Kimia Pembuatan Besi dengan Proses Tungku Ledakan
Kimia Proses Pembuatan Besi dengan Blast Furnace
Tungku sembur (BF) modern yang beroperasi dengan laju kokas rendah adalah unit pemrosesan yang efisien terutama karena karakteristik intrinsik dari reaktor gas-padatan arus berlawanan. Keberhasilan penggunaan konsep ini membutuhkan bahwa setiap bahan yang dibebankan ke tungku memiliki karakter fisik yang seragam, dan memiliki komposisi yang seragam. Selain itu, setiap material harus mempertahankan karakter fisik yang baik ini saat bergerak turun melalui tungku ke tempat terjadinya pelelehan.
Saat oksida besi, kokas, dan bahan pembentuk terak bergerak turun melalui tumpukan tungku, beberapa proses pertukaran penting terjadi. Panas dikeluarkan dari gas tanur menaik yang terutama terdiri dari karbon monoksida (CO), karbon dioksida (CO2), dan nitrogen (N2) dan dipindahkan ke bahan beban turun. Oksigen (O2) dikeluarkan dari oksida besi yang turun dan dipindahkan ke gas pereduksi yang naik. Oleh karena itu dalam reaktor arus berlawanan yang sangat efisien ini, reaksi kimia berlangsung dan ketika muatan turun, suhu bahan beban meningkat, fusi besi tereduksi, oksida besi dan bahan pembentuk terak dimulai, dan akhirnya logam cair dan terak terkumpul di perapian tungku. Sebagian besar kokas yang dibebankan ke tungku dibakar dengan oksigen dalam ledakan udara panas di tuyeres untuk menyediakan panas dan zat pereduksi CO.
Ketika bahan beban dan kokas yang dibebankan ke bagian atas BF turun melalui tumpukan, mereka dipanaskan oleh gas panas yang naik dari tuyeres. Sebagai hasil dari pemanasan awal ini, kokas terbakar dengan intensitas tinggi ketika mencapai bagian bawah tungku yang berdekatan dengan tuyer dan bersentuhan dengan udara ledakan panas. Namun, karena suhu yang sangat tinggi (sekitar 1.650 derajat C) dan sejumlah besar karbon (C) yang ada dalam bentuk kokas, CO2 yang terbentuk tidak stabil dan segera bereaksi dengan karbon tambahan untuk membentuk CO. Akibatnya, pembakaran karbon (kokas) dalam BF dapat dinyatakan dengan persamaan kimia 2C + O2 =2CO; delta H =+110.458 kJ/kmol. Dalam pengoperasian BF modern, antara 250 kilogram (kg) dan 400 kg karbon bereaksi dengan cara ini untuk setiap ton logam panas yang dihasilkan. Reaksi ini merupakan sumber panas utama untuk operasi peleburan dan juga menghasilkan gas pereduksi (CO) yang naik ke tumpukan tungku di mana ia memanaskan dan mengurangi sebagian besar oksida besi dalam beban saat turun ke perapian.
Setiap uap air (H2O) di udara ledakan juga bereaksi dengan beberapa karbon dalam kokas di zona pembakaran. Reaksi ini tidak menghasilkan panas seperti pembakaran, melainkan mengkonsumsi panas. Namun, untuk setiap unit karbon, reaksi ini menghasilkan lebih banyak gas pereduksi daripada yang dihasilkan ketika karbon dibakar di udara. Ketika karbon terbakar di udara, ia hanya menghasilkan satu unit CO, tetapi ketika bereaksi dengan H2O, menghasilkan satu unit CO dan satu unit hidrogen (H2). Oleh karena itu, dalam kasus tertentu, di mana tingkat reduksi bawaan bahan beban lebih rendah dari normal dan di mana suhu ledakan panas yang relatif tinggi tersedia (antara 1.000 derajat C dan 1.200 derajat C), telah dianggap menguntungkan untuk menjaga kadar air ledakan pada tingkat tinggi yang seragam dengan penambahan uap air (uap) untuk meningkatkan daya reduksi gas BF. Injeksi bahan bakar tambahan memberikan keuntungan serupa. Reaksi kimia ini dinyatakan dengan persamaan C + H2O =CO + H2; delta H =+131.378 kJ/kmol. Manfaat tambahan diperoleh dari pengenalan (atau peningkatan) hidrogen dalam gas pereduksi tungku. Ketika persen hidrogen meningkat, densitas gas berkurang. Hal ini menghasilkan volume pengurangan gas yang setara dengan memberikan ketahanan yang lebih rendah terhadap beban yang layak.
Gas naik mulai mengurangi oksida besi dari beban di bagian atas BF di mana suhu di bawah 925 derajat C. Pada suhu ini, kesetimbangan kimia mencegah semua CO dan H2 digunakan untuk reduksi (keseimbangan CO / CO2 rasio sekitar 2,3 untuk pengurangan wustite, jika rasio turun di bawah nilai ini besi dioksidasi ulang Oleh karena itu, rasio molekul CO atau H2 untuk oksida besi adalah sekitar tiga kali jumlah yang ditunjukkan oleh reaksi stoikiometrik (i ) 1/2 Fe2O3 + 3/2 CO =Fe + 3/2 CO2; delta H =+12.866 kJ/kmol, (ii) 1/3 Fe3O4 + 4/3 CO =Fe + 4/3 CO2; delta H =+3940 kJ/kmol, (iii) FeO + CO =Fe + CO2; delta H =–16.108 kJ/kmol, (iv) 1/2 Fe2O3 + 3/2 H2 =Fe + 3/2 H2O; delta H =+ 48.953 kJ/kmol, (v) 1/3 Fe3O4 + 4/3 H2 =Fe + 4/3 H2O; delta H =+51,042 kJ/kmol, dan (vi) FeO + H2 =Fe + H2O; delta H =+ 25.104 kJ/kmol.
Di masa lalu, jenis pengurangan ini disebut pengurangan tidak langsung berbeda dengan jenis yang terjadi pada suhu yang lebih tinggi yang disebut pengurangan langsung. Namun, nomenklatur ini menjadi membingungkan karena reaksi kimia yang sama ini disebut reduksi langsung dalam menggambarkan proses DRI seperti Wiberg, HIB, FIOR, dan proses serupa. Karena alasan ini, istilah ini biasanya tidak digunakan seperti dulu.
Bagian oksida besi yang tidak direduksi di bagian atas tungku yang suhunya relatif rendah harus dikurangi di bagian bawah di mana suhunya sangat tinggi. Karena CO2 dan H2O tidak stabil pada suhu ini dengan adanya sejumlah besar kokas, mereka bereaksi dengan karbon hampir secepat mereka terbentuk. Akibatnya, reaksi reduksi keseluruhan di bagian tungku ini dapat diwakili oleh reaksi FeO + C =Fe + CO; delta H =+156.482 kJ/kmol tidak peduli apakah H2 atau CO adalah reaktan. Reaksi ini diperoleh dengan menambahkan salah satu reaksi FeO + CO =Fe + CO2 secara aljabar; delta H =–16.108 kJ/kmol, dan CO2 + C =2CO; delta H =+172.590 kJ/kmol atau reaksi FeO + H2 =Fe + H2O; delta H =+25.104 kJ/kmol, dan H2O + C =CO + H2; delta H =+131.378 kJ/kmol.
Reaksi reduksi FeO + C =Fe + CO menyerap sejumlah besar panas, dan karenanya, semakin besar jumlah reduksi yang terjadi dengan cara ini, semakin besar jumlah panas yang harus disuplai ke tungku. Reaksi ini juga menghasilkan CO, yang merupakan gas yang digunakan dalam reaksi reduksi yang berlangsung di tumpukan BF. Dalam kebanyakan kasus, operasi yang paling efisien dicapai ketika kira-kira sepertiga dari reduksi dilakukan menurut reaksi FeO + C =Fe + CO dan keseimbangan menurut reaksi Fe2O3 + 3 CO =2 Fe + 3 CO2 melalui FeO + H2 =Fe + H2O.
Panas untuk proses ini tidak dihasilkan seluruhnya oleh pembakaran kokas, karena pada sebagian besar BF, kira-kira 40% dipasok dari panas sensibel dari udara panas ledakan. Sebagian besar bahan bakar dapat diinjeksikan secara ekonomis melalui tuyer sebagai gas alam, tar, bahan bakar minyak, atau batu bara baik dalam bentuk bubuk atau butiran. Dalam kasus seperti itu, karbon dalam bahan bakar terbakar menjadi CO, tetapi karena banyaknya kokas yang ada, hidrogen tetap sebagai H2 dan tidak teroksidasi sampai mereduksi oksida besi di suatu tempat di atas tuyer.
Komponen pembawa besi yang dibebankan ke tungku adalah oksida sederhana besi, Fe2O3, dan Fe3O4. Bijih alami biasanya adalah hematit (Fe2O3) atau magnetit (Fe3O4). Pelet pada dasarnya adalah Fe2O3. Komposisi sinter bijih besi bervariasi dari Fe2O3 dan Fe3O4 hingga campuran leburan yang mengandung magnetit, fayalit, 2FeO.SiO2, dan di-kalsium ferit. Reduksi oksida besi biasanya terjadi dalam beberapa langkah. Reaksi dengan CO diberikan oleh persamaan (i) 3Fe2O3 (s) + CO (g) =2Fe3O4 (s) + CO2 (g); delta H -48 kJ, (ii) Fe3O4 (s) + CO (g) =3FeO (s) + CO2 (g); delta H -21,7 kJ, dan (iii) FeO(s) + CO (g) =Fe(s) + CO2 (g); delta H-11 kJ. Reaksi ini dicapai pada suhu yang lebih tinggi berturut-turut, dan lebih jauh ke bawah tungku.
Persentase CO yang lebih tinggi berturut-turut diperlukan untuk menyelesaikan reaksi ini oleh gas yang naik. Harus diakui bahwa tidak mungkin seluruh CO dalam gas diubah menjadi CO2 untuk setiap reaksi. Misalnya, ada rasio keseimbangan seperti yang diberikan oleh konstanta K3 untuk ketiga persamaan dan K3 =P CO2 / P CO yang bergantung pada suhu. Pada 800 derajat C, campuran gas kesetimbangan mengandung sekitar 65% CO dan 35% CO2. Jika kandungan CO2 melebihi nilai ini dalam gas yang kontak dengan FeO dan besi padat pada suhu ini, besi yang ada cenderung teroksidasi kembali menjadi FeO. Oleh karena itu, untuk memaksa reaksi ini terjadi, diperlukan konsentrasi CO yang cukup besar dalam gas pada setiap langkah seperti yang ditunjukkan pada Gambar 1, dan tidak mungkin untuk mengubah CO sepenuhnya menjadi CO2 melalui reaksi. Gambar 1 menunjukkan diagram stabilitas untuk sistem Fe-C-O dan Fe-H-O. Kurva S dalam sistem Fe-C-O mewakili 'kehilangan larutan' atau Boudouard atau reaksi.
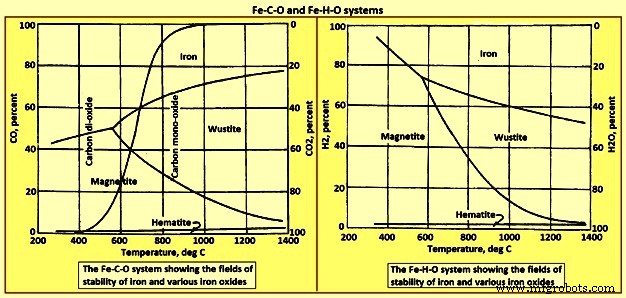
Gambar 1 Sistem Fe-C-O dan Fe-H-O
Karena hidrogen dalam bahan bakar tambahan dan uap air dari bahan bakar dan ledakan udara, gas yang meninggalkan tuyer juga dapat mengandung hingga 2% atau 3% hidrogen. Uap dapat ditambahkan ke semburan udara panas sebagai bantuan dalam mengendalikan tungku. Pengurangan uap oleh karbon dalam kokas dan bahan bakar berlangsung melalui reaksi keseluruhan H2O (g) + C (s) =CO (g) + H2 (g); delta H =131,3 kJ. Reaksi ini bersifat endoterm dimana oksidasi karbon oleh oksigen dalam ledakan menjadi CO dengan persamaan C (s) + 1/2 O (g) =CO (g); delta H =-110,5 kJ adalah eksotermik. Reduksi oksida besi oleh hidrogen juga berlangsung dengan langkah (i) 3Fe2O3 (s) + H2 (g) =2Fe3O4 (s) + H2O (g); delta H =-7.1 kJ, (ii) Fe3O4 (s) + H2 (g) =3FeO (s) + H2O (g); delta H 62,9 kJ, dan (iii) FeO(s) + H2 (g) =Fe(s) + H2O (g); delta H =30.2kJ.Suhu mempengaruhi kesetimbangan reaksi ini.
Reaksi perpindahan gas air CO2 (g) + H2 (g) =H2O (g) + CO (g); delta H =41,2 kJ dapat terjadi di antara berbagai spesies dalam fase gas untuk mendistribusikan kembali oksigen dan membawa spesies bantalan hidrogen dan gas bantalan karbon ke dalam kesetimbangan. Reaksi ini membutuhkan panas yang sangat sedikit dan konstanta kesetimbangan (P H2O.P CO) / (P H2.P CO2) adalah satu pada 825 derajat C. Gas-gas dalam tumpukan bereaksi dengan karbon dari kokas serta dengan oksida besi dalam muatan. Reaksi keseluruhan CO dan CO2 dengan karbon sebagai grafit adalah 'kehilangan larutan' atau reaksi Boudouard CO2 (g) + C (s) =2CO (g); delta H 172,4 kJ. Kesetimbangan reaksi bergeser kuat ke kanan pada suhu di atas 750 derajat C. Di bawah 600 derajat C kesetimbangan kuat ke kiri, mengakibatkan pengendapan karbon sebagai jelaga dalam beban tungku 2CO (g) =C (s ) + CO2 (g); delta H =-172.4. Kurva berbentuk 'S' yang mengarah dari kiri bawah ke tengah atas Gambar 1 mewakili keseimbangan. Gas yang suhu dan komposisinya menempatkannya di atas garis cenderung menyimpan karbon pada reaksi kedua, dan gas yang komposisi dan suhunya menempatkannya di bawah garis mengoksidasi karbon sesuai dengan reaksi pertama.
Efek utama dari reaksi larutan karbon pada suhu tinggi adalah pengurangan relatif panas yang dihasilkan pada tuyer di mana diperlukan dan peningkatan konsentrasi CO dalam gas di daerah tungku di atas 700 derajat C. Kondisi terakhir ini adalah sangat diinginkan karena meningkatkan volume gas dan membantu perpindahan panas. Perlu dicatat bahwa kombinasi reaksi kehilangan larutan dan reaksi FeO (s) + CO (g) =Fe (s) + CO2 (g); delta H -11 kJ sesuai dengan reduksi 'langsung' FeO oleh karbon yang diberikan oleh persamaan FeO (s) + C (s) =Fe (s) + CO (g); delta H =131,3 kJ. Jelaslah dari Gambar 1 bahwa gas-gas yang melewati cerobong biasanya tidak dapat berada dalam kesetimbangan dengan karbon dalam kokas dan oksida besi dalam beban yang menurun. Hubungan aktual antara komposisi gas dan suhu di tumpukan BF sangat bergantung pada praktik aktual yang digunakan.
Stabilitas relatif oksida
Stabilitas relatif berbagai oksida diplot terhadap suhu dalam diagram Ellingham (Gambar 2). Diagram Ellingham sangat berguna untuk memahami perilaku oksida dalam BF. Stabilitas relatif diukur dalam hal energi bebas pembentukan oksida. Semakin tinggi energi bebas negatif pembentukan oksida, semakin tinggi stabilitas oksida. Ini berarti bahwa oksida yang terletak di bagian atas diagram memiliki stabilitas yang relatif rendah, sedangkan oksida yang terletak di bagian bawah diagram memiliki stabilitas yang tinggi. Oksida yang terletak di tengah diagram memiliki stabilitas sedang. Oksida dengan stabilitas yang relatif rendah termasuk kalium oksida, natrium oksida, fosfor oksida dan oksida besi. Oksida dengan stabilitas sedang termasuk mangan oksida, kromium oksida, silika, dan titanium oksida. . Oksida dengan stabilitas tinggi termasuk alumina, magnesia, dan kapur.
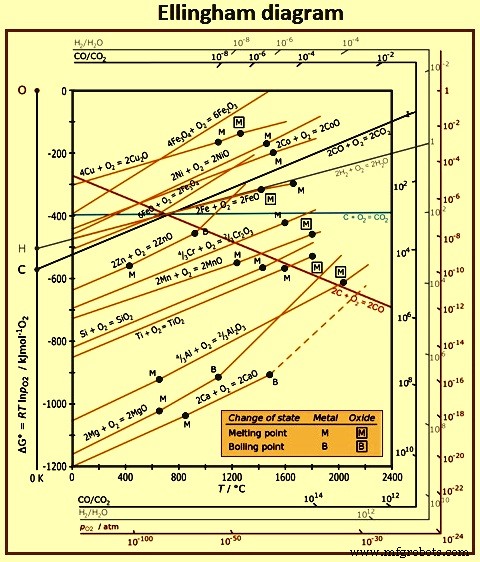
Gambar 2 Diagram Ellingham
Hal ini juga berguna untuk mempertimbangkan diagram ini dalam hal afinitas suatu elemen untuk oksigen. Misalnya, elemen yang terletak di bagian atas diagram memiliki afinitas rendah terhadap oksigen, sedangkan elemen yang terletak di bagian bawah diagram memiliki afinitas tinggi terhadap oksigen. Ini berarti bahwa oksida di bagian atas relatif mudah direduksi, sedangkan di bagian bawah sulit untuk direduksi. Hal ini ditunjukkan oleh garis untuk pembentukan oksida fosfor yang terletak di atas garis untuk pembentukan oksida besi pada suhu yang sesuai dengan yang ditemukan di perapian BF. Ini menyiratkan bahwa fosfor oksida memiliki stabilitas yang lebih rendah daripada oksida besi dan karenanya, karena kondisi reduksi dalam tungku cukup untuk mereduksi oksida besi, pada dasarnya semua fosfor yang memasuki tungku berakhir di logam panas. Di sisi lain, oksida stabil seperti alumina, magnesia, dan kapur tidak tereduksi dalam kondisi BF, dan berakhir dalam fase terak. Oksida dengan stabilitas sedang seperti mangan oksida, kromium oksida, silika, dan titanium oksida direduksi sebagian untuk menghasilkan beberapa mangan, kromium, silikon, dan titanium yang larut dalam logam panas, sedangkan oksida tak tereduksi yang tersisa merupakan bagian dari terak.
Diagram Ellingham dibangun atas dasar bahwa unsur murni pada unit aktivitas bereaksi dengan satu mol gas oksigen untuk membentuk oksida murni pada unit aktivitas. Istilah 'aktivitas' termodinamika adalah konsep yang sangat berguna untuk membahas perilaku unsur-unsur yang larut dalam besi cair, atau oksida yang dilarutkan dalam terak cair. Misalnya, ketika konsentrasi kecil unsur-unsur seperti oksigen atau belerang dilarutkan dalam baja cair, aktivitasnya sering dapat dianggap sama dengan konsentrasinya dalam persen. Namun, dengan adanya unsur-unsur lain dalam konsentrasi tinggi, misalnya karbon dalam logam panas, aktivitas belerang lebih tinggi dari konsentrasinya, sedangkan aktivitas oksigen lebih kecil dari konsentrasinya. Dalam kasus seperti itu, penting untuk membedakan antara aktivitas dan konsentrasi. · Konsentrasi suatu komponen dalam larutan adalah ukuran seberapa banyak komponen yang ada. · Aktivitas komponen dalam solusi adalah ukuran bagaimana komponen sebenarnya berperilaku.
Semua garis pada diagram Ellingham kecuali yang melibatkan karbon, memiliki kemiringan positif, yang menunjukkan bahwa stabilitas oksida menurun dengan meningkatnya suhu. Garis-garis oksida kalium oksida, natrium oksida, magnesium, dan kapur, masing-masing menunjukkan peningkatan kemiringan pada suhu yang sesuai dengan titik didih masing-masing logam. Garis untuk pembentukan CO2 dari karbon dan oksigen memiliki kemiringan hampir nol yang menunjukkan sedikit perubahan stabilitas dengan meningkatnya suhu, sedangkan untuk CO memiliki kemiringan negatif yang kuat yang berarti bahwa stabilitas CO sebenarnya meningkat dengan meningkatnya suhu. Garis untuk dua oksida karbon bersilangan pada sekitar 700 derajat C. Di atas suhu ini, CO lebih stabil daripada CO2 sedangkan pada suhu yang lebih rendah, CO2 lebih stabil daripada CO.
Reaksi karbon-oksigen
Ledakan udara pra-pemanasan yang disuntikkan melalui tuyer pada suhu sekitar 1.000 derajat C hingga 1.200 derajat C dan tekanan 0,2 MPa hingga 0,3 MPa, menghasilkan zona reaksi berbentuk buah pir di depan setiap tuyere. Suhu di wilayah ini adalah sekitar 2.000 derajat C dan reaksi cepat pertama terjadi antara kelebihan oksigen dan kokas untuk menghasilkan CO2. Ini adalah reaksi eksotermik (C + O2 =CO2). Segera di luar zona ini, tidak ada lagi oksigen bebas yang tersedia dan CO2 bereaksi dengan kokas berlebih menghasilkan CO (CO2 + C =2CO). Ini dikenal sebagai reaksi Boudouard dan bersifat endotermik. Penggabungan kedua reaksi ini menghasilkan reaksi pembakaran parsial karbon dengan oksigen untuk menghasilkan CO. (2C + O2 =2CO). Panas yang dihasilkan dalam pembentukan satu mol CO2 adalah sekitar tiga setengah kali lipat dari pembentukan satu mol CO dan satu ukuran efisiensi BF adalah derajat konversi karbon dalam kokas menjadi CO2.
Di bawah 700 derajat C, CO2 lebih stabil daripada CO dan reaksi kedua berlangsung ke kiri (2CO =C + CO2). Reaksi ini sering disebut sebagai deposisi karbon. Di atas 700 derajat C, CO lebih stabil daripada CO2 dan reaksi kedua berlangsung ke kanan. Reaksi ini kadang-kadang disebut reaksi kehilangan larutan karbon dan dalam pengertian ini menyiratkan perilaku negatif. Di sisi lain, reaksi mewakili regenerasi gas pereduksi dalam daerah tungku di atas 700 derajat C. Ini adalah salah satu fungsi penting kokas dalam BF dan sangat diinginkan karena meningkatkan volume gas dan membantu panas. transfer. Namun, reaksi ini bersifat endotermik dan ketika terjadi di dalam zona tuyere, reaksi ini menciptakan efek pendinginan di lokasi yang memerlukan suhu tinggi.
Pengaruh suhu pada reaksi kesetimbangan antara kokas dan campuran gas yang mengandung CO dan CO2 pada tekanan 0,1 MPa dan juga 0,3 MPa, yang lebih khas dari praktik BF modern, ditunjukkan pada Gambar 3. Di sebelah kanan grafik, CO lebih stabil daripada CO2, sedangkan pada suhu yang lebih rendah, di sebelah kiri grafik, CO2 lebih stabil daripada CO. Dari gambar ini jelas bahwa di atas 1.000 derajat C, persentase CO2 dalam kesetimbangan dengan kokas pada dasarnya nol. Di sisi lain, pada suhu di bawah 400 derajat C, konsentrasi CO kecil. Oleh karena itu, saat suhu menurun antara 1.000 derajat C hingga 400 derajat C, stabilitas CO menurun sementara stabilitas CO2 meningkat dan tekanan parsial kedua gas dalam kesetimbangan dengan kokas cukup besar.

Gbr 3 Pengaruh suhu terhadap kandungan CO campuran gas CO / CO2 dalam kesetimbangan dengan karbon
Gas yang meninggalkan bagian atas tungku biasanya pada suhu sekitar 200 derajat C dan jika kesetimbangan dicapai dengan kokas, rasio CO terhadap CO2 adalah sekitar 10 pangkat -5. Faktanya, rasio biasanya antara 1 dan 3, yaitu gas sangat jauh lebih tereduksi daripada yang diperkirakan dari pertimbangan keseimbangan dan penggunaan penuh dari potensi reduksi gas tidak dilakukan. Ini menyiratkan bahwa tingkat kokas melebihi persyaratan teoritis. Kurangnya keseimbangan antara gas dan kokas dapat dikaitkan terutama dengan kecepatan gas yang tinggi di tumpukan. Waktu retensi gas dalam tungku hanya sekitar 10 detik, dan kecepatan yang sangat tinggi dapat terjadi, terutama di daerah yang kaya akan kokas. Faktor lainnya adalah bahwa suhu gas turun sekitar 1.800 derajat C saat naik melalui tungku sehingga hanya ada sedikit kesempatan untuk mempertahankan keseimbangan.
Reaksi pengendapan karbon
Karena kandungan CO dari gas di dalam tumpukan BF pada suhu di bawah 1.000 derajat C jauh lebih tinggi daripada yang diperlukan, ada kekuatan pendorong untuk pengendapan karbon, atau reaksi jelaga untuk melanjutkan. Gaya penggerak ini sangat kuat antara 500 derajat C dan 700 derajat C. Gas dengan suhu dan komposisi di atas garis pada Gambar 3 cenderung menyimpan karbon melalui reaksi 2CO =C + CO2, dan gas dengan komposisi dan suhu di bawah suhu garis mengoksidasi karbon sesuai dengan reaksi CO2 + C =2CO. Untungnya reaksi deposisi karbon lambat dan keseimbangan tidak pernah tercapai, jika tidak, penyumbatan serius pada ruang di dalam beban di bagian atas tumpukan dapat terjadi.
Hal ini pada gilirannya dapat menyebabkan aliran yang tidak teratur dari gas pereduksi dan penurunan beban yang tidak merata. Bahkan untuk reaksi parsial, diperlukan permukaan katalitik yang sesuai, di mana karbon dapat berinti dan tumbuh. Partikel besi, bijih besi tereduksi parsial, dan karbida besi semuanya telah diusulkan sebagai katalis yang mungkin. Reaksi tampaknya ditingkatkan oleh hidrogen dan uap air sementara senyawa nitrogen dan belerang, misalnya, amonia, hidrogen sulfida dan karbon di-sulfida bertindak sebagai inhibitor. Seng oksida dan senyawa alkali menentang efek penghambatan belerang, dan meskipun konsentrasi senyawa ini dalam tungku biasanya kecil, mereka menguap pada suhu tinggi di perapian dan mengembun lagi di daerah yang lebih dingin dari tumpukan. Efek kumulatif adalah bahwa senyawa tersebut dapat mengimbangi pengaruh belerang. Karbon yang diendapkan oleh reaksi dalam bentuk yang sangat halus dan beberapa dapat ditampung di dalam pori-pori partikel bijih besi dan disimpan kembali ke tumpukan lagi. Hal ini dapat mempengaruhi proses pengurangan dalam beberapa cara.
Karena sifat aktif dari karbon dan hubungannya yang erat dengan bijih, reduksi oleh karbon padat dapat terjadi pada suhu yang lebih rendah daripada yang dibutuhkan untuk reduksi dengan kokas, terutama karena kokas tidak dapat menembus pori-pori dan reduksi hanya dapat terjadi pada titik-titik kontak antar partikel padat. Laju reduksi tersebut tergantung pada laju difusi oksigen dari bagian dalam partikel ke titik kontak. Di bagian atas tungku, reduksi dengan kokas dapat diabaikan, dibandingkan dengan reduksi gas. Ini menjadi cukup besar hanya di atas sekitar 1.000 derajat C, ketika reaksi gas terhambat oleh pembentukan terak. Sebaliknya, reduksi oleh karbon yang diendapkan dapat terjadi pada suhu serendah 800 derajat C.
Pembentukan CO selama reaksi di dalam pori-pori cenderung membuka celah yang dalam di dalam partikel, sehingga meningkatkan area kontak gas-padat, dan meningkatkan efisiensi reduksi gas. Ketika CO2 diproduksi di dalam pori-pori partikel melalui reaksi reduksi gas, ia dapat dengan cepat diregenerasi menjadi CO melalui reaksi dengan karbon di dalam pori-pori, sehingga memungkinkan reaksi berlanjut.
Sayangnya, reaksi deposisi karbon juga dapat memiliki efek samping tertentu. Reaksi dapat menyebabkan pemisahan refraktori dengan pengendapan pada titik besi aktif, di daerah di mana suhu sekitar 500 derajat C hingga 550 derajat C, misalnya di kulit terluar di tingkat yang lebih rendah di tumpukan, atau di dalam kulit bagian dalam di bagian atas. tingkat. Jika berlebihan, deposisi karbon dapat menyebabkan pelet bijih atau sinter hancur menjadi bubuk dan ini dapat menyebabkan aliran gas yang tidak teratur dan penurunan beban yang tidak merata.
Karena reaksi pengendapan karbon bersifat eksotermis, suhu gas keluar meningkat. Meskipun efek keseluruhan dari reaksi deposisi karbon dapat diperdebatkan, fakta-fakta tertentu tetap ada. Reaksi tersebut menurunkan rasio CO / CO2 dari gas yang keluar. Reaksi mensirkulasikan kembali sejumlah karbon, yang sebaliknya akan dilakukan dari tungku, sehingga meningkatkan waktu yang tersedia untuk reaksi dengan karbon dan meningkatkan efisiensi kimia dari proses reduksi.
Reduksi oksida besi
Reduksi oksida besi oleh CO dapat diwakili oleh reaksi (i) 3Fe2O3 + CO =2Fe3O4 + CO2, (ii) Fe3O4 + CO =3FeO + CO2, dan (iii) FeO + CO =Fe + CO2. Reaksi-reaksi ini terjadi pada suhu yang semakin tinggi dan seperti yang ditunjukkan pada Gambar 1, dengan persentase CO yang semakin tinggi. Ini berarti bahwa reaksi (i) dan (ii), yang relatif mudah dicapai, dapat berlangsung di daerah atas perapian. Reaksi (iii) yang memerlukan penghilangan jumlah oksigen terakhir dari besi, sebenarnya adalah yang paling sulit dicapai dan karenanya berlangsung lebih jauh ke bawah tungku di mana suhu lebih tinggi dan kandungan CO dari gas pereduksi lebih tinggi. Di bawah 570 derajat C, fase wustit non-stoikiometrik (FexO) tidak stabil dan dimungkinkan untuk mereduksi magnetit secara langsung menjadi besi.
Pada suhu tertentu, ada kandungan CO minimum dalam campuran gas yang diperlukan untuk reduksi oksida tertentu. Ini berarti bahwa tidak mungkin seluruh CO dalam gas diubah menjadi CO2 jika reaksi reduksi dilanjutkan. Sebagai contoh, pada 800 derajat C campuran gas kesetimbangan yang kontak dengan FeO dan besi padat mengandung sekitar 65% CO dan 35% CO2. Jika kandungan CO2 gas melebihi nilai ini pada suhu ini, besi cenderung teroksidasi kembali menjadi FeO. Oleh karena itu, agar reaksi ini terjadi, harus ada konsentrasi minimum CO dalam gas pada setiap langkah seperti yang ditunjukkan pada Gambar 1, dan tidak mungkin untuk mengubah CO sepenuhnya menjadi CO2 dengan reaksi ini. Untungnya pada suhu tersebut CO2 yang dihasilkan oleh reaksi reduksi tidak stabil dengan adanya coke dan CO diregenerasi berdasarkan reaksi CO2 + C =2CO sehingga reaksi reduksi dapat berlanjut. Perlu dicatat bahwa kombinasi reaksi ini dengan reaksi (iii) sesuai dengan reduksi 'langsung' FeO oleh karbon (FeO + C =Fe + CO), dan ini adalah reaksi endotermik yang kuat.
Pengurangan oksida besi juga dapat terjadi oleh hidrogen yang dihasilkan oleh pembakaran parsial bahan bakar tambahan yang disuntikkan melalui tuyer untuk menghasilkan dua gas pereduksi, CO dan hidrogen. Hidrogen juga diproduksi ketika uap ditambahkan ke ledakan sebagai bantuan dalam mengendalikan tungku. Sementara oksidasi karbon oleh oksigen dalam ledakan udara panas untuk membentuk CO adalah eksotermik, reduksi uap air oleh kokas untuk membentuk CO dan hidrogen (H2O + C =CO + H2) sangat endotermik.
Reduksi oksida besi oleh hidrogen kembali berlangsung secara berurutan. Reaksi yang terjadi adalah (i) 3Fe2O3 + H2 =2Fe3O4 + H2O, (ii) FeO + H2 =Fe + H2O, dan (iii) Fe3O4 + H2 =3FeO + H2O. Pengaruh suhu pada kesetimbangan reaksi ini ditunjukkan pada Gambar 1. Sementara reaksi (i) sedikit eksotermik, reaksi (ii) dan (iii) adalah endotermik. Kehadiran hidrogen, yang karena ukurannya yang kecil memiliki difusivitas tinggi, secara nyata mengurangi densitas dan viskositas gas BF dan, terutama pada suhu tinggi, meningkatkan pengurangan bahan baku yang dapat direduksi rendah. Reaksi perpindahan gas air (CO2 + H2 =H2O =CO) dapat terjadi antara komponen yang berbeda dalam fase gas untuk membawa gas bantalan hidrogen dan bantalan karbon ke dalam kesetimbangan.
Jelas dari Gambar 1 bahwa gas yang melewati tungku tidak dapat berada dalam kesetimbangan dengan karbon dalam kokas dan pada saat yang sama dalam kesetimbangan dengan oksida besi dalam beban yang menurun. Di atas sekitar 800 C reaksi gas dengan karbon lebih cepat daripada dengan oksida dan kesetimbangan antara kokas dan fase gas mungkin mendekati cukup dekat. Pengukuran suhu dan komposisi gas dalam tungku yang beroperasi menunjukkan bahwa mereka cenderung berada di antara garis CO/CO2-C dan garis FeO/Fe di atas 800 derajat C, memotong garis FeO/Fe antara 600 derajat C dan 800 derajat C dan kemudian tetap pada atau tepat di atas garis Fe3O4/Fe. Pada suhu di bawah 600 derajat C, aliran gas yang sangat cepat memungkinkan sedikit waktu untuk bereaksi dengan padatan dan kandungan CO dari gas jauh melebihi keseimbangan dengan kokas.
Jika oksida besi secara kimiawi terkait dengan oksida lain, aktivitasnya dalam BF menurun. Ini berarti oksida besi lebih sulit untuk direduksi dan rasio CO/CO2 yang dibutuhkan lebih tinggi daripada yang biasanya dipertimbangkan di sini. Misalnya dengan silikat besi, rasio CO /CO2 minimum yang diperlukan untuk reduksi pada 700 derajat C harus ditingkatkan dari sekitar 1,5 menjadi sekitar 22, yaitu dari sekitar 60% CO menjadi hampir 96% CO pada basis gas karbon. Karena oksida gabungan lebih sulit untuk direduksi, suhu yang lebih tinggi diperlukan untuk reduksi dan karenanya jumlah reduksi yang dicapai dengan CO sebelum pembentukan terak terjadi berkurang. Ini menyiratkan peningkatan laju kokas karena jumlah pengurangan yang dibutuhkan di bagian bawah tungku meningkat.
Reaksi di perapian dan perapian
Reduksi oksida lain – Pengurangan oksida yang lebih stabil daripada oksida besi seperti oksida mangan dan silika tidak terjadi di BF jika produknya adalah logam murni karena reaksi MnO + CO =Mn + CO2, pada kesetimbangan, memiliki persentase CO yang sangat dekat sampai 100%. Artinya, efisiensi reduksi sangat rendah dan sejumlah besar gas diperlukan untuk jumlah mangan yang sangat kecil tereduksi. Situasi dengan silika bahkan lebih ekstrim karena merupakan oksida yang sangat stabil. Namun dengan melarutkan mangan dan silikon dalam besi, maka reaksi MnO + CO =Mn (larut dalam besi) + CO2, dan SiO2 + 2CO =Si (larut dalam besi) + 2CO2 agak digeser ke kanan sehingga terjadi distribusi mangan dan silikon antara logam dan terak yang merupakan fungsi dari komposisi terak dan suhu. Karena reduksi kedua elemen ini bersifat endotermik, jumlah masing-masing dalam logam panas meningkat dengan suhu dan tingkat reaksi sampai tingkat tertentu dikendalikan dengan mengendalikan suhu di perapian tungku. Yang lebih penting adalah kenyataan bahwa CO2 yang dihasilkan oleh reaksi ini akan bereaksi dengan reaksi Boudouard dan menyebabkan peningkatan konsumsi kokas.
Jumlah mangan yang dikurangi jelas juga tergantung pada jumlah bijih yang diisi. Bijih dengan mangan hingga 2% memberikan kandungan mangan yang jauh lebih tinggi daripada normal dalam logam panas dengan konsekuensi tingkat kokas yang lebih tinggi per ton logam panas yang dihasilkan. 'Ayunan' silikon yang disebabkan oleh beban tungku yang tidak menentu atau oleh variasi suhu juga dapat memiliki efek serius lainnya, karena silikon yang direduksi menjadi logam panas akan dihilangkan dari terak, sehingga meningkatkan rasio kebasaan dan mengubah titik leleh dan fluiditas terak terkadang secara dramatis.
Efek Pembentukan Silikon Monoksida (SiO) – For several years it was considered that silica and manganese oxide are reduced directly from the slag by reaction with carbon in iron according to the reactions (i) SiO2 (slag) + 2C =Si + 2CO (g), and MnO (slag) + C =Mn + CO (g). It was thought that liquid iron droplets picked up silicon as they passed through the slag phase and on into the hearth. Various studies however, have shed new light on these reactions and also those involving sulphur. Several laboratory studies together with plant data have shown that at the temperature of the combustion zone, around 2,000 deg C, SiO gas is produced during the combustion of coke by the reaction SiO2 (coke ash) + CO =SiO (gas) + CO2. Combining this equation with the reaction for coke oxidation [CO2 + C (coke) =2CO] yields the overall reaction SiO2 (coke ash) + C (coke) =SiO (gas) + CO. While the presence of FeO in slag is likely to make SiO formation from slag very difficult, an additional source of silica is to be reduced silica-rich slag adhering to the coke particles. Following these reactions, silicon is transferred to iron droplets by reaction with SiO in the gas phase [SiO (gas) + C =Si + CO]. As iron droplets containing silicon pass through the slag layer, some of the silicon is oxidized by iron oxide and manganese oxide, and taken up by the slag [2FeO (slag) + Si =SiO2 (slag) + 2Fe, 2 MnO (slag) + Si =SiO2 (slag) + 2Mn.
Reduction of phosphorus – It is expressed by the reaction P2O5 + 5C =2P + 5CO; delta H =+995,792 kJ/kmol. The final reduction of phosphorus also takes place only at very high temperatures. However, unlike manganese and silicon the phosphorus is essentially completely reduced. For this reason, virtually all of the phosphorus in the charge is dissolved in the hot metal. The only means of controlling the phosphorus content of the hot metal is by limiting the quantity charged to the furnace.
Behaviour of sulphur – Sulphur is a troublesome element in BF operations since hot metal for steelmaking is to be low in sulphur. Levels of 0.035 % to 0.02 % are normal. The reaction by which sulphur is removed from liquid iron (S ) into the slag (S) is frequently represented by the reaction S + (CaO) + C =(CaS) + CO (g) Where sulphur (S ) and carbon (C ) in the metal react with lime (CaO) dissolved in the slag to form calcium sulphide in the slag and CO gas. The distribution of sulphur between slag and metal, (S) /S , is strongly influenced by a number of factors as described here. Increasing the basicity of the slag (CaO / SiO2 ratio) tends to raise the thermodynamic activity of CaO in the slag which pushes reaction to the right. An increased oxygen potential in the system pushes the reaction to the left. This is shown by rewriting the reaction S + (CaO) =(CaS) + O . This effect is very strong, and the presence of even small concentrations of FeO in the slag seriously limits the sulphur ratio (S) / S . Fortunately both silicon and carbon raise the thermodynamic activity of sulphur in hot metal by 5 times to 7 times. Accordingly, sulphur in hot metal is 5 times to 7 times easier to remove than it is from liquid steel which contains relatively little carbon and silicon.
Assuming sulphur in coke ash is present as CaS, the reaction which can occur with SiO in the combustion zone to form volatile SiS is CaS (coke ash) + SiO (gas) =CaO + SiS (gas). To a lesser extent, some CS gas can form by the reaction CaS (coke ash) + CO =CaO + CS (gas).
Sulphur transfer from these volatile species to liquid iron droplets then takes place within the bosh zone. A study has shown that when iron droplets containing silicon and sulphur are allowed to fall through the liquid slag, in the absence of MnO, the silicon content of the hot metal actually increases, and there is no transfer of sulphur. In the presence of MnO, silicon is removed from the metal by reaction and manganese transfers from slag to metal together with sulphur transfer from metal to slag take place. Based on the various results available, the sequence of reactions in the bosh and hearth are (i) the formation of SiO and SiS in the combustion zone, (ii) the transfer of silicon and sulphur to metal and slag droplets in the bosh, (iii) the oxidation of silicon by FeO and MnO in the slag as the iron droplets pass though the slag layer, and (iv) the desulphurization of metal droplets as they pass through the slag layer.
The sulphur distribution ratios found in the BF normally varies between 20 and 120. On the other hand experiments have shown that when metal and slag samples from BF are remelted in graphite crucibles at 0.1 MPa CO, the distribution ratio increases to between 120 and 220, depending on the slag basicity. This suggests that the oxygen potential of the system is higher than is to be expected for C-CO equilibrium in the furnace hearth. Hence, while thermodynamic conditions favour sulphur removal from the hot metal within the BF, kinetic considerations imply that the reaction can be more readily accomplished outside the furnace by external desulphurization.
Reaction of less abundant elements
In addition to the elements (that is Fe, P, Mn, Si, Al, Ca, Mg and S) which are normally considered in reporting the chemical composition of an iron-bearing material, there are a number of less abundant elements which undergo chemical reactions in the BF. Some of these can cause considerable operating difficulty and some can contaminate the product and make it unsuitable for certain steelmaking applications. The source of these elements is not only from natural iron ores, but also from waste materials such as scrap, steelmaking dust, and grindings etc., which are recycled through the BF. Some of the more important of these elements are arsenic, barium, chlorine, chromium, cobalt, copper, fluorine, lead, molybdenum, nickel, potassium, sodium, tin, titanium, vanadium and zinc.
Alkalis and zinc – Sodium, potassium and zinc, frequently called the ‘rogue elements’, can cause serious operating problems in the BF and are to be monitored and carefully controlled if stable conditions are to be maintained. The alkali metals enter the BF as the constituents of the gangue in the ore and also as a part of the coke ash, normally as silicates. In the stack of the furnace, the silicates react as per the equations (i) K2SiO3 + CO =2K + SiO2 + CO2 and (ii) Na2SiO3 + CO =2Na + SiO2 + CO2.
In the BF, the potassium reaction can take place above 500 deg C, while the sodium reaction occurs at around 600 deg C. At temperatures of around 900 deg C, the alkali metals are above their boiling point so they join the gas phase. However, as these gases start to rise up the furnace, the metal becomes unstable with respect to other compounds which can form and cyanides, oxides, and carbonates all start to precipitate from the gas phase as very fine fumes or mists, since the cyanides are liquid over a wide temperature range. These fine particles of solid and liquid can deposit on the iron ore particles, the coke, and the furnace wall, with some, of course, being swept out with the BF gas and being captured in the dust catching system. Particularly the liquid alkali compounds can penetrate the brick lining of the furnace and cause serious deterioration and spalling. As well, these compounds can build upon the wall and cause scaffolding, hanging, and slipping.
The alkalis which land on the iron and coke are carried to the lower part of the furnace. There, they are again reduced to the metal which rises up the stack as a gas, forms the same alkali compounds, and repeats the cycle, joining new material in the process. The reduction needs carbon, increasing the coke rate, and cooling the furnace, and the recycling material can build up to the point where it degrades the coke in the furnace, causing it to break into small pieces and increasing the reactivity of the coke to CO2.
This increased reactivity can again reduce the temperature of the furnace and decrease the heat efficiency of the whole system. The high concentration of alkalis in the furnace also affects the strength and reduction characteristics of the iron bearing materials, causing dramatic swelling and catalyzing carbon deposition on the pellets. These deleterious reactions with both the coke and the ore can have serious impacts on the gas permeability in the furnace and on the stability of the BF operation.
Fortunately, the alkali oxides are very basic oxides and can be fluxed with SiO2 in acid slags and removed from the furnace. Normally, decreasing the slag basicity can carry increasing quantities of alkali away in the slag. This is in direct contrast to sulphur removal, where increasing the slag basicity increases the sulphur removal. When majority of desulphurizing takes place in the BF, there is a conflict between the attainment of low sulphur and removal of alkalis and the basicity of the furnace is carefully controlled to balance both the problems. With external desulphurization, this is no longer a problem and the furnace can normally be burdened to minimize alkali attack.
Zinc normally originates in steelmaking off-gas dust from furnaces using galvanized scrap which in some fashion has been recycled to the BF. Occasionally, the zinc content of iron ores or coal ash can be also a considerable source. Behaving not unlike sodium, zinc is reduced from the oxide or ferrite at around 600 deg C, forms a vapour which subsequently forms oxides or carbonates that can react with the sidewalls or be carried down the furnace on coke or ore to be reduced and further cycled, consuming coke at each turn. Zinc which escapes as a fume in the gas stream, enters the BF filter-cake, making it unsuitable to recycle if present in a high enough percentage. Unlike the alkalis, zinc is not captured to any extent in the slag and can only effectively be removed by decreasing the input and allowing the recycling vapour to slowly leave through the gas phase.
Clearly, the best protection against alkali metals and zinc is to ensure that the absolute minimum is part of the BF feed. Because of the tendencies of these elements to circulate in the furnace, they are unseen and unknown consumers of coke and cause refractory, ore and coke problems. Unfortunately, the symptoms of the problem are not always evident until the problem is of fairly major proportions and then needs fairly drastic measures, such as eliminating certain feed materials, to affect a solution.
Lead and titanium – Lead is seldom a problem in the BF but occasionally enough can enter a BF through the ore or sinter to cause a problem. Lead is very easily reduced in the iron BF and falls to the bottom of the hearth which normally has a chilled hot metal layer which protects the hearth refractories. Lead has virtually no solubility in the hot metal so it forms a low melting point liquid pool on which the hot metal floats, and hence promotes more rapid attack on the hearth. In certain furnaces where this problem is known to occur, a second tap-hole, deeper than the iron notch, can be used to periodically tap the lead.
Titanium is an even more stable oxide than silica but in the BF it can form extremely stable carbides and nitrides. The titanium compounds, if present in small quantities can be effective in forming a light protective layer on the hearth surfaces and prolong the life of the hearth. For this reason, titani-ferrous ores are added judiciously to sinter mixes. However, at high concentrations, these same compounds can stiffen the slag while building up a heavy hearth layer, reducing the hearth capacity of the furnace. As with zinc, the best solution is to reduce the input and slowly eliminate the titanium from the furnace.
Arsenic – Arsenic is found in a number of iron ores. The behaviour of arsenic is very much like that of phosphorus, in that it is almost completely reduced and dissolves in the hot metal. It increases the fluidity of the hot metal and hence, it appears to increase the wear of refractories. It is not completely removed during the steel refining process and imparts brittleness to the finished steel.
Barium – Barium is chemically similar to calcium and occurs as a very basic oxide in some iron and manganese ores. It is not reduced in the BF but becomes part of the slag, increasing the slag basicity. It can cause difficulty in controlling the metal composition if the operator is not aware of its presence.
Chlorine – Chlorine occurs as alkali chlorides in several iron ores and as a contaminating compound in ores processed with sea water. Chlorine is also present in some coals used for injection. In the high temperature zone of the BF, these compounds are volatized and as they rise toward the top of the furnace they condense around cooling plates and cause corrosion. They can also condense in uptakes and down-comers where they form accretions which can eventually restrict the passage of the top gas, or react to form HCl (hydrochloric) acid and attack the gas cleaning system.
Chromium – Chromium is found in some ores and is reduced to a certain extent depending on the basicity of the slag and the operating temperature. Normally, around 50 % to 60 % of the chromium is reduced into the hot metal.
Cobalt, copper, and nickel – Cobalt, copper, and nickel occurs in several different ores. They are also present in iron-bearing tailings from the copper industry which are sometimes sintered and used in the BF to recover the iron. All three of these elements are reduced almost completely into the hot metal and are not oxidized in the steel refining process. As a result, in operations which produce steel which is to meet stringent ductility specifications, such ores cannot be used.
Fluorine – Fluorine compounds are found in several ores and behave somewhat like chlorine compounds. The ability of HF (hydrofluoric) acid to attack the gas cleaning system is well known.
Molybdenum and tungsten – Molybdenum and tungsten occur very rarely and only in such minute quantities that they can be ignored. If any compounds of these elements are present in the BF, they are at least 90 % reduced into the hot metal.
Tin – Tin is an element which enters the BF mostly by way of recycled materials such as scrap or sintered dusts. It is almost entirely reduced and dissolves in the hot metal.
Vanadium – Vanadium occurs and behaves in a manner somewhat similar to chromium. Around 50 % of the vanadium in the burden is reduced and enters the hot metal.
Selenium and tellurium – Selenium and tellurium, though somewhat rare, can be present in some raw materials. In their reactions they are similar to sulphur but possess an even greater tendency to remain with the metal.
Fluxes
Limestone charged to the furnace is calcined by the reaction CaCO3(s) =CaO(s) + CO2 (g); delta H =177.8 kJ at around 800 deg C. Magnesium carbonate in the dolomite of the charge is calcined by a similar reaction MgCO3(s) =MgO(s) + CO2(g); delta H =167.4 kJ at 50 deg C to 100 deg C lower temperatures. These reactions result in several undesirable conditions in the furnace. The first is that they need considerable heat and the second is that CO2 is released in the furnace. The additional CO2 raises the oxygen potential of the gases which inhibits the final step in the reduction of the iron ore, i.e., FeO to Fe. It also favours ‘solution’ of carbon from the coke by the equation CO2 (g) + C(s) =2CO (g).
A considerable improvement in the furnace operations is achieved when ‘self-fluxing’ agglomerates of iron-ore concentrates are the principal iron-bearing charge to the furnace. Limestone and dolomite can be added to the feed of sintering machines and pelletizing furnaces. When the sinter is fired and the pellets are indurated, the fluxes are calcined and reacted with iron oxides to form calcium-ferrites and other more complex compounds. The CaO and MgO carried into the BF by these agglomerates are then free of CO2.
Slags
The fundamentals of the BF slag are complex. At around 40 %, oxygen is the largest single element in slag. Slag is, hence, an oxide system and ionic in nature. The oxide system which forms the basis for BF slags is the lime-silica-alumina (CaO-SiO2-Al2O3) system modified due to the presence of certain percent of MgO in the slag. Fig 4 show phase diagram of CaO-Al2O3-SiO2-10 % MgO system. Due to the nature of the BF process, slag formation is a multi-step process involving considerable changes in composition and temperature. The four primary components of slags form numerous compounds which result in a wide range of chemical and physical properties. The lesser components of slag are of particular interest with respect for hot metal chemistry and furnace control, and add to the complexity of the physico-chemical properties of the slag.
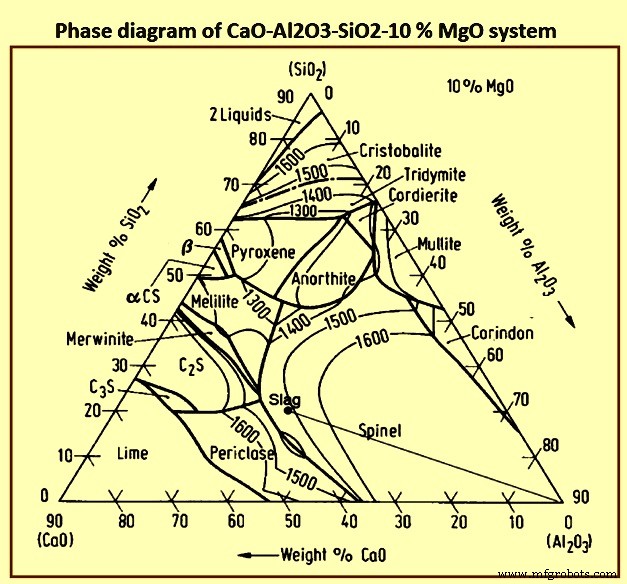
Fig 4 Phase diagram of CaO-Al2O3-SiO2-10 % MgO system
Slags with compositions in the region of 40 % SiO2, 48 % CaO, and 12 % A12O3 have low melting points, i.e., 1,300 deg C, and are appropriate for the control of sulphur and silicon in the hot metal. Frequently 6 % to 10 % MgO is used in place of an equivalent quantity of CaO to lower the viscosity of the slag. Small quantities of MnO, FeO, Na2O, and K2O etc. help to lower the melting point of the slag.
Essentially there are two slags in the furnace. The first is the ‘primary, or bosh, or early’ slag which is formed principally from the gangue constituents in the ores and agglomerates and CaO and MgO from the calcined fluxes, or the self-fluxing portions of the agglomerates. This slag is relatively basic compared to the final slag and contains some iron oxide. The ‘final or hearth’ slag is formed by the union of the early slag with constituents of the coke ash which are freed from the coke when it is burned before the tuyeres. This final slag continues to have its composition modified as it passes down into the hearth and mixes with liquid iron which also is flowing down into the crucible. There is an adjustment in the silica content of the slag, iron oxide can be reduced from it and it can absorb sulphur from the coke and liquid iron.
The formation of slags in the slag-formation zone is very furnace specific due to the impact of burden properties and furnace operation. The slag formation zone begins at the cohesive zone, where softening of burden begins, and continues down to below the tuyere elevation. The slag formation zone hence includes the cohesive zone, active coke zone, deadman, and raceway. The slag formed in the upper part of the slag formation zone is called the ‘bosh’ or ‘primary’ slag, and the slag leaving the zone at the bottom is the ‘hearth’ slag. The Primary slag is normally assumed to be made up of all burden slag components including the iron oxides not reduced in the granular zone, but does not include the ash from the coke or injected coal. The slag composition changes as it descends in the furnace due to the absorption of the coke ash and coal ash, sulphur and silicon from the gas, and the reduction of the iron oxide. The temperature of the slag increases of the order of 500 deg C as it descends to the tuyere elevation. These changes in composition and temperature can considerably impact the physical properties of the slag, specifically the liquidus temperature and the viscosity.
The slag produced in slag formation zone collects in the slag layer in the hearth zone, filling the voids in the hearth coke and ‘floating’ on the hot metal layer. The hot metal passes through the slag layer to reach the hot metal layer. The high surface area between the hot metal and slag as the hot metal passes through the slag layer enhances the kinetics of the chemical reactions. These reactions result in considerable changes in the hot metal chemistry. In particular the (Si) and (S) contents prior to entering the slag layer are much higher than those in the hot metal layer.