dengan bagian (1) Umpan, 2) Transisi, (3) Ventilasi, dan (4) Pengukuran. Sumber:Desain Dyze.
Bagian pencampuran tambahan di bagian pengukuran sekrup memiliki kelemahan (persyaratan torsi, pemanasan karena gerakan pemotongan ekstra) dan kinerja sekrup dan bahkan output dapat terpengaruh.
Jenis sekrup terbaik untuk mencampur pelet plastik adalah sekrup kembar . Ini adalah solusi yang paling umum digunakan dalam peracikan plastik. Contoh sekrup kembar adalah dua sekrup yang saling mengunci yang berputar bersama di dalam tong tertutup untuk memastikan pencampuran yang tepat dari lelehan dan hasil yang homogen.
Video 1. Simulasi compounding dengan sistem twin screw extrusion. Sumber:EnginSoftSpa.
Keuntungan ekstruder sekrup kembar dibandingkan ekstruder sekrup tunggal adalah bahwa dalam sistem ekstrusi dengan dua sekrup , aliran material yang baik tidak bergantung pada sifat aliran material karena dua sekrup meningkatkan efisiensi pemompaan . Selain itu, dalam sistem ekstruder kembar, transisi panas dari laras ke material lebih rata dan lebih cepat dibandingkan dengan sistem satu sekrup.
Beberapa sekrup tidak memiliki bagian pencampuran untuk mengurangi berat dan panjang sekrup . Contoh ekstruder pelet yang sekrupnya tidak berisi bagian pencampuran, adalah Pengekstrusi Pelet Dyze Pulsar . Pulsar memiliki mekanisme anti-pengaliran khusus ditambahkan di dekat nosel. Penambahan ini secara signifikan meningkatkan pencampuran dengan menambahkan beberapa jalur pencampuran dan pemisahan tetap ke lelehan tepat sebelum melewati nosel. Selain mekanisme anti bocor, Pulse memiliki penggeseran yang baik pada sekrup itu sendiri .
Video 2. Dyze Pulsar Pellet Extruder sedang bekerja. Sumber:Desain Dyze.
Gabungan kedua fitur tersebut mengkompensasi kurangnya tahap pencampuran di sekrup, dan memastikan homogenisasi yang tepat dari campuran polimer. Sebuah eksperimen melibatkan Dyze Pulsar Pellet Extruder, masterbatch pelet PETG, dan 1,6% pelet warna menghasilkan hasil yang memuaskan, dengan konsistensi warna dan homogenitas bahan yang sangat baik .
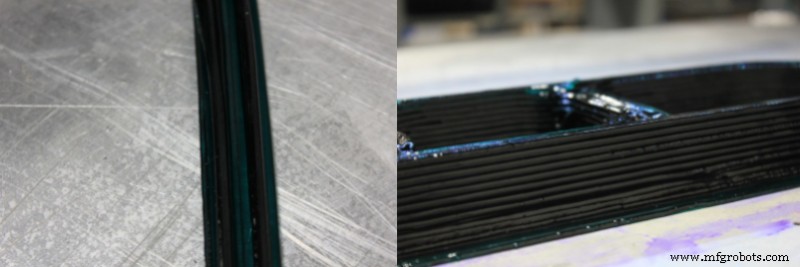
Gambar 4:Eksperimen yang melibatkan Dyze Pulsar Pellet Extruder, masterbatch pelet PETG dan 1,6% pelet warna. Sumber:Desain Dyze.
Penggabungan plastik dengan cara pencampuran pelet adalah teknologi yang tidak hanya memungkinkan produsen skala menengah dan besar mengurangi waktu dan biaya produksi tetapi juga memiliki kontrol lebih atas campuran polimer untuk aplikasi tertentu, karena pelet dan filamen khusus dapat dibuat dari pelet plastik sebagai bahan dasar dan penambahan masterbatch warna atau aditif.
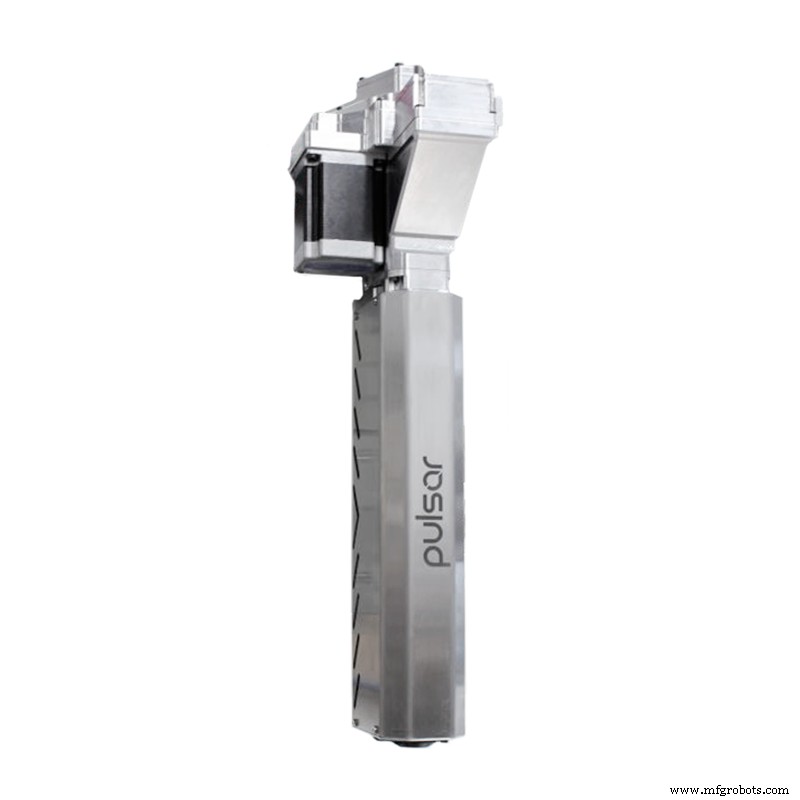
Dyze Pulsar Pellet Extruder
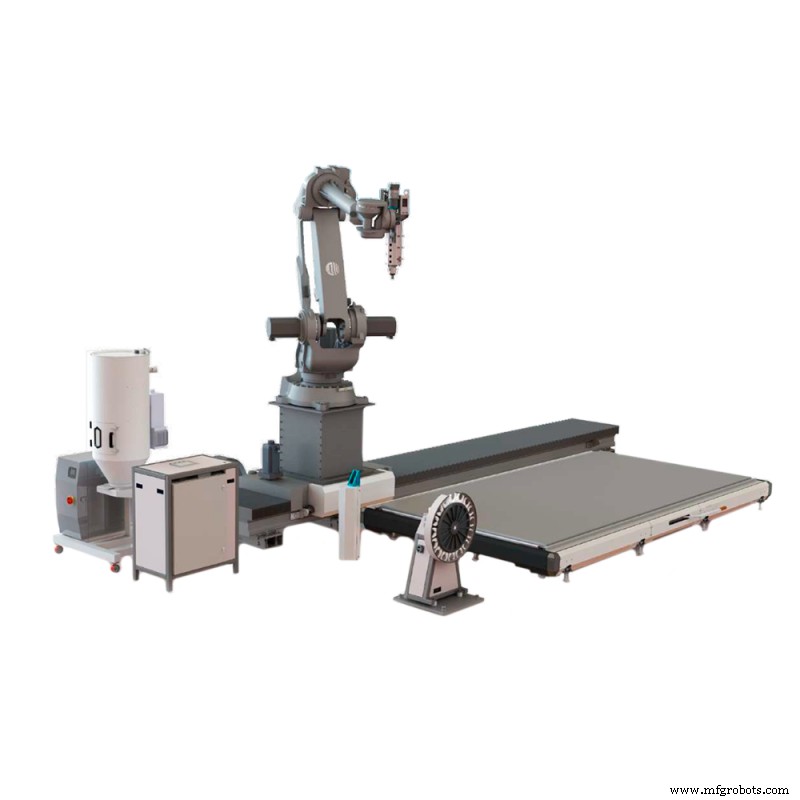
Sistem AM Flexbox
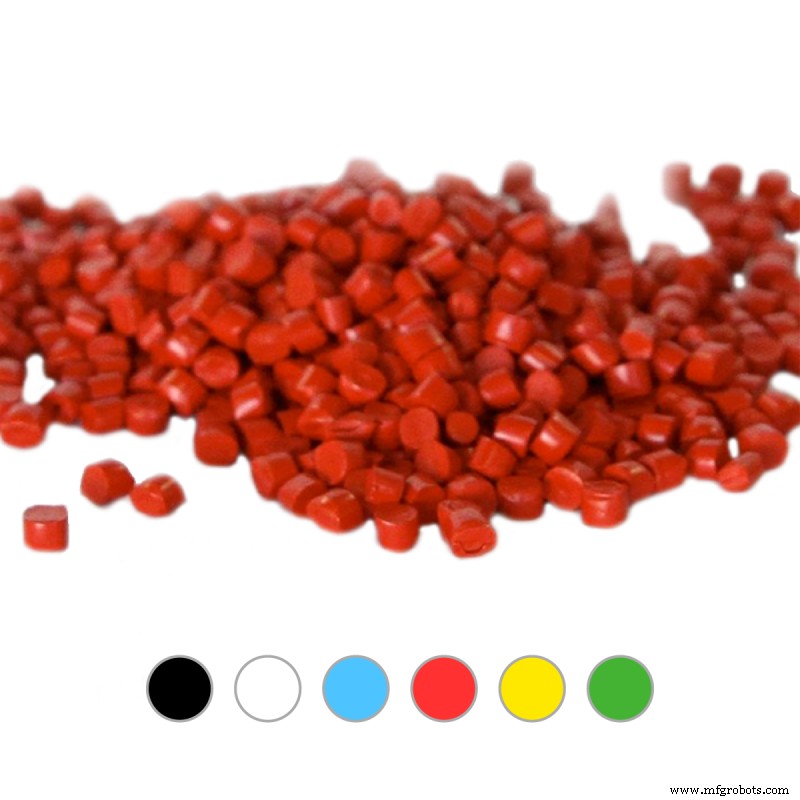
Masterbatch warna untuk pelet
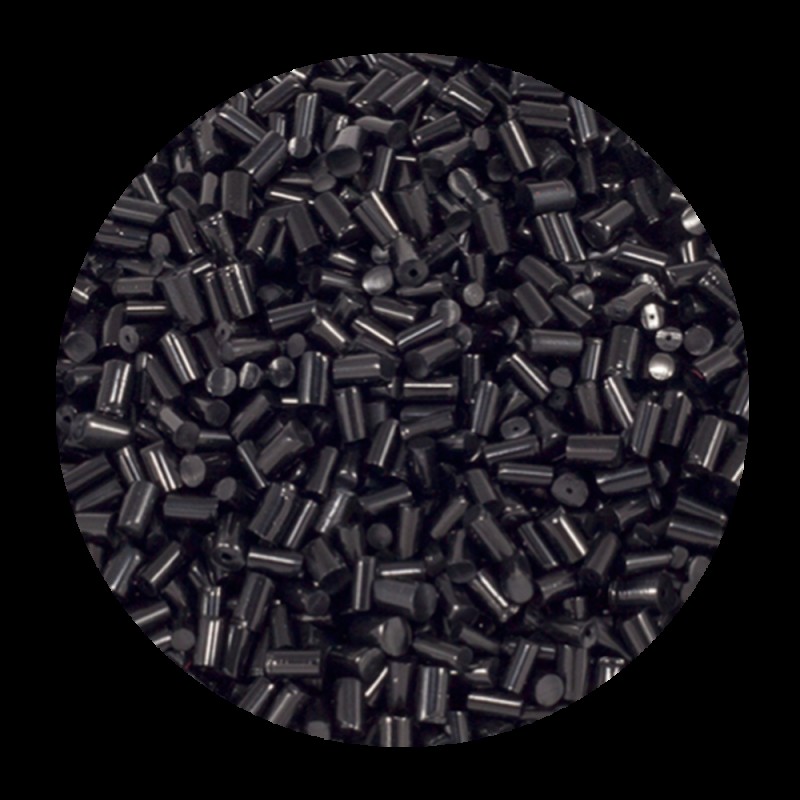
Pelet ABS ESD