Otomasi, Kontrol, dan Pemodelan Pembuatan Baja Oksigen Dasar
Otomasi, Kontrol, dan Pemodelan Pembuatan Baja Oksigen Dasar
Dalam proses pembuatan baja oksigen dasar, tungku oksigen dasar atau konverter menghasilkan baja cair dengan mengurangi kandungan karbon logam panas yang dibuat oleh tanur tinggi dari sekitar 4,5% menjadi 0,03% menjadi 1,0%. Konverter meniupkan sejumlah besar oksigen murni ke dalam logam panas dan memurnikannya menjadi baja dalam waktu singkat. Saat ini, proses pembuatan baja oksigen dasar menggunakan hembusan gabungan (tiupan atas dan bawah). Blowing bawah dilakukan dengan gas inert. Berbagai bahan digunakan oleh konverter selama pemurnian. Selain logam panas dan skrap besi sebagai bahan baku utama, bahan lain yang digunakan dalam proses pembuatan baja oksigen dasar adalah kapur terkalsinasi, dolomit terkalsinasi atau magnesit terkalsinasi untuk pembentukan terak yang tepat dan pendingin yang berbeda (seperti bijih, besi spons, dll.) selama proses berlangsung. . Pengoperasian konverter memerlukan suhu gas yang disetel tinggi, dan menghasilkan banyak debu.
Tujuan dari proses pembuatan baja oksigen dasar adalah untuk memurnikan logam cair (cairan cair + logam panas) dan untuk menyesuaikan komposisi dan suhu baja cair. Untuk memenuhi tujuan ini, sistem otomasi dan kontrol digunakan untuk proses pembuatan baja yang biasanya terdiri dari sistem otomasi dasar dan sistem kontrol proses.
Fasilitas teknik pada pembuatan baja oksigen dasar pada kenyataannya adalah desain dan pemasangan bersama dari berbagai sub-sistem. Peralatan utama pembuatan baja oksigen dasar adalah bejana konverter berlapis refraktori (tungku oksigen dasar) di mana proses pembuatan baja berlangsung. Selain bejana konverter, proses pembuatan baja memiliki beberapa sub-sistem yang terdiri dari (i) penggerak kemiringan bejana konverter, (ii) sistem oxygen lance, (iii) sistem pengadukan dasar gas inert, (iv) pendinginan gas atas (gas konverter), pembersihan, analisis, dan sistem pemulihan, (v) sistem pengukuran sub-lance, (vi) sistem pencegahan slopping, (vii) sistem penanganan material, (viii) sistem pengisian sisa, (ix) sistem pengisian fluks dan pendingin, (x) sistem pengisian ferro-alloy, (xi) pengukuran suhu horizontal dan sistem pengambilan sampel, (xii) sistem penyadapan otomatis, (xiii) sistem penghenti terak, (xiv) sistem dedusting sekunder, (xv) sistem interlocking dan alarm, dan (xvi) sistem antarmuka mesin manusia (HMI).
Selain sub-sistem ini, pembuatan baja oksigen harus dioperasikan secara terintegrasi dengan proses hulu dan hilir. Selain itu, proses pembuatan baja harus dihubungkan dengan sistem eksternal seperti (i) laboratorium bengkel peleburan baja yang menampung spektrometer emisi optik, dan spektrometer fluoresen sinar-x dan peralatan analisis lainnya, dan (ii) kontrol pengawasan dan akuisisi data (SCADA) sistem.
Pembuatan baja oksigen dasar adalah proses fisiko-kimia yang kompleks yang memiliki sejumlah besar faktor yang mempengaruhi. Dua metode digunakan untuk mengontrol hembusan di konverter. Metode pertama menggunakan pengukuran tidak langsung dengan gas buang, sedangkan metode kedua menggunakan pengukuran langsung dengan sub-lance. Pada metode kedua ada pengukuran langsung suhu (dalam derajat C) baja cair secara bersamaan selama peniupan. Metode ini juga digunakan untuk berbagai keperluan seperti bath levelling, slag levelling, pengukuran konsentrasi oksigen, dan slag sampling.
Dalam proses pembuatan baja oksigen dasar, model proses klasik masih berlaku di mana operator diharuskan mengetahui sebanyak mungkin tentang input, parameter proses, dan output, dan dia perlu memiliki informasi ini tersedia secara bebas untuk membuat yang diperlukan penyesuaian proses, sehingga menghasilkan produk dengan kualitas prima. Untuk mencapai hal ini, berbagai teknik kontrol dan estimasi diperlukan untuk digunakan dan teknik ini berfungsi secara terorganisir untuk memberikan informasi yang diperlukan untuk tindakan operator.
Sub-sistem yang sesuai dengan hierarki teknik ini adalah (i) pengukuran massa logam panas, (ii) analisis logam panas, (iii) pengadukan dasar gas inert, (iv) umpan oksigen, (v) suhu dan analisis pengisian, (vi ) sistem pengisian fluks dan pendingin, (vii) sistem pengisian ferro-alloy, (viii) komputer kontrol proses, dan (ix) komputer manajemen. Pengukuran yang diperlukan selama proses pembuatan baja adalah (i) pengukuran suhu, (ii) kandungan karbon bath, (iii) kedalaman bath, dan (iv) analisis kimia lengkap. Hal ini biasanya dicapai dengan menghentikan proses, memiringkan konverter, dan mengambil suhu dan sampel secara manual.
Kontrol proses adalah bagian penting dari operasi pembuatan baja oksigen dasar karena waktu produksi panas dipengaruhi olehnya. Beberapa strategi pengendalian proses pembuatan baja tersedia saat ini, dan pabrik baja menggunakan strategi tergantung pada fasilitas dan kebutuhannya. Model kontrol proses dapat dibagi menjadi dua kategori yaitu (i) statis, dan (ii) dinamis.
Bentuk paling sederhana dari kontrol proses didasarkan pada model proses statis. Ini terdiri dari satu set keseimbangan untuk panas, oksigen, besi, dan terak, dikombinasikan dengan persamaan keadaan. Yang terakhir menjelaskan hubungan antara kandungan besi dalam terak, kandungan mangan dan karbon yang sebenarnya dalam baja, dan kebasaan terak. Model statis menentukan jumlah oksigen yang akan ditiup dan muatan ke tungku, dengan memberikan informasi awal dan akhir tentang panas, tetapi tidak menghasilkan informasi tentang variabel proses selama peniupan oksigen. Model statis pada dasarnya seperti penembakan anak panah. Tidak ada kontrol lebih lanjut setelah panah meninggalkan busur.
Dalam hal kontrol proses dinamis, informasi yang akurat tentang keadaan sebenarnya dari proses blowing diperlukan. Idealnya, informasi berkelanjutan tentang komposisi baja, terak, dan gas serta suhu harus tersedia dan digunakan secara online untuk pengawasan proses. Setiap penyimpangan dari kemajuan proses yang diantisipasi kemudian dapat dideteksi dan, berdasarkan model, suplai oksigen dapat disesuaikan atau fluks tambahan dapat ditambahkan ke dalam konverter. Dalam konverter pembuatan baja dasar, ini hanya mungkin dalam situasi yang ideal. Dalam praktiknya, situasinya sama sekali berbeda. Khususnya dalam proses pembuatan baja oksigen dasar, ada batasan praktis yang kuat untuk pengukuran kontinu, misalnya getaran, debu, suhu tinggi dan logam cair serta fase terak. Model dinamis melakukan penyesuaian selama tiupan oksigen berdasarkan pengukuran tiupan tertentu.
Persyaratan proses yang dikontrol secara dinamis adalah (i) tidak mengganggu proses dan (ii) mendapatkan pengukuran waktu nyata. Sistem sub-tombak yang dapat menangani kondisi proses dan memanfaatkan sensor sekali pakai di ujung tombak digunakan untuk tujuan ini. Sensor yang berbeda dicirikan oleh fungsi pengukurannya, yang paling penting adalah (i) pengukuran suhu rendaman, (ii) pengukuran karbon rendaman, dan (iii) pengukuran level rendaman. Kombinasi apa pun dapat digunakan.
Fungsi utama dari sistem otomasi dasar termasuk kontrol tombak oksigen, kontrol material, kontrol pengadukan bawah, kontrol pendeteksian sub-tombak, dan kontrol titik akhir. Sistem kontrol proses melakukan manajemen produksi, model kontrol, kontrol proses, dan manajemen data. Sistem kontrol proses digunakan untuk mengontrol sistem otomasi dasar. Pertama, ia mengumpulkan informasi tentang proses peleburan dan deteksi yang dilakukan oleh sub-lance. Kemudian menilai status proses peleburan sesuai dengan hasil perhitungan model. Terakhir, ia mengirimkan sinyal ke sistem otomatisasi dasar untuk mengontrol parameter yang disesuaikan.
Otomatisasi dan kontrol pembuatan baja oksigen dasar tidak hanya mempertimbangkan fungsi proses khusus konverter, tetapi juga mempertimbangkan parameter yang relevan dari bahan pengisian, termasuk persiapan logam panas, pengelolaan halaman bekas, dan logistik penjadwalan. Solusi optimasi proses (Level-2) didasarkan pada persamaan algoritme lanjutan, yang secara akurat mewakili reaksi metalurgi termodinamika yang kompleks. Solusi ini terutama cocok untuk berbagai kondisi operasi, mis. memo variabel untuk rasio logam panas, praktik terak minimum, dan kandungan fosfor yang bervariasi.
Tujuan utama dari otomatisasi dan kontrol proses pembuatan baja oksigen dasar adalah (i) memenuhi persyaratan pembuatan baja, dan (ii) memberikan bantuan operasional. Selanjutnya, otomatisasi dan kontrol proses pembuatan baja adalah cara yang efektif (i) untuk memberikan informasi proses yang komprehensif dan konsisten untuk panduan operator, (ii) untuk memastikan operasi standar untuk kualitas homogen baja cair, (iii) untuk meningkatkan kinerja proses, (iv) meningkatkan akurasi kontrol titik akhir, (v) memperpendek siklus panas, (vi) meningkatkan produktivitas melalui pembuatan baja yang dioptimalkan, dan (vii) mengurangi biaya produksi dengan menggunakan proses model untuk penggunaan material dan input energi yang dioptimalkan. Otomatisasi dan kontrol terutama bergantung pada komputer dan tidak dapat dipisahkan dari mekanisasi proses pembuatan baja.
Struktur arsitektur umum dari otomatisasi dan kontrol proses pembuatan baja oksigen dasar menggabungkan (i) sistem informasi perusahaan, (ii) sistem informasi manajemen bengkel peleburan baja, (iii) kontrol proses, dan (iv) instrumen dan peralatan lapangan.
Seperti yang dapat dikurangkan dari berbagai sub-sistem dan antarmuka yang ada di antara mereka, menjadi jelas bahwa interlinking yang diperlukan tidak dapat dicapai dengan sirkuit konvensional (analog). Oleh karena itu, peralatan kontrol proses digital harus digunakan secara luas yang menawarkan berbagai keuntungan. seperti (i) penambahan dan perubahan sistem dapat dengan mudah diakomodasi, (ii) strategi kontrol lanjutan dapat ditangani, (iii) kecerdasan dapat diprogram ke dalam sistem, (iv) fasilitas cadangan yang efektif dapat ada, (v) CRT (katoda antarmuka operator tabung sinar) dapat digabungkan dengan opsi tampilan format besar, (v) keberadaan data yang disimpan, (vi) akses mudah ke informasi dan data yang disimpan, dan (vii) komunikasi antara hierarki yang lebih tinggi dan lebih rendah. Gambar 1 menunjukkan otomatisasi dasar dan sistem kontrol proses pembuatan baja oksigen dasar.
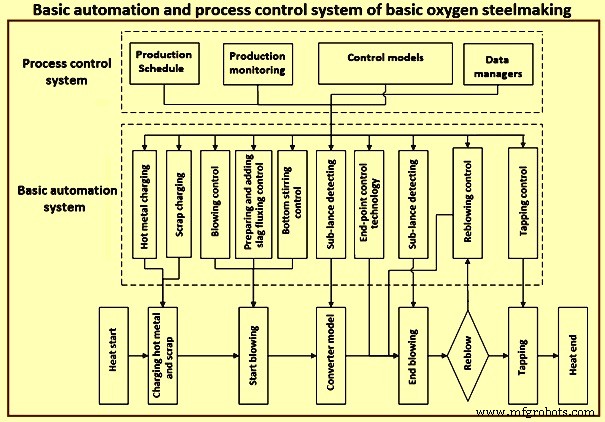
Gbr 1 Otomatisasi dasar dan sistem kontrol proses pembuatan baja oksigen dasar
Peningkatan kecepatan dan kapasitas komputer, adopsi pengontrol logika yang dapat diprogram (PLC) dalam sistem kelistrikan dan kontrol, dan peralihan dari instrumentasi analog ke digital telah menghasilkan peningkatan yang luar biasa dalam akurasi kontrol. Selanjutnya, penerapan kontrol digital langsung belakangan ini telah mempercepat otomatisasi proses pembuatan baja.
Seiring dengan kemajuan komputer proses dan teknologi pengukuran periferal, kontrol hembusan untuk konverter telah bergeser dari sistem kontrol statis ke sistem kontrol operasional dinamis atau otomatis penuh. Selanjutnya, karena kemajuan teknologi yang dibuat dalam sistem kelistrikan dan kontrol, pengontrol telah berpindah dari panel instrumen ke tampilan CRT yang memungkinkan operator memantau dan mengontrol proses pembuatan baja di layar CRT. Selain itu, dengan penggunaan model matematika dan sistem pakar (menggunakan program kecerdasan buatan), otomatisasi dan kontrol proses pembuatan baja menjadi lebih ramah operator.
Sistem kontrol untuk sub-sistem yang berbeda sering dikonfigurasi sebagai DCS (sistem kontrol terdistribusi) dan PLC (pengontrol logika yang dapat diprogram) yang terhubung dengan mulus ke DCS tungku oksigen dasar dan menyediakan pemantauan dan kontrol terintegrasi. Keuntungan unik dari pendekatan terpadu ini adalah mencakup aspek stabilitas proses, kualitas produk, fleksibilitas operasi, dan lingkungan kerja yang lebih baik sambil menjaga efisiensi dan efektivitas biaya.
Instrumentasi kontrol terdistribusi mengakomodasi (i) konsol operator produksi, (ii) mimik langsung, (iii) tampilan dan kontrol instrumen, (iv) grafik tren, (v) dan log. Komputer terdistribusi pada data-highway digunakan dengan I/O (input/output) yang diperlukan untuk menangani (i) sistem air, (ii) sistem penimbangan, (iii) sistem pengaduk bawah, (iv) sistem oksigen, dan (v ) komunikasi dengan komputer induk. Informasi manajemen / komputer kontrol biasanya merupakan sistem berkapasitas besar yang terutama digunakan untuk (i) menyediakan informasi yaitu laporan shift / hari / bulan, (ii) menangani produksi interaktif, (iii) penjadwalan antara pabrik hilir / hulu, (iv) mempersiapkan untuk pengisian (pre-Ioading scrap dll), (v) mengakomodasi model statis seperti keseimbangan panas, menentukan fluks (kapur/ dolomit) dan agen pendingin (besi spons / bijih besi), jumlah serta waktu pengisian , dan keseimbangan oksigen (menentukan laju, durasi, dan pola pukulan), (vi) mengakomodasi model dinamis yang mulai beroperasi setelah sub-tombak memberikan informasi waktu nyata. Sistem menghasilkan tampilan aktif yang memungkinkan operator untuk mengakhiri proses sesuai target, menghitung hasil akhir, dan menyarankan modifikasi kecil serta menambahkan paduan akhir.
Model kontrol adalah bagian inti dari sistem kontrol pembuatan baja otomatis. Mereka mengintegrasikan pengetahuan tentang mekanisme peleburan, statistik matematika, prinsip ahli, dan pembelajaran adaptif. Persamaan kontrol diturunkan dengan menggunakan pengetahuan tentang mekanisme peleburan dan parameter kontrol utama ditentukan oleh statistik matematika dan prinsip ahli. Selain itu, parameter kontrol ini dapat dimodifikasi secara teratur melalui pembelajaran adaptif. Model kontrol mengacu pada model kontrol statis, model bahan utama, model pembentukan terak, model suhu, model konsumsi oksigen, model kontrol dinamis, model slopping, model paduan, dan model titik akhir dll. Selanjutnya, ada juga pembelajaran adaptif model. Berbagai peralatan pendeteksi yang digunakan adalah sub-lance, spektrometer massa, spektrometer nyala, pengukur jarak gelombang mikro, dan alat pemantau getaran tombak oksigen, dll.
Selanjutnya, saat ini terdapat beberapa model kontrol, seperti model mekanisme, model statistik, dan model inkremental, dll. Model mekanisme didasarkan pada kekekalan panas dan massa. Ini menentukan hubungan antar variabel dengan derivasi matematis. Namun, tidak cocok untuk aplikasi karena kerumitan proses peleburan. Model statistik didasarkan pada teori kotak hitam. Proses fisiko-kimia diabaikan dalam model ini. Ini hanya berkaitan dengan hubungan statistik antara parameter input dan output. Keakuratan perhitungan model ini tidak dapat dipertahankan selama kondisi lelehnya berubah. Dengan menggunakan model inkremental, parameter operasi dapat disempurnakan dengan membandingkan dengan data produktivitas yang direkam. Dapat mengatasi pengaruh yang disebabkan oleh perubahan kondisi leleh. Namun, kelemahan utama dari model ini adalah akurasi perhitungan yang rendah. Gambar 2 menunjukkan fungsi sistem kontrol dan model proses.
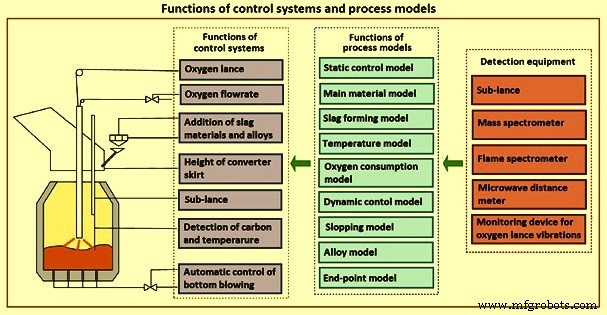
Gbr 2 Fungsi sistem kontrol dan model proses
Prediksi karbon titik akhir
Prediksi karbon titik akhir pada awalnya mengandalkan pengalaman dan keterampilan operator. Telah diketahui bahwa metode ini tidak efisien dan sulit, terutama untuk proses peleburan baja karbon tinggi sedang. Dengan berkembangnya teknologi komputer dan informasi, telah dilakukan studi tentang kendali komputer pada pembuatan baja oksigen dasar. Model muatan statis berdasarkan perhitungan komputer pertama kali dieksploitasi oleh Jones &Laughlin Steel Corporation, dan digunakan untuk menghitung jumlah logam panas yang dibebankan, skrap, dan material terak serta memandu kontrol karbon titik akhir baja cair.
Dengan perkembangan pesat metode deteksi otomatis, model matematika, dan algoritme, prediksi karbon titik akhir yang dinamis dan cerdas telah tersedia untuk proses pembuatan baja. Berdasarkan fitur data yang dikumpulkan, yang telah digunakan untuk menghitung kandungan karbon titik akhir, prediksi karbon titik akhir dibagi menjadi tiga tahap, seperti prediksi statis, prediksi dinamis, dan prediksi cerdas.
Prediksi statis – Selama seluruh proses pembuatan baja oksigen dasar, operator biasanya dibantu oleh sistem panduan berbasis komputer, yang mengusulkan parameter proses dan tindakan operator berdasarkan perhitungan neraca massa dan energi serta perhitungan termodinamika. Prediksi karbon titik akhir statis terutama bergantung pada model matematika yang dibuat berdasarkan keseimbangan massa dan panas, yang dapat menghitung kandungan karbon titik akhir dalam baja cair berdasarkan parameter muatan awal (seperti logam panas dan skrap bermuatan, dan komposisi dan suhu logam panas). Gambar 3 menunjukkan model statis untuk prediksi titik akhir untuk pembuatan baja oksigen dasar.
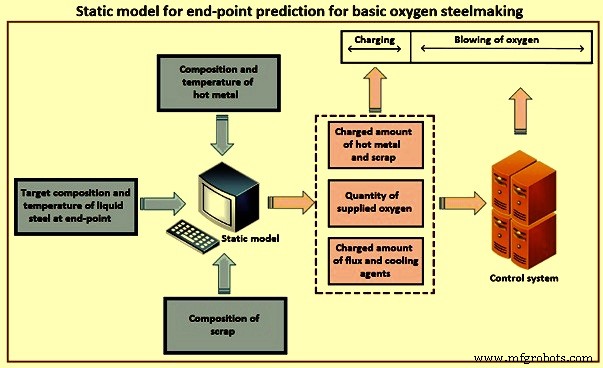
Gbr 3 Model statis untuk prediksi titik akhir untuk pembuatan baja oksigen dasar
Poin kunci dari prediksi karbon titik akhir statis adalah pembentukan mode matematis yang masuk akal dan perolehan data jumlah awal. Dibandingkan dengan keacakan dan ketidakpastian prediksi karbon titik akhir berdasarkan pengalaman dan keterampilan operator, prediksi karbon titik akhir statis dapat melakukan perhitungan kuantitatif oksigen yang ditiup dan kandungan karbon titik akhir, yang meningkatkan akurasi prediksi karbon titik akhir. Model matematika yang biasanya digunakan untuk prediksi karbon titik akhir statis terutama mencakup model teoretis, dan model statistik
Model teoritis dapat menghitung jumlah oksigen yang ditiup dan kandungan karbon titik akhir berdasarkan perhitungan keseimbangan massa dan panas selama proses pembuatan baja. Karena interaksi kompleks antara berbagai faktor yang berpengaruh dalam proses pembuatan baja dasar, perhitungan keseimbangan massa dan panas biasanya dilengkapi dengan nilai empiris dan tidak akurat, oleh karena itu, model teoritis menunjukkan kinerja yang relatif buruk pada prediksi karbon titik akhir konverter pembuatan baja dasar. .
Model statistik hanya menyangkut hubungan antara variabel input dan variabel output menggunakan analisis statistik dari data yang dikumpulkan tanpa mempertimbangkan mekanisme reaksi kimia dalam penangas cairan, yang digambarkan oleh persamaan X =F (W, S, T, t, Z) , di mana 'F' adalah fungsi linier atau nonlinier, 'W' adalah berat muatan logam panas dan skrap,' S' adalah nilai target komposisi titik akhir dalam baja cair, 'T' adalah suhu awal panas logam, 't' adalah waktu penghembusan oksigen, dan 'Z' adalah faktor penting lain yang berpengaruh (seperti ketinggian tombak atas dan tekanan oksigen).
Sebagai semacam model statistik, jaringan saraf propagasi balik yang dikombinasikan dengan algoritma yang berbeda diterapkan secara luas pada prediksi titik akhir untuk pembuatan baja oksigen dasar dalam beberapa tahun terakhir. Dibandingkan dengan model teoretis, jaringan saraf terspesialisasi dalam menganalisis penyimpangan acak dan menghilangkan pengaruh faktor acak dan dapat memberikan referensi yang lebih andal untuk prediksi karbon titik akhir. Gambar 4 menunjukkan jaringan saraf propagasi balik untuk prediksi karbon titik akhir.
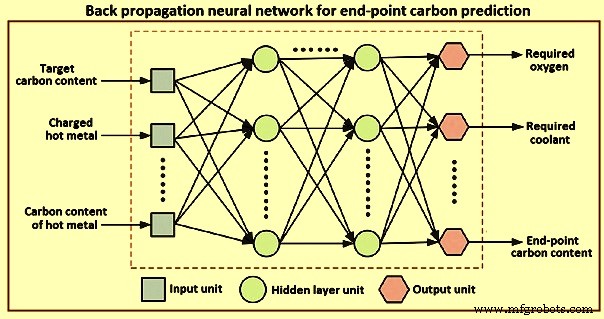
Gbr 4 Jaringan saraf propagasi balik untuk prediksi karbon titik akhir
Namun, model teoritis dan statistik yang dijelaskan pada bagian di atas hanya dibangun berdasarkan pertimbangan kondisi awal dan data proses statis (dataset kecil tanpa fitur deret waktu tidak dapat mewakili produksi aktual), membuat model prediksi karbon titik akhir statis tidak cocok untuk produksi aktual karena akurasi prediksi terbatas. Tantangan khusus prediksi karbon titik akhir statis adalah pembentukan model prediksi yang masuk akal berdasarkan kumpulan data produksi besar yang memiliki fitur deret waktu. Berdasarkan tantangan di atas, prediksi karbon titik akhir dinamis berkembang pesat berdasarkan prediksi statis.
Prediksi dinamis – Berbeda dengan kontrol statis, prediksi karbon titik akhir dinamis dapat memprediksi kandungan karbon titik akhir dalam baja cair dan memenuhi penyesuaian parameter operasi secara online dengan kalkulasi model dinamis yang ditetapkan pada data deret waktu (gerakan tombak , tingkat karbon mono-oksida dan karbon di-oksida dari off-gas, fitur spektral api) yang dikumpulkan oleh perangkat pemantauan. Saat ini, sistem sub-lance, sistem analisis off-gas, dan sistem analisis spektrometri nyala adalah metode utama yang diterapkan pada prediksi karbon titik akhir dinamis untuk pembuatan baja oksigen dasar. Gambar 5 menunjukkan prediksi karbon titik akhir dinamis dengan sistem sub-lanskap.
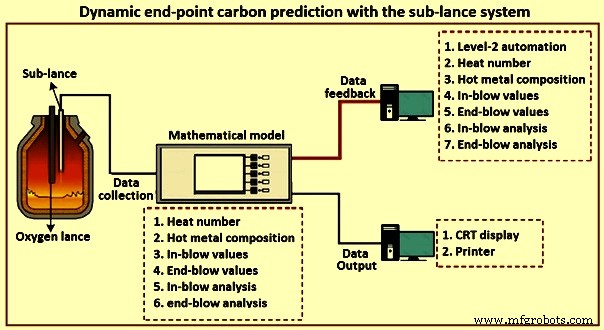
Gbr 5 Prediksi karbon titik akhir dinamis dengan sistem sub-lance
Prediksi titik akhir dinamis dengan sistem sub-lance secara langsung mengukur kandungan karbon baja cair pada tahap selanjutnya dari proses blowing, membangun model prediksi on-line, dan secara dinamis memprediksi kandungan karbon dengan waktu blowing yang berbeda. Dengan penerapan sistem sub-lance, pengaruh deviasi awal pada bahan bermuatan dapat dikurangi, dan prediksi karbon titik akhir lebih akurat dan tepat dibandingkan dengan prediksi statis. Beberapa toko peleburan baja Jepang mencapai akurasi prediksi karbon lebih dari 90% dengan toleransi kesalahan + / – 0,02 %.
Melalui pemantauan informasi off-gas (karbon mono-oksida dan perubahan kandungan karbon dioksida selama peniupan oksigen), kandungan karbon baja cair dapat disimpulkan secara dinamis dengan model matematika berdasarkan informasi off-gas, dan akhirnya kandungan karbon titik dapat diprediksi dan dikendalikan dengan umpan balik hasil perhitungan. Karena, ini adalah metode estimasi tidak langsung, keakuratan data yang dikumpulkan (seperti kandungan off-gas dan laju aliran) dan waktu respons model matematika sangat mempengaruhi akurasi prediksi karbon titik akhir. Oleh karena itu, sistem analisis off-gas biasanya digunakan bersama dengan sistem sub-lance untuk mengontrol karbon titik akhir dengan akurasi yang diperlukan di beberapa toko peleburan baja.
Fitur spektral api di mulut konverter oksigen dasar terkait dengan kandungan karbon baja cair dan karenanya, berubah selama proses pembuatan baja dasar. Berdasarkan karakteristik spektral dari informasi radiasi nyala, sistem analisis spektrometri nyala telah dikembangkan untuk memprediksi kandungan karbon titik akhir. Prediksi on-line kandungan karbon baja cair dapat diselesaikan, melalui analisis hubungan antara spektrum nyala dari waktu bertiup yang berbeda dan status mandi konverter.
Sensor optik telah digunakan untuk memprediksi secara dinamis kandungan karbon dari pemanasan karbon rendah (target titik akhir kandungan karbon lebih rendah dari 0,06 %) dalam pembuatan baja oksigen dasar di bengkel peleburan baja, yang telah menghasilkan peningkatan yang signifikan.
Meskipun prediksi karbon titik akhir dinamis dapat memberikan peningkatan prediksi yang signifikan jika dibandingkan dengan prediksi statis, kumpulan dataset nyata, berukuran penuh, dan kaya yang dapat mewakili perilaku keseluruhan dari seluruh proses pembuatan baja, pembelajaran mandiri, dan menyesuaikan diri dari model prediksi adalah tantangan khusus prediksi karbon titik akhir yang dinamis. Oleh karena itu, prediksi karbon titik akhir yang cerdas dibuat berdasarkan prediksi karbon titik akhir yang dinamis.
Prediksi cerdas – Dengan pengembangan pengumpulan data dan model cerdas, prediksi karbon titik akhir cerdas untuk pembuatan baja oksigen dasar kini telah tersedia. Ini dibuat berdasarkan kumpulan data berukuran penuh dan kaya dengan fitur berbeda dan memiliki kemampuan belajar mandiri yang kuat untuk meningkatkan akurasi prediksi. Selain sistem sub-lance, sistem pembuatan baja oksigen dasar otomatis terutama mengadopsi teknik lain yaitu (i) deteksi terak on-line selama peniupan oksigen memberikan panduan untuk operasi slagging, (ii) sistem analisis off-gas yang memperkirakan kandungan karbon dan suhu secara dinamis baja cair selama proses peniupan, dan (iii) model cerdas dengan kemampuan belajar mandiri dan adaptasi diri yang kuat. Gambar 6 menunjukkan pembentukan model cerdas.
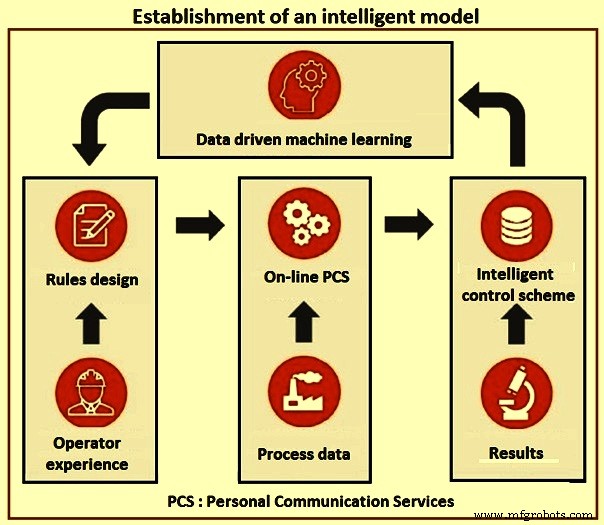
Gbr 6 Pembentukan model cerdas
Dengan penerapan teknik di atas, prediksi karbon titik akhir cerdas untuk pembuatan baja oksigen dasar dapat diterapkan secara otomatis dan efisien dengan komputer daripada operasi manual, dan akurasi prediksi kandungan karbon titik akhir sangat ditingkatkan. Dengan aplikasi praktis prediksi titik akhir cerdas di bengkel peleburan baja telah mengurangi rasio reblow dari 14% menjadi 1%, dan waktu ketuk-ke-ketukan telah berkurang dari 37 menit menjadi 29 menit, sehingga sangat meningkatkan efisiensi proses pembuatan baja oksigen dasar.
Tidak ada keraguan bahwa prediksi cerdas sangat meningkatkan akurasi prediksi kandungan karbon titik akhir. Baru-baru ini, semakin banyak teknik deteksi otomatis dikembangkan dan diterapkan pada kontrol karbon titik akhir untuk pembuatan baja oksigen dasar, seperti pengambilan sampel robotik dan sistem pengukuran suhu, sistem pengukuran komposisi nirkabel, dan sebagainya. Sementara itu, Industrial Internet of Things (IIoT) berkembang pesat seiring dengan teknologi komunikasi seluler generasi kelima (5G) dan analitik data besar, dan secara bertahap diterapkan pada manufaktur baja pintar. Oleh karena itu, prediksi karbon titik akhir yang cerdas untuk pembuatan baja oksigen dasar mendapatkan lebih banyak perhatian di masa depan.
Dari sudut pandang implementasi industri, model prediksi karbon titik akhir cerdas dengan akurasi tinggi dapat dipasang pada sistem proses yang ada, terus memprediksi kandungan karbon proses dan memberikan panduan bagi operator berdasarkan kejadian aktual dan kejadian yang direncanakan selama dasar proses pembuatan baja oksigen.
Sistem pakar
Sistem pakar adalah kelompok model proses yang komprehensif yang menggambarkan dan mengoptimalkan proses pembuatan baja. Sistem pakar memantau proses metalurgi dan termal, menghitung secara siklis kondisi sebenarnya dari rendaman baja dan terak. Ini memberikan analisis dan suhu rendaman baja dan terak setiap saat dan perhitungan model set-point selalu didasarkan pada situasi aktual.
Model proses sistem pakar mengoptimalkan dan mengontrol proses pembuatan baja selama seluruh perawatan di konverter. Sistem Level-2 membantu operator sesuai dengan perhitungan model berdasarkan skema produksi yang disimpan per grade baja. Sistem pakar terus menginformasikan personel pengoperasian tentang status keseluruhan panas (yaitu berat, suhu, dan analisis) selama perawatan.
Kelompok ekstensif model set-point dalam sistem pakar menentukan set-point sistem pakar, yang bertanggung jawab untuk menentukan pasokan bahan baku, volume gas, dan/atau energi yang dibutuhkan untuk langkah-langkah perlakuan yang berbeda. Beberapa model set-point dijelaskan di sini.
Perhitungan pengisian pertama sistem pakar dilakukan dengan mengambil skenario yang berbeda dari data input variabel (seperti skrap variabel dan logam panas variabel, skrap variabel dan logam panas tetap, atau skrap tetap dan logam panas variabel) dapat diterapkan. Selain itu optimasi biaya memo dapat digunakan. Sebagai keluaran model, campuran muatan yang optimal untuk mencapai target mengikuti tingkat baja yang direncanakan dari jadwal produksi disediakan.
Perhitungan muatan kedua sistem pakar dilakukan segera setelah data aktual terkait dengan logam panas dan skrap yang diisi, termasuk berat parsial dari jenis skrap yang berbeda telah diterima. Model perhitungan muatan kedua menghitung penambahan bejana dan volume oksigen yang diperlukan untuk mencapai analisis target dan suhu target baja pada akhir pukulan.
Perhitungan koreksi in-blow sistem pakar dilakukan dengan model sub-lance. Bergantung pada ketersediaan data (suhu, karbon), model online siklik mengambil alih nilai yang diukur dan menerapkan beberapa tindakan korektif karena fakta bahwa pengukuran sub-tombak dilakukan di dekat titik panas. Jumlah oksigen yang dibutuhkan yang tersisa, bahan pemanas, atau pendingin dan pembentuk terak tambahan dihitung.
Perhitungan koreksi tiupan ulang sistem pakar dapat dimulai jika sifat rendaman baja tertentu (misalnya suhu, kandungan karbon, atau kandungan fosfor) tidak berada dalam batas target yang ditentukan pada akhir peniupan. Analisis dan suhu rendaman baja aktual diambil dari pengukuran suhu atau dari sampel baja aktual. Jumlah oksigen yang dibutuhkan, bahan pemanas atau pendingin dan pembentuk terak tambahan untuk re-blow dihitung.
Model paduan sistem pakar menghitung biaya yang dioptimalkan bahan paduan dan deoksidasi yang diperlukan untuk ditambahkan ke sendok sadap. Analisis agen paduan dan kerugian spesifiknya diperhitungkan.
Model prediksi sistem pakar melakukan simulasi proses produksi secara lengkap dengan menggunakan model hasil supervisi dan set-point. Ini memberikan perkiraan kemajuan dan kondisi akhir panas. Ini juga memprediksi semua penambahan dan tindakan yang diperlukan dan berfungsi untuk mengoptimalkan proses produksi. Pada layar HMI tipikal untuk model prediksi, bagian layar yang berbeda menampilkan data target dan input, hasil model, analisis terhitung untuk baja, dan konsumsi terak dan spesifik.
Model pra-perhitungan sistem pakar mensimulasikan proses pembuatan baja lengkap sebelum / sesudah skrap dan logam panas dimasukkan ke dalam konverter. Model prediksi sistem pakar menentukan strategi peniupan dan pengadukan yang optimal, serta waktu dan porsi penambahan bejana yang tepat. The pre-calculation model is based on a pre-defined list of process steps (e.g. charging, main blowing, stirring, and tapping etc.) and target values from the standard operating practice (SOP) as defined by the process engineer.
The pre-calculation model consists of five different parts namely (i) calculation of hot metal and scrap input, (ii) calculation and distribution of heating and cooling agents, alloys, scraps and fluxes in order to reach the target weight, analysis, and basicity, (iii) calculation of blowing set-points in order to reach the target carbon content and temperature, (iv) calculation of ongoing reactions to predict the weight and analysis of steel, slag, and off-gas after each process step, and (v) information and warnings for the operator if target values for a process phase not reached.
Expert system supervision model which is an on-line model calculates cyclically the ongoing reactions in the steel bath and in the slag during the blowing process. This includes oxidation and reduction reactions, pick-up of oxygen, nitrogen and hydrogen, sulphur and phosphorus distribution between steel and slag and the post combustion from carbon di-oxide and hydrogen. In this way the effect of different blowing, stirring or material addition patterns as well as the dissolution of charged materials is taken into account for the course of the process.
Expert system dynamic control (a part of the expert system supervision model) is the dynamic blow end prediction for carbon based on actual off-gas data. From the actual off-gas data (such as off-gas flow, off-gas analysis (carbon mono-oxide, carbon di-oxide, oxygen, and nitrogen) as well as from actual process data expert system dynamic control predicts the carbon content at the end of the blowing process from the typical profile of the off-gas data close to blowing end. The result is a predicted carbon content at the end of the blowing process (typically for carbon contents below 0.3 %) and a blowing end request to reach the target carbon content at blowing end. In combination with the cyclic online model (expert system supervision model) a complete prediction of steel and slag (temperature, analysis and weight) can be made where the carbon content is taken from the expert system dynamic control and all other data are calculated by the expert system supervision model.
In the expert system, the carbon content calculation for the in-blow measurement is based on the raw data (i.e. the liquidus temperature Tliq) from the sub-lance measurement device instead of using the carbon content calculated by the measurement device. The in-blow carbon content is calculated using the equation Cin-bolw =a0 + a1xTliq + a2x square of Tliq. The tuning parameters a0, a1, a2 are maintained in the Level-2 database and are fitted by employing pairs of liquidus temperature and the carbon content from the in-blow sample.
The calculated carbon content from the in-blow measurement is taken over by the on-line model and thus corrects the carbon prediction model. To complete the existing automatic blow-stop functionality for basic oxygen converters based on dynamic off-gas measurement, this functionality is adopted for sub-lance systems as well. The automatic blow-stop functionality prolongs or shortens the final blowing phase in order to reach the temperature and carbon aims at end-of-blow.
The cyclic process model also known as saturation model considers the saturation concentrations of complex steelmaking slags by CaO (lime) and MgO (magnesia). Lime and dolomite dissolution is suspended when the corresponding saturation concentration is reached and continues when the slag composition allows further dissolution of slag-forming additions. Thus the process model keeps track of the liquid slag amount and analysis as well as the undissolved flux additions. The calculation of the equilibrium phosphorous distribution ratio is based on the optical basicity model. For determining the optical basicity only the composition of the liquid slag phase is employed, while the portion of undissolved fluxes is to be considered in the calculation of the mass transfer coefficients. Normally, the saturation model allows optimizing basicity (CaO / SiO2) and MgO and aims in order to avoid too much undissolved flux materials at the end-of-blow.
The expert system process model accounts for the thermal cracking of slag-forming additions which have been charged prior to hot metal charging. For these additions the portion of carbon di-oxide and water vapour is removed completely. This prevents to overestimate the cooling effect of pre-charge fluxes like limestone or raw dolomite and thereby improves the temperature calculation. Furthermore, the remaining slag in the converter from the previous heat is partially reduced by silicon after hot metal charging as per the reactions 2(FeO) + [Si] =2[Fe] + (SiO2], 2(Fe2O3) + 3[Si] =4[Fe] + 3(SiO2), 2(MnO) + [Si] =2[Mn] + (SiO2) and to a small extend also by carbon. In case of considerable amounts of remaining slag, the reduction of FeO, Fe2O3, and MnO affects the temperature profile.
Whereas the models are adjusted specifically to the special requirements of the different sub-systems, the principle of expert system of combining the features of prediction, supervision, and set-point models for perfect quality is applied throughout the steelmaking automation.