Inklusi, Rekayasa Inklusi, dan Baja Bersih
Inklusi, Teknik Inklusi, dan Baja Bersih
Inklusi adalah senyawa dan endapan non-logam yang terbentuk dalam baja selama produksi dan pemrosesannya dan karenanya merupakan produk sampingan dari pembuatan baja yang timbul dari berbagai kimia dan proses. Inklusi dapat sangat bervariasi dalam ukuran dan komposisi, sehingga menimbulkan berbagai efek yang sesuai dan memerlukan peralatan analitik yang canggih untuk karakterisasi.
Inklusi dibentuk oleh fase kaca-keramik yang tertanam dalam matriks logam baja. Kontrol inklusi adalah untuk mempromosikan penghapusan inklusi dari baja dan untuk mengurangi efek berbahayanya pada kualitas dan pemrosesan baja. Ini adalah aspek penting dari praktik pembuatan baja. Namun, keberadaan jenis inklusi tertentu juga dapat menghasilkan efek menguntungkan pada baja.
Sumber, penghilangan, dan konsekuensi mekanis dari inklusi bergantung pada jenis dan rekayasanya. Komposisi kimia dari inklusi dan fraksi volumenya ditentukan oleh pengelolaan berbagai langkah yang terlibat dalam proses produksi seperti operasi peleburan, pemurnian dan pengecoran. Oleh karena itu, populasi inklusi bergantung pada hubungan yang ada antara parameter operasi yang diterapkan dan fitur grade baja yang akan diproduksi.
Evolusi populasi inklusi dalam ladle dipengaruhi oleh beberapa faktor, seperti jenis dan ukuran distribusi inklusi induk dalam tungku pembuatan baja saat sadap, tingkat oksigen saat sadap, jumlah sisa terak dari tungku pembuatan baja, jenis, jumlah dan waktu penambahan terak sintetis ke sendok, jenis dan waktu penambahan deoksidan dan waktu dan intensitas pengadukan di sendok untuk beberapa nama. Bentuk inklusi dapat berbentuk globular, platelet, dendritic, atau polyhedral.
Bentuk globular diinginkan. Inklusi tertentu seperti MnS (mangan sulfida), oksi-sulfida yang terbentuk selama pemadatan di ruang antara lengan dendrit, aluminat besi, dan silikat berbentuk bulat. Bentuk trombosit tidak diinginkan. Baja terdeoksidasi aluminium mengandung MnS dalam bentuk film tipis yang terletak di sepanjang batas butir. Inklusi polihedral tidak terlalu berbahaya. Inklusi memiliki bentuk yang berbeda yang dijelaskan di bawah ini. Bentuk inklusi globular paling diinginkan karena pengaruhnya terhadap sifat mekanik baja sedang. Bentuk bulat dari inklusi globular adalah sebagai akibat dari pembentukannya dalam keadaan cair pada kandungan aluminium yang rendah.
Inklusi berbentuk trombosit ada pada baja yang dideoksidasi oleh aluminium. Inklusi ini mengandung MnS dan oxy-sulfida dalam bentuk film tipis (platelet) yang terletak di sepanjang batas butir baja. Inklusi tersebut terbentuk sebagai hasil dari transformasi eutektik selama pemadatan. Inklusi berbentuk trombosit tidak diinginkan. Mereka sangat melemahkan batas butir dan menyebabkan efek buruk pada sifat mekanik terutama dalam kondisi panas (hot shortness).
Inklusi berbentuk dendrit disebabkan oleh penggunaan deoxidizer kuat (aluminium) dalam jumlah berlebihan. Hal ini menghasilkan pembentukan inklusi oksida dan sulfida berbentuk dendrit (terpisah dan teragregasi). Inklusi ini memiliki titik leleh lebih tinggi dari baja. Tepi dan sudut yang tajam dari inklusi berbentuk dendrit dapat menyebabkan konsentrasi tegangan internal lokal, yang sangat mengurangi keuletan, ketangguhan, dan kekuatan lelah baja.
Inklusi polihedral terbentuk ketika morfologi inklusi berbentuk dendrit ditingkatkan dengan penambahan (setelah deoksidasi mendalam oleh aluminium) sejumlah kecil elemen tanah jarang (cerium, lantanum) atau alkali tanah (kalsium, magnesium). Karena bentuknya mendekati bentuk globular, inklusi polihedral menyebabkan efek yang lebih kecil pada sifat baja daripada inklusi bentuk dendrit.
Ada inklusi mikro (ukuran 1 mikrometer hingga 100 mikrometer) dan inklusi makro (ukuran lebih besar dari 100 mikrometer). Inklusi makro berbahaya. Inklusi mikro bermanfaat karena membatasi pertumbuhan butir, meningkatkan kekuatan luluh dan kekerasan. Mikro-inklusi bertindak sebagai inti untuk pengendapan karbida dan nitrida. Inklusi makro harus dihilangkan. Inklusi mikro dapat digunakan untuk meningkatkan penguatan dengan menyebarkannya secara seragam dalam matriks.
Efek berbahaya dari inklusi sangat tergantung pada komposisi kimianya, fraksi volume, dispersi, dan morfologinya. Biasanya inklusi besar dan tidak dapat dipecahkan dengan titik leleh tinggi adalah yang paling tidak diinginkan. Namun dibandingkan dengan inklusi ini, yang kecil dan mudah pecah atau yang memiliki titik leleh lebih rendah lebih disukai. Alasan preferensi ini adalah bahwa inklusi yang memiliki titik leleh lebih rendah atau mudah pecah cenderung berubah bentuk, dihancurkan menjadi inklusi yang lebih kecil, atau menghilang dalam proses pembentukan panas atau dingin (efek proses pembentukan dan rasio reduksi) atau perlakuan panas yang baja menjalani setelah proses pengecoran dan pemadatan.
Perilaku mekanis baja sebagian besar dikendalikan oleh fraksi volume, ukuran, distribusi, komposisi, dan morfologi inklusi dan endapan, yang bertindak sebagai penambah tegangan. Distribusi ukuran inklusi sangat penting, karena inklusi makro besar adalah yang paling berbahaya bagi sifat mekanik. Kadang-kadang cacat bencana disebabkan oleh hanya satu inklusi besar dalam panas baja utuh. Meskipun inklusi besar jauh kalah jumlah dengan inklusi kecil, fraksi volume totalnya bisa lebih besar.
Baja bersih adalah baja yang mengandung inklusi terbatas dalam hal ukuran, bentuk, komposisi, distribusi, dan frekuensi. Hasilnya, baja bersih mampu mengungguli material lain dan unggul dalam kondisi tegangan tinggi yang diterapkan, seperti yang digunakan pada peralatan transportasi dan aplikasi lainnya.
Kebersihan baja merupakan faktor penting dari kualitas baja dan permintaan akan baja yang lebih bersih meningkat setiap tahun. Namun, istilah 'baja bersih' digunakan dengan hati-hati oleh ahli metalurgi. Ini karena (i) tuntutan kebersihan yang berbeda-beda untuk baja untuk aplikasi yang berbeda, (ii) kebersihan yang berbeda-beda pada baja yang diproduksi dalam operasi yang berbeda, dan (iii) pemahaman normal tentang istilah 'baja bersih', yang oleh beberapa orang secara harfiah diartikan sebagai makna. tidak adanya inklusi dalam baja. Kebersihan baja memiliki implikasi dari sudut pandang operasional dan kinerja produk.
Tuntutan yang semakin meningkat akan kualitas tinggi membuat para produsen baja sangat memperhatikan persyaratan ‘kebersihan’ dari produk baja yang mereka produksi. Nilai baja yang berbeda sedang diproduksi oleh produsen baja untuk memenuhi berbagai persyaratan yang diharapkan dari produk baja. Tingkat kebersihan baja untuk setiap kebutuhan tergantung pada jumlah inklusi, morfologi, komposisi, dan distribusi ukuran masing-masing grade baja. Misalnya, dalam pemesinan bebas atau baja yang disulfurisasi, idenya bukan untuk sepenuhnya menghilangkan inklusi tetapi memodifikasinya untuk meningkatkan kemampuan pemesinan. Oleh karena itu, pendapat yang seimbang mengenai tingkat penyertaan atau kebersihan yang diizinkan untuk setiap grade baja sangat penting secara teknis dan ekonomis baik bagi produsen baja maupun pengguna baja. Untuk sebagian besar, istilah 'baja bersih' harus ditekankan untuk memenuhi spesifikasi dan persyaratan pelanggan untuk aplikasi yang berkaitan dengan karakteristik inklusi non-logam.
Dengan persyaratan kebersihan yang lebih ketat dan pengembangan grade pembuatan baja baru, memahami pembentukan inklusi dan proses evolusi serta mengembangkan metode untuk meningkatkan pelepasannya dari baja cair adalah penting. Penghapusan penyertaan disukai tidak hanya oleh ukuran penyertaan yang besar tetapi juga energi antarmuka yang tinggi antara penyertaan dan baja dan sudut kontak yang besar antara penyertaan dan baja dalam sistem gas penyertaan-baja.
Persyaratan inklusi baja bersih bervariasi tergantung pada grade dan aplikasi baja dan tujuan rekayasa inklusi adalah untuk mengurangi inklusi yang berbahaya dan mendorong pembentukan inklusi yang memiliki efek menguntungkan.
Kemajuan dalam pembuatan baja selama beberapa dekade terakhir telah menghasilkan nilai baja dengan tingkat pengotor yang sangat rendah. Dalam beberapa tahun terakhir, baja 'bersih' dan 'ultra-bersih' baru telah dikembangkan dan dikomersialkan oleh produsen baja di seluruh dunia, sehingga menanggapi permintaan pasar saat ini dan masa depan baja yang memiliki sifat mekanik yang jauh lebih baik (misalnya kekuatan lelah dan ketangguhan impak ) dan ketahanan korosi yang lebih baik. Baja ini dapat memiliki kandungan oksigen yang sangat rendah (kurang dari 10 ppm) dan belerang (kurang dari 10 ppm). Kekuatan pendorong di balik kemajuan ini adalah pengembangan baja baru yang dapat mentolerir aplikasi yang sangat menuntut, mis. komponen transmisi untuk industri otomotif, serta suku cadang dan tabung konstruksi untuk lingkungan yang agresif dan korosif.
Meskipun baja dengan tingkat kebersihan tinggi saat ini memiliki sifat mekanik dan/atau ketahanan korosi yang sangat baik, kemajuan dalam sifat fungsional ini mengakibatkan kerusakan chip yang lebih sulit dan dalam beberapa kasus masa pakai pahat yang jauh berkurang dalam operasi pemesinan.
Pemesinan baja dengan kebersihan tinggi, secara umum, terkait dengan konsumsi energi yang tinggi, peningkatan keausan pahat, dan biaya produksi yang tinggi. Diperkirakan bahwa lebih dari 40% dari total biaya produksi untuk memproduksi komponen otomotif berasal dari operasi pemesinan yang berbeda. Oleh karena itu, masalah utama dinilai untuk mengoptimalkan nilai baja saat ini sehubungan dengan persyaratan kemampuan mesin dan kinerja gabungan. Oleh karena itu, inklusi sampai batas tertentu diperlukan untuk kinerja kemampuan mesin yang tepat. Namun, isi dan karakteristik inklusi tetap untuk memastikan bahwa sifat kinerja tinggi dari baja dapat diperoleh.
Fitur penting dari proses pembuatan baja sekunder adalah proses produksi, baja cair, refraktori sendok, aditif, terak, suhu, dan waktu serta metode perawatan. Ini adalah faktor penting yang memiliki efek pada berbagai karakteristik inklusi seperti yang ditunjukkan pada Gambar 1.
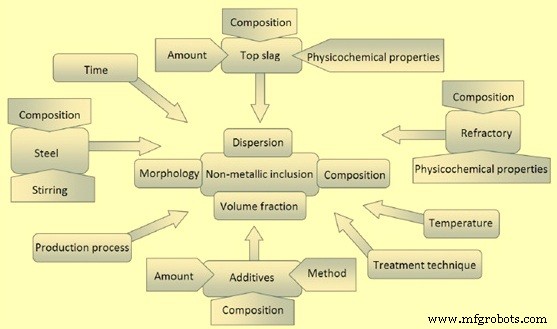
Gbr 1 Faktor yang mempengaruhi berbagai karakteristik inklusi selama pembuatan baja
Ada tiga tahapan dalam proses pembentukan inklusi. Tahapan tersebut adalah (i) nukleasi, (ii) pertumbuhan, dan (iii) koalesensi dan aglomerasi. Pada tahap nukleasi, inti fase baru terbentuk sebagai hasil super saturasi larutan (baja cair atau padat) dengan zat terlarut (misalnya aluminium dan oksigen) karena pelarutan aditif (agen deoksidasi atau desulfurisasi) atau pendinginan baja. Proses nukleasi ditentukan oleh tegangan permukaan pada batas baja cair-inklusi. Semakin kecil tegangan permukaan, semakin rendah super saturasi yang dibutuhkan untuk pembentukan inti fase baru. Proses nukleasi jauh lebih mudah dengan adanya fase lain (inklusi lain) dalam baja cair. Dalam hal ini pembentukan fase baru ditentukan oleh sudut pembasahan antara nukleus dan inklusi substrat. Kondisi pembasahan (sudut pembasahan rendah) menguntungkan untuk nukleasi fase baru.
Pada tahap pertumbuhan, terjadi pertumbuhan inti. Pertumbuhan inklusi baru berlanjut sampai kesetimbangan kimia tercapai (tidak ada super saturasi). Pertumbuhan inklusi dalam baja padat adalah proses yang sangat lambat sehingga tingkat kejenuhan super non-ekuilibrium tertentu dapat dipertahankan.
Penggabungan dan aglomerasi terjadi karena pergerakan cairan akibat konveksi termal atau pengadukan paksa menyebabkan tumbukan inklusi, yang dapat mengakibatkan koalesensi (penggabungan inklusi cair) atau aglomerasi (penggabungan inklusi padat). Proses koalesensi / aglomerasi didorong oleh keuntungan energi yang diperoleh karena penurunan permukaan batas antara inklusi dan baja cair. Inklusi dengan energi permukaan yang lebih tinggi memiliki peluang lebih tinggi untuk bergabung saat bertabrakan.
Penghapusan inklusi dari baja cair melibatkan flotasinya ke antarmuka baja-terak, pemisahan dari baja dan penyerapan selanjutnya ke dalam terak. Mekanisme dasar flotasi inklusi dalam baja adalah dengan hukum flotasi stokes. Dengan menggunakan persamaan ini dan untuk inklusi alumina bulat berukuran 20 mikrometer, perkiraan waktu untuk mengapung pada jarak 2 meter adalah sekitar 120 menit. Waktu flotasi ini dikurangi dengan bertambahnya ukuran inklusi dan selanjutnya ditingkatkan dengan pengadukan argon dan pelekatan selanjutnya dari inklusi ke gelembung gas argon. Sebagai contoh, inklusi alumina ukuran 100 mikrometer mengapung dalam 5 menit. Pengadukan argon juga mendorong pertumbuhan inklusi melalui tumbukan dan aglomerasi / koalesensi berikutnya
Inklusi besar mengapung lebih cepat daripada yang lebih kecil. Inklusi besar biasanya apung, dan sebagai hasilnya, mereka mengapung dengan mudah dari baja ke fase terak. Inklusi yang lebih kecil yang tidak begitu apung membutuhkan waktu lebih lama untuk mengapung dari baja. Inklusi mengambang diserap oleh terak. Proses mengambang dapat diintensifkan dengan pengadukan sedang. Pengadukan yang kuat menghasilkan pemecahan inklusi yang lebih besar menjadi inklusi berukuran lebih kecil. Gelembung gas yang bergerak ke atas melalui baja cair juga mendorong inklusi yang mengambang dan diserap oleh terak.
Klasifikasi penyertaan
Inklusi diproduksi dalam baja cair selama pemurnian pada suhu tinggi dan atau dari presipitasi selama pemadatan. Inklusi yang dihasilkan selama pemurnian baja pada suhu tinggi dikenal sebagai inklusi primer dan inklusi yang dihasilkan selama pemadatan dikenal sebagai inklusi sekunder. Setelah inklusi terbentuk dalam baja, karakteristik inklusi seperti ukuran, kuantitas, komposisi, dan morfologi tetap sama atau berubah / berkembang karena reaksi fisika-kimia dalam baja cair, antara baja cair dan terak dan ladle di sekitarnya yang tahan api , dan dari deformasi. Tergantung pada karakteristik akhir mereka, mereka dapat berbahaya bagi proses pengecoran, mengurangi sifat mekanik baja, dan menurunkan permukaan dan kualitas keseluruhan produk baja. Inklusi, yang keberadaannya menentukan kemurnian baja, diklasifikasikan berdasarkan kandungan kimia dan mineralogi, stabilitas, dan asal.
Menurut klasifikasi tradisional, inklusi dapat dibedakan dalam dua kelas utama sebagai fungsi asal mereka. Kelas-kelas tersebut adalah (i) inklusi endogen, dan (ii) inklusi eksogen. Inklusi endogen terbentuk oleh pengendapan dalam fase cair karena penurunan kelarutan spesies kimia yang terkandung dalam baja. Kelas inklusi non-logam ini tidak dapat sepenuhnya dihilangkan dari baja tetapi penurunan fraksi volume dan ukuran rata-rata harus dilakukan di bawah kendali yang ketat untuk menghindari aktivasi fenomena yang merusak.
Sebaliknya, inklusi eksogen adalah konsekuensi dari terperangkapnya bahan non-logam yang berasal dari terak, fragmen refraktori, atau dari bubuk naik dan penutup yang digunakan untuk melindungi baja dan menghindari lengket selama pengecoran baja. Inklusi yang termasuk dalam kelas ini dapat ditampilkan dengan ukuran besar dan asalnya tidak dapat langsung dikenali, meskipun kehadirannya dapat sangat membahayakan kesehatan mikrostruktur baja dan keandalan mekanis terkait. Karena inklusi eksogen selalu terkait dengan proses, mereka dapat dihilangkan dengan menerapkan prosedur pemrosesan yang sesuai.
Inklusi endogen – Inklusi endogen (juga dikenal sebagai inklusi asli) terjadi di dalam baja cair, mengendap selama pendinginan dan pemadatan. Inklusi yang termasuk dalam kelas ini dihasilkan dari aditif pada baja. Mereka adalah produk deoksidasi atau inklusi yang diendapkan selama pendinginan dan pemadatan baja. Inklusi alumina (Al2O3) dalam baja LCAK (low carbon aluminium kill), dan inklusi silika (SiO2) dalam baja silikon-killed dihasilkan oleh reaksi antara oksigen terlarut dan aluminium tambahan dan deoksidan silikon adalah inklusi deoksidasi yang khas.
Inklusi alumina bersifat dendritik ketika terbentuk dalam lingkungan oksigen tinggi (Gambar 2). Inklusi alumina tipe cluster dari deoksidasi atau reoksidasi (Gambar 2) adalah tipikal dari baja yang dibunuh aluminium. Inklusi alumina dengan mudah membentuk cluster tiga dimensi melalui tumbukan dan agregasi karena energi antarmuka yang tinggi. Inklusi individu dalam cluster dapat berdiameter 1 mikrometer hingga 5 mikrometer. Sebelum tumbukan, pecah atau agregasi dengan partikel lain, mereka dapat berbentuk pelat bunga atau inklusi polihedral (agregat). Sebagai alternatif, inklusi alumina seperti karang diyakini sebagai hasil dari 'pematangan Ostwald' dari inklusi alumina dendritik atau berkerumun. Inklusi silika biasanya berbentuk bola karena berada dalam keadaan cair atau kaca dalam baja cair. Silika juga dapat menggumpal menjadi kelompok.
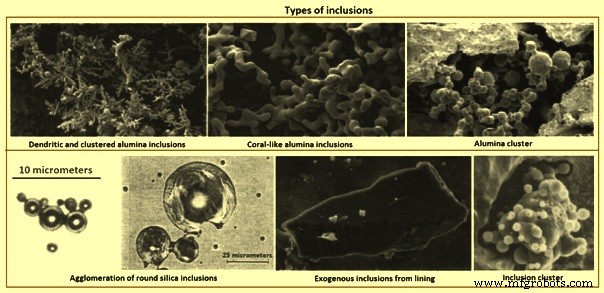
Gbr 2 Jenis inklusi
Inklusi yang diendapkan terbentuk selama pendinginan dan pemadatan baja. Selama pendinginan, konsentrasi oksigen terlarut/nitrogen/sulfur dalam cairan menjadi lebih besar sedangkan kelarutan unsur-unsur tersebut menurun. Jadi inklusi seperti alumina, silika, aluminium nitrida, dan endapan sulfida. Sulfida terbentuk secara inter-dendrit selama pemadatan, dan sering ternukleasi pada oksida yang sudah ada dalam baja cair. Inklusi ini biasanya kecil (kurang dari 10 mikrometer).
Inklusi endogen biasanya lebih merata daripada inklusi eksogen, yang merupakan jebakan bahan dari antarmuka tahan api, terak, atau bahan lain yang bersentuhan dengan baja cair. Inklusi endogen terjadi secara alami dan karenanya hanya dapat diminimalkan dan tidak dapat dihilangkan sepenuhnya. Oksida primer dan endogen seperti alumina dan magnesium-spinel menyumbat nozel masuk terendam dan bentuknya yang tidak beraturan bertindak sebagai penambah tegangan selama deformasi dan menurunkan kekuatan mekanik baja.
Inklusi eksogen – Inklusi eksogen muncul dari interaksi kimia dan mekanis yang tidak disengaja dari baja cair dengan sekitarnya. Mereka biasanya berbahaya bagi sifat mekanik yang sensitif terhadap fraktur karena ukurannya yang besar dan lokasinya yang dekat dengan permukaan. Sebagian besar inklusi ini dibentuk oleh reoksidasi di mana baja cair, memiliki 'bebas' deoksidan (aluminium, silikon, mangan, atau kalsium) yang dilarutkan dalam baja cair, mengambil oksigen dari kontak dengan udara selama penuangan dan transportasi melalui gating. sistem. Selain itu, inklusi dapat dibentuk dengan reaksi baja cair dengan gas atau uap air dari bejana transfer yang tidak dipanaskan sebelumnya. Inklusi eksogen biasanya terperangkap secara tidak sengaja selama penyadapan, penuangan dan pemadatan yang menghasilkan distribusi acak di seluruh produk baja tuang. Inklusi ini bertindak sebagai situs nukleasi heterogen untuk pengendapan inklusi baru selama gerakan mereka dalam baja cair.
Inklusi eksogen muncul terutama dari bahan kimia insidental (reoksidasi) dan interaksi mekanis baja cair dengan sekitarnya (terak entrainment dan erosi lapisan refraktori). Dalam pemesinan, mereka menghasilkan obrolan, menyebabkan lubang dan lubang pada permukaan bagian mesin, sering patah, serta keausan pahat yang berlebihan. Inklusi eksogen memiliki karakteristik umum berikut.
- Ukuran besar dengan inklusi dari erosi refraktori biasanya lebih besar daripada inklusi dari slag entrainment.
- Komposisi senyawa / multifase disebabkan oleh fenomena (i) akibat reaksi antara baja cair dan silika, FeO, dan MnO pada terak dan lapisan refraktori dengan inklusi alumina yang dihasilkan dapat tetap berada di permukaannya, (ii) sebagai inklusi eksogen bergerak, karena ukurannya yang besar, mereka dapat menjebak inklusi deoksidasi seperti alumina di permukaannya, (iii) inklusi eksogen bertindak sebagai situs inti heterogen untuk pengendapan inklusi baru selama gerakan mereka dalam baja cair, dan (iv) inklusi terak atau reoksidasi dapat bereaksi dengan refraktori lapisan atau mengeluarkan material lebih lanjut menjadi baja.
- Bentuk tidak beraturan, jika tidak bulat dari slag entrainment atau silika produk deoksidasi. Inklusi eksogen bola biasanya besar (lebih besar dari 50 mikrometer) dan sebagian besar multifase, tetapi inklusi deoksidasi bola biasanya kecil dan fase tunggal.
- Jumlah kecil dibandingkan dengan inklusi kecil
- Distribusi sporadis dalam baja dan tidak terdispersi dengan baik sebagai inklusi kecil. Karena mereka biasanya terperangkap dalam baja selama padat dan padat, kejadiannya tidak disengaja dan sporadis. Di sisi lain, mereka dengan mudah mengapung, jadi hanya berkonsentrasi di daerah bagian baja yang mengeras paling cepat atau di zona di mana pelepasan mereka dengan flotasi dalam beberapa cara terhambat. Akibatnya, mereka sering ditemukan di dekat permukaan.
- Lebih berbahaya bagi sifat baja daripada inklusi kecil karena ukurannya yang besar.
Salah satu masalah yang mengesampingkan sumber inklusi ini adalah mengapa inklusi besar seperti itu tidak mengapung dengan cepat begitu mereka terbentuk. Alasan yang mungkin adalah (i) pembentukan yang terlambat selama pembuatan baja, transfer, atau erosi dalam bejana metalurgi sehingga tidak cukup waktu untuk naik sebelum memasuki pengecoran, (ii) kurangnya panas berlebih yang cukup, dan (iii) aliran fluida selama pemadatan menyebabkan terak cetakan jebakan, atau re-entrainment inklusi mengambang sebelum mereka sepenuhnya memasuki terak.
Inklusi eksogen selalu terkait dengan praktik dan ukuran serta komposisi kimianya sering mengarah pada identifikasi sumbernya, dan sumbernya terutama adalah reoksidasi, entrainment terak, erosi lapisan, dan reaksi kimia.
Bentuk paling umum dari inklusi makro besar dari reoksidasi yang ditemukan dalam baja seperti gugus alumina ditunjukkan pada Gambar 2. Udara adalah sumber reoksidasi yang paling umum, yang dapat terjadi dalam beberapa cara seperti (i) baja cair dalam campuran tundish dengan udara dari permukaan atasnya pada awal penuangan karena turbulensi yang kuat dan lapisan oksida pada permukaan cairan yang mengalir terlipat ke dalam cairan, membentuk bidang partikel oksida yang lemah, (ii) udara tersedot ke dalam baja cair pada sambungan antara sendok dan tundish, dan antara tundish dan cetakan, dan (iii) udara menembus ke dalam baja dari permukaan atas baja di sendok, tundish, dan cetakan selama penuangan.
Selama jenis reoksidasi ini, elemen deoksidasi, seperti aluminium, kalsium, dan silikon, dll., dioksidasi secara istimewa dan produknya berkembang menjadi inklusi, biasanya satu hingga dua besaran lebih besar daripada inklusi deoksidasi. Solusi untuk mencegah reoksidasi semacam ini adalah dengan membatasi masuknya udara ke dalam proses pengecoran dengan (i) diselimuti oleh tirai gas inert dengan menggunakan manifold cincin baja atau cincin tahan api berpori di sekitar sambungan antara ladle dan tundish, dan antara ladle dan tundish. tundish dan mould, (ii) mengeluarkan gas ke dalam tundish sebelum dituang, dan ke dalam permukaan tundish selama penuangan, dan (iii) mengontrol injeksi gas di ladle untuk menghindari pembentukan mata.
Sumber reoksidasi lainnya adalah silika, mangan oksida, dan FeO dalam terak dan lapisan refraktori. Dengan mekanisme reoksidasi ini, inklusi di dalam baja tumbuh saat mereka berada di dekat antarmuka terak atau lapisan melalui reaksi SiO2 / MnO / FeO+[Al] =[Si] / [Mn] / [Fe]+Al2O3. Reaksi ini menghasilkan inklusi alumina yang lebih besar dengan komposisi yang bervariasi. Fenomena ini selanjutnya mempengaruhi inklusi eksogen dalam dua cara yaitu (i) reaksi ini dapat mengikis dan meratakan permukaan lapisan, yang mengubah pola aliran fluida di dekat dinding lapisan dan dapat menyebabkan percepatan pemecahan lapisan lebih lanjut, (ii) a inklusi eksogen besar dari lapisan rusak atau terak entrained dapat menjebak inklusi kecil, seperti produk deoksidasi, dan juga bertindak sebagai inti heterogen untuk presipitat baru. Ini memperumit komposisi inklusi eksogen.
Untuk mencegah reoksidasi dari terak dan lapisan refraktori, menjaga kandungan SiO2, MnO, dan FeO yang rendah sangat penting. Telah dilaporkan bahwa batu bata alumina atau zirkonia tinggi yang mengandung silika bebas tingkat rendah lebih cocok.
Pembuatan baja atau operasi transfer melibatkan pencampuran turbulen terak dan logam, terutama selama transfer antar bejana dan karenanya, menghasilkan partikel terak yang tersuspensi dalam baja. Inklusi terak, (berukuran 10 mikrometer hingga 300 mikrometer, mengandung CaO atau MgO dalam jumlah besar, dan biasanya cair pada suhu baja cair, jadi berbentuk bulat. Menggunakan tundish 'berbentuk H' dan menuangkannya melalui dua ladle mengurangi slag entrainment selama periode penggantian ladle Faktor-faktor yang mempengaruhi slag entrainment ke dalam baja cair selama proses continuous casting adalah (i) operasi transfer dari ladle ke tundish dan dari tundish ke cetakan terutama untuk penuangan terbuka, (ii) vortexing pada permukaan atas baja cair dengan vortex ketika baja cair berada pada level rendah dapat dihindari dengan beberapa cara seperti mematikan penuangan sebelum permulaan vortexing, (iii) emulsifikasi dan slag entrainment di permukaan atas terutama di bawah pengadukan gas di atas laju aliran gas kritis, (iv) turbulensi pada meniskus dalam cetakan, dan (v) sifat terak seperti tegangan antarmuka dan viskositas terak.Sebagai contoh, terak cetakan dapat dimasukkan ke dalam liq baja cair karena (i) turbulensi pada meniskus, (ii) vortexing, (iii) emulsifikasi yang disebabkan oleh gelembung yang bergerak dari baja ke terak, (iv) tersedot di sepanjang dinding nosel karena perbedaan tekanan, (v) aliran berkecepatan tinggi yang memotong terak dari permukaan, dan (vi) fluktuasi level.
Tegangan antarmuka antara baja dan bubuk tuang cair menentukan ketinggian meniskus baja, dan kemudahan masuknya fluks. Khususnya tegangan antarmuka 1,4 N/m untuk terak kapur-silika-alumina yang kontak dengan besi murni menghasilkan ketinggian meniskus sekitar 8 mm. Tegangan antarmuka dikurangi hingga nilai yang rendah oleh spesies aktif permukaan seperti belerang atau dengan reaksi pertukaran antarmuka seperti oksidasi aluminium dalam baja oleh oksida besi dalam terak. Tegangan antarmuka yang sangat rendah terkait dengan reaksi kimia dapat memberikan turbulensi spontan pada antarmuka, melalui efek Marangoni. Turbulensi seperti itu dapat membuat emulsi pada antarmuka, menciptakan butiran terak yang tidak diinginkan dalam baja.
Erosi refraktori, termasuk pasir blok sumur, kotoran lepas, bata tahan api yang pecah, dan partikel lapisan keramik, adalah sumber yang sangat umum dari inklusi eksogen besar yang biasanya padat dan terkait dengan bahan sendok dan tundish itu sendiri. Mereka biasanya besar dan berbentuk tidak beraturan. Inklusi eksogen dapat bertindak sebagai situs untuk nukleasi heterogen alumina dan dapat mencakup partikel pusat yang digambarkan, atau agregat dengan inklusi pribumi lainnya. Terjadinya produk erosi tahan api atau inklusi yang diperkenalkan secara mekanis dapat sepenuhnya merusak kualitas baja yang sangat bersih.
Erosi lapisan biasanya terjadi di daerah aliran turbulen, terutama bila dikombinasikan dengan reoksidasi, suhu tuang yang tinggi, dan reaksi kimia. Parameter yang sangat mempengaruhi erosi lapisan diberikan di bawah ini.
- Beberapa grade baja cukup korosif (seperti mangan tinggi dan grade yang hampir tidak terbunuh dan memiliki kandungan oksigen terlarut yang tinggi) dan menyerang lapisan batu bata.
- Reaksi reoksidasi, seperti aluminium terlarut dalam baja cair mereduksi SiO2 di lapisan refraktori, menghasilkan inklusi berbasis FeO yang sangat reaktif dan membasahi bahan lapisan, menyebabkan erosi lapisan refraktori di area turbulensi fluida tinggi. Tingkat reaksi ini dapat diukur dengan memantau kandungan silikon dari baja cair. Oksigen ini juga dapat berasal dari karbon monoksida, ketika karbon dalam refraktori bereaksi dengan pengikat dan pengotor.
- Komposisi dan kualitas bata berpengaruh signifikan terhadap kualitas baja. Sebuah pabrik baja telah mengadaptasi tiga jenis material (Al2O3 tinggi, Al2O3-SiC-C, dan MgO-C dengan laju keausan masing-masing 1,0, 0,34, 0,16 mm/panas) pada garis terak, di mana refraktori cenderung rusak oleh fluks tundish dan terak erosif, dan bata MgO-C menunjukkan daya tahan tertinggi di antara ketiganya. Mangan oksida secara khusus menyerang bagian-bagian yang mengandung silika dari refraktori. Butir alumina dan zirkonia dengan kemurnian sangat tinggi dapat menahan serangan oksida mangan.
- Erosi refraktori yang cepat dari baja mangan tinggi dapat dibatasi dengan (i) menggunakan refraktori alumina atau zirkonia dengan kemurnian sangat tinggi (mahal), dan (ii) meminimalkan oksigen dengan membunuh baja sepenuhnya dengan deoksidan kuat seperti aluminium atau kalsium, dan mencegah penyerapan udara. Lapisan tundish berbasis silika lebih buruk daripada pelapis semprot berbahan dasar magnesium. Refraktori alumina tinggi telah diusulkan sebagai yang paling menjanjikan. Memasukkan kalsium oksida ke dalam refraktori nosel dapat membantu dengan mencairkan inklusi alumina di dinding, selama difusi kalsium oksida ke antarmuka cukup cepat dan erosi nosel tidak menjadi masalah. Erosi nozzle dapat diatasi dengan mengontrol komposisi refraktori nozzle, (misalnya menghindari pengotor natrium, kalium, dan silikon), atau melapisi dinding nozzle dengan alumina murni, boron nitrida, atau bahan tahan lainnya. Tahan api pada permukaan dinding selubung harus dipilih untuk meminimalkan reaksi dengan baja yang menciptakan inklusi dan penyumbatan.
- Kecepatan berlebihan dari baja cair di sepanjang dinding di tundish, seperti zona saluran masuk. Sebuah pad dapat digunakan untuk mencegah bagian bawah tundish dari erosi, serta mengontrol pola aliran. Telah disarankan bahwa kecepatan baja cair lebih dari 1 m/s berbahaya terkait dengan erosi.
- Excessive contact or filling time and high temperature worsen erosion problems. During long holding period in the ladle, the larger inclusions can float out into the ladle slag. However the longer the steel is in contact with the ladle lining, the more tendency is there for the ladle erosion products. Solutions are based upon developing highly stable refractories for a given steel grade, developing dense wear resistant refractory inserts for high flow areas and preventing reoxidation.
Chemical reactions produce oxides from inclusion modification when calcium treatment is improperly performed. Identifying the source is not always easy, as for example, inclusions containing calcium oxide can also originate from entrained slag.
The agglomeration of solid inclusions can occur on any surface aided by surface tension effects, including on refractory and bubble surfaces. The high contact angle of alumina in liquid steel encourages an inclusion to attach itself to refractory in order to minimize contact with steel. High temperatures of 1,530 deg C enable sintering of alumina to occur. Large contact angle and larger inclusion size favour the agglomeration of inclusions. Due to the collision and agglomeration, inclusions in steel tend to grow with increasing time and temperature. The numerical simulation of inclusion nucleation starting from deoxidant addition and growth by collision and diffusion from nano-size to micro-size is reported. The fundamentals of alumina sintering into clusters, needs further investigation, though some studies have used fractal theory to describe the cluster morphology (features).
Another classification of the inclusions can be based on their chemical composition. The inclusions can be synthetically classified as (i) sulphides, (ii) aluminates, (iii) silicates, (iv) oxides, (v) nitrides, and (vi) complex combinations of two or more of these inclusion types. The majority of the inclusions in steels are oxides and sulphides since the content of phosphorus is very small. Silicates are very detrimental to steels, especially if it has to undergo heat treatment at a later stage. Normally nitrides are present in special steels which contain an element with a high affinity to nitrogen.
Sulphides inclusions are FeS, MnS, Al2S3, CaS, MgS, Zr2S, and others. The sulphides are frequently the consequence of the calcium treatment applied in order to modify the oxide inclusions, but the little and finely dispersed CaS highly refractory inclusions can be detrimental for the casting procedure (nozzle clogging) and for the damaging effect on steel. On the contrary the MnS non-metallic inclusions (frequently modified by the combination with CaS) are exploited for improving the cutting tool workability. In this case the MnS non-metallic inclusions are intentionally formed within the metal matrix in order to make the chipping brittle) during the tool working. This role implies that the volume fraction of the inclusions has to be significant and this aspect is the reason that excludes the application of EN10247:2003 for the estimation of the cleanliness of such a class of steels.
Aluminates inclusions normally consist of calcium aluminates obtained after the calcium treatment of the liquid steel. Calcium aluminates are 12CaO.7Al2O3 (C12A7), 3CaO.Al2O3 (C3A), and CaO.Al2O3 (CA) exist in the liquid state, whereas CaO.2Al2O3 (CA2) and CaO.6Al2O3 (CA6) are solid at steelmaking temperatures.
Silicates are present in steel like a glass formed with pure SiO2 or SiO2 with admixture of iron, manganese, chromium, aluminium, and tungsten oxides and also crystalline silicates. Silicates are the biggest group among non-metallic inclusions. In liquid steel non-metallic inclusions are in solid or liquid condition. It depends on the melting temperature.
Oxides inclusions in liquid steel are mostly produced during steel deoxidation but can also result from reoxidation and slag or refractory entrainment in the steel. These inclusions can have, single or multiple phases and compositions, spherical or irregular shape, and are either solid or liquid in the steel depending on their melting temperature.
Oxides inclusions can nucleate homogeneously or heterogeneously. Homogeneous nucleation occurs without the presence of foreign surfaces in the steel while heterogeneous nucleation occurs on foreign surfaces. Sources of foreign surfaces in liquid steel can be entrained materials, the surrounding ladle refractory, pre-existing inclusions, and or undissolved alloys. For the formation of a stable oxide, the absolute contribution of the bulk free energy to the overall energy is to be greater than the interfacial energy and this occurs at a critical oxide size. Inclusions less than this critical size are unstable and re-dissolve into the liquid steel while those which are larger than this size grow. For the heterogeneous nucleation, the presence of an existing surface reduces the critical oxide size and hence, reduces the overall free energy needed for a stable oxide to be produced. Heterogeneous nucleation is more favoured compared to homogeneous nucleation.
Important inclusion characteristics are their size, amount, composition, and morphology. After a stable oxide is produced in the steel, the inclusions grow and can also change their composition due to reactions within the steel and between the steel and surrounding slag and ladle refractory. Oxides inclusion growth occurs by diffusion of oxygen and deoxidant to the inclusion, and by agglomeration and coalescing after collision.
Oxides inclusions are FeO, MnO, Cr2O3, SiO2, Al2O3, TiO2 and others. By mineralogical content, oxide inclusions divide into two main groups namely (i) free oxides such as FeO, MnO, Cr2O3, SiO2 (quartz), Al2O3 (corundum) and others, and (ii) spinels which are compound oxides formed by bivalent and trivalent elements. Ferrites, chromites and aluminates are in this group. The fundamental tool for the description of the chemical composition of the oxide inclusions is the ternary phase diagram (CaO-SiO2-Al2O3), since this is the main system ruling the formation of these non-metallic compounds. This class of non-metallic compounds are formed by the deoxidizing elements added to the liquid steel for removing the oxygen content.
Composition, size, and distribution of precipitated oxides are greatly influenced by the deoxidants, conditions of the liquid steel, and the solidification process. Aluminum is widely accepted as deoxidant in steelmaking process. Its addition is very convenient and it effectively reduces oxygen content in liquid steel to low levels. However, the most of the steel problems can be traced to alumina or Aluminum rich oxides. Solid alumina inclusions in the liquid steel tend to rapid clustering due to their dendritic morphology. The alumina clusters hardly float to the top of the liquid steel because of their high apparent density in view of oxide clusters plus engulfed liquid steel. They are detrimental to the castability and quality of continuously cast steel.
The onset of clogging during the casting process starts when an alumina inclusion attaches to the nozzle wall. Certain types of refractories, especially the graphite-stabilized magnesia refractories, have been reported to promote agglomeration of alumina inclusions. The high contact angle between the alumina inclusions and the steel further promotes the tendency of the inclusions to agglomerate on refractories. In addition, the presence of significant amounts of alumina and MnS inclusions negatively impacts the performance of steel products. In general, oxide inclusions can cause lamellar tearing and degrade the toughness, bendability and ductility of steels.
When aluminum is added to liquid steel for deoxidation, the aluminum reacts with the oxygen to form dendritic alumina inclusions (alumina galaxy). Depending on size, the alumina inclusions formed as a result of deoxidation can be divided into macro-inclusions and micro-inclusions. Partial and complete substitution of titanium, zirconium, and / or rare earth metals for aluminum is increasingly pursued. This is done to improve the castability and the quality of the continuously cast steel through generation of finely dispersed oxides which effectively serve as heterogeneous nucleation sites for transformation and precipitation. Hence, control of the amount, size, composition and distribution of inclusions in steel is of importance.
Nitrides inclusions are ZrN, TiN, AlN, CeN and others which can be found in alloyed steel and has strong nitride generative elements in its content. The nitride generative elements are titanium, aluminum, vanadium, cerium and others. The nitride inclusions are normally formed by titanium nitride (TiN) and perform a detrimental effect worsened by the peculiar edged shape which increases the amplification of the stresses which are developed at the interface between the inclusion and the metal matrix. When TiN is present in large numbers, homogeneously distributed, and in relatively small sizes, they promote the formation of equi-axed grains which improve the mechanical strength of the cast steel. Also, the presence of a specific CaO∙Al2O3∙2SiO2 oxide (Anorthite) in stainless steel 316L has been found to improve the machining tool life. These inclusions when present, act as a lubricant by coating the machining tool tip. They also promote the breaking of machining chips.
Examples of complex combinations of two or more of these inclusion types are FeO·Fe2O3, FeO·Al2O3, FeO·Cr2O3, MgO·Al2O3, 2FeO·SiO2, FeS·FeO, MnS·MnO, Nb(C, N), V(C, N) and others.
Three main mechanisms have been recognized at the origin of the inclusions which are related to the damaging effects played by these non-metallic phases against the metal matrix. These mechanisms consider the inclusions as (i) notching elements which amplify the stress field around the inclusions, (ii) pressurized tanks of gas which progressively migrates into the inclusions generating a stress field around the inclusions, (iii) non-metallic phases which generate a residual stress due to the different thermal expansion coefficient associated to the metal phase and the glassy-ceramic ones.
The first mechanism is associated to a ductile process of crack formation which develops starting from the interface between the inclusions and the steel. The voids are the precursor of cracks and on a macroscopic level the cooperative detrimental effect related to the voids formed by a large number of inclusions produces a decrease of the ultimate tensile strain value. This relation points out that the factors detrimentally influencing the toughness and the macroscopic ductility of the steels are (i) the increase of the volume fraction, (ii) the decrease of the curvature radius, and (iii) the fracture of the non-metallic inclusions.
The coalescence among the nucleated voids is very dangerous since the voids of adjacent inclusions can coalesce to form a large crack, so the formation of elongated strips of inclusions represents an extreme situation. Hence, the inclusions constituted by the brittle ceramic phases which can form elongated fractured strips have to be carefully avoided. It is worth noting that the just described mechanism is featured by a ductile process on microscopic scale, but its effect on a macroscopic level turns out as a decrease of the toughness and of the ductility.
The second mechanism is related to the highest solubility shown for hydrogen by the sulphides. Hence, the inclusions become pressurized tanks pulling on the metal matrix and giving rise to a stress field which can be summed to the one formed by the external force applied during the service of the steel.
The third mechanism takes place as a consequence of the different thermal expansion coefficient featuring the steel and the glassy and / or ceramic structures characterizing the inclusions. The silicates, the aluminates, and normally all the oxides (except CaO and MgO) have a thermal expansion coefficient lower than one of the steel metal matrix, while the sulphides are featured by a contrary behaviour. The detrimental action is due to the residual stress generated on the interface between the inclusions and the metal matrix.
The higher the size of the inclusion the larger is the detrimental effect, so in order to prevent this mechanism the limitation of the size of the inclusion is a fundamental aspect while the overall volume fraction of the inclusion population does not play a significant role in this mechanism.
By stability, non-metallic inclusions are either stable or unstable. Unstable inclusions are those which dissolve in dilute acids (less than 10 % concentration). Unstable inclusions are iron and manganese sulphides and also some free oxides.
The formation and the control of the chemical composition of the inclusions involve the different steps of the production processes and the industrial systems through which they are performed. The production process has to be carefully implemented in each step in order to avoid problems related to (i) difficulties during the casting operation associated with the nozzle clogging between the tundish and the mould (continuous casting process) and between the ladle and the casting column (ingot casting), and (ii) detrimental effect on the mechanical properties of the steel.
There are four main treatment mechanisms for the removal of inclusions from the liquid steel. The first mechanism is the flotation of the inclusions. As per the Stokes law, because of the differences between densities of non-metallic inclusions and liquid steel, flotation leads to the removal of the inclusions. It is possible to calculate theoretically the rate of inclusion removal due to flotation. The second mechanism is the use of the magnetic stirring and argon gas injection. These two techniques assist the removal of non-metallic inclusions. Rate of inclusions entrapment by means of argon gas injection can be calculated.
The third mechanism is the calcium treatment. Calcium treatment is an effective way which can facilitate the removal of inclusions from the liquid steel. By adding calcium to the liquid steel (mostly in form of calcium silicide), it is possible to modify unmelted aluminum-magnesium rich inclusions (spinels) to large, isotropic, and spherical calcium aluminates and calcium sulphides with low melting points. This assists the removal of liquid inclusions. However, it can become a problem if for any reasons some of these large calcium aluminates remain or get trapped in the liquid steel.
The fourth mechanism is to optimize the properties of the top slag. Optimized properties of the top slag can enhance the inclusions removal in the ladle furnace. The three mechanisms mentioned above facilitate the inclusions movement from the middle or bottom parts of the liquid steel bring the inclusions to the ladle top. However without a proper top slag, it is highly probable that these inclusions cannot be removed efficiently. Hence, in order to ensure a very effective entrapment and absorption of non-metallic inclusions by means of top slag, it is necessary to have an optimized liquid top slag with high absorbing capacity for inclusions, proper wetting properties, and viscosity.
Inclusion engineering
Solid-phase inclusions can cluster together to clog nozzles and other flow control systems which mediate the flow of liquid steel, posing a threat to the process operations. Some inclusion chemistries reduce ductility, resistance to fatigue, or overall toughness in steels. The absence of inclusions poses issues as well because the ‘clean steels’ can be harder to machine, decreasing the lifespan of cutting tools, and require higher power consumption for machining. Understanding their nature is of critical importance in steelmaking operations, and ‘inclusion engineering’ is needed to be an operational focus during the process of steelmaking.
The term ‘inclusions engineering’ means the design of the inclusions so as to alleviate their harmful effects on the product properties. Inclusion engineering does not refer to removal of inclusions but it refers to modify them either in terms of chemical composition or shape so that harmful effects of the inclusions can be converted to improve the steel properties. Inclusion engineering also involves distribution of inclusion uniformly in the matrix, so that composite properties can be generated in the product. In some cases, deliberate attempts are made to form very fine inclusions (e.g. nitrides, and carbo-nitrides inclusions in hardening steel). Such inclusion can form by reaction between tungsten, titanium, aluminum with oxygen, nitrogen, sulphur, or carbon.
The approach for reducing the harmful effect of inclusions is to tailor the steelmaking process to avoid the presence of macro-inclusions while controlling the population, size, distribution, and morphology of the residual micro-inclusions in the steel. The application of new technology and the knowledge gained from end users on the performance of steel products are valuable information for use in the design of a clean steel strategy. The science of inclusion modification and shape control stems from the need to change the chemistry of the inclusions to enhance the performance of products in the field and ensure the castability during continuous casting. However, macro-size inclusions are required to be removed. In all other cases, depending on applications, inclusion can be modified to minimize their harmful effects.
As far as inclusion modification and shape control are concerned, the inclusions of interest are the endogenous type, particularly the inclusions which result from the process of deoxidation and sulphide-type inclusions. Oxides and sulphides are the two predominant inclusions in steel. The sources of oxides and sulphides are inherent to the steelmaking process. Oxygen is employed to react with the impurity elements (e.g. silicon, manganese) and carbon to generate chemical energy for the melting process. However, a significant amount of the oxygen ends up being dissolved in the liquid steel. The dissolved oxygen is required to be removed during the refining stage because of its harmful effect on the structural integrity of the finished product. Strong deoxidants, like aluminum and silicon, are normally used to scavenge oxygen from the steel. However, aluminum-killed steels routinely clog tundish well nozzles and submerged entry nozzles during continuous casting due to the residual alumina inclusions which remain in the steel.
The element which is to be added to modify the inclusions is to meet three requirements namely (i) it is to have high chemical affinity for the inclusion, (ii) it is to be able to modify the composition so that it becomes liquid, and (iii) it is to be able to modify the shape i.e. sharp edges and corner of inclusions to spherical.
The formation of the non-metallic phases is ruled by the thermodynamic relations. The oxide system represents the most difficult one to be studied because of the presence of different oxide species.
Moreover, the insertion of calcium aiming at the modification of the inclusions makes even more difficult the understanding of the interaction taking place in the steel bath. A good procedure for the engineering of the inclusions is aimed at developing low melting non-metallic oxides in order to avoid the nozzle clogging and at maintaining a prevalently glassy structure of the inclusions during the steel cooling and the successive heating imposed to perform the plastic deformation in order to avoid the formation of ceramic brittle phases. The need to stabilize the glassy structure makes interesting the formation of silicate system based on the presence of anorthite and pseudo-wollastonite which appears to be particularly favourable.
The prediction and the engineering of the oxide inclusions can be based on a powerful and simple thermodynamic model and can be divided into three main steps namely (i) computation of the oxygen potential associated with the slag, (ii) evaluation of the possibility of the development of the reactions to create some pure non metallic compounds, and (iii) definition of a hierarchy of the different reactions as a function of the associated oxygen potentials on the basis of the chemical composition of the steel.
Ductility is appreciably decreased by increasing amounts of either oxides or sulphides. Fracture toughness decreases when inclusions are present in higher-strength lower-ductility alloys. Similar property degradation from inclusions is observed in tests which reflect slow, rapid, or cyclic strain rates, such as creep, impact, and fatigue testing. Inclusions cause voids, which can induce cracks. Large exogenous inclusions can cause trouble in the form of inferior surface, poor polishability, reduced resistance to corrosion, and in exceptional cases, slag lines and laminations. Inclusions also lower resistance to HIC (hydrogen induced cracks). The source of most fatigue problems in steel are hard and brittle oxides, especially large alumina particles over 30 micrometers. Lowering the amount of large inclusions by lowering the oxygen content to 3 ppm to 6 ppm has extended the life of steel part such as bearing by almost 30 times in comparison with steels with 20 ppm oxygen. To avoid these problems, the size and frequency of detrimental inclusions are to be carefully controlled. Especially there is to be no inclusions in the casting above a critical size.
Although the solidification morphology of inclusions is important in steel castings, the morphology of inclusions in wrought products is largely controlled by their mechanical behaviour during steel processing, i.e., whether they are ‘hard’ or ‘soft’ relative to the steel matrix. The behaviour of different types of inclusions during deformation is schematically illustrated in Fig 3. ‘Stringer’ formation, type (b) and (c), increases the directionality of mechanical properties, adversely affecting the toughness and ductility in particular. The worst inclusions for toughness and ductility, particularly in through thickness direction properties of flat-rolled product, are those deforming with the matrix, like (d) in Fig 3.

Fig 3 Behaviour of inclusions during deformation
There is a lot of information available on the effect of inclusions on product performance and on the kinetic and thermodynamic phenomena associated with inclusion evolution and formation. With a careful analysis of the available information, it is possible to develop a good practice at each stage of the steelmaking process for clean steel production. However, it is not possible or even necessary to eliminate all inclusions, as certain inclusions which are detrimental to steels for one application can be entirely harmless when present for another application. Hence, steels are expected to have varying degrees of cleanliness depending on their application.
A classification for what has to be considered a macro-inclusion has not been defined in any standard. On the other hand this information can be extremely difficult to be provided, since for a round shape inclusion a diameter of 14 micrometers to 20 micrometers can be dangerous, but for edged inclusions (i.e. TiN) the dangerous size can be stated even at a lower level (2 micrometers to 4 micrometers) as a consequence of the higher stress amplification associated to the edged shape. The treatment of this aspect is further complicated by the fact that the danger level can be strongly affected by the configuration of the non-metallic system which is ruled by the chemical composition of the participating phases. Actually, a correct engineering of the inclusions can permit to realize a sulphide crown precipitated on an oxide core and this system configuration mutually compensates the expansion coefficient of the non- metallic phases, approximating the one of the steel metal matrix.
Calcium treatment – The process of reducing the harmful effect of micro-inclusions by controlling their size, shape, and properties is known as inclusion modification. A common approach to modifying oxide and sulphide inclusions to prevent clogging and minimize any negative effects on the structural integrity of steel is through calcium injection during secondary refining of the steel. Fig 4 gives schematic of inclusion modification with calcium treatment of steel.
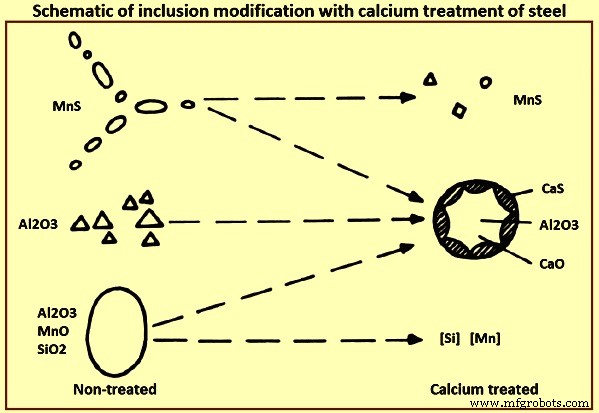
Fig 4 Schematic of inclusion modification with calcium treatment of steel
Calcium has a strong affinity for oxygen and can therefore be used as deoxidizers. However, the use of calcium as deoxidizer is challenged by its low boiling point of 1,439 deg C, limited solubility of 0.032 % of calcium in steel at 1,600 deg C, and a high vapour pressure of 1.81 atmospheres at 1,600 deg C. These properties make it difficult and non-economical to use calcium as deoxidizers. However, combinations of calcium and aluminum or manganese / silicon deoxidation form modified primary inclusions with lower activity and melting temperatures. For this reason, in steelmaking, calcium is added to steel more as an inclusion modifier rather than deoxidizer. Most steel grades are treated with calcium using either Ca-Si alloy or Ca-Fe(Ni) mixture depending on the alloy specification. Normally this treatment is effectively done after trim additions and argon rinsing.
The extent of inclusion modification in steel is an essential feature in secondary steel refining by calcium treatment. Portion of the calcium added to the melt undergoes reaction and remain in the melt as dissolved calcium in form of inclusions or go to the slag as slag constituent. The rest escape the system in form of vapour. It is vital that the calcium added is consumed by the liquid steel to the maximum extent to make the calcium injection efficient and cost effective.
The general effect of calcium treatment on inclusions modifications are (i) manganese sulphides are reduced in number and size, and they are transformed to calcium-manganese sulphides with varying properties, (ii) aluminum oxides, which are normally hard, angular and frequently appears in clusters are reduced in number or completely eliminated and replaced with complex CaO-Al2O3 or CaO-Al2O3-SiO2 inclusions, (iii) silicates are eliminated and replaced by CaO-Al2O3-SiO2 inclusions, and (iv) complex globular CaO-Al2O3-SiO2 inclusions are formed, frequently surrounded by sulphide rim.
Calcium is being frequently employed to treat aluminum killed steels to avoid the formation of solid alumina. Calcium treatment effectively improves the castability and the quality of the continuously cast steel, but is limited for all steel products which need either high fatigue resistance in service or high cold formability in very thin gauges. This is because of the presence of the globular calcium-aluminum oxides. The aluminum, calcium, and calcium-aluminum oxides are normally several to tens of micrometers in diameter.
Rare earth metals like cerium, and lanthanum etc., have also been used to modify inclusions, but they are not as efficient as calcium due to the slow flotation (due to their weight) of the modified inclusions. In addition, lanthanum and cerium readily corrode the ladle refractories. When calcium treatment is efficiently performed, the following two primary objectives are achieved.
- The alumina and silica inclusions are converted to liquid calcium aluminate and calcium silicate, which are globular in shape because of a surface tension effect. This change in inclusion composition and shape is known as inclusion morphology control.
- The calcium aluminate inclusions retained in liquid steel suppress the formation of MnS stringers during solidification of steel. This change in the composition and mode of the precipitation of sulphide inclusions during solidification of steel is known as sulphide morphology or sulphide shape control.
The conversion of inclusions to a globular shape plays a significant role on the separation rate of inclusions. For example, it has been observed that the alumina inclusions are non-wetting in liquid steel and tend to have a higher separation rate compared to CaO-SiO2-Al2O3. This implies that, by modifying the alumina inclusions with calcium, their ability to cluster is impeded as the liquid globular inclusions formed, and as a result are wetted by liquid steel. However, the high vapour pressure of calcium with the associated intense bath stirring promotes collision and coalescence of the alumina inclusions in the liquid steel. With the aid of calcium vapour and the resulting coalescence of the alumina inclusions through collision, their removal from the steel is enhanced compared to the small non-buoyant alumina inclusions which are to first cluster on their own (without forced convection) before they are able to separate from the liquid steel. This is why unmodified small alumina inclusions separate from the liquid steel and get attached to the refractory in the tundish only well after refining is complete in the ladle.
After effective calcium treatment all oxide inclusions normally contain some amount of calcium. Effective modification of oxide inclusions in steel depends on the dissolved aluminium and oxygen content of the steel before calcium treatment. For an essential inclusion modification, a calcium lower limit of 15 ppm to 20 ppm is needed. With a CaO-Al2O3 ratio of 12:7, low melting points of 1,455 deg C of calcium aluminate inclusions are formed. These inclusions exist in the liquid state at steelmaking temperatures.
Agglomeration of alumina, calcium aluminate and CaS inclusions on tundish nozzle refractories during continuous casting can result in a premature termination of casting due to a completely clogged nozzle. Depending on the population of the inclusions in the steel, complete clogging of the nozzle can occur within minutes of the start of casting. Analysis of clogged material in the tundish nozzle typically shows the presence of solid calcium aluminate inclusions with composition rich in either Al2O3 or CaO. For avoiding clogging during continuous casting, it is important to ensure low oxygen potential is achieved during refining prior to calcium treatment. The castability of steel has been shown to be directly related to its oxygen content.
When the calcium treatment is effective, alumina inclusions are converted to molten calcium aluminates which are globular in shape. The calcium aluminate inclusions retained in the steel suppress the formation of harmful MnS inclusions during the solidification of steel by modifying MnS inclusions to spherical CaS inclusions. When alumina is modified to calcium aluminate, the reaction sequence with additional calcium additions is Al2O3 to CA6 to CA2 to CA to C12A7. The presence of liquid calcium aluminates, CA2, CA, C12A7 at steelmaking temperatures (around 1,600 deg C) results in inclusions which are much easier to float than the solid alumina inclusions and also reduce the tendency of blocking ladle and casting nozzles.
The practice is to introduce calcium-bearing agents (CaSi, CaFe, CaAl, CaC, etc.) into the steel at the end of the steel refining in the form of powder or wire injection through hollow metallic tubes. Irrespective of the calcium bearing agent employed, the quantity of calcium required for treatment in a given weight of steel depends on the alumina content, and the oxygen and sulphur levels of the steel. A sufficient amount of calcium is required to be added to react with the alumina inclusions to form calcium aluminate compounds which are liquid at steelmaking temperatures. For completely modified inclusions, the equilibrium reactions are (i) [Ca] + [O] =(CaO), (ii) [Ca] + [S] =(CaS), (iii) 7(Al2O3) + 12[Ca] + 12[O] =12CaO·7Al2O3, and (iv) [MnS] + 2[O] + CaSi =(CaS) + (SiO2) + [Mn].
The reaction in equation (iv) for the precipitation of MnS in the bulk of the liquid steel is possible in steel containing a high sulphur level. Fig 5 shows the binary phase diagram of CaO-Al2O3. The highlighted region in the figure shows the desirable composition of the calcium aluminate inclusions. Outside the highlighted region, the phases are solid at steelmaking temperatures. These phases can be the prominent constituents when there is an over- injection or under-injection of calcium. While MnS inclusions are undesirable in the steel, the formation of solid CaS inclusions is equally undesirable. In terms of clogging, solid calcium aluminate or pure CaS inclusions are just as detrimental as the alumina inclusions. They also sinter and agglomerate on nozzle refractories.
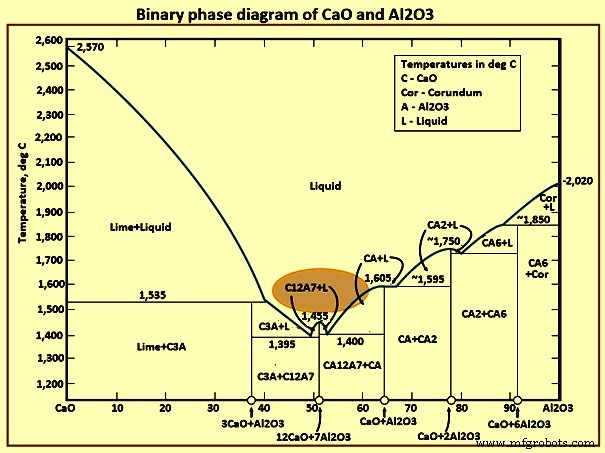
Fig 5 Binary phase diagram of CaO and Al2O3
The efficiency of calcium treatment is dependent on a number of factors, including the type, the amount and the injection rate of the calcium-bearing agent used for the treatment. Overall, by classifying the alumina and MnS inclusions according to their compositions and shapes, the efficiency of calcium treatment can be evaluated as given below.
- Class A inclusions are present when high levels of calcium have been added to the liquid steel and are liquid throughout processing. The intermingled sulphide and aluminate phases of these inclusions indicate that both phases solidified at about the same time. The sulphide phase tends to be a CaS composition. The calcium aluminate phase is either CaO·Al2O3 or 12CaO·7Al2O3. This indicates the presence of calcium aluminates with the lowest melting points and with high levels of calcium.
- Class B inclusions are the ‘bulls-eye’ type most prevalent in calcium-treated steels. The central, dark aluminate phase has solidified first, and then the outer sulphide phase precipitated onto it. In this instance, the sulphide phase tends to be (Ca, Mn)S. The calcium aluminate is of the CaO·Al2O3 or CaO·2Al2O3 composition.
- Class C inclusions are indicative of incomplete calcium treatment. These inclusions have an unmodified MnS phase, which is deformable during hot rolling. The central, dark calcium aluminate tends to be of the CaO·6Al2O3 composition, which has the lowest calcium content and remains undeformed during hot rolling.
- Class D inclusions are alumina-like oxide inclusion clusters which can have some calcium associated with them. However, there is not enough calcium present to result in complete fluxing of the alumina galaxy.
- Class E inclusions are MnS inclusions which are present when sulphur has not been completely tied up by calcium.
- Class F inclusions are inter-dendritic MnS inclusions which are present when sulphur is not completely tied up by calcium and the oxygen potential of the steel is high.
The end results of an optimized calcium treatment are:(a) the alumina is modified to form liquid calcium aluminate, and sulphur is tied up as CaS, which precipitates on the calcium aluminate inclusions, and (b) flotation of the inclusions is improved through the formation and agglomeration of spherical oxide and sulphide inclusions.
Several studies have attempted to determine the required amount of calcium addition for optimal cleanliness. For example, Ca/S ratios have been correlated to reduction of area in the Z direction and impact properties of steel. This approach cannot be generalized to all levels of sulphur. The acceptable level of Ca/S ratio in steels containing low sulphur levels can be several times higher than in steels containing higher sulphur levels, although the absolute amounts of calcium additions in the low-sulphur-containing steels are less than those of the steels containing higher sulphur levels. A good refining practice in the ladle and an efficient calcium treatment results in the majority of the alumina inclusions being converted to liquid calcium aluminate while most of the sulphur is tied up as CaS. The CaS precipitates on the calcium aluminate to produce the desirable bulls-eye shape.
Improvements of steel properties have been reported for calcium treated steel. These include (i) improvement of mechanical properties especially in transversal and through thickness direction by modifying MnS to undeformed globular (Ca-Mn)S or CaS, (ii) improvement of steel machinability at high cutting by forming protective film on the tool surface that prolongs the life of the carbide tool, (iii) improvement of surface quality and polishability, (iv) minimizing lamellar tearing in large restrained welded structures and the susceptibility of steel to reheat cracking as in the heat affected zones (HAZ) of welds, and (v) improvement of steel castability by preventing or minimizing nozzle clogging.