Menyesuaikan sensor ultrasonik untuk pengoptimalan dan kontrol proses komposit
Blog ini adalah tindak lanjut dari laporan saya tentang proyek CosiMo (“komposit untuk mobilitas berkelanjutan”). Proyek itu diluncurkan pada tahun 2018 oleh Faurecia Clean Mobility (Nanterre, Prancis) untuk mendemonstrasikan “pembuatan pintar” dari penutup kotak baterai komposit. Bagian tantangan sepanjang 1.100 milimeter dan lebar 530 milimeter menampilkan serat kaca bukan tenunan dan penguat serat karbon searah serta sisipan logam dan busa, geometri kompleks termasuk berbagai jari-jari dan ketebalan yang bervariasi dari 2,5 hingga 10 milimeter. Bagian tersebut dicetak menggunakan thermoplastic resin transfer moulding (T-RTM), di mana monomer kaprolaktam disuntikkan dan kemudian dipolimerisasi in-situ selama siklus tekan yang dipanaskan untuk membentuk komposit poliamida 6 (PA6). Tujuan utama proyek ini adalah untuk menyelidiki proses yang sepenuhnya otomatis menggunakan kontrol proses berbasis sensor loop tertutup.
Blog ini mengeksplorasi lebih detail jaringan 74 sensor yang digunakan di bagian tantangan CosiMo, dan khususnya sensor ultrasonik yang dikembangkan oleh Universitas Augsburg (UNA, Augsburg, Jerman) dan bagaimana data dari semua sensor digunakan untuk membangun model proses digital (kembar digital).
Berdasarkan keberhasilan CosiMo dan kebutuhan akan pusat pengembangan untuk pengembangan manufaktur berbasis sensor dan AI, UNA telah membentuk Augsburg AI Production Network, bekerja sama dengan mitra proyek CosiMo German Aerospace Center (DLR) Center of Lightweight Production Technologies ( ZLP, Augsburg) dan Institut Fraunhofer untuk Teknologi Pengecoran, Komposit dan Pemrosesan (Fraunhofer IGCV). “Kami sedang menyiapkan fasilitas baru seluas 5.000 meter persegi yang akan kami operasikan bersama-sama,” kata Dr. Markus Sause, profesor UNA dan direktur Augsburg AI Production Network. “Kami akan memiliki sel produksi otomatis, banyak yang berfokus pada teknologi komposit, yang memungkinkan kami mendemonstrasikan apa yang dapat dilakukan AI.”
Jaringan sensor CosiMo
Untuk proyek CosiMo, 74 sensor diintegrasikan ke dalam perkakas baja RTM yang dipasok oleh Christian Karl Siebenwurst GmbH &Co. KG (Dietfurt, Jerman) untuk mencetak penutup kotak baterai T-RTM. Digunakan untuk memantau parameter proses selama injeksi resin, infiltrasi (pemantauan aliran depan) dan polimerisasi in-situ, jaringan ini mencakup:
- 1 sensor vakum
- 4 sensor tekanan/suhu oleh Kistler (Winterthur, Swiss)
- 4 sensor suhu oleh Kistler
- 8 analisis dielektrik (DEA)/sensor suhu oleh Netzsch (Selb, Jerman)
- 57 sensor ultrasonik yang dikembangkan oleh University of Augsburg.
Dalam laporan awal saya tentang CosiMo, saya membahas bagaimana jaringan sensor ini untuk R&D, bukan produksi standar:
“Untuk produksi serial industri, tidak ada yang akan memasang begitu banyak sensor dan bukan itu yang kami harapkan,” kata pemimpin proyek manufaktur CosiMo di DLR ZLP, Jan Faber. “Tetapi untuk penyelidikan penelitian ini, jaringan sensor besar ini sangat presisi dan membantu kami memiliki visibilitas penuh ke dalam proses dan perilaku material . Kami dapat melihat efek lokal dalam proses sebagai tanggapan untuk variasi ketebalan bagian atau bahan terintegrasi, seperti inti busa.”
Jadi, bagaimana jaringan ini dirancang? “Sebagian besar adalah sensor ultrasonik karena harganya paling murah,” Faber menjelaskan. “Kami menggunakannya dalam kotak pada jarak yang ditentukan satu sama lain. Di beberapa posisi, kami mengeluarkan sensor ultrasonik dan memasang sensor suhu/tekanan Kistler atau Netzsch DEA/suhu. Dan untuk sensor khusus ini, baik DEA maupun Kistler, kami hanya mencoba menempatkan satu di dekat sariawan, tempat resin masuk, dan kemudian yang jauh. Dengan demikian, kami dapat memantau lokasi kedatangan resin setelah melihat suhu cetakan selama beberapa waktu.”
Mengapa menggunakan berbagai jenis sensor? “Salah satu tugas penelitian adalah membandingkan sinyal dan melihat bagaimana kinerja sensor yang berbeda,” kata Faber. Ini penting karena berbagai jenis sensor didasarkan pada prinsip pengukuran yang berbeda. Misalnya, sensor DEA mengukur impedansi AC dari resin, yang dapat dipecah menjadi fraksi yang berbeda, yang pada gilirannya menunjukkan efek yang berbeda pada polimer. Kistler, sementara itu, menggunakan sensor piezoresistif yang mengandalkan Jembatan Wheatstone berbasis silikon - sejenis sirkuit yang digunakan untuk mengukur hambatan listrik dinamis - yang terhubung ke membran yang membentuk ujung penginderaan yang dipasang di dinding rongga cetakan. Membran memanjang di bawah tekanan, yang mengubah hambatan listrik dari Jembatan Wheatstone silikon, yang pada gilirannya mengeluarkan sinyal listrik. “Kami juga menggunakan sensor 4001a baru dari Kistler yang mengukur tekanan dan suhu,” catat Faber. “Sangat berguna memiliki kedua nilai untuk titik lokal tertentu di alat ini.”
Sensor ultrasonik UNA
Mayoritas sensor yang digunakan dalam jaringan bagian CosiMo adalah sensor ultrasonik yang dikembangkan oleh UNA. Sause mencatat bahwa ini disukai bukan hanya karena biayanya yang rendah (<10 euro) tetapi juga karena dapat menyampaikan berbagai informasi.
Sensor ultrasonik telah digunakan selama beberapa dekade untuk memeriksa bagian komposit jadi, tetapi juga memiliki sejarah panjang dalam cetakan injeksi. Sensor ultrasonik mengirimkan gelombang suara frekuensi tinggi ke dalam medium dan mengukur pantulannya (pulse-echo) dan/atau transmisi. Dalam proyek CosiMo, frekuensi nominalnya adalah 2.000 kilohertz. Dari 57 sensor ultrasonik yang dipasang di cetakan — pada jarak 20 milimeter dari permukaan rongga — 10 dioperasikan dalam mode transmisi, dan sisanya dalam mode gema pulsa. Sensor ultrasonik mengukur kecepatan gelombang dan penurunan amplitudo (atenuasi); keduanya sensitif terhadap sifat-sifat polimer. Selanjutnya, kecepatan gelombang dapat dihitung sebagai fungsi dari tekanan dan suhu, tetapi data ultrasound harus dikalibrasi dengan polimer yang sedang diselidiki.
“Sensor ultrasonik yang kami kembangkan sebenarnya tidak jauh berbeda dengan yang tersedia secara komersial,” kata Sause. “Ini didasarkan pada bahan piezoelektrik, yang cukup sensitif dalam mengubah gerakan elastis menjadi sinyal listrik. Tetapi jika sensor biasa dapat beroperasi pada suhu hingga 150 °C, kami harus menyesuaikan suhu tinggi cetakan termoplastik lebih dari 200 °C, yang sedikit menantang untuk elektronik sensor.”
“Kami juga harus merancang sistem mekanis untuk mengintegrasikan sensor dengan benar ke dalam cetakan,” jelasnya, “yang membutuhkan pemuatan pegas dengan penyegelan yang baik untuk memberikan sambungan yang baik. Ada portofolio besar persyaratan yang harus dipenuhi sensor; jadi, kami harus mendesainnya dari awal. Kami juga melakukan desain akustik yang tepat untuk keseluruhan sistem.”
Pemantauan polimerisasi dan aliran depan
“Akustik berfokus pada sifat elastis bahan dalam cetakan,” lanjut Sause. “Pada dasarnya, kekakuan dalam cairan tidak sama dengan saat polimerisasi selesai. Kami secara efektif memantau transisi itu. Kami melihat intensitas akustik pantulan gelombang pada antarmuka dari cetakan ke bahan polimer di setiap lokasi sensor, dan dengan demikian terus melacak proses curing dari waktu ke waktu.”
Mekanisme pengukuran ini dijelaskan oleh Sause dan Faber, et. al., dalam makalah konferensi SAMPE Europe 2021, “Pemantauan proses polimerisasi in-situ berbasis sensor dalam pembuatan T-RTM dengan kaprolaktam”. Rasio amplitudo gema sinyal akustik sebelum dan sesudah impregnasi bentuk awal bergantung pada indeks reflektif pada antarmuka cetakan-ke-bagian, R. Ini mendekati nilai konstan saat polimerisasi berlangsung. Idealnya, setelah polimerisasi hampir selesai, perubahan R akan menjadi nol.
Hal ini juga memungkinkan, dari sinyal transmisi akustik, untuk mengekstrak waktu tempuh gelombang ultrasonik untuk melewati bentuk awal yang diresapi. Ini berguna karena kecepatan suara melalui bentuk awal terkait dengan derajat polimerisasi. Untuk eksperimen yang diselesaikan pada saat makalah SAMPE Europe 2021, waktu antara pembasahan preform secara menyeluruh di lokasi sensor hingga penyelesaian polimerisasi adalah 240 detik.
“Kami juga dapat memantau aliran selama injeksi,” jelas Sause, “karena informasi sinyal akustik berubah saat aliran polimer melewati sensor.” Juga diverifikasi dalam makalah SAMPE Europe 2021, sinyal akustik turun tiba-tiba dari nilai normalisasi awal 1 menjadi antara 0,85-0,9 saat aliran depan kaprolaktam tiba untuk sensor yang dipilih pada 15 detik setelah injeksi dimulai.
Mengembangkan proses kembar digital
Sause mengatakan mengembangkan sensor ultrasonik sebenarnya adalah bagian yang sangat kecil dari apa yang dilakukan UNA dalam proyek CosiMo, "dan bahkan bukan bagian yang paling menarik." Pencapaian sebenarnya, catatnya, adalah dalam analisis data dan pengembangan model digital dari proses untuk memungkinkan kontrol loop tertutup selama pembuatan suku cadang.
"Apa yang kami coba lakukan adalah memberikan informasi tentang apa yang sebenarnya terjadi di cetakan," tambahnya. “Kami telah menetapkan rute untuk menyesuaikan proses dengan suhu dan tekanan, kurang lebih, tetapi yang kami lakukan sekarang adalah memanfaatkan informasi sinyal akustik dengan melakukan pulsing aktif di setiap lokasi sensor. Dan ini memungkinkan kami untuk menentukan berbagai hal seperti bentuk muka aliran, waktu untuk mencapai setiap bagian bentuk awal, dan tingkat polimerisasi di setiap lokasi sensor.”
“Idealnya, Anda dapat menetapkan pengaturan untuk mengaktifkan kontrol loop tertutup dan untuk menyesuaikan selama proses berlangsung,” kata Sause. “Ini akan mencakup parameter seperti tekanan injeksi dan tekanan dan suhu cetakan. Anda juga dapat menggunakan informasi ini untuk mengoptimalkan materi Anda.”
Pengembangan kembar digital adalah upaya multi-tahap dan multi-mitra. Ini dimulai dengan salah satu paket pekerjaan yang ditugaskan ke DLR ZLP. “Kami menyiapkan simulasi berdasarkan pelat 2D, di mana kami ingin mensimulasikan pengisian dan polimerisasi menggunakan perangkat lunak simulasi PAM-RTM dari ESI Group (Rungis, Prancis),” kata Faber. “Kami mendapat data permeabilitas preform dari mitra proyek ITA (Institute for Textile Technology, RWTH Aachen, Jerman) dan SGL Carbon (Wiesbaden, Jerman) dan juga model reaktif reaksi polimer termoplastik dari Universitas Augsburg. Kami kemudian mengintegrasikan semuanya ke dalam simulasi dan mencoba melihat seberapa dekat kami sebenarnya dengan data sensor yang sebenarnya.”
Titik-titik biru muda di cetakan atas dan bawah untuk bagian demonstran proyek CosiMo memberikan data pada titik-titik tertentu selama proses berlangsung. Ini kemudian digunakan dalam simulasi kembar digital untuk menginterpolasi antara lokasi sensor dan memodelkan proses di seluruh bagian. Kredit Foto:Proyek CosiMo, DLR ZLP Augsburg, Universitas Augsburg
“Kami menemukan, berdasarkan model pelat 2D, bahwa kami sebenarnya sangat dekat, dalam hal pengisian,” lanjut Faber. “Tetapi kami memiliki beberapa efek suhu selama polimerisasi yang tidak dapat kami gambarkan dalam simulasi. Misalnya, reaksi polimerisasi ini eksotermal, dan Anda melihat sedikit peningkatan pada sensor suhu dalam data nyata, tetapi peningkatan simulasi jauh lebih tinggi. Jadi, ini adalah area di mana kami terus melakukan beberapa pekerjaan.”
Salah satu hal yang tim ingin temukan dari simulasi adalah waktu yang dibutuhkan untuk polimerisasi selesai. “Apa yang benar-benar kami inginkan adalah waktu minimum yang kami butuhkan dalam cetakan,” catat Faber. Informasi ini diturunkan dari model simulasi, dan mengandalkan, seperti semua simulasi, pada berbagai jenis sensor dan algoritma AI. Misalnya, Netzsch menyediakan sensor dielektrik yang digunakan untuk analisis dielektrik, tetapi juga membantu bagian kembaran digital dari proses tersebut. “Mereka membuat model AI prediktif untuk menyelidiki mekanisme di dalam injeksi dan untuk memprediksi kapan polimerisasi harus selesai dan apa yang akan menjadi keadaan polimerisasi,” kata Faber.
(Catatan, Netzsch telah menggabungkan kompetensinya dalam karakterisasi material, simulasi kinetik, dan teknologi sensor untuk membuat penawaran baru dalam solusi AI dan cloud. Jenis solusi terintegrasi ini telah berhasil didemonstrasikan di CosiMo untuk memberikan evaluasi real-time dari tingkat polimerisasi dan akan dikomersialkan dengan merek sensXPERT.)
Dari rangkaian lengkap sensor dan simulasi, ditemukan bahwa 96% adalah polimerisasi maksimum yang dicapai dan membutuhkan 4,5 menit. “Jadi itu jauh lebih cepat daripada proses infus tetapi jauh lebih lambat daripada injeksi berkecepatan tinggi menggunakan termoset, misalnya.”
“Data sensor cocok dengan model kembar digital,” kata Sause. “Idenya adalah memiliki model yang berjalan pada saat yang sama dengan proses yang distabilkan secara numerik oleh informasi sensor. Titik-titik biru menyediakan kisi kasar sensor ultrasonik, dan kemudian kami dapat melakukan interpolasi di antara titik-titik tersebut. Misalnya, kami dapat menyediakan video tentang bagaimana aliran depan berkembang di bagian CosiMo sebagai fungsi waktu berdasarkan data pengukuran dari sensor kami.”
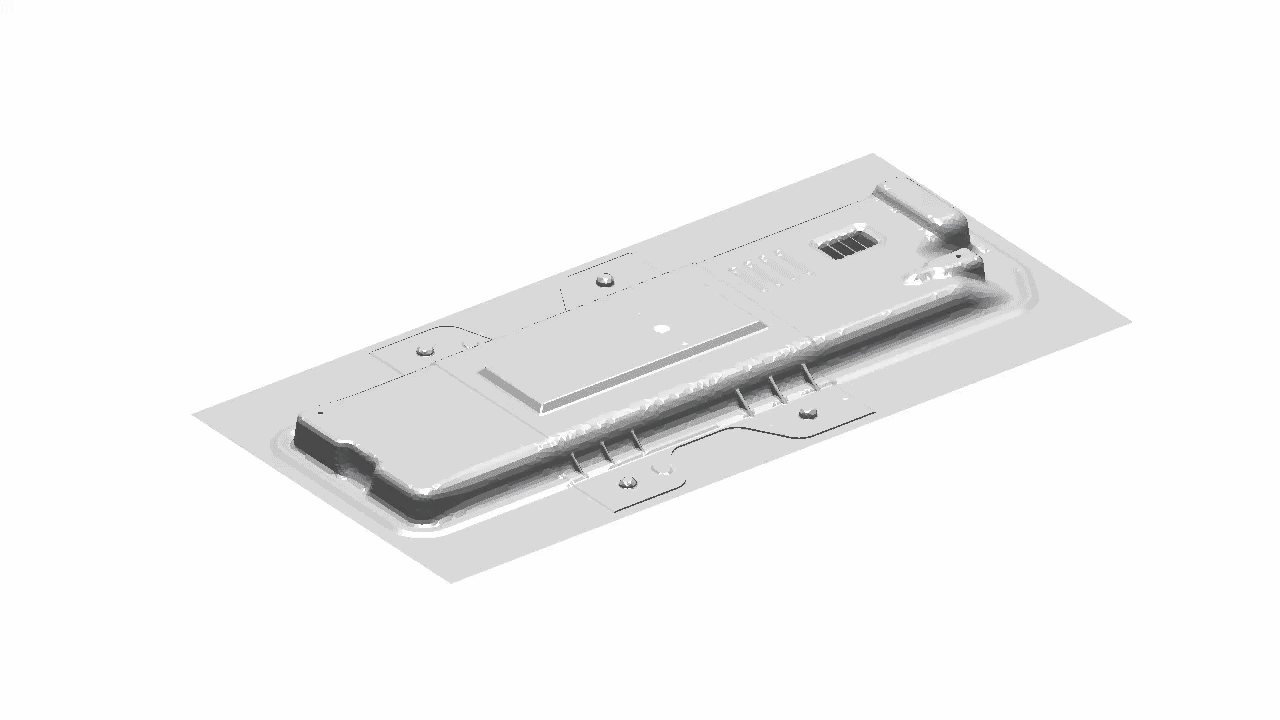
Tangkapan layar video bagaimana aliran depan berkembang di bagian CosiMo (inlet injeksi adalah titik putih di tengah) sebagai fungsi waktu berdasarkan data pengukuran dari jaringan sensor cetakan. Kredit Foto:Proyek CosiMo, DLR ZLP Augsburg, Universitas Augsburg
Bagaimana prediksi tingkat polimerisasi divalidasi? “Kami memiliki beberapa pendekatan,” kata Sause. “Pertama, seorang mahasiswa PhD di sini di UNA melakukan pemodelan lengkap untuk kinetika reaksi sistem material kaprolaktam-ke-PA6. Jadi, dia mempelajari spektroskopi inframerah secara bersamaan dengan data reometrik dan data dari sensor analisis dielektrik untuk memberikan model material yang sangat tepat untuk kinetika yang disembuhkan dari sistem itu dan untuk memvalidasi model itu. Jadi, kami menggunakan model yang sama untuk memvalidasi silang sensor kami.”
Arsitektur kembaran digital
Arsitektur bagaimana kembar digital beroperasi dijelaskan oleh Stieber, et. Al. dalam makalah teknis 2020, “Menuju pemantauan proses waktu nyata dan pembelajaran mesin untuk pembuatan struktur komposit”:
Ini terdiri dari tiga bagian:mesin T-RTM, sensor in-situ di perkakas cetakan dan kembaran digital. Struktur ini dan kembar digital, khususnya, telah dikembangkan dengan tujuan berikut O1 – O4:
- O1:Pantau proses pembuatan setiap komponen komposit dengan sensor in-situ dari perkakas.
- O2:Visualisasikan setiap proses manufaktur secara real-time untuk mendapatkan wawasan proses lebih lanjut.
- O3:Latih model ML pada data simulasi dan nyata untuk memprediksi hasil proses manufaktur.
- O4:Gunakan model ML terlatih untuk mengurangi penolakan produksi.
Sensor kemudian memasukkan data ke analisis tepi kembaran digital, yang kemudian dapat digunakan untuk memprediksi dinamika aliran depan di masa mendatang, menentukan kandungan volume serat dari setiap bentuk awal tekstil, memprediksi titik kering, dan mendeteksi anomali yang dapat mengurangi suku cadang yang ditolak.
Mesin T-RTM terdiri dari dua komponen siap pakai:mesin press panas 440 kilonewton Wickert (Landau in der Pfalz, Jerman) dan unit injeksi T-RTM oleh KrausMaffei (Munich, Jerman). Kedua mesin ini serta seluruh jaringan sensor terhubung ke PLC (programmed logic controller) yang bertanggung jawab untuk mengendalikan keseluruhan proses manufaktur.
Karena sensor memerlukan pra-pemrosesan waktu nyata untuk mengubah data mentah menjadi informasi tingkat tinggi tentang aliran depan atau pengawetan resin, data yang telah diproses sebelumnya direkam langsung di tepi menggunakan unit akuisisi data ibaPDA dari iba AG ( Furth, Jerman). Dengan demikian, data sensor direkam dan digabungkan dengan stempel waktu yang konsisten terkait dengan data proses dan sebagian informasi dengan data sensor per tujuan O1 dan O2.
Untuk mengoptimalkan proses manufaktur secara otomatis, data yang disimpan digunakan untuk melatih model machine learning (ML) untuk menangani O3 objektif. Model-model ini bertanggung jawab, misalnya, untuk merekonstruksi bagian depan aliran resin dari jaringan sensor, untuk memprediksi kemajuan aliran bagian depan, dan – idealnya – untuk mengadaptasi parameter proses untuk mengoptimalkan hasil baik selama contoh proses atau untuk proses selanjutnya. . Karena data nyata umumnya tidak cukup untuk melatih model yang andal, tim kembar digital menggunakan simulasi berjalan PAM-RTM untuk menambah data yang diukur. Setelah pra-pelatihan menggunakan data simulasi, kembaran digital itu disesuaikan dengan data dunia nyata. Strategi ini dikenal sebagai Transfer Learning dan telah berhasil diadopsi dalam visi komputer dan aplikasi pemrosesan bahasa alami. Analisis lanjutan yang dimungkinkan dengan ML memungkinkan peningkatan kemampuan prediksi dan visualisasi proses serta kontrol loop tertutup.
Integrasi sensor untuk produksi komposit industri
Jadi, bagaimana produsen suku cadang komposit menerapkan teknologi ini untuk mengembangkan kontrol loop tertutup dalam proses produksi mereka sendiri? Sause mengatakan masuk akal untuk menggunakan beberapa jenis sensor untuk memvalidasi silang pemantauan aliran dan penyembuhan/polimerisasi dan untuk memberikan informasi gratis. Dan kemudian masalah menentukan penempatan sensor, termasuk jenis yang ditempatkan di setiap lokasi. “Misalnya,” ia mencatat, “Anda tidak memerlukan sensor tekanan dan suhu di mana-mana, tetapi hanya di tempat yang Anda perlukan titik data penting tersebut, seperti entri resin, titik geometri kompleks, dll.”
Berapa banyak sensor? “Untuk CosiMo, kami menggunakan 74 sensor, tetapi untuk bagian setengah meter Anda akan menggunakan lebih sedikit, mungkin 35-40 tergantung pada geometri dan poin utama yang Anda minati,” kata Sause. “Tergantung proses produksinya juga. Ada proses di luar angkasa, misalnya, yang telah digunakan selama beberapa dekade dan sudah mapan. Untuk ini, Anda mungkin tidak memerlukan banyak sensor dan dimungkinkan untuk mengintegrasikannya tanpa banyak pekerjaan pengembangan di awal. Tetapi proses lain lebih tidak diketahui dan akan membutuhkan lebih banyak pekerjaan di muka. Untuk CosiMo, kami melihat penggunaan T-RTM dengan polimerisasi in-situ ke PA6, dan ini tidak didokumentasikan dengan baik seperti RTM dengan epoksi, misalnya.”
Peralatan manufaktur dalam proyek CosiMo terdiri dari mesin press Wickert 440-kN dan mesin injeksi KraussMaffei. Kredit Foto untuk seri ini:Proyek CosiMo, DLR ZLP Augsburg, Universitas Augsburg
Seberapa intensif waktu membangun model digital? Dan apakah itu selalu diperlukan untuk mencapai kontrol loop tertutup? “Sekali lagi, itu tergantung pada proses Anda dan level apa yang ingin Anda capai,” kata Sause. “Pertama-tama, memiliki informasi sensor yang terintegrasi memungkinkan Anda memvisualisasikan apa yang terjadi di dalam kotak hitam pemrosesan Anda dan parameter apa yang digunakan.
Sistem kontrol loop tertutup yang dikembangkan di CosiMo juga mengintegrasikan sensor cetakan dan sistem akuisisi data (sistem pengukuran ditampilkan di sini) oleh iba AG.
Setelah target pertama tercapai, ada beberapa langkah lagi untuk mencapai kontrol proses loop tertutup. Setengah jalan, mungkin, adalah memiliki visualisasi dan Anda dapat menekan tombol berhenti sendiri untuk menyesuaikan proses dan mencegah bagian yang ditolak. Jadi itu juga merupakan permulaan. Dan kemudian Anda dapat mengembangkan kembaran digital, tetapi membutuhkan data pelatihan. Jadi, Anda harus menyediakannya, yang berarti Anda dapat menghasilkan beberapa bagian untuk digunakan sebagai data input. Tapi kemudian, Anda juga perlu memproduksi suku cadang dengan kualitas rendah. Jadi, ini masalah kesediaan Anda untuk berinvestasi dalam pelatihan pendekatan pembelajaran mesin Anda.”
Setelah dilatih, kembaran digital dapat mengoptimalkan parameter proses dan menyediakan kontrol proses loop tertutup.
Namun, Sause mengakui bahwa pendekatan pembelajaran transfer yang diambil di CosiMo, “dapat ditransfer ke tingkat tertentu ke geometri atau sistem material yang serupa dan variasi lain yang tidak sepenuhnya mengubah situasi. Jadi, Anda dapat membangun database Anda dengan cara itu, dengan kemungkinan untuk mengidentifikasi tren efisiensi menggunakan data yang sudah diperoleh. Anda kemudian dapat menggunakannya untuk pertanyaan lain yang mungkin Anda miliki bersama.”
Jadi, cara untuk memulai tampaknya adalah:mulai menggunakan sensor dan membuat model digital agar sesuai dengan sensor sehingga Anda dapat memahami proses Anda? "Tentu saja," kata Sause. “Dan saya dapat meyakinkan Anda bahwa sebagian besar mesin yang digunakan dalam produksi saat ini masih sangat bodoh. Banyak mesin tidak memiliki sensor yang dapat memberi Anda database untuk memberikan umpan balik tentang apa yang terjadi. Jadi, ya, integrasi sistem sensor akan menjadi langkah pertama. Tapi Anda perlu melakukan sistematis akuisisi data, dan juga menyediakan arsitektur penyimpanan data, untuk dapat melakukan sesuatu dengan data . Anda sebenarnya melihat banyak perusahaan yang memiliki sensor terintegrasi, tetapi kemudian mereka tidak melakukan apa pun dengan data tersebut.”
Jaringan Produksi AI
Dalam menjawab pertanyaan di atas, Sause terus kembali ke berbagai kelompok di lingkungan UNA serta perusahaan spin-off yang dapat menyediakan layanan integrasi sensor dan kembaran digital. Untuk itu, Augsburg AI Production Network diluncurkan pada Januari 2021 oleh UNA, DLR ZLP dan Fraunhofer IGCV. “Kerangka kerja kolaborasi berasal dari proyek yang kami miliki dengan DLR dan Fraunhofer di masa lalu,” kata Sause. “Kami mengambil cetak biru dalam pengembangan produksi berbasis AI dari CosiMo dan sekarang memperluasnya ke skala yang sangat luas. Jadi, misalnya, anggaran untuk pekerjaan kami di CosiMo adalah 10 juta euro, tetapi untuk Jaringan Produksi AI adalah 92 juta euro sebagai pendanaan awal. Ini akan memberi kami kemungkinan untuk memulai banyak proyek penelitian baru seperti CosiMo dalam mengeksploitasi AI di bidang manufaktur. Dan kami tidak bekerja hanya dalam komposit, tetapi kami memiliki fokus yang kuat pada mereka.”
Menggunakan sensor ultrasonik untuk meningkatkan permesinan CNC adalah salah satu proyek yang sudah dimulai pada tahun 2021. “Ada proyek yang akan dimulai pada daur ulang komposit matriks keramik (CMC),” kata Sause, “dan kami akan memiliki beberapa proyek dengan hubungan erat antara manufaktur aditif dan penggunaan kembali bahan yang diperkuat serat secara khusus didaur ulang.”
Adapun peran yang akan dimainkan masing-masing organisasi, Sause menjelaskan tidak ada persaingan, karena setiap lembaga memiliki anggaran yang dialokasikan. “Kita semua memiliki bagian kita masing-masing, dan dengan demikian bebas untuk berkolaborasi seperti yang kita lakukan di masa lalu. Juga, kami saling mengenal dengan baik dan kompetensi, kekuatan dan kelemahan kami. Sangat menyenangkan bekerja bersama karena kami tahu apa yang bisa dan tidak bisa kami lakukan. Kami telah didekati oleh banyak perusahaan yang ingin bekerja sama dengan kami dan sekarang kami sedang mendiskusikan bagaimana menemukan pasangan yang ideal dari sisi kompetensi kami.”
Mengenai fasilitas produksi 5.000 meter persegi, “kita semua akan menjalankannya bersama-sama,” kata Sause. “Kami berencana untuk membuka pada awal 2023 dan mulai memasang mesin. Dan kami akan menyediakan pengaturan produksi otomatis yang menghubungkan sel-sel individual. Banyak dari mereka akan memiliki fokus pada teknologi produksi komposit. Dan kami akan melakukannya untuk juga memamerkan dan menunjukkan kepada mitra dari industri, apa yang dapat dilakukan AI dalam pengaturan produksi seperti itu. Kami juga ingin memiliki mitra dari industri yang masuk dan juga menempatkan mesin di fasilitas kami sehingga kami dapat menjalankan proyek bersama untuk melihat cara menautkan dan mengintegrasikan solusi baru untuk situs mereka.”