Ferro-silikon (Fe-Si) adalah paduan besi yang memiliki unsur utama besi (Fe) dan silikon (Si). Paduan besi biasanya mengandung Si dalam kisaran 15% sampai 90%. Kandungan Si yang biasa terdapat dalam Fe-Si yang beredar di pasaran adalah 15%, 45%, 65%, 75%, dan 90%. Sisanya adalah Fe, dengan sekitar 2% unsur lain seperti aluminium (Al) dan kalsium (Ca).
Fe-Si diproduksi secara industri dengan reduksi karbo-termik silikon dioksida (SiO2) dengan karbon (C) dengan adanya bijih besi, besi tua, skala pabrik, atau sumber besi lainnya. Peleburan Fe-Si merupakan proses kontinyu yang dilakukan dalam electric submerged arc furnace (SAF) dengan elektroda self-baking.
Fe-Si (kualitas khas 65%, 75% dan 90% silikon) terutama digunakan selama pembuatan baja dan dalam pengecoran untuk produksi baja C, baja tahan karat sebagai agen deoksidasi dan untuk paduan baja dan besi tuang. Ini juga digunakan untuk produksi baja silikon yang juga disebut baja listrik. Selama produksi besi cor, Fe-Si juga digunakan untuk inokulasi besi untuk mempercepat grafitisasi. Dalam pengelasan busur Fe-Si dapat ditemukan pada beberapa pelapis elektroda.
Reaksi reduksi yang ideal selama produksi silikon Fe-Si adalah SiO2+2C=Si+2CO. Namun reaksi sebenarnya cukup kompleks karena zona suhu yang berbeda di dalam SAF. Gas di zona terpanas memiliki kandungan silikon mono oksida (SiO) yang tinggi yang diperlukan untuk dipulihkan di lapisan muatan luar jika pemulihan Si ingin tinggi. Reaksi pemulihan terjadi di lapisan muatan luar di mana mereka memanaskan muatan ke suhu yang sangat tinggi. Gas keluar dari tungku mengandung SiO2 yang dapat diperoleh kembali sebagai debu silika. Cairan formasi Si melewati beberapa reaksi antara. Ini dijelaskan nanti di artikel. Fitur karakteristik utama dari produksi Fe-Si dapat diringkas dalam tiga poin berikut.
- Gas di zona terpanas SAF memiliki kandungan gas yang mengandung Si yang tinggi yang diperlukan untuk diambil kembali di lapisan muatan luar jika ingin mendapatkan kembali Si tinggi.
- Reaksi pemulihan Si di lapisan muatan luar memanaskan muatan ke suhu yang sangat tinggi dan membuat muatan lengket yang tidak mudah mengalir ke zona terpanas.
- Gas dari tungku mengandung sejumlah besar debu yang terdiri dari SiO2.
Skema flowsheet untuk proses produksi Fe-Si diberikan pada Gambar 1.
Gambar 1 Skema flowsheet proses produksi Fe-Si
Bahan baku
Fe-Si diproduksi dengan melebur bahan yang mengandung Fe dan bahan yang mengandung Si biasanya dalam SAF. Fe dalam bentuk bijih besi, skrap baja atau skala pabrik dan Si biasanya dalam bentuk gumpalan kuarsit. Ini dikombinasikan dengan bahan berkarbon seperti batu bara atau kokas minyak bumi dan bahan pengisi seperti serpihan kayu. Kuarsit adalah sumber Si dalam proses karbo-termik. Kemurnian kuarsit biasanya lebih rendah daripada jenis endapan kuarsa lainnya dan biasanya cocok untuk produksi Fe-Si.
Furnaceability adalah istilah kualitas industri internasional umum yang digunakan untuk kuarsit. Kuarsit memiliki kemampuan tungku yang baik ketika semua kriteria kimia dan fisiknya sedemikian rupa sehingga menjadikannya bahan baku silika yang sesuai untuk produksi Fe-Si dengan kandungan Si tinggi pada tingkat kinerja proses yang tinggi. Persyaratan kualitas mutlak dari bahan baku kuarsit adalah yang diperlukan untuk mencapai proses yang akan dioptimalkan dan mencakup (i) kimia, (ii) ukuran bahan (biasanya 10 mm hingga 150 mm), (iii) kekuatan mekanik, ( iv) kekuatan termal, dan (v) sifat pelunakan.
Kimia dan ukuran adalah spesifikasi yang paling umum digunakan oleh semua produsen Fe-Si untuk menentukan kuarsit. Persyaratan kimia berkaitan dengan kandungan unsur pengotor terutama unsur-unsur seperti Al, Ca, titanium (Ti), boron (B), dan fosfor (P). Biasanya, unsur-unsur yang lebih mulia dari Si (misalnya Al dan Ca) berakhir di produk, sedangkan komponen volatil masuk ke off-gas. Namun, reaksi dalam tungku jauh lebih rumit dari itu, dan distribusi unsur-unsur dalam bahan baku juga menentukan ke mana unsur-unsur itu pergi. Beberapa unsur terutama alkali seperti natrium (Na) dan kalium (K) justru dapat menurunkan titik leleh kuarsit. Umumnya, persyaratan bahan baku berhubungan dengan persyaratan produk. Produksi Fe-Si biasanya memiliki persyaratan yang memungkinkan kandungan unsur yang paling sulit lebih tinggi.
Persyaratan ukuran dapat bervariasi untuk tanaman yang berbeda dan berkisar dari 10 mm hingga 150 mm. Namun, beberapa produsen memiliki spesifikasi untuk ukuran yang lebih sempit. Beberapa produsen Fe-Si fokus pada, atau mengukur kekuatan mekanik dan kekuatan termal, meskipun ini biasanya tidak termasuk dalam spesifikasi ke pemasok. Selain itu, beberapa produsen fokus pada sifat pelunakan kuarsit. Selanjutnya, persyaratan tambahan dapat ditentukan oleh masing-masing produsen, menurut apa yang paling optimal untuk operasi tertentu.
Sifat mekanik kuarsit mempengaruhi pengurangan ukuran bahan baku selama produksi di tambang, transportasi dan penyimpanan sebelum pengisian. Bahan halus yang dihasilkan menimbulkan masalah bagi proses karbotermik karena dapat menurunkan permeabilitas muatan dan menghalangi aliran gas dari bagian bawah tungku ke bagian atas di mana gas SiO bereaksi dengan C yang tidak bereaksi dalam muatan untuk membentuk SiC, yang merupakan reaksi penting dalam tungku. Selain itu, beberapa gas SiO mengembun dan membentuk campuran lengket SiO2 dan Si cair. Hilangnya gas SiO melalui saluran off gas dan penurunan perolehan kembali Si dapat disebabkan oleh permeabilitas muatan yang rendah.
Denda didefinisikan oleh dua kriteria yang berbeda. Dalam konteks ini, denda didefinisikan sebagai material yang berukuran kurang dari 2 mm, yang merupakan yang paling kritis untuk proses tersebut. Denda kurang dari 2 mm menurunkan permeabilitas muatan. Denda juga dapat didefinisikan sebagai bahan dengan ukuran gumpalan di bawah spesifikasi (misalnya -10 mm). Adapun sifat mekanik, sifat termo-mekanis terutama terkait dengan pembentukan butiran halus, namun dalam kasus ini, pembentukan butiran halus terjadi di dalam tungku karena sifat termo-mekanis yang buruk mengakibatkan disintegrasi kuarsit sebagai akibat dari panas yang ekstrim dalam tungku. Idealnya, kuarsit kental adalah untuk mempertahankan ukuran aslinya saat bergerak ke bawah melalui muatan, sampai kuarsit mulai melunak dan meleleh di bagian bawah tungku dekat dinding rongga.
Meskipun, sebagian besar kuarsit cenderung hancur sampai tingkat tertentu, itu tidak dihancurkan dan menghasilkan terlalu banyak butiran halus yang menurunkan permeabilitas muatan seperti dijelaskan di atas. Pengurangan ukuran ini juga, dalam kasus-kasus ekstrim, menghasilkan efek letupan di mana dalam beberapa kasus pecahan kuarsit dapat terlempar ke udara. Kuarsit dengan stabilitas termal rendah yang hancur dalam muatan juga dapat berkontribusi pada pembentukan terak di tungku.
Sifat pelunakan kuarsit adalah sisi lain dari sifat termo-mekanis. Suhu pelunakan, atau interval pelunakan, adalah suhu di mana kuarsit mulai meleleh. Ini lebih rendah dari titik leleh kuarsit pada 1723 derajat C. Suhu pelunakan harus sedekat mungkin dengan suhu leleh kuarsit untuk mencapai proses ideal di mana kuarsit turun ke dinding rongga sebelum mulai meleleh dan menetes. kuarsit cair menetes dari dinding rongga ke dalam rongga, di mana reaksi pembentukan Si berlangsung. Unsur-unsur alkali (dan pada tingkat yang lebih rendah alkali tanah) diketahui mempengaruhi suhu leleh kuarsit. Perlu dicatat bahwa kuarsit yang mulai melunak atau bahkan meleleh terlalu tinggi di tungku, menciptakan massa lengket, yang menggumpal dengan partikel lain dan menjadi konduktif listrik dan mengubah jalur listrik di tungku dan bahkan mengurangi kekuatan busur.
Tungku busur terendam untuk produksi Fe-Si
Fe-Si kadar komersial dengan kadar Si 15% umumnya diproduksi di tanur tinggi (BF) yang dilapisi dengan batu bata api asam. Fe-Si dengan kandungan Si yang lebih tinggi biasanya diproduksi di SAF. Ukuran SAF yang menghasilkan Fe-Si diberikan dalam bentuk beban listrik dan bervariasi dari 1-2 MVA hingga lebih dari 40 MVA. Ukuran SAF biasanya terdiri dari diameter hingga 10 meter dan kedalaman 3,5 meter. Energi listrik disuplai melalui arus bolak-balik 3 fasa (AC) oleh tiga elektroda yang terendam jauh di dalam muatan. Konsumsi energi spesifik biasanya mencapai 9 MWh – 10 MWh (megawatt hour) per ton Fe-Si yang dihasilkan (75% Si). Untuk beroperasi secara efisien dan mengurangi biaya tetap unit, SAF diperlukan untuk berjalan terus menerus, 24 jam per hari.
Panas yang diperlukan untuk reaksi yang sangat endotermik dari reduksi SiO2 dihasilkan langsung dalam muatan muatan SAF sebagai akibat dari aliran arus dengan pemanasan resistif, dan oleh pemanasan busur yang terbakar di kamar gas yang terletak di dekat ujung elektroda. Struktur internal tungku dan distribusi suhu di zona reaksi memiliki hubungan yang erat dengan proporsi panas yang dihasilkan dalam tungku berdasarkan prinsip pemanasan resistansi dan pemanasan busur. Salah satu elemen struktural terpenting dari tungku Fe-Si direndam dalam elektroda 'Soderberg' yang dapat membakar sendiri muatan yang membawa listrik yang dibutuhkan untuk proses tersebut. Pembakaran busur listrik dan kondisi suhu zona reaksi memiliki hubungan yang erat dengan posisi ujung elektroda di dalam tungku. Arus memanaskan sebagian muatan hingga sekitar 2000 derajat C di bagian terpanas. Pada suhu tinggi ini, SiO2 direduksi menjadi Si cair.
Distribusi suhu zona reaksi tidak dikenakan pengukuran langsung, tetapi untuk memberikan kondisi listrik dan suhu yang benar dari proses, perlu dilakukan slip elektroda secara sistematis. Posisi optimal elektroda mengarah pada minimalisasi indikator ekonomi proses. Dalam periode operasi SAF yang baik dan stabil di zona reaksi adalah kondisi untuk evolusi berkelanjutan produk baru dari reduksi SiO2. Proses ini memiliki sifat siklus dan terkait dengan peleburan dan penetrasi periodik cairan SiO2 di dalam ruang busur.
SAF memiliki tudung di bagian atas tungku yang mengarahkan gas panas melalui cerobong asap ke sistem pembersihan gas. Bahan baku yaitu kuarsit, bahan bantalan Fe, dan bahan bantalan C diangkut pada ban berjalan dan disimpan secara terpisah di tempat sampah. Bahan baku berupa batch campuran yang terdiri dari kuarsit, reduksi C, dan pembawa Fe ditimbang, digabungkan dalam proporsi yang diperlukan, dicampur dan dimasukkan ke dalam tungku melalui tabung pengisian. Tabung ini terletak dengan outlet menuju elektroda. Jumlah tabung yang mengelilingi elektroda berbeda dari tungku ke tungku. Bahan yang diisi berada pada tingkat yang sama dengan lantai di luar tungku yang dikelilingi oleh tudung yang memiliki gerbang penyalaan di bagian yang berbeda dan bagian ini dapat dibuka selama periode penyalaan.
Proses produksi Fe-Si
Bahan baku dibebankan ke tungku dari atas. Tinggi?arus, listrik bertegangan rendah dikirim melalui transformator dan masuk ke tungku melalui elektroda C. Prosesnya sangat hemat energi, membutuhkan sekitar 9.000 kWh hingga 10.000 kWh (kilowatt hour) listrik untuk menghasilkan satu ton 75% Fe-Si.
SAF yang digunakan untuk produksi Fe-Si biasanya dioperasikan dalam siklus-siklus dengan operasi utama yaitu stoking, charging dan tapping. Selama penyalaan, kerak tipis di atas muatan rusak dan muatan lama didorong menuju elektroda. Tagihan baru kemudian diletakkan di atas tagihan lama.
Siklus pengisian stoking adalah siklus operasional. Stoking dilakukan dengan mesin penggerak khusus yang dilengkapi dengan batang stoking yang dipasang di depan mesin. Beban yang tidak merata dapat didistribusikan dengan mesin melalui gerbang stoking. Bahan bermuatan lama di permukaan didistribusikan menuju elektroda di mana depresi telah terbentuk di sekitar elektroda. Depresi ini dibentuk oleh zona reaksi panas di dalam rongga.
Dalam tungku, muatan dipanaskan hingga sekitar 1815 derajat C. Pada suhu itu, kuarsit bergabung dengan C dalam reduktor membentuk gas karbon monoksida (CO) dan melepaskan Si, yang membentuk paduan dengan Fe cair. Fe-Si cair terakumulasi di dasar tungku. Kandungan elemen jejak dari bahan mentah (termasuk bahan reduksi kuarsit dan elektroda) dibawa ke produk.
Secara berkala, sekitar pada interval waktu yang sama paduan besi cair disadap ke dalam sendok, melalui salah satu lubang keran di lapisan tungku. Taphole terletak di transisi antara lapisan samping dan bawah tungku. Jumlah lubang keran bervariasi dari tungku ke tungku. Lubang keran biasanya dibuka secara mekanis dan ditutup dengan campuran tanah liat khusus.
Gas lepas dilewatkan melalui pabrik pembersih gas untuk menghilangkan debu yang kandungan utamanya adalah SiO2 terkondensasi amorf. Debu ini umumnya digunakan sebagai bahan pengisi pada beton, keramik, refraktori, karet dan aplikasi lain yang sesuai. Sebuah tungku menghasilkan sekitar 0,2 ton hingga 0,4 ton debu SiO2 per ton paduan besi. Gas yang dibersihkan terutama mengandung CO, sulfur di oksida (SO2), karbon di oksida (CO2), dan oksida nitrogen (NOx). Panas gas dapat dipulihkan dalam sistem pemulihan panas limbah.
Reaksi
Proses produksi Fe-Si terdiri dari proses temperatur tinggi dimana SiO2 direduksi dengan C menjadi Si dan CO (g). Reaksi keseluruhan dari proses ini didasarkan pada reaksi karbo-termal yang diidealkan sebagai reaksi yang diberikan di bawah ini.
SiO2(s) + 2C(s) =2Si (l) + 2CO (g) Delta H pada 2000 derajat C =687 kJ/mol
Tungku Fe-Si biasanya dibagi menjadi dua zona yaitu (i) zona panas bagian dalam, dan (ii) wilayah bagian luar yang lebih dingin. Si diproduksi di zona dalam. Kondisi kesetimbangan untuk produksi Si diberikan oleh reaksi berikut.
SiO (g) + SiC (s) =2Si (l) + CO (g)
Temperatur untuk produksi Si adalah sekitar 2000 derajat C. Maka tekanan kesetimbangan SiO untuk reaksi di atas pada 1 atmosfer adalah 0,5 atmosfer. Untuk mendapatkan perolehan kembali Si yang tinggi, SiO ini harus diperoleh kembali di bagian tungku yang lebih dingin. SiO diperoleh kembali melalui reaksi dengan C atau dengan kondensasi. SiO yang tidak diperoleh kembali hilang sebagai debu SiO2.
Kemampuan bahan C untuk bereaksi dengan SiO disebut reaktivitas. Dalam kasus reaktivitas tinggi, banyak C bereaksi dengan SiO untuk membentuk SiC di zona luar. Jika reaktivitasnya rendah, C bebas dapat mencapai zona dalam. Kemudian lebih sedikit Si dan lebih banyak SiO dan CO yang dihasilkan. Karena reaktivitas rendah di zona luar, lebih banyak SiO yang terkondensasi. Karena kondensasi memasok panas, ada batas untuk kondensasi. Bila batas tersebut terlampaui maka SiO keluar dari tungku. Jika reaktivitasnya rendah, keseimbangan C dalam muatan harus dikurangi untuk menghindari endapan SiC. Dalam kasus seperti itu, pemulihan Si berkurang.
Dalam operasi praktis selalu ada kehilangan silikon dalam gas. Hal ini terutama disebabkan oleh hilangnya spesies gas SiO. SiO2 terbakar bersama dengan CO2 di udara berlebih di atas muatan. Deskripsi proses yang lebih akurat lebih kompleks dan melibatkan banyak reaksi antara dan memperumit situasi jauh dari apa yang dijelaskan oleh reaksi di atas. Bagian dalam SAF dapat dibagi menjadi zona suhu tinggi (sekitar 2000 derajat C) dan suhu rendah (kurang dari 1815 derajat C), di mana reaksi yang berbeda mendominasi. Di zona suhu tinggi di sekitar ujung elektroda, reaksi berikut terjadi.
2SiO2 (s, l) + SiC(s) =3SiO (g) + CO (g) Delta H pada 2000 derajat C =1364 kJ/mol
SiO2 (s, l) + Si (l) =2SiO (g) Delta H pada 2000 derajat C=599 kJ/mol
SiO (g) + SiC (s) =Si (l) + CO (g) Delta H pada 2000 derajat C =167 kJ/mol
Yang paling lambat dari ketiganya mungkin adalah reaksi yang menghasilkan SiO (g) yang mengkonsumsi sebagian besar energi listrik yang dikembangkan. Si dapat diproduksi melalui reaksi pada suhu di atas 1815 derajat C. Gas SiO bergerak ke atas dalam tungku dan diperoleh kembali baik dengan reaksi C dengan bahan seperti yang diberikan di bawah ini atau dengan kondensasi di mana suhunya cukup rendah (kurang dari 1800 derajat C) . Dua reaksi terakhir yang diberikan di bawah ini dapat dibalik.
SiO (g) + 2C (s) =SiC (s) + CO (g) Delta H pada 1800 derajat C =-78 kJ/mol
3SiO (g) + CO (g) =2SiO2 (s, l) + SiC (s) Delta H pada 1800 derajat C =-1380 kJ/mol
2SiO (g) =SiO2 (s, l) + Si (l) Delta H pada 1800 derajat C =– 606 kJ/mol
Dua reaksi penghasil kondensat terakhir sangat eksotermik dan merupakan faktor utama bagaimana panas diangkut ke atas dalam tungku. Kondisi kesetimbangan untuk reaksi lain ditunjukkan pada Gambar 2.
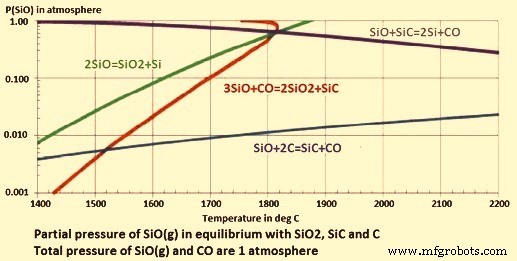
Gbr 2 Tekanan parsial SiO (g) dalam kesetimbangan dengan SiO2, SiC dan C
Di bagian atas pengisian tungku, suhu dapat bervariasi antara 1000 derajat C sampai 1700 derajat C. Hasil silikon industri yang khas adalah sekitar 85 % dalam tungku yang dioperasikan dengan baik. Reaksi pembentukan SIC adalah reaksi perolehan kembali SiO yang lebih disukai di atas 1512 derajat C. Di bawah suhu ini, gas SiO umumnya ditangkap oleh dua reaksi penghasil kondensat terakhir. Suhu memiliki pengaruh yang besar pada kondisi kesetimbangan untuk reaksi ini. Jika suhu di bagian atas sekitar 1620 derajat C (tekanan parsial SiO=0,1 atm.) dan pengambilan SiO utama melalui kondensasi, maka rendemen Si sekitar 80%.
Pemurnian dan casting Fe-Si
Kotoran dalam paduan besi cair seperti Al dan Ca dapat dihilangkan dengan oksigen (O2) dan udara saat paduan berada dalam tahap cair di sendok sebelum pengecoran. Paduan besi cair dapat disadap dari tungku ke dalam sendok baja berlapis tahan api.
Fe-Si cair dituangkan dari ladle ke dalam cetakan besi tuang datar yang besar. Cetakan dibuat dengan menambahkan lapisan halus Fe-Si pada permukaan cetakan. Bahan cor dikeluarkan dari cetakan ketika telah didinginkan ke tingkat di mana kekuatan bahan cukup tinggi untuk dikeluarkan dan ditumpuk dalam tumpukan untuk pendinginan lebih lanjut. Setelah pendinginan dan pemadatan, Fe-Si dihancurkan dan disaring untuk menghasilkan ukuran gumpalan yang dibutuhkan. Dalam proses penghancuran, beberapa butiran halus dihasilkan. Bahan halus tersebut selanjutnya dapat digiling menjadi bubuk, dikombinasikan dengan bahan pengikat, dan dibentuk menjadi briket. Lelehan juga bisa digranulasi.
Semua kadar Fe-Si diproduksi dengan menggunakan proses yang pada dasarnya sama, tetapi langkah-langkah tambahan tertentu diperlukan untuk menghasilkan kadar Fe-Si yang lebih murni. Nilai tersebut diproduksi menggunakan bahan baku yang mengandung jumlah pengotor yang lebih rendah. Selain itu, penyempurnaan Fe-Si cair untuk menghilangkan pengotor yang tidak diinginkan dan penambahan elemen paduan khusus terjadi pada ladle. Pengolahan lebih lanjut untuk menghasilkan Fe-Si dengan kemurnian lebih tinggi ini dikenal sebagai metalurgi sendok. Kelas khusus 15% Fe-Si untuk aplikasi medium padat biasanya diproduksi dengan melebur kembali 75% Fe-Si dengan skrap baja di tungku busur listrik dan dituangkan ke dalam semprotan air bertekanan tinggi.