Proses Pembuatan Besi Karbida
Proses Pembuatan Besi Karbida
Besi karbida (Fe3C) adalah senyawa sintetik dengan titik leleh tinggi, non-piroforik, dan sangat magnetis yang diperoleh dalam bentuk butiran. Ini terdiri dari sekitar 90% total besi (Fe) dan sekitar 7% total karbon (C). Penggunaan utama produk ini adalah sebagai muatan logam selama pembuatan baja untuk substitusi logam panas (HM), besi tereduksi langsung (DRI), atau skrap baja. Proses karbida besi melibatkan konversi partikel bijih besi halus yang dipanaskan sebelumnya menjadi karbida besi. Ini mereduksi bijih besi menjadi besi karbida dalam reaktor fluidized bed, dengan mengontak bijih besi dengan gas proses yang terutama terdiri dari metana (CH4) dan hidrogen (H2).
Proses pembuatan karbida besi pada awalnya dirancang dan dikembangkan di Hazen Research Inc. di Golden, Colorado, AS oleh wakil presiden teknis Dr. Frank M. Stephens. Proses ini melibatkan reduksi partikel bijih besi halus yang dipanaskan sebelumnya (0,1 mm menjadi 1,0 mm) dalam reaktor unggun terfluidisasi sirkuit tertutup dengan gas proses yang dipanaskan sebelumnya yang mengandung CH4, H2, CO (karbon mono oksida), CO2 (karbon di oksida) dan uap air ( H2O) pada 600 derajat C. Reaktor batch berdiameter 50 mm digunakan untuk pengujian laboratorium. Ini diikuti dengan pengujian terus menerus pada reaktor berdiameter 600 mm. Sampel bijih besi dari beberapa negara diuji di Hazen. Produk ini berhasil diubah menjadi baja oleh MEFOS di Swedia dalam tungku oksigen dasar (BOF) pada tahun 1979.
Setelah uji laboratorium awal di Hazen Research, Inc., Dr. Stephens mengajukan permohonan paten dan dikeluarkan pada 11 Oktober 1977 'US Patent No. 4.053.301' oleh kantor Paten Amerika Serikat. Pada tahun 1985 Dr. Stephens pensiun dan memperoleh hak paten atas karbida besi. Dia membentuk perusahaan dengan nama 'Iron Carbide Development Corporation' (ICDC) dan mulai memasarkan prosesnya. Pada tahun 1988, ICDC dan perusahaan Australia dari PACT Resources, Pty. Ltd. bergandengan tangan untuk membentuk 'Iron Carbide Holdings, Limited' (ICH). Pekerjaan pengembangan tambahan kemudian dilakukan di pabrik percontohan yang dibangun pada tahun 1989 dari pabrik vanadium yang menganggur yang terletak di Wundowie, Australia Barat. Reaktor di pabrik percontohan berdiameter 1830 mm, dioperasikan dengan kedalaman dasar sekitar 3700 mm. Ini menghasilkan sekitar 25 ton per hari.
Selama tahun 1989, ICH memproduksi 310 ton besi karbida di pabrik percontohan. Besi karbida dijual kepada tujuh pelanggan. Lima perusahaan (Nucor, North Star Steel, Mitsubishi, Qualitech Steel dan Cleveland Cliffs) membeli lisensi atau opsi untuk menggunakan teknologi ini. Nucor Corporation mengonversi karbida besi dari pabrik percontohan di pabrik baja mereka di Darlington, Carolina Selatan, AS menggunakan tanur busur listrik (EAF) 32 ton. Besi karbida disuntikkan dengan kecepatan hingga 90 kg/menit di EAF menggunakan tangki gunite yang ada.
Nucor memperoleh lisensi pada tahun 1992. Ini memberi wewenang kepada PLS Engineering di Denver, Colorado, (sekarang bagian dari Harris Group) untuk membangun pabrik di Point Lisas, Trinidad untuk memproduksi 300.000 ton besi karbida per tahun dan pada akhir tahun 1994 pabrik tersebut sedang beroperasi. Nucor memulai pembangunannya pada 1993, namun sayangnya dana terbatas untuk PLS. PLS menghabiskan dana tersebut sebelum menyelesaikan desain pabrik. Nucor menyelesaikan desainnya. Selain itu, Nucor meminimalkan pengeluaran untuk beberapa peralatan pabrik, termasuk penukar panas.
Pabrik dimulai pada akhir September 1994. Namun, perusahaan mengalami masalah dengan kompresor untuk gas proses dan pabrik shutdown. Itu membiarkan air pendingin mengalir. Selama periode ini, seorang teknisi melepas sensor level di kolom menara yang dikemas untuk kalibrasi ulang dan karenanya alarm untuk level cairan diblokir. Dia memberi tahu ruang kontrol. Salah satu katup yang dipasang di menara yang dikemas, meskipun dalam posisi tertutup, bocor dan tidak diketahui selama beberapa hari. Begitu ditemukan, kolom itu langsung dikeringkan, tetapi kerusakan telah terjadi. Air telah melewati pipa dan bercampur dengan debu oksida besi dan sangat mencemari penukar panas. Nucor menghabiskan lebih dari satu tahun mencoba untuk membersihkan penukar tetapi tidak berhasil.
Nucor juga menghadapi beberapa masalah operasional lainnya di pabrik. Masalah-masalah tersebut adalah (i) pipa berukuran kecil untuk gas proses yang membatasi aliran gas hingga nilai maksimum 65% dari kapasitas desain, (ii) seringnya pemutusan segel gas untuk pelat tuyere reaktor unggun terfluidisasi, (iii) meninggalkan sistem pemanas bijih karena gagal karena abrasi yang telah menyebabkan kompromi kimia dalam reaktor dan selanjutnya membatasi kualitas dan kuantitas produk, (iv) tangki pengumpul yang terlalu kecil untuk scrubber, (v) tidak dapat diandalkan sistem untuk mengatur aliran produk melalui pendingin produk yang memerlukan perawatan yang tinggi, (vi) sistem pengangkat pneumatik yang tidak dapat diandalkan untuk produk yang membutuhkan perawatan yang sering, (vii) pengumpan ulir berukuran sangat kecil yang memasok umpan bijih ke pabrik, dan (viii ) kelenjar pengepakan yang tidak memadai dari pengumpan sekrup yang bocor parah.
Nucor menghabiskan empat tahun bekerja dengan masalah ini, tetapi pada tahun 1998, karena jatuhnya harga baja, mereka menutup pabrik. Pabrik tersebut kemudian dibongkar pada tahun 2002. Terlepas dari semua kesulitan yang dihadapi di atas, 357.712 ton besi karbida diproduksi di pabrik yang menunjukkan bahwa proses tersebut layak secara teknis. Kegagalan mekanis yang dihadapi telah menekankan persyaratan fasilitas yang memadai dan andal.
Upaya kedua untuk memproduksi besi karbida dalam skala komersial dilakukan oleh Qualitech Steel Corporation di Corpus Christi, Texas, di mana ia membangun pabrik baru. Qualitech memperoleh lisensi untuk memproduksi besi karbida dari ICH, tetapi mengubah prosesnya, ketika Mitsubishi Corporation mendanai proyek tersebut dan ingin menggunakan dua reaktor dan model jaringan pipa, sistem distribusi gas proses dalam reaktor fluidized bed.
Pabrik Texas baru saja ditugaskan ketika perusahaan induk bangkrut pada bulan Maret 1999, dan pabrik tersebut hanya memproduksi beberapa ribu ton besi karbida sebelum ditutup pada tahun 1999 dan dihancurkan pada tahun 2004.
Frank A. Stephens, putra Dr. Frank M. Stephens, Jr. memperoleh kepemilikan eksklusif hak atas proses karbida besi pada tahun 2010. Selama bulan-bulan awal tahun 2011, ia membentuk International Iron Carbide LLC. Perusahaan memiliki hak atas 35 paten. Perusahaan baru secara menyeluruh menganalisis masalah yang dihadapi di pabrik di Trinidad dan Corpus Christi dan menyiapkan solusi terdokumentasi untuk masalah tersebut. Namun, banyak dari solusi tersebut dianggap sebagai hak milik. Beberapa solusinya adalah (i) desain yang kokoh dari shell and tube heat exchanger, (ii) perubahan desain sistem gas proses untuk mencapai kapasitas penuh, (iii) peningkatan desain reaktor fluidized bed dan sistem distribusi gas membuat reaktor lebih toleran terhadap penghentian instalasi, (iv) desain baru untuk segel gas untuk pelat tuyere di reaktor unggun terfluidisasi menjadikannya segel gas ganda, (v) pengenalan sistem pemanas kilat untuk umpan bijih yang mencakup transfer pneumatik bahan panas, persediaan padatan minimal untuk start dan stop yang cepat, penghapusan offset sudut untuk menghindari abrasi, dan konstruksi modular untuk memfasilitasi perawatan, (vi) perubahan dalam desain scrubber membuat scrubber memadai untuk mencapai kapasitas penuh, (vii) penyederhanaan dalam sistem penanganan produk yang menghilangkan sistem angkat untuk produk yang memasuki pendingin produk, dan (viii) penggunaan eduktor untuk memindahkan padatan menggantikan konveyor mekanis.
Seperti pada hari ini tidak ada pabrik yang bekerja untuk produksi besi karbida. Namun, International Iron Carbide telah menggunakan pengalaman mereka (baik positif maupun negatif) yang diperoleh dari dua pabrik generasi pertama di Trinidad dan Texas dan telah mengembangkan desain untuk pabrik generasi kedua yang didasarkan pada banyak pelajaran yang didapat. International Iron Carbide secara aktif mencari wirausahawan untuk berkolaborasi dalam membangun pabrik generasi kedua.
Proses
Proses pembuatan besi karbida bersih dan sederhana. Tiga langkah proses utama dari proses (Gbr 1) meliputi (i) pemanasan bijih besi hingga sekitar 700 derajat C, (ii) mengontak bijih besi panas dengan campuran gas H2 dan CH4 bertekanan pada suhu sekitar 600 derajat C dan tekanan absolut sekitar 4,5 kg/sq cm dalam reaktor fluidized-bed untuk konversi oksida besi menjadi besi karbida dengan gas pereduksi kuat, dan (iii) mendinginkan produk hingga sekitar 65 derajat C.
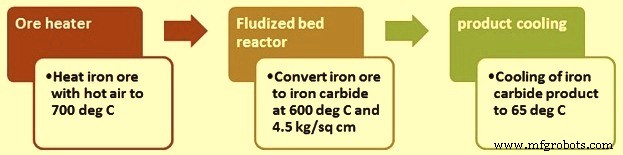
Gbr 1 Tiga langkah proses dari proses
Bijih besi biasanya hematit, yang biasanya memiliki komposisi 62% sampai 65% Fe, 1% sampai 5% gangue dan 1 sampai 6% kadar air. Bijih yang disimpan biasanya tidak perlu ditutup, jika cuaca memungkinkan. Faktor-faktor yang mempengaruhi keputusan untuk menutupi mineral tersebut atau tidak adalah biaya bahan bakar, kandungan kelembaban alami, dan iklim.
Dari tempat penyimpanan bijih, bijih diangkut ke silo (day bin). Silo menyimpan bijih yang cukup untuk mengoperasikan pabrik selama sekitar 24 jam. Konveyor kecepatan variabel mengukur dan mengontrol jumlah bijih yang diumpankan ke sistem pemanas bijih.
Pemanas bijih adalah 'flash heater' yang terdiri dari tiga siklon secara seri. Pemanas bijih memanaskan bijih hingga 710 derajat C dengan mengontak bijih dengan gas pengoksidasi panas yang meninggalkan tungku atau pembakar. Peningkatan suhu bijih besi berguna untuk proses tersebut. Ini membantu proses karena (i) menghilangkan kelembaban dari umpan bijih, dan (ii) mengoksidasi sebagian magnetit jika ada dalam bijih menjadi hematit. Ini membantu reaksi dalam reaktor, karena hematit berubah lebih cepat menjadi besi karbida daripada magnetit. Pemanas bijih melepaskan bijih besi panas ke dalam hopper pengunci umpan, di mana bijih tersebut ditahan sebelum diumpankan ke reaktor unggun terfluidisasi.
Pasokan bijih panas ke reaktor diumpankan melalui dua gerbong kunci yang beroperasi secara paralel. Hopper kunci dilapisi dengan bahan tahan api. Mereka memiliki dasar piramida atau kerucut (hopper). Biasanya, salah satu hopper memberi makan reaktor selama sekitar satu jam. Hopper bekerja sedemikian rupa sehingga saat salah satu mengisi reaktor, hopper lainnya terisi.
Hopper pengumpan juga mencegah masuknya gas pengoksidasi ke dalam reaktor. Setelah itu bijih panas dibersihkan dengan N2 dan tekanan ditingkatkan, bijih panas terus menerus diumpankan ke reaktor pada tingkat yang memungkinkan satu hopper kosong dan diturunkan tekanannya pada saat hopper lainnya diisi.
Reaktor unggun terfluidisasi dan reaksi proses
Reaktor unggun terfluidisasi menggunakan butiran bijih besi yang membatasi kebutuhan untuk perlakuan awal seperti sintering atau pelletizing. Bahan umpan yang ideal untuk reaktor adalah bijih besi halus hematit dengan ukuran berkisar antara 0,1 mm sampai 1,0 mm.
Diameter dalam reaktor sekitar 12 meter dan beroperasi pada suhu sekitar 600 derajat C. Reaktor menerima gas proses yang pada dasarnya terdiri dari H2 dan CH4. H2 dimasukkan untuk menjaga tekanan di dalam reaktor freeboard pada tekanan absolut 4,5 kg/cm2. Kompresor mendaur ulang gas proses untuk mendapatkan kecepatan superfisial 0,92 m/detik.
Dalam reaktor fluidized bed, H2 dan CH4 mengubah bijih besi yang dipanaskan menjadi besi karbida. Oksigen bergabung dengan H2 membentuk air dan karbon (C) bergabung dengan besi membentuk besi karbida. Kimia umum dari proses ini dijelaskan oleh persamaan 3 Fe2O3 + 2 CH4 + 5 H2 =2 Fe3C + 9 H2O. Reaksi ini adalah semacam ringkasan keseluruhan dari semua reaksi yang terjadi dalam proses. Reaksi berlangsung dalam laju yang relatif lambat, dan tempat tinggal di dalam reaktor jauh lebih banyak bila dibandingkan dengan proses dalam tungku pembuatan baja. Namun, waktu ini dapat dikurangi dengan mengubah suhu dan tekanan.
Pada bagian fase gas reaksi terdapat tiga komponen dasar yaitu (i) H2, (ii) O2 (oksigen), dan (iii) C. Ketiga unsur ini saling berinteraksi membentuk H2, H2O, CO, CO2 dan CH4. Konsentrasi masing-masing senyawa ini tergantung pada beberapa faktor seperti (i) rasio massa masing-masing unsur, (ii) suhu sistem, (iii) tekanan sistem, dan (iv) sampai batas tertentu waktu dalam di mana elemen-elemen tersebut bersentuhan.
Salah satu dari dua reaksi gas utama adalah reaksi reformasi uap CH4 + H2O =CO + 3 H2. Dalam reaksi ini, gas alam bereaksi dengan uap membentuk gas H2 yang diperlukan untuk proses tersebut. Reaksi gas penting kedua adalah perpindahan gas air seperti yang dijelaskan dalam persamaan CO + H2O =CO2 + H2.
Ketika reaktan ditempatkan bersama-sama pada suhu tinggi diperoleh campuran gas yang mengandung H2, H2O, CO, CO2 dan CH4. Campuran ini juga mengandung sedikit N2.
Reaksi gas cenderung dikatalisis oleh adanya besi metalik dan/atau besi karbida. C dan H2 untuk reaksi di atas berasal dari reagen yang ditambahkan dalam proses. O2 diekstraksi dari bijih melalui reaksi Fe2O3 + 3H2 =2Fe + 3H2O. Dengan mengontrol konsentrasi relatif C dan H2 dalam gas proses, dimungkinkan untuk mempromosikan penghilangan O2 dari bijih dan penambahan C untuk membentuk besi karbida.
Reaksi untuk membentuk besi karbida sedikit endotermik, sehingga dapat mempertahankan suhu sekitar 600 derajat C, dan perlu memanaskan gas proses hingga 633 derajat C.
Reaktor beroperasi sebagai reaktor fluidized bed fase padat. Gelembung gas terbentuk dari proses gas di fluidized bed. Reaktor menerima bijih di satu sisi dan mengeluarkan produk dari ukuran lain. Penyekat internal reaktor membawa padatan di dalam reaktor. Baffle meminimalkan hubungan arus pendek padatan dalam reaktor dan menciptakan distribusi waktu tinggal yang lebih seragam untuk padatan. Waktu retensi padatan adalah sekitar 16 jam.
Komposisi gas proses, suhu dan tekanan terus dipantau oleh instrumentasi proses. Proses tersebut menghasilkan produk non-piroforik, yang kemudian dapat disimpan dan diangkut.
Reaktor menghasilkan sekitar 42 ton per jam produk (besi karbida). Produk dikeluarkan secara terus-menerus melalui hopper kunci dari reaktor dan siklon off gas sebelum dilewatkan melalui pendingin produk.
Salah satu masalah proses sebelumnya adalah produksi C (jelaga) bebas yang tidak diinginkan, yang berasal dari reaksi Boudouard, yang membentuk C dan CO2 dari CO (2CO =C + CO2). Namun, International Iron Carbide telah mengidentifikasi kondisi proses yang tidak memungkinkan pembentukan C bebas, dan masih menghasilkan besi karbida berkualitas tinggi. Spesifik dari kondisi ini bersifat kepemilikan.
Reaktor melepaskan produk besi karbida melalui dua hopper kunci yang (mirip dengan yang digunakan untuk memberi makan bijih besi panas ke reaktor. Hopper kunci melepaskan produk ke tekanan atmosfer. Bahkan, sementara satu menerima produk panas di sekitar 3,5 kg/cm2 tekanan, yang lain membuang produk ke perangkat pendingin (pendingin produk) pada tekanan atmosfer.Besi karbida meninggalkan hopper kunci di sekitar 590 derajat C dan didinginkan hingga sekitar 65 derajat C dengan melewati produk Kuantitas produk dalam pendingin produk dikendalikan dengan sabuk konveyor pelepasan kecepatan variabel yang membawa besi karbida ke pemisah magnetik kering. Pemisah magnetik menghilangkan sejumlah besar gangue yang dibebaskan (biasanya 50%), yang, bagaimanapun, tergantung pada kualitas bijih besi yang diumpankan ke proses.
Sebuah lembar aliran skema dari proses karbida besi diberikan pada Gambar 2.
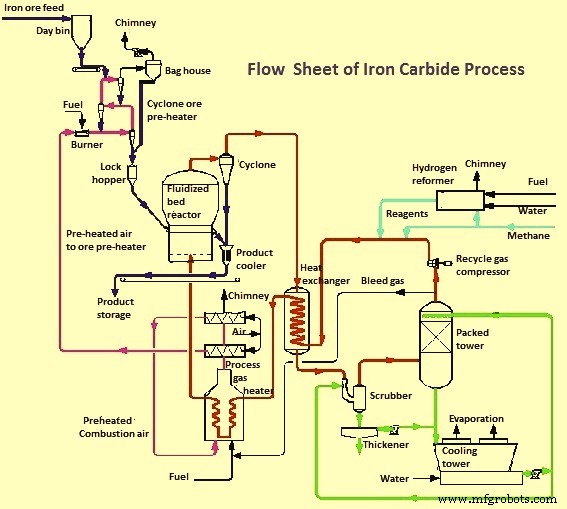
Gbr 2 Diagram alir skema proses pembuatan karbida besi
Sistem pengolahan gas
Gas proses meninggalkan reaktor pada suhu sekitar 590 derajat C. Gas melewati empat siklon paralel (siklon reaktor) yang dilapisi dengan bahan tahan api. Siklon ini menghilangkan sebagian besar padatan yang terperangkap dari gas proses yang meninggalkan reaktor. Denda yang dikumpulkan oleh siklon (sekitar 36 ton per jam) mengalir secara gravitasi ke tempat penampung gelombang sebelum didaur ulang ke reaktor. Setiap padatan tambahan melewati serangkaian hopper kunci sebelum memasuki pendingin produk, yang mendinginkan padatan di bawah 65 derajat C (biasanya sekitar 40 derajat C), dan akhirnya menambahkan padatan ke produk dari reaktor yang didinginkan di bagian hulu pemisah magnetik.
Gas proses yang meninggalkan siklon reaktor melewati empat penukar panas paralel (penukar panas gas proses) yang menurunkan suhu gas proses hingga 150 derajat C. Sebuah scrubber venturi dan kolom unggun yang dikemas (menara yang dikemas) selanjutnya mendinginkan proses gas ke sekitar 30 derajat C untuk menghilangkan air yang dihasilkan dalam reaktor dan menghilangkan partikel halus yang tersisa yang tersuspensi dalam gas proses yang telah lolos dari siklon. Ini memastikan bahwa jumlah butiran halus dalam gas proses cukup rendah untuk menghindari kerusakan pada 'kompresor daur ulang gas proses'.
Aliran kecil gas proses dikeluarkan dari gas proses resirkulasi (gas pembuangan) meninggalkan bagian atas menara yang dikemas dan sebelum memasuki kompresor gas daur ulang, untuk mencegah akumulasi N2 di sirkuit. Jumlah perdarahan tergantung pada kandungan N2 dari gas alam, jumlah N2 yang masuk ke sistem dengan umpan bijih besi panas yang masuk ke dalam reaktor.
Gas reagen make-up, biasanya terdiri dari H2 dan gas alam, memasuki proses resirkulasi sebelum kompresor. Tekanan freeboard dalam reaktor unggun terfluidisasi mengatur jumlah tepat H2 yang akan dimasukkan ke dalam sistem. Jumlah gas alam yang akan ditambahkan ke gas proses ditentukan oleh konsentrasi CH4 dalam gas proses.
Dua kompresor sentrifugal (kompresor gas daur ulang), satu beroperasi dan yang lain siaga, mendaur ulang gas proses dengan tekanan sekitar 4,20 kg/cm2 pada intake dan sekitar 5,30 kg/cm persegi pada pelepasan. Tekanan diferensial di seluruh kompresor mengatur aliran gas proses ke reaktor.
Empat penukar panas gas-gas, yang mendinginkan gas proses yang berasal dari reaktor fluid bed, memanaskan gas proses yang berasal dari kompresor, hingga suhu sekitar 520 derajat C. Pemanas gas (pemanas gas proses) semakin meningkatkan suhu proses menjadi sekitar 630 derajat C, menggunakan bleed gas dan gas alam sebagai bahan bakar. Gas buang yang berasal dari pemanas menyediakan energi untuk memanaskan udara pembakaran yang dipasok ke pemanas bijih.
Dalam prosesnya, ada dua sistem pendingin air. Satu sistem untuk kontak langsung dengan gas proses (air pendingin kontak langsung"), yang menyediakan air pendingin ke 'venturi scrubber' dan 'packed tower', di mana dalam perangkat ini air bersentuhan langsung dengan gas proses. Sistem pendingin air lainnya adalah sistem pendingin air tidak langsung yang menyediakan air pendingin untuk (i) sistem pendingin produk (pendingin produk), (ii) reformer H2, dan (iii) penukar panas minor lainnya yang digunakan untuk proses tersebut.
Air panas yang meninggalkan menara yang dikemas kembali langsung ke menara pendingin kontak untuk menghilangkan panas, sedangkan air yang meninggalkan scrubber venturi melewati pengental terlebih dahulu, di mana ia disaring untuk menghilangkan padatan yang ada dalam air yang terkontaminasi.
Proses ini biasanya menghasilkan produk yang telah diubah 93% menjadi besi karbida. Komposisi mineralogi dan unsur khas produk terdiri dari Fe3C- 91 % sampai 96 %, Fe (total) – 89 % sampai 93%, Fe (met) – 0,5 % sampai 1 %, SiO2 + A12O3 – 2 % sampai 5 % , Fe3O4 -2% hingga 5%, C (sebagai Fe3C) – 6% hingga 6,5%, dan O (sebagai Fe3O4) – 0,5% hingga1,5%. Besi karbida bersifat magnetis, sehingga jika gangue dibebaskan secara fisik, baik sebelum, selama atau setelah proses karburasi, maka pemisahan magnetik kering dapat dilakukan untuk menurunkan kandungan gangue dalam produk akhir dan dengan demikian meningkatkan kadar besinya.
Meskipun analisis produk dapat bervariasi tergantung pada jenis bijih yang digunakan, tidak ada kandungan belerang yang signifikan. Tingkat fosfor tergantung pada jenis bijih yang digunakan dan biasanya ada dalam produk sebagai P2O5. Tetapi sebagian besar fosfor dipindahkan ke terak tungku, bukan ke dalam produk.
Unsur-unsur sisa dalam bijih biasanya ada dalam produk sebagai oksida, tetapi karena sebagian besar bijih besi memiliki kadar tembaga, nikel, kromium, molibdenum atau timah yang sangat rendah, tidak ada jumlah yang signifikan dari unsur-unsur ini dalam produk akhir. Hasilnya, besi karbida yang dihasilkan sangat bersih dan memberikan metode yang efektif untuk mengencerkan logam sisa selama pembuatan baja, sambil menghindari belerang yang umumnya datang dengan beberapa sumber besi murni.
Konsumsi khas bahan, energi, dan pada batas baterai per ton besi karbida adalah bijih besi – 1,42 ton, gas alam – 350 M kal, listrik – 400 kWh, air – 1,2 cum, nitrogen – 10 cum dan tenaga kerja – 0,22 jam kerja.
Besi karbida juga sangat ramah lingkungan dan memberikan keuntungan lingkungan yang besar. Proses ini mencapai emisi C terendah dari semua proses pembuatan baja murni, hanya menghasilkan 1,09 kg CO2 untuk setiap kg baja yang diproduksi. Ini jauh lebih kecil dari 2,01 kg untuk rute pembuatan baja tanur sembur - tungku oksigen dasar konvensional, 3,09 kg untuk DRI berbasis batubara, dan 1,87 kg untuk rute DRI – EAF berbasis gas alam untuk pembuatan baja. Hanya baja yang seluruhnya terbuat dari skrap yang menghasilkan emisi lebih rendah.
Kelebihan besi karbida dan produksinya
Keunggulan besi karbida dan proses produksinya antara lain sebagai berikut.
- Ini adalah bahan pengisi yang lebih baik daripada bahan lain untuk EAF karena mengandung sekitar 6,0% hingga 6,5% C dan diproduksi dari bijih besi perawan dan karenanya mengandung elemen tramp yang dapat diabaikan. Penggunaan besi karbida dalam proses pembuatan baja mengakibatkan rendahnya kandungan N2 dan H2 dalam baja.
- Ini bukan piroforik sehingga aman dan mudah ditangani.
- Ini adalah bubuk granular padat yang mudah larut dalam baja cair. Itu dapat dengan mudah disuntikkan ke BOF dan/atau EAF, yang langsung larut.
- Proses produksi besi karbida ramah lingkungan karena tidak ada persyaratan aglomerasi bijih besi.
- Satu-satunya produk sampingan dari proses ini adalah air dan CO2, dan jumlah CO2 yang dihasilkan jauh lebih sedikit daripada jumlah yang dihasilkan selama produksi baja oleh proses lain. Selanjutnya, sejumlah besar CO2 meninggalkan reformer dalam aliran gas yang terkonsentrasi, yang mudah diserap dan/atau digunakan kembali untuk tujuan lain.
- Prosesnya menggunakan butiran halus bijih besi, yang lebih murah daripada pelet dan bongkahan bijih besi.
- Kebutuhan briket produk tidak ada.
- Proses beroperasi pada suhu rendah dan merupakan proses yang efisien secara termal.
- Prosesnya adalah proses loop tertutup yang menggunakan 100% reagen yang ditambahkan.
- Prosesnya sederhana, terdiri dari reaktor satu tahap, yang mudah dikendalikan.