Teknologi untuk Peningkatan dalam proses Coking di Oven Coke Produk Samping
Teknologi untuk Peningkatan Proses Coking di Oven Coke Produk Sampingan
Batubara kokas diubah menjadi kokas dalam produk sampingan baterai oven kokas. Proses kokas terdiri dari memanaskan campuran batu bara kokas yang dihancurkan tanpa adanya udara untuk mengusir senyawa volatil. Kokas yang dihasilkan adalah bahan karbon keras, tetapi berpori yang digunakan untuk mereduksi bahan bantalan besi dalam tanur tinggi. Oven kokas produk sampingan juga memulihkan bahan kimia yang mudah menguap dalam bentuk gas oven kokas, amonium sulfat, ter, dan minyak. Dalam tiga sampai empat dekade terakhir beberapa teknologi telah dikembangkan yang tidak hanya menghasilkan (i) penggunaan batubara inferior dalam campuran batubara, (ii) peningkatan besar dalam proses kokas, (iii) peningkatan kualitas metalurgi yang dihasilkan kokas, (iv) peningkatan hasil, (v) pemulihan energi limbah, dan (vi) peningkatan kontrol emisi pada baterai. Beberapa teknologi utama dalam hal ini diberikan di bawah ini.
Penghancuran batubara secara selektif
Batubara merupakan material yang heterogen. Berbagai komponennya memiliki kekerasan yang berbeda, sehingga selama kerusakan dengan cara mekanis apakah kerusakan yang tak terhindarkan dalam penambangan atau penghancuran selama persiapan batubara untuk kokas, komponen yang lebih lemah cenderung terkonsentrasi di fraksi halus dan yang lainnya di fraksi kasar. Berbagai fraksi ini diharapkan memiliki sifat kokas yang berbeda. Hal ini memicu konsep penghancuran selektif yang bertujuan untuk mengontrol tingkat penghancuran berbagai konstituen campuran batubara. Teknologi ini berguna ketika batubara secara petrografi heterogen.
Teknologi ini secara teoritis merupakan teknologi yang baik dan bertujuan untuk mengontrol tingkat penghancuran berbagai konstituen batubara. Hal ini bertujuan untuk meningkatkan homogenitas komponen reaktif dan inert dalam batubara. Komponen reaktif batubara terutama vitrinit dan merupakan konstituen paling lembut sedangkan bahan mineral batubara adalah komponen yang paling sulit. Dalam unit penghancur batubara konvensional, di mana seluruh batubara dihancurkan bersama-sama, vitrinit dihancurkan ke ukuran yang relatif lebih halus dibandingkan dengan konstituen bahan mineral. Untuk menghasilkan kokas dengan kualitas lebih tinggi, diinginkan untuk menghancurkan bahan mineral lebih halus daripada komponen vitrinit dari batu bara sehingga selama proses kokas, ketika muatan batu bara melunak, bahan mineral diasimilasi lebih baik, yang mengarah pada peningkatan kekuatan. Ini biasanya dilakukan dengan menghancurkan setiap jenis batubara secara terpisah.
Penghancuran batubara selektif terdiri dari bak penampung, stasiun penghancur, stasiun pencampuran, pencampur batubara dan mengarahkan batubara ke menara batubara di baterai oven kokas. Batubara diangkut oleh konveyor sabuk dari tempat penyimpanan batubara ke tempat penampung, yang menahan aliran massa tinggi dari tempat penyimpanan batubara terhadap aliran massa yang berkurang ke stasiun penghancur. Di stasiun penghancur, batu bara dihancurkan jenis demi jenis dengan pengaturan penghancur individual. Setelah proses penghancuran, batubara yang dihancurkan diangkut ke stasiun pencampuran. Setiap jenis batubara disimpan di tempat pencampur terpisah. Disesuaikan dengan jumlah jenis batubara dan persentasenya relatif terhadap komposisi campuran batubara, jumlah dan ukuran bin yang berbeda dirancang.
Di hilir tempat pencampur, berbagai jenis batubara diumpankan ke konveyor keluar oleh pengumpan penimbangan sabuk. Dari blending station, batubara diangkut ke mixer. Aditif, seperti minyak, air, dan debu kokas dll., ditambahkan ke batubara di saluran transfer hulu sebelum mixer. Dalam mixer, campuran batubara dihomogenkan. Setelah proses pencampuran, batubara diumpankan ke menara batubara. Pengukuran kadar air batubara dilakukan di bagian hulu di ujung konveyor sabuk ke menara batubara. Konsep dasar untuk penghancuran selektif batubara ditunjukkan pada Gambar 1.
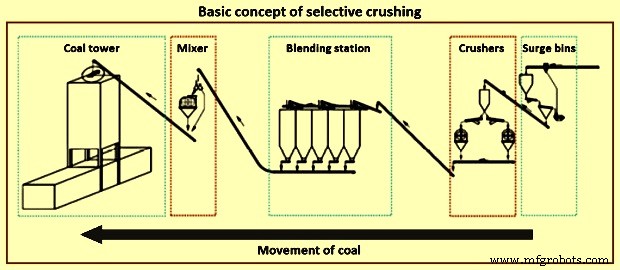
Gbr 1 Konsep dasar penghancuran selektif
Dalam konsep penghancuran batu bara selektif, penyesuaian penghancur batu bara diubah secara otomatis mengikuti pra-pengaturan untuk setiap jenis batu bara. Hal ini memberikan kemungkinan, untuk mencapai ukuran butir optimal dari setiap jenis batubara dengan mempertimbangkan komposisi campuran batubara dan untuk bereaksi terhadap perubahan sifat batubara setiap saat. Misalnya, jenis batubara dengan kemampuan kokas yang lemah dihancurkan ke ukuran butir rata-rata yang lebih besar untuk memastikan permukaan spesifik yang lebih rendah. Batubara kokas lunak dengan sejumlah besar inert dapat digiling ke ukuran butir rata-rata yang lebih rendah dalam kaitannya dengan komposisi pencampuran batubara. Campuran batu bara lebih homogen daripada dalam kasus penghancuran campuran. Kandungan inert dan reaktif batubara terdistribusi secara merata dalam campuran batubara dan tidak terkonsentrasi pada fraksi butir tertentu. Hal ini menghasilkan titik-titik yang kurang rapuh dalam kokas dan menghindari perbedaan dalam hal penyusutan oleh inert yang didistribusikan secara tidak homogen.
Pra-penyaringan sebelum penghancur
Langkah proses tambahan yang direkomendasikan adalah pra-penyaringan batubara sebelum disalurkan ke stasiun penghancur batubara. Sebagian besar jenis batubara mentah memiliki 30% sampai 50% dari ukuran butir kurang dari 3 mm, yang tidak perlu dihancurkan lebih lanjut. Menghapus ukuran butir ini dari batu bara sebelum penghancur memiliki efek positif dan membantu mengurangi kapasitas penghancur secara signifikan. Selanjutnya, porsi partikel halus dapat dikontrol dengan lebih efektif.
Pemisahan batubara halus dapat dipengaruhi oleh pengklasifikasi pneumatik atau dengan layar flip-flop. Investasi tambahan untuk peralatan ini sebagian dikompensasikan dengan pengurangan kapasitas penghancur batubara.
Dengan pengurangan partikel halus, ukuran butir rata-rata campuran batubara berkurang secara efektif, meningkatkan kerapatan curah dengan efek positif pada produktivitas oven kokas. Selanjutnya, sifat kokas dari campuran batubara ditingkatkan dengan mengurangi permukaan spesifik. Hal ini memungkinkan penggunaan persentase yang lebih tinggi dari batubara kokas kualitas rendah dalam campuran.
Penambahan minyak
Dimungkinkan untuk menyesuaikan densitas curah batubara dengan penambahan minyak dalam jumlah yang relatif kecil dari 0,1% hingga 0,5%. Ini menunjukkan efek positif pada sifat kokas. Dalam kasus penambahan minyak untuk mengkompensasi pengurangan densitas curah karena peningkatan persentase partikel yang lebih kecil dari 0,5 mm, telah ditemukan bahwa tekanan gas batubara tidak meningkat secara bersamaan. Dalam kasus distribusi ukuran partikel konstan, tekanan gas batubara bahkan sedikit menurun karena penambahan minyak. Selain itu, karakteristik aliran yang lebih baik di dalam ruang selama pengisian telah dikonfirmasi dalam banyak uji coba oleh operator baterai oven kokas. Oleh karena itu, distribusi batubara yang lebih merata di dalam chamber dengan jalur batubara yang konstan dapat dicapai dan ada pengurangan carryover. Hal ini menyebabkan lebih sedikit batubara yang tumpah dan karbonisasi batubara yang seragam di seluruh ruang oven kokas. Selain itu, konsumsi panas juga dioptimalkan dan panas berlebih dari ruang pengumpulan gas di atas batubara dapat dihindari. Ini mengurangi pembentukan karbon dari reaksi perengkahan yang terjadi pada suhu di atas 850 derajat C.
Kontrol kelembapan batubara
Pengendalian kadar air batubara dilakukan dengan cara mengeringkan batubara sampai tingkat kelembaban yang konstan. Ini sekarang menjadi fitur umum. Tingkat kelembapan yang konstan menyediakan pengoperasian yang stabil dari baterai oven kokas. Pengeringan dilakukan dengan cara memutar tube dryer atau fluidized bed dryer yang disusun di belakang blending station. Kontrol kelembaban batubara menggunakan panas buangan dari gas oven kokas untuk mengeringkan batubara yang digunakan untuk pembuatan kokas.
Kadar air campuran batubara untuk pengisian dalam oven kokas biasanya bervariasi dalam kisaran 8% sampai 10%. Pengeringan campuran batubara mengurangi kadar air dalam campuran batubara ke tingkat sekitar 6%. Hal ini pada gilirannya mengurangi konsumsi bahan bakar dalam oven kokas. Kokas dikeringkan menggunakan kandungan panas gas oven kokas, uap bertekanan rendah, atau sumber panas limbah lainnya. Bagan alir skema kontrol kelembaban batubara diberikan pada Gambar 2.
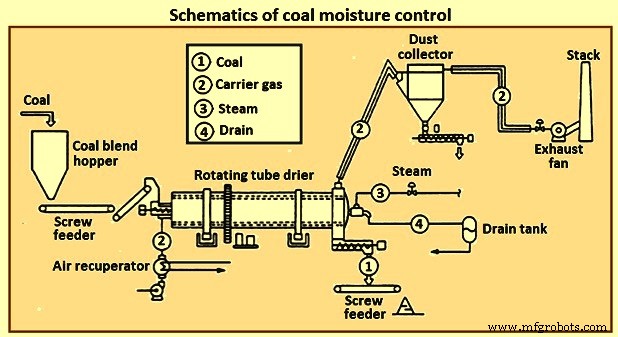
Gbr 2 Skema kontrol kelembapan batubara
Manfaat pengendalian kadar air batubara adalah (i) penghematan bahan bakar sekitar 71.700 kkal/ton, (ii) peningkatan kualitas kokas sebesar 1,7%, (iii) peningkatan produksi kokas sekitar 10%, (iv) pengurangan dalam periode kokas, dan (v) penurunan polusi air.
Alternatif lain yang menguntungkan, tetapi belum direalisasikan, adalah kombinasi pengklasifikasi pneumatik untuk menghilangkan butiran halus batubara dan mengeringkan batubara dengan aliran udara di depan stasiun penghancur. Sistem seperti itu menggabungkan keunggulan pra-penyaringan dan pengeringan awal dalam satu stasiun proses. Peralatan dasar yang dibutuhkan untuk proses tersebut tersedia di pasar, tetapi aplikasi gabungannya belum diadopsi secara praktis di pabrik pengolahan batubara.
Stempel pengisian batu bara
Meluasnya penggunaan injeksi batubara bubuk di tanur tinggi memiliki persyaratan kualitas kokas yang lebih tinggi. Lebih lanjut, karena batu bara kokas menjadi lebih mahal, dengan harga yang fluktuatif dan ketersediaan relatif, pengenalan batu bara yang lebih murah dalam campuran batu bara menjadi kebutuhan. Hal ini menyebabkan penggunaan cap charging batubara yang pada awalnya dikembangkan untuk penggunaan batubara kokas buruk yang mudah menguap tinggi.
Teknik persiapan muatan terdiri dari menyiapkan kue dengan campuran batubara dalam kotak logam, kemudian mengisinya di oven kokas. Kepadatan muatan yang lebih tinggi menyiratkan kualitas kokas yang lebih baik jika dibandingkan dengan pengisian konvensional. Jadi, tergantung situasinya, kualitas kokas yang lebih baik dapat dicapai, atau batu bara kokas yang lemah dapat dimasukkan ke dalam campuran.
Stamping batubara meningkatkan densitas muatan sebesar 30% sampai 35% menjadi sekitar 1.150 kg/cum. Penghancuran batubara hingga lebih dari 90% di bawah ukuran -3 mm dan 40% hingga 50% di bawah – ukuran 0,5 mm diperlukan untuk kue yang stabil. Dengan pengisian cap, batubara peringkat rendah, kokas lemah, dan batubara volatil tinggi dapat digunakan hingga sekitar 20%, tetapi karena muatan batubara dipadatkan hingga densitas curah tinggi, dapat terjadi masalah peningkatan tekanan dinding. Untuk memastikan bahwa dinding oven tahan api tidak rusak, campuran batubara yang digunakan harus dipilih secara hati-hati dengan keseimbangan optimal antara batubara volatil tinggi dan rendah.
Proses pengisian stempel telah digunakan sejak awal abad ke-20. Teknologi ini lahir di Silesia dan Polandia lebih dari 100 tahun yang lalu. Di pabrik sebelumnya, stasiun stamping terletak di ruang antara dua baterai. Jerami digunakan sebagai bantuan untuk kekuatan kue. Sedotan digunakan sebagai pengikat dan charger mobil / ram yang dirancang khusus untuk memuat muatan ke dalam oven dari belakang. Coke yang dibuat dengan proses pengisian cap memiliki variasi yang lebih padat dan lebih besar daripada yang dibuat dengan metode lain, sehingga membuatnya lebih cocok untuk pembuatan besi di pengecoran di mana kekuatan merupakan faktor penting. Keuntungan lain yang dicatat adalah bahwa rentang batubara yang jauh lebih besar dapat digunakan dengan batas volatilitas (tinggi) dan sifat kokas yang jauh lebih tinggi.
Pengembangan proses modern berlangsung di pabrik kokas Fuerstenhausen, Volklingen, Jerman, yang berfokus pada penggunaan batubara volatil tinggi. Pada tahun 1978, setelah penelitian dan pengembangan intensif, kue pertama setinggi 6 meter diproduksi, mengatasi hambatan untuk implantasi ekonomis teknologi ini. Pabrik pertama dari dimensi ini dimulai pada tahun 1984 di Jerman. Baik oven slot konvensional maupun oven non-pemulihan/pemulihan panas menggunakan teknologi ini.
Teknologi ini pada dasarnya melibatkan pembentukan kue batu bara yang stabil dengan batu bara yang dihancurkan secara halus dengan stamping mekanis di luar oven untuk karbonisasi. Dalam pengisian cap, densitas curah batubara yang diisikan dalam oven ditingkatkan dengan secara fisik memasukkan muatan ke dalam kue. Kue yang ukurannya hampir mirip dengan oven itu kemudian dimasukkan ke dalam oven. Stamping dilakukan dalam mesin dorong cum pengisian cum stamping yang menggunakan palu jatuh untuk stamping.
Peralatan stamping dapat ditempatkan di gedung yang dibangun untuk tujuan ini atau di mesin pengisian / dorong. Proses stamping biasanya terdiri dari memasukkan campuran batubara yang sebelumnya digiling pada ukuran tertentu, di dalam kotak baja, sebagai lapisan berturut-turut yang ditabrak secara mekanis. Itu dapat diterapkan secara vertikal atau horizontal. Selain itu, getaran dapat diterapkan untuk memfasilitasi akomodasi partikel. Kotak horizontal diisi dengan campuran batubara, dengan distribusi ukuran butir dan kadar air yang ditentukan, dalam tiga lapisan yang sama. Pemadatan dan getaran diterapkan, melalui sejumlah pelat palu jatuh yang menutupi seluruh permukaan kue, selama dua menit untuk setiap lapisan, untuk mendukung transfer dari kotak ke oven. Dikatakan bahwa dalam hal ini ukuran butir halus tidak diperlukan seperti pada stamping konvensional.
Dua aspek harus diperhitungkan. Ini adalah (i) densifikasi, dan (ii) sifat mekanik. Densifikasi diperlukan untuk proses kokas. Semakin padat kue, semakin baik kualitas kokas, dengan mempertimbangkan kekuatan mekanik dingin dan perilaku pada suhu tinggi. Sifat mekanik harus cukup untuk mendukung pengangkutan kue untuk diisi ke dalam oven kokas.
Ketika densifikasi dimulai, partikel batubara menghasilkan di bawah tekanan yang diterapkan oleh mesin stamping, mengisi rongga interstisial dengan partikel yang lebih kecil. Penataan ulang partikel didukung oleh kelembaban permukaan, yang mengurangi gesekan internal. Dengan regangan lebih lanjut, terjadi deformasi plastis-elastik partikel yang sebagian mengakibatkan kerusakan partikel dan pengisian pori-pori kecil dengan fragmen. Sementara volume pori menurun, saturasi pori dengan naiknya air menyebabkan efek redaman.
Selain pengaruh air kapiler terhadap proses densifikasi itu sendiri, sifat mekanik massa yang dipadatkan juga ditentukan oleh air permukaan karena berfungsi sebagai bahan pengikat dalam pembentukan gaya adhesi. Dalam sistematika proses rekayasa kue cap dapat disebut sebagai gumpalan basah yang dicirikan oleh gaya rekat yang dihasilkan dari jembatan cair di dalam sistem pori kapiler.
Kepadatan cake ditujukan pada 1.100 kg/cum 1.150 kg/cum dan tergantung pada kelembaban dan ukuran butir dari campuran batubara dan energi pemadatan yang diterapkan. Sifat mekanik batubara juga berpengaruh. Kepadatan basah meningkat terus menerus ketika kelembaban meningkat dari 6% menjadi 13%. Untuk kelembaban yang lebih tinggi, energi yang diterapkan digunakan untuk mengeluarkan air dari kue. Biasanya dua variabel penting dari campuran batubara adalah kelembaban dan ukuran butir untuk mencapai kekuatan yang dibutuhkan untuk pengangkutan kue dan pengisian. Variabel operasi adalah energi pemadatan yang diterapkan dan sifat mekanik yang relevan adalah kuat tekan dan kuat geser.
Untuk pengisian kue ke oven kokas, teknik yang berbeda digunakan tergantung pada desain oven kokas (oven slot vertikal atau oven kokas non-pemulihan/pemulihan panas horizontal. Untuk oven kokas vertikal, pengisian kue dilakukan melalui pendorong pintu samping. Prosedur ini menyebabkan emisi tinggi. Untuk mengurangi emisi tersebut, beberapa sistem telah dicoba selama pengisian bungkil batubara, terutama melalui penggunaan bingkai segel. Namun, sistem kontrol emisi hanya mengurangi sebagian emisi tanpa menghilangkannya sama sekali. Solusi yang diadopsi baru-baru ini dalam baterai baru untuk mengurangi emisi selama proses pengisian oven adalah dengan menciptakan depresi yang kuat (minus 400 Pa) di saluran utama pengumpul selama fase pengisian. diatur ke tekanan negatif nominal. Peralihan ke titik setel depresi yang lebih tinggi dilakukan sebelum memulai proses mendorong kue.
Biasanya spesifikasi campuran batubara mencakup 25% sampai 32% bahan volatil (basis kering bebas abu) dan indeks pengembangan bebas minimal 3. Namun, spesifikasi campuran batubara berubah dari pabrik ke pabrik, tergantung pada ketersediaan dan biaya batubara. Di beberapa pabrik, campuran batu bara mencakup kokas minyak bumi dan kokas halus.
Keuntungan dari pengisian cap adalah (i) peningkatan throughput dari 8% menjadi 10% karena densitas curah yang lebih tinggi, dan (ii) peningkatan kekuatan kokas (nilai mikum dan CSR) karena pengemasan yang lebih dekat dari partikel batubara individu selama karbonisasi. kokas yang dihasilkan lebih padat, lebih kecil, dan ukurannya lebih seragam.
Oven kokas isi atas ruang besar
Oven kokas ruang besar tingginya 7,6 m. Kompleks baterai oven kokas ruang besar mewakili keadaan seni dan teknologi terkonsolidasi untuk pabrik pembuatan kokas. Tab 1 menunjukkan tabel perbandingan antara baterai oven kokas isi atas ruang besar dengan baterai oven kokas setinggi 6,25 m berdasarkan produksi kokas sebesar 1,9 juta ton produksi tahunan.
Tab 1 Perbandingan oven kokas ruang besar dengan oven kokas 6,25 m |
Subjek | Satuan | Oven kokas ruang besar | oven kokas setinggi 6,25 m |
Produksi tahunan | ton | 1.900.000 | 1.900.000 |
Tinggi oven | m | 7.6 | 6.25 |
Lebar oven | mm | 550 | 410 |
Volume oven | Sum | Sekitar 79 | Sekitar 40 |
Jumlah baterai | Tidak. | 2 | 4 |
Jumlah oven | Tidak. | 118 | 160 |
Mendorong per hari | Tidak. | 116 | 226 |
Pintu oven kokas | Tidak. | 236 | 320 |
Tutup pengisi daya | Tidak. | 472 | 640 |
Tutup pipa berdiri | Tidak. | 118 | 160 |
Set mesin operasi | Tidak. | 31 | 2 |
Perbandingan masa pakai baterai |
Waktu pembuatan kokas | jam | 24.5 | 17 |
Dorongan per hari per oven | Tidak. | 0,98 | 1,41 |
Dorongan per oven per tahun | Tidak. | 358 | 515 |
Masa pakai yang diharapkan per baterai (16.000 dorongan per oven) | Tahun | 44.6 | 31 |
Pengurangan jumlah dorongan per hari dari baterai oven kokas ruang besar memungkinkan hanya memiliki 1 set mesin yang beroperasi dalam operasi alih-alih 2 set untuk baterai oven kokas setinggi 6,25 m, dengan keuntungan dalam hal (i) biaya investasi oven kokas mesin, dan (ii) biaya operasi. Tab 1 juga menunjukkan bahwa dengan mempertimbangkan jumlah rata-rata dorongan yang dapat dilakukan setiap oven selama masa pakainya, hasilnya adalah masa pakai yang diharapkan meningkat secara signifikan.
Setiap dinding pemanas terdiri dari 38 cerobong pemanas yang memiliki konfigurasi yang terdiri dari (i) cerobong asap kembar, dengan sirkulasi ulang sebagian gas buang untuk produksi NOx rendah, (ii) tiga tingkat saluran masuk udara terhuyung-huyung untuk meminimalkan pembentukan dan menjaga NOx distribusi suhu vertikal yang tepat, dan (iii) laju aliran gas dan udara campuran yang mudah disesuaikan dengan menggunakan pelat pengatur yang ditempatkan di bagian bawah level regenerator.
Sistem aspirasi cairan amonia bertekanan tinggi
Sistem aspirasi cairan amoniak bertekanan tinggi efektif untuk mengendalikan emisi pengisian dalam baterai oven kokas. Dalam sistem ini, cairan amoniak, yang merupakan produk sampingan, diberi tekanan hingga sekitar 35 kg/cm2 hingga 40 kg/cm2 dan disuntikkan melalui nozel khusus yang disediakan di leher angsa pada saat pengisian. Ini menciptakan isapan yang cukup di dalam oven sehingga menahan polutan agar tidak dilepaskan ke atmosfer. Sistem ini terdiri dari pompa booster multitahap bertekanan tinggi, pekerjaan pipa yang kokoh, nozel semprot yang dirancang khusus, katup yang sesuai, dan instrumen kontrol. Sistem kontrol emisi ini menghasilkan penghematan dalam jumlah uap proses dan peningkatan hasil gas mentah.
Pendinginan Coke kering
Pendinginan kering dengan kokas merupakan alternatif dari pendinginan basah tradisional. Ini adalah proses hemat energi yang digunakan selama produksi kokas di baterai oven kokas. Pabrik pendinginan kering kokas juga disebut pabrik pendingin kering kokas. Dalam proses pendinginan basah kokas tradisional, kokas merah panas yang didorong dari oven kokas didinginkan dengan menyemprotkan air ke kokas panas. Air yang digunakan untuk pendinginan diuapkan dan dilepaskan ke atmosfer. Masalah dengan sistem konvensional ini adalah hilangnya energi ketika energi panas dari kokas merah panas diubah menjadi uap yang diuapkan dan dilepaskan tanpa digunakan. Kelemahan lain adalah bahwa proses pendinginan basah kokas juga menghasilkan debu kokas di udara, dan karenanya, proses ini dikaitkan dengan emisi karbon dioksida yang tinggi dan kehilangan energi panas.
Selama proses pendinginan kokas basah untuk pendinginan jalannya kokas oven, panas sensibel dari kokas panas dibuang ke atmosfer dan hilang. Selain itu, ada emisi yang terbawa udara (0,5 ton uap per ton kokas, yang sarat dengan fenol, sianida, sulfida, dan debu) dan sejumlah besar air (sekitar 0,6 cum per ton kokas) diperlukan untuk pendinginan basah. . Kontaminan dalam air juga dibuang ke lingkungan.
Di pabrik pendinginan kokas kering, kokas merah panas didinginkan dalam ruang pendingin baja berlapis tahan api yang dirancang khusus dengan media gas inert yang beredar saat ini di sirkuit tertutup yang terdiri dari ruang pendingin, ruang pengumpul debu, boiler panas limbah, siklon debu, kipas pabrik, perangkat bertiup dan saluran sirkulasi. Energi panas dari kokas merah panas diperoleh kembali di ketel limbah panas untuk digunakan sebagai uap, menghasilkan konservasi energi serta pengurangan emisi partikel kokas. Tab 2 menunjukkan perbandingan sifat khas dari kokas yang dihasilkan oleh kedua proses tersebut.
Tab 2 Perbandingan sifat khas dari kokas yang dihasilkan |
No. Sl. | Parameter | Satuan | Proses pendinginan basah kokas | Proses pendinginan kering kokas |
1 | Konten air | % | 2-5 | 0,1-0,3 |
2 | Konten abu | % | 11,35 | 11,39 |
3 | Komponen yang mudah menguap | % | 0,5 | 0,41 |
4 | Ukuran partikel rata-rata | mm | 65 | 55 |
5 | Kecepatan angin coke (setelah dipotong pada -15 mm) | % | 10 | 13 |
6 | Porositas | % | 49 | 48 |
7 | Indeks drum | % | 83,5 | 85 |
8 | Kekuatan kokas setelah reaksi (CSR) | % | 58 | 60 |
Kokas panas setelah didorong dibawa dari baterai oven kokas ke pabrik pendinginan kokas kering di ember bukaan bawah yang disimpan di mobil pendinginan. Ember ini diangkat di pabrik pendinginan kokas kering dengan alat pengangkat / pengisi daya ke bagian atas ruang pendinginan kokas kering dan kokas merah panas dibuang ke pra-ruang oleh perangkat pengisi daya. Kokas panas (suhu sekitar 1.000 derajat C hingga 1.100 derajat C) didinginkan di dalam ruangan oleh gas yang bersirkulasi. Di dalam ruangan, gas yang bersirkulasi bergerak berlawanan arah dengan gerakan kokas, yaitu gas yang bersirkulasi bergerak ke atas sementara kokas bergerak ke bawah oleh gravitasi.
Gas yang bersirkulasi di pabrik pendinginan kering coke yang terus berjalan adalah gas campuran yang terutama terdiri dari nitrogen bersama dengan sejumlah kecil karbon dioksida, karbon mono-oksida, dan hidrogen. Kokas panas, saat turun di dalam ruang, didinginkan hingga suhu yang kurang dari 200 derajat C oleh gas yang bersirkulasi yang dihembuskan dari zona bawah ruang pendingin dan dikeluarkan dari fasilitas pengosongan di bagian bawah ruang. Waktu berlalunya kokas melalui ruang adalah sekitar 5 jam hingga 6 jam.
Gas sirkulasi suhu tinggi (sekitar 800 derajat C hingga 850 derajat C) setelah proses pertukaran panas di ruang pendingin melewati penangkap debu primer dan disuplai ke boiler. Sirkulasi gas setelah proses pertukaran panas di boiler didinginkan hingga sekitar 180 derajat C. Steam yang dihasilkan di boiler digunakan baik sebagai steam proses untuk keperluan umum, atau diubah menjadi steam bertekanan tinggi super panas untuk pembangkitan listrik. daya melalui generator turbin.
Gas yang bersirkulasi melewati penangkap debu sekunder ke dalam peniup sirkulasi gas, yang dengannya tekanannya ditingkatkan, dan komposisinya dikoreksi dengan penambahan gas nitrogen dan kemudian gas yang bersirkulasi disuntikkan di bagian bawah ruang pendinginan kering kokas. Jika perlu, sub-penghemat dipasang untuk menurunkan suhu sirkulasi gas menjadi sekitar 130 derajat C, meningkatkan efisiensi pendinginan ruang pendingin.
Ada beberapa fasilitas tambahan yang meliputi alat pemutus untuk mengeluarkan kokas dari chamber, sistem penghilang debu untuk menghilangkan debu dalam gas inert yang bersirkulasi, dan penangkap debu sekunder yang dipasang sebelum blower sirkulasi. Flowsheet dari proses pendinginan coke kering ditunjukkan pada Gambar 3.
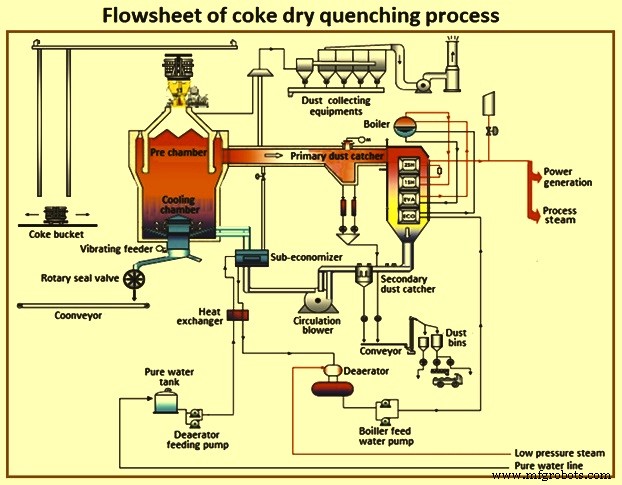
Gbr 3 Flowsheet proses dry quenching
Dalam proses pendinginan kokas kering, kokas merah-panas didinginkan oleh gas yang bersirkulasi dalam sistem tertutup, sehingga mencegah pelepasan debu kokas di udara. Energi panas dari kokas merah-panas, yang hilang dalam proses pendinginan basah kokas konvensional, dikumpulkan dan digunakan kembali sebagai uap dalam proses pendinginan kokas kering. Teknologi ini menggunakan lebih sedikit bahan bakar fosil dan menghasilkan emisi karbon dioksida yang lebih rendah, sehingga berkontribusi pada pencegahan pemanasan global. Saat ini, pabrik pendinginan kering kokas telah menarik banyak perhatian dunia karena pemulihan energinya yang efisien dan karakteristiknya yang mengurangi pencemaran lingkungan. Mereka dianggap sebagai fasilitas penting untuk tindakan balasan terhadap masalah lingkungan seperti pemanasan global oleh karbon dioksida dan polusi udara. Dalam sebuah studi, di mana perhitungan penghematan energi telah dilakukan berdasarkan operasi proses pendinginan kering kokas yang ada, telah ditunjukkan bahwa 85% dari panas buangan yang dihasilkan selama karbonisasi batubara diperoleh kembali oleh proses pendinginan kering kokas. .
Pendinginan kering juga meningkatkan kekuatan kokas. Keuntungan lain dari pendinginan kokas kering adalah pengurangan emisi gas rumah kaca (GRK) dan peningkatan efisiensi air.
Pintu anti bocor modern
Pintu bocor baterai oven kokas selalu menjadi sumber utama polusi. Desain pintu oven telah melalui proses evolusi, mulai dari pintu beralur hingga generasi sekarang yang dapat mengatur sendiri pintu tanpa kebocoran. Fitur impor dari pintu anti bocor adalah (i) diafragma baja tahan karat tipis dengan ujung pisau sebagai bingkai penyegel yang dibangun di antara badan pintu dan penahan bata, (ii) pengaturan pegas pada tepi pisau untuk penyegelan sendiri, (iii) penyediaan pendingin udara pada badan pintu, dan (iv) saluran gas ukuran besar untuk memudahkan sirkulasi gas di dalam oven.
Keuntungan dari pintu anti bocor adalah meminimalkan kebocoran pintu, pengoperasian bebas regulasi, masa pakai lebih lama karena lebih sedikit lengkungan pada badan pintu berpendingin udara dan pengurangan perawatan.
Sistem kontrol emisi pendorong berbasis darat
Emisi yang dihasilkan selama mendorong kokas merah panas mengandung sejumlah besar debu kokas (sekitar 11% dari total polutan dalam oven kokas. Sistem kontrol mendorong berbasis darat mengurangi polusi ini. Ini terdiri dari (i) tudung hisap besar yang dipasang di mobil pemandu kokas dan bergerak dengan pemandu kokas, mengarahkan asap ke saluran pengumpul debu samping kokas (ii) saluran pengumpul debu dan (iii) dan peralatan pembersihan asap Sejumlah besar asap suhu tinggi paroksismal dikumpulkan di bawah kipas pelampung panas ke dalam kap pengisap gas besar yang dipasang di mobil pemandu kokas, dan memasuki saluran pengumpul debu melalui peralatan lain.Udara dibuang ke atmosfer setelah pemurnian oleh pengumpul saluran pulsa dan setelah didinginkan oleh pendingin akumulator. Sistem dikendalikan oleh pengontrol logika yang dapat diprogram (PLC).
Otomasi dan sistem kontrol proses
Otomatisasi oven kokas disusun dalam level klasik, dari Level 0 (Level bidang) hingga Level 3 (Level manajemen). Desain otomatisasi pabrik oven kokas biasanya dibagi menjadi enam lapisan peralatan dasar. Gambar 4 menunjukkan hierarki sistem otomasi pabrik oven kokas.
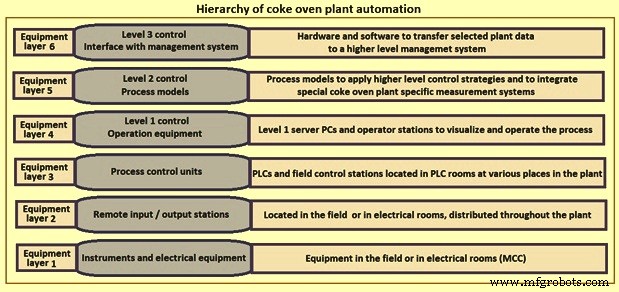
Gbr 4 Hirarki otomatisasi pabrik oven kokas
Peralatan listrik, elemen kontrol dan instrumentasi biasanya terhubung ke unit I/O (input/output) jarak jauh redundan yang dilakukan dengan antarmuka standar 4-20 mA dan 24 DC. Subsistem cerdas biasanya digabungkan dengan Profibus atau Modbus. Semua peralatan otomatisasi terhubung melalui jaringan pabrik serat optik yang berjalan melalui semua lokasi pabrik di mana peralatan yang relevan ditempatkan. Semua data dikumpulkan dan didistribusikan melalui jaringan ini, di mana sumber data dan target data dapat saling terhubung secara fleksibel menggunakan koneksi fisik dengan panel patch dan sakelar serta koneksi logis menggunakan sistem manajemen jaringan. Melalui jaringan ini semua sistem dapat berkomunikasi satu sama lain.
Di area pabrik oven kokas, 'sistem kontrol terdistribusi' (DCS) terintegrasi digunakan pada tingkat kontrol proses. Banyak aplikasi di pabrik oven kokas adalah fungsi kontrol urutan, yang paling baik dijalankan oleh PLC.
Otomatisasi dan kontrol proses untuk pemanas dan mesin baterai oven kokas dicapai dengan menggunakan sistem kontrol level 2 yang melakukan berbagai perhitungan model proses berdasarkan data yang diproses yang dikumpulkan dari sistem otomatisasi level 1. Sistem kontrol level-2 memberi operator oven kokas alat pendukung yang canggih, akurat, dan mudah digunakan, yang dapat berhasil digunakan untuk meningkatkan kinerja operasional dan lingkungan pabrik.
Manfaat dari sistem otomasi dan kontrol proses termasuk konsumsi energi yang lebih rendah melalui pengurangan konsumsi bahan bakar gas, menstabilkan kondisi dan pengoperasian baterai oven kokas, kualitas kokas yang konsisten, pengurangan emisi, peningkatan masa pakai baterai dan kemudahan dalam pelaporan dan analisis operasional dan data pemeliharaan.