Dirgantara dan Pertahanan Dalam Fokus:Komponen Landing Gear
Sebagai Bagian 3 dalam seri kami tentang manufaktur kedirgantaraan, kami mencermati manufaktur komponen landing gear dengan memperhatikan pengalaman pembuat perkakas bekerja dengan beberapa produsen dan subkontraktor kedirgantaraan terbesar di industri.
Sejauh tahun ini, kami telah mendalami pembuatan sayap pesawat dan komponen mesin di kedirgantaraan dan pertahanan. Sekarang kita akan mendalami komponen roda pendaratan.
Sebagai salah satu bagian pesawat yang paling kritis, sistem roda pendarat menanggung beban berat. Secara harfiah, semua berat pesawat, jet tempur, atau helikopter didukung oleh roda pendarat selama taksi, pendaratan, dan lepas landas. Dan tergantung di mana pesawat itu mendarat, seperti misalnya kapal induk di tengah Samudra Pasifik, bahan yang membentuk roda pendarat bisa berbeda.
“Roda pendaratan yang dapat ditarik yang sekarang biasa digunakan pada pesawat komersial dan militer pertama kali dikembangkan untuk pesawat Triad Glenn Curtiss pada tahun 1911,” tulis National Air and Space Museum dalam sebuah postingan blog.
Roda pendarat pesawat mengontrol cara menanganinya di darat, tetapi juga cara pesawat menangani di langit, karena hal itu memengaruhi area lain termasuk bobot, performa, dan keandalan.
Kami berbicara dengan tiga produsen perkakas terkemuka di industri untuk perspektif tentang tantangan material dan nuansa pemotongan logam—dan mendiskusikan contoh dunia nyata di mana perkakas dan permesinan membuat perbedaan bagi pembuat dirgantara.
Material yang Digunakan dalam Komponen Landing Gear Saat Ini
Terutama, pemasok perkakas mengatakan bahwa mereka melihat dua jenis material utama dalam komponen besar roda pendarat saat ini yang mencakup 300M, baja paduan rendah yang sangat keras, atau Ti-5553, paduan titanium, yang dikenal karena kekuatan dan kemampuan mengeras.
Pada pesawat komersial, Boeing dan Airbus masing-masing menggunakan kedua bahan ini, tetapi itu tergantung pada persyaratan beban model pesawat, kata Scott Causey, seorang insinyur aplikasi untuk Seco Tools.
Sebagian besar jenis material ini digunakan pada berbagai komponen roda pendarat ini termasuk—balok truk, penyangga, tautan torsi, dan penyangga, yang terkadang juga disebut “silinder utama”.
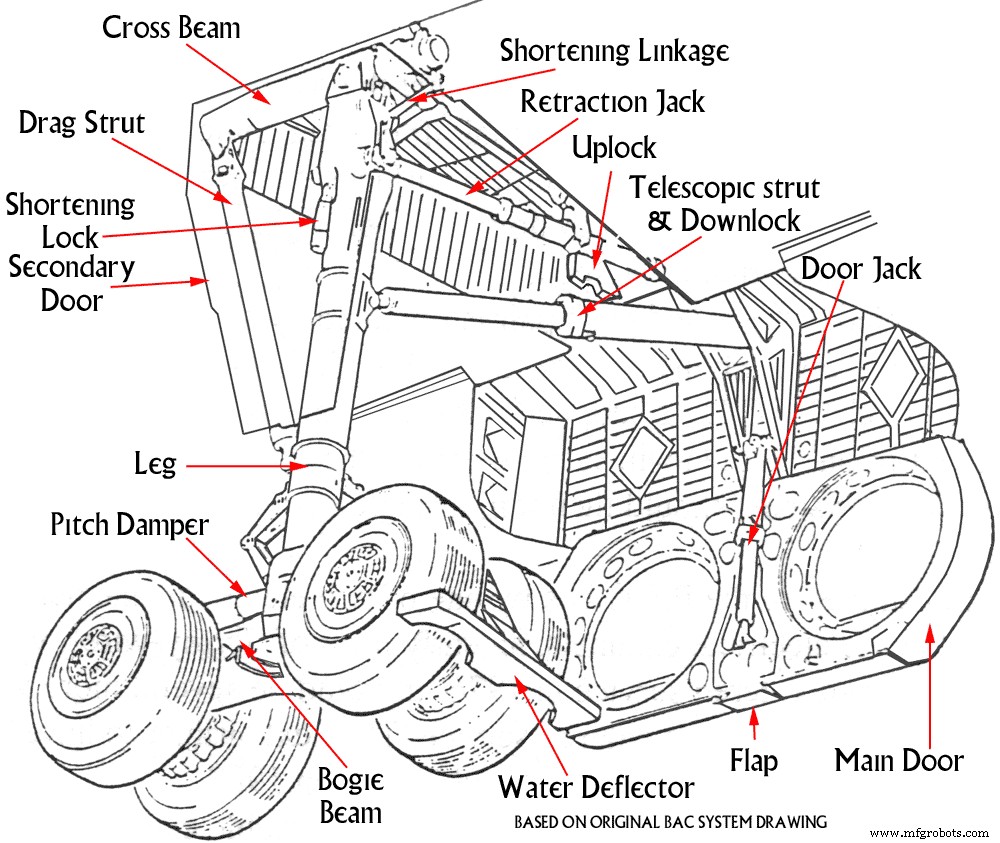
Sumber:Concordest.com
Tetapi ada bahan lain yang digunakan dalam komponen lain dari roda pendarat, termasuk aluminium, baja paduan 4340 dan beberapa titanium, yang sering ditemukan pada braket roda pendarat, penyangga dan tautan, Causey menjelaskan.
Dan ada komponen lain yang lebih kecil di roda pendarat, termasuk flensa, kantong, lubang reamed, lubang bor, dan banyak titik koneksi, kata Mark Francis, staf insinyur untuk kedirgantaraan dan pertahanan di Kennametal. Misalnya, sebuah lubang bisa berdiameter 8 hingga 10 inci dan dalamnya 36 inci. Anda memerlukan alat dan proses khusus untuk menyelesaikan tugas.
“Material lain yang kami lihat untuk kasus penggunaan kapal induk yang sangat spesifik adalah penggunaan AerMet 100—baja berkekuatan tinggi yang sulit dikerjakan dengan mesin” kata Francis. “Ini dapat menahan beban berdampak tinggi—bayangkan ketahanan patah dan ketangguhan yang diperlukan untuk pendaratan kapal induk di landasan pendek kapal induk—serta sangat tahan korosi dengan garam dan air di laut.”
AerMet 100 digunakan hampir secara eksklusif pada jet tempur yang menuju kapal induk.
Apakah Anda perlu menjawab pertanyaan teknis? Tanyakan kepada Tim Teknologi Pengerjaan Logam MSC di forum.
Area Komponen Landing Gear yang Paling Menantang untuk Mesin dan Manufaktur
Seperti yang Anda bayangkan, komponen terbesar dari roda pendarat bisa lambat untuk dikerjakan—yaitu karena ukurannya. Bagian seperti silinder utama dan balok truk, yang biasa disebut sebagai “balok gandar”, dapat memanjang hingga sekitar 25 kaki tingginya.
Bagian sulit lainnya termasuk penggeser, atau “silinder bagian dalam”, kata Causey.
“Bore ID pada bagian ini dapat berjalan hingga 70 inci,” kata Atul Sharma, seorang insinyur aplikasi kedirgantaraan untuk Seco Tools. “Mereka sangat besar dan panjang. Dan toleransi bisa sulit dipegang saat memotong. Menjepit bisa menjadi tantangan.”
Semua pembuat perkakas yang kami ajak bicara menjelaskan dengan sangat jelas bahwa bagian-bagian besar ini sering lambat untuk dikerjakan. Ada asumsi bahwa Anda dapat mengerjakan 300 juta material dengan permukaan kaki yang tinggi per menit. Namun kenyataannya, potongan besar ini terlalu berat dan besar—dan membutuhkan pemasangan khusus agar komponen tidak bergetar dan mendapatkan hasil maksimal dari alat pemotong.
Namun dibandingkan dengan banyak bahan nikel, Waspalloy, dan Rene, bahan baja dan titanium ini tidak terlalu sulit, jelas Bill Durow, manajer kantor proyek teknik global untuk kedirgantaraan, di Sandvik Coromant.
“Dalam banyak kasus, ini adalah skala komponen. Mereka sangat besar, ”kata Durow. “Dan tidak ada yang seragam. Mereka sering memiliki bentuk yang aneh, jadi Anda tidak bisa membuangnya begitu saja di mesin bubut. Seringkali, pembuat kedirgantaraan menggunakan bore mill besar atau mesin gantry besar, yang membutuhkan banyak waktu.”
Lihat sistem roda pendarat mulai dari desain hingga manufaktur dan bagian jadi. Sumber:Sistem Pendaratan Safran
Pembuat perkakas melihat tren beberapa pabrikan kedirgantaraan yang beralih dari mesin gantry dan bore milling ke pemesinan sumbu-B dan menggunakan aplikasi turn mill untuk pengaturan yang lebih sedikit dan pemasangan yang lebih sedikit—dan melakukan pembuatan profil 4-ke-5-sumbu di sekitar suku cadang.
Tetapi metode yang lebih baru ini membutuhkan lebih banyak pemrograman—dan pemikiran baru tentang geometri pemotongan untuk membantu meningkatkan efisiensi dalam produksi roda pendarat. Bukan hal yang aneh jika landing gear membutuhkan waktu berbulan-bulan untuk diselesaikan dari awal hingga selesai.
Apa yang baru di luar angkasa? Inovasi dalam manufaktur aditif. Baca “ Evolusi Menakjubkan Pencetakan 3D di Ruang Angkasa dan Pertahanan .”
Membuat Mesin Pendarat di Dunia Nyata
Berikut adalah tiga contoh suku cadang dan komponen landing gear dunia nyata yang dibuat di mana perkakas yang tepat atau pendekatan baru memberikan dampak.
Tautan Torsi
Tantangan: Seorang pelanggan Seco Tool berjuang dengan torsion link—area landing gear yang menyatukan silinder dalam dan luar—sambil memotong material titanium 10-2-3. Waktu siklus adalah 60 jam dengan enam pengaturan berbeda. Pelanggan selalu terlambat dalam pengiriman suku cadang dan hampir kehilangan kontraknya dengan OEM.
Solusi: Seco Tools bekerja dengan pelanggan dan mitra untuk menangani pemesinan pelanggan melalui kemitraan dengan DMG Mori. Seco Tools membantu menemukan pendekatan baru mulai dari awal dengan gambar, model, dan perkakas.
Hasil: Pelanggan mengurangi pembuatan suku cadang dan pengaturan perkakas dari enam menjadi dua—dan mengurangi waktu siklus dari 60 jam menjadi 23 jam, atau 62 persen. Ini meningkatkan produksi dan memungkinkan pengiriman suku cadang tepat waktu. Pada akhirnya, solusi tersebut memungkinkan produsen kedirgantaraan untuk mempertahankan kontraknya.
Perkakas Dirancang untuk Material
Tantangan: Komponen roda pendarat seberat 400 pon yang terbuat dari Ti-5553 terbakar melalui alat untuk pelanggan Kennametal. Pelanggan memprogram perubahan alat baru setiap 30 menit. Setelah selesai, bagian ini sekitar 210 pound. Tapi bahan titanium ini memiliki casing alfa yang sulit ditembus.
Solusi: Kennametal menggunakan pemotong frais dengan desain heliks dengan sisipan dan bor 8 sisi yang dirancang khusus untuk kelas titanium yang spesifik dan tangguh ini.
Hasil: Waktu kasar berubah dari 25 jam menjadi 15 jam. Waktu siklus berkurang hingga 40 persen. Masa pakai alat ditingkatkan hingga 300 persen:Alat sekarang bertahan 120 menit sebelum alat canggih baru diperlukan.
Pendekatan Baru Menggunakan Alat yang Ada
Tantangan: Suku cadang untuk komponen roda pendarat mendapatkan banyak 5-sumbu dan pergerakan pahat karena pahat yang sudah ada mengambil bagian belakang sisipan—dan memutuskan sekrup karena pemotong memiliki kunci mata untuk menjaganya tetap kencang. Pelanggan kedirgantaraan harus terlalu sering menghentikan produksinya, karena suku cadang membutuhkan terlalu banyak intervensi manual dan pengasuhan anak. Segalanya berjalan terlalu lambat.
Solusi: Sandvik Coromant menerapkan alat yang awalnya dirancang untuk pemesinan blade dalam pemesinan horizontal dan menerapkannya pada aplikasi vertikal ini—dan menyarankan ramping atau “menyembuhkan” alat sehingga dinaikkan sedikit, dua hingga tiga derajat, untuk menghindari pemotongan kembali alat . Itu juga menggunakan teknik round bossing dan performanya sangat baik.
Hasil: Keamanan proses. Gerakan memasukkan hilang. Sekrup insert tidak rusak lagi. Dan pelanggan dapat berhenti mengasuh proses dan pindah ke lingkungan produksi yang lebih “padam”. Operator dapat bekerja pada beberapa mesin secara bersamaan.
Bagaimana Anda menangani waktu siklus yang menyusut dalam manufaktur kedirgantaraan Anda? Bicaralah dengan rekan Anda di forum pengerjaan logam . [pendaftaran diperlukan]