Pembuatan Baja Netral Karbon
Pembuatan Baja Netral Karbon
Industri produksi besi dan baja adalah sektor tunggal terbesar dalam hal total emisi fosil dan industri global, menyumbang sekitar 7% hingga 9% dari emisi gas rumah kaca (GRK). Pada saat yang sama, baja merupakan komponen material utama bagi masyarakat industri modern. Konsumsi baja lebih lanjut akan terjadi karena kebutuhan untuk memperluas dan meningkatkan infrastruktur dan meningkatkan standar hidup global dengan kecepatan yang cukup untuk mencapai tingkat yang memuaskan. Oleh karena itu, tantangannya terletak dalam menemukan jalur yang memungkinkan penggunaan baja oleh masyarakat sebagai bahan, sementara pada saat yang sama menghindari dampak negatif lingkungan dari produksinya.
Proses produksi besi dan baja tradisional dikaitkan dengan emisi GRK lingkungan yang sangat tinggi. Emisi saat ini dari pabrik besi dan baja berada pada tingkat sekitar 1,8 ton CO2 (karbon dioksida) per ton baja mentah (tCO2/tCS). Meskipun ada upaya berkelanjutan yang signifikan untuk mengurangi emisi GRK dari pembuatan baja selama beberapa dekade terakhir, terobosan teknologi besar memang masih diperlukan jika sektor besi dan baja ingin mengimbangi pengurangan emisi menyeluruh yang dibutuhkan di bawah Paris. Perjanjian, yang bertujuan untuk membatasi kenaikan suhu global pada pergantian abad ini hingga jauh di bawah 2 derajat C di atas tingkat pra-industri, dan menyatakan bahwa upaya harus diarahkan pada target yang lebih ambisius yaitu kenaikan suhu hanya 1,5 derajat C.
Emisi CO2 dari industri besi dan baja termasuk yang paling sulit untuk diturunkan, karena karbon digunakan sebagai zat pereduksi stoikiometrik dalam produksi besi dan baja di sebagian besar pabrik baja. Karbon ini berakhir sebagai campuran CO / CO2 dalam gas pabrik baja, yang dibakar untuk menghasilkan panas, listrik, dan lebih banyak CO2. Strategi untuk karbon, penangkapan dan penyimpanan (CCS), untuk karbon, penangkapan, dan pemanfaatan (CCU), atau untuk menghindari CO2 ada dalam produksi besi dan baja, tetapi sangat bergantung pada ketersediaan tenaga listrik terbarukan untuk produksi hidrogen ( H2).
Perkiraan permintaan baja masa depan saat ini sangat bervariasi dengan proyeksi tingkat pertumbuhan tahunan berfluktuasi antara 1,4% dan 3,3%. Dengan laju pertumbuhan tersebut, proyeksi kebutuhan baja pada tahun 2025 mencapai 2,4 miliar ton. Dekarbonisasi sebagian dari industri besi dan baja yang sedang berkembang ini hanya dapat dicapai melalui peningkatan efisiensi dan integrasi tenaga listrik terbarukan dalam rute pembuatan baja konvensional, sedangkan dekarbonisasi lengkap memerlukan teknologi nol-karbon dan/atau emisi negatif yang baru. Di sisi lain, upaya untuk mendekarbonisasi proses produksi besi dan baja belum mencapai tingkat adopsi industri skala besar, terlepas dari upaya penelitian dan pengembangan (R&D) substansial yang sedang berlangsung saat ini. Kelayakan dan penerapan CCS dalam konteks pembuatan baja tetap sangat diragukan dalam skenario saat ini.
Dalam rute tanur sembur / tungku oksigen dasar (BF / BOF) konvensional, karbon (dalam bentuk kokas dan batubara) digunakan untuk mendorong reaksi reduksi endotermik serta untuk menyediakan suhu tinggi yang diperlukan. Proses BF-BOF tipikal menghasilkan 1,6 tCO2/tCS hingga 2,2 tCO2/tCS. Ada perbedaan regional yang cukup besar dalam emisi terkait baja, dengan beberapa negara produsen baja memiliki jejak emisi CO2 yang jauh lebih tinggi dibandingkan dengan negara-negara OECD (Organisasi untuk Kerjasama Ekonomi dan Pembangunan). Ada juga perbedaan yang signifikan antara rute pembuatan baja yang berbeda seperti BF-BOF, DRI-EAF (tungku busur listrik-besi tereduksi langsung) dan scrap-EAF. Melalui peningkatan teknologi, pabrik baja terus mengurangi tingkat konsumsi bahan bakarnya selama lima dekade terakhir hingga pada titik di mana rute BF-BOF sekarang dapat dipertimbangkan untuk dioptimalkan secara besar-besaran. BF paling efisien di dunia sekarang beroperasi dalam kisaran 5% di atas minimum teoritis dalam hal emisi CO2 mereka.
Transisi industri berat pada umumnya dan industri besi dan baja pada khususnya, menuju dekarbonisasi, hingga saat ini, belum banyak mendapat perhatian dari sudut pandang penelitian energi dan iklim. Namun, dengan emisi industri yang hampir setinggi emisi dari pembangkit listrik, langkah-langkah mitigasi untuk dekarbonisasi mendalam harus dilakukan dengan penuh semangat di industri besi dan baja. Strategi dekarbonisasi mendalam untuk industri besi dan baja sebagian besar dapat mengikuti dua rute berbeda seperti yang diberikan di bawah ini.
- Mengubah proses yang ada yang akan dilakukan untuk menghilangkan ketergantungan yang melekat pada bahan bakar fosil. Jalur ini cenderung sangat mengandalkan penggunaan tenaga listrik, baik secara langsung maupun melalui H2 yang dihasilkan dari elektrolisis.
- Menjaga proses yang ada seperti itu dan mengatasi emisi melalui kombinasi aplikasi CCS dan CCU dan pergeseran ke sumber terbarukan untuk energi proses.
Pengkategorian kedua jalur tersebut yang diterapkan pada industri besi dan baja memiliki beberapa karakteristik serta tantangan dan peluang yang berkaitan dengan implementasinya seperti yang dijelaskan di bawah ini. Gambar 1 memberikan perkiraan pengurangan emisi CO2 untuk berbagai alternatif.
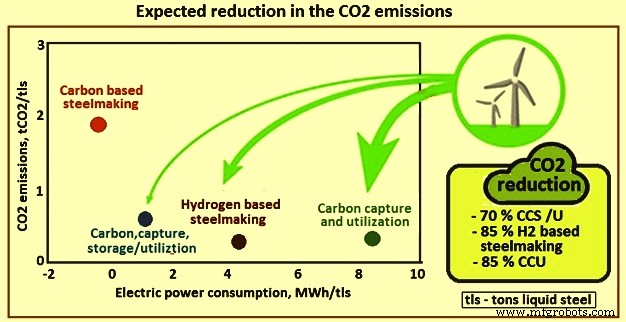
Gbr 1 Pengurangan emisi CO2 yang diharapkan
Mengubah proses yang ada
Dengan meningkatnya ketersediaan listrik terbarukan berbiaya rendah, berbagai bentuk elektrifikasi semakin dilihat sebagai pilihan menarik untuk dekarbonisasi industri besi dan baja. Sejumlah solusi teknologi yang berbeda telah disarankan untuk tujuan ini. Di antara teknologi yang lebih menjanjikan adalah elektrolisis atau 'pemenang elektro' dari bijih besi. Ini memerlukan penggunaan tenaga listrik sebagai zat pereduksi, mirip dengan produksi aluminium (Al) dari aluminium oksida (Al2O3). Proses ini masih dalam tahap awal pengembangan dan sejauh ini hanya dicoba pada skala laboratorium, tetapi ini merupakan opsi pembuatan baja dengan efisiensi tinggi dengan janji pengurangan emisi yang besar dalam jangka panjang.
Elektro-winning adalah salah satu teknik elektrolitik tertua yang digunakan untuk ekstraksi logam dari bijihnya dengan menggunakan listrik. Teknologi ini biasanya digunakan untuk elektro-winning logam seperti timah, tembaga dan elemen tanah jarang. Ada beberapa teknologi elektro-winning khusus bijih yang tersedia secara komersial untuk besi yaitu (i) proses Boucher, elektro-pemurnian dalam larutan FeSO4-FeCl2, (ii) proses Eustis, elektro-winning dalam larutan FeCl2 menggunakan bijih besi sulfida, dan (iii) proses Pyror, elektro-winning dalam larutan FeSO4 menggunakan bijih besi sulfida. Namun, elektro-winning Fe yang lebih umum berlaku dari bijih besi hanya ditetapkan pada skala laboratorium. Tergantung pada jejak karbon dari campuran listrik yang digunakan untuk elektrolisis, rute ini berpotensi bebas karbon. Dalam skenario futuristik, di mana pasokan energi primer global didominasi oleh sumber terbarukan, teknologi ini menawarkan potensi pengurangan karbon yang signifikan. Inisiatif SIDERWIN Eropa saat ini, yang merupakan proyek di bawah kerangka Horizon 2020 dengan target pengurangan emisi CO2 dan konsumsi energi sebesar 87% dan 31% (dibandingkan dengan rute BF-BOF), masing-masing bertujuan untuk memvalidasi teknologi ini pada skala percontohan , dan menunjukkan tingkat kesiapan teknologi (TRL) pada tahun 2022.
Rute elektrolitik lain yang baru-baru ini menarik minat untuk pembuatan baja adalah elektrolisis oksida cair dari bijih besi (juga dikenal sebagai piro-elektrolisis). Prosesnya mirip dengan metode standar untuk reduksi Al dari Al2O3 melalui proses Hall-Heroult, di mana Al2O3 dilarutkan dalam penangas kriolit cair (aluminium natrium fluorida) 800 derajat C dan kemudian dielektrolisis di antara anoda grafit (di atas ) dan katoda dari aluminium cair (bawah). Operasi proses serupa untuk reduksi bijih besi pada suhu yang sangat tinggi diharapkan menghasilkan potensi penurunan konsumsi energi dibandingkan dengan rute elektrolisis suhu rendah. Bukti konsep telah ditunjukkan, tetapi kelayakan teknis dengan efisiensi yang dapat diterima masih sulit dipahami. Tantangan termasuk korosivitas elektrolit cair, kurangnya bahan anoda yang sesuai, dan pemahaman mekanistik yang terbatas tentang proses elektrolitik suhu sangat tinggi. Meskipun produksi baja dengan elektrolisis oksida cair menawarkan potensi keuntungan ekonomi dan lingkungan dibandingkan metalurgi ekstraktif klasik, kelayakannya masih jauh dari dibuktikan secara meyakinkan sebagai alternatif nol-karbon langsung.
Sebuah studi telah membandingkan kebutuhan energi dan emisi CO2 dari empat rute produksi baja yang berbeda, yaitu, kasus referensi BF-BOF, BF-BOF dengan penangkapan karbon (BF-CCS), H2-DRI dan proses electro-winning. Jalur elektro-winning memiliki kebutuhan energi 50% lebih rendah dari kasus referensi BF-BOF, diikuti oleh H2-DRI dan BF-CCS pada kebutuhan energi 28% dan 13% lebih rendah masing-masing. Yang penting, analisis juga menyimpulkan bahwa lebih dari 50% pengurangan emisi CO2 tidak mungkin dilakukan melalui rute BF-CCS, sedangkan, baik rute reduksi-H2 dan elektro-winning pada akhirnya dapat mengarah pada dekarbonisasi lengkap sektor besi dan baja. Entri pasar untuk H2-DRI dan pemenang elektro tidak diharapkan masing-masing sampai tahun 2035 dan 2040.
Konsumsi stoikiometri H2 untuk reduksi hematit adalah 54 kg per ton besi. Pabrik besi dan baja 1 Mtpa (juta ton per tahun) membutuhkan kapasitas pabrik H2 sebanyak 70.000 cum pada STP/jam. Produksi H2 skala besar saat ini dicapai dengan reformasi uap metana. Opsi ini dapat dipertahankan dan bahkan dioptimalkan untuk pembuatan besi berbasis H2, misalnya, dengan menargetkan kemurnian H2 97% hingga 98% alih-alih kemurnian normal 99,9% plus. Namun, karena berdasarkan sumber daya fosil, kinerja dalam hal mitigasi CO2 secara keseluruhan tetap rata-rata, kecuali jika unit penangkap CO2 ditambahkan, yang mewakili strategi yang berbeda dari strategi yang dilakukan saat ini. Pilihan lain yang lebih disukai adalah menghasilkan H2 dengan elektrolisis air, asalkan daya listrik yang dibutuhkan bebas fosil. Ukuran tanaman dapat dicapai dengan mengalikan sel elektrolitik. Teknologi baru yang ditingkatkan juga telah diidentifikasi, seperti membran penukar proton dan elektrolisis tekanan tinggi atau suhu tinggi.
Dalam reduksi berbasis H2, bijih besi direduksi melalui reaksi gas-padat, mirip dengan rute DRI. Satu-satunya faktor pembeda adalah bahwa zat pereduksinya adalah H2 murni, bukan gas CO (karbon monoksida), syngas, atau kokas. HYBRIT, kependekan dari 'HYdrogen BReakthrough Ironmaking Technology', adalah perusahaan patungan antara tiga perusahaan Swedia yaitu SSAB, LKAB dan Vattenfall. Ini bertujuan untuk sepenuhnya menghilangkan karbon dari pembuatan baja, menggunakan reduksi H2. Proses HYBRIT termasuk dalam kategori konsep teknologi yang secara substansial lebih dekat dengan penerapan komersial.
Proses HYBRIT didasarkan pada penggunaan H2 sebagai agen reduksi, dengan H2 diproduksi melalui elektrolisis berdasarkan listrik terbarukan. Dari sudut pandang lingkungan, keuntungan terpenting dari proses ini adalah bahwa gas buang dari proses ini adalah air (H2O) bukan CO2, dengan konsekuensi pengurangan emisi GRK. Seperti pembuatan baja DRI konvensional, besi yang diproduksi menggunakan rute DRI berbasis H2 dapat diproses lebih lanjut menjadi baja menggunakan teknologi EAF yang tersedia secara komersial. Tahap produksi H2 dan pembuatan baja EAF dapat dibuat bebas karbon jika tenaga listrik dan H2 diproduksi menggunakan sumber terbarukan seperti PV (fotovoltaik) / elektrolisis bertenaga angin / hidro, produksi H2 fotokimia, atau pemisahan air panas matahari .
Proses HYBRIT menggantikan batubara dengan H2 untuk reduksi langsung (DR) besi, dikombinasikan dengan EAF. Prosesnya hampir sepenuhnya bebas fosil, dan menghasilkan pengurangan substansial dalam emisi gas rumah kacanya. Proses ini merupakan salah satu dari beberapa inisiatif yang menggunakan pengaturan H2-DR/EAF, menggabungkan reduksi langsung bijih besi dengan menggunakan H2 dengan EAF untuk diproses lebih lanjut menjadi baja. Produk dari proses H2-DR adalah DRI atau besi spons, yang dimasukkan ke dalam EAF, dicampur dengan bagian skrap yang sesuai, dan diproses lebih lanjut menjadi baja. Lembar aliran khas proses H2-DR/EAF ditunjukkan pada Gambar 2.
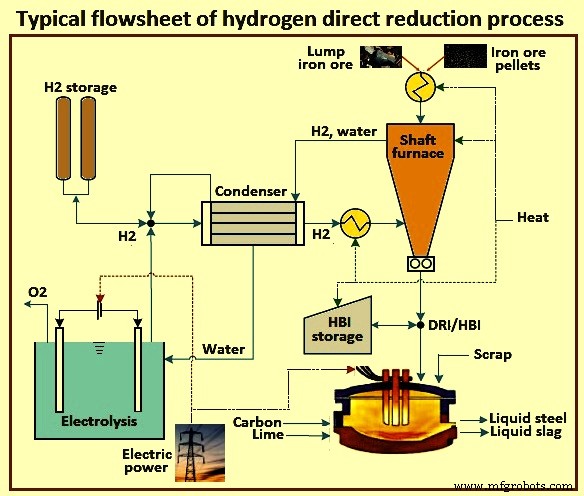
Gbr 2 Flowsheet khas proses reduksi langsung hidrogen
Meskipun kombinasi spesifik dari proses ini belum diterapkan pada skala komersial, beberapa komponen individu sudah banyak digunakan dalam industri besi dan baja global. Baja berbasis EAF menghasilkan sekitar 30% dari produksi global tahunan. Proses DR juga digunakan secara luas, menjadi dasar untuk sekitar 7% dari total produksi besi global dan biasanya terintegrasi dengan EAF. Sementara H2 murni telah digunakan secara komersial sebagai reduktor dalam reduksi langsung, kapasitas produksi DRI yang ada bergantung pada gas alam yang di steam-reformed untuk mendapatkan reduktor, campuran CO dan H2. Baru-baru ini, proses zero reform (ZR) telah dikembangkan yang secara substansial telah mengurangi konsumsi gas alam.
Karena biaya gas alam merupakan faktor kunci untuk kelayakan ekonomi dari pengaturan ini, sebagian besar produksi DRI terletak di daerah yang kaya akan gas alam berbiaya rendah (CH4). Terlepas dari kenyataan bahwa beberapa komponen pengaturan H2-DR/EAF telah diuji dan digunakan dalam pengaturan industri, tantangan utama masih tetap ada untuk proses tersebut. Ini terkait dengan integrasi proses, kualitas produk, peningkatan infrastruktur H2 (produksi dan penyimpanan) dan integrasi pabrik besi dan baja H2-DR/EAF ke dalam sistem energi berdasarkan sumber listrik terbarukan. Salah satu tantangan utamanya adalah bagaimana memasukkan karbon ke dalam besi untuk membuatnya menjadi baja.
Mempertahankan proses yang ada
CCS telah menjadi topik penting dalam studi pengendalian emisi GRK. Minat tumbuh pada 1990-an dengan analisis teknologi yang lebih mendalam. Konsep ini masuk lebih luas ke dalam diskusi kebijakan iklim di awal tahun 2000-an sebagai teknologi potensial di mana penggunaan bahan bakar fosil secara global dapat berlanjut tanpa berkontribusi pada tingkat GRK di atmosfer. Teknologi penangkapan karbon sendiri sudah cukup matang, menyusul komersialisasi pada pertengahan abad ke-20 di industri makanan dan kimia. Penyimpanan juga telah berhasil dicoba di reservoir gas alam. Pada tahap awal studi CCS untuk tujuan mitigasi perubahan iklim, fokus utamanya adalah pada aplikasi pada sektor pembangkit tenaga listrik, khususnya produksi tenaga listrik berbasis batu bara. Namun, terlepas dari daftar panjang pabrik percontohan dan proyek percobaan, CCS komersial gagal terwujud. Hal ini sebagian disebabkan oleh pembengkakan biaya, sebagian karena penolakan publik terhadap penyimpanan CO2 bawah tanah dan sebagian lagi karena penurunan biaya pembangkit listrik lain yang kurang berpolusi seperti energi terbarukan dan gas alam.
Meskipun ekspektasi untuk peran CCS di sektor listrik telah menurun, namun perkembangan terbaru dalam penangkapan karbon dari pembangkit listrik gas alam, dengan menggunakan apa yang disebut siklus Allam, tampak menjanjikan. Ini masih dianggap sebagai pilihan utama untuk mengurangi emisi GRK dari industri berat termasuk industri besi dan baja tanpa perubahan besar pada proses yang ada. CCS dalam industri memiliki karakteristik pembeda tertentu dalam hal kondisi implementasi. Keuntungannya adalah aliran CO2 cenderung cukup murni di industri dibandingkan dengan produksi tenaga listrik, yang dapat membuat tahap pemisahan dan penangkapan menjadi lebih mudah. Selain itu, penentangan publik diperkirakan tidak akan terlalu parah, karena hanya ada sedikit alternatif berbasis energi terbarukan untuk beberapa industri, seperti industri semen.
Namun, industri besi dan baja juga memiliki beberapa fitur yang dapat mempersulit aplikasi CCS. Pertama, tidak seperti industri pembangkit tenaga listrik, industri besi dan baja bersaing secara global, yang membuatnya semakin rentan terhadap kenaikan biaya dan lebih bermasalah untuk menanggung kenaikan biaya kepada pelanggan. Kerugian lain untuk opsi CCS adalah bahwa lokasi industri menampung sejumlah sumber CO2 dengan konsentrasi dan volume yang bervariasi. Sebagian besar penilaian CCS hanya berfokus pada sumber utama CO2, sedangkan menangkap semua CO2 dari pabrik terbukti jauh lebih sulit dan membutuhkan pembangunan kembali besar-besaran. Menangkap dan menyimpan 50% hingga 60% dari emisi CO2 di lokasi industri dapat menelan biaya sekitar USD 70 hingga USD 80 per ton CO2, menurut beberapa penilaian. Namun, untuk menangkap bagian emisi yang lebih tinggi, struktur biayanya lebih tidak pasti. Khususnya, tidak ada perkiraan biaya yang dapat diandalkan untuk menangkap lebih dari 90% emisi.
Proyek ‘Pembuatan Baja Karbon Dioksida Ultra Rendah’ (ULCOS) telah mengidentifikasi sejumlah teknologi yang dapat mendukung penerapan CCS di industri besi dan baja. Salah satunya, proses TGR-BF (Top Gas Recycling – Blast Furnace) telah berhasil diuji di pabrik percontohan, menghasilkan potensi pengurangan emisi CO2 sebesar 24%. Namun, penangkapan dan penyimpanan CO2 yang sebenarnya bukanlah bagian dari penyiapan percontohan ini.
Singkatnya, CCS saat ini tampak seperti solusi yang lebih menjanjikan di industri daripada di pembangkit listrik, tetapi masih ada masalah yang melekat. Pertama, potensi penurunan emisi GRK dari CCS terbatas pada sekitar 50%, karena sumber emisi yang kecil dan tersebar, kurangnya ruang untuk instalasi, dan masalah lainnya. Kedua, masalah terkait penyimpanan, seperti pengawasan dan integritas jangka panjang dari reservoir penyimpanan, masih belum terselesaikan. Ketiga, CCS hadir dengan sangat sedikit manfaat tambahan, dan keberadaan manfaat tambahan telah diidentifikasi sebagai fasilitator utama dalam hal percepatan proses transisi. Ini adalah faktor yang dapat menghambat penyerapan secara luas. Jika penangkapan karbon dikombinasikan dengan beberapa bentuk pemanfaatan CO2 (CCU), ada peluang yang lebih besar, tetapi masih banyak proses pengembangan yang perlu dilakukan. Juga, bahkan jika CO2 digunakan sebagai bahan mentah seperti dalam beberapa bentuk bahan kimia khusus atau bahan bakar, namun akhirnya berakhir di atmosfer.
Peran biomassa
Sepanjang sebagian besar sejarah pengolahan besi dan baja, biomassa adalah sumber daya utama. Arang berbahan dasar kayu bertindak baik sebagai zat pereduksi yang diperlukan untuk membebaskan bijih besi dari komponen oksigennya, serta sebagai sumber energi yang dibutuhkan untuk mencapai suhu tinggi yang diperlukan. Baru sekitar tahun 1875 kokas, yang dihasilkan dari batu bara, mengambil alih, meskipun penting untuk dicatat bahwa arang terus digunakan hingga pertengahan 1900-an. Arang yang dihasilkan dari eukaliptus yang tumbuh cepat masih digunakan sebagai zat pereduksi utama di pabrik baja yang lebih kecil di Brasil, tetapi ini sepertinya tidak layak di pabrik besi dan baja yang lebih besar karena batasan yang dikenakan oleh kekuatan tekan arang yang lebih rendah dibandingkan dengan kokas. Selain itu, jumlah besar yang dibutuhkan dan tantangan signifikan dalam menjaga kualitas membuat peralihan penuh dari kokas ke biokokas sangat tidak mungkin.
Namun biomassa masih dapat memainkan peran penting dalam dekarbonisasi sektor besi dan baja, dan beberapa opsi berbeda telah diusulkan. Di sisi tambahan skala adalah kemungkinan pencampuran 5% sampai 10% arang dengan batubara kokas dalam produksi kokas metalurgi untuk digunakan di BF yang ada. Pilihan lain adalah menggunakan biomassa dalam pengolahan bijih besi mentah, baik sebagai bahan bakar untuk proses itu sendiri atau untuk menghasilkan pelet bijih besi bio-karbon-komposit yang kemudian dapat digunakan dalam proses DR. Ada juga percobaan yang ditujukan untuk menggunakan biomassa gasifikasi dalam proses DR. Pendekatan ini layak tetapi membutuhkan percobaan dan studi lebih lanjut. Höganäs AB, sebuah perusahaan Swedia yang menggunakan proses DR berbasis batu bara untuk menghasilkan serbuk besi, telah memulai uji coba dunia nyata dari proses menggunakan gasifikasi kayu untuk menghasilkan bio-kokas, yang akan digunakan sebagai agen reduksi, serta syngas, untuk digunakan sebagai energi proses (dan mungkin juga untuk reduksi.
Bio-metana juga akan menjadi pilihan rendah karbon yang penting untuk pemanasan dalam proses metalurgi sekunder jika gas oven kokas dari oven kokas dan pabrik produk sampingan tidak lagi tersedia. Di pabrik besi dan baja terintegrasi, gas oven kokas dari oven kokas dan pabrik produk sampingan digunakan untuk pemanasan dalam proses metalurgi sekunder. Dengan konsep H2-DR, energi ini harus diganti. Dalam jangka panjang, ada pilihan yang berbeda untuk pemanas listrik, tetapi bio-metana dapat menggantikan gas alam dan gas coke-oven yang saat ini digunakan secara langsung, dengan sedikit perubahan pada prosesnya.
Namun, tantangan sistemik untuk biomassa cenderung substansial. Berbeda dengan batu bara, sumber daya biomassa tidak terkonsentrasi di tempat tertentu (seperti tambang), yang menyebabkan biaya pengadaan tinggi karena biomassa dari area yang tersebar secara geografis harus dikumpulkan, diproses, dan diangkut ke pabrik besi dan baja. Kedua, meningkatnya permintaan kayu dapat menyebabkan persaingan dengan pengguna yang ada (seperti industri kehutanan), serta sektor lain yang bertujuan untuk memanfaatkan biomassa untuk mencapai ambisi mitigasi. Hal ini pada gilirannya dapat menyebabkan harga yang lebih tinggi, kecuali jika fokus dialihkan ke residu hutan yang kurang diminati. Terakhir, untuk memastikan pengurangan emisi GRK, biomassa harus bersumber dari hutan yang dikelola secara lestari.
Singkatnya, biomassa dapat memainkan peran penting baik dalam rute terbarukan maupun CCS. Keduanya membutuhkan panas dalam jumlah besar dalam proses pengolahan bijih besi, metalurgi sekunder dan proses rolling panas. Ini dapat disediakan dengan sangat baik melalui pembakaran bio-metana. Dalam rute CCS, arang setidaknya dapat menggantikan sebagian kokas, selama stabilitas mekanis muatan BF dipertahankan. Dalam konsep HYBRIT, biomassa diperkirakan juga berfungsi sebagai sumber karbon untuk proses besi dan baja dan berpotensi juga dalam proses pengerjaan logam hilir.