Panduan untuk Desain PCB RF dan Microwave
Saat ini telah menyaksikan aplikasi luas PCB RF/Microwave di berbagai perangkat nirkabel genggam dan industri komersial termasuk medis, komunikasi, dll. Karena sirkuit RF (frekuensi radio)/Microwave didistribusikan sirkuit parameter yang cenderung menghasilkan efek kulit dan efek kopling, interferensi dan radiasi di sirkuit sulit dikendalikan dalam desain papan sirkuit cetak (PCB) praktis. Masalah yang umum terjadi termasuk interferensi silang antara sirkuit digital dan sirkuit analog, gangguan kebisingan yang disebabkan oleh daya, dan masalah gangguan serupa yang disebabkan oleh tata letak yang tidak masuk akal. Akibatnya, bagaimana menyeimbangkan keuntungan dan kerugian dalam desain PCB dan mencoba mengecilkan interferensi merupakan aspek penting untuk desain PCB RF/Microwave.
Setiap desain berbeda, tetapi pengalaman memainkan peran aktif sebagai guru yang hebat dan insinyur manufaktur mampu memberikan solusi untuk perangkap utama. Panduan desain PCB terperinci mengenai RF/Microwave PCB akan diperkenalkan dan dibahas dalam artikel ini.
Bagaimana menentukan bahan substrat?
Sebagai tahap awal dalam desain sirkuit, pemilihan bahan substrat PCB memainkan peran penting dalam desain RF/Microwave PCB sehingga bahan substrat yang optimal berkontribusi pada kinerja yang sangat baik dan keandalan produk akhir yang tinggi. Saat mempertimbangkan material substrat yang sesuai dengan desain PCB Anda, beberapa aspek harus difokuskan seperti permitivitas relatif, tangen kerugian, ketebalan, lingkungan, dll. Konten berikut akan merinci signifikansinya dan pendekatan pemilihan ideal akan ditampilkan.
• Izin Relatif
Permitivitas relatif mengacu pada rasio antara konstanta dielektrik dan permitivitas vakum. Permitivitas relatif bahan substrat yang diterapkan untuk desain RF/Microwave PCB harus cukup tinggi untuk memenuhi tuntutan ruang dan berat. Namun, aplikasi lain seperti interkoneksi berkecepatan tinggi memerlukan permitivitas relatif yang sangat rendah untuk menghasilkan sirkuit impedansi tinggi dengan lebar saluran dan toleransi impedansi yang dapat diterima.
Sebelum penentuan bahan substrat akhir, beberapa parameter harus dikonfirmasi termasuk lebar garis untuk kisaran ketebalan papan tertentu, panjang gelombang frekuensi kerja sirkuit dan perkiraan dimensi komponen utama. Sebuah sketsa diagram papan sirkuit harus digambar untuk menetapkan permitivitas relatif maksimum dan minimum yang dapat diterima.
Selain itu, deviasi permitivitas relatif yang disediakan oleh produsen bahan substrat harus cukup rendah untuk membuat kinerja listrik dalam kisaran toleransi.
• Rugi Tangen
Rugi dielektrik adalah fungsi yang berkaitan dengan tangen rugi dan permitivitas relatif. Adapun beberapa bahan substrat, kerugian dielektrik per satuan panjang mungkin dapat diimbangi dengan penerapan saluran yang lebih pendek yang dapat mengurangi kerugian konduktor juga, yang sangat penting ketika kehilangan konduktor menjadi jelas dalam situasi frekuensi tinggi. Jadi, ketika parameter rugi-rugi komponen di beberapa rangkaian diestimasi, rugi per satuan panjang atau frekuensi yang diestimasi, bukan rugi biasa per satuan panjang saluran di bawah frekuensi yang diberikan.
Dalam rentang frekuensi tertentu, kehilangan material substrat harus cukup rendah untuk memenuhi kebutuhan daya input/output dengan menghindari masalah pembuangan panas. Selanjutnya, respon daya dari beberapa elemen rangkaian (seperti filter) harus mempertahankan karakteristik frekuensi yang tajam sehingga kebutuhan kinerja listrik dapat dipenuhi. Secara alami, kehilangan dielektrik dapat memengaruhi karakteristik frekuensi ini.
• Ketebalan
Ketebalan bahan substrat dikaitkan dengan elemen desain berikut:
a. Lebar jejak. Untuk mempertahankan impedansi karakteristik yang diberikan, ketebalan bahan substrat harus dikurangi untuk memenuhi persyaratan pengurangan lebar jejak. Jejak impedansi tinggi pada bahan substrat tipis mungkin membutuhkan lebar jejak yang sangat rendah dalam hal manufaktur.
b. Kinerja Mekanik. Sirkuit yang dibangun di atas bahan substrat tipis yang tidak disangga dapat melengkung, melengkung, atau terdistorsi, yang tidak mungkin terjadi pada bahan kaku dan termoset.
c. Stabilitas Ukuran. Secara umum, bahan substrat tipis berkinerja lebih buruk daripada yang tebal dalam hal stabilitas ukuran. Selain itu, bahan substrat tipis juga akan merugikan produsen atau menyebabkan peningkatan biaya.
d. Biaya. Umumnya bahan substrat yang tebal per satuan luas lebih mahal daripada yang tipis per satuan luas.
e. Kesesuaian. Untuk papan sirkuit yang perlu ditekuk menjadi bentuk tekukan sederhana seperti silinder atau kerucut, papan tipis mampu menekuk ke radius kelengkungan yang lebih rendah dengan bahan substrat atau foil tembaga berhenti dihancurkan.
f. Kerusakan Dielektrik. Untuk papan paralel, bahan dielektrik tipis memiliki tegangan tembus dielektrik yang secara proporsional lebih tinggi daripada bahan tebal.
g. Kemampuan Penanganan Daya. Kemampuan penanganan daya papan sirkuit frekuensi tinggi dibatasi oleh dua aspek yang dapat dikurangi dengan menambahkan ketebalan bahan substrat. Di satu sisi, daya tinggi sebagian dapat dihamburkan melalui panas. Di sisi lain, tingkat daya puncak yang tinggi dapat menyebabkan timbulnya korona untuk menghasilkan listrik dan memperpendek masa pakai bahan substrat.
• Lingkungan
Fabrikasi papan sirkuit cetak dan lingkungan operasional menjaga kendala pemilihan bahan substrat. Materi pokok pertunjukan yang harus diperhatikan antara lain:
a. Stabilitas Suhu. Suhu tertinggi dan terendah operasional dan teknis harus dijamin dan batas suhu harus ditunjukkan sebagai "puncak" atau "terus menerus". Modifikasi kinerja listrik harus dihitung pada suhu puncak dan dibandingkan dengan persyaratan desain. Papan sirkuit tidak mungkin berfungsi selama rentang puncak suhu yang terputus-putus sehingga suhu "terus-menerus" harus diterapkan untuk memperkirakan kinerja. Kerusakan permanen yang terjadi pada kinerja mekanis papan sirkuit harus diperiksa dalam rentang suhu batas "intermiten".
b. Ketahanan Kelembaban dan Kimia. Bahan substrat harus menyerap kelembaban dalam jumlah rendah sehingga kinerja listrik papan sirkuit tidak akan menurun secara nyata di lingkungan dengan kelembaban tinggi. Lagi pula, solusi perlindungan lingkungan ekstra menimbulkan biaya produksi ekstra dan kompromi desain. Teknik yang akan digunakan harus sesuai dengan ketahanan kimia dan ketahanan pelarut bahan substrat.
c. Kinerja Anti-Radiasi. Ketika RF/Microwave PCB diterapkan di ruang angkasa atau aplikasi nuklir, bahan substrat akan mengalami radiasi pengion besar-besaran. Pengaruh pada kinerja mekanik dan listrik substrat dengan radiasi pengion harus dipastikan dan diperkirakan. Selain itu, efek akumulatifnya harus dipastikan dan umur pengoperasian papan sirkuit yang efektif harus dibandingkan dengan itu.
• Aturan Desain Lainnya Mengenai Bahan Substrat
a. Daya rekat kumparan tembaga harus cukup tinggi untuk menahan aplikasi dan lingkungan manufaktur agar tidak menyebabkan kerusakan permanen.
b. Permitivitas relatif berubah dengan suhu, yang mungkin akan mempengaruhi kinerja listrik dalam rentang suhu kerja.
c. Keandalan perangkat pemasangan permukaan (SMD) dan lubang berlapis (PTH) juga dikaitkan dengan CTE.
d. Konduktivitas termal bahan substrat akan mempengaruhi desain dengan mempertimbangkan masalah manajemen termal.
e. Saat memutuskan rumah dan pemasangan, kemiringan papan harus dipertimbangkan terlebih dahulu.
f. Kinerja mekanis mungkin akan mempengaruhi desain perakitan dan pemasangan.
g. Berat jenis bahan substrat menentukan berat papan sirkuit.
h. Koefisien ekspansi termal (CTE) harus dipertimbangkan secara hati-hati dalam proses perancangan dan penerapan suhu lingkungan batas dan komponen daya tinggi dan penerapan penyolderan reflow atau manufaktur suhu tinggi lainnya.
i. Resistivitas listrik mungkin akan menjadi elemen yang terkait dengan kinerja listrik, terutama ketika saluran impedansi tinggi mentransmisikan tegangan tinggi, rangkaian penguatan daya, misalnya.
Bagaimana memproses karakteristik listrik?
Karakteristik listrik frekuensi tinggi yang penting mengandung impedansi karakteristik (Z0 ), koefisien atenuasi (α) dan kecepatan transmisi sinyal (v). Impedansi karakteristik dan kecepatan transmisi sinyal ditentukan oleh permitivitas relatif efektif sedangkan kehilangan sinyal oleh koefisien atenuasi.
Di antara semua struktur transmisi yang mungkin, seperti stripline (definisi stripline akan diperkenalkan pada Bagian a di bawah), mikrostrip, pulsa atau alur bipolar, stripline dan mikrostrip paling banyak diterapkan dalam desain sirkuit gelombang mikro dan umumnya bergantung pada bahan dasar lunak. Untuk stripline atau mikrostrip, rasio antara jarak tanah dan lebar konduktor, ketebalan konduktor dan jarak antara konduktor kopling sangat mempengaruhi impedansi karakteristik dan koefisien atenuasi. Dalam rentang frekuensi tertentu dan pada struktur saluran transmisi, koefisien atenuasi, permitivitas relatif dan impedansi karakteristik dapat menampilkan ketergantungan frekuensi.
Ketika ukuran penampang strip atau mircrostrip lebih besar dari panjang gelombang dalam dielektrik, mode transmisi lain (lebih tinggi) menjadi signifikan, yang membuat kinerja listrik saluran transmisi melemah. Saat kecepatan sinyal dan frekuensi meningkat, dimensi saluran transmisi harus dikurangi secara proporsional untuk menghindari mode urutan yang lebih tinggi, yang memerlukan penerapan bahan substrat yang lebih tipis dengan impedansi karakteristik tertentu yang dipertahankan.
• Garis Garis
Stripline adalah struktur saluran transmisi, termasuk saluran sinyal dan dua landasan yang lebih luas yang sejajar dengan saluran sinyal yang dijepit di antaranya. Gambar di bawah menunjukkan garis garis khas dalam tampilan penampang yang dikutip dari IPC-2252.
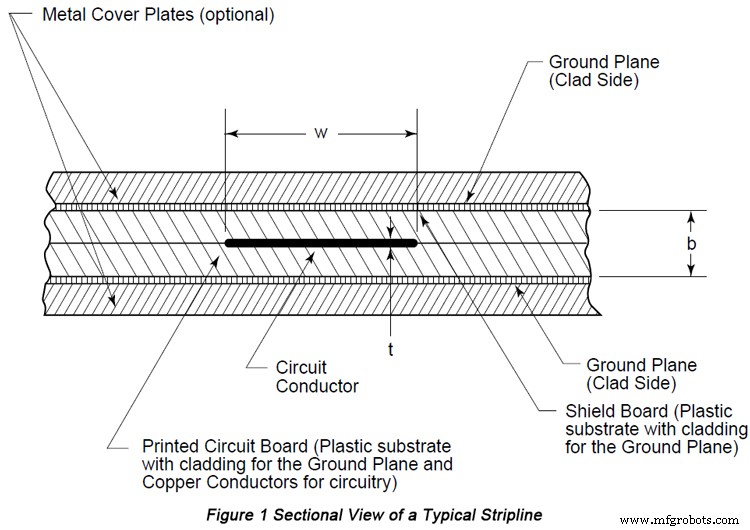
Rumus untuk impedansi karakteristik stripline diklasifikasikan menjadi dua aspek:garis sinyal sempit dan garis sinyal lebar.
sebuah. Garis sinyal sempit
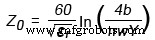
Z0 mengacu pada impedansi karakteristik (ohm);
εr mengacu pada permitivitas relatif;
b mengacu pada jarak antara ground (m);
w mengacu pada lebar garis sinyal (m).
Nilai Y memenuhi rumus:
Dalam rumus ini,
, t mengacu pada ketebalan tembaga (m).
b. Garis sinyal lebar
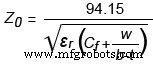
Dalam rumus ini, Cf mengacu pada kapasitansi fringing dan sesuai dengan rumus berikut:
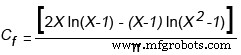

• Garis Garis Asimetris
Ketika garis sinyal ditempatkan di antara dasar (atau kekuatan) tetapi tidak pada posisi tengah, rumus perhitungan garis strip harus dimodifikasi. Dalam proses modifikasi, perlu untuk menggabungkan perbedaan antara jalur sinyal dan ground yang lebih dekat dan lebih jauh. Jika garis sinyal terletak pada kisaran sepertiga pusat, penyimpangan yang ditimbulkan oleh asumsi bahwa garis sinyal terletak di tengah akan sangat kecil.
Ketika kopling sangat diperlukan antara garis sinyal, struktur garis asimetris harus bergantung, mengorbankan dua garis sinyal yang terletak di permukaan yang berbeda dan dipisahkan oleh dielektrik. Kopling dilakukan melalui garis sejajar atau garis silang. Dalam hal desain sirkuit frekuensi tinggi, kopling tidak diperlukan, struktur garis sinyal yang bersilangan secara vertikal tidak berfungsi.
• Mikrostrip
Mikrostrip juga merupakan jenis struktur saluran transmisi, termasuk jalur sinyal dan ground yang sejajar dengan jalur sinyal.
Rumus impedansi karakteristik mikrostrip didasarkan pada model mikrostrip sederhana yang hanya berisi satu dielektrik yaitu konduktor tanpa ketebalan. Rumusnya seperti Formula 7
Dalam rumus ini, rumus 8, "0" dan "1" kedua setelah Z mengacu pada ketebalan konduktor nol dan jenis dielektrik. Dengan demikian, akurasi model ini lebih baik dari 0,01% ketika nilai u kurang dari 1. Ketika nilai u kurang dari 1000, akurasinya lebih baik dari 0,03%.
Bagaimana cara menyusun aspek penting lainnya?
• Fitur Mesin
sebuah. Dimensi dan Toleransi
Di antara elemen desain, desain dimensi dan toleransi sangat penting. Dalam perancangan lapangan, toleransi bilateral dan toleransi posisi sebenarnya biasanya diterapkan.
Dimensi dan toleransi posisi sebenarnya yang hanya ditandai membuat pabrikan mengatur penyimpangan dalam posisi dan dimensi pada proporsi apa pun, yang biasanya mengarah pada peningkatan kemampuan manufaktur. Akibatnya, desainer memastikan persyaratan fungsionalitas dan memberikan kebebasan yang cukup bagi produsen untuk mengatur penyimpangan utama dalam proses manufaktur di mana akurasinya paling rendah.
Kapasitas toleransi posisi terutama tergantung pada jenis material, ketebalan dan ukuran keseluruhan komponen. Diameter posisi sebenarnya 0,254 mm (0,01 inci) adalah yang paling sering terlihat dan paling mudah diperoleh. Ketika persyaratan toleransi harus lebih tinggi dari 0,152 mm (0,006 inci), kemampuan manufaktur akan terganggu. Namun, jika diperlukan dengan tepat, kondisi material maksimum harus diperlukan untuk memungkinkan produsen menyeimbangkan antara kesalahan bukaan dan kesalahan posisi untuk meningkatkan kemampuan manufaktur.
Ketika sebuah via diproduksi sesuai dengan diameter minimumnya, toleransi posisi sebenarnya diperlukan untuk digunakan oleh kondisi material maksimum yang hanya ditandai. Namun demikian, melalui diproduksi oleh diameter yang lebih besar dan dapat diterima biasanya diposisikan dengan akurasi yang lebih rendah, yang masih memastikan fit dan fungsi. Dengan demikian, vias yang lebih besar bisa mendapatkan toleransi posisi yang cukup, sama dengan nilai tambah yang dapat diterima untuk diameter via minimum. Dengan toleransi ekstra yang ditambahkan ke toleransi posisi sebenarnya, toleransi inspeksi dihasilkan.
Ketika kondisi material minimum diterapkan, toleransi ditetapkan sesuai dengan diameter maksimum. "Terlepas dari ukuran fitur" mengacu pada penerapan toleransi tanda tanpa toleransi ekstra dan toleransi dimensi karakteristik ditentukan sesuai dengan kemampuan manufaktur berbeda yang dapat diterima.
Meskipun dimensi dan toleransi posisi sebenarnya dapat diterapkan dalam kasus apa pun yang dapat dibayangkan, keduanya paling baik diterapkan pada fitur yang serupa dengan posisi lubang, kantong, dan sumbu X dan Y lainnya.
b. Lubang Berlapis
Diameter aperture minimum ditentukan oleh ketebalan seluruh material. Rasio aspek biasanya digunakan untuk menunjukkan koefisien kesulitan, yaitu rasio antara ketebalan material dan diameter bukaan. Misalnya, ketika rasio aspek adalah 5:1 dan papan sirkuit stripline memiliki ketebalan 3,3 mm (0,13 inci), ini menunjukkan bahwa diameter bukaan minimum adalah 0,66 mm (0,026 inci).
Secara umum, rasio aspek sekitar 3 lebih mudah dibuat sementara 5 lebih sulit dan 10 sangat sulit dan kadang-kadang bahkan gagal diproduksi. Sederhananya, lubang berlapis dengan rasio aspek tinggi cenderung lebih mudah dibuat pada material tipis sementara lubang pengeboran dengan rasio aspek tinggi cenderung dibuat lebih sulit. Ketika datang ke lubang pengeboran dengan diameter lebih kecil dari 0,33mm (0,013 inci), bor rusak dan melalui kekasaran akan menjadi masalah praktis. Selain itu, lubang dengan rasio aspek tinggi sulit dibersihkan, diaktifkan, dan diberi logam. Karena dispersibilitas larutan, metalisasi didistribusikan secara tidak merata di dalam lubang. Dispersi terbatas mengurangi transmisi material atom dan molekul di dalam lubang dan membuat distribusi arus asli pelapisan menjadi kompleks.
Diameter lubang dapat diatur menjadi sebelum metalisasi dan pasca metalisasi. Metalisasi membuat diameter lubang mengecilkan ketebalan berlapis dua kali lipat. Kesalahan bukaan setelah metalisasi dibatasi oleh kesalahan yang terjadi selama pengeboran lubang dan metalisasi. Meskipun toleransi yang lebih ketat dapat dicapai, zona toleransi 0,13-0,25 mm (0,005-0,01 inci) adalah yang paling sering terlihat. Secara umum, biaya dan tingkat kesulitan meningkat dengan pengurangan toleransi diameter aperture. Aturan empiris mengatakan:jika rasio aspek lebih besar dari 4:1, melalui diameter harus ditingkatkan menjadi 0,10 mm (0,04 inci) atau lebih.
Diameter bukaan melalui metalisasi gagal diprediksi secara akurat karena distribusi kerapatan arus berlapis. Perbedaan dalam hal kerapatan arus lokal menyebabkan ketebalan logam dipengaruhi oleh diameter bukaan, kerapatan lubang, sirkuit ambien, dan bentuk tanah. Umumnya, dimensi lubang sebelum metalisasi dan ketebalan metalisasi minimum diatur untuk meningkatkan kemampuan manufaktur. Ketika lubang berlapis melarang interkoneksi ground atau internal sebagai mode, cocok untuk menentukan lubang berlapis minimum. Ketika lubang dianggap sebagai komponen timah, toleransi bilateral harus dipertimbangkan dalam dimensi lubang.
Ketika timah/timbal yang dilapisi perlu dilebur atau dialiri ulang, dimensi lubang harus ditunjukkan seperti sebelum penyolderan reflow. Pada tahap penyolderan reflow, setiap detail desain seperti dimensi pad, dimensi lubang dan ketebalan material serta ketebalan rangkaian akan mempengaruhi aliran solder dan dimensi setelah penyolderan reflow. Lubang berlapis setelah batasan modular tidak dapat ditutup sebagian atau seluruhnya oleh logam.
• Metalisasi
sebuah. Desain Tepi Berlapis
Dalam PCB multilayer, tepi berlapis telah menjadi teknologi yang dapat diterima untuk mengurangi mode penekanan lubang berlapis. Desain tepi berlapis harus berisi tiga hingga empat konektor lebar 6,4 mm (0,25 inci) yang bertanggung jawab untuk menghubungkan tab di seluruh papan. Akibatnya, banyak tab dapat diproduksi sebagai bentuk papan utuh. Tepi berlapis harus tumpang tindih dengan lebar setidaknya 1,3 mm (0,050 inci) dari lapisan atas atau lapisan bawah sehingga daya rekat mekanis lebih kuat. Ketebalan metalisasi harus setidaknya 0,025 mm (0,001 inci).
b. Pelapisan Tembaga
Sebelum pelapisan, semua permukaan logam dan dielektrik yang terbuka ditutupi dengan lapisan pelapis tanpa pelapisan listrik atau konduktivitas. Maka ketebalan tembaga yang diperlukan harus dilapisi di seluruh papan atau grafik.
Secara umum, pelapisan panel adalah pilihan yang optimal jika keseragaman ketebalan sangat dibutuhkan. Lagi pula, gambar tidak akan memengaruhi distribusi pelapisan. Selain itu, ketika metalisasi tebal diperlukan, pelapisan panel mampu menenggelamkan sejumlah besar logam dengan bridging yang tidak terbentuk di antara gambar. Sebaliknya, pelapisan gambar hanya dapat dianggap sebagai pilihan yang optimal ketika lebar jejak/toleransi jarak membutuhkan keketatan yang tinggi karena foil tembaga yang perlu digores disatukan oleh bahan substrat dengan tingkat ketebalan yang sama.
Kinerja mekanis tembaga pelapisan menentukan ketahanan kejut termal dan ketahanan siklus termal dari lubang berlapis. Dalam proses perakitan solder dan sirkulasi suhu lingkungan, retakan mungkin terjadi pada lubang berlapis. Tembaga harus dengan kelenturan yang cukup untuk menahan goncangan suhu tinggi dan untuk menahan kegagalan kelelahan yang disebabkan oleh suhu lingkungan yang lebih rendah. Dalam hal keandalan yang tinggi, sistem tembaga pelapisan asam disarankan untuk diterapkan oleh produsen PCB karena tembaga pelapisan mampu mencapai kelenturan setidaknya 20% dan kekuatan tarik minimal 2,76x10
8
Pa.
Ketebalan pelapisan biasanya menentukan ketebalan minimum dinding lubang berlapis yang biasanya diatur menjadi 0,0025 mm (0,001 inci). Ingat dinding lubang 0,0025 mm (0,001 inci) akan menyebabkan ketebalan 0,004-0,005 mm (0,0015-0,002 inci) dari permukaan lainnya. Jika teknologi penyolderan pelapisan gambar tidak diterapkan, ketebalan pelapisan akan melebihi 0,05 mm (0,002 inci), menimbulkan masalah terkait akurasi korosi.
Dalam pelapisan panel dan pelapisan gambar, jenis lubang mempengaruhi distribusi logam. Lubang independen menerima penyolderan lebih cepat daripada lubang padat. Tingkat keseragaman ketebalan logam pada komponen ditentukan oleh persentase logam yang tercakup dalam area pelapisan. Ketika lubang dan gambar tidak merata, toleransi ketebalan akan lebih besar. Ketebalan tembaga pelapisan tipikal adalah ± 0,013 mm (0,005 inci). Setelah toleransi ±0,005mm (0,0002 inci) atau lebih rendah, kemampuan manufaktur akan berkurang.
Jika ketebalan metalisasi atau ketebalan keseluruhan produk akhir diatur, toleransi harus merupakan penjumlahan dari toleransi pelapisan dan ketebalan foil tembaga dan/atau toleransi dielektrik. Ketebalan foil tembaga ditentukan oleh berat tembaga per satuan luas.
Foil tembaga RA memiliki toleransi ketebalan yang lebih rendah daripada foil tembaga elektrolitik. Oleh karena itu, beberapa perubahan kecil terjadi pada ketebalan foil tembaga tetapi persyaratan masih dapat dipenuhi. Telah ditemukan bahwa ketebalan berubah menjadi ±0,005mm (0,0002inci) pada kertas tembaga 0,5 hingga 1oz.
Ketebalan metalisasi keseluruhan diperoleh melalui analisis mikroskopis setelah pemolesan dan korosi. Sampel internal ditempatkan di sekitar komponen dan akan dipotong dari panel. Sampel internal memberikan indikator terbaik untuk ketebalan komponen. Jika sampel internal tidak diterapkan, sampel dapat ditambahkan ke area lateral atau komponen dapat diterapkan untuk uji destruktif.
• Etsa
Akurasi manufaktur akhir adalah jumlah penyimpangan dari pencitraan dan etsa.
Retak lebih sulit daripada garis untuk dicitrakan dan digores. Jika memungkinkan, perlu untuk mengatur retakan menjadi lebih lebar dari garis di sirkuit kepadatan tinggi. Ketika garis dan lebar retak lebih rendah dari 0,10 mm (0,004 inci), kemampuan manufaktur akan berkurang.
Sangat sulit untuk mendapatkan garis yang dua kali lebih kecil dari ketebalan foil tembaga. Ini berarti bahwa garis 0,035 mm (0,0014 inci) bekerja dengan sempurna untuk foil tembaga 0,5 oz [0,017 mm (0,00067 inci)] sedangkan garis 0,070 mm (0,0028 inci) bekerja dengan sempurna untuk foil tembaga 1 ons [0,035 mm (0,00014 inci)]. Secara umum, yang terbaik adalah mengurangi ketebalan foil tembaga yang dibutuhkan.
Garis-garis sempit yang dipisahkan oleh celah lebar lebih mudah diukir daripada garis-garis halus yang padat. Saat garis berubah arah, sudut tajam lebih sulit diukir daripada transisi kurva atau sudut 45°.
Singkatnya, penentuan bahan substrat yang sangat baik, modifikasi karakteristik kelistrikan yang masuk akal dan ilmiah dan pengaturan aspek penting lainnya, pasti akan mengarah pada desain RF/Microwave PCB yang akurat berdasarkan produk akhir yang andal yang dapat diharapkan sepenuhnya.
Sumber Daya Bermanfaat:
• Kemunduran dan Solusi dalam Desain PCB RF
• Desain PCB untuk Sirkuit Frekuensi Radio dan Kompatibilitas Elektromagnetik
• Aturan Utama Desain PCB yang Harus Anda Ketahui
• Kemungkinan Masalah dan Solusi dalam Proses Desain PCB
• Bagaimana Menerapkan Pemeriksaan Kualitas PCB
• Layanan Pembuatan PCB Fitur Lengkap dari PCBCart - Beberapa Opsi Nilai Tambah
• Layanan Perakitan PCB Tingkat Lanjut dari PCBCart - Mulai dari 1 buah