Otomatisasi, Instrumentasi, dan Pemodelan Pengecoran Baja Berkelanjutan
Otomasi, Instrumentasi, dan Pemodelan Pengecoran Baja Berkelanjutan
Proses continuous casting untuk baja cair adalah proses dimana baja cair dipadatkan menjadi produk baja setengah jadi (billet, bloom, beam-blank, round, atau slab) untuk selanjutnya di rolling di rolling mills. Operasi dasar mesin pengecoran kontinu adalah mengubah baja cair dari komposisi tertentu menjadi untaian bentuk dan ukuran yang diinginkan melalui sekelompok operasi seperti zona pendinginan primer, zona pendinginan semprot, dan pelurus dll.
Proses pengecoran kontinyu pada dasarnya terdiri dari (i) tundish, terletak di atas cetakan, yang menerima baja cair dari sendok baja yang padat dan memasukkannya ke cetakan dengan kecepatan yang diatur, (ii) zona pendinginan primer yang terdiri dari air yang didinginkan cetakan tembaga melalui mana baja cair diumpankan dari tundish untuk menghasilkan cangkang baja luar yang dipadatkan cukup kuat untuk mempertahankan bentuk untaian saat melewati zona pendinginan sekunder, (iii) zona pendinginan sekunder yang berhubungan dengan bagian penahanan yang diposisikan di bawah cetakan, di mana untaian baja (sebagian besar masih cair) lewat dan disemprot dengan air atau campuran air dan udara (kabut udara) untuk pemadatan lebih lanjut dari untaian baja, (iv) bagian untuk pembengkokan dan pelurusan untai baja, (v) bagian pemotongan yang terdiri dari obor pemotong atau gunting mekanis untuk memotong untaian baja yang dipadatkan menjadi panjang yang diinginkan untuk dilepas, dan (vi) meja rol habis untuk mendinginkan tempat tidur ling atau langsung ke area transfer produk.
Proses pengecoran kontinyu baja adalah proses teknologi yang kompleks yang mencakup isu-isu yang berkaitan dengan perpindahan panas, proses pemadatan baja cair, aliran baja cair, dan transisi fase dari cair ke keadaan padat. Ini melibatkan kesulitan yang cukup besar dalam menciptakan sistem kontrol proses yang optimal, yang mencakup pengaruh semua fenomena fisiko-kimia yang dapat terjadi selama proses pengecoran kontinyu baja cair. Karena itu, kontrol proses pengecoran kontinu adalah salah satu tugas tersulit dalam proses pembuatan baja.
Proses pengecoran kontinyu karena kompleksitasnya disertai dengan beberapa fenomena fisik. Proses pemadatan baja cair di dalam cetakan dan setelah meninggalkan cetakan di zona pendinginan sekunder memiliki sebagian besar fenomena penting ini. Di zona pendinginan primer, proses parsial yang terjadi adalah (i) aliran turbulen baja cair melalui area geometri yang kompleks dan nosel masuk terendam atau selubung yang disebabkan oleh konveksi, (ii) perpindahan panas di dalam baja cair luas, (iii) perpindahan panas dalam cetakan antara cangkang pembentuk dan dinding cetakan, (iv) aliran panas melalui lapisan terak padat dan cair, (v) pembentukan tegangan termal, (vi) penyusutan cangkang pemadatan terkait transisi yang terjadi selama proses pemadatan baja, (vii) efek termal yang menyertai fenomena pemadatan, (viii) dampak mekanis dinding cetakan pada untai pemadatan, (ix) proses pembentukan celah udara antara dinding cetakan dan pengerasan strand, dan (x) pembentukan kristal di dalam zona solidifikasi disertai dengan efek segregasi elemen.
Pembentukan cacat permukaan terjadi di zona pendinginan sekunder. Proses-proses yang berlangsung di zona ini adalah (i) perpindahan panas di dalam area inti cair (konduksi dan konveksi), (ii) konduksi panas di lapisan cangkang yang memadat, (iii) efek termal yang menyertai fenomena solidifikasi, (iv) perpindahan panas multi-tahap yang dihasilkan dari pendinginan untai oleh sistem nosel, terkait dengan jumlah zona semprotan dan jenis pendinginan yang diterapkan, (v) penyusutan untaian pemadatan, terkait dengan transisi yang terjadi selama proses pemadatan baja, (vi) pembentukan zona solidifikasi individu (zona kristal dendritik dan zona kristal equi-axed), dan (vii) pembentukan tegangan yang terkait dengan kontak gulungan dengan untai, dan kemungkinan menggembung di antara gulungan mesin pengecoran kontinu.
Ada beberapa penggerak untuk otomatisasi, instrumentasi, dan pemodelan pengecoran baja kontinu. Penggerak ini mencakup peningkatan permintaan pelanggan akan kualitas, peningkatan persaingan, peraturan lingkungan yang lebih ketat, dan peningkatan persyaratan keselamatan. Selanjutnya, keseluruhan sistem produksi pada mesin continuous casting adalah untuk memastikan konsistensi proses dengan unit sebelumnya dan selanjutnya. Selanjutnya, sistem otomasi proses pengecoran kontinu juga diperlukan untuk melakukan tugas-tugas penting yang meliputi perencanaan dan penjadwalan produksi, jaminan kualitas, dan fungsi kontrol pengawasan yang lebih konvensional.
Kontrol proses dari proses pengecoran kontinyu membutuhkan instrumentasi yang rumit untuk kontrol penuh dari proses solidifikasi untai. Sistem pengukuran mesin continuous casting memberikan banyak informasi proses. Namun, informasi penting, seperti perubahan ketebalan cangkang pada titik individual mesin dan panjang metalurgi (panjang inti cair), tidak ada. Oleh karena itu, model matematika sangat penting untuk sistem kontrol proses pengecoran kontinu. Keakuratan model matematika ini memungkinkannya digunakan untuk mengambil keputusan teknologi selama proses tersebut.
Sistem otomasi dan instrumentasi bersama dengan model matematika meningkatkan dan menegaskan kualitas produk cor kontinu dan mengurangi waktu henti alat berat dengan berbagai cara. Sistem pakar menggabungkan model matematika telah dikembangkan. Tantangan baru yang berasal dari tuntutan kualitas yang semakin meningkat serta ide-ide baru untuk mengatasi berbagai masalah terkenal dari proses pengecoran kontinu telah menghasilkan beberapa kemajuan dalam otomatisasi dan kontrol proses.
Sistem otomatisasi modern untuk proses pengecoran kontinu menggunakan beberapa model matematika untuk mensimulasikan berbagai fase proses pengecoran. Data input untuk perhitungan ini diperoleh secara real time oleh adaptor transportasi khusus dari otomatisasi Level-1. Parameter target dari proses pengecoran harus ditentukan oleh program produksi yang diberikan atau oleh operator. Sistem pakar digunakan untuk menghitung nilai optimal untuk parameter proses, untuk mengontrol kualitas produksi, untuk menjalankan pemodelan on-fly dari berbagai status proses teknologi, dan untuk memeriksa penyiapan roller dan segmen. Sistem pakar adalah bagian dari otomatisasi Level-2. Arsitektur perangkat lunak yang jelas dan platform middleware yang stabil untuk transfer data memainkan peran penting untuk keberhasilan interaksi antara berbagai sistem otomasi, sistem pakar, dan operator.
HMI (human machine interface) memandu operator melalui proses produksi. Interaksi personel operasi terbatas pada aktivitas yang terkait dengan kualitas dan keselamatan. Ikhtisar informasi penting disajikan di layar utama dan detailnya dapat diakses dengan mudah melalui serangkaian layar khusus yang ekstensif. Layar operator ditampilkan dalam bahasa dan unit yang dipahami oleh personel operasi. Seluruh sistem terdiri dari serangkaian aplikasi yang dapat dikonfigurasi dan pengguna dapat memilih teks yang telah ditentukan alih-alih memasukkannya. Gambar menunjukkan sistem otomatisasi khas dari proses pengecoran kontinu.
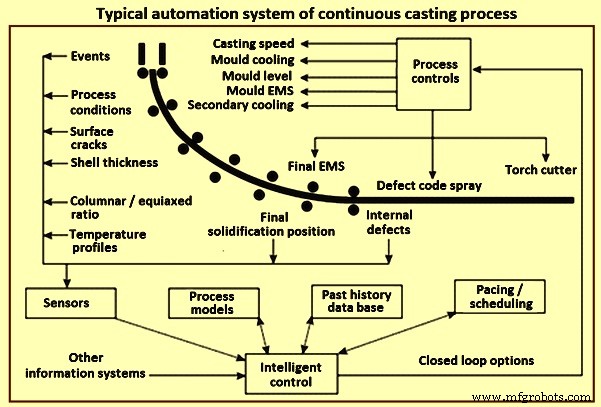
Gbr 1 Sistem otomatisasi khas dari proses pengecoran kontinu
Hirarki sistem otomatisasi
Klasifikasi tingkat tanggung jawab, persyaratan, dan respons berikut dari sistem otomatis ditentukan saat merancang dan mengembangkan sistem otomatisasi dan kontrol untuk proses teknologi dalam mesin pengecoran kontinu.
Otomasi tingkat 0 - Ini terdiri dari kontrol unit individu. Unit individu dalam area otomatis dikendalikan menggunakan sensor yang terhubung, transduser, transduser putar, drive, kontrol, dan sirkuit kontrol. Kontrol manual langsung dilakukan melalui unit, drive, dan interlock yang ditangani secara bergantian oleh sistem otomatisasi Level 0. Sebagian besar mekanisme keamanan juga disimpan pada tingkat ini.
Otomasi tingkat 1 – Ini mengontrol kelompok unit melalui kontrol PLC (pengontrol logika yang dapat diprogram). Tugas yang ditangani oleh sistem otomasi Level 1 mencakup sistem kontrol beberapa perangkat dalam satu area otomatis. Tugas kontrol biasanya dilakukan oleh modul PLC dan pengontrol mikro secara real time, dengan interval waktu respons sistem yang dipastikan dari 20 milidetik (md) hingga 150 md untuk kontrol PLC, dan antara 10 md hingga 20 mdtk untuk pengontrol mikro (untuk contoh, pengontrol gerak). Karena keterbatasan waktu respons yang ketat untuk sistem ini, model proses produksi yang kompleks tidak dapat diterapkan, misalnya, tugas yang berkaitan dengan pelacakan material dan perencanaan cakupan menggunakan unit bergerak didelegasikan ke tingkat otomatisasi lainnya.
Fungsi otomatisasi Level 1 untuk mesin continuous casting biasanya mencakup (i) kontrol turret, dummy bar car, dan tundish, (ii) penentuan posisi dummy bar, (iii) penyesuaian drive roller, ( iv) penyesuaian lebar, lancip cetakan, dan kontrol level cetakan, dan (iv) pengaturan udara dan air sesuai dengan titik setel yang dipilih dalam sistem pendingin primer dan sekunder
Otomasi tingkat 2 – Otomatisasi level 2 adalah untuk kontrol proses. Sistem otomatisasi Level 2 memainkan peran penting dalam menentukan efisiensi dan jaminan kualitas proses produksi. Sistem otomasi Level 2 mengelola dan memantau proses pengecoran menggunakan instruksi dan pengaturan yang telah ditentukan sebelumnya oleh insinyur operasional atau standar yang relevan. Selain itu, setiap instruksi pengecoran mencakup serangkaian parameter penilaian kualitas yang menunjukkan kondisi terbaik untuk menghasilkan kualitas produk target. Penggunaan satu set model metalurgi berarti proses pengecoran dapat sepenuhnya otomatis, meminimalkan kebutuhan akan masukan atau intervensi operator. Model proses menghubungkan semua fakultas untuk mencapai kinerja yang optimal secara keseluruhan.
Sistem otomasi Level 2 bertanggung jawab atas bidang-bidang seperti (i) jaminan kualitas produksi, (ii) kontrol proses dan transmisi perintah dan parameter ke sistem otomasi Level 1, (iii) akuisisi data produksi otomatis, (iv) simulasi dan peramalan kondisi sistem menggunakan model matematis terintegrasi dari proses teknologi, (v) pelacakan material, (vi) optimalisasi sistem penanganan material dan perencanaan cakupan menggunakan peralatan bergerak, dan (vii) sistem peringatan dan indikasi kesalahan, termasuk evaluasi produksi kesalahan dan pengaturan waktu.
Persyaratan sistem otomasi Level 2 untuk proses pengecoran kontinu meliputi (i) pengumpulan dan tampilan parameter proses selama pengecoran, (ii) perhitungan distribusi suhu 3D di untai, di permukaan untai, dan di tepi, (iii) perhitungan pertumbuhan cangkang untai, panjang pemadatan, penyusutan tepi, kerak, dan karakteristik pengecoran lainnya, (iv) pemosisian dinamis sistem pendingin sekunder untai, (v) pelaksanaan penyesuaian dinamis segmen (reduksi lunak), (vi ) pelacakan perubahan material dan posisi solidifikasi, dan (vii) menerima dan meneruskan intervensi operator.
Program dan model yang biasanya termasuk dalam otomatisasi Level 2 meliputi (i) kontrol aliran baja cair dengan mekanisme stopper, (ii) kontrol level cetakan, (iii) kontrol level bubuk cetakan, (iv) start otomatis pengecoran, ( v) sistem pencegahan pecahnya cetakan, (vi) cetakan, untai, dan pengadukan akhir, (vii) osilasi cetakan hidrolik, (viii) model pelacakan panas, (ix) evaluasi kualitas waktu nyata, (x) model optimasi pemotongan, ( xi) model solidifikasi untai real-time, (xii) kalkulator kurva solidifikasi on-line / off-line, (xiii) reduksi lunak mekanis dinamis, (xiv) kontrol pendinginan sekunder dinamis, (xv) mesin penandaan produk cor, (xvi) sistem pengenalan produk optik, (xvii) analisis dan simulasi proses, (xviii) pengelolaan data metalurgi, (xix) deteksi penundaan produksi, (xx) pelacakan masa pakai peralatan, dan (xxi) logistik penanganan produk cor, termasuk pendinginan tersier.
Saat menerapkan fungsi kontrol otomatisasi Level 2 untuk proses pengecoran berkelanjutan, struktur data yang kompleks digunakan untuk memodelkan berbagai istilah teknis untuk suatu domain. Antara lain, pemetaan domain masalah menggunakan rencana semprot, rencana udara, kurva suhu referensi, bubuk cor, set data parameter pengecoran, nilai baja, analisis referensi kimia, kelompok kelas baja, retak, dan potongan sampel diperiksa dari sudut yang berbeda. berkaitan dengan masalah metalurgi yang khas. Selain itu, model matematika, mekanisme kontrol, dan antarmuka pengguna memerlukan deskripsi standar yang disederhanakan dari proses pengecoran kontinu di mana sifat-sifat benda nyata yang relevan untuk perhitungan didefinisikan dengan jelas seperti panduan untai, cetakan, segmen, gulungan, nozzle semprotan, sirkuit kontrol pendinginan sekunder, dan segmen pendinginan. Istilah yang disebutkan dapat dijelaskan dengan mudah dengan memperkenalkan bahasa spesifik domain yang ringkas.
Tugas sistem otomasi Level 1 atau Level 2 dalam hal pengecoran kontinu tidak selalu dapat diklasifikasikan dengan jelas. Kesimpulan mengenai penempatan dan distribusi setiap tugas otomatisasi individu ditentukan oleh lokalisasi parameter input dan data proses, waktu respons yang mungkin dari model yang disematkan, ruang penyimpanan yang dibutuhkan, dan oleh tingkat otonomi. Persyaratan sering didistribusikan antara dua sistem seperti pelacakan material dan beberapa bahkan diduplikasi seperti interlock keselamatan. Kedua sistem memiliki antarmuka pengguna sendiri yang biasanya dirancang untuk tugas tingkat otomatisasi masing-masing.
Tingkat 3 – Otomatisasi Level 3 untuk perencanaan produksi. Ini berkaitan dengan pembuatan rencana produksi, misalnya, program casting, penjadwalan dan persiapan kerja, atau manajemen toko, dan dengan perencanaan pemeliharaan, waktu penghentian dan tugas pemeliharaan.
Arsitektur perangkat lunak dari sistem otomatisasi Level 2 terdistribusi – Persyaratan penting yang harus dipenuhi oleh sistem otomatisasi Level 2 adalah komunikasi yang stabil dan aman dari model matematika terintegrasi dengan sistem kontrol Level 1, sistem perencanaan Level 3, database yang terhubung, dan dengan personel pengoperasian mesin pengecoran kontinu . Selama merancang dan mengonfigurasi otomatisasi Level 2, variasi komponen yang berbeda, antarmuka dan sumber data yang terhubung adalah penting, dan logika perilaku setiap komponen tidak dapat diremehkan.
Model proses produksi matematis yang terintegrasi dalam sistem otomasi Level 2 membentuk inti dari sistem kontrol proses. Dengan memantau status proses yang sebenarnya, model dapat terus disuplai dengan nilai aktual dari sistem otomasi Level 1. Di sisi lain, data tersebut juga dilengkapi dengan hasil perencanaan jangka pendek, dan dengan data material dan pesanan dari sistem otomasi Level 3. Hasil perhitungan dan tampilan keseluruhan dari proses produksi ditampilkan pada mesin pengecoran kontinyu untuk personel operasi pada antarmuka pengguna. Setiap intervensi kontrol proses yang diperlukan oleh personel operasi dapat dilakukan dengan menggunakan masker input sistem otomasi Level 1 seperti pengaturan kecepatan, dan antarmuka pengguna sistem otomasi Level 2 seperti mengubah rezim kontrol (suhu referensi dan kontrol rencana semprotan) .
Berbagai pola arsitektur perangkat lunak digunakan untuk mengimplementasikan sistem tersebut, dan ini sering kali mencakup model (arsitektur multi-agen), peristiwa dan pengirim pesan (arsitektur yang digerakkan oleh peristiwa), dan layanan terdistribusi (arsitektur berorientasi layanan).
Instrumentasi
Instrumen telah digunakan pada mesin pengecoran kontinyu sejak awal pengecoran kontinyu. Instrumen sedang digunakan pada setiap komponen utama dari mesin pengecoran kontinu antara menara, atau mobil sendok, dan meja rol run-out untuk produk cor. Instrumen digunakan secara luas dalam mesin pengecoran kontinu untuk memantau variabel di sendok, tundish, cetakan, zona pendinginan sekunder, zona radiasi, dan meja rol run-out, seperti yang ditunjukkan pada Gambar 2. Faktanya, peningkatan penggunaan instrumen untuk mengukur dan parameter kontrol casting telah dikreditkan sebagai salah satu kontributor utama untuk keuntungan besar yang dicapai dalam produktivitas dan kualitas mesin pengecoran kontinu.
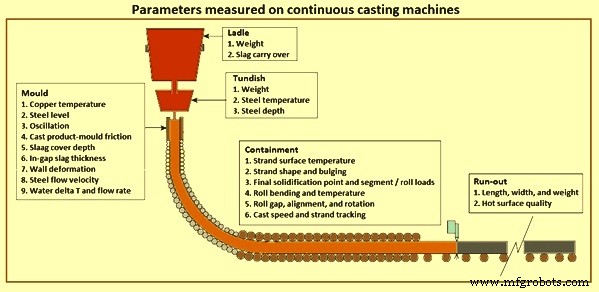
Gbr 2 Parameter yang diukur pada mesin continuous casting
Instrumen sangat penting untuk sistem kontrol dan otomasi apa pun dan kontribusinya untuk mencapai produktivitas modern dan standar kualitas tidak dapat ditaksir terlalu tinggi. Instrumen adalah 'mata' dari sistem kontrol dan otomatisasi, dan dengan teknologi saat ini, instrumentasi permanen tersedia untuk proses dan sistem kontrol kualitas untuk 'melihat' variabel sendok, tundish, dan cetakan yang paling penting.
Fungsi utama instrumen dalam proses pengecoran kontinu adalah untuk (i) mengukur parameter yang digunakan untuk mengontrol kinerja fungsi mekanis dan metalurgi dari pengecoran kontinu, (ii) menetapkan peringkat kualitas untuk setiap bagian cor, (iii) ) mendiagnosis masalah pengoperasian dan mesin, (iv) mengembangkan pengetahuan yang menghubungkan kualitas produk dan produktivitas dengan desain dan pengoperasian mesin pengecoran.
Jumlah dan kecanggihan instrumen yang digunakan pada mesin continuous casting telah berkembang pesat. Alasan utama untuk pertumbuhan yang cepat adalah tuntutan yang terus meningkat untuk produktivitas yang lebih tinggi dan sebagai kualitas produk cor, dan ketersediaan komputer digital on-line modern. Hal ini terutama berlaku untuk mesin slab casting, di mana tuntutan kualitas dan produktivitas adalah yang paling ketat. Sebelumnya, penekanan ditempatkan pada instrumentasi cetakan karena praktik dan parameter cetakan memiliki dampak paling besar pada kualitas dan produktivitas produk. Namun, akhir-akhir ini, kemajuan signifikan telah dicapai dalam pengembangan dan penerapan instrumentasi pada meja roller run out ladle, tundish, containment, dan casting.
Mengingat lingkungan berbahaya yang ditemukan di dalam ruang semprot dari zona pendinginan sekunder dari mesin pengecoran kontinu, tidak mengherankan bahwa sistem kontrol mesin pengecoran sering 'buta' terhadap perubahan variabel proses kritis, seperti suhu permukaan untai, dalam hal ini. daerah. Instrumentasi yang digunakan di sini biasanya bersifat sementara dan karenanya digunakan secara eksperimental. Instrumentasi penting lainnya termasuk yang digunakan untuk mengukur penonjolan antar-gulungan, ketebalan cangkang yang dipadatkan, dan gesekan cetakan/untai.
Pemodelan proses pengecoran kontinu
Pemodelan proses pengecoran kontinyu baja adalah tugas yang sangat kompleks, dan dapat diselesaikan dengan menggunakan berbagai jenis model matematika. Saat ini, tidak mungkin untuk secara bersamaan menangkap semua efek yang terjadi selama proses lengkap pengecoran kontinu, dan menyajikannya dalam bentuk model numerik tunggal yang komprehensif. Pembagian alami yang diterapkan dalam pemodelan proses pengecoran kontinu terkait dengan upaya mengidentifikasi masalah berikutnya selama pengecoran baja cair yang sebenarnya, atau berfokus pada bagian proses yang dipilih untuk meningkatkan teknologi yang ada.
Pada tahap awal pemecahan masalah, pemilihan tipe model yang benar dan kemungkinan terkait untuk adaptasinya ke kelas masalah yang dipecahkan telah menjadi tantangan yang sulit. Secara teoritis, model yang lebih kompleks (yang berarti lebih 'cerdas') dapat dengan mudah menjawab pertanyaan tentang parameter teknologi utama dari proses pengecoran. Namun dalam prakteknya sejumlah keterbatasan ditemui. Dengan asumsi hipotesis bahwa model yang kompleks telah diverifikasi sebagai benar, dalam kasus terbaik diperlukan perpanjangan waktu komputasi yang tidak perlu. Ini hasil dari fakta bahwa model menghitung lebih banyak parameter daripada yang dibutuhkan untuk memecahkan masalah yang ditentukan. Bahaya kedua yang disebabkan oleh ketidaksinkronan kompleksitas masalah yang ditetapkan dengan 'kecerdasan' alat yang digunakan adalah masalah verifikasi parameter model dan korelasinya dengan data proses. Semakin teoritis penjabaran model, semakin banyak parameter dan semakin tinggi risiko terjadinya parameter yang tidak terukur. Komentar terakhir menyangkut masalah strategi memperoleh pengetahuan tentang nilai parameter model yang diperlukan. Beberapa tahun pengalaman dalam pemodelan proses pengecoran kontinyu menunjukkan bahwa pilihan terbaik adalah pengukuran eksperimental dari semua parameter model terukur. Hal ini dapat diilustrasikan dengan parameter berupa panas jenis baja cor sebagai fungsi suhu, konduktivitas panas untuk baja, dan viskositas dll.
Pemodelan fisik – Pemodelan fisik dari proses pengecoran kontinu seperti menggunakan air untuk mensimulasikan baja cair memungkinkan wawasan yang cukup tentang perilaku aliran baja cair selama proses pengecoran kontinu. Pemahaman sebelumnya tentang aliran fluida dalam proses pengecoran kontinu telah muncul terutama melalui eksperimen menggunakan model air fisik. Teknik ini adalah cara yang berguna untuk menguji dan memahami efek konfigurasi baru sebelum mengimplementasikannya dalam proses. Model skala penuh memiliki manfaat tambahan yang penting dalam memberikan pelatihan dan pemahaman operator.
Konstruksi model fisik didasarkan pada pemenuhan kriteria kemiripan tertentu antara model dan proses aktual dengan mencocokkan geometri dan keseimbangan gaya yang mengatur fenomena penting yang menarik. Untuk mereproduksi pola aliran baja cair dengan model air, semua rasio antara gaya dominan harus sama di kedua sistem. Ini memastikan bahwa rasio kecepatan antara model dan proses baja sama di setiap lokasi. Ukuran kelompok tanpa dimensi menunjukkan kepentingan relatif dari dua kekuatan. Kelompok yang sangat kecil atau sangat besar dapat diabaikan, tetapi semua kelompok tak berdimensi dengan ukuran menengah dalam proses pengecoran harus dicocokkan dalam model fisik. Skala geometri dan fluida yang sesuai harus dipilih untuk mencapai kecocokan ini.
Untunglah air dan baja memiliki viskositas kinematik yang sangat mirip. Oleh karena itu, bilangan Reynolds dan Froude dapat dicocokkan secara bersamaan dengan membangun model air skala penuh. Memenuhi dua kriteria ini sudah cukup untuk mencapai akurasi yang wajar dalam pemodelan sistem aliran fase tunggal isotermal, seperti nozzle dan cetakan pengecoran kontinu dan ini telah dilakukan dengan sangat sukses.
Model skala penuh memiliki manfaat ekstra berupa kemudahan pengujian komponen alat berat dan pelatihan operator. Sebenarnya, model air dari setiap skala geometris menghasilkan hasil yang masuk akal untuk sebagian besar sistem aliran, selama kecepatan di kedua sistem cukup tinggi untuk menghasilkan aliran turbulen penuh dan bilangan Reynolds yang sangat tinggi. Karena aliran melalui tundish dan nozel cetakan digerakkan oleh gravitasi, angka Froude biasanya terpenuhi dalam model air apa pun dari sistem ini di mana kepala hidraulik dan geometri semuanya diskalakan dengan jumlah yang sama.
Model fisik terkadang memenuhi kriteria keserupaan panas. Dalam model aliran fisik aliran tunak di sendok dan tundish, misalnya, daya apung termal relatif besar terhadap aliran dominan inersia, seperti yang ditunjukkan oleh ukuran nomor Froude yang dimodifikasi, yang oleh karena itu harus dijaga tetap sama dalam model seperti pada sistem baja cair. Dalam sendok, di mana kecepatan sulit diperkirakan, akan lebih mudah untuk memeriksa kuadrat bilangan Reynolds dibagi dengan bilangan Froude yang dimodifikasi, yang disebut bilangan Grashof. Inersia dominan dalam cetakan, sehingga daya apung termal dapat diabaikan di sana. Besaran relatif dari gaya apung termal dapat dicocokkan dalam model air panas skala penuh. Ini tidak mudah, bagaimanapun, karena fenomena yang mengatur kehilangan panas bergantung pada sifat-sifat seperti konduktivitas fluida dan panas spesifik dan konduktivitas dinding bejana, yang berbeda dalam model dan bejana baja. Dalam sistem lain, seperti yang melibatkan kecepatan rendah, transien atau solidifikasi, secara bersamaan memenuhi beberapa kriteria keserupaan lain yang penting untuk perpindahan panas hampir tidak mungkin.
Kompleksitas proses pengecoran kontinyu dan fenomena yang mengaturnya seperti yang ditunjukkan pada Gambar 3 membuat sulit untuk memiliki model fisik. Namun, dengan meningkatnya kekuatan perangkat keras dan perangkat lunak komputer, pemodelan matematika telah menjadi alat penting untuk mengendalikan semua aspek proses pengecoran berkelanjutan.
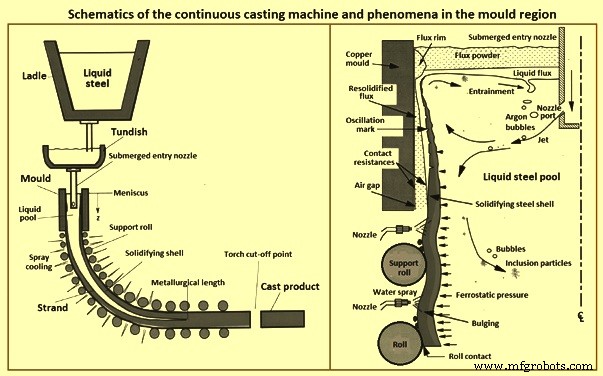
Gbr 3 Skema pengecoran kontinyu dan fenomena di daerah cetakan
Pemodelan komputasi atau matematika – Saat ini, penurunan biaya komputasi dan peningkatan kekuatan paket pemodelan komersial telah mempermudah penerapan model matematika sebagai alat tambahan untuk memahami langkah-langkah proses material yang kompleks dari proses pengecoran kontinyu baja cair. Model komputasi memiliki keuntungan perluasan yang mudah ke fenomena lain seperti perpindahan panas, gerakan partikel dan aliran dua fase, yang sulit dilakukan dengan model air isotermal. Model komputasi juga mampu merepresentasikan lebih tepat kondisi aliran yang dialami oleh baja cair. Misalnya, tidak diperlukan dasar fisik yang mengganggu aliran yang keluar dari model air untai, dan keberadaan cangkang padat yang bergerak dapat diperhitungkan.
Model matematika sekarang dapat mensimulasikan sebagian besar fenomena penting untuk proses pengecoran kontinyu. Ini termasuk (i) turbulen penuh, gerakan fluida transien dalam geometri kompleks (nosel masuk dan kolam cairan untai), dipengaruhi oleh gelembung gas argon, daya apung termal dan solutal, (ii) reaksi termodinamika di dalam dan di antara fase bubuk dan baja, (iii) aliran dan perpindahan panas di dalam lapisan fluks cair dan padat, yang mengapung di permukaan atas baja, (iv) gerakan dinamis dari permukaan dan antarmuka cairan bebas, termasuk efek tegangan permukaan, osilasi dan gravitasi yang diinduksi gelombang, dan aliran dalam beberapa fase, (v) pengangkutan superheat melalui baja cair turbulen, (vi) pengangkutan zat terlarut (termasuk pencampuran selama perubahan kadar), (vii) pengangkutan inklusi geometri kompleks melalui cairan, termasuk efek daya apung, interaksi turbulen, dan kemungkinan jebakan inklusi pada dinding nosel, gelembung gas, dinding baja yang mengeras, dan permukaan atas, (viii) interaksi termal, fluida, dan mekanik di wilayah meniskus antara meniskus pemadatan, pelek terak padat, fluks cair infiltrasi, baja cair, lapisan bubuk, dan partikel inklusi, (ix) perpindahan panas melalui cangkang baja pemadatan, antarmuka antara cangkang dan cetakan (yang mengandung lapisan bubuk dan celah udara yang tumbuh) , dan cetakan tembaga, (x) transportasi massal serbuk menuruni celah antara cangkang dan cetakan, (xi) distorsi dan keausan dinding cetakan dan gulungan pendukung, (xii) nukleasi kristal padat, baik dalam lelehan maupun melawan cetakan dinding, (xiii) pemadatan cangkang baja, termasuk pertumbuhan dendrit, butiran dan struktur mikro, transformasi fase, pembentukan endapan, dan segregasi mikro, (xiv) penyusutan cangkang baja pemadatan karena kontraksi termal, transformasi fase dan internal tegangan, (xv) pembangkitan tegangan di dalam cangkang baja yang mengeras akibat gaya eksternal (gesekan cetakan, penonjolan di antara gulungan pendukung, penarikan, dan gravitasi), (xvi) regangan termal, rangkak, dan plas ticity (yang bervariasi dengan suhu, kadar dan laju pendinginan), (xvii) pembentukan retak, dan (xviii) segregasi gabungan, pada skala mikroskopis dan makroskopik.
Kompleksitas yang mengejutkan dari proses pengecoran kontinyu membuat tidak mungkin untuk memodelkan semua fenomena ini secara bersamaan. Oleh karena itu, perlu untuk membuat asumsi yang masuk akal dan untuk memisahkan atau mengabaikan fenomena yang kurang penting. Pemodelan kuantitatif membutuhkan penggabungan semua fenomena yang mempengaruhi isu tertentu yang menarik. Oleh karena itu setiap model membutuhkan tujuan tertentu. Setelah persamaan pengatur dipilih, persamaan tersebut biasanya didiskritisasi dan diselesaikan menggunakan metode beda hingga atau elemen hingga. Validasi numerik yang memadai harus dilakukan.
Kesalahan numerik biasanya muncul dari domain komputasi yang terlalu kasar atau konvergensi yang tidak lengkap saat menyelesaikan persamaan nonlinier. Memecahkan masalah pengujian yang diketahui dan melakukan studi penyempurnaan mesh untuk mencapai solusi independen grid adalah cara penting untuk membantu memvalidasi model. Akhirnya, sebuah model diperlukan untuk diperiksa terhadap pengukuran eksperimental pada skala laboratorium dan tanaman sebelum dapat dipercaya untuk membuat prediksi kuantitatif dari proses nyata untuk studi parametrik.
Pengujian terakhir dari sebuah model adalah apakah hasilnya dapat diimplementasikan dan perbaikan dapat dicapai, seperti menghindari cacat pada produk baja. Uji coba pabrik pada akhirnya diperlukan untuk implementasi ini. Percobaan harus dilakukan atas dasar wawasan yang diberikan dari semua sumber yang tersedia, termasuk model fisik, model matematika, literatur dan pengalaman sebelumnya. Karena peningkatan daya komputasi terus memajukan kemampuan alat simulasi numerik, pemodelan memainkan peran yang meningkat dalam kemajuan masa depan untuk proses pengecoran kontinu berteknologi tinggi. Modelling can augment traditional research methods in generating and quantifying the understanding needed to improve any aspect of the process. Areas where advanced computational modelling plays a crucial role in future improvements include (i) transient flow simulation, (ii) mould flux behaviour, (iii) taper design, (iv) on-line quality prediction and control, especially for new problems and processes such as high-speed billet casting, thin slab casting, and strip casting.
Future advances in the continuous casting process are not going to come from models, experiments, or plant trials. They are going to come from ideas generated by people who understand the process and the problems. This understanding is rooted in knowledge, which can be confirmed, deepened, and quantified by tools which include computational models. As the computational tools continue to improve, their importance is increasing in fulfilling this important role, leading to future process advances.
The assumed computing objective and the required accuracy are to be the key in selecting the model. In several cases, the desired information is knowledge of the metallurgical length of the strand and the dynamics of changes in the shell thickness. This is the case when determining a place for carrying out the so‐called soft reduction operation. As can happen when the strand casting speed needs to be changed, a procedure allowing a new cooling intensity to be determined is needed. A problem like this does not need answering a series of questions related to stress occurring in the strand, the structure formed, or potential cast strand defects. Thus, it is understandable that the model is naturally simplified to a form, which still provides a credible answer to the questions which needs solution.
Some of the important models used in the automation and control of the continuous casting process are given below. The models are normally incorporated at the Level 2 automation level.
Dynamic secondary cooling control – There is a third dimension in the dynamic secondary cooling control. The model set up takes the precision and control possibilities to the next dimension allowing completely new philosophies for secondary cooling and soft reduction. When setting up the secondary cooling system, it is prerequisite to consider all known parameters which have a known influence to the calculation of 3-dimensional temperature profile of the strand. All different nozzle types are measured at the nozzle test stand to evaluate the spray water distribution. This derived information is input to the maintenance and setup system (MSS) of the 3D model. The visualized spray distribution can be seen in the maintenance system.
The exact positions of the nozzles in the cooling zones are entered and the spray distribution of one zone can be seen in the MSS. The heat removal of a cooling zone is calculated considering the heat removal of the spray water, rolls, and heat radiation. The MSS allows all cooling-relevant settings to be configured in such a way that the spray-water distribution in the cooling zones and the application of cooling practices are optimized for continuous casting machines. Metallurgical know-how can be easily incorporated into the automation setup. A built-in off-line simulation system enables comprehensive testing of new parameter settings prior to application in the production process.
The Level 2 automation system for secondary cooling provides a mathematical model for calculating the temperatures on the strand surface and inside the strand as a function of the spray plan to be used, the interpolation points in the reference temperature curve, or in relation to time changes for the spray water quantities across the complete machine. The dynamic secondary cooling control system can handle three control regimes namely (i) temperature control, (ii) strand age, and (iii) spray plan control.
In the temperature control regime the dynamic secondary cooling control system calculates the volumes of water for strand secondary cooling which are needed to maintain the specified reference temperature on the strand surface. The strand age regime is one way of controlling the secondary cooling process, taking into account the change in parameters over a given period of time. With the spray plan control regime a spray plan is produced for secondary cooling whereby preset spray water volumes correspond to a specific casting speed. As the change in casting speed takes effect, the spray water volumes are also immediately modified, and the resulting temperatures on the strand surface are displayed to the continuous casting machine operator. If temperature scanners are used in the plant, the dynamic secondary cooling control system is able to adapt to the values delivered by the scanners, so that the coefficients of the strand temperature field calculation can be adapted to the values measured.
Dynamic 3D secondary cooling system – The first-generation dynamic solution was characterized by a two-dimensional temperature calculation of the strand centre. The strand corners were largely neglected by the process model. Continuous improvements in computer performance have now made it possible to calculate the temperature at any point within the entire strand in real time, in a full three-dimensional mode and in a sufficiently fine discretization yielding very detailed temperature profiles as can be seen for strand surface and strand centre.
The model is based on an explicit finite-volume approximation which solves the heat transfer equation and takes into consideration temperature-dependent material properties such as density as well as the position-specific cast product thickness and width. Dynamic 3D secondary cooling system accurately assesses the heat transfer from the cast product surface resulting from radiation, heat transfer to the rolls, natural convection and spray water. Further, the dynamic 3D secondary cooling system can be applied for both spray cooling and air-mist cooling and takes into account the spray distribution pattern of the nozzles and the actual spray water temperature. This ensures an accurate spray-cooling heat transfer prediction to temperatures below 700 deg C when the Leidenfrost phenomenon disappears. The result is an even more precise determination of the strand surface-temperature profile and the final point of strand solidification.
Based on the precise temperature calculations the dynamic 3D secondary cooling system allows specifying the desired surface temperature not only along the strand length, but also across the strand width. Even individual control of the water flow and positioning of each cooling nozzle is possible. The control algorithms of the dynamic 3D secondary cooling system calculate the water flow set-points to achieve the target strand surface temperature values. Pyrometer measurement results show an excellent fit in between calculated and measured lateral strand temperature profile.
Application of the dynamic 3D secondary cooling system allows introducing completely new philosophies to set up cooling practices for upcoming challenges in continuous casting. The combination with moveable spray nozzles (3D sprays) yields unprecedented quality results.
The advanced secondary cooling dynamic 3D model derives correct water flow rates even in transient casting situations such as steel grade changes, casting speed variations, different tundish temperatures, tundish exchanges, and at the beginning and end of a casting sequence. The water flow rate for each cooling zone is calculated to maintain a defined surface temperature profile throughout the entire casting sequence. The maintenance system allows the process engineer to change cooling practices easily and introduce continuous casting shop specific cooling expertise. The off-line simulation system is used to test the effect of the new settings in various casting situations before utilization in the production process.
Dynamic phase calculation of material properties – In order to calculate a 3-dimensional temperature profile of the strand, material properties like enthalpy, solid fraction, density, and conductivity as a function of the temperature are to be known. In case, these properties are experimentally known for a given steel grade composition, these functions can be entered by the process engineers in the MSS, which is very time-consuming. Normally the process engineer does not know these thermo-physical properties. The software model calculates all the thermo-physical data used by 3D model. Dynamic phase calculation of material properties is available as an on-line tool to determine the material properties for the current steel grade analysis.
The traditional approach is to define the thermo-physical properties for grade groups with a pre-defined concentration range of the chemical analysis. Using the dynamic phase calculation, these data can be calculated for each individual steel grade. This makes the prediction of quantities such as the point of complete solidification on the strand and the temperature distribution of the strand during casting more accurate and hence allows for precise metallurgical treatments which can lead to an improved quality of the products. Further, the model indicates whether the current analysis of the steel is peritectic or not and alerts the operator in the event of an unexpected peritectic grade. This can reduce the risk of breakouts and improves quality.
The dynamic phase calculation is based on thermodynamical models. The liquid-solid phase transformation in the high temperature range is described by a Gibbs free energy model in combination with a micro-segregation model. For solid-solid phase transformations in the low temperature range an Avrami type model is employed. The free parameters of the models are determined with the help of experimentally measured quantities. Using off-line simulations of dynamic phase calculation together with the 3D model allows metallurgical development of new steel grades.
Traditionally the steel grades are grouped and a typical chemical analysis for the group is used to determine the material properties. With dynamic phase calculation, the material properties are derived from the actual steel analysis. Calculations can show that there can be a difference in the point of final solidification of half a meter or even more by comparing the results of the actual steel analysis versus the grade group analysis. This fact shows the importance of having an on-line calculation of the actual steel grade in order to improve the quality of the cast products.
Dynamic gap soft reduction – Dynamic gap soft reduction stands for dynamic roll-gap adjustment in the continuous casting process. This is made possible by specially designed strand-guide segments – known as ‘smart segments’ in which the roller gaps can be remotely adjusted for strand thickness changes and for improved internal strand quality. On the basis of the on-line information provided by the dynamic 3D thermal-tracking model, the dynamic gap soft reduction dynamically calculates the set points of the adjustable roll gap.
Supervision of the roll engagement, depending on the state of solidification (liquid, mushy, or solid) and the calculated strand-thickness profile, is a decisive factor for precise roll adjustments and thus improved product quality. An optimized roll engagement also reduces excessive forces on the strand and decreases roller wear. The more accurate control of the roller gaps allows additional casting strategies to be implemented such as liquid-core reduction and intentional bulging soft reduction. I.e. intentional dynamic gap increase before the soft reduction area allows for higher thickness reduction in this area. This further improves the casting flexibility and the product quality.
Dynamic gap soft reduction makes it possible to freely define scenarios for start-up, tundish change, and tail out strategies based on the strand thickness, steel grade, and casting status. In this way roll damage and production interruptions, which can arise from the different casting behaviour of the cold strand head or end, can be avoided.
Nozzle expert for early clogged nozzle detection – Cooling water is sprayed through nozzles onto the strand with the objective of achieving uniform cooling of the steel. However, if one or more of these nozzles are clogged, then a section of the strand cannot be uniformly cooled to the required temperature. This can lead to surface defects, and the cast product possibly has to be down-graded. The issue of changing segments in the continuous casting machine is also a source of difficulty. Hoses can easily be ruptured or jammed. Aware of the consequences of leakages or clogged nozzles, maintenance personnel spend a large number of working hours checking whether nozzles are operating properly.
The nozzle expert helps to detect clogged nozzles and broken hoses in the continuous casting machines and thus ensures that the strand is evenly cooled for high quality steel production. It automatically monitors the condition of the nozzles during the casting process. The model can also be manually activated during casting breaks. The advantage is that nozzle status can be checked following maintenance work or segment changes and immediately repaired before the casting process is restarted.
The model calculation considers parameters like nozzle type (measuring results from the nozzle test stand), height between pressure measuring device, water pressure, pipe lengths, pipe diameters, and nozzle positions. Any modifications to the secondary cooling system e.g. use of different nozzle types needs a change in the set-up of the nozzle expert in order to get correct computational results.
The nozzle expert is based on statistical models and indicates the clogging ratio in each zone (e.g., zone 2 nozzles clogged 10 % with a probability of 96 %). Operators need only to inspect zones for which an alarm is generated. Calculations begin automatically with the start cast signal, and the condition of the nozzles is monitored throughout the casting process. Several alarms help to detect leakages, clogged nozzles, and even falsely installed nozzles on a segment.
Inter-mix expert – It improves yield by prior simulations. During sequence casting, a mixing of steel grades takes place in the tundish and therefore in the strand with each ladle change. On the basis of the chemical composition of the steel, the inter-mix expert calculates whether the mixed steel zones can be used for the foreseen product application or if the steel has to be downgraded or even scrapped. Information acquired from tundish flow experiments combined with analysis results of steel samples taken from solidified products ensures a high degree of accuracy of Inter-mix predictions with respect to the actual composition of the mixed steel zones.
The inter-mix expert determines traces of the previously cast heat present in the current heat. Steel mixing takes place not only in the tundish but also in the mould and upper parts of the strand. Mixing in these areas is evaluated by a mix-box-type sub-model of inter-mix which makes it possible to calculate the chemical composition of the steel at any position along the cast strand.
Tundish changes or the use of separator plates are treated individually. Inter-mix calculations are cyclically performed for selected chemical elements starting with the ‘ladle open event’ of a new heat. The final decision about the compatibility of heats cast in sequence is performed by the heat-assignment function of inter-mix. The concentration profiles of certain critical elements which have an impact on the final product disposition (prime, downgraded, or outright rejection) are determined. A deviation is detected if one of the critical elements does not match the steel-grade specification.
The full benefit from the inter-mix model is achieved by combining the model output with the yield expert model which assures maximum prime quality yield by applying cut-length optimization to incompatible steel areas along the strand which are designated as scrap.
Process engineers work with the powerful simulation environment, which makes it possible to simulate any combinations of different steel grades. Input parameters like analysis, tundish weight, and dimensions of the strand can be easily entered and modified and the computed results are made visible in the HMI. Graphs are displayed for single analysis elements or combinations of more elements. Valuable information like volume concentration, mixed steel length, scrap length, and heat ranges on the strand are shown on the bottom of the graphs.
Configuration of the model can be easily done in the MSS. The process engineer can choose which chemical elements are to be used to determine the inter-mix for any grade link. A powerful simulation environment allows simulating the mixing behaviour of two different grades and the computed volume concentration, calculated analysis along the strand, and heat ranges including possible scrap sections are displayed.
Speed expert – The speed expert model is for the optimum casting speed in any casting situation. Selection of a proper casting speed on the continuous casting machine is of high importance. Several aspects (e.g. quality, safety, machine limits, and production requirements) influence the choice of the casting speed. These different aspects are frequently contradictory such as increase in production calls for a high casting speed whereas the safety requirements limit the casting speed. Normally, several continuous casting shops have self-made software solutions to calculate the casting speed considering different aspects. The aim of the speed expert is to cover most aspects and to provide an easy maintenance tool which enables the process engineer to adjust the behaviour of the speed expert to the special needs.
The speed expert calculates cyclically the optimum casting speed. The calculation of the casting speed is based on various rules, which consider the different aspects and are specified in the speed expert practice. Each rule determines a speed range which satisfies its requirements. The speed expert first determines the inter-section of all these speed ranges. If the inter-section is not empty, then it selects a casting speed depending on the predefined strategy, which can be maximum speed, aim speed, or avoid speed changes as long as actual casting speed is in the valid range. If there is a conflict between the different rules, then the inter-section is empty. In this case the pre-selected conflict resolve strategy is applied which can be (i) priority (lower priority rules are to be neglected till a solution can be found), or (ii) minimum of maximum speed (the smallest of all maximum speeds is to be selected).
On the on-line HMI the casting machine operator can view the speed ranges of all rules and the derived optimum casting speed. The casting operator can change the priorities of the different rules, the strategy, and the conflict resolve strategy to fine adjust the calculation if necessary. Speed set-points are sent to Level 1 and can be executed automatically.
MSS is used to define the speed expert practice considering (i) quality related rules consisting of quality expert rule, minimum / aim / maximum speed for the steel grade, superheat, Mn/S ratio, low tundish weight, and optimum soft reduction, (ii) production related rules consisting of heat pacing, start cast, and clearing, and (iii) safety related rules consisting of machine protection, and forecast calculation for minimum and maximum speed.
Optimum soft reduction can be achieved if the final point of solidification is at the end of a strand segment. A pre-calculation assuming steady state conditions determines the required casting speeds for each strand segment.
Yield expert – The aim of the yield expert is to minimize scrap and to optimize the yield. It considers scrap portions, quality defects, weight restrictions, sample cuts, and width changes while producing the maximum number of scheduled products. The important features of the yield expert are (i) optimization of product length or product weight in the case of scrap sections or quality-related defects, (ii) scheduling of mould width adjustments, (iii) scrap section allocation algorithms, (iv) optimization steps can be switched on-line and off-line, and (v) replay of cut-to-length optimization steps, even in actual production situations
Quality expert – Quality expert determines the definitions necessary for the quality-related process parameters, tracks the actual data during production, predicts the quality of the cast products, and automatically determines the subsequent product disposition. It supports the continuous casting machine operators by on-line quality alerts and a preview of the quality of the cast strands in the casting machine. Quality expert is of two distinct types distinguished by basic or comprehensive product quality rating capability.
All the tracked information and calculation results can be transferred from the production module of the quality expert to the so-called discovery system. This system is dedicated to the long-term archiving and evaluation of the huge amount of information tracked.