Regenerasi Asam untuk Minuman Keras Acar Hidroklorik Bekas
Regenerasi Asam untuk Minuman Acar Hidroklorik Bekas
Pengawetan baja adalah salah satu langkah penting dalam industri manufaktur baja. Ini adalah bagian dari proses finishing dalam produksi produk baja tertentu di mana oksida dan kerak dihilangkan dari permukaan baja strip, kawat baja, dan beberapa bentuk baja lainnya, dengan pelarutan dalam asam. Selama proses tersebut, asam bereaksi untuk melarutkan oksida permukaan, sehingga ion logam terakumulasi dalam larutan pengawet.
Pengawetan adalah proses yang terdiri dari penghilangan kerak (oksida permukaan) dan kotoran lainnya dari baja secara kimia dengan perendaman dalam larutan asam berair. Selama proses pengawetan, asam bereaksi dengan kerak serta baja dasar untuk menghasilkan garam logam terlarut. Untuk tujuan ini, solusi pengawetan digunakan, terutama terdiri dari asam mineral. Mandi asam pengawet digunakan untuk menghilangkan, memodifikasi, pasif atau membersihkan permukaan baja dengan cara yang ditentukan. Larutan asam klorida (HCl) atau asam sulfat (H2SO4) biasanya digunakan untuk pengawetan produk baja karbon. Konsentrasi asam ini menurun selama proses pengawetan, sedangkan persentase produk pengawetan dalam bak pengawetan meningkat.
Pengawetan baja karbon dengan demikian adalah proses mengkonsumsi asam sulfat segar atau asam klorida dan memberikan sulfat besi atau besi klorida. Keduanya, pengadaan asam segar serta pembuangan sulfat dan klorida, biasanya disertai dengan biaya tinggi dan logistik yang kompleks.
Untuk pengawetan asam dari baja karbon dan produk baja, asam sulfat terutama digunakan, hingga pertengahan abad kesembilan belas. Mulai tahun 1964, beberapa fasilitas pengawetan baja telah beralih dari pengawetan asam sulfat ke pengawetan asam klorida. Saat ini, asam klorida adalah asam yang paling umum digunakan untuk pengawetan baja karbon.
Bak pengawetan yang baru disiapkan biasanya mengandung 12% sampai 16% asam klorida, meskipun konsentrasi ini secara bertahap berkurang seiring dengan penggunaan asam. Mandi pengawetan dianggap habis ketika konsentrasi asam menurun antara 75 % dan 85 % dari nilai awalnya, dan konsentrasi logam dalam larutan meningkat menjadi 150 gram per liter menjadi 250 gram per liter.
Asam klorida sekarang lebih disukai daripada asam sulfat karena (i) memberikan kualitas permukaan yang optimal dan pengawetan yang cepat, (ii) secara konsisten menghasilkan permukaan abu-abu muda yang seragam pada baja karbon, (iii) memiliki kemampuan untuk melarutkan semua senyawa lapisan kerak, (iv) kemungkinan over-pickling jauh lebih kecil, (v) konsentrasi besi bisa setinggi 13%, (vi) pembilasan difasilitasi karena kelarutan besi klorida yang tinggi, (vii) asam lebih aman untuk menangani jika dibandingkan dengan asam sulfat, (viii) pengawetan dilakukan pada suhu operasi yang lebih rendah, (ix) memiliki keuntungan dari biaya yang lebih rendah, (x) pengawetan asam klorida menawarkan pengawetan yang lebih cepat dan lebih bersih, konsumsi asam yang lebih rendah, dan pemanfaatan yang lebih tinggi asam, (xi) konsumsi uap yang lebih sedikit dan pengurangan jumlah produksi cairan acar bekas, dan (xii) keserbagunaan yang lebih besar dan kualitas produk yang lebih seragam daripada pengawetan asam sulfat.
Produk sampingan utama dari proses pengawetan baja adalah pembentukan cairan pengawet bekas atau asam bekas. Cairan pengawet bekas dapat dikelola dengan beberapa cara yaitu (i) mengangkutnya ke organisasi pemrosesan yang memulihkan dan mengubah besi klorida menjadi besi klorida dan menjual produk sebagai pengendap ke instalasi pengolahan air limbah, (ii) mengolahnya di -lokasi dengan kaustik dan mengangkut lumpur yang dihasilkan, (iii) meregenerasinya dengan proses regenerasi asam di lokasi, atau di fasilitas di luar lokasi, dan menggunakan kembali asam yang diregenerasi, (iv) memulihkan asam bebas dengan beberapa pemulihan yang tersedia secara komersial proses, dan (v) menyuntikkannya dengan injeksi sumur dalam.
Regenerasi asam klorida mengacu pada proses reklamasi asam klorida terikat dan tidak terikat dari larutan logam klorida seperti besi klorida. Asam yang diregenerasi tidak memiliki efek buruk pada efisiensi pembersihan logam dibandingkan dengan asam murni. Ini mengasinkan seefisien asam perawan.
Regenerasi cairan pengawet bekas dari asam klorida adalah proses tambahan di mana cairan pengawet bekas, yang mengandung besi klorida ditambah larutan asam klorida, diubah melalui proses seperti proses oksidasi semprot menjadi produk oksida besi yang dapat dipasarkan ditambah asam klorida. solusi yang dapat didaur ulang untuk operasi pengawetan. Proses regenerasi asam menghilangkan kebutuhan dan biaya pembuangan asam bekas dan biaya penggantian cairan acar hidroklorik, membuat pabrik hampir mandiri. Pada saat yang sama, proses tersebut mengurangi emisi dan dengan demikian dampak pabrik terhadap lingkungan.
Bergantung pada komposisi cairan pengawet bekas, berbagai metode regenerasi digunakan. Beberapa metode memungkinkan pemulihan hanya asam klorida.
Pabrik regenerasi asam klorida total menyediakan sarana untuk hampir menghilangkan biaya dan logistik kompleks yang terkait dengan pasokan dan pembuangan asam segar dan bekas. Untuk regenerasi regenerasi asam klorida, ada berbagai proses untuk regenerasi total dari cairan acar hidroklorik yang dihabiskan, menghasilkan tingkat pemulihan hingga 99,5%. Semua proses ini menghadirkan peningkatan yang signifikan dalam kelayakan dibandingkan proses penguapan tradisional untuk reklamasi hanya asam klorida yang tidak terikat. Selain itu, regenerasi asam total merupakan bagian dari tanggung jawab lingkungan dari pabrik yang mengoperasikan jalur pengawetan.
Ada beberapa teknologi regenerasi yang tersedia untuk regenerasi asam klorida. Ini adalah (i) piro-hidrolisis, (ii) kristalisasi, (iii) pengendapan hidrolitik, (iv) ekstraksi pelarut, dan (v) sistem manajemen asam Kleingarn
Piro-hidrolisis – Piro-hidrolisis adalah proses di mana cairan acar bekas didekomposisi secara termal untuk mengubah cairan acar bekas kembali menjadi asam klorida dan oksida besi. Proses ini dilakukan pada suhu yang sangat tinggi bersama dengan uap air dan oksigen. Cairan acar bekas dipompa ke dalam pirohidroliser yang mengubah besi klorida (FeCl2) menjadi komponen oksida besi (Fe2O3) dan asam klorida. Pabrik piro-hidrolisis sangat intensif energi, terutama karena sejumlah besar pembakaran bahan bakar diperlukan untuk menguapkan larutan logam klorida dan untuk memanaskan isi pemanggang. Gambar 1 menunjukkan diagram skema untuk proses pirohidrolisis.
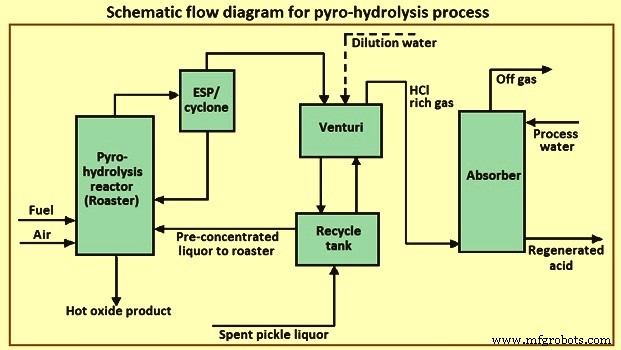
Gbr 1 Diagram skematis untuk proses piro-hidrolisis
Pemulihan asam klorida dari cairan pengawet bekas dengan piro-hidrolisis menguntungkan lingkungan karena menghilangkan kebutuhan untuk menetralkan dan membuang asam bekas dan mengurangi konsumsi air. Ini juga sangat hemat biaya, karena menghilangkan biaya pembuangan, mengurangi biaya penggantian asam dan menghasilkan produk sampingan oksida yang berharga.
Piro-hidrolisis adalah konversi kimia garam logam menggunakan uap dan oksigen pada suhu tinggi. Tergantung pada suhu piro-hidrolisis, produk oksida baik dalam butiran jika dirawat di pabrik fluidized bed, atau sebagai bubuk, jika diperlakukan pada suhu yang lebih rendah di pabrik panggang semprot. Proses pemanggangan semprot bekerja pada suhu jauh di bawah suhu sintering oksida besi sehingga oksida diperoleh sebagai bubuk merah, biasanya berukuran kurang dari 1 mikrometer.
Regenerasi asam klorida menggunakan piro-hidrolisis memberikan pemulihan total larutan asam bekas menjadi produk bebas logam. Proses ini tidak hanya memulihkan asam klorida dalam keadaan bebas dan terikat, tetapi juga memperoleh oksida besi berkualitas tinggi, baik sebagai pelet atau bubuk halus, yang sangat dibutuhkan oleh ferit, pigmen, dan industri lainnya.
Regenerasi asam klorida menggunakan metode piro-hidrolisis biasanya dipertimbangkan oleh pabrik pengawetan besar karena metode ini mahal karena biaya energi yang tinggi yang terlibat dalam pengoperasian pirohidroliser. Metode ini tidak ramah lingkungan karena garam klorida korosif yang ada dalam debu yang dikeluarkan oleh proses ini. Oleh karena itu, teknologi proses ini membutuhkan instalasi sistem pengumpul debu yang terdiri dari cyclone atau electrostatic precipitator (ESP).
Kristalisasi – Regenerasi asam menggunakan metode kristalisasi pada awalnya digunakan untuk regenerasi limbah asam sulfat. Namun, karena perkembangan selanjutnya, regenerasi menggunakan kristalisasi juga dapat dilakukan untuk cairan pengawet bekas asam klorida. Penerapan regenerasi menggunakan kristalisasi untuk asam klorida telah dikonfirmasi setelah melakukan beberapa studi kelayakan teknis yang menyimpulkan bahwa kristalisasi multi-tahap perlu dilakukan dalam serangkaian kristalisasi reaktor tangki berpengaduk kontinyu. Limbah asam klorida juga perlu melalui proses daur ulang kristal untuk menghasilkan kristal bebas pengotor.
Proses regenerasi melalui kristalisasi besi klorida melibatkan teknik standar yang tidak memiliki batasan ukuran. Asam klorida yang diregenerasi dapat berdampak pada proses pengawetan karena beban mati klorida. Masalah ini dapat dihilangkan dengan menyesuaikan kondisi tingkat pengawetan setidaknya sama dengan asam klorida murni dengan permukaan akhir yang dapat diterima.
Presipitasi hidrolitik – Regenerasi cairan pengawet bekas hidroklorik menggunakan teknologi presipitasi hidrolitik melibatkan proses distilasi uap di bawah kondisi hidrolisis evaporatif pada suhu setinggi 250 derajat C. Ketika tidak ada garam klorida lain, proses distilasi hidrolitik berlanjut hingga selesai pada sekitar 175 derajat C. Namun, ketika magnesium klorida hadir, suhu yang lebih tinggi diperlukan untuk menyelesaikan proses distilasi hidrolitik.
Teknologi ekstraksi pelarut – Teknologi rute ekstraksi pelarut adalah teknologi regenerasi yang populer. Teknologi regenerasi ini lebih disukai karena menghasilkan produk sampingan yang kurang berbahaya dalam proses pengolahan cairan pengawet bekas. Dengan menggunakan teknologi ekstraksi pelarut, besi klorida dapat dipisahkan dari asam klorida. Produk sampingan yang dihasilkan dari regenerasi cairan pengawet bekas hidroklorik harus melalui pasca-perawatan.
Sistem pengelolaan asam kleingarn – Dengan mengadopsi teknologi regenerasi ini, biaya penggantian cairan pengawet bekas dengan asam baru dapat dikurangi. Teknologi ini membutuhkan investasi awal yang lebih sedikit. Penerapan sistem manajemen asam Kleingarn sebagai metode regenerasi membantu mengurangi volume limbah dengan menghemat jumlah asam klorida yang digunakan. Metode regenerasi ini juga dapat memudahkan daur ulang limbah asam.
Sistem pengelolaan asam Kleingarn tidak hanya membutuhkan investasi awal yang lebih sedikit tetapi pada saat yang sama membantu mengurangi volume minuman keras pengawetan yang dihabiskan. Regenerasi cairan pengawet bekas menggunakan sistem manajemen asam Kleingarn dapat membantu meningkatkan kekuatan asam dan mengurangi konsentrasi besi pada saat yang bersamaan. Perlu dilakukan eksperimen untuk mendapatkan laju acar yang optimum dengan menggunakan metode regenerasi ini. Proses regenerasi ini dapat diulang hingga bak mandi asam klorida khusus perlu dikosongkan untuk dibersihkan atau diperbaiki. Setelah tangki mandi asam klorida khusus dikosongkan, larutan segar harus dibuat menggunakan sebagian asam bekas dari tangki lain ditambah asam segar. Regenerasi asam klorida menggunakan sistem pengelolaan asam Kleingarn memiliki keuntungan ekologis.
Proses regenerasi minuman acar bekas
Ada beberapa proses untuk regenerasi cairan pengawet asam klorida bekas yang telah dikembangkan sejak akhir 1960-an, tetapi tidak ada yang cocok dengan penerimaan komersial yang luas dari proses pemanggangan semprot, yang telah menunjukkan kelayakan dan viabilitas jangka panjangnya di sejumlah besar industri. implementasi. Proses pemanggangan semprot dan beberapa proses lain untuk regenerasi asam klorida dijelaskan di bawah ini.
Proses pemanggangan semprot
Di antara semua proses yang dikenal untuk regenerasi asam klorida seperti kristalisasi dan pirohidrolisis unggun fluida, proses pemanggang semprot adalah yang paling layak dalam hal konsumsi energi, biaya operasi, biaya pemeliharaan, ketersediaan, dan produk sampingan yang dapat dipasarkan.
Proses spray roaster adalah proses piro-hidrolitik di mana asam yang dihabiskan disemprotkan ke dalam tungku pembakaran langsung (melalui kontak dengan oksigen) dan dipecah menjadi bubuk oksida besi (fase padat) dan asam klorida (fase gas). Gas asam klorida diserap dalam air untuk membentuk asam klorida yang diregenerasi dengan kekuatan sekitar 18% yang dapat digunakan kembali untuk pengawetan. Adalah umum dan menarik untuk menggunakan air bilasan yang sedikit asam dari garis pengawetan sebagai cairan penyerap.
Pemanggang semprot hanyalah bejana baja berlapis tahan api besar dengan pembakar yang ditembakkan langsung di dekat bagian bawah untuk memanaskan isi pemanggang. Jumlah pembakar dan posisinya tergantung pada ukuran pemanggang dan panas yang dibutuhkan. Temperatur nyala api dapat mencapai kisaran 1.200 derajat C hingga 1.750 derajat C tergantung pada rasio udara dan bahan bakar. Karena efek pendinginan dari semprotan umpan, suhu rata-rata di zona reaksi biasanya antara 600 derajat C hingga 700 derajat C. Dalam jenis pemanggang piro-hidrolisis ini, larutan logam klorida disemprotkan ke dalam papan kosong yang kosong. bejana silinder, sedangkan energi yang dibutuhkan disuplai oleh aliran gas panas ke atas yang dihasilkan di pembakar bawah.
Pemanggang semprot harus dirancang untuk memberikan waktu pengeringan yang cukup bagi tetesan cairan terbesar untuk terhidrolisis sebelum mencapai bagian bawah bejana. Pemanggang semprot komersial memiliki ketinggian mulai dari 5 meter hingga 8 meter untuk menyediakan waktu pengeringan ini. Selanjutnya, diameter pemanggang harus dirancang untuk kecepatan gas (ruang) ke atas yang cukup tinggi untuk mencegah tetesan membasahi bagian bawah bejana, tetapi cukup rendah untuk mencegah hilangnya debu yang tinggi ke sistem off-gas. Kecepatan ruang biasanya 0,3 meter per detik hingga 1 meter per detik untuk unit komersial dan bisa lebih rendah lagi untuk unit yang lebih kecil.
Gambar 2 menunjukkan sketsa alat pemanggang semprot. Pemanggang semprot biasanya memiliki diameter yang sangat besar untuk menjaga kecepatan gas tetap rendah. Jika kecepatan gas menjadi terlalu tinggi, terlalu banyak partikel yang terbawa bersama dengan off-gas dari roaster, dan kualitas produk serta efisiensi dari roaster akan turun. Di dalam spray roaster, off-gas dan oksida meninggalkan roaster berlawanan arah pada sekitar 400 derajat C sampai 500 derajat C. Karena aliran berlawanan arah, suhu keluar dalam spray roaster kurang dari suhu zona reaksi.
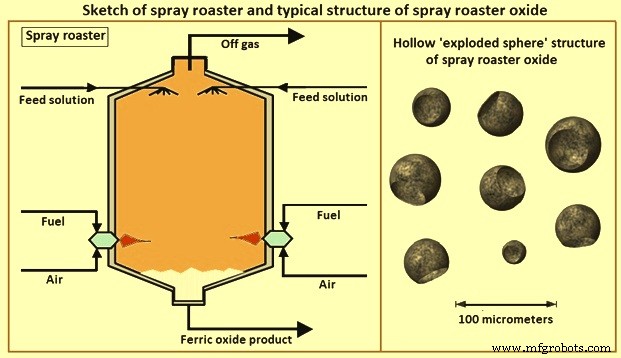
Gbr 2 Sketsa spray roaster dan struktur khas spray roaster oxide
Waktu tinggal partikel yang disemprotkan di zona reaksi suhu tinggi sangat singkat dan karenanya, tetesan cairan yang sangat kecil, yang dapat dengan cepat dipanaskan, harus dibuat dengan atomisasi. Panas yang cepat dari partikel yang terpancar menghasilkan pembentukan kerak oksida logam padat pada permukaan setiap tetesan. Saat sebagian besar tetesan memanas, kandungan air menguap dan menembus kulit oksida. Oleh karena itu, oksida panggang semprot sering kali terdiri dari bola yang sangat halus (beberapa mikrometer), 'berbulu', berongga. Struktur khas dari spray roaster oxide ditunjukkan pada Gambar 2.
Tiga langkah proses dasar dari proses spray roster adalah (i) pra-konsentrasi, (ii) pemanggangan, dan (iii) penyerapan. Pada tahap pra-konsentrasi, asam limbah yang masuk mengalami panas langsung dan pertukaran massa dengan gas buang panas dari tungku pemanggang. Pertukaran panas langsung dilakukan dalam evaporator venturi di mana asam limbah diatomisasi dan bercampur secara turbulen dengan gas pemanggang dengan kecepatan tinggi. Dengan demikian, limbah gas diuapkan sebagian, meninggalkan asam limbah yang telah dikonsentrasikan sebelumnya untuk digunakan sebagai umpan cair ke tungku pemanggangan semprot.
Dalam tungku pemanggangan semprot, asam limbah pra-konsentrat yang disuntikkan dari atas melalui nozel atomisasi bertekanan tinggi mengalami penguapan setetes demi setetes air dan asam klorida serta reaksi piro-hidrolisis sisa besi klorida dan oksigen berlebih. disediakan oleh pembakar. Burner ini disejajarkan secara tangensial di sekitar lingkar tungku untuk membentuk pola aliran 'putaran' tertentu yang meningkatkan waktu retensi tetesan dengan meningkatkan panjang jalurnya melalui tungku. Hampir semua jenis bahan bakar fosil kelas industri seperti misalnya gas alam, gas minyak cair (LPG), gas alam cair (LNG), gas oven kokas, atau bahan bakar minyak dapat digunakan.
Dalam sistem regenerasi piro-hidrolisis, besi klorida (FeCl2) diubah menjadi asam klorida dan oksida besi melalui dekomposisi hidrolitik. Reaksi berlangsung dalam reaktor pada suhu berkisar antara 600 derajat C sampai 800 derajat C. Pada suhu reaksi larutan besi klorida dipecah menjadi hidrogen klorida dan oksida besi melalui uap air dan oksigen atmosfer. Reaksi kimianya adalah (i) 12 FeCl2 + 3 O2 =8 FeCl3 + 2 Fe2O3, (ii) 2FeCl3 + 3 H2O =6 HCl + Fe2O3, dan (iii) 4FeCl2 + 4H2O + O2 =Fe2O3 + 4 HCl.
Dalam kolom absorpsi, gas pemanggang yang didinginkan dari gas keluar dari pra-konsentrator mengalami pertukaran panas adiabatik dengan air bilasan dalam kolom yang dikemas dan membentuk asam yang diregenerasi dengan konsentrasi khas sekitar 18% asam klorida, yang dapat digunakan kembali untuk pengawetan. . Pemanggang biasanya dilengkapi dengan sistem off-gas yang ekstensif, termasuk kontaktor gas / cair (venturi) untuk penguapan sebagian dari pakan segar, penyerap untuk memulihkan asam klorida gas sebagai asam yang dipulihkan, dan peralatan penghilang debu seperti siklon atau ESP . Lembar aliran khas dari proses pemanggangan semprot diberikan pada Gambar 3.
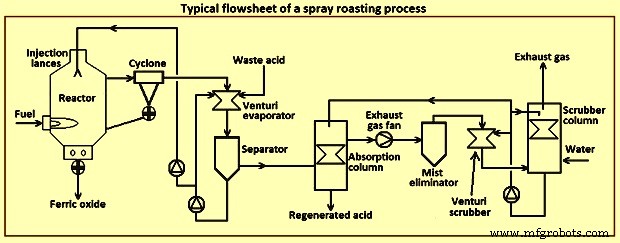
Gbr 3 Flow sheet khas dari proses spray roasting
Produk reaksi kimia dari reaksi piro-hidrolisis terdiri dari asam klorida yang diekstraksi dari bagian atas tungku bersama-sama dengan uap dan produk pembakaran dan bubuk oksida besi yang mengendap di bagian bawah kerucut tungku secara pneumatik dibawa ke tempat penyimpanan , dari mana dapat diisi dalam berbagai sarana transportasi komersial seperti ke dalam tas besar atau ke truk.
Bubuk oksida besi panggang semprot memiliki kemurnian oksida tinggi dan struktur permukaan yang baik. Karena sifat-sifat ini, bahan ini menjadi bahan masukan yang berharga bagi industri hilir seperti produsen cat arsitektur, produk bangunan, katalis styrene, toner untuk printer laser, dan ferit.
Proses fluidized bed
Proses unggun terfluidisasi juga merupakan proses piro-hidrolitik seperti proses pemanggang semprot dan berlangsung dalam tungku yang dipanaskan secara langsung. Dalam pemanggang unggun terfluidisasi, larutan logam klorida dimasukkan ke dalam unggun besar oksida logam panas, sedangkan energi panas yang dibutuhkan disediakan oleh gas pembakaran fluidisasi panas. Gambar 4 menunjukkan sketsa skema dari fluidized bed roaster.
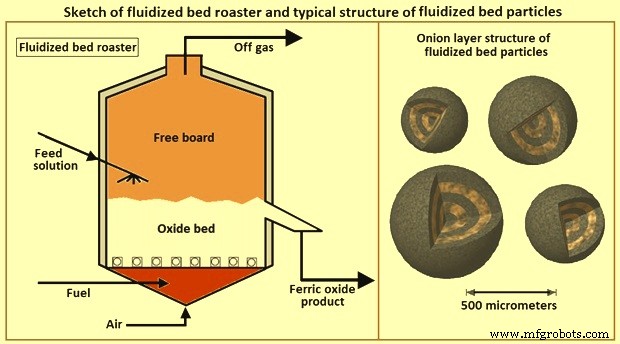
Gbr 4 Sketsa fluidized bed roaster dan struktur tipikal partikel fluidized bed
Pemanggang unggun terfluidisasi harus dirancang untuk kecepatan ruang yang 3 kali hingga 10 kali kecepatan fluidisasi minimum unggun oksida. Untuk pelet oksida besi dengan diameter 200 mikrometer hingga 2.000 mikrometer, kecepatan ruang dari 2 meter per detik hingga 2,5 meter per detik adalah hal biasa. Ketinggian roaster dipilih untuk meminimalkan jumlah debu yang terbawa ke sistem off-gas. Ketinggian total dari fluidized bed roaster adalah 5 meter hingga 6 meter.
Gas pembakaran panas biasanya dihasilkan oleh tuyer terendam yang langsung menyuntikkan udara dan bahan bakar ke bagian bawah fluidized bed. Gas panas mengalir ke atas dan memfluidisasi lapisan partikel. Saat gas pembakaran mengalir melalui unggun oksida yang diaduk dengan baik, dengan cepat mencapai kesetimbangan termal dengan unggun. Umpan cair tidak disemprotkan, tetapi langsung diumpankan (dituangkan) di atas, atau di dalam, lapisan oksida. Menurut satu penjelasan, umpan cair membasahi lapisan luar partikel oksida panas (dengan orde 0,5 mm) dan dengan cepat diuapkan untuk membentuk lapisan oksida padat baru seperti bawang di atas oksida yang ada, sehingga menghasilkan partikel homogen, seperti yang ditunjukkan pada Gambar 4.
Karena off-gas dari fluidized bed roaster lebih panas daripada spray roaster, jumlah air yang lebih tinggi diuapkan sebelumnya di venturi. Jadi, beberapa pengenceran air perlu ditambahkan ke venturi, untuk mengontrol besi klorida, konsentrasi di bawah tingkat saturasi. Tanpa pengenceran air, cairan venturi yang bersirkulasi membentuk kristal yang dapat menyebabkan penyumbatan dan kerusakan pada kontaktor venturi. Kebutuhan bahan bakar dalam proses fluidized bed lebih tinggi daripada proses spray roaster, terutama karena kebutuhan air pengenceran. Dalam beberapa kasus, jumlah air pengenceran dapat dikurangi dengan (i) mengoperasikan unggun terfluidisasi pada suhu yang lebih rendah (misalnya 800 derajat C), (ii) meningkatkan efisiensi penangkapan debu oksida dalam siklon (misalnya menggunakan multi-siklon) , (iii) menurunkan jumlah pembentukan debu halus di unggun terfluidisasi. Karena suhu pembakaran yang aman untuk gas alam adalah sekitar 760 derajat C, suhu unggun kurang dari 800 derajat C biasanya tidak digunakan untuk sistem yang dioperasikan dengan gas alam. Gambar 5 menunjukkan diagram alir sederhana untuk proses fluidized bed.
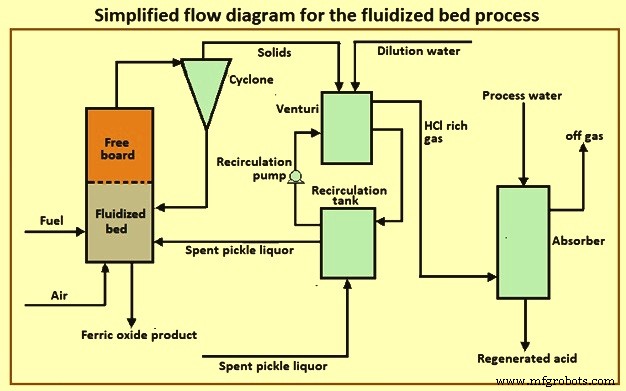
Gbr 5 Diagram alir yang disederhanakan untuk proses fluidized bed
Pada proses fluidized bed pengubahan asam limbah menjadi oksida besi dan hidrogen klorida berlangsung dalam fluidized bed pada suhu sekitar 800 derajat C sampai 900 derajat C. Karena itu, oksida besi diperoleh dari regenerasi asam klorida bed terfluidisasi. tanaman adalah granular, konsistensi disinter dan disebut pelet. Diameter rata-rata pelet adalah 200 mikrometer hingga 2.000 mikrometer tergantung pada pengaturan reaktor. Pelet adalah pengganti bijih besi dan dapat didaur ulang kembali di dalam pabrik baja terintegrasi.
Dalam proses unggun terfluidisasi, penyerapan asam klorida dilakukan dengan cara yang sama seperti dalam pemanggangan semprot, tetapi konsentrasi asam yang diperoleh sedikit lebih rendah biasanya pada 17%. Proses piro-hidrolitik unggun terfluidisasi memiliki beberapa keunggulan berbeda dibandingkan proses pemanggang semprot. Ini adalah (i) produk oksida adalah padatan granular dan biasanya bebas debu karena pertumbuhan partikel seperti lapisan bawang di dalam fluidized bed roaster, (ii) tidak diperlukan unit pembakaran terpisah karena piro-hidrolisis dan reaksi pembakaran terjadi secara simultan di unggun terfluidisasi, (iii) kontrol atas ukuran partikel dimungkinkan melalui kontrol waktu tinggal, daur ulang parsial produk partikulat, atau dengan memvariasikan pengiriman umpan, (iv) pencampuran yang baik dan kontrol suhu yang biasanya dikaitkan dengan fluidized bed, dan (v) fluidized bed roaster biasanya lebih kecil dari spray roaster.
Proses PHAR
PHAR (Pickliq hydrochloric acid regenerasi) adalah proses regenerasi asam klorida bekas dari pengawetan baja. Proses ini berlaku untuk operasi pengawetan ukuran apa pun. Teknologi PHAR menghilangkan masalah pembuangan, menciptakan pengurangan yang cukup besar dalam biaya operasi, lingkungan, dan modal. Proses ini menggunakan asam sulfat untuk mengembalikan asam klorida untuk digunakan kembali. PHAR menghasilkan kristal besi sulfat (sulfat hepta-hidrat), produk sampingan yang ekonomis, yang dapat dijual untuk keperluan industri. Dengan menghilangkan transportasi dan/atau pengolahan minuman acar bekas, bersama dengan biaya yang terkait dengan menghasilkan asam klorida untuk menggantikan larutan minuman keras bekas, PHAR menghasilkan penghematan energi sebesar 95%, penghematan biaya sebesar 52%, dan pengurangan emisi CO2 sebesar 91%, dibandingkan dengan teknologi yang ada.
Dalam proses PHAR, cairan acar bekas biasanya keluar dari jalur pengawetan pada sekitar 11% hingga 13% besi dan 2% hingga 4% asam klorida bebas. Suhu asam adalah sekitar 80 derajat C hingga 90 derajat C untuk jalur pengawetan kontinu tetapi bisa lebih rendah untuk operasi pengawetan batch. Dengan menggunakan penukar panas aliran silang, cairan acar bekas yang keluar menukar panas dengan 'minuman acar yang diregenerasi' (RPL) kembali ke jalur pengawetan.
Cairan acar bekas yang akan diregenerasi kemudian dialirkan ke dalam reaktor yang dikontakkan dengan asam sulfat pekat (93%). Asam sulfat bereaksi dengan besi klorida sehingga membebaskan asam klorida bebas dalam larutan. Penurunan suhu akhir disertai dengan pendinginan campuran reaksi hingga suhu -15 derajat C hingga -1 derajat C dalam tangki kristalisasi. Penurunan suhu mengurangi kelarutan besi sulfat, menyebabkannya mengendap dari larutan. Besi sulfat yang dihasilkan dipisahkan dengan kristalisasi. Cairan induk, sekarang diperkaya dengan asam klorida, tetapi mengandung sisa asam sulfat kemudian dipisahkan dari kristal dengan penyaringan vakum atau sentrifugasi dan didaur ulang ke proses pengawetan.
Sejumlah kecil air digunakan untuk mencuci sisa larutan induk dari kristal. Air ini mengkompensasi air hidrasi yang dikombinasikan dengan besi sulfat. Tingkat asam sulfat sisa dalam asam klorida yang diregenerasi tergantung pada konsentrasi besi dan suhu. Proses ini beroperasi pada suhu rendah dan menghasilkan besi sulfat hepta-hidrat (FeSO4.7H2O). Gambar 6 menunjukkan tata letak khas proses PHAR.
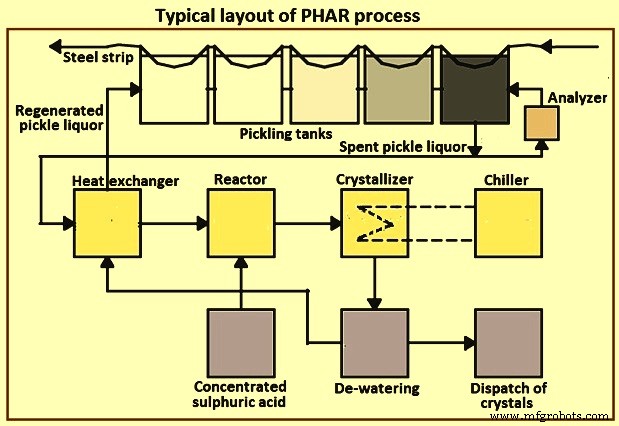
Gbr 6 Tata letak khas proses PHAR
Proses PHAR memiliki sejumlah keunggulan potensial dibandingkan dengan alternatif lainnya. Ini adalah (i) proses beroperasi pada suhu rendah, sehingga meminimalkan korosi dan memungkinkan penggunaan plastik murah untuk perpipaan dan peralatan lainnya, (ii) konsumsi energi untuk pendinginan dan kristalisasi secara inheren kurang dari penguapan dan dapat diminimalkan dengan reklamasi panas dari minuman acar bekas dengan penukar panas, (iii) besi sulfat hepta-hidrat adalah bahan yang siap dipasarkan, yang digunakan sebagai koagulan pengolahan air serta penghilang bau kotoran, (iv) investasi modal untuk sistem jauh lebih sedikit dibandingkan alternatif lain dan secara fisik jauh lebih kecil, (v) tidak diperlukan pasokan bahan bakar gas untuk operasi, dan (vi) prosesnya lebih memaafkan terhadap kontaminasi dengan logam lain seperti seng.
Proses penyulingan
Proses distilasi telah digunakan di mana ada tingkat yang signifikan dari asam bebas yang tersisa dalam cairan acar bekas. Asam klorida murni, pada konsentrasi azeotropik sekitar 15% diperoleh dari 'overs' sedangkan cairan besi klorida pekat diperoleh dari 'bottom'. Proses ini hanya memulihkan nilai 'asam bebas'. Dalam satu variasi proses ini, besi klorida yang terakumulasi di dasar dikristalisasi. Dalam variasi lain, proses pertukaran ion retardasi asam digunakan untuk mengurangi keasaman produk samping besi klorida cair.
Proses penyulingan asam sulfat
Dalam proses ini asam sulfat ditambahkan ke minuman acar bekas. Hal ini menyebabkan reaksi FeCl2 + H2SO4 =2HCl + FeSO4 berlangsung. Asam klorida yang dibebaskan diperoleh kembali bersama dengan asam klorida bebas asli dengan distilasi, sedangkan besi dikristalkan sebagai besi sulfat monohidrat.
Proses piro-hidrolisis hibrida
Ketika tujuan utama dalam pengoperasian pabrik piro-hidrolisis adalah produksi bubuk oksida besi berkualitas tinggi, maka desain reaktor yang menggabungkan efisiensi energi tungku pemanggangan semprot dengan kondisi proses homogen dan stabil dari proses fluidized bed adalah diadopsi. Hal ini membutuhkan investasi yang lebih tinggi dalam teknologi penghilang debu dan pendinginan gas.
Proses regenerasi hidro-termal
Proses regenerasi hidro-termal adalah teknologi yang relatif baru. Ini menggantikan tungku pembakaran langsung dan penyerapan gas / cairan dengan rute proses alternatif yang terdiri dari oksidasi dan hidrolisis. Pembentukan oksida besi terjadi dalam fase cair yang mengurangi konsumsi energi panas. Konsentrasi asam hasil regenerasi sama dengan konsentrasi total HCl asam limbah. Konsentrasi asam regenerasi ini dapat ditingkatkan ke tingkat yang lebih tinggi dari 30% dengan menggunakan pra-konsentrator. Kualitas oksida besi yang dihasilkan oleh proses ini sebanding dengan proses piro-hidrolitik dalam hal kontaminasi ion klorida. Namun permukaan partikel tertentu dapat disesuaikan ke angka yang jauh lebih tinggi dengan menyetel kondisi hidrolisis.