Teknologi Sintering untuk Bijih Besi dan Optimalisasi Desain Mesin Sinter
Teknologi Sintering untuk Bijih Besi dan Optimalisasi Desain Mesin Sinter
Teknologi sintering dalam bentuk yang paling dasar sangat sederhana dan telah digunakan sejak awal abad kedua puluh. Namun, meskipun teknologi dasarnya sederhana, kontrol proses bergantung pada sejumlah parameter proses yang saling bergantung yang sangat kompleks dan memerlukan pemahaman menyeluruh tentang pengaruh parameter ini terhadap kapasitas produksi dan kualitas sinter.
Teknologi sintering dasar
Teknologi sintering pada dasarnya adalah proses aglomerasi untuk bijih besi halus yang bergantung pada panas untuk melelehkan permukaan partikel yang lebih kecil bersama-sama untuk membentuk aglomerat yang lebih besar. Sebuah pabrik sinter khas terdiri dari sejumlah unit operasi berurutan dengan mesin sinter di jantung pabrik. Urutan proses yang disederhanakan adalah sebagai berikut.
Bahan baku yang terdiri dari bijih besi halus, coke angin, pengubah terak seperti batu kapur, dolomit, bijih mangan, kapur, kuarsit, dan pasir dll, dan bahan limbah seperti skala pabrik, penyaringan, debu, lumpur, dan terak konverter dll dikumpulkan dan dikirim ke sistem pencampuran. Bahan baku dicampur dalam drum pencampur yang berputar setelah penambahan butiran halus sinter dan air untuk mencapai umpan hijau untuk suatu proses. Proses pencampuran biasanya disebut sebagai 'nodulizing'. Umpan hijau bernodul dibebankan ke untaian mesin sinter di atas lapisan perapian berukuran untuk membentuk 'tempat tidur sinter'. Tempat tidur ini melewati tungku pengapian (hood) untuk memulai reaksi. Pembakar di kap mesin menyalakan karbon dalam umpan hijau yang diisi dalam bentuk angin kokas. Reaksi tersebut disebarkan oleh reaksi kimia antara karbon dan udara yang dihisap melalui sinter bed oleh exhaust fan. Sinter terbakar secara vertikal sementara unggun bergerak secara horizontal menuju ujung pelepasan. Bahan yang disinter dibuang melalui penghancur sinter panas ke pendingin sinter, di mana udara sekitar dihembuskan melalui bahan panas sinter yang dihancurkan dari bawah. Setelah pendinginan, sinter dibawa ke bagian penghancuran dan penyaringan di mana ukurannya dan akhirnya dibawa ke gudang penyimpanan tanur sembur atau ke penyimpanan sinter.
Mesin sinter yang biasa digunakan adalah mesin garis lurus untuk pabrik sinter besar dan mesin annular untuk pabrik sinter kecil. Gas buang biasanya dibersihkan dalam siklon dan pemisah elektrostatik sebelum dibuang ke atmosfer.
Selain semua tuntutan lainnya, desain pabrik sinter modern dengan mesin sinter tipe strand adalah untuk memenuhi persyaratan persiapan dan penanganan bahan baku serta ukuran dan penanganan produk bersama dengan kontrol dan instrumentasi yang cukup canggih.
Homogenitas yang unggul dan permeabilitas yang tinggi dari campuran mentah sinter merupakan faktor penentu dalam mencapai produktivitas dan kualitas sinter yang tinggi dengan pengurangan konsumsi energi.
Setelah didinginkan, produk sinter diukur di bagian penghancuran dan penyaringan. Di sana bahan sinter yang didinginkan dirampingkan untuk digunakan dalam tiga aplikasi yang berbeda yaitu (i) mengembalikan halus ke proses sinter, (ii) lapisan perapian, dan (iii) untuk digunakan dalam beban tanur tinggi. Partikel butiran kecil disirkulasikan kembali ke proses sinter, partikel berukuran sedang umumnya digunakan sebagai lapisan perapian untuk perlindungan mobil palet, dan partikel berukuran lebih besar dibawa ke tanur tinggi.
Mesin sinter yang tepat tetap menjadi inti dari teknologi pembuatan sinter dan memiliki komponen utama ( Gambar 1) yaitu (i) mobil pelet, (ii) penggerak untuk sinter strand, (iii) mekanisme take-up, (iv) tungku pengapian, dan (v) dek kecelakaan dan penghancur sinter panas. Garis besar persyaratan desain dan pendekatan teknik untuk komponen mesin sinter ini dijelaskan di bawah ini.
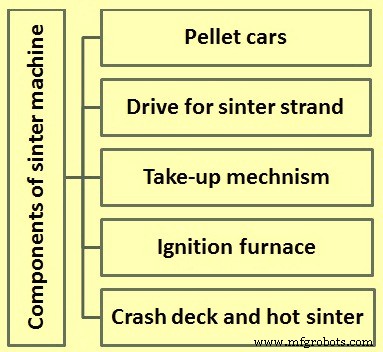
Gbr 1 Komponen utama mesin sinter
Mobil palet
Mobil palet membawa bahan umpan hijau di sepanjang untaian mesin dan di atas kotak angin (di mana ada tekanan sistem negatif) saat proses sintering bahan umpan hijau sedang berlangsung. Untai sinter terdiri dari beberapa mobil pelet dan dapat dianggap sebagai rantai tak berujung yang tidak terhubung karena gerakannya. Oleh karena itu, mobil palet mengalami tekanan akibat hal berikut.
- Paparan terhadap variasi termal siklik karena suhu tinggi yang dialami pada sisi sintering (atas) untaian dan pendinginan mobil yang terjadi di sisi belakang (bawah) bagian untaian.
- Paparan terhadap beban statis siklik dari massa feed/sinter hijau.
- Paparan terhadap beban dinamis siklik dari gaya yang diberikan oleh sproket penggerak, serta oleh mobil palet terhadap satu sama lain.
Meskipun pengembangan mesin sinter tipe untai dan bahan untuk komponennya telah berlangsung selama lebih dari satu abad, faktanya tetap bahwa tugas menuntut yang disebutkan di atas menghasilkan kelelahan bahan yang paling sesuai (nodular, grafit serpihan, dan besi cor putih dll.) dalam jumlah siklus yang terbatas. Oleh karena itu, banyak pabrik sinter biasanya membuat rencana penggantian untuk mobil pelet berdasarkan masa pakai rata-rata 10 tahun, kurang dari 330 hari per tahun.
Pilihan bahan dan bentuk komponen mobil palet selanjutnya ditentukan oleh persyaratan yaitu (i) penurunan tekanan minimal melalui batang parut, (ii) ketahanan abrasi maksimum dari batang parut, (iii) keuletan dan ketahanan abrasi maksimum pelat pipi sehubungan dengan gerakan geser umpan hijau dan bahan yang disinter terhadap bahan yang sama, dan (iv) penggantian cepat komponen yang aus atau tidak dapat diperbaiki oleh personel yang tidak sepenuhnya terampil.
Drive untuk untai sinter
Mobil palet, yang tidak dihubungkan, didorong di sepanjang untaian atas rangka mesin oleh sprocket penggerak, yang dilengkapi dengan cakram susut pada poros umum. Sprocket biasanya dilengkapi dengan segmen gigi yang dapat diganti, cetakan presisi dari baja khusus. Gigi memberikan tindakan bergulir pada roda bagian dalam dari rakitan poros rintisan, yang empat terpasang ke setiap mobil palet. Roda luar dari rakitan poros rintisan berfungsi untuk memandu palet pada titik kembalinya, yaitu di stasiun penggerak dan pelepasan, sedangkan roda dalam membawa beban statis dan dinamis saat palet didorong sepanjang untai.
Penggerak untai sinter biasanya tidak ditempatkan di ujung pelepasan untai, karena alasan panas dan perawatan. Pilihan penggerak utama yang tersedia adalah (i) elektro-mekanis, dengan penggerak kecepatan variabel, atau (ii) elektro-hidraulik, dengan pompa atau motor perpindahan variabel. Dimungkinkan untuk menggunakan drive ganda atau tunggal. Alasan utama dalam pemilihan penggerak dan pengaturan penggerak adalah (i) pengurangan beban yang digantung, dengan menggunakan planetary gear-box yang dipasang di poros, (ii) rentang kecepatan, dan (iii) pemeliharaan.
Mekanisme penerimaan
Mekanisme pengambilan disediakan untuk mengimbangi ekspansi termal diferensial antara mobil palet yang bergerak dan rangka bersama dengan rel dan kotak angin dari mesin sintering, sambil mempertahankan tekanan yang memadai untuk menghindari pemisahan permukaan bodi palet. Mekanisme pengambilan umumnya otomatis melalui sistem counterweight/pulley, atau dengan sistem hidrolik. Manfaat sistem hidraulik adalah (i) tekanan minimum dapat dipertahankan untuk mengurangi keausan gesekan antara permukaan bodi palet, dan (ii) penggantian rakitan palet tunggal (membuka untaian) difasilitasi dengan penggunaan silinder kerja ganda (atau silinder).
Pembuat mesin untuk alasan teknis yang sah biasanya menyediakan untaian mesin besar, mekanisme pengambilan yang terletak di ujung pelepasan untaian. Tetapi untuk mesin yang lebih kecil, lebih layak untuk menyediakan mekanisme pengambilan di ujung hard drive yang dingin. Dalam kedua kasus tersebut, mekanisme masing-masing harus dirancang sebagai unit bergerak, baik dipasang pada susunan roda/rel, atau digantung darinya. Mekanisme pemandu yang akurat, yang memungkinkan penyelarasan stasiun penggerak pada garis tengah untai, diperlukan.
Tungku pengapian
Tungku pengapian dalam mesin sinter dapat digambarkan sebagai kotak baja berlapis tahan api, di mana dua atau lebih pembakar yang berlawanan secara horizontal diatur. Setiap jenis bahan bakar, seperti bahan bakar gas (gas oven kokas, gas tanur sembur, gas campuran, atau gas alam dll.), bahan bakar cair, atau bahan bakar padat (batubara bubuk) dapat digunakan sebagai sumber panas. Pintu yang dapat dioperasikan secara vertikal menutup permukaan tungku pengapian hingga ke tingkat atas umpan hijau, untuk meminimalkan kehilangan panas. Tujuan tungku pengapian adalah untuk menyalakan lapisan atas dengan menyalakan karbon dari angin kokas di umpan hijau.
Untuk memenuhi persyaratan di atas, tungku pengapian harus dilengkapi dengan fitur berikut.
- Nyala api burner harus beroperasi dengan kecepatan rendah untuk menghindari gangguan green feed bed.
- Api berbentuk datar bermanfaat untuk penyalaan umpan hijau yang cepat dan merata.
- Penyediaan yang sesuai sangat penting untuk mendapatkan pasokan udara pendingin yang terkontrol ke burner untuk mencapai suhu nyala yang diinginkan.
- Harus tersedia kontrol burner yang memadai dan mudah dioperasikan.
- Semua kontrol tungku harus aman dari kegagalan.
- Api pilot harus dapat diandalkan, mis. jika pembakar dioperasikan dengan gas dengan nilai kalori yang rendah dan/atau berfluktuasi, seperti gas tanur sembur atau gas campuran, maka nyala api percontohan harus dioperasikan dengan bahan bakar gas cair (LPG).
Deck-crash dan penghancur sinter panas
Crash-deck disediakan untuk memandu material sinter panas, saat dikeluarkan dari gerbong palet, ke dalam hot sinter crusher yang juga kadang-kadang disebut 'finger crusher'. Karena dek tabrakan dapat mengalami benturan dan abrasi yang parah, dek tersebut dilapisi dengan lapisan tebal. Di beberapa mesin, dek kecelakaan dilapisi dengan kubus keramik. Masa pakai liner ini harus sesuai dengan periode pemeliharaan tanaman terjadwal tahunan. Untuk mesin sintering berkapasitas lebih kecil, pelapisan dek tabrakan biasanya dilakukan dengan pelat tahan pakai, atau bahkan dengan pelat tuang dari bahan tahan aus yang biasanya dianggap memadai.
Penghancur sinter panas mengurangi gumpalan kue sinter hingga ukuran lebih kecil dari 150 mm, sebagai persiapan untuk pendinginan dan penghancuran sekunder. Karena kue sinter mempertahankan suhu sekitar 850 derajat C pada saat meninggalkan untaian, penghancur sinter panas beroperasi di lingkungan yang sangat tidak bersahabat. Oleh karena itu desain penghancur sinter panas adalah untuk menjaga lingkungan yang tidak bersahabat ini. Masalah ini ditangani dengan fitur desain berikut seperti (i) jari/roda jari yang dapat ditukar, (ii) bantalan berpelindung, (iii) poros berpendingin air (pada mesin sinter yang lebih besar), dan (iv) penggantian poros lengkap yang cepat perakitan, termasuk jari, bantalan dan pelindung bantalan. Hal ini menuntut fasilitas untuk menghilangkan kanopi debu dengan mudah, serta melepas drive penghancur dengan mudah.
Teknologi pendinginan sinter dengan alternatif pemulihan panas
Pendingin sinter sering menjadi penghambat produksi sinter, dengan teknologi yang sudah ketinggalan zaman yang menyebabkan produktivitas rendah dan biaya operasi dan pemeliharaan yang tinggi. Biasanya pendingin annular digunakan untuk pendinginan sinter. Di beberapa mesin sintering, pendingin garis lurus juga digunakan.
Desain pendingin annular sekarang pada dasarnya terdiri dari konstruksi rangka cincin yang kaku untuk pemusatan material yang mudah dan berkelanjutan. Desain canggih dari saluran pengisian pendingin memastikan distribusi sinter yang lebih homogen ke pendingin sinter, menjaga potongan dengan diameter lebih besar di dekat bagian bawah dan yang lebih kecil di bagian atas. Hal ini meningkatkan kinerja pendinginan, mengurangi konsumsi daya kipas, dan mencegah kerusakan pada peralatan terkait. Pendingin memiliki segel karet khusus antara bak pendingin yang bergerak dan sistem saluran udara yang menghasilkan pemanfaatan udara pendingin yang lebih efisien.
Untuk lebih meningkatkan efisiensi energi pembangkit sinter, sejumlah jenis sistem pemulihan panas yang berbeda dipasang di pendingin sinter, di mana panas sensibel dari udara keluar digunakan untuk menghasilkan energi listrik atau uap proses. Ada tiga kemungkinan alternatif pemulihan panas yang umumnya digunakan. Ini adalah (i) pemanasan awal udara pembakaran untuk tungku penyalaan dan pasca pemanasan sinter yang baru dinyalakan, (ii) sistem resirkulasi gas limbah selektif, menyediakan konservasi kokas dan CO2 (karbon di oksida), dan (iii) panas limbah pabrik pemulihan untuk pembangkit tenaga uap dan/atau listrik.
Peran pengujian saat mendesain pabrik sintering
Biasanya pengujian saat merancang pabrik sintering memiliki tiga tujuan. Tujuannya termasuk (i) untuk mengkonfirmasi parameter proses tertentu yang telah dipilih sebelumnya berdasarkan pabrik sinter serupa yang ada, (ii) untuk menilai parameter yang dipilih dalam hal kapasitas produksi yang diusulkan dari pabrik sinter, dan (iii) untuk mendapatkan informasi desain yang spesifik ke pabrik sintering yang diusulkan.
Mengubah parameter seperti persentase penambahan angin kokas dan pada tingkat lebih rendah juga persentase penambahan air biasanya digunakan untuk mencapai titik optimasi untuk satu set parameter operasi. Jika rangkaian kondisi dipilih cukup mendekati target, pengoptimalan dinilai dengan 'rasio halus sinter' (berat butiran halus yang dihasilkan / berat butiran halus yang dikembalikan ke umpan hijau) yang harus sedekat mungkin dengan 1 (sinter dianggap baik jika rasionya antara 0,95 dan 1,05).
Jika variasi angin air dan kokas gagal mencapai rasio butiran halus sinter, maka hanya dapat dioptimalkan lebih lanjut dengan mengubah masukan butiran halus sinter ke campuran umpan hijau untuk kedalaman lapisan dan penurunan tekanan (hisap) yang ditetapkan.
Parameter proses berikut biasanya awalnya diidentifikasi untuk mesin garis lurus dan ditetapkan pada nilai yang telah dipilih sebelumnya untuk pengujian.
- Tekanan hisap – pengukur air (WG) 1200 hingga 1400 mm
- Tinggi tempat tidur – 400 hingga 450 mm
- Waktu penyalaan – 1,5 – 2,0 menit
- Suhu penyalaan – Sekitar 1000 derajat C
- Lapisan perapian – 30 hingga 50 mm
- Denda pengembalian – 25% hingga 30% dari produksi sinter
Alternatif pengujian umumnya dipilih berdasarkan proyeksi persyaratan operasi dari pabrik sinter yang diusulkan. Beberapa alternatif yang disarankan adalah (i) base case hanya terdiri dari bijih halus tanpa penambahan debu atau lumpur, (ii) dengan persentase tertentu dari debu dan lumpur yang ditambahkan ke bijih halus tetapi tanpa nodulisasi, dan (iii) dengan persentase tertentu. persentase debu dan lumpur yang ditambahkan ke butiran halus, tetapi kali ini dinodulisasi terlebih dahulu sebelum dicampur dengan butiran halus.
Peran penambahan air
Air ditambahkan ke campuran sinter untuk berbagai alasan, yang paling penting adalah propagasi aglomerasi debu halus ke partikel yang lebih besar selama proses pembentukan nodul. Ini bersama dengan waktu pembentukan nodul memainkan peran penting dalam kontrol permeabilitas campuran sinter dan akibatnya kue sinter. Namun, hal itu juga mempengaruhi kualitas kue sinter (kekuatan dingin) dan tingkat produksi, hasil dan rasio halus sinter. Oleh karena itu, ada kebutuhan kontrol kelembaban selama proses sintering. Biasanya ketika tingkat penambahan air tinggi maka energi yang lebih tinggi diperlukan selama sintering dan ketika tingkat penambahan air lebih rendah dari yang dibutuhkan maka nodulizing yang tepat tidak terjadi. Oleh karena itu tingkat penambahan air perlu dioptimalkan melalui pengujian. Karena alasan ini, kontrol penambahan air yang optimal sangat penting untuk operasi yang stabil dan penyediaan yang memadai untuk ini diperlukan selama desain. Namun, penambahan air adalah parameter yang dapat dengan mudah dioptimalkan lebih lanjut selama commissioning pabrik skala penuh.
Penambahan coke semilir
Reaksi sintering diperbanyak dengan peleburan lapisan permukaan partikel individu dari bijih halus dan menggabungkannya bersama-sama. Panas (energi) yang tersedia untuk reaksi ini dikendalikan oleh reaksi antara karbon dari angin kokas yang ditambahkan ke campuran sinter dan oksigen dari udara yang dihisap melalui unggun. Interaksi antara dua parameter ini kompleks dan memainkan peran besar dalam menentukan keluaran proses yaitu laju produksi, hasil, rasio halus sinter, dan kualitas sinter untuk serangkaian parameter proses tetap tertentu.
Penting untuk dicatat bahwa tidak ada parameter proses yang berbeda (penurunan tekanan, hasil, laju produksi, suhu penyalaan, dan penambahan angin kokas, dll.) yang benar-benar independen satu sama lain. Namun, jumlah karbon dalam bentuk angin kokas yang ditambahkan ke umpan sinter hijau mungkin yang paling penting untuk dikontrol karena menentukan perilaku lapisan selama sintering dan juga mempengaruhi sifat pendinginan sampai batas tertentu.
Biasanya, dengan terlalu banyak karbon dalam campuran sinter, unggun menyatu terlalu jauh dan mulai menutup, mencegah aliran udara melalui unggun untuk penurunan tekanan tetap. Hal ini pada gilirannya menyebabkan waktu sintering yang lama dan tingkat produksi yang rendah. Sebaliknya, terlalu sedikit karbon dalam campuran sinter mencegah sintering yang memadai dan meningkatkan jumlah pengembalian halus dari proses, pada saat yang sama menurunkan hasil. Pengujian adalah cara terbaik untuk menentukan persentase karbon (angin coke) yang dibutuhkan untuk optimalisasi proses sintering.
Selama pengujian yang dilakukan untuk desain pabrik, satu set parameter dipilih berdasarkan data terbaik yang tersedia untuk campuran sinter hijau tertentu. Jumlah angin kokas yang ditambahkan ke umpan bervariasi dan efektivitas sintering dinilai oleh jumlah butiran halus (dikurangi fraksi 5 mm) yang dihasilkan oleh proses (bahan dasarnya tidak disinter). Bergantung pada rasio halus input dan output, jumlah hembusan kokas disesuaikan.
Penurunan tekanan
Seperti yang dinyatakan sebelumnya, propagasi reaksi sintering dikendalikan oleh jumlah karbon (angin coke) dan udara dalam sistem karena menyediakan energi untuk reaksi. Namun dalam mesin sinter, sulit dan tidak praktis untuk mengontrol aliran udara melalui unggun dan karenanya, penurunan tekanan dikontrol daripada aliran udara. Jumlah udara yang dihisap melalui unggun sinter tergantung pada permeabilitas campuran sinter di unggun untuk penurunan tekanan tertentu dan karenanya bervariasi sepanjang untai sinter karena perubahan permeabilitas. Penurunan tekanan melalui sistem dijaga konstan pada tingkat yang telah ditentukan oleh hisapan yang dibuat oleh kipas buang sistem pembersih gas. Kontrol kotak hisap individu dimungkinkan secara online tetapi tidak perlu, kecuali untuk kotak di bawah kap mesin. Pengapian terjadi pada sekitar 180 -200 mm WG, sebagian besar tidak tergantung pada kedalaman lapisan, tetapi penurunan tekanan sinter terkait dengan kedalaman lapisan.
Kedalaman tempat tidur
Praktis, ada banyak konfigurasi pabrik sinter yang mungkin untuk tingkat produksi tertentu meskipun memvariasikan lebar, panjang atau kedalaman lapisan yang memiliki dampak yang sedikit berbeda. Efek utama dari lapisan yang lebih dalam adalah karena hubungan antara luas permukaan dan volume sinter yang dihasilkan. Dengan bertambahnya kedalaman lapisan, rasio volume terhadap luas meningkat dan karenanya diharapkan permukaan halus yang tidak disinter lebih kecil. Hal ini biasanya berdampak pada rasio hasil dan halus sinter, tetapi belum tentu tingkat produksi.
Sebagai aturan, asalkan penurunan tekanan disesuaikan, laju produksi tidak terpengaruh karena pada kecepatan sintering vertikal tetap (kecepatan pembakaran melalui unggun juga dikenal sebagai kecepatan depan nyala api) memerlukan jumlah waktu yang proporsional untuk kedalaman unggun yang berbeda. Namun, hal itu dapat berdampak pada kecepatan horizontal untai sinter karena titik bakar bergeser dengan waktu sintering.
Biasanya terlihat bahwa campuran sinter bekerja lebih baik dengan lapisan yang lebih dalam. Rasio halus sinter dan kecepatan untai untuk unggun yang lebih dalam jauh lebih dapat diterima dengan tetap mempertahankan kapasitas produksi yang diperlukan. Manfaat tambahan dari tempat tidur yang lebih dalam adalah konsumsi angin coke, yang turun secara substansial. Juga secara umum terlihat bahwa dengan bertambahnya ketinggian tempat tidur, ada beberapa fleksibilitas dalam hal penurunan tekanan yang diperlukan melalui tempat tidur.
Waktu penyalaan
Penyalaan umpan sinter hijau adalah dengan pembakar yang mungkin dinyalakan dengan sumber bahan bakar apa pun. Waktu penyalaan tidak dianggap sebagai parameter kritis selama angin kokas di lapisan atas cukup tersulut untuk menyebarkan reaksi lebih lanjut melalui unggun. Tergantung pada sumber bijih, waktu pengapian dapat bervariasi dari 0,5 hingga 2,0 menit, tetapi biasanya waktu pengapian 1,5 menit dianggap cukup.
Suhu penyalaan
Berlawanan dengan waktu pengapian, suhu pengapian biasanya dianggap kritis. Suhu selama pengapian mengontrol jumlah lapisan atas dan sebagai konsekuensinya juga menghasilkan produk akhir dari untaian. Selain itu juga dapat mempengaruhi kualitas produk akhir (kekuatan), rendemen produk dan laju produksi. Lebih lanjut, telah sering diamati bahwa kejutan termal dari suhu pengapian yang terlalu tinggi menyebabkan pembentukan retakan di sepanjang sinter bed di mana arus pendek aliran udara biasanya terjadi. Di area yang berdekatan dengan retakan ini, terjadi sintering yang tidak lengkap yang dianggap sebagai penyebab utama hasil yang lebih rendah, tingkat produksi yang lebih rendah, dan kualitas sinter yang buruk.
Namun, perlu dicatat bahwa suhu penyalaan dan energi yang dibutuhkan untuk penyalaan tidak sama dan tidak boleh dikacaukan satu sama lain. Selanjutnya, kedua parameter ini idealnya dikontrol secara individual yang biasanya sulit dilakukan di pabrik sinter.
Lapisan perapian
Lapisan perapian pada dasarnya memiliki satu fungsi non-kritis yaitu untuk mencegah kerusakan pada mobil palet dan batang kisi yang disebabkan oleh sintering kue ke perapian. Telah terlihat bahwa beberapa campuran sinter yang dibuat dari bijih besi kadar rendah tertentu bahkan tidak memerlukan lapisan perapian. Biasanya efek yang sangat kecil dari ketebalan lapisan perapian dan distribusi ukuran pada permeabilitas kue sinter diharapkan tetapi mereka tetap tidak signifikan untuk semua tujuan praktis. Namun, ada satu kekhawatiran yang ada selama operasi pabrik sinter adalah bahwa akan ada kesulitan dengan kontinuitas pasokan lapisan perapian resirkulasi. Kadang-kadang tidak ada cukup jumlah kisaran ukuran yang benar yang tersedia untuk memasok lapisan perapian. Dalam kasus seperti itu, ada kebutuhan untuk mengontrol penghancuran sinter di hilir dalam proses sinter.
Hasil sinter
Hasil dari proses sintering umumnya dinyatakan sebagai jumlah sinter yang dihasilkan dibandingkan dengan jumlah bahan baku yang dimasukkan ke dalam proses. Tergantung pada batas baterai perhitungan, (ujung untai atau produk akhir) hasil perhitungan mungkin berbeda. Hasil akhir untai hanya menunjukkan kerugian karena LOI (kehilangan penyalaan) dan debu yang tersedot ke sistem gas buang sementara hasil produk akhir juga memperhitungkan pembentukan fraksi halus ( kurang dari 5 mm). Berdasarkan analisis bahan masukan, biasanya diharapkan LOI sekitar 20% dan hasil sinter ujung untai sebesar 80%.
Tingkat produksi
Tingkat produksi atau indeks produksi telah menjadi norma dimana kapasitas pabrik sinter dinilai dan biasanya dinyatakan sebagai massa sinter yang diproduksi per meter persegi area perapian aktif per jam. Di beberapa tempat dinyatakan sebagai massa sinter yang dihasilkan per meter persegi area perapian aktif per 24 jam. Namun, mungkin ada beberapa kebingungan mengenai definisi area perapian aktif serta batas baterai (ujung untai dibandingkan dengan produk akhir) yang mungkin terjadi. Oleh karena itu, praktis untuk mendefinisikan istilah sebagai berikut.
- Batas baterai untuk massa sinter yang dihasilkan adalah setelah penyaringan produk akhir dan oleh karena itu tidak termasuk butiran halus yang didaur ulang ke umpan sinter hijau dan mengabaikan fraksi lapisan perapian, yang dianggap sebagai beban resirkulasi terus menerus.
- Area perapian aktif didefinisikan sebagai total area yang tersedia untuk sintering dari awal inlet kap pengapian hingga titik pembakaran. Perlu dipahami bahwa jika jenis bijih tertentu terbakar lebih cepat dari yang lain pada untai yang sama, itu tidak secara otomatis berarti bahwa tingkat produksi lebih tinggi. Kecepatan untai perlu diatur untuk mendorong titik bakar ke ujung untai untuk meningkatkan area untai aktif. Hal ini pada gilirannya meningkatkan tingkat produksi.
Rasio denda sinter
Rasio halus sinter adalah parameter yang menentukan kinerja proses sintering. Oleh karena itu masuk akal untuk mengatakan bahwa yang ideal adalah bertujuan untuk rasio 1 di mana jumlah butiran halus yang dihasilkan sama dengan jumlah yang dikembalikan ke umpan hijau dan proses berada dalam keseimbangan. Dalam proses sintering rasio halus sinter umumnya diperbolehkan bervariasi antara 0,95 dan 1,05, yang memerlukan kebutuhan penyimpanan buffer.