Sistem Pendingin Tungku Ledakan
Sistem Pendingin Tungku Ledakan
Mempertimbangkan investasi modal besar yang dibutuhkan untuk pelapisan ulang tanur tinggi (BF), upaya besar telah dilakukan di masa lalu untuk memperpanjang masa kampanye BF. Pengembangan proses pembuatan besi BF dan kemajuan ilmu material telah meningkatkan produktivitas, konsumsi bahan bakar, kualitas produk, dan masa pakai BF. Durasi kampanye BF hingga 1990-an terutama dipengaruhi oleh masa pakai poros bawah, yaitu area dengan beban termal tertinggi. Jika perpindahan panas, tegangan termal, dan masa pakai tungku semua parameter tersebut tidak dianalisis maka dapat menyebabkan kegagalan BF.
Pendinginan yang efisien diperlukan untuk menyeimbangkan beban termal dan keausan terkait pada lapisan dalam tungku, dan untuk melindungi cangkang dan elemen pendinginnya. Sistem pendingin BF memainkan peran kunci dalam masa pakai kampanye BF dan karenanya biaya pengoperasian. Elemen pendingin dengan sirkulasi air di dalamnya dipasang di antara cangkang BF dan lapisan tahan api di bagian atas tungku untuk melindungi komponen ini dari radiasi panas.
Fritz W Lurman, seorang pria BF terkenal pada waktu itu berpendapat pada tahun 1892 bahwa 'terlepas dari penggunaan yang disebut bahan tahan api, cara terbaik untuk menjaga dinding BF adalah dengan air pendingin'. Fungsi sistem pendingin BF adalah untuk mendinginkan cangkang tungku dan mencegah panas berlebih dan pembakaran selanjutnya. Sistem pendingin menghilangkan kelebihan panas yang dihasilkan di BF yang jika tidak dimuat di shell. Sistem pendingin sehingga mencegah peningkatan suhu shell dan lining. Ada beberapa metode yang ada untuk mendinginkan cangkang BF.
Sistem pendingin BF sedang dikembangkan sejak 1884. Sebelumnya (hingga 1920-an) pendinginan hanya diterapkan pada area perapian dan bosh. Pada 1930-an dan 1940-an, pendinginan juga diterapkan pada poros. Secara bersamaan, metode pendinginan eksternal seperti pancuran dan pendinginan jaket dari cangkang tungku dicoba. Metode ini mengandalkan ekstraksi panas melalui cangkang tungku ke media pendingin, menghasilkan tekanan termal yang tinggi selama perpindahan panas dan karenanya membahayakan integritas cangkang.
Di masa lalu, selain memiliki pendingin sendiri, bagian cangkang yang berdekatan dengan perapian dan bagian bawah tungku juga didinginkan di beberapa tungku di bagian luar dengan semprotan air. Juga, di masa lalu, kotak pendingin dengan ukuran, jumlah, dan desain yang berbeda digunakan untuk mentransfer panas tungku ke media pendingin bersama dengan pendinginan eksternal (pendingin semprot, cangkang ganda).
BF dengan tongkat pendingin besi cor beroperasi sejak pertengahan 1900-an. Stave adalah perangkat pendingin yang memiliki satu atau lebih saluran air internal, dan dipasang dalam jumlah di permukaan bagian dalam BF untuk melindungi cangkang bajanya dari gas suhu tinggi dan material beban cair di tungku, dan mempertahankan profil di dalamnya. tungku. Tiga sifat yang terutama dibutuhkan dari sebuah stave adalah (i) umur panjang dan keandalan, (ii) kemampuan pendinginan yang tepat, dan (iii) kemampuan isolasi termal.
Yang pertama adalah umur panjang dan keandalan. Karena tidak mungkin memperbaiki paranada dari luar BF karena strukturnya, pekerjaan penggantian yang ekstensif diperlukan bila paranada itu rusak. Stave yang rusak memiliki efek buruk yang serius pada operasi BF, menyebabkan penghentian hembusan yang lama dan penurunan suhu di dalam tungku karena kebocoran air, atau mengubah profil yang dapat mengakibatkan kegagalan operasional. Untuk alasan ini, umur panjang yang stabil diperlukan untuk tongkat.
Yang kedua adalah kemampuan pendinginan yang sesuai. Untuk melindungi cangkang dari gas bersuhu tinggi sekitar 1.200 derajat C dan bahan cair, diperlukan kemampuan pendinginan yang tepat dari paranada. Karena kemampuan pendinginan yang tinggi diperlukan untuk mendinginkan bagian tungku antara bosh dan bagian bawah poros yang terkena suhu tinggi, dalam beberapa kasus, tongkat tembaga digunakan untuk bagian ini.
Yang ketiga adalah kemampuan isolasi termal. Sebuah BF di mana oksida besi direduksi dan dilebur pada suhu tinggi diinginkan memiliki struktur insulasi panas agar tidak membuang energi panas. Di sisi lain, seperti dijelaskan di atas, paranada didinginkan untuk mempertahankan profil di dalam BF dan untuk melindungi cangkang. Oleh karena itu, ia menghilangkan energi panas dari gas dan material bersuhu tinggi. Menghilangkan panas dengan tongkat melibatkan konsumsi bahan bakar (kokas) yang setara, secara langsung menyebabkan peningkatan tingkat zat pereduksi (RAR). Peningkatan RAR pada gilirannya dapat menyebabkan peningkatan emisi karbon di-oksida dan menaikkan unit harga besi cair Untuk itu, stave diperlukan memiliki insulasi panas (heat removal restriksi) yang sesuai yaitu kemampuan untuk meminimalkan energi panas yang diambil dari dalam tungku, serta kemampuan pendinginan yang sesuai. Secara konvensional, batu bata dengan konduktivitas termal rendah disematkan di bagian depan tongkat besi cor untuk mendapatkan kemampuan pendinginan dan kemampuan insulasi panas. Sementara itu, paranada tembaga digunakan untuk membentuk lapisan insulasi panas dari bahan semi-cair yang terletak di depan tongkat dengan mendinginkan bahan tersebut dengan kemampuan pendinginan yang tinggi agar dapat menempel pada permukaan bagian dalam tongkat.
Pendingin stave pertama kali mulai dikembangkan sekitar pertengahan 1900-an. Pendinginan tiang besi cor pada awalnya merupakan penemuan bekas Uni Soviet dari mana ia melakukan perjalanan awalnya ke India dan Jepang. Pada 1970-an, tongkat pendingin besi cor telah diterima di seluruh dunia. Sejak diperkenalkannya pendingin stave besi cor, pekerjaan pengembangan pendinginan BF dipercepat dan saat ini berbagai macam pendingin seperti pendingin pelat, pendingin cerutu, dll. tersedia untuk pendinginan internal cangkang tungku agar sesuai dengan kondisi stres yang ekstrem. dalam BF kinerja tinggi modern yang besar. Keuntungan pendinginan stave dibandingkan pendinginan plat datar adalah efek pendinginan selimut dari staves dibandingkan dengan efek pendinginan titik ke titik dari plat datar dan pendingin cerutu. Ini memastikan kinerja pendinginan yang lebih seragam.
Untuk sebagian besar BF berkapasitas besar yang beroperasi saat ini, insinyur desain telah memutuskan untuk menggunakan stave untuk sistem pendingin karena mereka memungkinkan pendinginan tungku yang intensif dan, yang terpenting, seragam. Secara klasik, tongkat terbuat dari besi cor nodular, yang dilemparkan di sekitar pipa air pendingin. Mereka dipasang di seluruh cangkang tungku, dari pelat bawah hingga tenggorokan. Seringkali, bagaimanapun, paranada mengalami tekanan berat yang disebabkan oleh beban panas yang tinggi, terutama di daerah perut dan perut, yang dapat membatasi panjang kampanye tungku. Hal ini dapat menyebabkan hilangnya seluruh badan tongkat, dengan hanya pipa penghantar air yang tersisa. Diyakini bahwa baik konduktivitas termal dari bahan besi tuang dan perpindahan panas antara pipa dan badan cor dapat menjadi masalah. Bahkan dengan sistem pendingin yang paling terkenal, area cangkang bawah tetap menjadi titik lemah BF.
Para tongkat dibuat secara konvensional dari besi tuang, tetapi kelayakan pembuatannya dari tembaga, yang memiliki konduktivitas panas yang sangat baik, dikonfirmasi di Jerman sekitar pertengahan 1990-an, dan karenanya tongkat tembaga telah digunakan untuk beberapa BF sejak itu. Pada tahun 1993, tongkat tembaga diperkenalkan untuk pertama kalinya di Jerman di BF nomor 2 Thyssen Krupp di Schwelgern dan BF 'B' di Salzgitter. Memproduksi tongkat dari tembaga, baik menggunakan saluran air bor sebagai pengganti pipa, atau menyediakan saluran yang sesuai saat pengecoran lempengan tembaga, telah terbukti menjadi langkah penting dalam desain BF modern.
Teori bahwa konduktivitas termal yang tinggi dari tembaga menyebabkan peningkatan disipasi panas proses telah dibantah. Konduktivitas tembaga yang tinggi menghasilkan suhu permukaan yang rendah dan pembentukan lapisan tipis yang cepat yang mengurangi pelepasan panas dari tungku. Efek pendinginannya begitu kuat sehingga lapisan pelindung terbentuk dalam beberapa menit, bahkan di depan tongkat yang tidak terlindungi. Hasil terbaru menunjukkan bahwa tingkat panas yang dikeluarkan dari tungku bahkan lebih rendah daripada yang dialami dengan tongkat besi tuang.
Efek isolasi dari lapisan-lapisan tersebut menjaga kehilangan panas seminimal mungkin. Untuk alasan ini, ketika BF nomor 2 Stahlwerke Bremen dipasang kembali, tidak ada bahan tahan api permanen yang dipasang di depan paranada di atas tuyeres. Sebaliknya, hanya, lapisan pelindung tipis yang ditembakkan. Tongkat ini terbukti sangat sukses sehingga saat ini penggunaan tongkat tembaga di area dengan beban panas tinggi adalah teknologi tanur sembur yang canggih. Tumpukan yang lebih rendah tidak lagi dianggap sebagai faktor pembatas untuk masa kampanye BF. Sebaliknya, status perapian menentukan kehidupan kampanye BF. Pendingin stave tembaga saat ini melindungi kulit terluar dari proses panas yang dihasilkan dalam tungku bertekanan tinggi. Namun, tergantung di mana mereka diposisikan dalam BF, mereka mengalami tingkat beban termal yang berbeda.
Kunci keberhasilan pengoperasian sistem pendingin dalam BF dengan beban panas tinggi adalah pembentukan tengkorak pada permukaan panas elemen pendingin. Tengkorak ini terdiri dari uap kental, terak padat dan logam yang menempel pada permukaan elemen pendingin dengan memercikkan, menetes, dan membeku di atasnya. Ketebalannya dapat bervariasi hingga 20 mm. Stabilitas tengkorak terutama tergantung pada kapasitas pendinginan dan kemampuan kepatuhan mekanis dari elemen pendingin yang melekat padanya. Tingkat keparahan aliran gas di dinding juga mempengaruhi retensi tengkorak. Tengkorak adalah isolator alami jika kandungan logamnya rendah. Selama periode beban panas yang ekstrem (yaitu pancaran gas suhu tinggi atau gangguan proses), tengkorak dapat mengelupas, lalu menumpuk lagi setelahnya. Jatuh dan menumpuknya tengkorak menyebabkan fluktuasi beban panas yang signifikan pada dinding tungku dengan beban puncak berkisar antara 300.000 watt per meter persegi (W/sq m) hingga 500.000 W/sq m.
Oleh karena itu, desain pelapis dan pendingin biasanya harus mampu menangani beban panas tersebut untuk menghindari kegagalan dini. Penyelidikan terperinci telah mengungkapkan bahwa semakin tinggi efisiensi pendinginan elemen pendingin, semakin stabil tengkorak dan semakin lama melekat pada elemen pendingin dan mempertahankan sifat isolasi dan pelindungnya. Hasilnya adalah sistem pendinginan yang sangat efisien biasanya menghasilkan kehilangan panas keseluruhan yang lebih rendah dari tungku.
Sementara sebagian besar BF adalah tipe berdiri bebas tanpa dukungan pada cangkang tungku, beberapa desain tungku menggabungkan mantel di mana tungku didukung dari permukaan tanah baik oleh baja atau kolom beton. Penggunaan mantel biasanya menghilangkan area perut. Mantel merupakan bagian integral dari desain tungku tungku ini dan harus dilindungi dari panas berlebih di bawah kondisi yang sama seperti yang dialami di area perut BF yang berdiri bebas. Pendinginan lapisan tungku di daerah mantel menggunakan pelat tembaga sulit karena akses terbatas untuk mengubah dan panjang pelat pendingin yang diperlukan untuk digunakan. Penggunaan tongkat di area tersebut memiliki keuntungan memberikan cakupan pendinginan yang lengkap dari mantel. Gambar 1 menunjukkan pengaturan pendinginan stave di mantel serta berbagai jenis pengaturan pendinginan di BF.
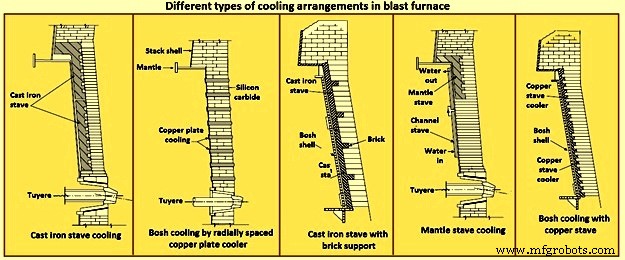
Gbr 1 Berbagai jenis pengaturan pendinginan dalam tanur tinggi
BF modern dapat memiliki tingkat produksi lebih tinggi dari 3 ton logam panas per meter kubik volume kerja per hari. Tingkat produktivitas di BF ini dicapai dengan menggunakan bahan beban yang ditingkatkan, teknik distribusi beban, kontrol proses, suhu ledakan panas yang tinggi, pengayaan oksigen dan injeksi bahan bakar tambahan. Namun, praktik produktivitas tinggi ini menghasilkan beban panas yang tinggi dan fluktuasi beban panas yang bekerja pada dinding BF. Meskipun zona spesifik dan besarnya beban panas puncak dapat sangat bervariasi antar tungku, bagian perut dan cerobong bawah biasanya menghadapi fluktuasi panas tertinggi seperti yang ditunjukkan pada Gambar 2.
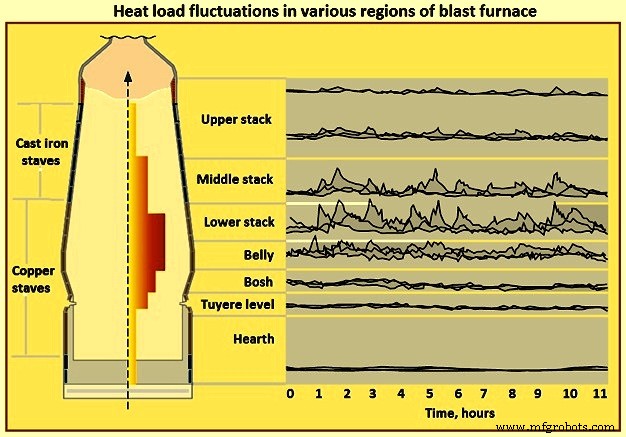
Gbr 2 Fluktuasi beban panas di berbagai wilayah tanur sembur
Daerah di mana beban panas tertinggi dialami terkait erat dengan posisi dan bentuk zona kohesif dan pola pengisian spesifik tungku. Penyebab utama fluktuasi panas yang tinggi adalah aliran gas berkecepatan tinggi yang tidak teratur yang mengalir ke dinding tungku melalui celah kokas pada beban. Temperatur yang tinggi dan berfluktuasi adalah beban utama yang harus dihadapi oleh elemen pendingin di BF. Komposisi dan kualitas beban telah diamati sangat mempengaruhi beban panas dan fluktuasi panas. Beban BF dengan sinter lebih dari 70 % dapat menghasilkan beban puncak 100.000 W/sq m sampai 200.000 W/sq m, sedangkan beban dengan persentase pellet atau lump yang tinggi dapat menghasilkan beban panas puncak lebih dari 400.000 W/sq m. Tergantung pada beban panas yang diharapkan, elemen pendingin yang berbeda harus diterapkan. Tab 1 memberikan ikhtisar tentang desain pendinginan dan refraktori yang berbeda dengan kemampuan beban panas puncak maksimumnya.
Tab 1 Ikhtisar desain pendinginan dan refraktori yang berbeda dengan kemampuan beban panas puncak maksimumnya |
Desain | Beban panas puncak dalam W/m² |
Pendingin pelat dengan refraktori alumina | 50.000 |
Tongkat besi cor, generasi pertama | 100.000 |
Tongkat besi cor yang lebih tebal dengan beberapa sirkuit air pendingin | 200.000 |
Pendingin pelat, jarak yang lebih dekat (300 mm) dengan refraktori khusus | 400.000 |
Tongkat tembaga performa tinggi | 500.000 |
Perlu ditekankan di sini bahwa beban termal puncak ini adalah faktor penentu utama untuk kelangsungan jangka panjang lapisan tungku atau elemen pendingin.
Berbagai elemen pendingin yang dikembangkan untuk sistem pendingin BF adalah (i) tiang besi cor dari generasi yang berbeda, (ii) pendingin pelat tembaga dengan jarak rapat, (iii) pendingin cerutu, dan (iv) tiang pendingin tembaga. Elemen pendingin ini dijelaskan di bawah ini .
Pendingin tiang besi cor
Untuk pendingin stave besi cor, awalnya digunakan besi abu-abu lamellar perlitik paduan tetapi hari ini telah diganti dengan besi ulet atau besi nodular, karena kurang rentan terhadap keretakan pada suhu lebih tinggi dari 760 derajat C. Baru-baru ini tongkat baja cor di tempat tongkat besi cor juga telah berhasil diuji. Efek pendinginan tongkat besi tuang ditentukan oleh ukuran dan bentuk tabung air pendingin di dalam pendingin tongkat. Dimensi khas dari tongkat besi cor terdiri dari panjang 1,8 m hingga 2,4 m, lebar 0,8 m hingga 1,1 m dan ketebalan 0,25 m hingga 0,6 m. Berbagai jenis tongkat pendingin besi cor ditunjukkan pada Gambar 3. Pendingin tipe C jauh lebih tipis dan dirancang untuk menghemat ruang di dalam tungku untuk meningkatkan volume kerjanya.
Gbr 3 Berbagai jenis tongkat besi tuang
Sejak memperoleh teknologi tongkat besi tuang dari bekas Uni Soviet pada tahun 1969, Jepang telah melakukan berbagai perbaikan untuk meningkatkan daya tahan tongkat tersebut. Ini termasuk penyempitan jarak pipa dan pemasangan pipa pendingin sudut dan pipa serpentine belakang. Tongkat generasi keempat dicirikan oleh fakta bahwa mereka memiliki dua bidang pendingin, empat tabung vertikal di bidang sisi panas dan satu tabung serpentin di bidang sisi dingin. Para staf dilengkapi dengan hidung yang didinginkan dan / atau braket untuk mendukung bahan tahan api. Selanjutnya sudut-sudut tongkat didinginkan secara intensif. Bahan tahan api dilemparkan ke dalam lubang pendukung khusus di tongkat. Perbaikan yang dilakukan dari generasi pertama hingga generasi keempat dari besi cor stave cooler ditunjukkan pada Gambar 4.
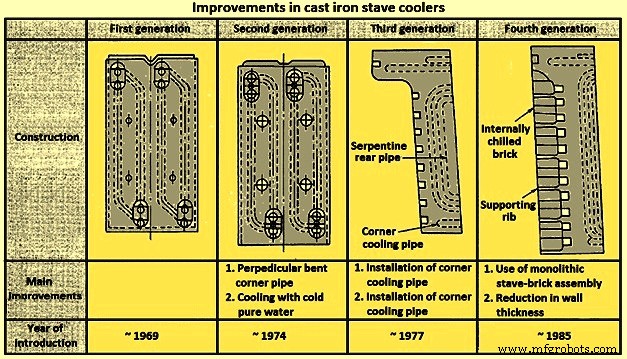
Gbr 4 Peningkatan pada pendingin stave besi cor
Tongkat besi cor di area bosh dan tumpukan BF memiliki harapan hidup rata-rata sekitar 8 tahun hingga 10 tahun. Stave besi cor biasanya gagal karena hilangnya material besi cor dan terbukanya koil pipa internal. Besi cor retak saat digunakan karena beban panas yang tinggi yang terkena. Celah acak antara tabung pendingin dan besi tuang mengurangi jumlah panas yang dikeluarkan. Juga perbedaan antara koefisien muai panas bahan tabung dan pendingin yang tepat dapat menyebabkan besi terpisah dari tabung dan merusak pendingin. Penggunaan pendingin besi tuang di mana tabung lebih dekat ke besi tuang memperumit desain cangkang, namun tidak serta merta meningkatkan masa pakai sistem pendingin.
Mekanisme kegagalan tongkat besi cor di bawah beban panas berfluktuasi tinggi adalah karena konduktivitas termal yang rendah (sekitar 45 W/m.K) besi cor. Stave besi cor memiliki efisiensi pendinginan yang lebih rendah dibandingkan dengan stave tembaga karena konduktivitas besi cor yang relatif rendah dan adanya lapisan isolasi. Lapisan ini menghasilkan penghalang termal antara tabung berpendingin air dan badan tiang besi cor yang mengurangi perpindahan panas. Perpindahan panas yang tidak efisien menghasilkan suhu muka panas yang jauh lebih tinggi dari tongkat besi cor (lebih dari 700 derajat C) dan deformasi termal berikutnya dari tongkat besi cor. Bodi besi cor juga mengalami transformasi volume fase pada suhu tinggi, yang mengakibatkan retak lelah, hilangnya material bodi stave, dan paparan pipa pendingin baja langsung ke panas tungku.
Pendingin pelat datar tembaga
Pendingin pelat datar tembaga, seperti namanya, adalah pelat datar yang disusun secara horizontal ke dalam cangkang tungku. Pendingin pelat datar ini telah digunakan hampir di semua BF Eropa. Pendingin ini dilas atau dicor dalam tembaga elektrolitik. Dengan yang terakhir, maka tidak ada masalah pada lapisan las dan ada keseragaman sifat material yang lebih besar di atas elemen pendingin lengkap. Pendingin jenis ini biasanya digunakan di area mulai dari bosh hingga dan termasuk tumpukan bawah. Biasanya dirancang untuk mempertahankan kecepatan air yang tinggi di seluruh pendingin, sehingga memberikan koefisien perpindahan panas yang merata dan tinggi. Pendingin pelat datar tembaga tipikal ditunjukkan pada Gambar 5.
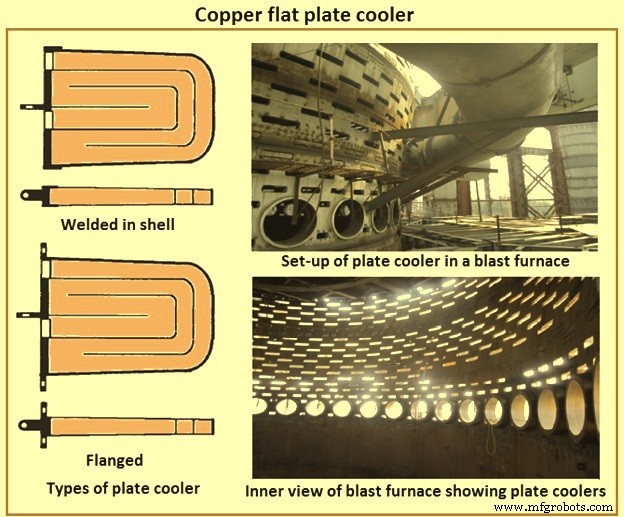
Gbr. 5 Pendingin pelat datar tembaga
Ukuran pelat normal pendingin pelat datar tembaga terdiri dari panjang 0,5 m hingga 1,0 m, lebar 0,4 m hingga 0,8 m, dan tinggi sekitar 75 mm. Jarak vertikal pendingin adalah 0,3 m hingga 0,6 m. Di zona dengan beban panas yang tinggi, terutama di bagian atas dan bawah tumpukan, jarak sering dikurangi menjadi 0,25 m. Pendingin datar tembaga memiliki keseragaman sifat material yang lebih besar dibandingkan elemen pendingin lengkap. Di daerah BF yang mengalami kerusakan mekanis, sisi depan elemen pendingin biasanya diperkuat dengan bahan khusus. Pendingin ini sebagian besar dilas ke cangkang BF untuk memastikan penyegelan kedap gas. Pendingin pelat datar tembaga biasanya memiliki beberapa saluran dengan satu atau dua ruang independen. Kehilangan minimum tekanan air dipastikan baik di perpipaan dan elemen itu sendiri.
Salah satu desain pendingin pelat datar capper memiliki enam lintasan dengan ruang tunggal. Pendingin ini dirancang untuk mempertahankan kecepatan air yang tinggi di seluruh pendingin, sehingga memiliki koefisien perpindahan panas yang merata dan tinggi.
Kegagalan pendingin datar tembaga dikaitkan dengan empat mekanisme kegagalan. Mereka adalah (i) defleksi, (ii) kegagalan las pipa, (iii) kegagalan las sumbat, dan (iv) abrasi muka. Perbandingan pendingin pelat tembaga dengan pendingin stave besi cor diberikan di Tab 2.
Tab 2 Perbandingan antara sistem pendingin |
Deskripsi | Satuan | Pendingin pelat tembaga | Pendingin besi cor |
Rata-rata | Maksimum | Rata-rata | Maksimum |
Luas permukaan spesifik elemen pendingin per cangkang meter persegi | m persegi / m persegi | 1-2 | 2,5 | 0,8-1 | 1-2 |
Aliran air pendingin spesifik per meter persegi (m persegi) shell | cum / jam | 5-10 | | 3-5 | |
Kecepatan air pendingin biasa | m / detik | 0,5-1 | 2-2,5 | 1-1.2 | 2,5-3 |
Pendingin cerutu
Pendingin cerutu digunakan untuk pendinginan yang lebih intensif atau dengan jarak yang tidak memadai dari pendingin pelat datar. Ini juga dikenal sebagai jaket tembaga. Pendingin cerutu digunakan di area terbuka di antara pendingin pelat saat pendinginan yang lebih intensif diperlukan atau jarak yang ada pada pendingin pelat datar tidak mencukupi. Ini juga kadang-kadang digunakan untuk perbaikan sistem pendingin yang ada selama kampanye. Pendingin cerutu biasanya dikerjakan dari batang tembaga padat untuk membentuk inti silinder dan saluran tunggal ditambahkan dengan mengebor dan menyumbat.
Pendingin cerutu biasanya dimasukkan pada garis tengah antara pendingin pelat datar yang berdekatan pada bidang horizontal dan vertikal. Untuk keperluan pemasangan pendingin cerutu biasanya lubang silinder dibor melalui cangkang tungku dan lapisan tahan api yang ada dengan bor inti. Penggunaan pendingin cerutu di area bosh, perut, dan tumpukan bawah meningkatkan area sistem pendingin. Karena area BF ini memiliki suhu dan fluktuasi suhu tertinggi, penggunaan pendingin cerutu dapat meningkatkan ketahanan lapisan tahan api terhadap mekanisme serangan kimia dan mekanis. Namun karena penggunaan pendingin cerutu mengakibatkan peningkatan bukaan di tungku, kekuatan cangkang harus diperiksa sebelum digunakan. Pendingin cerutu khas dan posisinya di antara pelat pendingin seperti yang terlihat dari luar cangkang BF ditunjukkan pada Gambar 4.
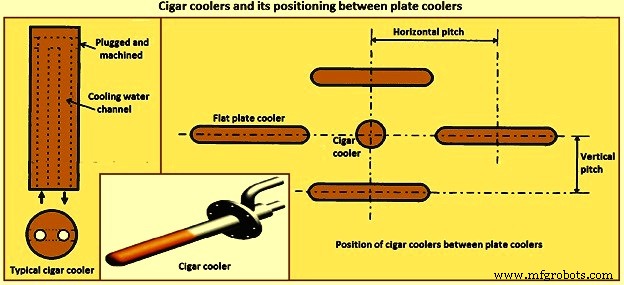
Gbr 6 Pendingin cerutu dan posisinya di antara pendingin pelat
Tongkat tembaga
Mengingat besarnya investasi modal yang dibutuhkan untuk pelapisan ulang BF, upaya besar telah dilakukan untuk memperpanjang masa kampanye BF. Teknologi tongkat tembaga adalah salah satu produk dari upaya tersebut.
Stave besi cor, karena karakteristik materialnya, menyebabkan kerusakan material di bagian bawah tanur sembur, yang terkena beban panas tinggi. Hal ini membuat sulit untuk mencapai masa pakai tungku yang stabil selama 20 tahun menggunakan stave besi cor. Sebagai sarana pendinginan alternatif untuk paranada besi cor mengingat beban panas yang tinggi, paranada tembaga gulung dikembangkan. Jenis tongkat ini terbuat dari pelat tembaga yang digulung di mana lubang dibor dan pasokan air dan pipa pembuangan dilas untuk membentuk saluran air. Penggunaan tongkat tembaga gulung dimulai di Jerman pada pertengahan 1990-an, dan telah menyebar ke BF di beberapa negara.
Tongkat tembaga lain yang dikembangkan hingga saat ini termasuk tongkat tembaga cor dengan saluran air yang dibentuk menggunakan inti dalam proses pengecoran, dan tongkat tembaga pipa monel cor dengan saluran air yang dibentuk menggunakan pipa monel yang ditekuk menjadi bentuk saluran dan dicor.
Tongkat tembaga pertama kali digunakan di BF pada akhir 1970-an sebagai elemen pendingin dinding beban panas tinggi terbaik. Ketika produktivitas BF meningkat dan tujuan hidup kampanye yang diinginkan meningkat menjadi 20 tahun, menjadi jelas bahwa tongkat tembaga memiliki potensi terbaik untuk memenuhi atau melampaui tuntutan ini. Meskipun penggunaan tongkat tembaga menjadi lazim pada pertengahan 1990-an, sebagian besar instalasi pada atau setelah tahun 2000. Pengembangan tongkat tembaga dilakukan baik di Jepang dan Jerman untuk digunakan di wilayah bosh, perut, dan bawah. tumpukan untuk mengatasi beban panas yang tinggi dan fluktuasi suhu yang besar. Sementara Jepang telah menggunakan tongkat tembaga cor, tongkat tembaga Jerman adalah pelat tembaga gulung yang memiliki toleransi luar yang dekat dan dengan pengeboran yang dilakukan untuk saluran pendinginan. Tongkat tembaga yang dibor dan dipasang biasanya dirancang untuk empat pipa air dalam garis lurus di bagian atas dan empat pipa air dalam garis lurus di bagian bawah. Bahan untuk gulungan pipa internal termasuk monel, tembaga, atau baja. Tidak seperti tongkat besi cor, tongkat tembaga dimaksudkan untuk direkatkan ke pipa pendingin.
Saluran air dari tongkat tembaga sebagian besar dibentuk dengan mengebor lubang ke pelat tembaga yang digulung dan mengelas pipa air di ujung lubang, dan kadang-kadang dibentuk dengan casting menggunakan inti pasir sekali pakai, namun, pekerjaan pengelasan tembaga sangat diperlukan. dalam salah satu kasus. Sementara tongkat tembaga konvensional terbukti sangat baik dalam kapasitas pendinginan, pembuatannya memerlukan beberapa langkah kerja, dan karenanya, harganya mahal.
Saat ini, jenis tongkat tembaga yang paling populer adalah tongkat tembaga yang digulung, proses pembuatannya melibatkan pengeboran lubang pada pelat tembaga. Ujung saluran air dari paranada ini dilas dengan steker. Stave tembaga pipa baja cor, yang telah dikembangkan, dibuat dengan memasukkan pipa baja bengkok ke dalam tembaga, proses pembuatan yang sama sekali berbeda dari stave tembaga gulung konvensional. Metode manufaktur yang unik ini telah memungkinkan pencapaian efisiensi energi yang tinggi dan masa pakai BF yang panjang, yang tidak dapat dicapai dengan menggunakan stave tembaga yang digulung.
Batang tembaga yang digulung terkadang memiliki tiga masalah yaitu (i) deformasi, (ii) retak las karena kelelahan termal, dan (iii) keausan. Masalah pertama adalah deformasi. Batang tembaga yang digulung melengkung karena perbedaan ekspansi termal antara permukaan bagian dalam tongkat, yang terkena gas suhu tinggi, dan permukaan luar tongkat yang didinginkan. Mereka berubah bentuk secara serius jika tongkat terlalu panjang atau ketika posisi baut pemasangan tidak sesuai. Deformasi seperti itu dapat menyebabkan keausan pada bagian yang menonjol dan kerusakan pada lasan karena gas suhu tinggi yang mengalir ke sambungan stave dan permukaan belakang. Masalah kedua adalah retak las. Karena kelelahan termal, ini terjadi karena lasan tongkat tembaga yang digulung mengalami tekanan termal berulang. Karena fluktuasi suhu, tongkat tembaga yang digulung menyebabkan keretakan dan patah. Masalah ketiga adalah keausan. Bijih besi, sinter, dan kokas memiliki kekerasan yang lebih tinggi daripada tembaga. Bahan-bahan ini mengikis tongkat tembaga ketika mereka menyentuh permukaan tongkat dan turun. Secara umum, tingkat keausan stave tembaga tergantung pada gaya kontak dan kecepatan turun material yang bersentuhan dengan permukaan stave, kekerasan tembaga dan material, dan bentuk material.
Pengembangan paranada tembaga cor telah mempertimbangkan aspek-aspek berikut. Sesuai dengan aspek pertama, untuk pencegahan deformasi, desain yang tepat dari panjang stave dan titik-titik yang dibatasi baut adalah penting. Aspek pertama adalah bahwa penggunaan stave tembaga pipa baja cor dengan desainnya sendiri bermanfaat untuk mengurangi risiko deformasi secara efektif. Gambar 7 menunjukkan titik-titik terbatas dari tongkat tembaga yang digulung dan tongkat tembaga pipa baja yang dicor. Sebuah tongkat tembaga yang digulung dibatasi ke cangkang dengan memasang baut dan pin. Untuk mencegah las di dasar pipa naik dari kerusakan akibat tekanan, pipa naik dihubungkan ke shell dengan sambungan ekspansi. Karena struktur ini, ujung atas dan bawah paranada dapat dipindahkan secara bebas, menyebabkan paranada mudah berubah bentuk. Beban termal besar yang berulang kali diterapkan pada stave tembaga selama fluktuasi dalam operasi BF dll., menyebabkan regangan plastik terakumulasi secara bertahap, dan menghasilkan deformasi yang besar. Ada kasus di mana deformasi di ujung atas telah mencapai 50 mm atau lebih dan lasan telah putus, dalam kondisi tongkat yang terlalu panjang, posisi baut yang tidak sesuai, atau beban panas tinggi yang melebihi kondisi desain.
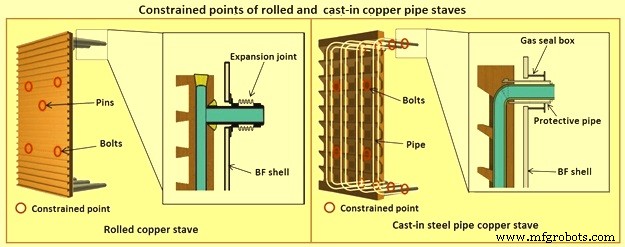
Gbr 7 Titik-titik terkendala dari gulungan dan tongkat tembaga pipa tuang
Keandalan yang tinggi dan biaya produksi yang rendah diwujudkan dalam kasus stave tembaga pipa baja cor dengan teknologi casting untuk menanamkan pipa baja dalam casting tembaga yang diterapkan pada produksi stave tembaga tipe baru. Teknologi pengecoran ini telah dikembangkan berdasarkan pembuatan tongkat besi tuang. Stave tembaga tipe baru yang memiliki pipa baja tertanam memiliki keunggulan (i) kapasitas pendinginan yang tinggi karena pengecoran tembaga kemurnian tinggi memastikan kapasitas pendinginan setinggi stave tembaga konvensional, (ii) keandalan yang tinggi sejak embedding pipa baja dalam pengecoran tembaga menghilangkan pengelasan tembaga dalam pembentukan saluran air dan kemungkinan kebocoran air, (iii) fleksibilitas yang luas dalam desain karena pembuatan dengan pengecoran dan penyematan pipa baja memungkinkan fleksibilitas yang jauh lebih besar pada stave disain dibandingkan dengan tongkat tembaga konvensional dalam hal bentuk dan susunan saluran air, dan (iv) biaya rendah.
Stave tembaga pipa baja cor memiliki fitur tahan deformasi berikut. Seperti yang ditunjukkan pada Gambar 7, untuk stave tembaga pipa baja cor memiliki, kotak segel gas selain baut yang digunakan untuk memperbaiki pipa pelindung di ujung stave. Ini menerapkan batasan perpindahan ke ujung atas dan bawah tongkat. Selain itu, karena pipa pelindung dicor di badan tongkat tembaga, tidak ada lasan dengan risiko kerusakan yang digunakan.
Selanjutnya, pipa baja cor tembaga stave menggunakan pipa baja, yang lebih kaku dari tembaga dan berfungsi sebagai kerangka kerja. Penggunaan pipa baja memberikan struktur yang lebih tahan deformasi daripada tongkat tembaga konvensional. Permukaan bagian dalam tongkat tembaga pipa baja cor dibuat bergelombang. Karena tongkat tembaga yang digulung memiliki bentuk penampang persegi panjang, suhu meningkat di lokasi di permukaan bagian dalam tongkat yang jauh dari saluran air. In contrast, the cast-in steel pipe copper stave uses a bumpy surface to render the distance between the stave inner surface and each water channel virtually constant around the water channel. This allows the stave inner surface to be uniformly cooled. Such uniform cooling in turn reduces the temperature difference between the stave inner and outer surfaces, and suppresses thermal stresses and deformation.
In addition, under large thermal load, compression plastic strain is caused on the stave inner surface of a rolled copper stave by the temperature difference between the stave inner and outer surfaces, which can lead to stave deformation. In contrast, the inner surface of the cast-in steel pipe copper stave is isolated at each bump, thereby making compression stresses less likely to act on the stave and suppressing plastic strain. Hence, the bumpy surface of the cast-in steel pipe copper stave reduces stresses and strains which act on the stave, and suppresses deformation. Also, since the cast-in steel pipe copper stave forms water channels using steel pipes, plug welding or pipe connection welding, which are indispensable for making rolled copper staves, are not necessary. By avoiding the use of welding, which is structurally weak parts, the risk for breakage of welds can be eliminated.
Copper staves prevent wear by the scabs formed by using its high cooling ability, thereby avoiding direct contact with the descending material in front of the stave. However, such accretion frequently falls off due to the fluctuations during furnace operations. Without accretion, the wear of a copper stave depends on the contact force and descending speed of the material in front of the stave, hardness of copper and the material, and shape of the material. Given this, counter-measures against wear feasible for a stave include reducing the contact force and descending speed of the material when there is no accretion, in addition to stably retaining accretion, as well as not allowing the hardness of copper to be reduced. While grooves for rolled copper staves is formed by machining, the cast-in steel pipe copper stave forms ribs by integrally casting, allowing for forming as-desired rib shapes. Based on this feature, cast-in copper stave normally has an upward rib structure with wear resistance. The hardness of copper depends on the cooling ability.
If there is no accretion inside-furnace surface of a rolled copper stave, material once entered between ribs hardly moves because the ribs are small. Hence, material in front of the stave descends without being influenced by the ribs. In contrast, since the ribs of the cast-in steel pipe copper stave face upward and are large, material which has entered between the ribs is discharged back into the furnace, creating a flow (load transfer). At this time, the material is discharged upward. This upward flow pushes the material in front of the stave back to the furnace, causing the contact force and descending speed of the material to be reduced at the rib tips.
In addition to the technical advantages in extending life and saving energy, the cast-in steel pipe copper stave has also the characteristic of the high design flexibility. When a cast iron stave or cooling plate which a BF uses is broken and something needs to be done in order to extend the life, the replacement with a copper stave using the existing shell opening may be needed. In the case of rolled copper staves, since water channels are formed by drilling, the water channel layout is restricted, making it difficult to freely form water channels in a manner tailored to the existing shell opening. In contrast, water channels of the cast-in steel pipe copper stave, which are formed using bent steel pipes, allow for flexible layout adopting steel pipes for the existing opening of the shell. Fig 8 shows high flexibility of cooling channel layout in cast-in steel pipe copper stave.
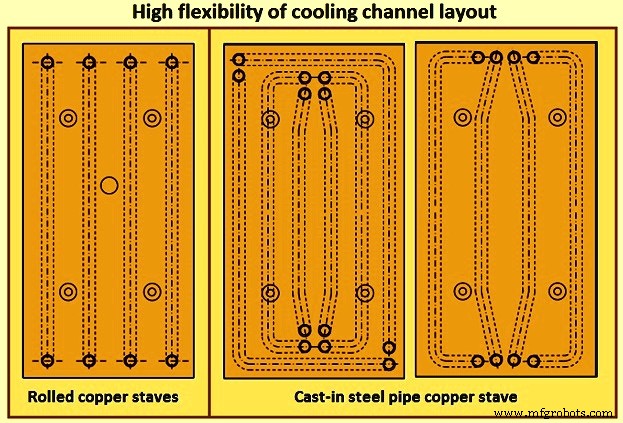
Fig 8 High flexibility of cooling channel layout
Layouts of cooling systems
Water cooling systems are normally designed to operate in a closed loop rather than the conventional open systems. This allows the pipe work to be chemically cleaned, and by controlling water chemistry throughout the campaign, this clean surface can be maintained, thus ensuring maximum heat transfer. The development of the sealing of the cooling tubes to the shell is towards the use of ever, thinner, ’softer’ metallic expansion joints. For both systems, i.e. flat plate coolers or staves, there is an increasing use of rubber bend and hoses.
Independent series are typical for water distribution in flat coolers. With stave coolers, it is normal to provide a number of independent flow and return headers in accordance with the number of tubes. This ensures that in the case of failure one feed system, the remaining stave tubes receive sufficient cooling. Nose and corner tubes are connected to the additional water circuits.
The rise in the BF productivity has been accompanied by a greater demand for efficient cooling systems. High-performance cooling systems are needed to ensure that the operational process runs smoothly even when under such stress. Reliable and effective cooling system solution is needed in the high loaded zones of the BF. There are three types of cooling circuits which are normally used for the BF cooling systems. These are (i) closed loop cooling circuits, (ii) combined closed loop cooling circuits, and (ii) semi-closed or open loop cooling circuits or evaporation cooling circuit
Closed loop cooling circuits – These cooling system circuits are normally designed with two or three nitrogen pressurized closed loop water circuits with forced recirculation. The advantages of such a system, as compared to an open loop cooling circuit are (i) circuit can be operated with treated, softened water, (ii) no corrosion, fouling, and clogging of pipes and cooling elements, (iii) low cost for chemical additives, (iv) low water consumption, (v) no contact with oxygen of ambient air, (vi) very sensitive leakage detection is possible, (vii) increase of the evaporation temperature of the cooling water due to operation under adjustable nitrogen pressure (e.g. pressure – 8 bar, evaporation temperature – 170 deg C), (ix) low electrical power consumption, since only the pressure drop is to be covered by the pumps and the differential height is not to be considered, (x) easy flow adjustment and control for the different cooling elements, (xi) low maintenance costs, and (xii) longer life time of circuit equipment and cooling elements resulting in high availability of and hence high productivity.
Combined closed loop cooling circuits – These circuits constitute an economic, but still efficient, reliable, and safe solution. The cooling water is used to cool serially different blocks of cooling elements, still respecting the operation requirements of the individual cooling elements. The total flow rate is considerably reduced while temperature difference of the cooling water is still in an acceptable range and the cooling tower operates efficiently.
Semi-closed or open loop cooling circuits or evaporation cooling circuit – These can also be used as an option in accordance with site conditions. This solution is mainly good for minimum cost upgrades at the existing BFs.