Peningkatan Desain dan Masa Pakai Kampanye Tungku Ledakan
Desain yang Disempurnakan dan Masa Pakai Kampanye Tungku Ledakan
Biaya pembangunan kembali atau pelapisan ulang tanur sembur (BF) sangat tinggi. Oleh karena itu, teknik untuk memperpanjang usia kampanye BF adalah penting dan perlu dilakukan dengan sangat aktif.
BF besar biasanya memiliki hasil kampanye yang sedikit lebih tinggi per unit volume. Perbedaan ini karena BF yang lebih besar umumnya memiliki desain yang lebih modern dan terotomatisasi dengan baik. Karena kelangsungan hidup pabrik baja terintegrasi bergantung pada pasokan logam panas (HM) yang berkelanjutan, yang, di pabrik dengan sejumlah kecil BF besar, sangat mementingkan masa pakai kampanye yang panjang.
Teknik untuk memperpanjang masa kampanye BF termasuk dalam tiga kategori berikut.
- Praktik operasional – Kontrol proses BF memiliki pengaruh besar pada kehidupan kampanye. BF akan dioperasikan tidak hanya untuk memenuhi kebutuhan produksi tetapi juga untuk memaksimalkan umurnya. Oleh karena itu, perlu untuk memodifikasi praktik operasi saat kampanye berlangsung dan sebagai tanggapan terhadap area masalah untuk memaksimalkan masa pakai kampanye.
- Tindakan perbaikan – Setelah keausan atau kerusakan yang memengaruhi masa pakai BF terbukti, teknik perbaikan teknik harus digunakan atau dikembangkan untuk memaksimalkan masa pakai kampanye.
- Desain yang ditingkatkan – Seiring dengan pengembangan material dan peralatan yang lebih baik, ini akan dimasukkan ke dalam pembangunan kembali di masa mendatang untuk memperpanjang masa pakai area kritis BF, yang hemat biaya untuk melakukannya.
Peningkatan desain BF untuk meningkatkan kehidupan kampanye dibahas dalam artikel ini. Desain tungku yang tepat adalah dasar untuk pengoperasian yang andal, kinerja metalurgi, produktivitas tinggi yang berkelanjutan, masa pakai kampanye yang panjang, dan ketersediaan lebih dari 98%.
Desain BF telah mengalami banyak peningkatan dalam beberapa dekade terakhir dan kampanye lebih dari 20 tahun sekarang telah diperoleh. Armor bosh, stack, dan throat adalah area desain yang penting di masa lalu, tetapi saat ini penerapan stave tembaga, pendingin pelat tembaga, grafit dan SiC di tumpukan bosh, belly, bawah dan tengah, dalam kombinasi dengan pendingin stave besi cor di tumpukan atas ditambah pelindung tenggorokan memungkinkan operasi kampanye yang panjang dan produktivitas yang tinggi. Namun sekarang ada penekanan pada pentingnya desain dasar dan perapian yang kokoh.
Desain BF yang canggih memerlukan efisiensi tinggi dan sistem pendingin berkapasitas tinggi serta instrumentasi dan kontrol yang canggih. Sistem seperti itu mencakup sistem instrumentasi dan kontrol untuk memantau proses, operasi, dan kinerja lapisan.
Desain dan dimensi BF
Desain BF adalah untuk mengatasi reaksi dan metalurgi. Biasanya bosh dan poros BF mengalami erosi oleh kokas sedangkan bagian bawah dan perapian mengalami erosi oleh HM. Harus dipasang berdiri bebas, cangkang tipis, dan struktur struktur yang kokoh sepenuhnya dioptimalkan untuk menahan stres dan retak akibat kelelahan termal, bahkan menjelang akhir kampanye BF.
Desain cangkang BF berdiri bebas terbaru adalah dengan menara akses. Desain mekanik yang canggih biasanya didasarkan pada analisis distribusi tegangan yang komprehensif. Penggunaan baja tahan retak memastikan persyaratan perawatan serendah mungkin.
Filosofi desain BF berorientasi pada kinerja maksimal dengan memastikan bahwa selama kampanye, profil internal tetap sedekat mungkin dengan profil seperti pada saat peluncuran. Desain dioptimalkan berdasarkan analisis berbagai mekanisme serangan termal, kimia, dan mekanis per area. Mekanisme serangan ini diprediksi tergantung pada campuran bahan baku yang dipilih, praktik pembebanan, dan parameter proses lainnya. Secara umum, desain lapisan difokuskan pada pembentukan lapisan terak dan material beban yang dipadatkan yang mengurangi efek mekanisme serangan ini secara signifikan.
Area-area yang penting untuk mencapai tujuan nilai maksimal BF harus diidentifikasi dan perhatian khusus perlu diberikan untuk penguatan area-area tersebut.
Profil tungku diputuskan berdasarkan pengalaman yang diperoleh dari sudut pandang profil dan hasil pengoperasian, keausan refraktori bodi tungku, pengoperasian yang stabil, dan karakteristik lain dari BF skala besar yang ada.
Ketinggian poros biasanya merupakan kompromi antara persyaratan yang berlawanan. Untuk efisiensi bahan bakar, diinginkan untuk memperpanjang kontak gas/padat, sehingga penggunaan panas sensibel dan daya reduksi gas dapat mendekati batas teoritis. Juga sangat penting untuk memiliki ketinggian poros BF di atas nilai tertentu untuk memastikan bijih besi memasuki zona kohesif dengan tingkat metalisasi maksimum, sehingga perapian tidak menjadi dingin dan menimbulkan masalah dalam peleburan.
Selanjutnya untuk BF volume yang lebih tinggi, sebagai aturan, volume dalam BF diperluas dengan meningkatkan diameter BF dengan tinggi tungku dipertahankan hampir tidak berubah. Dilihat dari pengalaman yang diperoleh dari hasil operasional yang diperoleh di masa lalu, biasanya dianggap bahwa mengingat volume dalam tertentu, BF yang tinggi kecil dan diameter besar lebih baik daripada yang tinggi dan diameter kecil dalam hal permeabilitas dan efisiensi penyadapan
BF tenggorokan
Kegagalan pelindung tenggorokan memiliki efek merugikan yang signifikan pada distribusi beban pada jalur stok dan langsung di bawahnya. Ini menghasilkan penurunan beban yang tidak teratur dan stabilitas proses yang terganggu. Oleh karena itu desain pelindung tenggorokan perlu dioptimalkan sehubungan dengan ketahanan terhadap spalling, fluktuasi suhu, retak tegangan, kelelahan, dan abrasi/erosi.
Untuk poros atas (area tenggorokan), pendingin stave biasanya digunakan untuk mempertahankan profil tungku dan untuk mencegah gangguan distribusi beban yang digabungkan dengan keausan batu bata di bawah pelat pelindung tenggorokan (pemakaian). Pemasangan pelat penyangga berpendingin air atau kotak pendingin untuk sistem pelindung tenggorokan tetap juga telah digunakan untuk mengamankan bagian pelindung.
Tumpuk, perut, dan perut
Area tumpukan dan perut terkena beban panas dan abrasi parah. Area bosh sangat terbebani oleh beban menurun yang dibawanya dan gas raceway di sekitarnya. Jika area ini tidak dirancang dengan benar maka badan pendingin dan lapisan aus ke tingkat kritis terlalu cepat setelah pukulan masuk, menyebabkan risiko pecah. Di area bosh, itu juga berarti bahwa beban dibawa oleh tuyere nose dan jumbo cooler, menyebabkan seringnya berhenti tanpa persiapan. Oleh karena itu, desain bosh dan tumpukan akhir-akhir ini terdiri dari pendingin stave tembaga atau pendingin pelat tembaga dan grafit konduktivitas tinggi bersama dengan grafit silikon pelindung di area atas. Desain ini membantu dalam mentransfer sekitar 95% dari beban panas ke air pendingin sehingga mengamankan suhu kurang dari 50 derajat C dari shell BF. Sistem pendingin air, jumlah dan posisi stave, laju aliran air, instrumentasi, dan sistem pemantauan panas semuanya dioptimalkan sepenuhnya untuk memastikan masa pakai cangkang tungku yang lama dan persyaratan perawatan yang minimal.
Perkembangan stave cooler telah menghasilkan apa yang disebut dengan stave generasi keempat saat ini. Fitur khasnya adalah pipa pendingin tambahan di sudut stave, pipa tambahan berbentuk berkelok-kelok (serpentine) di sisi cangkang dan rusuk penahan yang diperpanjang untuk lapisan tahan api. Ini membuat tembok pelindung menjadi tidak berguna. Para tongkat generasi ketiga telah menunjukkan bahwa keretakan dan keausan yang berlebihan terjadi di sudut-sudut dan ujung atas dan bawah tongkat. Pada generasi keempat, pipa sudut telah dimasukkan untuk menghilangkan masalah ini. Penambahan pipa pendingin berkelok-kelok berfungsi sebagai sistem pendingin cadangan, jika terjadi kerusakan pada pipa pendingin lainnya.
Perkembangan lebih lanjut dari stave generasi keempat adalah dimana lapisan tungku melekat pada stave, diamankan dengan rusuk runcing, di pengecoran itu sendiri. Mempertimbangkan fakta bahwa kecepatan keausan stave metal yang didinginkan adalah sepersepuluh atau kurang dari bata di depan stave metal, ketebalan bata dikurangi menjadi 200 mm, dan ketebalan stave ditingkatkan 400 mm, sehingga masa pakai bata depan dan paranada hampir tidak berubah. Para stave generasi keempat adalah konstruksi unit berdinding tipis yang terbuat dari batu bata yang dicor di dalam stave. Konstruksi unit ini telah menghilangkan kebutuhan akan pekerjaan pemasangan batu bata dan meminimalkan perubahan profil muka panas, berkontribusi dalam stabilisasi operasi BF. Peningkatan pada stave cooler, terutama stave generasi keempat, telah meningkatkan daya tahan stave secara signifikan. Keuntungan umum dari stave generasi keempat adalah (i) perpanjangan umur lapisan refraktori, (ii) pengurangan retak dan keausan yang berlebihan pada stave corner, dan (iii) melawan hilangnya kapasitas pendinginan karena kegagalan pipa oleh penambahan pipa pendingin berbentuk berkelok-kelok.
Dengan tujuan untuk lebih menstabilkan operasi BF melalui pemeliharaan profil muka panas yang stabil, pengurangan ketebalan dinding stave dan perpanjangan umur stave, stave tembaga diperkenalkan.
Stave memiliki keuntungan utama mendinginkan seluruh area cangkang BF, sedangkan pelat pendingin hanya mendinginkan area yang terlokalisasi. Namun, pelat pendingin yang rusak dapat dengan mudah diganti, sedangkan secara praktis tidak mungkin mengganti tongkat tanpa meniup tungku.
Namun keuntungan untuk mendinginkan seluruh area cangkang BF lebih penting, dan kerugian karena tidak dapat dengan mudah menukar elemen pendingin harus diatasi dengan mendesainnya untuk masa pakai yang sangat lama dan aman. Hal ini menyebabkan pengembangan tongkat dengan target waktu hidup yang identik dengan waktu hidup BF dibandingkan 12 hingga 15 tahun dengan tongkat besi tuang yang canggih. Pengalaman dengan tongkat besi cor telah menunjukkan keausan dan kehilangan material, pertama di sudut, dan kemudian di tepi. Itu karena pipa cor harus ditempatkan kira-kira 80 mm dari tepi dan 110 mm dari sudut stave, untuk memenuhi persyaratan pengecoran dan memberikan geometri lentur yang diizinkan. Kondisi ini, bersama dengan konduktivitas besi cor yang relatif rendah, mencegah tepi dan sudut menjadi cukup dingin. Kondisi pendinginan lebih diperparah oleh celah tanpa pendinginan yang relatif lebar antara dua tiang besi cor yang berdekatan. Selain itu, masalah pendinginan diakibatkan oleh lapisan pipa isolasi yang digunakan untuk mencegah pengambilan karbon selama pengecoran, yang menghasilkan suhu sisi panas yang lebih tinggi, menyebabkan keretakan dan peningkatan keausan. Untuk menghindari retak pada sudut dan tepi tiang besi tuang, pipa sudut telah dipasang pada tiang generasi keempat, yang berarti pipa tambahan, lubang di cangkang tanur tinggi, dan kebutuhan air dan energi tambahan.
Masalah ini tidak ada dengan tongkat tembaga yang digulung. Pelat tembaga digulung dengan toleransi yang sempit dan dapat dikerjakan dekat dengan sisinya. Saluran pendingin dapat dibor secara akurat, dan ditempatkan sedekat mungkin dengan tepi dan sudut seperti yang ditentukan oleh ketebalan dinding minimal yang diperlukan untuk menghindari kebocoran di bawah tekanan air. Akhirnya, jarak antar tongkat bisa menyempit, sehingga area kritis dan tidak dingin ini bisa dihilangkan. Mengenai sifat fisik, konduktivitas panas tembaga sepuluh kali lebih tinggi daripada besi tuang dan fakta bahwa, karena kekuatan mekanik tembaga, suhu perlu dijaga di bawah 120 derajat C, berarti lebih banyak panas yang dihilangkan dari BF saat menggunakan tongkat tembaga dibandingkan dengan sistem pendingin tongkat lainnya. Untuk menghindari efek ini, solusi desain telah ditemukan di mana konduktivitas rendah, batu bata tahan api alumina tinggi dipasang di sisi panas tongkat tembaga. Sesuai pengalaman operasi, lapisan akresi yang sangat stabil juga melindungi stave dan menghindari kerugian termal yang tinggi dari BF.
Hasil lapangan dengan tongkat tembaga telah menunjukkan hasil yang sangat baik. Setelah 9 tahun beroperasi, tongkat besi cor umumnya menunjukkan tanda-tanda keausan yang parah, retak dan pipa pendingin yang terbuka, sedangkan tongkat tembaga memiliki penampilan yang hampir tidak digunakan, dengan tepi dan sudut yang tajam. Bahan tembaga yang tersisa telah mempertahankan sifat fisik aslinya setelah periode ini. Aspek teknis utama dari penggunaan tongkat tembaga diringkas sebagai berikut.
- Untuk sistem tongkat tembaga dengan tiga baris tongkat tembaga di perut/area poros bawah dan tongkat besi tuang di area yang tersisa, laju sirkulasi pembuangan panas dan air pendingin sebanding dengan sistem tongkat besi cor murni. Dalam beberapa kasus, penghilangan panas tongkat tembaga bahkan lebih rendah daripada tongkat besi tuang, karena lapisan akresi yang stabil.
- Tampan tembaga, berbeda dengan tongkat besi tuang dan pelat pendingin tembaga, tidak memerlukan lug atau hidung. Tongkat tembaga menyajikan permukaan yang halus ke bagian dalam BF dan tidak mengganggu lapisan muatan, yang biasanya mempengaruhi permeabilitas gas di area dinding.
- Karena lapisan akresi yang stabil terbentuk di depan tongkat tembaga, tidak perlu memasang bahan tahan api yang mahal yang akan digantikan oleh kerak setelah waktu tertentu. Dalam sistem stave tembaga, kemungkinan umur tambahan yang diperoleh oleh bahan tahan api yang mahal dapat diabaikan jika dibandingkan dengan umur keseluruhan yang diharapkan. Oleh karena itu, paranada dapat dipasang dengan refraktori yang murah.
Secara total, BF yang didinginkan dengan stave tembaga, di bagian terkait elemen pendinginnya, sekitar 10% lebih tinggi dalam biaya investasi daripada BF dengan sistem stave klasik, dan 5,4% lebih mahal daripada BF dengan pelat pendingin tembaga yang padat. Ini dikompensasi oleh bahan tahan api yang lebih murah di depan tongkat tembaga dan dengan waktu hidup yang lebih lama dari tongkat tembaga.
Perapian BF
Operasi tanur sembur yang terus menerus dan lancar, serta kualitas kokas yang baik, merupakan prasyarat untuk umur tungku yang panjang. PCI tinggi (injeksi batu bara bubuk) menantang masa pakai perapian karena pengurangan permeabilitas dan peningkatan turbulensi. Volume perapian yang besar dan kedalaman bah mengurangi kecepatan cairan. Kecepatan cairan yang lebih rendah menghasilkan beban panas yang lebih rendah. Beban panas yang lebih rendah menghasilkan suhu lapisan yang lebih rendah dan suhu lapisan yang lebih rendah menghasilkan masa pakai yang lebih lama.
Perapian BF menghadapi proses dan kondisi operasi yang menuntut, oleh karena itu kinerja lapisan perapian sangat penting. Kinerja perapian BF saat ini menjadi faktor pembatas di banyak pabrik yang ada dan kondisi perapian BF menentukan umur kampanye. Aliran cairan menyebabkan keausan yang cukup besar melalui mekanisme seperti erosi dan pelarutan karbon. Selain itu, integritas struktural perapian kemungkinan akan terpengaruh karena pemuaian selama pemanasan dapat menyebabkan perpindahan.
Sebagai langkah-langkah untuk memperpanjang umur perapian, perlu untuk meningkatkan kapasitas pendinginan perapian dan meningkatkan kualitas blok karbon yang digunakan untuk perapian. Untuk bagian dinding samping perapian yang paling banyak mengalami erosi (bagian di bawah setiap lubang keran), tongkat besi tuang atau tongkat tembaga yang menawarkan konduktivitas panas tinggi juga digunakan. Selain itu, suhu air pendingin harus diturunkan. Untuk perapian, sistem pendingin dua langkah atau sistem pendingin berbentuk donat dll. yang laju pendinginannya dapat disesuaikan biasanya digunakan untuk mencegah orang mati menjadi tidak aktif karena pendinginan berlebih. Untuk refraktori bawah, kombinasi blok karbon dan lapisan keramik bagian dalam digunakan. Masa pakai blok karbon telah diperpanjang terutama melalui peningkatan konduktivitas termal dan ketahanan besi cair dari bahan tahan api. Desain lanjutan perapian BF mencakup pendinginan air dasar dan pendinginan jaket cangkang perapian karena ini memberikan lebih banyak ruang di dalam cangkang.
Desain perapian dan lubang keran yang lebih baik
Lubang keran terkena lingkungan yang sangat dinamis. Tidak hanya suhu dan tekanan yang tinggi, serangan bahan kimia cukup besar dan seringnya pengeboran dan penyumbatan lubang keran membuat keadaan menjadi lebih rumit. Merancang lubang keran pamungkas yang mampu memfasilitasi operasi BF untuk masa pakai kampanye lebih dari 20 tahun adalah salah satu tantangan paling berat yang dikenakan pada desainer BF. Saat ini, hasil optimal dapat dicapai dengan pendinginan luar biasa pada cangkang di sekitar lubang keran, desain lapisan yang berlebihan, dan kemampuan pemantauan yang memadai.
Kedalaman bah (jarak dari lubang keran ke permukaan bawah) perapian tampaknya menjadi faktor penentu dalam keausan dinding perapian oleh aliran HM selama penyadapan. Direkomendasikan agar orang yang meninggal itu beristirahat sepenuhnya di dasar perapian atau mengapung sepenuhnya di bak HM. Untuk mencegah keausan 'kaki gajah', apungan sebagian dari orang yang sudah meninggal harus dihindari. Karena keausan bagian bawah seiring berjalannya waktu, sebuah benda yang awalnya bertumpu sepenuhnya di bagian bawah dapat menjadi mengambang sebagian. Oleh karena itu, kedalaman bah harus dipilih sejak awal pada tingkat sedemikian rupa sehingga orang mati dapat mengapung. Kedalaman bah kritis yang dibutuhkan tergantung pada ukuran dan metode operasi BF.
Harus dipertimbangkan bahwa perubahan komposisi beban dapat menyebabkan perubahan situasi dan aliran HM di perapian pada penyadapan, jika ketebalan lapisan beban rata-rata dan dengan demikian tegangan tekan beban pada orang mati diubah. Contohnya adalah perbedaan antara semua operasi kokas, dan operasi dengan laju injeksi minyak atau batubara yang tinggi. Kemungkinan lebih lanjut untuk mencegah keausan lebih lanjut dari dinding perapian di bawah lubang keran adalah dengan meruncingkan jaket perapian dan untuk meningkatkan ketebalan dinding dari lapisan tahan api di area ini.
Teknik penyadapan dan desain lubang keran memiliki pengaruh besar pada kehidupan kampanye BF. Perhitungan model dan percobaan penyadapan dilakukan dalam model air 1:10 (diameter 1,4 m) dari tanur sembur berdiameter 14 m, memiliki tempat tidur penuh yang mensimulasikan orang mati. Dari uji coba ini, direkomendasikan agar BF tidak dikosongkan ke titik di mana gas bisa keluar. Pengamatan laju ini dapat mencegah pembentukan pusaran pemacu keausan di daerah sambungan bawah ke dinding. Interupsi proses penyadapan harus dibuat sesingkat mungkin. Ini mencegah logam cair panas dan tak jenuh, dari zona leleh, bersentuhan dengan lapisan tahan api, di mana ia dapat melarutkan batu bata karbon. Diameter lubang keran harus dijaga tetap kecil, karena ini membantu mengurangi tingkat laju aliran secara keseluruhan.
Pengaruh panjang lubang keran pada tegangan aliran dinding perapian diselidiki dengan perhitungan dan pemodelan. Dengan lubang keran yang lebih panjang, titik serang aliran menjauh ke kiri dan ke kanan lubang keran. Intensitas point of attack berkurang dengan bertambahnya jarak dari tap hole. Oleh karena itu, tujuan pengendalian proses untuk BF adalah untuk menjaga lubang keran selama mungkin untuk menggeser aliran sadapan dari dinding perapian ke bagian dalam perapian.
Desain lubang keran dipasang di salah satu BF, di mana enkapsulasi tembaga tidak hanya membuat daerah lubang keran kedap gas tetapi juga melindunginya dari masuknya air.
Secara umum, bata tap hole harus unggul dalam ketahanan terhadap alkali, spalling, oksidasi, leleh dalam HM, terak, dan pembukaan oleh oksigen. Untuk menstabilkan lubang keran, batu bata AI2O3-C-SiC, dengan daya tahan yang baik, telah dikembangkan dan diterapkan dalam BF. Bahan yang dikembangkan telah menunjukkan kinerja yang sangat baik, dengan pengecualian ketahanan terhadap oksidasi. Selain itu, blok karbon memiliki ketahanan yang lebih rendah terhadap leleh dalam HM dan ketahanan yang lebih rendah terhadap oksidasi dibandingkan bahan AI2O3-C-SiC.
Peningkatan refraktori
Pilihan refraktori dan sistem pendingin yang tepat di setiap zona BF sangat penting untuk masa pakai kampanye BF yang panjang. Desain tahan api sedang dikembangkan secara terus menerus dan hari ini ini terbukti dengan baik sehubungan dengan kampanye produktivitas panjang mereka. Desain dan bahan terbaru diterapkan dalam pendekatan terpadu, dengan mempertimbangkan masa pakai kampanye, operasi proses, persyaratan pendinginan, tata letak pabrik, dan prosedur konstruksi.
Di tumpukan atas, di mana keausannya terutama mekanis, refraktori untuk lapisan BF telah berkembang selama bertahun-tahun dari bata tanah liat api normal, dengan 39% Al2O3, menjadi tanah liat api padat yang dipres kering, dengan sekitar 45% Al2O3 . Keuntungannya untuk area itu adalah ketahanan abrasi yang baik dan ketahanan yang tinggi terhadap oksidasi. Karena ketahanan kejut termal yang buruk merupakan masalah, maka di area kritis tumpukan atas, berbagai jenis pelapis komposit digunakan, yang melibatkan batu bata dengan 60% Al2O3 dan silikon karbida untuk meningkatkan ketahanan kejut termal. Daya tahannya yang memadai, yang hanya dapat ditingkatkan dengan biaya yang jauh lebih tinggi dengan menggunakan batu bata bermutu lebih tinggi, tidak menimbulkan ekspektasi pengembangan baru untuk zona ini.
Zona di bawah tumpukan atas, yaitu bosh, perut, tumpukan bawah hingga ke tingkat tuyere, juga terkena keausan termal dan kimia. Itu berarti keausan oleh suhu tinggi, fluks panas yang tinggi dan berfluktuasi, serta serangan kimia oleh alkali, seng, terak, dll. ditambah dengan abrasi.
Solusi keausan untuk zona ini juga dapat dibagi menjadi solusi termal dan solusi refraktori.
Solusi termal adalah grafit, semi-grafit dan batu bata SiC, dengan batu bata SiC telah menemukan penerimaan untuk zona ini karena kekerasan bahan baku. Di salah satu tanur tinggi, lapisan bosh telah ditingkatkan dibandingkan dengan pelapisan ulang tahun 1980, dari sistem gabungan grafit/semi-grafit ke desain grafit penuh, karena desain refraktori grafit penuh mungkin lebih baik mengatasi suhu tinggi dan fluktuasi suhu.
Dari paralel bosh hingga tumpukan tengah, sistem refraktori adalah kombinasi grafit dan silikon karbida. Tujuan utama grafit adalah untuk mendinginkan silikon karbida ke suhu yang relatif rendah, sedangkan tujuan utama silikon karbida adalah untuk melindungi grafit dari abrasi. Sebagai solusi tahan api untuk bosh, perut dan tumpukan bawah, penggunaan bata korundum sialon khusus telah dikembangkan. Konduktivitas batu bata ini baik, meskipun tidak berbeda jauh dengan suhu dan lebih rendah daripada batu bata silikon karbida. Nilai bata korundum sialon memiliki butiran korundum dan sistem ikatan non-oksida yang mirip dengan batu bata SiC. Hasil operasi yang memuaskan telah dicapai dengan batu bata ini.
Refraktori perapian BF biasanya menentukan masa pakai tungku. Pemilihan bahan, spesifikasi, inspeksi, dan pemasangan yang benar sangat menentukan untuk perapian tungku yang aman dan bebas masalah.
Pada prinsipnya, lapisan tahan api perapian BF yang dibangun dalam dekade terakhir dapat dibagi lagi menjadi desain lapisan tahan api 'hitam' dan 'hitam/putih'. Untuk perapian hitam, blok karbon format kecil atau format besar dengan kualitas variabel digunakan. Desain hitam/putih memiliki lapisan keramik di bagian bawah atau di atas lapisan bawah karbon, dengan dinding perapian berlapis yang terbuat dari blok karbon atau aditif dengan berbagai ketinggian tutup keramik. Definisi lain untuk konstruksi lapisan perapian adalah 'larutan termal', menggunakan refraktori konduktivitas tinggi yang dikombinasikan dengan pendinginan yang kuat, dan 'larutan tahan api', yang melibatkan bahan refraktori dengan konduktivitas rendah.
Varian pelapis 'larutan termal' harus ditingkatkan terkait dengan sifat termo-mekanis dan termokimia. Sifat batu bata, yang dipengaruhi oleh pilihan bahan baku dan proses pembuatan batu bata, sebagian besar bertindak berlawanan arah dan harus dinilai pengaruhnya dalam aplikasi operasi.
Peningkatan mutu modern bata pelapis perapian berdasarkan karbon bertujuan untuk memperbaiki satu sifat yang dianggap penting, jika memungkinkan tanpa memperburuk yang lain. Hal ini dicapai melalui pilihan bahan baku, proses manufaktur dan aditif logam dan/atau keramik dalam campuran mentah. Dengan demikian, berbagai produsen batu bata bekerja dengan cara yang berbeda, seringkali bekerja sama erat dengan pabrik BF dan lembaga penelitian. Berikut ini telah menyebabkan perkembangan baru.
- Pengenalan Al2O3 yang terdistribusi sangat halus dalam matriks ikatan
- Impregnasi dengan larutan koloid SiO2
- Penambahan modifikasi yang mengandung Si atau Si pada matriks ikatan, yang membentuk ikatan SiC dan/atau Si-O-N pada kondisi pembakaran yang sesuai
- Impregnasi tar dengan pembakaran pos
Aditif biasanya tidak digunakan dalam batu bata grafit. Aditif oksida logam berkurang pada suhu pembakaran yang tinggi. Batu bata semi-grafit menjadi berpori mikro oleh aditif tersebut. Ada beberapa batu bata Semi-grafit dengan hanya aditif Si dan SiC dan beberapa di mana bubuk Al2O3 dicampur selama peracikan.
Bata karbon amorf berpori mikro juga diproduksi dari bata karbon amorf tradisional berdasarkan antrasit, dengan penambahan silikon atau modifikasi silikon ke peracikan bata. Al2O3 Juga ditambahkan selama peracikan oleh produsen lain untuk meningkatkan ketahanan terhadap pembubaran oleh HM di bawah jenuh. Kerugiannya, Al2O3 dapat bereaksi dengan alkali yang terinfiltrasi yang mengakibatkan peningkatan volume dan pengelupasan bata, dapat ditoleransi.
Resistensi terhadap pembubaran HM dan infiltrasi HM dianggap lebih penting oleh produsen dan pengguna. Dengan kecenderungan menuju pori-pori yang lebih halus dan menuju jenis batu bata super-mikro-porositas, bahan baku telah dioptimalkan sehubungan dengan persiapan dan kemurnian dalam peracikan. Jika perlu, peracikan juga menggabungkan proporsi grafit yang lebih besar.
Keuntungan potensial yang ditunjukkan adalah (i) konduktivitas termal yang lebih tinggi, (ii) pengurangan panjang balok dalam arah dinding tembus, (iii) bahwa penggunaan semen melepaskan tegangan termal, (iv) konduktivitas termal yang ditingkatkan dari perapian karena batu bata berada dalam kontak dekat dengan tongkat, (v) bahwa porositas rendah, dikembangkan selama pembuatan dengan pemanasan dan tekanan bersamaan, meminimalkan penetrasi air dan besi, dan (vi) ketahanan alkali yang tinggi.
Sebagai solusi tahan api untuk perapian, batu bata yang dimasukkan ke dalam ini dicirikan oleh ketahanan yang tinggi terhadap mekanisme keausan pada suhu tinggi. Diusahakan untuk meminimalkan tingkat keausan sampai penerapan sistem pendingin dari luar. Batu bata karbon tersebut didasarkan pada bahan baku antrasit.
Untuk batu bata antrasit kekuatan tinggi dan kelarutan rendah dalam HM disebutkan sebagai keuntungan. Konduktivitas termal yang rendah, -modulus yang tinggi dan koefisien ekspansi termal yang lebih tinggi dibandingkan dengan grafit, dan ketahanan yang lebih rendah terhadap alkali disebut sebagai kerugian.
Sebuah 'cangkir keramik' juga telah disarankan, dan dipasang di beberapa BF, sebagai solusi tahan api untuk perapian. Dapat dilihat dari perhitungan isoterm, bahwa isoterm 800 derajat C, yang bertanggung jawab atas pembentukan lapisan getas pada refraktori karbon, terletak di dalam material keramik. Dikombinasikan dengan kedalaman tungku yang cukup, cangkir keramik adalah alat pendukung lebih lanjut untuk mencegah keausan blok karbon, terutama 'kaki gajah'.
Instrumentasi yang lengkap dan andal
Karena perapian BF dipandang sebagai faktor kunci untuk durasi kampanye, pemantauan kemajuan keausan di perapian menjadi sangat penting. Pengukuran suhu oleh termokopel digunakan untuk memantau kemajuan keausan di perapian dan termokopel dipasang di kisi-kisi dengan berbagai tingkat di dinding perapian. Termokopel NiCr-Ni biasanya diracuni dalam kisaran suhu di atas 600 derajat C dan kemudian dapat menunjukkan tingkat suhu yang terlalu rendah. Oleh karena itu, termokopel hanya ditempatkan di mana suhu di atas 400 derajat C tidak diharapkan. Masalah ini dihindari dengan menggunakan termokopel yang dapat diganti dengan tabung pelindung yang sesuai.
Perlu dicatat bahwa termokopel hanya menunjukkan keausan lokal dan pemantauan komprehensif hanya mungkin dilakukan dengan termokopel densitas yang sangat tinggi. Secara umum, oleh karena itu, hanya mungkin untuk mendeteksi kursus keausan rata-rata. Metode alternatif untuk memantau kemajuan keausan adalah penggunaan kamera termovisual atau probe fluks panas.
Sebagai program penelitian, serangkaian 12 probe fluks panas telah dipasang di bata perapian dari satu tanur sembur, untuk mengukur kerapatan fluks panas secara langsung. Keuntungan berikut dari probe fluks panas dibandingkan termokopel ditunjukkan.
- Probe fluks panas dapat dipasang di dekat jaket tanur sembur di area yang lebih dingin dari lapisan tahan api. Oleh karena itu daya tahannya lebih tinggi dibandingkan termokopel.
- Lapisan tahan api bata karbon tidak rusak.
- Daripada beberapa termokopel, hanya satu sensor di tempat pengukuran yang diperlukan untuk menentukan kerapatan fluks panas.
- Probe fluks panas bereaksi lebih peka terhadap kerusakan pada bata tahan api.
Perhitungan mengenai distribusi lokal yang optimal dari probe fluks panas telah menunjukkan bahwa jarak antara dua probe 3 m tampaknya cukup untuk kontrol keausan yang andal dan lengkap. Untuk mencapai kepastian yang sama dengan termokopel, ini harus ditempatkan di tengah bata karbon dengan jarak satu sama lain sekitar 1 m. Profil keausan biasanya dihitung berdasarkan data yang diberikan pada kerapatan fluks panas.
Berbagai jenis lapisan perapian dan posisi probe fluks panas ditunjukkan pada Gambar 1.
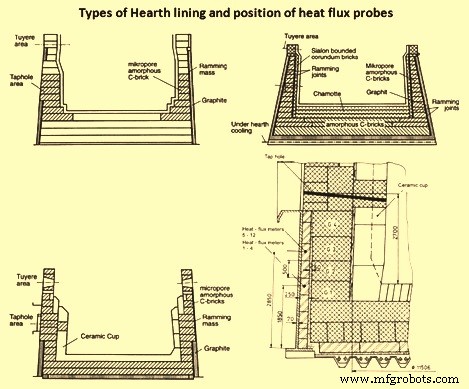
Gbr 1 Berbagai jenis lapisan perapian dan posisi probe fluks panas