Proses Produksi untuk Refraktori Berbentuk
Proses Produksi untuk Refraktori Berbentuk
Produk refraktori dapat berbentuk (formed) atau tidak berbentuk (monolitik/castables). Mereka dapat dibuat dari bahan asam, netral, basa atau komposit. Bahan yang digunakan untuk produksi refraktori mungkin mengandung aditif atau tidak. Refraktori berbentuk lebih lanjut dapat dibuat dalam beberapa bentuk dan biasanya disebut bata tahan api. Aliran produksi tipikal yang digunakan dalam proses produksi refraktori diberikan pada Gambar 1.
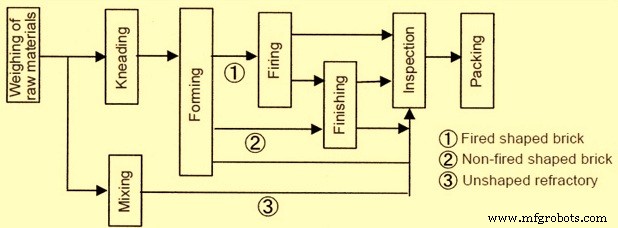
Gbr 1 Aliran khas dalam proses produksi untuk refraktori
Refraktori tak berbentuk biasanya dikirim dari pabrik pembuatan refraktori bukan sebagai refraktori tetapi sebagai bahan refraktori yang menjadi refraktori hanya setelah mengalami pencampuran, pembentukan, penuaan, pengeringan, dan pemanasan awal dll di lokasi penggunaan. Ini berarti bahwa dalam kasus refraktori tak berbentuk, bagian dari proses dalam pembuatan refraktori berbentuk bergeser ke lokasi penggunaan.
Dasar-dasar pembuatan batu bata tahan api tidak berubah dari waktu ke waktu. Namun, kemajuan teknologi telah membuat pabrik batu bata kontemporer jauh lebih efisien dan telah meningkatkan kualitas produk secara keseluruhan. Pembuatan refraktori ini didasarkan pada mengetahui kombinasi senyawa kimia dan mineral mana yang akan memberikan refraktori yang dihasilkan sifat-sifat yang dibutuhkan seperti refraktori, stabilitas termal, ketahanan korosi, ekspansi termal, dan kualitas penting lainnya. Pengetahuan yang lebih lengkap tentang bahan mentah dan sifat-sifatnya, kontrol pembakaran yang lebih baik, desain tungku yang lebih baik yang digunakan untuk pembakaran refraktori hijau, dan mekanisasi yang lebih maju, semuanya berkontribusi pada kemajuan industri bata tahan api.
Tujuan teknis pembuatan refraktori tertentu adalah untuk mendapatkan sifat dan kinerjanya untuk aplikasi yang dimaksudkan. Untuk memenuhi tujuan tersebut, komponen dasar pembuatan refraktori terdiri dari pemilihan bahan baku yang tepat, metode pemrosesan, dan pemeliharaan parameter teknologi selama pembuatan. Wawasan pembuatan berkaitan dengan fitur komposisi fase dan struktur mikro (secara kolektif dikenal sebagai karakter material) yang dikembangkan melalui pemrosesan, dan yang bertanggung jawab atas sifat produk dan perilakunya selama penggunaan.
Bahan mentah
Bahan baku yang dipilih dengan baik adalah bagian penting untuk pengembangan dan produksi produk tahan api yang memuaskan. Sifat bahan baku mempengaruhi sifat refraktori yang penting secara langsung dan tidak langsung. Bahan baku harus cocok dengan setidaknya enam sifat berbeda berikut untuk produksi produk tahan api berkinerja tinggi.
- Ukuran butir awal yang cukup
- Kepadatan / porositas
- Bagian mineral / oksida utama
- Batas dalam oksida tereduksi dan / atau fluks oksida
- Keseimbangan molar oksida penting
- Ukuran kristal mineral utama / oksida
Sifat yang berbeda dari refraktori seperti densitas, porositas, permeabilitas, kekuatan hancur, modulus pecah dan elastisitas serta ketahanan kejut termal terutama ditentukan oleh bahan baku selain proses produksi refraktori.
Bahan baku yang digunakan untuk pembuatan refraktori meliputi berbagai jenis tanah liat (baik dalam bentuk alami atau dikalsinasi), minuman keras (juga disebut chamotte), bahan baku olahan (dikalsinasi, disinter, dibakar atau dilebur), aditif juga dikenal sebagai bahan kimia matriks ( bisa dalam bentuk padat, cair atau koloid), dan bahan pengikat dll.
Pemrosesan bahan mentah
Pemrosesan bahan baku untuk pembuatan refraktori terdiri dari langkah-langkah berikut.
- Menghancurkan dan menggiling
- Menyaring atau menilai
- Pemisahan magnetis besi gelandangan
- Penimbangan batch
- Pencampuran batch
Operasi penghancuran dan penggilingan dilakukan di unit penghancuran/penggilingan primer, sekunder dan halus untuk memenuhi persyaratan ukuran butir yang berbeda dari bahan baku sesuai dengan granulometri yang diinginkan untuk komposisi batch tahan api. Untuk penghancuran primer dan untuk ukuran butir minimum 10-12 mm, biasanya digunakan penghancur rahang dan penghancur gyratory. Roller crusher, disk crusher, impact mill, dan berbagai jenis hammer mill digunakan untuk penghancuran sekunder untuk mencapai ukuran butir minimum sekitar 4 mm. Pulverizer dari berbagai jenis seperti pabrik atribusi, pabrik bola, pabrik batang, dan pabrik tabung dll. digunakan untuk penggilingan halus hingga ukuran minimum 200 mesh. Vibrating mill, jet mill, micronizer, dll. digunakan untuk beberapa produk khusus, yang memerlukan bubuk super halus dari beberapa bahan mentah berukuran hingga 10 mikron atau bahkan kurang.
Bahan baku yang dihancurkan dan digiling diayak atau dinilai ke dalam fraksi ukuran yang berbeda sesuai kebutuhan refraktori yang sedang diproduksi. Ini dilakukan dengan melewatkannya melalui saringan bergetar atau berputar atau pengklasifikasi udara. Dalam hal layar bergetar, satu set layar, seperti yang diinginkan, dipasang di bingkai bergetar sehingga beberapa fraksi diperoleh dalam operasi. Rotary screen berbentuk silinder putar, terdiri dari screen dengan beberapa ukuran yang disusun secara seri, dipasang pada sumbu miring yang sama, bukaan yang lebih besar pada set up adalah ke arah ujung bawah atau ujung pelepasan, sedangkan bukaan terkecil ada di bagian bawah. ujung atas atau ujung umpan. Jenis layar ini cocok untuk mengklasifikasikan terutama fraksi yang lebih kasar. Klasifikasi udara dilakukan untuk fraksi halus. Pengklasifikasi udara nyaman untuk partikel halus, hingga diameter beberapa hingga 10 mikrometer. Untuk pemisahan, jenis sentrifugal atau 'siklon' adalah umum. Di sini partikel yang lebih besar disirkulasikan kembali ke sistem dan partikel halus diumpankan ke silo.
Klasifikasi ukuran dilakukan untuk mengalihkan berbagai fraksi ukuran ke tempat penyimpanan yang berbeda dan dapat dilakukan dengan menggunakan sejumlah tingkatan yang sesuai dan rangkaian ukuran layar atau nomor mesh yang dipilih. Materi kecil yang partikelnya mungkin tidak beraturan dan bentuknya bergerigi, atau memanjang atau lonjong. Layar standar digunakan dengan bukaan persegi. Mereka melewati dan menahan apa yang mereka mau. Layar menjadi lengket jika ukurannya lebih halus dan layar dapat membutakan, mencegah beberapa atau semua partikel yang lebih halus melewatinya. Ini adalah pengamatan umum ketika penyaringan dilakukan untuk bahan yang lebih halus. Inilah alasan mengapa penyaringan kering jarang dilakukan untuk ukuran halus. Penyaringan basah (yaitu, bubur) dapat menghilangkan kebutaan untuk tujuan klasifikasi.
Besi bebas atau besi tramp yang masuk dalam bahan yang dihancurkan dan digiling dikeluarkan dari bahan dengan pemisahan magnetis. Potongan-potongan besi gelandangan dihilangkan dengan bantuan pemisah magnetik yang merupakan jenis katrol atau gantung dengan baik permanen atau elektromagnet. Bahan yang dihancurkan dari mana besi akan dilepas ditempatkan pada sabuk bergerak yang melewati rol magnet atau dibiarkan jatuh langsung pada rol magnet yang berputar secara tunggal atau seri, satu di atas yang lain, untuk melepaskan setrika.
Batu bata tahan api diproduksi dalam batch. Satu batch bahan baku terdiri dari fraksi halus, sedang dan kasar dalam jumlah (rasio) yang dibutuhkan. Mobil penimbangan batch biasanya digunakan untuk menarik jumlah material yang dibutuhkan secara akurat dalam fraksi ukuran yang tepat dari tempat penyimpanan. Untuk jumlah kecil, biasanya dilakukan secara manual menggunakan mesin timbang.
Bahan yang ditimbang dicampur secara menyeluruh menggunakan mixer yang sesuai. Beberapa jenis mixer yang tersedia untuk pencampuran bahan dalam batch. Ini adalah pan mixer, trough mixer, drum mixer, pug mill, dan counter current mixer dll. Biasanya, untuk proses pembentukan semi kering dan plastik, batch untuk fire clay refraktori dicampur dalam trough mixer dan pug mills. Mixer jenis arus berlawanan digunakan untuk memproduksi campuran untuk pemrosesan kering alumina tinggi atau refraktori dasar khususnya di mana kadar air kurang dari 10 %.
Mesin pencampur dan pengaduk untuk pembuatan refraktori biasanya terdiri dari dua jenis yaitu (i) jenis bejana tetap, dan (ii) jenis bejana yang digerakkan. Mesin pencampur dan pengaduk untuk produksi batu bata tahan api eksklusif untuk aplikasi pengepresan kering dan semi kering karena jumlah pengikatnya minimal. Oleh karena itu, mesin pencampur dan pengaduk dilengkapi dengan pisau pencampur atau roda penghancur.
Membentuk atau membentuk
Batu bata tahan api dibentuk dengan berbagai metode yang mencakup cetakan tangan atau dalam berbagai jenis mesin pembentuk dan cetakan yang mencakup pengepres. Jenis cetakan yang diadopsi tergantung pada bentuk dan ukuran refraktori dan kuantitasnya. Secara garis besar metode pencetakan / pengepresan dapat dibagi menjadi tiga kategori yaitu (i) proses pengepresan semi kering atau lumpur kaku, (ii) proses pencetakan plastik atau lumpur lunak, dan (iii) proses pengepresan kering. Bata yang dibentuk disebut bata hijau.
Dalam lumpur kaku atau proses ekstrusi, air dalam kisaran 10% sampai 15% dicampur untuk menghasilkan plastisitas. Setelah pencampuran, campuran tahan api melewati ruang dearing yang mempertahankan vakum 375 mm hingga 725 mm merkuri. Deairing menghilangkan lubang udara dan gelembung, memberikan campuran tahan api meningkatkan kemampuan kerja dan plastisitas, menghasilkan kekuatan yang lebih besar. Setelah ini, campuran tahan api diekstrusi melalui cetakan untuk menghasilkan kolom campuran. Saat kolom campuran meninggalkan cetakan, tekstur atau pelapis permukaan dapat diterapkan. Pemotong otomatis kemudian memotong kolom campuran untuk membuat bata individual. Jarak pemotong dan ukuran cetakan harus dihitung dengan hati-hati untuk mengimbangi penyusutan normal yang terjadi selama pengeringan dan pembakaran. Sebagian besar batu bata tahan api biasanya diproduksi melalui proses ekstrusi.
Lumpur lunak atau proses pencetakan plastik sangat cocok untuk campuran tahan api yang mengandung terlalu banyak air untuk diekstrusi dengan proses lumpur kaku. Campuran tahan api dicampur mengandung 20% sampai 30% air dan kemudian dibentuk menjadi bentuk dalam cetakan. Untuk mencegah campuran tahan api menempel, cetakan dilumasi dengan pasir atau air untuk menghasilkan batu bata 'terpukul pasir' atau 'terpukul air'. Batu bata dapat diproduksi dengan cara ini dengan mesin atau dengan tangan.
Pengepresan kering dicapai di bawah tekanan tinggi pada pengepres tugas berat atau bahkan dengan aksi menyentak dan menekan terutama untuk campuran butiran halus. Proses ini terutama cocok untuk campuran tahan api dengan plastisitas sangat rendah. Campuran tahan api dicampur dengan sedikit air (hingga 10 %), kemudian ditekan ke dalam cetakan baja di bawah tekanan dari 3,4 MPa hingga 10,3 MPa dengan pengepres hidrolik atau ram udara tekan.
Pengeringan dan pembakaran
Batu bata basah dari cetakan atau mesin pemotong mengandung banyak uap air, tergantung pada proses pembentukannya. Sebelum proses pembakaran dimulai, sebagian besar air ini harus diuapkan dalam ruang pengering pada suhu berkisar dari sekitar 40 derajat C sampai 200 derajat C untuk menurunkan kadar air ke tingkat yang lebih disukai kurang dari 1%. Tingkat waktu pengeringan, yang bervariasi dengan campuran tahan api, umumnya antara 24 hingga 48 jam. Meskipun panas dapat dihasilkan khusus untuk ruang pengering, biasanya dipasok dari panas pembuangan kiln untuk memaksimalkan efisiensi termal. Dalam semua kasus, panas dan kelembaban harus diatur dengan hati-hati untuk menghindari retak pada batu bata hijau. Batu bata yang lebih besar yang sulit ditangani dikeringkan di lantai panas yang dipanaskan dari bawah oleh gas buang atau uap.
Operasi terakhir dalam produksi batu bata tahan api dan bentuk adalah pembakarannya. Selama pembakaran, batu bata dipanaskan hingga suhu yang diinginkan dan disimpan pada suhu tersebut selama beberapa waktu tertentu agar batu bata matang sempurna.
Ada beberapa jenis tungku/kiln yang digunakan. Tungku/kiln secara luas dapat dibagi menjadi intermiten, semi kontinyu dan kontinyu. Jenis yang paling umum adalah kiln terowongan, diikuti oleh kiln intermiten. Bahan bakar dapat berupa minyak, gas, atau batu bara, atau kombinasi dari bahan bakar ini.
Kiln intermiten adalah yang dimuat, dipecat, dibiarkan dingin dan dibongkar, setelah itu langkah yang sama diulang. Batu bata kering diatur dalam kiln ini sesuai dengan pola yang ditentukan yang memungkinkan sirkulasi gas kiln panas. Kiln ini biasanya adalah kiln down draft yang hanya digunakan di unit manufaktur kecil. Tempat pembakaran down draft dirancang untuk menampung tumpukan besar batu bata tahan api. Ini berbentuk bulat atau persegi panjang, dilengkapi dengan ' sejumlah kotak api (untuk pembakaran batubara) atau port burner (untuk pembakaran gas atau minyak) di sekitar kiln. Ketinggian atap disediakan untuk menampung volume gas pembakaran di dalam ruang yang dibiarkan kosong di atas tumpukan batu bata di bawah atap. Gas buang bersama dengan nyala api diarahkan ke atap dan kemudian dipantulkan ke bawah melalui saluran dan cerobong asap yang disediakan di lantai dan di bawahnya. Dalam kiln seperti itu, kehilangan panas sangat besar karena gas pembakaran keluar ke cerobong asap tanpa melakukan fungsi tambahan apa pun. Juga, sejumlah besar panas hilang dalam memanaskan struktur tungku setiap kali tungku dibakar karena sifatnya yang terputus-putus. Efisiensi panas kiln semacam itu buruk sekitar 15%.
Kiln semi kontinyu adalah kiln ruang cincin dan kiln shuttle. Kiln kontinu adalah kiln terowongan. Tanur kontinu adalah tanur yang paling umum dalam industri refraktori karena profil suhu dipertahankan sepanjang terowongan dan batu bata bergerak di dalam mobil di dalam terowongan di atas rel.
Proses pemuatan mobil kiln atau kiln dengan batu bata berbentuk disebut hacking. Jumlah batu bata pada mobil kiln ditentukan oleh ukuran kiln. Batu bata lebih disukai ditempatkan dengan cara mekanis. Pola pengaturan memiliki beberapa pengaruh pada penampilan. Batu bata yang diletakkan berhadap-hadapan memberikan warna yang lebih seragam dibandingkan dengan bata yang dipasang bersilangan atau diletakkan berhadap-hadapan.
Penembakan batu bata dilakukan antara 10 dan 40 jam, tergantung pada jenis kiln dan variabel lainnya. Di kiln terowongan, batu bata dimuat ke mobil kiln, melewati berbagai zona suhu saat mereka melakukan perjalanan melalui terowongan. Kondisi panas di setiap zona dikontrol dengan hati-hati, dan kiln dioperasikan terus menerus.
Pembakaran dapat dibagi menjadi lima tahap umum yaitu (i) pengeringan akhir (penguapan air bebas), (ii) dehidrasi, (iii) oksidasi, (iv) vitrifikasi, dan (v) pengapian atau pembakaran reduksi. Semua kecuali berkedip berhubungan dengan kenaikan suhu di kiln. Meskipun suhu sebenarnya berbeda dengan jenis campuran tahan api.
Campuran tahan api umumnya melunak secara perlahan dan meleleh atau mengalami vitrifikasi secara bertahap ketika mengalami kenaikan suhu. Vitrifikasi memungkinkan campuran menjadi massa yang keras dan padat dengan penyerapan yang relatif rendah. Peleburan terjadi dalam tiga tahap yaitu (i) peleburan baru jadi, ketika partikel campuran menjadi cukup lunak untuk saling menempel dalam massa ketika didinginkan, (ii) vitrifikasi, ketika fluks ekstensif terjadi dan massa menjadi rapat, padat dan tidak menyerap, dan ( iii) peleburan kental, ketika massa campuran pecah dan menjadi cair, yang mengarah ke batu bata yang berubah bentuk. Kunci dari proses pembakaran adalah untuk mengontrol suhu di dalam kiln sehingga terjadi fusi yang baru jadi dan vitrifikasi parsial tetapi fusi yang kental dapat dihindari. Tingkat perubahan suhu harus dikontrol dengan hati-hati dan tergantung pada bahan baku, serta ukuran dan pengawetan batu bata yang diproduksi. Kiln biasanya dilengkapi dengan sensor suhu untuk mengontrol suhu pembakaran dalam berbagai tahap. Menjelang akhir, batu bata mungkin di-flash untuk menghasilkan variasi warna.
Setelah suhu mencapai puncaknya dan dipertahankan untuk waktu yang ditentukan, proses pendinginan dimulai. Waktu pendinginan jarang melebihi 10 jam untuk tanur terowongan dan dari 5 hingga 24 jam pada tanur berselang. Pendinginan merupakan tahap penting dalam pembuatan batu bata karena laju pendinginan memiliki efek langsung pada warna batu bata. Setelah pendinginan, batu bata diperiksa, disortir, dinilai, dan dikemas untuk pengiriman.