Prinsip dan Alat Lean
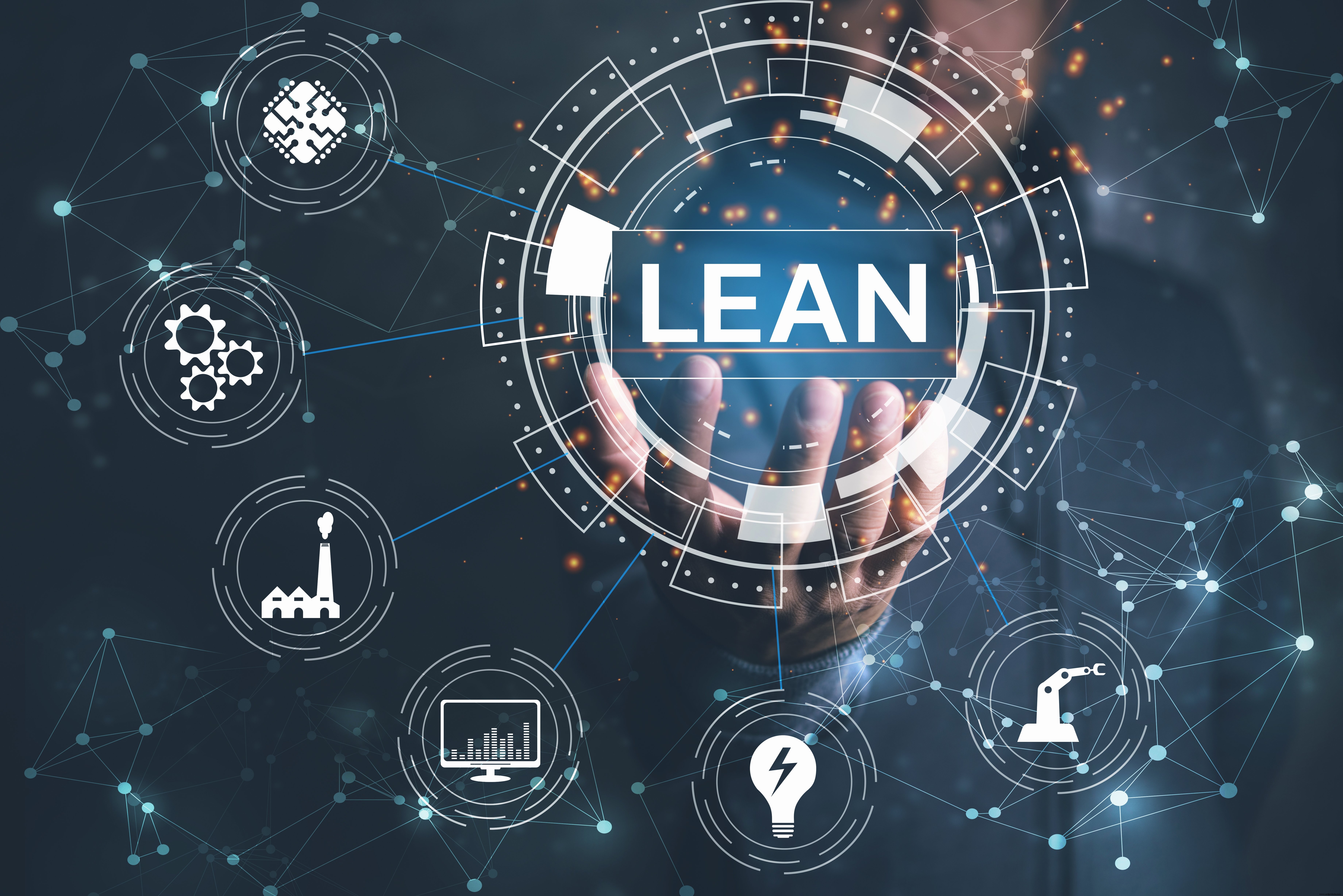
Selamat datang di seri kedua dari Lean dan Six Sigma. Seperti yang kita lihat di posting pertama, Lean dan Six Sigma adalah metodologi perbaikan berkelanjutan yang mengurangi pemborosan keseluruhan dan variabilitas dalam proses produksi. Meskipun kedua metodologi ini menggunakan pendekatan dan alat yang berbeda untuk mendorong peningkatan produktivitas dan profitabilitas, keduanya memiliki kesamaan yaitu dapat digunakan untuk meningkatkan setiap aspek bisnis Anda.
Filosofi ramping
Pilar Ramping
Filosofi lean memiliki dua pilar yang saling berhubungan:"Eliminate Waste" dan "Respect for Humanity." Elemen-elemen dasar ini sangat berkontribusi pada keberhasilan Lean Manufacturing. Mari kita bahas satu per satu — yang kedua dulu.
Konsep Penghormatan terhadap Kemanusiaan diwujudkan dengan menghormati para pekerja dan mengakui kecerdasan, kreativitas, dan kecerdasan bawaan mereka. Hal ini dicapai dengan memberdayakan dan menantang mereka untuk meningkatkan produk yang mereka buat bersama dengan proses produksi dan alat yang digunakan untuk membuatnya.
Konsep Menghilangkan Pemborosan adalah mekanisme yang digunakan organisasi untuk meningkatkan kualitas dan profitabilitasnya. Dari perspektif Lean, pelanggan menetapkan harga berdasarkan nilai yang mereka terima. Berdasarkan harga yang ditetapkan pelanggan tersebut, cara terbaik bagi organisasi Lean untuk meningkatkan profitabilitas dan berkembang adalah dengan menghilangkan penyebab kualitas rendah, keterlambatan pengiriman, masalah keamanan, dan biaya yang tidak perlu — semuanya didefinisikan dalam Lean sebagai "pemborosan."
5 Prinsip Lean
- Pahami "nilai" seperti yang didefinisikan oleh pelanggan
Memahami secara detail apa yang pelanggan hargai dan bersedia bayar untuk produk, layanan, atau informasi tertentu
- Tentukan aliran nilai untuk setiap produk
Identifikasi semua langkah terkait yang membentuk bisnis saat ini dan proses produksi yang diperlukan untuk mengubah input menjadi produk, layanan, dan informasi yang dihargai pelanggan
- Membangun aliran berkelanjutan dalam organisasi
Merampingkan proses, menghilangkan limbah sebanyak mungkin, sehingga produk, layanan, dan informasi berkualitas mengalir dengan lancar melalui aliran nilai
- Pertahankan aliran selama penggunaan sistem tarik
Berdasarkan aliran berkelanjutan, menyelaraskan dan menyeimbangkan produksi untuk memenuhi permintaan "Tepat pada waktunya" tanpa inventaris yang berlebihan, mempertahankan kualitas dan tingkat layanan yang tinggi
- Kejar kesempurnaan melalui peningkatan proses yang berkelanjutan
Berkomitmen untuk terus mengejar nol pemborosan dalam semua proses aliran nilai dengan mengulangi langkah-langkah ini dan mengadaptasi produk, layanan, dan informasi untuk mengubah permintaan pelanggan
Pekerjaan "Tidak Bernilai Tambah"
Seperti disebutkan di atas, menghilangkan pemborosan adalah pilar dasar Lean. Untuk mengidentifikasi pemborosan, semua tugas yang saat ini dilakukan dilihat melalui lensa pekerjaan yang bernilai tambah dan tidak bernilai tambah. Pekerjaan bernilai tambah secara langsung menciptakan fitur, karakteristik, dan manfaat yang diinginkan dan bersedia dibayar oleh pelanggan (misalnya, mengoperasikan mesin yang menghasilkan sisir plastik). Pekerjaan yang tidak bernilai tambah terdiri dari tugas-tugas yang tidak dipedulikan oleh pelanggan dan tidak ingin dibayar (misalnya biaya bahan dan tenaga kerja dari produk bekas yang diserahkan kepada pelanggan dengan harga sisir). Beberapa pekerjaan yang tidak bernilai tambah diperlukan. Misalnya, tugas untuk memenuhi persyaratan pelaporan menurut undang-undang perusahaan adalah tugas yang tidak secara langsung berkontribusi pada produksi sisir. Sementara pelanggan yang membeli sisir plastik mungkin tidak terlalu peduli dengan pelaporan menurut undang-undang, pemegang saham dan karyawan perusahaan melakukannya — tidak bernilai tambah tetapi perlu. Either way, melihat semua tugas yang diselesaikan, merampingkan, dan idealnya menghilangkan semua pekerjaan yang tidak perlu dan tidak bernilai tambah adalah tujuannya. Sejumlah penelitian telah dilakukan yang menunjukkan bahwa di banyak organisasi, lebih dari 90 hingga 95% pekerjaan yang dilakukan untuk menghasilkan produk atau layanan adalah pekerjaan yang tidak bernilai tambah.
Alat Lean
Ada sejumlah besar alat di toolkit Lean — lebih dari 20 atau 30, tergantung pada siapa Anda berbicara — semuanya memiliki aplikasi dalam berbagai situasi. Di bawah ini adalah daftar beberapa alat dasar di Lean.
Penerapan Kebijakan (Hoshin Kanri)
Penerapan Kebijakan adalah proses perencanaan dan pelaksanaan yang strategis. Ini dirancang untuk memastikan bahwa tujuan dan strategi perusahaan secara keseluruhan didefinisikan dan dikomunikasikan ke atas dan ke bawah tingkat organisasi. Selanjutnya, melalui proses tersebut, semua tingkatan organisasi mengidentifikasi bagaimana tujuan kerja departemen dan individu mereka dipetakan ke tujuan dan strategi perusahaan. Penyelarasan ini, hingga ke tingkat kontributor individu, memastikan pemahaman dan dukungan di seluruh organisasi dan menghilangkan pemborosan dengan memperbaiki tujuan yang tidak selaras sebelum sumber daya dihabiskan.
Pemetaan Aliran Nilai
Peta Aliran Nilai adalah alat yang memungkinkan tampilan ''horizontal'' dari langkah-langkah tingkat tinggi yang terlibat dalam menciptakan produk, layanan, atau informasi. Ini mendokumentasikan semua aliran material dan informasi dalam proses serta garis waktu di seluruh aliran nilai. Ini memetakan keadaan proses saat ini dan membawa visibilitas ke area peluang di jalur menuju keadaan masa depan yang lebih baik dengan membandingkan waktu siklus total dengan waktu nilai tambah.
8 Sampah
Dalam Lean, pemborosan biasanya diidentifikasi sebagai salah satu dari delapan kategori, yang semuanya merupakan pekerjaan yang tidak bernilai tambah. Ingat saja "D.O.W.N.T.I.M.E ."
- D efek - Produk, layanan, atau informasi yang tidak sesuai dengan spesifikasi pelanggan
- O verproduction - Menciptakan lebih banyak produk, layanan, atau informasi daripada yang diminta dari pelanggan pada waktu tertentu
- A aiting - Keterlambatan dalam pemrosesan produk, dan waktu idle yang dialami oleh orang dan mesin karena aliran yang tidak seimbang
- N Keterampilan yang Digunakan / Kreativitas yang Tidak Digunakan - Kegagalan untuk mencocokkan orang dengan bakat mereka, melibatkan mereka, dan memberdayakan mereka untuk mengembangkan peningkatan pada produk dan proses
- B ransportation - Perpindahan produk atau informasi yang tidak perlu
- Saya nventory (Kelebihan) - Produk, layanan, atau informasi melebihi jumlah yang sedang diproses dan yang tidak diperlukan untuk memenuhi permintaan pelanggan saat ini
- L otion - Pergerakan orang dan/atau mesin yang tidak menambah nilai produk
- E pemrosesan xcessive - Langkah-langkah proses atau aktivitas yang tidak perlu, sering usang, yang tidak lagi menambah nilai pada produk, layanan, atau informasi
Analisis Akar Penyebab - 5 Mengapa?
Dalam fasilitas manufaktur modern, ada sejumlah besar kerumitan dalam sistem dan proses yang digunakan untuk membuat produk, layanan, dan informasi. Ketika masalah terjadi, pendekatan Lean adalah untuk tidak puas dengan menangani gejala, tetapi bekerja untuk mengidentifikasi akar penyebabnya. Ini adalah praktik standar untuk bertanya dan menjawab pertanyaan "Mengapa?" setidaknya lima kali untuk melacak rantai sebab akibat kembali melalui gejala ke akar penyebab yang sebenarnya. Akar penyebab ini kemudian diselesaikan.
PDCA
Dalam Lean, proses yang sering digunakan untuk mencapai eliminasi pemborosan adalah siklus PDCA. Ini adalah proses berulang, terkadang memerlukan pengulangan beberapa kali sebelum akar penyebab pemborosan yang sebenarnya dapat diidentifikasi dan diselesaikan.
PDCA terdiri dari langkah-langkah berikut.
-
Rencana - Tentukan peluang/tujuan dan perubahan yang diperlukan
-
Lakukan - Lakukan perubahan untuk mewujudkan peluang yang teridentifikasi
-
Periksa - Mengukur dan mengevaluasi hasil perubahan yang dilakukan
-
Bertindak - Standarisasi proses baru atau mulai siklus lagi, berdasarkan hasil
5S / CANDO
5S berasal dari Sistem Produksi Toyota. Ini tentang menciptakan area kerja yang diatur untuk sukses di mana semua yang dibutuhkan, dan hanya yang dibutuhkan, adalah tempat yang seharusnya meminimalkan pemborosan dalam proses. Setiap S memiliki arti berdasarkan bahasa Inggris yang hampir setara dengan kata-kata Jepang. Mereka adalah:
Urutkan - Sortir semua bahan di area kerja dan singkirkan yang tidak diperlukan
Tetapkan dalam Urutan - Atur barang-barang yang dibutuhkan dan buat tempat untuk semuanya
Bersinar - Sering membersihkan area kerja
Standarkan - Tetapkan standar terdokumentasi untuk langkah-langkah Sortir, Atur dalam Urutan dan Kilau
Bertahan - Periksa dan perkuat standar yang ditetapkan
5S adalah adaptasi dari proses serupa yang dibuat oleh Henry Ford pada tahun 1920-an yang disebut CANDO :
C mencondongkan tubuh ke atas, A mengatur, N makan, D disiplin, O perbaikan berkelanjutan
Perubahan Cepat (Pertukaran Die Satu Menit - SMED)
Pernahkah Anda menonton balapan NASCAR dan bertanya-tanya bagaimana mereka mengganti empat ban dan mengisi tangki bensin dalam 7,3 detik? Ini melalui penerapan Rapid Changeovers atau S.M.E.D. teknik. Proses Perubahan Cepat mengurangi waktu set-up dan transisi untuk mesin dan proses. Di Lean, tujuan pengurangan waktu pengaturan dan pergantian adalah untuk meningkatkan fleksibilitas penjadwalan produksi dengan mengurangi ukuran batch yang optimal. Perubahan Cepat dicapai melalui metodologi lima langkah:
Langkah 1 - Amati dan pelajari set-up langkah/kegiatan proses changeover
Langkah 2 - Mengklasifikasikan langkah/kegiatan sebagai internal dan eksternal. Langkah-langkah internal hanya dapat terjadi ketika mesin/proses dihentikan - mis. mobil berada di pit. Langkah-langkah eksternal dapat terjadi saat mesin/proses sedang berjalan - mis. mobil keluar di trek.
Langkah 3 - Konversi langkah/aktivitas proses internal ke eksternal
Langkah 4 - Cari cara untuk mengurangi waktu dan upaya yang diperlukan untuk langkah internal yang tersisa
Langkah 5 - Cari cara untuk mengurangi waktu dan upaya yang diperlukan untuk langkah-langkah eksternal yang tersisa
Kanban
Kanban adalah metodologi untuk menyusun aliran material melalui proses manufaktur yang didasarkan pada tarikan. Ini biasanya didasarkan pada Kanbans, atau kartu tarik, yang menandakan proses hulu bagian mana yang harus diproduksi dan dalam jumlah berapa berdasarkan kebutuhan hilir. Sistem Kanban meminimalkan tingkat persediaan dan pemborosan produksi yang berlebihan.
Kaizen
Kaizen adalah istilah Jepang yang dapat diterjemahkan sebagai "Berubah untuk Kebaikan." Ini adalah proses terus-menerus membuat peningkatan bertahap, seringkali setiap hari, dalam proses dengan meminta perspektif karyawan tingkat lini untuk memanfaatkan kreativitas dan kecerdikan mereka. Kaizen dapat dilakukan secara langsung di lantai produksi saat peluang diidentifikasi, atau di acara ruang konferensi untuk peluang lintas fungsi. Tim Kaizen akan sering menggunakan siklus PDCA.
Pemeriksaan Kesalahan (Poka-Yoke)
Salah satu cara untuk menghilangkan pemborosan adalah dengan merancang proses dan alat dengan cara yang tidak memungkinkan untuk menyelesaikan tugas secara tidak benar. Pikirkan steker listrik tiga cabang standar AS. Karena dua fitur persegi panjang paralel dan satu putaran satu offset di antaranya, tidak mungkin untuk mencolokkannya ke stopkontak secara tidak benar. Ini hanya cocok satu cara. Dengan memastikan bahwa tugas tidak dapat dilakukan dengan tidak benar, kualitas dibangun dan pemborosan dihilangkan di stasiun kerja tertentu, serta di stasiun kerja mana pun nanti dalam proses di mana dampak cacat akan diperbesar.
Pekerjaan Standar
Dalam lean, langkah-langkah untuk menyelesaikan tugas aktivitas tertentu dikodifikasikan ke dalam pekerjaan standar. Pekerjaan Standar pada dasarnya adalah dokumentasi metode yang paling dikenal saat ini untuk menyelesaikan suatu tugas. "Terkenal" karena, dalam sistem perbaikan berkelanjutan, pekerja selalu waspada untuk cara yang lebih baik dalam melakukan pekerjaan mereka. Setiap perbaikan dimasukkan ke dalam dokumentasi kerja standar, dan semua pekerja kemudian dilatih tentang metode terbaru.
Untuk informasi lebih lanjut tentang Lean dan Six Sigma, lihat seri ketiga kami, “Prinsip dan Alat Six Sigma”, segera hadir .
Siapa Kami Di CMTC
CMTC menawarkan bantuan teknis, pengembangan tenaga kerja, dan layanan konsultasi kepada produsen kecil dan menengah (SMM) di seluruh California untuk membantu SMM meningkatkan produktivitas dan daya saing global mereka.
Untuk informasi lebih lanjut tentang CMTC, kunjungi situs web kami di www.cmtc.com atau hubungi kami di 310-263- 3060.
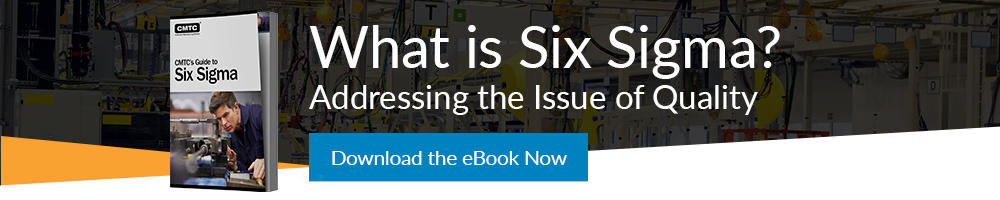