Produksi Ferro-Chrome
Produksi Ferro-Chrome
Ferro-chrome (Fe-Cr) adalah paduan yang terdiri dari besi (Fe) dan krom (Cr) yang digunakan terutama dalam produksi baja tahan karat. Rasio di mana dua logam (Fe dan Cr) digabungkan dapat bervariasi, dengan proporsi Cr berkisar antara 50% dan 70%.
Fe-Cr sering diklasifikasikan berdasarkan rasio Cr terhadap karbon (C) yang dikandungnya. Sebagian besar Fe-Cr yang diproduksi adalah 'charge chrome'. Ini memiliki rasio Cr terhadap C yang lebih rendah dan paling sering diproduksi untuk digunakan dalam produksi baja tahan karat. Ferro-alloy Fe-Cr terbesar kedua yang diproduksi adalah 'Fe-Cr karbon tinggi (HC Fe-Cr) yang memiliki kandungan Cr lebih tinggi dan diproduksi dari bijih kromit dengan kadar lebih tinggi. Kadar Fe-Cr lainnya adalah 'Fe-Cr karbon sedang' (MC Fe-Cr) dan 'Fe-C karbon rendah (LC Fe-Cr). MC Fe-Cr juga dikenal sebagai karbon menengah Fe-Cr dan dapat mengandung hingga 4% karbon. LC Fe-Cr biasanya memiliki kandungan Cr minimal 60% dengan kandungan C berkisar antara 0,03% hingga 0,15%. Namun kandungan C dalam LC Fe-Cr bisa mencapai 1%.
Paduan ferro-chrome (Fe-Cr) sangat penting untuk produksi baja tahan karat dan baja khusus yang banyak digunakan dan berkualitas tinggi, biasanya dicirikan oleh ketahanan korosi yang tinggi dan kecenderungan magnetisasi yang rendah. Siklus pemrosesan Fe-Cr melibatkan reduksi kimia bijih kromit.
Smelting HC Fe-Cr ferro-alloy
HC Fe-Cr dan charge chrome biasanya diproduksi dengan proses peleburan konvensional menggunakan reduksi karbo-termik dari bijih kromit (terdiri dari oksida Cr dan Fe) menggunakan electric submerged arc furnace (SAF) atau DC (direct current) open arc electric tungku.
Dalam SAF, energi ke tungku sebagian besar disuplai dalam mode pemanasan resistif. Fitur utama dari mode ini adalah resistivitas listrik terak dan suhu cairan terak yang dipilih secara ketat untuk mengoperasikan proses dengan nyaman. Kedua parameter ini juga memberlakukan beberapa batasan pada proses peleburan dalam hal suhu operasi.
SAF yang digunakan untuk peleburan bijih kromit terdiri dari dua jenis yaitu (i) tipe tertutup, dan (ii) tipe terbuka. Tungku tipe tertutup menawarkan kesempatan untuk mengumpulkan gas kaya karbon mono oksida (CO) untuk pemanasan awal dan pengurangan beban sebagian. Pemanasan awal dan pengurangan beban sebagian menghasilkan pengurangan konsumsi energi listrik yang signifikan. Namun, pengoperasian tungku tertutup menuntut perhatian lebih dalam persiapan beban untuk kelancaran produksi.
Tungku busur DC menggunakan elektroda grafit berongga pusat tunggal sebagai katoda, dengan perapian tungku refraktori yang menghantarkan listrik sebagai anoda. Tungku beroperasi dengan bak terbuka, sehingga tidak ada masalah dengan lapisan penutup, dan butiran halus bijih kromit, bersama dengan batu bara dan fluks diumpankan langsung ke dalam bak melalui elektroda berongga. Tungku memiliki bagian atas yang tertutup. Beberapa karakteristik operasi tungku busur DC adalah (i) penggunaan bijih halus tanpa aglomerasi, (ii) penggunaan reduktor yang lebih murah dan oleh karena itu ada pilihan reduktor yang lebih banyak, (iii) perolehan Cr yang lebih tinggi, (iv) perubahan yang disengaja dalam komposisi muatan direfleksikan dengan cepat dalam terak atau paduan besi, dan (v) operasi tutup atas memungkinkan penggunaan energi off-gas tungku.
Energi ke tungku busur terbuka DC terutama dipasok dalam mode lengkung. Energi ini sebagian besar tidak tergantung pada kimia terak. Dengan demikian memberikan lebih banyak kebebasan dalam pemilihan komposisi terak dan suhu proses. Kebebasan ini telah memberikan tungku busur terbuka DC kemampuan yang lebih besar untuk mengontrol reduksi silika (SiO2) lebih dekat dengan kimia terak. Rentang suhu proses yang cukup besar dapat dicapai pada busur terbuka DC dibandingkan dengan SAF. Oleh karena itu dalam sub-liquidus tungku busur terbuka DC dan terak super panas dapat diproduksi dalam proses peleburan. Terak super panas meningkatkan sampai batas tertentu kinetika reaksi kimia dan pemisahan terak-logam sementara terak sub-liquidus memiliki efek yang menguntungkan pada lapisan tungku. Meskipun perubahan kimia terak dimungkinkan, hal ini umumnya dibatasi oleh keekonomisan proses.
Konversi bijih kromit menjadi Fe-Cr didominasi oleh peleburan SAF di mana elektroda dikubur dalam beban material kental yang terdiri dari bijih kromit, reduktor karbon, terutama kokas, dan fluks untuk membentuk komposisi terak yang benar. Arus listriknya adalah arus bolak-balik 3 fase (AC) dan tungku memiliki tiga elektroda grafit yang dapat dipanggang sendiri dengan jarak yang sama dalam wadah silindris berlapis tahan api dengan lubang keran bawah. Karakteristik SAF untuk peleburan bijih kromit termasuk (i) relatif mudah dikendalikan asalkan muatannya disortir dengan baik untuk mempertahankan lapisan penutup yang permeabel yang memungkinkan pelepasan gas yang dihasilkan dengan mudah, (ii) pengaturan sendiri dengan input daya yang menentukan tingkat konsumsi pengisian (overburden), dan (iii) beberapa pemanasan awal dan pengurangan overburden oleh gas naik panas. SAF dapat berupa bagian atas terbuka, setengah tertutup, atau tertutup dengan efisiensi termal yang lebih baik dan kemampuan untuk memanfaatkan energi dalam off-gas dari tungku bagian atas tertutup.
Peleburan Fe-Cr (Gambar 1) adalah proses yang intensif energi. Energi ditransfer ke proses melalui elektroda karbon yang memanggang sendiri. Elektroda secara lateral ditutupi oleh beban kental yang memiliki resistivitas listrik lebih tinggi daripada rendaman cair di bawah ujung elektroda. Oleh karena itu dipastikan bahwa arus listrik mengalir ke zona reaksi panas. Konsumsi energinya relatif tinggi, dan untuk HC Fe-Cr konsumsi energi listrik bervariasi antara 2000 kWh/ton Fe-Cr dengan pra-reduksi hingga 4000 kWh/ton Fe-Cr tanpa pra-reduksi dan pemanasan awal umpan. Karena kompleksitas struktur umpan dan interaksi listrik-termal-kimia, gradien suhu yang besar ada di tungku dari beberapa ratus di permukaan beban hingga lebih dari 2000 derajat C di sekitar ujung elektroda. Ini mengarah ke berbagai zona di tungku dan mekanisme reduksi yang berbeda.
Gambar 1 Skema peleburan Fe-Cr di SAF
Dalam tungku, satu pelet kromit atau bijih kental mengalami lingkungan suhu yang meningkat saat muatannya turun, dan dikurangi oleh gas CO yang naik dan didorong oleh partikel kokas yang dihubungi. Jelas bahwa profil suhu di SAF memiliki pengaruh besar pada tingkat pengurangan dan efisiensi produksi. Karena kepekaan sistem kontrol elektroda terhadap distribusi suhu tungku, distribusi suhu di dalam umpan dan berbagai zona reaksi biasanya tidak terdistribusi secara simetris. Distribusi suhu yang tidak merata ini menyebabkan kesulitan dalam kontrol tungku, kualitas produk, dan efisiensi tungku.
Zona dalam SAF
Dari penyelidikan SAF yang dipadamkan yang digali, dan tinjauan umum tentang teknologi dan langkah-langkah proses, enam nomor zona reaksi ideal dapat diidentifikasi. Namun posisi yang tepat dari zona ini dapat bervariasi dengan desain tungku dan praktik pengoperasian. Zona tidak perlu mengikuti struktur berlapis sederhana. Diagram skema dari zona reaksi dalam tungku busur terendam untuk produksi Fe-Cr ditunjukkan pada Gambar 2.
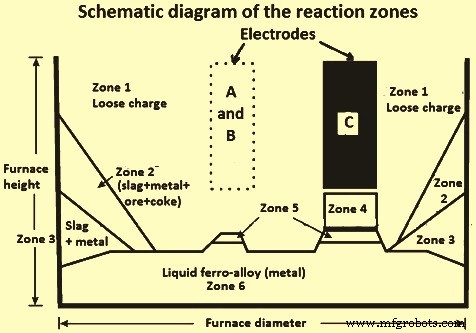
Gbr 2 Diagram skematis zona reaksi dalam tungku busur terendam untuk produksi Fe-Cr
Zona pertama (zona 1) adalah zona tungku atas. Zona ini memiliki muatan lepas yang memanjang dari atas lapisan muatan sampai ke dekat ujung elektroda. Kegiatan yang berlangsung di zona ini adalah (i) pemanasan awal muatan (ii) dekomposisi (kalsinasi) fluks mis. batu kapur, dolomit dll., (iii) gasifikasi bahan berkarbon karena reaksi dengan udara dan karbon di-oksida (CO2), dan (iv) reduksi gas bijih kromit dan metalisasi parsial oksida Fe dan Cr. Faktanya, sebagian besar volume di SAF memiliki beban sinter yang longgar. Waktu retensi rata-rata di zona ini diperkirakan 24 jam, tetapi hanya sekitar 20% pengurangan muatan yang terjadi di zona muatan lepas ini dan tidak ada terak cair yang terbentuk. Bahan beban di zona ini biasanya turun dalam distribusi berbentuk V, dan laju penurunan mencapai maksimum pada posisi antara dinding tungku dan elektroda dan antara elektroda itu sendiri. Data yang terkait dengan profil suhu dan tekanan gas berlebih di zona ini menunjukkan bahwa isoterm 1600 derajat C dicapai hanya dekat dengan ujung elektroda, dan bahwa di atas 1400 derajat C tekanan gas naik dengan cepat, suhu selanjutnya sesuai dengan permulaan terak formasi.
Zona 2 hingga zona 6 ada di bagian bawah tungku. Kegiatan yang berlangsung di bagian bawah tungku adalah (i) pembentukan terak, (ii) pelarutan bijih kromit dalam terak, (iii) reduksi logam dari fase terak dan pembentukan paduan logam, dan (iv) pemisahan paduan dan terak.
Zona 2 terdiri dari sidewall slag, metal, ore, dan coke. Ini memiliki tepi bahan kaku, sebagian menyatu dan sebagian berkurang yang terbentuk berdekatan dengan dinding tungku. Tepian ini paling tebal pada jarak terjauh dari elektroda.
Zona 3 terdiri dari terak dinding samping dan logam. Ini adalah bahan di bawah zona 2 dan mengandung campuran terak dan logam.
Zona 4 adalah di bawah elektroda. Bahan yang ada langsung di bawah ujung elektroda memiliki beberapa ketidakpastian. Zona di bawah salah satu elektroda umumnya tidak terhubung dengan zona serupa di bawah dua elektroda lainnya. Adanya rongga dapat disebabkan oleh kontraksi unggun selama pendinginan tungku. Ada juga kemungkinan terak dan kokas di bawah elektroda. Kemungkinan lain adalah adanya lapisan kokas, yang mengandung campuran mineral gangue yang meleleh, fluks dan magnesia (MgO) dan alumina (Al2O3) yang dibebaskan dari bijih kromit selama reduksinya. Karena pembentukan bahan muatan yang dipadatkan sebagian di sekitar elektroda (zona 2 dan 3) zona reduksi terak aktif dibatasi ukurannya. Waktu tinggal di zona peleburan suhu tinggi, yang didefinisikan di sini sebagai lapisan kokas (zona 4), relatif singkat, mungkin berkisar antara 30 menit hingga 40 menit.
Zona 5 adalah wilayah di mana terdapat wilayah besar bijih kental yang tidak meleleh sebagian bereaksi antara terak dan logam.
Zona 6 adalah wilayah pembentukan lapisan paduan Fe-Cr cair yang berbeda di dasar tungku.
Proses reaksi
Setelah mencapai zona di bawah ujung elektroda (zona 4), semua oksida cair dan reduksi karbotermik dapat terjadi dengan partikel kokas padat, menurut persamaan Cr2O3 + 3C =2Cr + 3 CO. Oksida yang tersisa seperti SiO2, Al2O3, CaO, dan MgO menjadi terak. Terak ini membentuk lapisan cair di atas Fe-Cr cair. Tetesan Fe-Cr cair turun melalui lapisan terak ini dan terkumpul di dasar tungku.
Selama produksi Fe-Cr melalui reduksi karbo-termik, logam Cr yang terbentuk cenderung bereaksi lebih lanjut dengan C yang tersedia untuk membentuk Cr karbida (Cr3C2, Cr7C3, dan Cr23C6). Demikian pula logam Fe bereaksi dengan C yang tersedia untuk membentuk karbida Fe (Fe3C dan Fe2C). Kehadiran karbida ini meningkatkan kandungan C total dari paduan besi Fe-Cr melampaui batas yang ditentukan karena kandungan C teoritis dari karbida ini berkisar antara 5,5% hingga 13,3%. Berikut ini adalah reaksi sederhana yang terjadi selama proses tersebut.
Cr2O3 (l) + 3 C =2 Cr (l) + 3 CO (g)
3 Cr2O3 (l) + 13 C =2 Cr3C2 + 9 CO (g)
2 Cr2O3 (l) + 7 C =Cr4C + 6 CO (g)
7 Cr2O3 (l) + 27 C =2 Cr7C3 + 21 CO (g)
23 Cr2O3 (l) + 81 C =2 Cr23C6 + 69 CO (g)
Fe2O3 (l) + 3 C =2 Fe (l) + 3 CO (g)
3 Fe2O3 (l) + 11 C =2 Fe3C + 9 CO (g)
Fe2O3 (l) + 4 C =Fe2C + 3 CO (g)
Energi bebas Gibbs standar untuk pembentukan karbida ini (melalui reaksi antara Cr2O3 yang terlarut dalam terak dan padatan, C yang tidak bereaksi) telah dipelajari oleh beberapa peneliti. Studi-studi ini menunjukkan bahwa nilai energi bebas Gibbs untuk pembentukan Fe3C lebih rendah daripada untuk pembentukan logam Fe untuk seluruh rentang suhu yang dipelajari (1500 derajat C hingga 2000 derajat C). Oleh karena itu termodinamika mendukung pembentukan Fe3C.
Demikian pula, energi Gibbs reaksi untuk pembentukan Cr3C2 lebih rendah daripada Cr logam untuk sebagian besar rentang suhu (sampai sekitar 1920 derajat C). Cr7C3 dan Cr4C juga dapat terbentuk pada suhu masing-masing 1650 derajat C dan 1550 derajat C. Oleh karena itu, beberapa karbida lebih disukai daripada logam Cr dan Fe selama proses reduksi bijih kromit.
Akibatnya, LC Fe-Cr tidak dapat diproduksi secara langsung melalui reduksi karbo-termik dari bijih kromit. Oleh karena itu, produk dari reduksi karbo-termik adalah HC Fe-Cr atau muatan krom tergantung pada rasio Cr terhadap Fe dalam bijih kromit.
Partikel kokas (jumlah dan ukuran) memiliki pengaruh besar pada hambatan listrik di zona reaksi dan di kolom beban. Oleh karena itu kokas memiliki fungsi ganda, untuk reaksi peleburan dan untuk konversi energi listrik menjadi energi panas. Ini juga membantu menjaga beban permeabel untuk gas CO yang naik.
Pembentukan karbida dalam reduksi karbo-termik Fe-Cr sudah dimulai pada suhu rendah. Temperatur terak hingga 1650 derajat C selalu menghasilkan kandungan C 7% sampai 8% dalam Fe-Cr. Hanya jika kandungan MgO bijih tinggi dan suhu terak melebihi 1700 derajat C maka kandungan C berada pada kisaran 4% hingga 6%. Level C yang lebih rendah tidak dapat dicapai di SAF dan diperlukan langkah proses kedua.
Bahan mentah
Jenis dan kombinasi bahan pengisi (bijih, reduktor dan fluks) yang digunakan untuk peleburan Fe-Cr mempengaruhi operasi tungku dan pada akhirnya mempengaruhi konsumsi listrik. Volume terak yang dihasilkan selama proses tersebut sangat tergantung pada kualitas bahan pengisi yang digunakan untuk proses produksi. Konsumsi energi listrik dipengaruhi oleh volume terak. Semakin tinggi volume terak semakin tinggi pula kebutuhan energi listriknya.
Umpan tungku biasanya terdiri dari bijih kromit (bijih kental, pelet, dan briket), reduktor (antrasit, arang, kokas, dan batubara), dan fluks (kuarsit, dolomit, dan kapur). Partikel bijih kromit tidak selalu memiliki komposisi yang seragam karena ada variasi antara badan bijih, dan bahkan di antara dan di dalam lapisan bijih. Bijih kromit umumnya merupakan bagian dari keluarga kristal spinel, dengan rumus umum (Fe2+, Mg2+)O.(Al3+,Cr3+,Fe3+)2O3.
Melalui kontrol yang cermat terhadap kisaran ukuran dan komposisi bahan pengisi, kondisi tungku yang ideal dapat dipertahankan. Kontrol yang ketat dari jenis bahan baku dan kisaran ukuran memastikan permeabilitas yang baik di dalam unggun yang dikemas, sementara komposisi mempengaruhi sifat terak. Namun demikian, ada sejumlah pra-perawatan muatan yang dapat digunakan untuk meningkatkan stabilitas dan produktivitas tungku.
Proses aglomerasi yang umumnya digunakan untuk bijih kromit meliputi (i) sintering, (ii) pelletizing, dan (iii) briquetting. Juga efisiensi proses produksi Fe-Cr tergantung pada jenis dan pra-kondisi bahan pakan yaitu (i) pemanasan awal, dan (ii) pra-reduksi.
Dalam kasus bijih kromit yang rapuh, menjadi perlu untuk membuat peletnya, setelah penggilingan lebih lanjut jika perlu, dengan pengikat, reduktor dan fluks dan melewatkannya melalui tanur putar di mana mereka dikeraskan (disinter), dipanaskan terlebih dahulu dan direduksi menjadi a derajat sebelum mengisi ke SAF.
Muatan bijih kromit ke tungku terutama dalam bentuk bijih lump dan/atau pelet. Dalam kasus bijih benjolan, materialnya terdiri dari partikel kromit yang dikelilingi oleh batuan induk yang dipadatkan. Pelet biasanya dibuat dari konsentrat bijih kromit yang telah diaglomerasi dan diolah untuk membentuk partikel bulat. Ukuran butir dan struktur mikro dari bijih kromit bervariasi dari butiran bulat padat dalam gumpalan hingga butiran acicular yang sangat retak dalam hal pelet. Rentang ukuran partikel gumpalan, pelet, dan kokas dikontrol untuk memaksimalkan permeabilitas lapisan.
Metode lain untuk pengolahan bijih halus adalah dengan pra-reduksi kiln di mana butiran halus kromit yang tidak diaglomerasi dan batubara berbiaya rendah, dengan fluks digunakan sebagai umpan ke kiln. Dalam metode ini, aglomerasi diri butiran halus dicapai dekat dengan pembuangan dari kiln dimana muatan menjadi pucat di zona suhu tinggi sekitar 1.500 derajat C. Derajat reduksi yang sangat tinggi dicapai (80 % hingga 90%) sehingga mengurangi beban pada tungku listrik hilir (SAF atau busur DC) yang pada dasarnya menjadi tungku peleburan.
Pendekatan yang lebih baru, dan yang sedang dipasang oleh beberapa pabrik, lagi-lagi dengan pelletizing. Pelet diproduksi dengan kokas yang disertakan dan ini disinter dan sebagian direduksi pada sistem sintering sabuk baja. Dari sana, pelet dikirim ke kiln poros pra-pemanasan yang biasanya ditempatkan di atas SAF dan yang beroperasi sebagai tempat umpan langsung, memanfaatkan panas off-gas dari tungku. Lump ore, coke dan flux juga diarahkan ke feed bins.
Selain di atas, ada beberapa pendekatan lain untuk persiapan bijih kromit untuk peleburan. Ini termasuk sintering perapian putar dan pra-reduksi pelet, dan pra-pemanas unggun terfluidisasi untuk butiran halus kromit.
Proses produksi
Fe-Cr pada dasarnya diproduksi oleh reduksi karbo-termik yang berlangsung pada suhu tinggi. Bijih kromit direduksi oleh batubara dan kokas untuk membentuk paduan Fe-Cr. Panas untuk reaksi ini dapat berasal dari beberapa bentuk, tetapi biasanya dari busur listrik yang terbentuk di antara ujung elektroda di bagian bawah tungku dan perapian tungku. Busur ini menghasilkan suhu sekitar 2.800 derajat C. Dalam proses peleburan, sejumlah besar listrik dikonsumsi.
Proses produksi Fe-Cr sangat intensif energi listrik karena semua panas yang dibutuhkan untuk reaksi reduksi endotermik dan untuk mencapai kesetimbangan termodinamika dalam tungku disuplai melalui energi listrik saja. Dengan demikian energi listrik merupakan input yang paling vital dalam proses tersebut.
Penyadapan bahan dari tungku berlangsung sebentar-sebentar. Ketika jumlah Fe-Cr yang cukup telah terakumulasi di perapian tungku, lubang keran dibor terbuka dan aliran paduan cair dan terak mengalir turun melalui palung ke dalam chill atau sendok. Fe-Cr cair mengeras dalam coran besar, yang dihancurkan, diayak, dan dikemas atau diproses lebih lanjut.
Berikut ini adalah karakteristik penting dari proses produksi Fe-Cr dalam SAF.
- Reduksibilitas bijih kromit penting untuk efisiensi proses. Hal ini ditentukan oleh mineraloginya (rasio MgO/Al2O3), bentuk struktural MgO dalam bijih kromit, ukuran butir kromit, tingkat distribusi butir dalam bijih dan suhu leleh bijih. Bijih perlu memiliki porositas karena reduksi keadaan padat dari bijih kromit sangat penting karena reaksi antara gas dan padatan berpori. Juga, bijih harus memiliki kekuatan mekanik yang cukup untuk menahan abrasi dan penghancuran untuk mencapai zona reduksi tungku. Temperatur leleh yang tinggi dari bijih, jika reduksi yang baik dalam keadaan padat ada, memungkinkan lebih banyak waktu untuk bijih dikurangi sebelum mencapai zona leleh. Ini berarti lebih sedikit kehilangan Cr2O3 pada terak.
- Pemulihan Cr terutama bergantung pada kemampuan mereduksi bijih kromit. Dari masukan Cr ke tungku, selain Cr yang dipulihkan menjadi paduan besi, neraca utamanya dilaporkan ke terak dan sebagian lagi ke debu tungku. Dalam kasus bijih keras dan padat, bagian debu rendah, tetapi tergantung pada reduksi bijih dan ukurannya, kandungan Cr2O3 terak dapat meningkat. Karena reduksi bijih kromit dalam keadaan padat adalah signifikan, bijih halus dapat digunakan dalam tungku. Bijih kromit halus sangat mudah direduksi dalam bentuk padat sebelum dilebur, menghasilkan kandungan Cr2O3 dalam terak dalam kisaran 1,5% hingga 4%. Juga penting bahwa pemisahan sempurna antara paduan besi cair dan terak selama penyadapan sehingga Fe-Cr cair yang menjadi terak minimal untuk optimalisasi perolehan Cr.
- Reduksi yang baik dan terutama reduksi solid state membantu dalam pemanfaatan lebih banyak gas CO untuk reduksi bijih kromit. Rasio MgO/Al2O3 dalam terak yang sama dengan 2,1 sesuai dengan titik leleh terak paling bawah yang menghasilkan konsumsi energi minimum untuk bagian terak yang akan dicairkan. Namun, karena adanya beberapa Cr2O3 dalam terak dan oksida lainnya, rasio MgO/Al2O3 memiliki nilai tipikal 2,2. Ini juga menghasilkan pengurangan SiO2 menjadi Si yang lebih rendah. Karena reduksi SiO2 menjadi Si sangat intensif energi, ada penghematan energi yang baik pada akun ini juga.
- Pengurangan pada suhu yang lebih rendah dengan rasio MgO/Al2O3 yang tinggi pada hasil slag menjadi pembentukan jumlah karbida bantalan C yang lebih tinggi. Kehadiran karbida Cr seperti Cr3C2 dan Cr7C3 dengan Cr23C6 yang lebih sedikit menunjukkan reduksi keadaan padat yang lebih baik dari bijih kromit. Rasio Cr/Fe juga berperan dalam penentuan kandungan C dari Fe-Cr. Karena Cr memiliki afinitas yang lebih tinggi untuk membentuk karbida daripada Fe, rasio Cr/Fe yang lebih tinggi berarti kandungan C yang lebih tinggi dalam Fe-Cr.
- Rasio MgO/Al2O3 yang tinggi dalam terak dan terak dasar menghambat reduksi SiO2 menjadi Si. Temperatur yang lebih tinggi diperlukan untuk mereduksi SiO2. Cr2O3 dan FeO tereduksi dalam keadaan padat dan pada suhu yang lebih rendah, sehingga sangat kecil peluang bagi SiO2 untuk tereduksi. Sekali lagi, kandungan Si yang rendah adalah akibat dari reduksi Cr2O3 dan FeO dalam keadaan padat dan suhu rendah.
- Normalnya kandungan belerang (S) dan fosfor (P) dari bijih kromit tidak tinggi. Oleh karena itu S dan P dalam Fe-Cr sebagian besar berasal dari reduktor. Kokas yang memiliki kandungan S dalam kisaran 0,6% hingga 1% berkontribusi dalam kandungan Fe-Cr a S sebesar 0,014% hingga 0,025%. Untuk desulfurisasi, slag dasar, atmosfir pereduksi dan suhu yang lebih tinggi sehubungan dengan defosforisasi diperlukan. Kondisi ini memang ada. Untuk defosforisasi persyaratan termasuk terak dasar, suhu yang lebih rendah dan atmosfer pengoksidasi. Dari semua ini, hanya kondisi terak dasar yang tersedia. Peningkatan kandungan Si dari paduan ferro menunjukkan atmosfer yang berkurang. Meskipun sebagian besar P masuk ke dalam ferro-alloy, kebasaan terak yang tinggi dapat mengakibatkan penurunan kandungan P.
- Komposisi terak dalam kondisi normal tidak berpengaruh besar terhadap kandungan Cr2O3 terak. Kandungan Si yang tinggi dalam ferro-alloy dapat mereduksi Cr2O3 yang terlarut dalam terak melalui reaksi silico-termik dan pada gilirannya kandungan Si dari Fe-Cr menurun, tetapi reaksi ini hanya signifikan pada kandungan Si yang tinggi. Pada kondisi ini warna terak akan menjadi lebih terang.
Produksi LC Fe-Cr
LC Fe-Cr biasanya diproduksi dari HC Fe-Cr atau charge chrome. Produksi LC Fe-Cr biasanya dilakukan dengan menambahkan bijih kromit atau dengan meniup oksigen (O2) dalam HC Fe-Cr. Namun, proses ini tidak menarik karena suhu tinggi (sekitar 2100 derajat C) yang diperlukan untuk menurunkan kandungan C sampai dalam spesifikasi LC Fe-Cr serta karena hilangnya Cr yang terjadi selama proses. Oleh karena itu, metode penurunan C dari HC Fe-Cr ini sebagian besar digunakan untuk produksi MC Fe-Cr dan LC Fe-Cr sebagian besar diproduksi oleh proses produksi metalotermik.
Dalam proses produksi metalotermik, reaksi reduksi dilakukan dengan logam tertentu yang memiliki energi Gibbs negatif. Oleh karena itu, reduktor logam yang sesuai secara teknis yang diproduksi dalam jumlah besar adalah aluminium (Al), magnesium (Mg), mangan (Mn) dan silikon (Si). Konsumsi stoikiometrik reduktor logam ini per ton Cr adalah 0,519 ton untuk Al, 0,701 ton untuk Mg, 1,585 ton untuk Mn dan 0,405 ton untuk Si, meskipun dalam praktik sebenarnya konsumsi dapat sedikit berbeda untuk mencapai pemulihan Cr yang ditargetkan. Namun, reduktor Si dan Al lebih ekonomis untuk digunakan. Di antara keduanya, proses reduksi silico-thermic lebih populer daripada proses alumino-thermic untuk produksi LC Fe-Cr.