Sensor dielektrik DC untuk produksi komposit industri
Karena produsen berusaha untuk secara bersamaan mengurangi biaya dan meningkatkan tingkat produksi suku cadang komposit, kemampuan untuk melihat proses pencetakan bagian dalam secara real time dan memantau aliran resin, viskositas, suhu, tekanan, dan Tg/keadaan penyembuhan menjadi pembeda. Synthesites (Uccle, Belgia) telah mengembangkan kemampuan ini. Berdasarkan hasil yang dilaporkan oleh Pusat Dirgantara Jerman (DLR, Stade) dan Pusat Komposit Nasional (NCC, Bristol, Inggris), teknologi ini berpotensi memangkas waktu siklus hingga 50%, dengan keputusan penyembuhan berdasarkan Tg dan derajat penyembuhan per resin dan bagian vs periode waktu konservatif berdasarkan studi bahan generik. Faktanya, ini adalah kemajuan menuju produksi Komposit 4.0, menggunakan data dari sensor untuk mengontrol proses dan peralatan, dan juga untuk meningkatkan simulasi dan desain.
Saya pertama kali melaporkan di Synthesites melalui proyek OPTO-Light (lihat “Termoset termoplastik yang ditampung , siklus 2 menit, satu sel"). Faktanya, kemampuan untuk menggabungkan termoplastik ke termoset di OPTO-Light tanpa permukaan yang dilapisi laser dimungkinkan dengan menggunakan sensor cetakan untuk tekanan, suhu, resistivitas arus searah (DCR) dan analisis dielektrik (DEA). Sensor DCR dipasok oleh Synthesites dan sensor untuk DEA dipasok oleh Netzsch (Selb, Jerman). Keduanya adalah sensor dielektrik yang mengukur sifat listrik resin. Saya akan membahas sejarah dan perbedaan teknologi tersebut di bawah ini.
Teknologi yang telah dikembangkan Synthesites dengan berbagai pelanggan komersial sangat mengesankan, termasuk produksi industri bilah angin dan sayap yang diresapi resin untuk Seri-C, sekarang Airbus 220. Teknologi ini juga telah didemonstrasikan untuk berbagai bahan dan proses, termasuk autoklaf -prepreg yang diawetkan, infus resin, dan pencetakan transfer resin tekanan tinggi (HP-RTM).
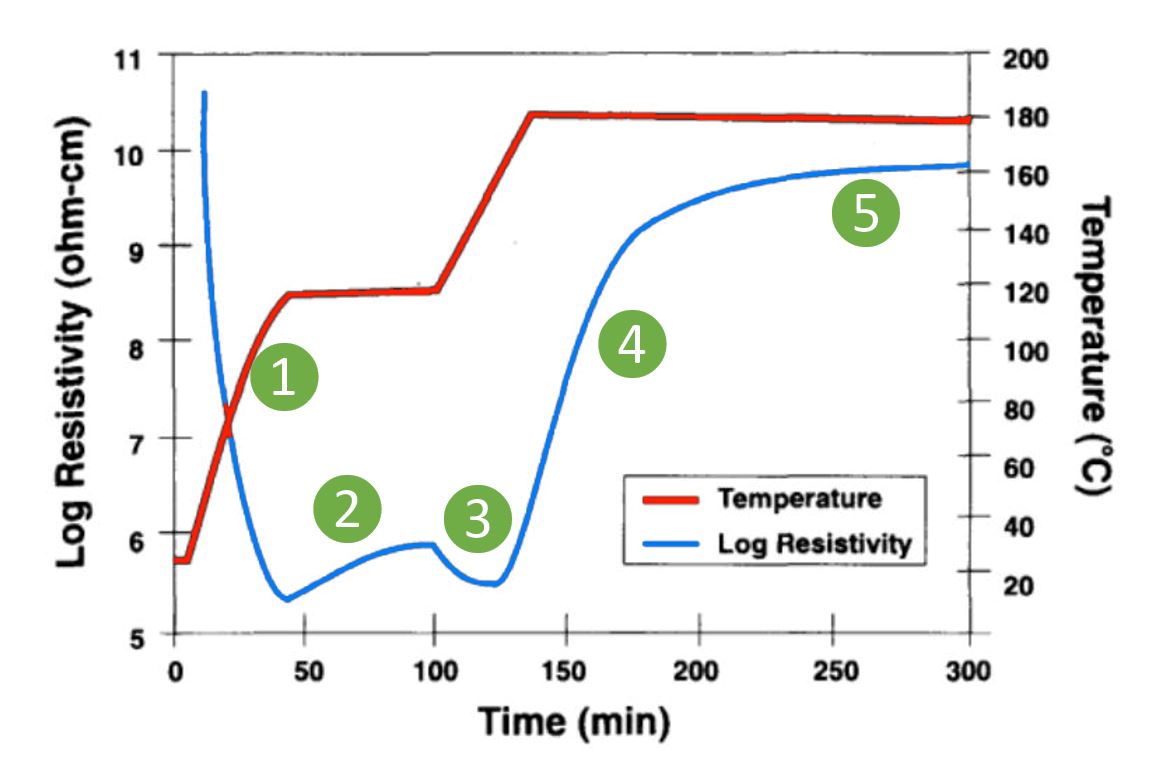
- Penurunan awal resistivitas mencerminkan penurunan viskositas resin selama ramp hingga 120 °C.
- Selama diam ini pada 120°C, resistivitas meningkat seiring dengan meningkatnya viskositas resin karena reaksi resin dan hilangnya volatil.
- Resistivitas menurun lagi dan mencapai minimum saat resin dipanaskan hingga 177°C.
- Resistensi kemudian meningkat dengan cepat saat reaksi penyembuhan berlangsung dengan cepat.
- Peningkatan resistivitas melambat saat reaksi curing melambat, mendekati kemiringan nol setelah 300 menit saat reaksi curing hampir selesai.
SUMBER | Karakterisasi Nondestructive Material VIII diedit oleh Robert E. Green, hal. 385.
Konduktivitas ion berbanding terbalik dengan viskositas resin sebelum gelasi dan dengan kekakuan setelah gelasi (mobilitas ion tinggi, viskositas resin rendah, dan kekakuan rendah). Kebalikan dari konduktivitas ion, resistivitas, dengan demikian secara langsung berhubungan dengan perubahan viskositas/kekakuan dalam resin matriks.
Peningkatan resistivitas telah terbukti berkorelasi dengan peningkatan Tg. Ini adalah dasar dari resistivitas arus searah (DCR), yang hanya DEA menggunakan arus searah (DC), dan deskripsi awalnya diberikan untuk proses Sintesa dikembangkan.
Seperti dijelaskan di atas, teknik penggunaan tegangan DC untuk DEA ini didasarkan pada korelasi antara resistivitas dan keadaan penyembuhan. Ini dilaporkan pada tahun 1962 oleh R.W. Warfield dalam “Properties of Crosslinked Polymers as Evidenced by Electrical Resistivity Measurements”, Makromoleculare Chemistry, Jil. 58. (Lihat bagian bawah untuk referensi yang digunakan di bagian ini.)
Riwayat sensor DEA dan AC vs. DC
“Ide pemantauan penyembuhan sudah cukup lama,” jelas Dr. Nikos Pantelelis, direktur Synthesites. “Pada 1980-an, metode penginderaan dielektrik dianggap lebih matang daripada yang lain, seperti serat optik. MIT (Massachusetts Institute of Technology) mengerjakannya dan mencoba mengimplementasikannya dalam produksi. Teknologi inilah yang dibeli dan digunakan Netzsch hari ini.”
Synthesites didirikan pada tahun 2008. “Kami mengembangkan teknologi kami dari awal menggunakan sensor listrik dengan arus searah, bukan arus bolak-balik,” Pantelelis menceritakan. “Bagi kami, kelemahan menggunakan sensor dielektrik AC konvensional adalah persyaratan untuk mengeksitasi resin pada rentang frekuensi dan kemudian mengukur respons impedansi untuk berbagai sinyal. Tidak hanya sulit untuk memproses semua data ini, tetapi karena resin berubah dari cair menjadi padat, Anda perlu fokus pada frekuensi sinyal yang berbeda untuk mendapatkan informasi yang tepat.”
Pantelelis mengatakan bahwa sensor DC Synthesites dapat mengukur konduktivitas yang sangat rendah dan resistivitas yang tinggi, "yang diperlukan untuk mengukur transformasi resin selama penyembuhan." Ia menegaskan, penggunaan DEA konvensional hanya pada satu frekuensi untuk mempermudah tidak memberikan data yang akurat. “Kami tidak memiliki banyak frekuensi tetapi hanya menerapkan tegangan konstan. Kelemahannya adalah pendekatan ini sangat sempit, artinya ini bekerja dengan baik untuk aplikasi yang sangat spesifik seperti pengawetan resin tetapi tidak untuk semuanya. Namun, ketika membandingkan kinerja peralatan kami dengan DEA konvensional, peralatan kami dapat mengukur seluruh rentang perawatan bahkan pada suhu yang lebih rendah. Perusahaan yang memasok instrumen dan layanan di luar komposit tidak menyukai pendekatan kami karena memiliki parameter yang terbatas untuk disesuaikan.”
Ini bukan masalah bagi Synthesites karena memiliki komposit yang ditargetkan secara khusus. “Pendekatan kami bekerja dengan baik di berbagai resin komposit dan proses, termasuk termoset, RTM, prepreg, dan bahkan termoplastik reaktif seperti Elium.” (Elium adalah termoplastik dengan viskositas rendah dari Arkema (Colombes, Prancis) yang dapat diproses menggunakan infus resin.)
Jika DEA menggunakan DC dikenal di tahun 1960-an, lalu mengapa sensor AC disukai di tahun 1980-an dan terus maju? “Tiga puluh tahun yang lalu, teknologi DEA yang menggunakan sensor DC belum begitu berkembang,” kata Pantelelis. “Tetapi kami telah memajukan pendekatan kami untuk memberikan pengukuran yang sangat halus dan akurat untuk produksi industri. Kami telah mendemonstrasikan dan terus mengembangkan sistem kami dengan pelanggan seperti GE Aviation (Batesville dan Ellisville, Miss., A.S.) dan Bombardier yang memproses sebagian besar dengan cetakan resin cair. Sistem kami juga digunakan setiap hari dalam produksi bilah angin dan telah menunjukkan kemampuan untuk produksi industri laminasi prepreg yang diawetkan dengan autoklaf.”
Kontrol proses
Pantelelis menjelaskan bagaimana sensor DC Synthesites hanyalah salah satu bagian dari sistem terintegrasi untuk memantau pemrosesan dan pengawetan komposit. “Kami secara langsung mengukur resistansi dan suhu, dan dari sini kami menghitung viskositas online, derajat gelasi, dan derajat penyembuhan. Kami menggunakan sensor in-mold yang tahan lama, tetapi juga sensor gerbang dan sensor in-line untuk saluran masuk resin, outlet, dan saluran umpan, serta sensor sekali pakai pada suku cadang. Anda menggunakan sensor hanya jika Anda membutuhkannya.”
Sensor suhu adalah detektor suhu resistansi platinum (RTD), yang menawarkan akurasi yang jauh lebih tinggi (dalam 0,1°C) daripada termokopel serta stabilitas selama bertahun-tahun versus kemungkinan penyimpangan pengukuran dengan termokopel. RTD adalah peralatan standar di banyak aplikasi industri. Sensor gerbang (lihat diagram kontrol proses di bawah) adalah biner, melaporkan aliran resin sebagai aktif atau nonaktif, meskipun ada versi kedua yang juga dapat melaporkan viskositas. Synthesites telah mengembangkan sensor untuk digunakan dengan serat karbon tanpa risiko korosi galvanik, sensor yang dapat digunakan melalui kantong vakum dan sensor berbentuk dalam cetakan agar sesuai dengan geometri cetakan.
Komponen selanjutnya adalah unit akuisisi data OPTIFLOW dan OPTIMOLD. OPTIFLOW menyediakan in situ, pemantauan waktu nyata kedatangan resin dan suhu untuk cetakan komposit cair. Ini memverifikasi dan mencatat aliran resin dan dapat mengidentifikasi penyimpangan produksi selama infiltrasi resin. OPTIMOLD menggunakan pengukuran suhu dan ketahanan resin untuk membuat perhitungan dan memantau keadaan resin termasuk rasio campuran, penuaan kimia, viskositas, Tg, dan tingkat penyembuhan. Dapat digunakan dengan proses prepreg dan cetakan cair.
Unit OPTIFLOW dan OPTIMOLD dikendalikan oleh perangkat lunak OPTIVIEW. “Perangkat lunak ini menyediakan akuisisi dan penyimpanan data dan disediakan secara gratis dengan peralatan kami,” Pantelelis menjelaskan. “Kami juga menawarkan perangkat lunak Online Resin State (ORS), opsi yang lebih canggih yang dapat dibeli pelanggan secara ekstra. Ini mengumpulkan input, membuat perhitungan online, dan mengirimkan output untuk kontrol proses yang cerdas.”
Baik sistem OPTIFLOW dan OPTIMOLD terus memeriksa untuk memastikan sensor terhubung dan pembacaan berada dalam jangkauan. “Saat Anda mengandalkan sensor ini untuk kontrol proses, sistem harus membunyikan alarm jika sensor tidak berfungsi atau jika pembacaannya melampaui batas yang ditentukan,” kata Pantelelis. Kedua sistem juga memiliki keluaran relai untuk mengendalikan peralatan proses. Misalnya, katup saluran umpan dapat dibuka atau ditutup berdasarkan data kedatangan resin, dan peralatan pemanas/pendingin dapat diatur berdasarkan viskositas resin. “Anda dapat memasukkan output dari sensor tekanan ke OPTIMOLD,” catat Pantelelis, “dan dengan demikian mengontrol tekanan dalam cetakan berdasarkan data viskositas.”
Pengukuran dan kurva data biasa
Tangkapan layar di bawah ini menunjukkan pengukuran OPTIMOLD dari uji coba RTM kompresi tekanan tinggi (HP-CRTM) di NCC (Bristol, Inggris). Set pertama, dari percobaan sederhana pada 115 °C, menunjukkan bagaimana pengukuran real-time dari resistansi listrik resin dan suhu diubah menjadi perkiraan viskositas dan Tg oleh perangkat lunak ORS.
Pada grafik di bawah, hambatan listrik dan suhu (grafik atas) direkam pada 110° (kiri) dan 120°C (kanan). Di bawah pembacaan resistansi (R) dan suhu (T) adalah grafik yang menunjukkan viskositas yang dihitung dan Tg pada 110°C (kiri) dan 120°C (kanan) . Pengukuran ini berasal dari dua sensor OPTIMOLD yang terletak di bagian cetakan atas (Sn.1 dan Sn.2, foto bawah ) sementara tekanan rongga direkam menggunakan dua sensor tekanan Kistler 6162A (Sn.3 dan Sn.4).
Semua data yang direkam oleh sensor in-mold serta peralatan press dan injeksi dapat disusun menjadi satu file log, memungkinkan gambar detail dari proses manufaktur untuk setiap komponen yang dibuat.
Mengurangi waktu penyembuhan
“Kami memiliki potensi untuk menurunkan waktu penyembuhan lebih dari 30% karena produsen dapat melihat Tg secara real time, sehingga mereka dapat memutuskan kapan harus menghentikan siklus penyembuhan,” Pantelelis menjelaskan. “Mereka tidak perlu menunggu untuk menyelesaikan siklus warisan yang lebih lama dari yang diperlukan. Misalnya, siklus lama untuk RTM6 adalah 2 jam pada 180 °C untuk penyembuhan penuh. Kami telah melihat bahwa dalam geometri tertentu ini bisa berlangsung hingga 70 menit.”
Tujuannya kemudian, adalah untuk menghentikan proses setelah penyembuhan selesai? “Ini bukan tentang penyembuhan penuh tetapi mencapai tingkat penyembuhan yang dibutuhkan setiap komponen,” kata Pantelelis. “Penyembuhan penuh membutuhkan waktu terlalu lama. Kuncinya adalah mampu melihat kapan penyembuhan yang cukup tercapai. Produsen kincir angin memiliki target Tg. Ketika mereka mencapai itu, mereka dapat mulai mendingin. Jadi yang dibutuhkan adalah sensor yang dapat memberikan pengukuran Tg yang sangat akurat secara real-time.”
Synthesites menyelesaikan proyek demonstrasi dengan Hutchinson (Paris, Prancis) untuk memproduksi bilah suspensi otomotif yang dibuat dengan serat kaca/epoksi dan RTM untuk proyek ECOMISE yang didanai UE (Mengaktifkan Manufaktur Komposit Generasi Berikutnya oleh Evaluasi Struktural dan Penyesuaian Proses In-Situ, 2013 -2016). Tujuan dari proyek ini adalah untuk mengoptimalkan siklus RTM berdasarkan pemantauan proses waktu nyata:
- Ramp pemanas pertama akan dipicu oleh penyelesaian infiltrasi resin berdasarkan sensor.
- Ramp pemanasan kedua akan dipicu oleh penyelesaian penyembuhan berdasarkan perhitungan Tg.
- Pendinginan akan dipicu oleh penyelesaian pasca-penyembuhan berdasarkan perhitungan Tg.
Sistem Synthesites terdiri dari dua (2) dalam cetakan sensor untuk penyembuhan (CS1, CS2), satu (1) dalam cetakan sensor untuk aliran dan suhu resin (Sensor Aliran 1) dan delapan (8) sekali pakai sensor untuk aliran/suhu resin — empat (4) tertanam ke bagian uji dan empat (4) terpasang ke permukaan pahat.
“Unit OPTIMOLD dan OPTIFLOW dapat dihubungkan bersama melalui ethernet sehingga semua sensor dapat direkam dalam satu sesi Optiview,” jelas Pantelelis. “Dengan demikian, CS1 dan CS2 terhubung ke dua unit OPTIMOLD, sensor aliran dalam cetakan 1 dan delapan sensor aliran sekali pakai terhubung ke tiga unit OPTIFLOW.”
Sistem sensor, unit akuisisi data OPTIMOLD/OPTIFLOW dan perangkat lunak OPPTIVIEW/ORS ini kemudian diterapkan selama uji coba pencetakan RTM untuk menetapkan target untuk berbagai tahap proses, termasuk injeksi/infiltrasi resin dan dua target Tg. “Ini adalah bagian tebal yang dibuat menggunakan serat searah dan resin epoksi Huntsman,” kata Pantelelis. “Dalam hal ini, kami menggunakan sensor kawat aliran untuk memeriksa aliran di dalam lapisan UD ini, yang biasanya padat dan dapat menimbulkan tantangan selama infiltrasi resin.”
Dengan menggunakan sistem kontrol proses ini, proyek ECOMISE di Hutchinson mampu mengurangi siklus penyembuhan hingga lebih dari 30%.
Kalibrasi
Kalibrasi diperlukan untuk pemantauan Tg online. Saat pengukuran dikumpulkan dari sensor melalui unit OPTIMOLD, perangkat lunak ORS menerjemahkannya ke dalam viskositas dan Tg berdasarkan kalibrasi untuk resin spesifik tersebut. “Kalibrasi ini adalah pekerjaan yang dilakukan sebelum pemrosesan untuk memberikan korelasi yang akan digunakan perangkat lunak ORS untuk perhitungannya,” Pantelelis menjelaskan. “Kami mengkalibrasi dengan menempatkan resin dalam rheometer dan mengukur suhu dan viskositas. Dengan menerapkan rumus yang sesuai, Anda kemudian menghitung hambatan yang sesuai dan Tg. Kami mengembangkan kalibrasi resin untuk pelanggan kami berdasarkan standar mereka, dan mempelajari siklus penyembuhan resin yang berbeda. Data kalibrasi ini kemudian digunakan oleh perangkat lunak ORS setiap kali memproses resin tersebut.”
Keakuratan perhitungan Tg real-time perangkat lunak ORS ditunjukkan dalam uji coba oleh produsen bilah angin Carbon Rotec Composite Technology (Lemwerder, Jerman). Tg yang dihitung secara online oleh perangkat lunak ORS dibandingkan dengan Tg yang diukur tepat setelah pembongkaran dengan melakukan Diferensial Scanning Calorimeter (DSC). Untuk pengolahan isotermal, perbedaan rata-rata adalah 1,61°C dan untuk pengolahan non-isotermal adalah 2,15°C.
“Akurasi ini telah berulang kali ditunjukkan dalam proyek pribadi dengan pelanggan lain,” kata Pantelelis.
Kemajuan untuk produksi industri
Kontrol proses yang digerakkan oleh sensor dan data ini memang merupakan langkah besar menuju manufaktur Komposit 4.0 yang sepenuhnya otomatis dan cerdas. Meskipun telah didemonstrasikan di ECOMISE dan juga dengan NCC di Bristol, itu belum digunakan dalam produksi sehari-hari. “Ide menggunakan sensor untuk melihat Tg dan kemudian memulai pendinginan memang telah dimulai dalam pembuatan bilah angin,” lapor Pantelelis, “tetapi belum sepenuhnya otomatis. Sistem alarm ketika target Tg tercapai dan kemudian operator menghentikan siklus penyembuhan. Otomatisasinya mudah, dan akan selesai setelah pabrikan memvalidasi akurasi sistem selama fase uji coba.”
“Untuk mencapai target ini, kami telah mengembangkan workstation baru untuk memungkinkan operator produksi mengawasi proses otomatis, yang tidak memerlukan masukan dari pihaknya,” lanjutnya. “Kami telah melihat dalam pembuatan bilah turbin angin yang menggunakan satu stasiun kerja selama pengawetan resin dan perekat dapat mempersingkat waktu siklus setidaknya 2-3 jam tanpa mengorbankan kualitas.”
Meskipun Bombardier Belfast, sekarang Spirit AeroSystems, menggunakan peralatan Synthesites dalam produksi sayap komposit yang diresapi resin untuk C-Series, sekarang Airbus A220, kontrol prosesnya tidak otomatis. Namun, Synthesites juga bekerja dengan Bombardier di ECOMISE, dan pengembangan itu terus dilakukan. Salah satu pencapaian utama adalah sensor yang mengalir melalui dinding autoklaf. Seperti yang dijelaskan di blog saya tahun 2013, “sayap komposit C-Series”:
Bombardier disuntikkan setelah layup ditempatkan di autoclave berdiameter 5,6m sepanjang 21,3m, memungkinkan suhu dan tekanan dipertahankan pada tingkat yang diperlukan untuk mengurangi viskositas dan wetout — Cytec 890 adalah disuntikkan pada 80˚C. . . Setelah injeksi resin selesai, tekanan positif diterapkan dalam autoklaf selama konsolidasi, menyebabkan elemen perkakas menutup, memadatkan laminasi basah dan mengeluarkan kelebihan resin kembali dari saluran masuk resin ke tempat pembuangan resin yang dirancang khusus.
“Seperti kebanyakan produsen di ruang angkasa komersial, mereka tertarik untuk memastikan kualitas dan tingkat kenaikan,” jelas Pantelelis. Tata letak di bawah dan hasil dari ECOMISE adalah untuk demonstran, bukan bagian komersial. Ini menggunakan dua unit OPTIMOLD dengan dua sensor penyembuhan dalam cetakan dan tiga unit OPTIFLOW dengan empat sensor aliran dalam cetakan dan empat sensor sebaris pada saluran vakum. “OPTIFLOW dapat memantau hingga empat kedatangan resin dan empat sensor suhu/resistensi,” catat Pantelelis. “Target demonstrasi tercapai sepenuhnya. Kami membuktikan bahwa sensor, kabel, dan sistem dapat bekerja tanpa masalah di bawah spesifikasi kedirgantaraan yang paling menantang. Sangat menarik bahwa pengukuran kedatangan resin menunjukkan perbedaan besar dibandingkan dengan simulasi aliran. Selain itu, pemantauan Tg online menunjukkan bahwa siklus penyembuhan yang diikuti untuk demonstran tertentu bisa jadi lebih pendek secara signifikan.”
“Kami sekarang sedang mengembangkan sistem pemantauan untuk bondlines,” kata Pantelelis, “terutama untuk produksi blade turbin angin tetapi pada akhirnya untuk setiap proses bonding. Meskipun kami saat ini sangat sibuk dengan industri turbin angin, yang mencoba untuk mengurangi biaya, kami melihat semakin banyak minat dari sektor kedirgantaraan saat bergerak menuju cetakan komposit cair untuk produksi massal. Produsen mencari untuk mendapatkan lebih banyak wawasan tentang apa yang sebenarnya terjadi selama pencetakan dan bagaimana mereka dapat menstabilkan dan mengoptimalkan proses mereka.”
Proyek Ecomise dan Recotrans menerima dana dari Program Penelitian dan Inovasi FP7 dan Horizon 2020 Uni Eropa berdasarkan Perjanjian Hibah nº NMP2-SL-2013-608667 dan 768737, resp.
Referensi untuk bagian “Analisis dielektrik (DEA), AC vs. DC” termasuk:
- “Pemantauan penyembuhan UV waktu nyata” oleh VINCENTZ, diterbitkan dalam European Coatings Journal, edisi 11/2003, hlm. 7.
- “Sistem Pemantauan Proses Online – Studi Tolok Ukur dan Uji” oleh Reinhold Meier
1
, Swen Zaremba
1
, Florian Springl
1
, Klaus Drechsler
1
, Fabrice Gaille
2
dan Christian Weimer
2
—
1
Institut Komposit Karbon, TU Munich, Garching, Jerman.
2
Eurocopter Deutschland GmbH, Donauwörth. Alur Proses dalam Material Komposit – FPCM 11, 9-12 Juli 2012, Auckland, Selandia Baru.
- Karakterisasi Tak Merusak Bahan VIII diedit oleh Robert E. Green, Prosiding ke-8
th
Internasional Symposium on Nondestructive Characterization of Materials, 16-20 Juni 1997, Boulder, Colorado, AS, diterbitkan oleh Springer Science &Business Media, hlm. 384-385.
Referensi bermanfaat lainnya adalah “Buku Pegangan Analisis Dielektrik dan Pemantauan Penyembuhan” oleh Huan L. Lee, diterbitkan oleh Lambient Technologies.