Granulasi Kering dari Blast Furnace Slag untuk Pemulihan Energi
Granulasi Kering Terak Tungku Ledakan untuk Pemulihan Energi
Sekitar 300 kg terak cair diproduksi sebagai produk sampingan saat memproduksi satu ton logam panas dalam tanur tinggi (BF). Terak ini berada pada suhu sekitar 1500 derajat C dan memiliki panas sensibel sekitar 400 M Cal per ton. BF slag kaya akan CaO, SiO2, Al2O3, dan MgO yang mirip dengan komponen semen Portland.
Ketika terak BF cair suhu tinggi didinginkan cukup cepat maka terak memiliki persentase fase kaca yang besar dengan aktivitas sementasi yang tinggi dan karenanya dapat digunakan sebagai produk bernilai lebih tinggi, terutama untuk substitusi semen Portland. Ini juga merupakan cara yang baik untuk mengurangi emisi CO2 karena pabrik semen juga menghasilkan CO2 dalam jumlah besar.
Untuk mendapatkan fasa glassy pada BF slag, cairan BF slag dilakukan proses granulasi air. Saat ini pendinginan cepat terak cair di pabrik granulasi terak air tertutup adalah proses canggih. Pendinginan cepat terak BF cair di dalam air mencegah kristalisasi terak dan memecah terak menjadi partikel kecil oleh tekanan termal. Terak BF cair membeku dalam butiran amorf, yang disebut terak BF butiran. Tingkat non kristalisasi terak BF butiran air dapat mencapai tingkat 95%. Sebaliknya, fase kaca yang diperoleh selama kristalisasi terak BF cair dengan pendinginan lambat di udara cukup terbatas.
Namun, granulasi air terak BF cair mengkonsumsi air dalam jumlah besar (1.000 hingga 1.500 liter kehilangan penguapan per ton terak BF cair yang diproses) dan dapat menghasilkan kabut asam yang menyebabkan polusi udara. Juga ada kebutuhan pengelolaan air yang tepat di satu sisi dan kebutuhan pengeringan terak BF butiran di sisi lain. Jadi, tidak hanya panas sensibel terak BF cair yang hilang, tetapi juga perlu memiliki unit pengering terak hulu untuk menggunakan terak BF granulasi dalam industri semen. Proses pengeringan biasanya mengkonsumsi energi panas hingga 72 M Cal/ton terak.
Di bidang granulasi kering BF cair bersama dengan pemulihan panas, proses sedang dikembangkan di banyak negara. Pekerjaan yang dilakukan untuk pengembangan proses dijelaskan di bawah ini.
Kemajuan pekerjaan di Eropa
Dalam proses yang sedang dikembangkan di anak perusahaan perusahaan baja negara, Merox Ltd di Swedia, terak digranulasi dengan memukul lapisan terak yang jatuh dengan partikel terak yang sebelumnya dipadatkan. Ini memecah film menjadi butiran yang kemudian jatuh ke dalam unggun terfluidisasi bertingkat dari mana panas diperoleh kembali. Dikatakan bahwa lebih dari 60% panas sensibel dalam terak dapat diperoleh kembali sebagai uap dengan metode ini dan bahwa produk terak memiliki kandungan kaca yang tinggi sehingga cocok untuk pembuatan semen.
Pada tahun 1990 tes pertama dengan granulasi terak kering dilakukan di British Steel (sekarang Tata Steel) di Redcar (UK). Jarak dari cangkir atomisasi ke dinding ruang sekitar 10 m untuk mencegah terak cair menempel. Partikel terak dengan kualitas yang sama dan struktur amorf seperti terak granulasi yang dibuat dengan sistem basah dapat ditemukan, sehingga tampaknya metode kering cocok di masa depan. Namun penskalaan tidak dilakukan.
Pada tahun 2002 hingga 2004 granulator yang dirancang lebih kecil digunakan di Vitkovice di Republik Ceko. Tes ini juga berhasil. Granulator ini dirancang untuk aliran massa 20 kg/menit terak cair dan tanpa pemulihan panas juga.
Rig lab terak kering baru (disingkat DSG) telah dipasang oleh Siemens VAI bekerja sama dengan Montanuniversität Leoben di aula Ketua Teknologi Pemrosesan Termal untuk penelitian dan pengembangan. Dalam proyek ini terdapat co-partner voestalpine Stahl GmbH, ThyssenKrupp Steel Europe AG dan FEhS-Institut für Baustoff-Forschung e.V. Proyek ini didanai oleh Kementerian Federal Jerman untuk Ekonomi dan Teknologi (BMWi). Rig DSG telah dikembangkan untuk menghindari aspek negatif dari proses granulasi basah.
Tujuan utama dari DSG adalah produksi terak granulasi untuk industri semen dengan sifat yang hampir sama (> 95% seperti kaca) seperti metode basah di satu sisi dan mendapatkan udara panas dari pendinginan terak untuk pemulihan panas di sisi lain. DSG didasarkan pada 'Cangkir Berputar' atau disebut juga prinsip Davy, di mana terak cair diatomisasi oleh cangkir, yang dapat diputar dengan kecepatan variabel. Partikel cair membeku selama penerbangan mereka menuju dinding granulator sebelum jatuh ke unggun terfluidisasi yang dikembangkan yang dibuat oleh partikel yang dipadatkan sebelumnya.
Rig lab di University of Leoben telah dirancang berdasarkan hasil tes lab di FEhS-Institut dan pemodelan Siemens VAI untuk menemukan parameter operasi terbaik untuk menghasilkan terak BF butiran berkualitas tinggi dan suhu saluran keluar udara setinggi mungkin. Oleh karena itu sekitar 300 kg terak dilebur dalam 'Flash-Reactor' untuk setiap percobaan di bengkel Universitas. Terak cair disadap ke dalam pot terak khusus yang dilapisi dengan bahan tahan api untuk mencegah kehilangan panas. Setelah itu pot terak dimanipulasi menjadi unit miring, dipasang dekat dengan granulator. Umpan terak cair ke dalam granulator dapat diukur dan dikendalikan melalui sel beban. Terak cair kemudian dikirim ke pusat granulator melewati pelari terak dan pipa tahan api vertikal. Setelah atomisasi, tetesan terak mendingin dengan cepat selama penerbangan mereka menuju dinding granulator setelah disebarkan oleh cangkir yang berputar cepat. Permukaan partikel harus memadat selama waktu penerbangan yang singkat ini sebelum jatuh ke unggun terfluidisasi yang dikembangkan yang dibuat oleh partikel butiran.
Bekerja di Australia
Penelitian di CSIRO (Commonwealth Scientific and Industrial Research Organization), Australia telah menunjukkan di laboratorium dan skala pilot bahwa granulasi kering menghasilkan terak yang cocok sebagai pengganti semen; dan bahwa panas yang dilepaskan dari terak dapat ditangkap oleh sejumlah kecil udara – membuat proses ini cocok untuk pemulihan panas tingkat tinggi. Sebuah proyek direncanakan dengan tujuan untuk mengembangkan lebih lanjut teknologi granulasi kering, dengan penekanan khusus pada penggunaannya sebagai sarana untuk menangkap limbah panas yang dilepaskan dari pendinginan terak dan untuk mengembangkan pengetahuan bagaimana meningkatkan skala dari skala percontohan ke skala industri. Pekerjaan ini merupakan bagian dari kontribusi industri baja Australia terhadap Program Terobosan CO2 Asosiasi Baja Dunia. Tujuan keseluruhan dari proyek ini adalah untuk mengembangkan proses granulasi kering yang menghasilkan terak bernilai tinggi dan memungkinkan penangkapan/pemulihan panas limbah yang dilepaskan dari pendinginan terak, sambil menunjukkan manfaat tekno-ekonomi, energi, dan keberlanjutannya pada skala percontohan. Proyek ini juga bertujuan untuk meningkatkan teknologi dan mendemonstrasikannya melalui uji coba pabrik.
Konsep granulasi kering terintegrasi dan pemulihan panas telah berhasil ditunjukkan melalui fasilitas percontohan prototipe di CSIRO. Proses yang dirancang telah berjalan dengan baik, menghasilkan operasi yang mulus dalam kondisi yang bervariasi dan tingkat penyadapan terak yang tinggi. Banyak pengujian telah dilakukan dengan menggunakan terak tanur sembur industri dan produk butiran dikumpulkan. Produk dikarakterisasi dan dinilai dengan memperhatikan sifat-sifat semen. Penilaian lebih lanjut oleh laboratorium pihak ketiga menemukan bahwa terak butiran kering memiliki sifat semen yang baik dan cocok untuk produksi semen.
Evaluasi tekno ekonomi menunjukkan bahwa granulasi terak kering memiliki keunggulan yang signifikan dibandingkan proses granulasi basah baik dari segi modal dan biaya operasi. Kunjungan pabrik dilakukan untuk mengumpulkan data tentang laju pengecoran dan mengukur suhu terak dan logam panas dari tanur tinggi di pabrik baja Whyalla One Steel dan pabrik baja Port Kembla BlueScope Steel. Data ini dinilai lebih lanjut dalam kaitannya dengan penerapan granulasi kering dan hasilnya didokumentasikan dalam sebuah laporan.
Pemodelan dinamika fluida komputasi (CFD) tingkat lanjut dari proses granulasi kering berhasil dilakukan. Model CFD untuk perpindahan panas dan mekanika fluida dalam proses atomisasi cakram pemintalan dirakit dan model divalidasi menggunakan data eksperimen dari pabrik percontohan di CSIRO. Draf rencana bisnis untuk tahap proyek selanjutnya telah dikembangkan.
Bekerja di Jepang
Di Jepang tiga skema terpisah sedang diselidiki. Sumitomo Metals Industries sedang mengembangkan proses granulasi kering untuk terak tanur sembur di mana aliran terak pecah saat menabrak drum yang berputar. Partikel terak kemudian jatuh ke dalam fluidized bed di mana panas diperoleh kembali. Proses ini bertujuan untuk menghasilkan terak partikulat untuk menggantikan pasir sungai serta memulihkan sekitar 55% panas dalam terak cair dalam aliran udara panas. Mitsubishi Heavy Industries dan Nippon Kokan KK sedang mengembangkan proses granulasi terak tungku oksigen dasar menggunakan ledakan udara yang kuat untuk memecah aliran terak. Partikel terak memadat saat bergerak melalui udara dan panas diperoleh kembali melalui radiasi dari semburan partikel dan juga dari fluidized bed tempat partikel jatuh. Kawasaki Steel Corporation juga mengembangkan proses untuk memulihkan panas dari terak tanur tinggi. Ini melibatkan granulasi terak dengan agitasi mekanis dan pemulihan panas dari proses granulasi dengan radiasi dan kemudian dari partikel terak granulasi dalam unggun terfluidisasi. Produk terak digunakan sebagai agregat untuk industri konstruksi.
Granulasi terak kering menggunakan alat penyemprot ledakan udara cangkir putar
Proses granulasi terak kering pada dasarnya adalah untuk mengatomisasi terak cair dan kemudian mendinginkan partikel dengan cepat sehingga menghasilkan terak kaca. Atomisasi dilakukan menggunakan alat penyemprot ledakan udara cangkir putar. Partikel mendingin saat mereka melakukan perjalanan melalui udara dan kemudian didinginkan lebih lanjut dalam unggun terfluidisasi. Kedua proses ini memberikan pendinginan cepat yang diperlukan untuk pembentukan produk terak kaca. Fluidized bed adalah metode yang nyaman untuk menahan partikel terak karena mencegah aglomerasi partikel panas selain memberikan pendinginan yang cepat.
Partikel terak dengan diameter rata-rata sekitar 2 mm dapat diproduksi oleh alat penyemprot sehingga produk terak dalam bentuk yang mudah ditangani. Pengujian telah menunjukkan bahwa partikel terak didinginkan cukup cepat sehingga produk memiliki kandungan kaca lebih dari 95%. Juga sangat sedikit wol terak yang diproduksi dalam prosesnya. Prinsip alat penyemprot cangkir putar ditunjukkan pada Gambar 1.
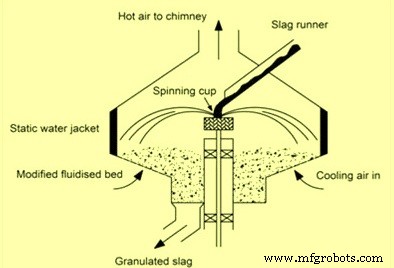
Gbr 1 Prinsip alat penyemprot cangkir putar
Alat penyemprot ledakan udara cangkir putar memiliki keuntungan sebagai berikut.
- Ini menawarkan kontrol yang baik dengan sangat mudah. Ukuran partikel dapat dikontrol dengan memvariasikan kecepatan cangkir putar atau aliran ledakan udara. Alat penyemprot ini juga menghasilkan kisaran ukuran partikel yang relatif sempit. Masalah memiliki cangkir berputar yang bersentuhan dengan terak cair tidak perlu dibatasi dan dapat diselesaikan dengan desain yang cermat dan pilihan bahan yang tepat.
- Daya yang dibutuhkan untuk menggerakkan alat penyemprot ini jauh lebih kecil daripada yang dibutuhkan oleh alat penyemprot cairan kembar. Alat penyemprot cairan kembar membutuhkan lebih dari 20 kali lebih banyak daya untuk mengatomisasi terak menjadi partikel berukuran serupa seperti yang dibutuhkan oleh alat penyemprot putar. Hal ini dapat memengaruhi penghematan biaya keseluruhan proses pemulihan panas hingga 5%.
- Lintasan partikel terak adalah ke luar dan ke atas. Gerakan ke atas berarti bahwa alat penyemprot dapat digunakan di lokasi di mana ada batasan ketinggian antara titik pengiriman terak dan tanah seperti dalam kasus di tanur tinggi di mana terak disuplai dari lantai rumah cor yang biasanya 7 m di atas tanah.
Alat penyemprot ledakan udara cangkir putar beroperasi dengan memutar film tipis terak yang memanjang secara radial dari bibir cangkir. Saat lapisan terak cair memanjang dari bibir cangkir, lapisan itu pecah dengan sendirinya. Namun kehadiran pancaran udara melingkar di sekitar cangkir membantu pemecahan terak dengan menginduksi gelombang tidak stabil dalam film. Ledakan udara memiliki efek menghasilkan partikel kecil dengan ukuran yang lebih seragam dan membelokkan partikel ke atas untuk menghasilkan semprotan berbentuk kerucut yang bergerak keluar dari alat penyemprot.
Panas diperoleh kembali dari terak dengan cara berikut.
- Saat semprotan partikel terak bergerak keluar dari alat penyemprot, panas hilang melalui radiasi ke bejana dan dengan konveksi ke udara yang bergerak melalui bejana. Namun, karena waktu penerbangan yang singkat (sekitar 0,1 detik), suhu turun hanya sekitar 100-200 derajat C.
- Saat tumbukan dengan dinding kapal, sebagian panas dipindahkan dari terak ke dinding. Telah ditemukan dari pengujian bahwa jika dinding dijaga relatif dingin, partikel terak tidak menempel ke dinding tetapi langsung terpental atau jatuh setelah waktu yang sangat singkat. Dalam kedua kasus, waktu kontak antara partikel terak dan dinding bejana jauh kurang dari 0,1 detik dan sekali lagi penurunan suhu terak adalah sekitar 150 derajat C.
- Lebih banyak panas yang hilang melalui radiasi dan konveksi saat partikel jatuh dari dinding ke unggun terfluidisasi primer.
- Sisa dari pemulihan panas berada di dalam fluidized bed, dengan perpindahan panas hanya ke udara fluidizing atau tambahan dengan tabung boiler yang terendam atau permukaan perpindahan panas lainnya. Dalam unggun terfluidisasi, udara terfluidisasi dan padatan meninggalkan unggun pada suhu yang sama dengan padatan di unggun. Suhu tempat tidur sekunder harus dipilih dengan hati-hati. Jika suhu partikel terak curah terlalu panas, panas yang dapat dipulihkan dalam terak akan terbuang sia-sia dan jika terlalu dingin, kegunaan udara fluidisasi panas pada pelepasan dari proses akan berkurang.
Pekerjaan eksperimental dilakukan dengan tujuan awal untuk menyelidiki apakah proses atomisasi akan menghasilkan partikel terak kecil dan apakah partikel tersebut memiliki struktur seperti kaca. Sebuah cangkir putar, alat penyemprot ledakan udara dibangun, dengan cangkir berdiameter 100 mm dan kisaran kecepatan 500 -1500 putaran/menit. Laju aliran terak yang digunakan dalam pengujian bervariasi dari 0,2 kg/detik hingga 0,5 kg/detik. Pengujian dibatasi hingga durasi sekitar 2,5 menit karena kapasitas yang terbatas (sekitar 30 kg) dari tungku peleburan terak laboratorium.
Tes awal membuktikan bahwa prosesnya berhasil; partikel kecil dengan kandungan kaca 95% diproduksi. Tes lebih lanjut kemudian dilakukan untuk menyelidiki ukuran partikel dan lintasan semprotan yang dihasilkan oleh alat penyemprot.
Panas sensibel dalam slag cair relatif terhadap 30 derajat C saat meninggalkan tanur tinggi pada 1500 derajat C adalah sekitar 400 M Cal/kg. Dari total aliran terak, sekitar 14% akan membanjiri akumulator terak hingga terbuang seperti yang disebutkan di atas. Dari sisa 86%, 32% kandungan panas tidak dapat dipulihkan karena hal berikut.
- Panas laten kristalisasi tidak dilepaskan ketika terak kaca terbentuk
- Produk terak padat dikeluarkan dari proses pemulihan panas pada 250 derajat C
- Kehilangan panas terjadi di akumulator terak
Dengan demikian, hanya 58,5% dari kandungan panas sensibel terak yang dikeluarkan dari tanur tinggi yang dapat diperoleh kembali.
Tantangan utama dari proses granulasi kering adalah memastikan pembekuan terak yang cepat untuk mencapai titik transformasi terak dengan sangat cepat. Jika tidak, terak yang dipadatkan tidak sepenuhnya seperti kaca tetapi sebagian kristal yang tidak cocok untuk digunakan lebih lanjut dalam industri semen. Pendinginan dengan udara jauh lebih sulit karena kapasitas panas yang jauh lebih rendah dibandingkan dengan air yang digunakan di pabrik granulasi terak konvensional. Selanjutnya udara memanas saat mengalir melalui tempat tidur yang gelisah. Selain itu, perbedaan suhu memperburuk proses pengaturan.
Kampanye awal menunjukkan hasil yang menjanjikan mengenai konten kaca, distribusi ukuran butir dan bentuk partikel. Juga peningkatan suhu gas yang signifikan dapat diukur. Dengan data yang diperoleh, optimasi proses dapat dilakukan dan peningkatan untuk penyelidikan lebih lanjut dapat direalisasikan di masa mendatang. Menggunakan granulasi terak kering di pabrik pabrik baja terintegrasi akan mendapatkan akses ke panas yang masuk akal dari terak tanur tinggi. Energi yang diperoleh kembali dapat digunakan untuk produksi uap atau listrik atau untuk proses pemanasan awal yang berguna lainnya. Potensi energi untuk memulihkan energi panas 20 MW atau sebagai alternatif pembangkit tenaga listrik sekitar 6 MW dari umpan terak satu ton per menit dapat dihitung. Tanpa memerlukan sistem pengeringan hulu untuk energi terak tanur tinggi dan sebagai konsekuensinya CO2 dapat dihemat. Ringkasnya granulasi kering terak tanur sembur memungkinkan pemrosesan selanjutnya yang ramah lingkungan dan berkelanjutan untuk salah satu potensi pemulihan panas yang besar di tanur sembur modern.