Produktivitas dan Kualitas Produk di Continuous Casting Machine
Produktivitas dan Kualitas Produk di Mesin Pengecoran Berkelanjutan
Pengecoran kontinyu adalah proses dimana baja cair dipadatkan menjadi produk baja setengah jadi (billet, bloom, atau slab dll.) untuk pengerolan selanjutnya di pabrik pengerolan panas. Pengecoran terus menerus dari baja cair diperkenalkan untuk aplikasi komersial pada 1950-an. Dalam rentang waktu yang relatif singkat sejak diperkenalkannya continuous casting untuk aplikasi komersial, proses tersebut telah berkembang dengan berbagai macam pengembangan proses baru yang diarahkan untuk mencapai peningkatan produktivitas dan kualitas produk yang unggul. Perkembangan ini mencakup konsep desain baru mesin pengecoran kontinu, praktik metalurgi, dan penerapan kontrol proses dan otomatisasi oleh sistem komputer.
Kekuatan pendorong utama di balik perkembangan ini adalah pengakuan bahwa peningkatan substansial dalam hasil dan penghematan energi dimungkinkan yang memiliki efek dramatis pada biaya operasi. Melalui perkembangan ini, dimungkinkan untuk mencapai peningkatan kualitas utama dari produk cor terus menerus. Mesin continuous casting saat ini menghasilkan produk baja cor yang memiliki kualitas yang sepenuhnya setara dan melebihi produk yang dihasilkan dari baja ingot. Mesin pengecoran kontinu modern secara efisien menghasilkan semua jenis baja, termasuk kualitas tertinggi untuk aplikasi kritis.
Peningkatan produktivitas
Dua metode untuk meningkatkan produktivitas proses pengecoran kontinu meliputi peningkatan throughput mesin pengecoran kontinu (ton/jam) dan rasio kerja bersih. Throughput mesin continuous casting ditingkatkan dengan meningkatkan kecepatan casting serta dengan meningkatkan luas penampang, sedangkan rasio jaringan ditingkatkan dengan mengurangi waktu henti mesin casting.
Kecepatan casting mesin continuous casting dibatasi oleh beberapa fenomena berbeda seperti yang diberikan di bawah ini.
- Kecepatan pengecoran yang tinggi menghasilkan peningkatan yang signifikan dalam kecepatan aliran baja cair dalam cetakan. Setiap gangguan kecil dalam aliran baja cair mengganggu pembentukan cangkang pemadatan dalam cetakan, menghambat pengapungan inklusi, dan dapat menyebabkan masuknya serbuk tuang ke dalam untaian. Fluktuasi level yang berlebihan dan gelombang pada meniskus dalam cetakan menjadi lebih buruk dengan kecepatan casting yang lebih tinggi. Hal ini dapat menyebabkan masalah kualitas permukaan dan bahkan stiker pecah. Masalah ini dapat diatasi dengan mengubah desain nozzle (mengarahkan aliran lebih ke bawah, atau mungkin dengan menambahkan port vertikal bawah), menerapkan pengadukan elektromagnetik, mengganti bubuk tuang, dan menggunakan metode lain untuk mengontrol pola aliran dalam cetakan.
- Kecepatan pengecoran yang tinggi menghasilkan regangan aksial yang berlebihan yang disebabkan oleh gaya osilasi dan penarikan yang diperlukan untuk mengatasi gesekan pada antarmuka antara cangkang pemadatan dan cetakan. Retak melintang terkait dan pecah dapat membatasi kecepatan pengecoran, terutama jika ada misalignment, lancip yang berlebihan dari cetakan, atau lapisan bubuk pengecoran cair terputus-putus. Tekanan kecil jika lapisan cair dari bubuk cor dapat terus menerus di seluruh permukaan cetakan dan keselarasan yang baik.
- Dengan kecepatan pengecoran yang tinggi, regangan membran yang berlebihan dapat dihasilkan dalam cangkang tipis oleh tekanan ferostatik dari kolam cairan di bawah cetakan. Hal ini dapat menyebabkan retak dan pecah jika cangkang tidak cukup tebal saat keluar dari cetakan. Ketebalan cangkang kritis harus dalam urutan 3 mm untuk sebagian besar nilai baja. Ini mudah dicapai dengan kecepatan casting yang layak, yang menunjukkan bahwa kriteria lain lebih penting.
- Ketidakseragaman lokal apa pun dalam pertumbuhan cangkang karena kecepatan pengecoran yang tinggi dapat menyebabkan daerah panas dan tipis lokal di dalam cangkang, yang dapat memicu keretakan dan breakout longitudinal bahkan jika cangkang berada di atas ketebalan kritis rata-rata. Masalah ini biasanya diatasi dengan mengoptimalkan perilaku serbuk tuang selama pemadatan awal, praktik osilasi, dan desain lancip, sehingga pelumasan serbuk tuang terus menerus, fluks panas awal rendah dan seragam, dan lancip dinding cetakan sesuai dengan profil penyusutan cangkang. Nilai baja peritektik dan baja tahan karat austenitik paling rentan terhadap masalah ini. Panas berlebih dari baja cair yang memasuki cetakan juga dapat menyebabkan masalah ini, terutama di dekat permukaan tempat jet baja cair mengenai saat pengecoran dengan nozel bercabang dua yang terendam.
- Penonjolan untaian yang berlebihan di bawah cetakan dapat terjadi karena kecepatan pengecoran yang tinggi dan hal ini dapat menyebabkan berbagai retakan internal dan bahkan jerawat jika penonjolan itu ekstrem. Penggembungan dapat dikontrol dengan memilih gulungan pendukung yang cukup, mempertahankan pelurusan gulungan, mengontrol pendinginan semprotan di bawah cetakan, dan dengan menghindari perubahan mendadak pada pitch gulungan, semprotan, atau dengan mengurangi kecepatan casting.
- Jarak di bawah meniskus titik pemadatan akhir dari pusat untaian meningkat sebanding dengan kecepatan pengecoran untuk ketebalan bagian tertentu dan membatasi kecepatan pengecoran maksimum dalam mesin pengecoran kontinu tertentu. Sistem pendukung cut-off dan roll obor harus diperluas untuk mengakomodasi peningkatan panjang metalurgi ini. Panjang metalurgi tidak dapat dipersingkat secara signifikan dengan meningkatkan intensitas pendinginan semprotan.
- Pemanasan ulang untaian di bawah ujung zona pendinginan semprot dapat terjadi karena kecepatan pengecoran yang tinggi. Pemanasan ulang untaian ini menghasilkan tegangan tarik internal dan retakan air mata panas, yang semakin parah seiring dengan kecepatan pengecoran. Ini harus diperhatikan selama desain zona semprotan. Zona pendinginan semprotan harus diperluas untuk menghindari retakan ini.
- Ada beberapa masalah kualitas khusus, yang terkadang membatasi kecepatan casting. Misalnya, pada baja karbon ultra-rendah, kecepatan pengecoran dibatasi pada batas atas yang relatif lambat untuk mengurangi pipa pensil dan cacat blister lainnya karena jebakan gelembung argon pada radius bagian dalam mesin pengecoran kontinu tipe cetakan melengkung. Kecepatan pengecoran hanya dapat ditingkatkan dalam situasi seperti itu dengan perubahan hati-hati dalam kondisi operasi yang dapat menghindari cacat khusus ini. Oleh karena itu pertimbangan yang cermat dari berbagai fenomena yang menjadi perhatian diperlukan untuk meningkatkan kecepatan casting. Setidaknya ada delapan kriteria terpisah yang harus dipenuhi di mana lima kriteria terpenting yang dapat membatasi kecepatan pengecoran untuk operasi tertentu adalah suhu, bulging, regangan, tegangan, dan fraktur pada produk cor. Selalu penting untuk menemukan kecepatan pengecoran kritis untuk menghindari masalah kualitas yang terkait dengan penonjolan di bawah cetakan.
Break-out adalah salah satu masalah operasional yang paling mempengaruhi produksi mesin continuous casting. Ini terjadi sebagai berikut. Selama pemadatan awal baja cair dalam cetakan pengecoran kontinu, cangkang pemadatan mungkin tidak terbentuk secara memadai pada beberapa posisi karena alasan apa pun, dan ketika posisi itu keluar dari ujung bawah cetakan, baja cair mengalir keluar melalui bagian yang rusak dari baja cair. kerang. Break-out tidak hanya menurunkan produksi, tetapi juga menyebabkan kerusakan parah pada peralatan, sehingga membutuhkan pekerjaan perbaikan yang ekstensif. Untuk mencegah pecah, oleh karena itu, penting untuk memastikan bahwa cangkang solidifikasi awal yang baik terbentuk secara stabil di dalam cetakan. Faktor utama yang mempengaruhi pemadatan awal baja cair dalam cetakan continuous casting adalah suhu baja, serbuk tuang, lapisan tembaga cetakan, dan air pendingin primer.
Hal yang penting untuk meningkatkan produksi mesin pengecoran kontinyu berdasarkan solidifikasi awal yang stabil adalah pemeliharaan keseimbangan yang memadai dari suhu baja dalam cetakan, penghilangan panas, dan kecepatan pengecoran. Ketika suhu baja dan kecepatan pengecoran tinggi, cangkang pemadatan tidak cukup berkembang, dan mungkin ada kasus di mana baja cair menembus cangkang tepat di bawah cetakan (re-melting break-out). Hal ini menunjukkan bahwa, untuk meningkatkan produksi tanpa break-out, suhu baja cair dan kecepatan pengecoran harus dikontrol secara memadai.
Meningkatkan waktu kerja dan waktu pengecoran mesin continuous casting juga merupakan cara yang efektif untuk meningkatkan produksi mesin continuous casting. Sehubungan dengan mesin continuous casting, istilah-istilah ini didefinisikan sebagai berikut.
Waktu kalender =Waktu kerja jaringan + Waktu henti
Waktu kerja bersih =Waktu pengecoran + Waktu persiapan mesin
Kunci untuk kapasitas produksi yang lebih tinggi adalah bagaimana mengurangi waktu henti untuk meningkatkan rasio waktu kerja bersih terhadap waktu kalender dan bagaimana mengurangi waktu persiapan mesin untuk meningkatkan rasio waktu pengecoran.
Peningkatan produktivitas juga dapat dicapai dengan meningkatkan rasio jaringan kerja. Rasio kerja bersih dapat ditingkatkan dengan mengurangi waktu henti mesin pengecoran kontinu dan dengan demikian meningkatkan waktu mesin benar-benar casting (waktu pemanfaatan mesin) sambil mempertahankan kemampuan untuk menghasilkan berbagai ukuran produk baja cor dan grade baja.
Untuk mengurangi waktu henti dan untuk mencegah masalah mesin pengecoran seperti kerusakan gulungan segmen dan bantalan, mesin pengecoran kontinu biasanya mengalami shutdown berkala selama 12 hingga 24 jam dalam setiap tiga hingga empat minggu untuk perubahan segmen.
Berikut ini adalah lima faktor utama (gambar 1) yang berkontribusi terhadap waktu henti mesin pengecoran kontinu dan harus ditangani.
- Waktu persiapan mesin setelah urutan pemeran selesai
- Perubahan cetakan diperlukan untuk mentransmisikan ukuran bagian yang berbeda
- Mesin casting atau penghentian untaian karena kegagalan seperti putusnya untaian, penyumbatan nozel tundish yang terhalang oleh baja dingin atau oleh penumpukan inklusi, dan aliran baja cair yang tidak terkontrol dari sendok baja yang padat (mis. stopper berjalan)
- Di luar spesifikasi panas dalam komposisi atau/dan suhu
- Perawatan mesin continuous casting.
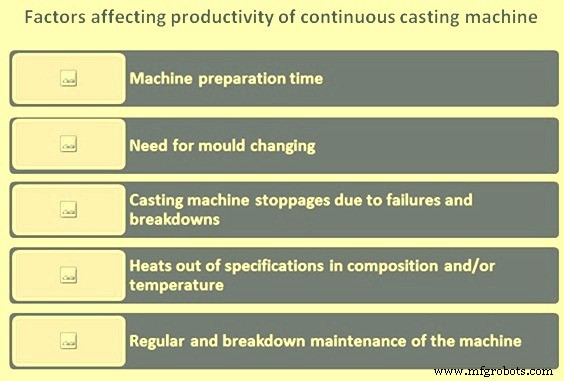
Gbr 1 Faktor yang mempengaruhi produktivitas mesin pengecoran kontinu
Selain praktik dan teknik kontrol yang lebih baik selama pembuatan baja, pengaruh faktor-faktor ini telah dikurangi dengan mengembangkan konsep operasi dan desain peralatan baru dalam mesin pengecoran kontinu. Perubahan besar dalam konsep operasi meliputi berikut ini.
- Urutan casting untuk mengurangi waktu persiapan mesin continuous casting
- Memotong produk cor untuk mengurangi frekuensi penggantian cetakan serta mengurangi persediaan cetakan.
- Penggunaan cetakan dengan penyesuaian lebar variabel untuk mengurangi waktu penggantian cetakan
- Membagi atau membagi cetakan untuk mengurangi waktu penggantian cetakan dan inventaris cetakan serta untuk meningkatkan kecepatan pengecoran (ton per jam per untai)
- Dummy bar diumpankan ke atas (penyisipan ke bawah) untuk mengurangi waktu persiapan
- Penggunaan pengadukan elektromagnetik yang memungkinkan untuk meningkatkan kecepatan pengecoran yang pada gilirannya meningkatkan produktivitas mesin pengecoran
Jumlah panas yang dilemparkan melalui mesin pengecoran kontinu tanpa gangguan antara penyisipan dummy bar berbeda dari mesin pengecoran ke mesin pengecoran tergantung pada faktor-faktor seperti ukuran lot produksi kimia baja yang sama, masa pakai nozel masuk terendam, dan terjadinya penyumbatan nozzle dan masalah lain dalam sistem yang padat.
Pekerjaan persiapan antara gips meliputi ekstraksi potongan akhir, penyisipan dummy bar, perubahan tundish, dan penyegelan cetakan. Potongan terakhir dari cetakan sebelumnya diekstraksi dengan hati-hati untuk mencegah pendarahan, masalah terak cair atau baja yang mengalir keluar dari ujung atas, di mana pemadatan seringkali tidak mencukupi. Untuk melakukan ini dengan cepat penting untuk mempersingkat waktu persiapan.
Adapun penyisipan batang tiruan, jenis penyisipan ke bawah saat ini lebih disukai karena batang tiruan dapat dimasukkan saat potongan cetakan akhir sedang diekstraksi. Jika menggunakan tipe inserting ke atas, sebaliknya, penyisipan dummy bar harus menunggu sampai potongan terakhir keluar dari mesin casting sepenuhnya, yang meningkatkan waktu persiapan 10 hingga 20 menit.
Kualitas produk
Kualitas baja cor terus menerus tergantung pada pembuatan baja dan praktik pengecoran yang digunakan. Hal ini dipengaruhi oleh interaksi faktor kimia dan fisik yang harus dikontrol secara ketat untuk mendapatkan potensi penuh dari proses.
Cacat umum yang dialami dalam pengecoran kontinu meliputi hal berikut.
- Cacat permukaan seperti (i) deformasi penampang (termasuk cekung dan cembung), (ii) retak (membujur dan melintang), (iii) putaran, kerak dan inklusi dan terak yang terperangkap, dan (iv) tanda osilasi dll .
- Cacat bawah permukaan seperti (i) lubang kecil dan lubang sembur, (ii) inklusi, dan (iii) retak
- Cacat internal seperti (i) retakan (tengah, diagonal dan setengah jalan), (ii) porositas, (iii) inklusi, dan (iv) segregasi dll.
Pembentukan retakan terjadi karena berbagai penyebab fisik. Teknik yang digunakan untuk menghilangkan atau mengurangi terjadinya retakan eksternal dan internal antara lain sebagai berikut.
- Retak permukaan – Cetakan dan pendinginan sekunder, pelumasan cetakan, pelapisan cetakan, kontrol keausan cetakan, pelurusan mesin dan kecepatan pengecoran.
- Retak internal (dan porositas) – Jenis mesin, pelurusan mesin, pengadukan elektromagnetik, reduksi in?line, pelurusan multi-titik, pengecoran kompresi, suhu baja cair, dan kecepatan pengecoran.
Lap dan keropeng terkait dengan kontrol kecepatan casting dan integritas aliran penuangan antara tundish dan cetakan. Tanda osilasi adalah fungsi dari cor kelas baja dan jenis osilasi cetakan.
Lubang kecil dan lubang sembur dikendalikan oleh deoksidasi dan selubung aliran tundish. Pemisahan garis tengah telah diminimalkan dengan suhu pengecoran rendah, pengadukan elektromagnetik, dan kecepatan pengecoran.
Frekuensi penyertaan, baik di permukaan, di bawah permukaan, atau di bagian dalam bagian cor, telah dikurangi secara bertahap melalui peningkatan, misalnya, dalam praktik pembuatan baja, deoksidasi dan selubung, serta desain peralatan. Perbaikan ini merupakan bagian integral dari upaya berkelanjutan untuk lebih meningkatkan kualitas produk baja cor terus menerus.
Perkembangan terbaru yang paling signifikan dalam meningkatkan kualitas produk adalah sebagai berikut.
- Konsep baja bersih
- Aplikasi pengadukan elektromagnetik
- Pendinginan kabut udara untuk lebih mengurangi timbulnya retakan pada permukaan.
Salah satu tujuan utama adalah untuk menghasilkan produk baja tuang dengan permukaan yang tidak memerlukan pengkondisian sebelum diproses lebih lanjut.
Persyaratan pengguna baja telah beragam, dan fungsionalitas yang lebih tinggi dicari dalam hal pengurangan berat, kemampuan kerja yang lebih baik, dan kekuatan yang lebih tinggi, dll. Kontrol yang lebih ketat terhadap cacat permukaan dan penghapusan cacat internal sekarang semakin dituntut. Semua ini, bersama-sama dengan mengejar hasil dan produktivitas yang lebih tinggi, telah membuat tingkat kualitas yang dibutuhkan untuk pembuatan baja dan proses pengecoran baja terus menerus sangat menuntut. Di sisi lain, memang benar bahwa persyaratan pengguna yang semakin ketat telah membantu meningkatkan kemampuan teknis pembuatan baja dan praktik pengecoran baja kontinu.
Meminimalkan inklusi dalam cetakan adalah salah satu masalah kualitas yang paling penting dari pengecoran kontinyu. Inklusi memperburuk sifat mekanik baja di bawah tegangan, pembengkokan, pemuaian lubang, pembentukan tekan, dan jenis pekerjaan lainnya, dan menyebabkan cacat permukaan. Oleh karena itu, sangat penting untuk meminimalkan kontaminasi baja dan menghilangkan inklusi darinya dalam proses pengecoran berkelanjutan.
Cacat permukaan yang khas yang berasal dari proses pembuatan baja adalah karena masuknya alumina dan bubuk tuang. Mereka terperangkap dalam cangkang baja selama pemadatan awal, dan ketika baja digulung dalam rolling mill, mereka diregangkan dan membentuk cacat pada garis-garis di permukaan yang biasanya dikenal sebagai tumpahan, keropeng, atau serpihan. Inklusi seperti itu di dekat permukaan produk cor dapat dihilangkan dengan penggoresan, tetapi karena pengikisan melibatkan biaya dan penurunan hasil, lebih disukai untuk meminimalkan jebakan selama pemadatan awal dalam cetakan mesin pengecoran kontinu. Pengadukan elektromagnetik cetakan membuat baja segera di dalam cangkang pemadatan mengalir pada kecepatan yang ditentukan atau lebih cepat untuk mencegah inklusi terperangkap di dalam cangkang.
Mengenai bedak tuang, untuk mencegah jebakan, kekentalan serbuk biasanya ditingkatkan. Juga akurasi kontrol tingkat baja cair dalam cetakan ditingkatkan, osilasi cetakan dimodifikasi, dan masuknya baja cair ke dalam cetakan menjadi lebih stabil. Akibatnya, cacat permukaan karena inklusi yang berasal dari bubuk cor berkurang secara nyata.
Selain itu, untuk meminimalkan jumlah inklusi yang masuk ke cetakan, langkah-langkah diambil untuk memisahkan inklusi dari baja di tundish sebanyak mungkin. Salah satu ukuran tersebut adalah pembesaran kapasitas tundish. Sebuah tundish berfungsi sebagai pemegang perantara untuk memastikan aliran baja yang stabil dari sendok ke cetakan pengecoran kontinu, dan dalam kasus mesin pengecoran multi-untai, mendistribusikan baja ke untaian. Dengan meningkatkan ukuran tundish, inklusi dapat mengapung ke permukaan baja cair dengan lebih mudah dan menekan suspensi terak dalam baja pada posisi penuh dari sendok.