Teori dan Praktek Sintering Bijih Besi
Teori dan Praktik Sintering Bijih Besi
Sintering bijih besi adalah istilah umum yang digunakan untuk menggambarkan proses dimana campuran sinter (campuran mentah atau campuran hijau) bijih besi halus, fluks, bahan bakar (coke angin) dan denda pabrik kembali (misalnya skala pabrik, debu tanur tinggi) , dan butiran halus sinter yang dikembalikan, dll.) diubah menjadi bentuk aglomerat tertentu. Ini terdiri dari memanaskan campuran sinter dengan ukuran partikel kurang dari 10 mm ke suhu sedemikian rupa sehingga permukaan setiap butir campuran muatan mulai meleleh dan lelehan yang terbentuk menciptakan jembatan cair antara butiran, yang, setelah pemadatan, memastikan pembentukan bahan berpori padat yang disebut sinter yang memiliki ukuran tersaring biasanya dari 5 mm hingga 30 mm (ukuran atas dapat mencapai hingga 50 mm untuk memenuhi persyaratan lokal), dan yang dapat menahan tekanan operasi dan lingkungan suhu di dalam tanur sembur (BF).
Proses sintering adalah operasi termal yang melibatkan reaksi peleburan dan asimilasi. Tahap pertama dari proses sintering adalah pembentukan lelehan yang melibatkan reaksi antara partikel bijih besi halus dan fluks. Lelehan awal dihasilkan dari melekatnya butiran halus selama pemanasan melalui reaksi antara bijih besi dan fluks. Kemudian, partikel inti sebagian berasimilasi atau dilarutkan ke dalam lelehan primer untuk membentuk lebih banyak lelehan. Sebelum pelelehan sempurna tercapai, suhu sintering turun karena waktu tinggal yang singkat pada suhu maksimum dan kemudian lelehan membeku dan fase mineral mengendap, menghasilkan pembentukan fase ikatan.
Selama proses sintering, reaksi kimia berlangsung pada suhu tinggi dan bijih besi serta fluks digabungkan bersama dan membentuk kue sinter yang terdiri dari bijih besi, silika-ferit kalsium dan aluminium (SFCA), dikalsium silikat dan fase kaca. . Reaksi sintering juga mengatur fraksi volume setiap mineral yang dapat mempengaruhi kualitas sinter dan karenanya, kinerja BF.
Tahap pertama sintering adalah granulasi (nodulization atau pelletization) dari campuran sinter, yang terdiri dari homogenisasi dalam drum pencampur selama beberapa menit dengan penambahan 6% sampai 8% air. Campuran sinter butiran kemudian dimuat ke parut untai sinter permeabel. Bagian atas tempat tidur dipanaskan sampai suhu tinggi dengan bahan bakar gas dan udara ditarik melalui perapian. Setelah waktu pengapian yang singkat, pemanasan bagian atas unggun dihentikan dan zona pembakaran sempit atau bagian depan nyala api (FF) bergerak ke bawah melalui unggun, memanaskan setiap lapisan unggun secara berurutan. Di unggun, butiran dipanaskan sampai kisaran suhu 1250 derajat C sampai 1350 derajat C untuk mewujudkan pelunakan mereka dan kemudian mencair sebagian. Dalam serangkaian reaksi bahan semi cair diproduksi yang, dalam pendinginan berikutnya, mengkristal menjadi beberapa fase mineral komposisi kimia dan morfologi yang berbeda.
Selama proses sintering, pembakaran kokas menghasilkan zona temperatur tinggi (combustion zone) yang bergerak ke bawah melalui sinter bed. Partikel halus bereaksi lebih cepat, dan membentuk lelehan primer yang sebagian melarutkan partikel bijih kasar. Representasi skema penampang unggun sinter dari proses sintering terputus ditunjukkan pada Gambar 1. Kemajuan pembakaran kokas menentukan profil suhu dan pembentukan zona yang berbeda di unggun. Saat zona pembakaran bergerak ke bawah, pemadatan fase leleh terjadi oleh hisap udara, menghasilkan pembentukan zona sinter. Zona di bawah zona pembakaran terdiri dari campuran sinter (bahan yang tidak bereaksi) dan dapat dibagi menjadi dua wilayah. Wilayah tepat di bawah zona pembakaran sesuai dengan dehidrasi campuran sinter oleh gas panas dari zona pembakaran, sedangkan zona di bawah wilayah ini adalah bagian dingin dari lapisan sinter tempat uap dikondensasi.
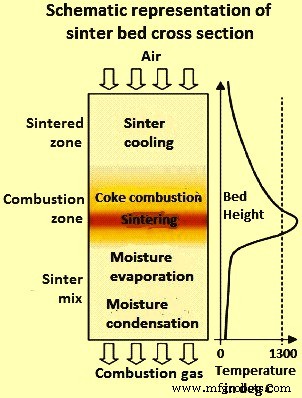
Gbr 1 Representasi skema penampang sinter bed
Pada prinsipnya, reaksi sintering melibatkan reaksi bijih halus dengan fluks yang menghasilkan pembentukan fase leleh yang digunakan selama reaksi padat-cair untuk asimilasi bijih kasar. Lelehan yang terbentuk selama sintering bertindak sebagai fase ikatan. Karena SFCA dianggap sebagai komponen yang paling penting dari fase ikatan karena kelimpahannya di sinter dan pengaruhnya yang signifikan pada kualitas sinter, reaksi sinter secara khusus telah dipelajari berkaitan dengan kontrol konsentrasi dan struktur mikro fase SFCA yang terbentuk selama proses sintering. Volume fase leleh memainkan peran utama selama sintering. Pelelehan yang berlebihan menghasilkan struktur kaca yang homogen, yang memiliki kemampuan mereduksi yang rendah, sedangkan konsentrasi leleh yang sangat rendah menyebabkan kekuatan sinter yang tidak mencukupi, sehingga menghasilkan jumlah halus sinter yang kembali tinggi.
Energi proses disuplai oleh pembakaran angin kokas. Menjelang zona pembakaran, air menguap dan zat-zat yang mudah menguap dikeluarkan. Di zona pembakaran, reaksi berlangsung menghasilkan pembentukan sinter yang kuat. Sebagian besar panas dari gas yang meninggalkan zona pembakaran diserap untuk pengeringan, kalsinasi dan pemanasan awal lapisan bawah unggun. Ketika zona pembakaran mencapai dasar unggun, proses selesai dan kue sinter panas dikeluarkan dari jeruji dan dipecah secara kasar dalam penghancur panas.
Sintering adalah proses yang berkelanjutan. Untai sinter dibentuk oleh serangkaian palet, masing-masing pelet memiliki dinding samping dan jeruji permeabel, yang dimuat dengan campuran sinter, lewat di bawah kap pengapian, dikenai hisap aliran ke bawah, berujung, dan kemudian kembali ke posisi pemuatan. Kotak angin di bawah untaian terhubung ke kipas melalui sistem pembersihan gas.
Campuran sinter
Campuran sinter yang membentuk sinter bed terutama terdiri dari bijih besi, angin kokas, fluks dan butiran halus kembali. Perilaku campuran sinter selama sintering dan kualitas sinter sangat bergantung pada komposisi kimia, granulometrik, dan mineralogi bijih besi. Karakteristik bijih mempengaruhi perilaku sintering dan karenanya merupakan aspek penting dalam produksi sinter. Berbagai penelitian telah dilakukan tentang pengaruh komposisi campuran sinter pada fase sinter yang pada gilirannya berdampak pada kebasaan (CaO/SiO2), suhu, rezim termal dan kandungan Al2O3 (alumina) dan MgO (magnesia) terhadap kandungan ferit, hematit total, hematit reoksidasi teroksidasi dari magnetit, indeks reducibility (RI), indeks degradasi reduksi (RDI) dan indeks tumbler (TI), porositas dan laju coke.
Perilaku campuran sinter selama proses sintering tergantung pada komposisi kimianya. Beberapa penelitian telah dilakukan untuk menguji pengaruh komposisi kimia campuran sinter terhadap pembentukan lelehan dan reaksi asimilasi. Perubahan kecil dalam komposisi kimia bijih besi dapat menyebabkan modifikasi signifikan dalam pembentukan fasa selama sintering.
Kualitas sinter tergantung pada pembentukan fase ikatan yang, pada gilirannya, tergantung pada kemampuan sintering bijih besi. Di sisi lain, reaktivitas bijih besi secara signifikan dipengaruhi oleh ukuran butirnya yang menentukan luas permukaan reaksi dan kerapatan pengepakan (porositas) campuran sinter. Oleh karena itu, ukuran partikel bijih besi penting untuk mengontrol reaksi sintering selama proses sintering.
Perubahan ukuran partikel bijih mempengaruhi proses sintering. Telah ditemukan bahwa kemampuan asimilasi partikel bijih halus lebih besar daripada partikel kasar. Luas permukaan reaksi untuk partikel halus tinggi sehingga menghasilkan laju reaksi yang tinggi. Namun, pembentukan konsentrasi lelehan yang lebih tinggi dapat menyebabkan peningkatan viskositas lelehan, yang mengakibatkan penurunan fluiditas lelehan. Oleh karena itu, pemasukan partikel kasar ke dalam campuran sinter diperlukan untuk meningkatkan permeabilitas sinter bed, yang dikaitkan dengan peningkatan pergerakan skala besar antara partikel leleh dan padat.
Ukuran partikel rata-rata bijih besi mempengaruhi permeabilitas unggun sinter, yang pada gilirannya mempengaruhi struktur mikro dan produktivitas sinter. Partikel yang lebih besar mendukung ikatan difusi, dan partikel yang lebih kecil mendukung ikatan terak dalam proses sintering. Fraksi tinggi dari partikel kecil membentuk lelehan yang berlebihan, mengakibatkan penurunan kualitas sinter, sedangkan sinter dari partikel kasar dalam jumlah besar menyebabkan penurunan kekuatan sinter. Telah ditemukan bahwa peningkatan ukuran partikel rata-rata bijih besi meningkatkan produktivitas sinter.
Selama studi tentang sinterabilitas unggun sinter di mana partikel besar digabungkan, telah ditemukan bahwa penggunaan partikel bijih yang lebih besar menghasilkan peningkatan permeabilitas unggun sinter serta reaksi sintering selama proses. Ketika partikel besar ditempatkan di tempat tidur, daerah dengan kepadatan rendah terbentuk di sekitar partikel. Karena peningkatan permeabilitas sinter bed, laju aliran gas serta kecepatan FF lebih tinggi di sekitar partikel besar dibandingkan dengan partikel halus. Oleh karena itu, reaksi leleh dan asimilasi dapat terjadi dengan cepat di sekitar partikel besar karena fluiditas lelehan yang tinggi.
Distribusi ukuran partikel juga berpengaruh pada kerapatan pengepakan pelet yang dipadatkan, yang mempengaruhi laju sintering. Kepadatan pengepakan campuran yang terdiri dari partikel halus meningkat dengan mengganti beberapa di antaranya dengan partikel kasar. Selama pemadatan, partikel padat dapat bergerak lebih dekat satu sama lain, menghasilkan jumlah kontak yang tinggi antara partikel dan kerapatan pengepakan yang tinggi (porositas rendah). Penggantian partikel halus dengan partikel besar menyebabkan peningkatan kerapatan pengepakan hingga maksimum, setelah itu menurun untuk fraksi partikel kasar yang lebih tinggi. Kepadatan pengepakan maksimum terjadi pada titik di mana semua rongga antara partikel kasar diisi oleh partikel kecil. Oleh karena itu, keberadaan partikel kasar dapat menghasilkan bubuk yang dipadatkan dengan kerapatan pengepakan yang lebih tinggi (porositas lebih rendah), menghasilkan peningkatan laju sintering.
Kandungan ultra-halus dalam campuran bijih, terutama fraksi halus minus 50 mikro meter (mikron), memainkan peran penting dalam granulasi, pertama dalam memulai pembentukan lapisan pelapis di sekitar partikel inti dan kemudian mengikat partikel yang lebih besar. ukuran partikel halus yang menempel dengan lapisan.
Kokas adalah bahan bakar terbaik untuk sintering bijih besi. Klasifikasi ukuran merupakan faktor penting. Ekonomi dan efisiensi terbaik dicapai dengan ukuran partikel kokas kurang dari 3 mm. Beberapa penelitian telah menunjukkan bahwa ukuran kokas terbaik untuk produktivitas dan reducibility sinter adalah antara 0,25 mm dan 3 mm. Studi lain menunjukkan bahwa meskipun ukuran kokas kurang dari 0,25 mm memiliki efek negatif pada produktivitas; tidak mempengaruhi efisiensi proses pembakaran. Selanjutnya, fraksi yang lebih kasar lebih disukai dan lebih ekonomis dalam hal konsumsi. Perbandingan fraksi ukuran angin kokas yang berbeda telah menunjukkan bahwa hasil yang lebih baik dicapai dengan kokas kasar (kurang dari 3 mm dan lebih besar dari 1 mm) dibandingkan dengan kokas halus (kurang dari 1 mm). Kokas halus dianggap terutama sebagai butiran halus yang melekat dalam granulasi yang membentuk lapisan permukaan di sekitar butir. Kokas halus terbakar dengan cepat, sedangkan kokas kasar terbakar lebih lambat dan dapat memperlebar FF, yang menyebabkan kemungkinan hilangnya produktivitas. Selain itu, bahan bakar yang lebih kasar lebih ekonomis, memperkuat produksi sinter, meningkatkan RDI, dan menurunkan emisi SO2.
Pengaruh ukuran partikel kokas di unggun sinter pada produktivitas, konsumsi kokas dan kualitas sinter telah dipelajari dalam tes sinter-pot. Pengujian ini telah menunjukkan bahwa fraksi angin kokas yang lebih kasar menghasilkan kecepatan FF yang lebih tinggi dan efisiensi pembakaran yang lebih baik. Kokas halus mencapai efisiensi pembakaran yang lebih buruk, menghasilkan lebih sedikit panas dan menurunkan suhu sintering. Akibatnya, tingkat kokas perlu ditingkatkan saat kokas yang lebih halus digunakan untuk menjaga kualitas sinter.
Granulasi campuran sinter
Tujuan granulasi adalah untuk membuat partikel halus saling menempel dan membentuk partikel yang lebih kasar. Akibatnya bijih yang digranulasi mengandung kisaran ukuran partikel yang lebih kecil, dan akibatnya menawarkan ketahanan yang lebih kecil terhadap aliran gas.
Granulasi sangat penting untuk sintering bijih besi, karena permeabilitas sinter bed yang baik sangat menentukan tingkat kemajuan proses dan produktivitas pabrik sinter. Granulasi campuran sinter umumnya dilakukan dalam drum putar sebelum proses sintering, selama beberapa menit dengan penambahan 6% sampai 8% air. Proses granulasi lengkap membutuhkan waktu sekitar 30 menit hingga 1 jam, termasuk penambahan moisture, granulasi dan penyisipan ke dalam mesin sintering.
Studi awal tentang struktur campuran butiran sinter dilakukan di Nippon Steel Corporation (NSC). Studi ini telah menciptakan istilah 'kuasi-partikel' juga kadang-kadang disebut partikel semu (Gambar 2), yang terdiri dari inti bijih besi. Selama sintering, partikel kuasi ini sebagian tetap tidak meleleh, dikelilingi oleh butiran bijih yang lebih halus dengan gangue silika (SiO2) dan dengan adanya kebasaan tinggi (CaO/SiO2).
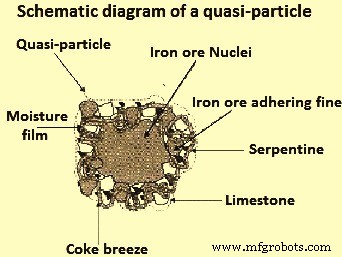
Gbr 2 Diagram skema partikel kuasi
Selama proses granulasi, partikel kuasi terbentuk ketika partikel halus (kurang dari 0,2 mm) menempel pada permukaan partikel besar (lebih besar dari 0,7 mm) dan kemudian membentuk butiran. Partikel antara (0,2 mm hingga 0,7 mm) sulit untuk digranulasi dan tidak memiliki peran yang jelas. Dalam prakteknya, jumlah partikel antara perlu diminimalkan karena pengaruhnya yang merugikan pada granulasi dan efek yang merugikan pada permeabilitas unggun sinter. Peningkatan kadar air dari campuran sinter dapat menyebabkan partikel perantara bertindak sebagai partikel halus yang melekat, yang melekat dengan buruk pada partikel kasar, dan dapat terlepas selama tahap pengeringan. Partikel perantara juga dapat bertindak sebagai inti dan membentuk partikel kuasi dengan ukuran kecil dibandingkan dengan yang terbentuk dengan inti yang lebih kasar. Hal ini secara bijaksana dapat mengurangi permeabilitas sinter bed serta produktivitas proses sintering.
Selama proses sintering, terbentuk ferit pada lapisan yang menempel pada inti karena reaksi padat-cair antara hematit dan lelehan CaO-Fe2O3 yang mengandung sejumlah kecil SiO2 dan Al2O3. Adhesi sangat dipengaruhi oleh kelembaban yang tersedia untuk granulasi. Faktor-faktor lain seperti sifat inti, bentuk partikel dan sifat permukaan adalah kepentingan sekunder.
Kadar air dalam campuran sinter yang akan disinter merupakan parameter yang sangat penting dalam proses granulasi. Proses melekatnya partikel halus ke inti untuk membentuk quasi-partikel sangat dipengaruhi oleh kadar air yang tersedia untuk granulasi (kelembaban total dikurangi kadar air yang diserap oleh komponen umpan sinter). Produksi maksimum dicapai dengan penambahan kelembaban optimum, yang kurang dari yang dibutuhkan untuk permeabilitas udara maksimum. Itu normal untuk beroperasi di sekitar 0,85 kali dari yang dibutuhkan untuk permeabilitas maksimum. Ini karena uap air mengembun di lapisan bawah unggun setelah menguap dari bagian atas saat FF mendekat. Kondensasi biasanya terjadi selama 2 menit pertama sintering sebelum campuran sinter mencapai suhu titik embunnya.
Kontrol yang baik dari penambahan kelembaban sangat penting. Penambahan air dalam drum pencampur harus disesuaikan untuk menjaga tingkat kelembaban yang ditetapkan. Kontrol otomatis diinginkan untuk metode manual karena memastikan respons yang lebih cepat dan pengumpanan yang lebih konsisten ke untai sinter.
Granulasi yang dilakukan dengan menggulung bahan dalam drum yang berputar, meningkatkan ukuran butiran dengan adhesi karena pada dasarnya aksi dua jenis gaya yaitu (i) 'saling mengunci' partikel, dan (ii) gaya tarik oleh penciptaan fase cair 'jembatan' antara partikel. Pentingnya besarnya gaya interlocking dapat divariasikan dengan mengubah urutan pembentukan campuran yang akan disinter sehingga mendukung aksi agregasi inti granulasi yang disediakan oleh komponen tertentu (misalnya butiran halus sinter kembali).
Besarnya gaya interlocking juga dapat divariasikan dengan memodifikasi urutan pembentukan campuran sinter untuk memasukkan granulasi selektif atau proses pra-penggumpalan. Dalam kasus seperti ini, ini melibatkan pengolahan bijih halus dan konsentrat, beberapa mengembalikan butiran halus sinter dan kapur secara terpisah menggunakan jalur proses tambahan. Bahan-bahan ini dicampur dengan air dan pelet mikro dalam drum atau piringan sebelum dimasukkan ke sirkuit granulasi utama sebelum drum granulasi. Dalam proses ini butiran halus sinter kembali bertindak sebagai nukleus dan kapur bertindak sebagai agen penggumpalan. Praktik ini memungkinkan penggunaan denda dalam jumlah yang lebih besar tanpa kehilangan produktivitas.
Gaya jenis terakhir (jembatan) berasal dari adanya air yang ditambahkan ke dalam campuran, dan pengaruhnya dapat ditingkatkan dengan penggunaan zat aditif. Dalam kedua kasus (saling mengunci dan menjembatani) kekuatan partikel butiran tidak tinggi. Ini hanya cukup untuk memastikan bahwa campuran butiran dapat diangkut dan dilapisi pada parutan sinter tanpa pecah. Distribusi ukuran campuran butiran saat dimasukkan ke dalam sinter grate berkisar dari sekitar 1 mm hingga 10 mm.
Kajian untuk mengetahui struktur granul pada citra tiga dimensi, umumnya dilakukan dengan menggunakan teknik 3D X-ray tomography. Dalam salah satu studi campuran bijih besi halus (konsentrat), halus kembali sinter dan batu kapur telah disiapkan pada rasio konsentrat/bijih 20:80, 50:50, 80:20 dan 100:0 dan sinter telah diproduksi dengan kebasaan 0.8, 1.4 dan 2.0. Menggabungkan peningkatan jumlah konsentrat dalam campuran sinter telah membuat granulasi menjadi lebih kompleks.
Partikel superhalus tidak hanya melekat pada partikel kasar tetapi juga dapat membentuk inti yang tahan lama saat mengikat partikel berukuran menengah, dan semakin banyak superhalus yang digunakan dalam campuran sinter, semakin tidak dapat diprediksi distribusi ukuran butiran. Granula yang termasuk dalam campuran sinter tanpa bijih kasar (rasio konsentrat/bijih 100:0) tidak memiliki inti dan sangat sedikit partikel batugamping yang menempel di permukaan yang awalnya dibentuk oleh mekanisme pelletizing, dan menyajikan struktur yang mirip dengan pellet. Perilaku granulasi tidak dapat sepenuhnya dijelaskan oleh satu faktor saja, seperti rasio konsentrat/bijih, dan perubahan mineralogi bijih, komposisi dan jumlah gangue, konsumsi panas dan kandungan air dalam campuran, semuanya merupakan faktor yang sangat relevan.
Produktivitas sinter berhubungan langsung dengan permeabilitas unggun. Pada gilirannya, permeabilitas berhubungan dengan distribusi ukuran granul dan ukuran granul rata-rata, yang bergantung pada penambahan air. Permeabilitas naik ke nilai maksimum sebagai fungsi dari kelembaban. Produktivitas maksimum diperoleh dengan menggunakan 85% kelembaban yang dibutuhkan untuk permeabilitas maksimum karena kondensasi kelembaban di lapisan bawah lapisan.
Dalam beberapa penelitian yang telah dilakukan untuk memprediksi perilaku granulasi sejumlah bijih besi dengan sifat yang berbeda, telah diusulkan persamaan untuk menghitung kelembaban optimum dari campuran mentah sebagai fungsi dari sifat, komposisi dan granulometri dari bijih. Kadar air optimum didefinisikan sebagai jumlah terendah yang diperlukan untuk mencapai permeabilitas unggun maksimum. Persamaan diterapkan untuk setiap bijih dan campuran bijih, dengan penambahan kokas, fluks, dan denda sinter kembali. Korelasi yang baik telah ditemukan antara nilai eksperimental dan yang dihitung.
Dalam beberapa penelitian lain tentang granulasi, peralatan telah dirancang untuk menentukan kapasitas kelembaban beberapa jenis bijih besi dan campuran bijih. Kapasitas kelembaban telah didefinisikan sebagai kadar air maksimum yang dapat dipertahankan antara partikel bijih. Telah terlihat bahwa kapasitas kelembaban meningkat sejalan dengan luas permukaan luar dan menurun seiring dengan meningkatnya volume pori bijih. Persamaan untuk menentukan perbandingan antara kelembaban optimum (W) dan kapasitas kelembaban (MC) yang didapat adalah W =6,94 + 0,12 MC. Data eksperimen menunjukkan korelasi yang sangat tinggi antara W dan MC.
Berdasarkan penelitian lebih lanjut maupun penelitian awal, persamaan yang diusulkan untuk menghitung kadar air optimum (W) sebagai fungsi dari sifat, komposisi dan granulometri bijih besi adalah W =2,28 + 0,427 L + 0,810 A – 0,339 S + 0.104D + 0.036 E dimana L adalah kehilangan berat bijih selama pemanasan dalam gram, A adalah % Al2O3 dalam bijih, S adalah % SiO2 dalam bijih, D adalah fraksi ukuran bijih kurang dari 0,2 mm, dan E adalah fraksi ukuran bijih antara 0,2 mm dan 1 mm. Telah ditetapkan bahwa sampel dengan kapasitas kelembaban yang lebih tinggi membutuhkan kadar air yang lebih tinggi untuk mencapai permeabilitas unggun terbaik. Tidak mungkin untuk secara langsung menghubungkan permeabilitas dengan sifat bijih.
Studi juga telah dilakukan untuk menentukan pengaruh penambahan kelembaban dan keterbasahan pada granulasi dengan menentukan sudut kontak antara oksida besi dan air dan kebugaran granulasi bijih besi. Studi ini mempertimbangkan berbagai jenis bijih untuk menentukan interaksi antara berbagai parameter yaitu (i) sifat bijih (porositas), (ii) kadar air, (iii) waktu keterbasahan, (iv) pengukuran sudut kontak bijih-air, (v) kekasaran permukaan, (vi) rpm drum pelletizing, (vii) rasio halus yang melekat (AR) partikel halus, dan (viii) kekuatan patah (FS) partikel semu. Granulasi terbaik dicapai dengan inti bijih goetit, dengan porositas tinggi, kekasaran rendah, dan sudut kontak rendah (lebih basah).
Sistem granulasi dua tahap juga telah digunakan di beberapa pabrik sintering. Sistem granulasi dua tahap membantu mengolah bijih halus sekaligus meningkatkan kecepatan FF, permeabilitas, dan produktivitas proses.
Hal ini menguntungkan untuk meningkatkan proses granulasi konvensional, terutama bila menggunakan bijih goetit dan limonit yang biasanya memiliki kandungan Al2O3 lebih tinggi daripada bijih hematit dan menyebabkan penurunan sifat sinter. Dalam hal ini, penelitian telah menunjukkan bahwa kualitas sinter meningkat ketika tahap granulasi konvensional dalam mixer drum diikuti oleh tahap kedua. Pada tahap pertama campuran bijih besi dan butiran halus sinter kembali ditempatkan di dalam drum. Pada tahap kedua, kokas ditambah batu kapur plus dolomit ditambahkan ke dalam campuran yang dihasilkan dari tahap pertama dan butiran yang diperoleh dibentuk oleh inti yang sebagian besar terdiri dari bijih besi yang dikelilingi oleh kokas dan fluks. Proses granulasi pelapisan ini meningkatkan reaksi pembentukan fluks akibat segregasi CaO (kalsium oksida) dari batugamping pada Fe (besi) dari bijih besi. Hal ini menyebabkan sintering berlangsung pada suhu yang lebih rendah, meningkatkan permeabilitas dan produktivitas, dan menurunkan pembentukan hematit sekunder, dengan peningkatan konsekuen dalam RDI. TI dan reducibility juga meningkat, karena pembentukan lebih banyak pori-pori mikro, yang juga mencegah penyebaran retakan yang menyebabkan kerusakan RDI.
Waktu pencampuran dalam drum pada tahap kedua sangat penting, dan sekitar 50 detik telah ditetapkan sebagai waktu optimal. Waktu yang lebih singkat tidak memungkinkan nukleus terlapisi dengan baik oleh kokas + fluks. Waktu yang lebih lama menyebabkan penghancuran partikel kuasi, karena masuknya kokas dan fluks ke dalam butiran (dari inti), dan menghasilkan partikel kuasi yang serupa dengan yang diperoleh dalam granulasi konvensional satu tahap.
Studi rinci telah dilakukan pada metode granulasi coke dan lapisan batu kapur dengan tujuan meningkatkan produktivitas, reducibility dan operasi BF. Teknologi ini terdiri dari pelapisan kokas dan batugamping pada permukaan kuasi-partikel yang telah digranulasi di bagian utama drum mixer. Kokas dan batu kapur disuntikkan dari ujung mixer drum oleh konveyor sabuk dengan kecepatan tinggi untuk mencapai lapisannya pada partikel kuasi. Waktu granulasi pelapisan adalah faktor kontrol yang paling penting dan disesuaikan dengan mengubah kecepatan konveyor. Waktu normalnya berkisar antara 40 detik sampai 60 detik dengan waktu yang lebih singkat tidak semua partikel kuasi terlapisi, dan dengan waktu yang lebih lama partikel kuasi tersebut hancur.
Studi juga telah dilakukan untuk menilai pemisahan partikel yang digranulasi secara terpisah (pelapisan kokas dan pelapisan batu kapur), dan dalam kedua kasus granulasi, produktivitas terlihat meningkat dibandingkan dengan produktivitas konvensional. Pelapisan kokas meningkatkan tegangan kohesi partikel kuasi dan dengan demikian meningkatkan permeabilitas di zona basah. Dengan lapisan batu kapur, sinter menyajikan kandungan hematit sekunder yang lebih rendah dan struktur dengan toleransi retak (RDI yang ditingkatkan), lebih banyak hematit primer dan SFCA (RI yang ditingkatkan), dan fluiditas lelehan yang lebih baik. Dalam BF, efisiensi poros meningkat sebesar 1%, dan tingkat zat pereduksi dapat diturunkan sebesar 7 kg/ton logam panas.
Teknologi granulasi selektif juga digunakan di beberapa pabrik sintering di Jepang. Teknologi ini digunakan untuk memungkinkan sintering bijih besi dengan kandungan Al2O3 tinggi, yang sebaliknya sulit untuk disinter karena reaktivitas rendah dari bahan bantalan Al2O3 dan viskositas lelehan primer yang tinggi. Granulasi selektif terdiri dari penyaringan bijih dan pengiriman fraksi ukuran lebih besar yang memiliki kandungan Al2O3 lebih rendah ke sirkuit granulasi konvensional, sedangkan fraksi ukuran lebih kecil dengan kandungan Al2O3 lebih tinggi dipelet menjadi butiran berukuran 2 mm sampai 5 mm yang tergabung dalam sirkuit granulasi konvensional. Fraksi ukuran yang lebih kecil mengandung bijih lempung yang tinggi Al2O3 dan membutuhkan suhu leleh yang lebih tinggi. Granulasi selektif mencapai inti granul dengan kandungan Al2O3 lebih tinggi daripada granulasi konvensional. Dengan proses ini, butiran halus yang menempel pada inti dengan kandungan Al2O3 yang lebih rendah melalui reaksi dengan batu kapur mendorong pembentukan lelehan primer pada suhu yang lebih rendah.
Proses granulasi selektif memiliki tingkat pemrosesan bahan baku yang tinggi, dan dapat memproses bahan baku yang lengket secara terus menerus. Selanjutnya, pengurangan kokas bahan bakar dan pengurangan daya blower tercapai. Juga, produktivitas meningkat dan kandungan FeO berkurang. Peningkatan reducibility pada gilirannya menyebabkan pengurangan konsumsi coke di BF. Ada juga peningkatan nilai RDI sinter.
Api depan
Temperatur depan nyala api atau zona pembakaran memiliki pengaruh yang sangat besar terhadap waktu dan produktivitas sintering karena berpengaruh terhadap permeabilitas FF. Umumnya penurunan suhu FF sangat bermanfaat bagi produktivitas karena hambatan FF terhadap aliran udara merupakan fungsi dari kecepatan gas pangkat tiga. Menaikkan suhu FF secara signifikan meningkatkan hambatan aliran udara dan mengarah pada peningkatan waktu sintering dan penurunan produktivitas. Pengukuran suhu pada tingkat yang berbeda di unggun sinter memungkinkan pergerakan zona pembakaran dipantau dan konsep kecepatan FF didefinisikan sebagai laju di mana tingkat kenaikan suhu tercepat terjadi bergerak melalui unggun. Gambar 3 menunjukkan distribusi temperatur (panas) yang ideal di sinter bed.
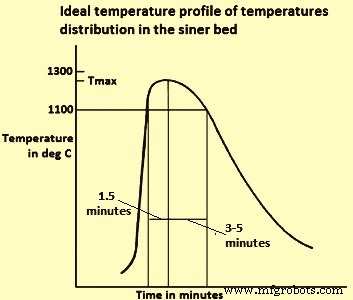
Gbr 3 Distribusi suhu ideal di sinter bed
Waktu pemanasan di zona suhu tinggi (lebih tinggi dari 1100 derajat C) perlu singkat (1,5 menit) karena ukuran tekanan oksigen parsial (pO2) di zona ini rendah karena pembakaran kokas dan FeO, yang berbahaya bagi reduksi sinter , mudah dibentuk. Waktu pendinginan (sampai 1100 derajat C) perlu lama (dari 3 menit sampai 5 menit) untuk mencapai struktur sinter yang kuat dengan pembentukan matriks gangue, yang disukai dengan adanya SiO2 (silika). Profil waktu-suhu telah diukur di beberapa posisi di lapisan, dan menunjukkan bahwa lebar dan Tmax zona pembakaran meningkat saat turun melalui lapisan.
Untuk mencapai Tmax yang seragam, dua lapisan sintering dilakukan di beberapa pabrik sinter. Ini terdiri dari mempersiapkan tempat tidur dengan kandungan kokas yang lebih tinggi di lapisan atas daripada di lapisan bawah untuk melawan kecenderungan Tmax naik. Selain dua lapisan untuk mengontrol distribusi panas di unggun, peralatan pengukur kontinu telah dikembangkan yang secara langsung memberi sinyal distribusi suhu di seluruh unggun, bersama dengan perangkat untuk mengukur distribusi volume yang dihisap melalui sinter grate. Distribusi panas dapat dikontrol dengan mengadaptasi kecepatan untai dan kandungan kokas dalam campuran sinter.
Ada hubungan antara suhu FF maksimum dan struktur sinter. Ketika sintering dilakukan pada suhu di bawah 1300 derajat C, pada sekitar 1200 derajat C, lelehan (terutama terdiri dari Fe2O3 dan CaO) dihasilkan di unggun sintering, dan oksida besi dan partikel halus diasimilasi dalam lelehan. Jika lelehan menembus butir hematit, terjadi kerusakan antarmuka, meninggalkan hematit primer (tidak meleleh) yang dianggap bermanfaat untuk sintering karena meningkatkan RI. Ketika CaO dan Al2O3 diasimilasi dalam lelehan, ini bereaksi dengan oksida besi dan menghasilkan kalsium ferit acicular (dengan ukuran kurang dari 10 mikron) yang mengandung Al2O3 dan SiO2 sebagai pelarutan padat, sesuai dengan reaksi umum Fe2O3 + CaO + SiO2 + Al2O3? SiO2·CaO·(Fe, Al)2O3. Siliko-ferit kalsium dan aluminium (SFCA) dianggap sebagai komponen yang sangat bermanfaat untuk struktur sinter karena memiliki kemampuan mereduksi yang baik dan memberikan kekuatan mekanik sinter, serta meningkatkan indeks pecah (SI) dan indeks gelas (TI).
Selama sintering pada suhu rendah (kurang dari 1300 derajat C) pembentukan magnetit berkurang (kurang FeO) dan sintering meningkatkan RI dan menurunkan (meningkatkan) RDI. Juga, struktur optimal untuk reducibility sinter di BF tercapai, yang akan dibentuk oleh inti hematit (tidak meleleh) yang dikelilingi oleh kisi ferit acicular. Ketika sintering pada suhu lebih tinggi dari 1300 derajat C, bagian dari ferit larut dan meleleh menjadi hematit atau magnetit dan menjadi komponen gangue. When the melt cools it forms as new phases of (i) large ferrite crystals, whose reducibility is inferior to the acicular ferrite, and (ii) secondary hematite, which is detrimental to the RDI. Fig 4 illustrates schematically the development of the different structures of sinter as a function of the Tmax reached in the bed.
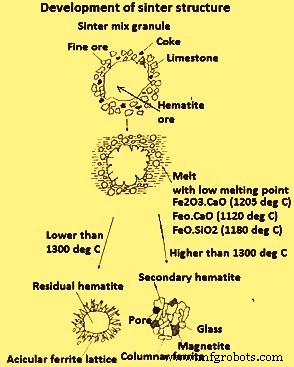
Fig 4 Development of sinter structure
Tab 1 shows the variance of the phase composition and sinter quality indices as a function of the temperature Tmax.
Tab 1 Typical values of phase composition and sinter quality at maximum temperature in the bed |
Subject | Satuan | Tmax in deg C |
| | Around 1200 | Around 1250 | Around 1300 |
Primary hematite | % | 50 | 42 | 22 |
Secondary hematite | % | 5 | 5 | 20 |
Magnetite | % | 10 | 15 | 20 |
SFCA | % | 35 | 38 | 30 |
Glass+2CaO.SiO2 | % | 7 | 10 | 12 |
FeO | % | 35 | 30 | 15 |
Porosity | % | 3 | 4 | 5.5 |
RDI | % | 30 | 32 | 36 |
Reducibility index | % | 72 | 70 | 64 |
Shatter index (SI) | % | 93 | 94 | 95 |
The best results are obtained in the temperature of around 1250 deg C, with a maximum percentage of ferrites, high primary hematite, low secondary hematite, good porosity, and good quality indices (FeO, RDI, RI and SI).
Softening and melting of sinter in BF
The BF operation is dependent upon the geometry and condition of the cohesive zone, which is limited by the softening (ST) and melting (FT) isotherms. The cohesive zone is constituted by alternate layers of soft sinter and coke. The latter (known as ‘coke window’) allows the reducing gas to pass through to the BF shaft. Hence, it is important for the cohesive zone to be as narrow as possible, in order to facilitate the penetration of the reducing gas, and as low as possible in the BF, so that the furnace preparation zone above the cohesive zone is sufficiently large to allow the reduction of iron oxides. In order to fulfill both conditions the ST and FT is to be as high as possible and the difference between them is to be minimal. Part of coke consumption saving in BF takes place due to the improved sinter quality, in particular its reducibility and high temperature properties.
Several studies have been carried out into the fundamental mechanism underlying the softening and melting of the sinter in the BF. The sequence which takes place during softening and melting consists of (i) pre-softening, (ii) softening, (iii) exudation, and (iv) dripping stage. The softening mechanism is related with the melting rate of the core as a function of the temperature. Deformation is considered to be directly related with the macro-porosity generated by the transfer of melt from the core to the outer layer. Initial melt formation plays a role in the start of softening, reduction, retardation and dripping of melt from the bed.
In one of the studies in an experimental unit which reaches a maximum temperature of 1400 deg C, the softening and melting of sinters has been determined for different basicities (range 1.5 to 3.0), MgO contents (range 3.3 % to 10 %) and many sinter reducibility grades. The softening-melting range has been defined as the temperature range between the point of reversal (T1 softening) and 10 % contraction (T2 melting). It has been noticed that the behaviour of BF improves (lower and narrower cohesive zone) as the sinter/ore ratio in the BF charge increases.
Another study done for finding the effect of the FeO content in sinter (sinter type A 10 % and sinter type B 12 %) on softening and melting, and its impact on the BF working. The sinter with more FeO caused early softening of the burden, a phenomenon which is undesirable in the BF. Unreduced FeO is reduced at a higher temperature, according to the equation FeO + C =Fe + CO, and such direct reduction in a higher amount leads to a higher coke rate in the process. A lower wind volume, production and productivity have also been noticed in comparison with the behaviour of BF when operating with a sinter load with 10 % FeO. A drop in the MgO content in sinter from 1.75 % to 1.5 % gives rise to changes in furnace behaviour which is attributed to variations in the softening and melting temperatures.
Another study has been carried out to find the influence of the material composition on softening and melting properties in the BF burden materials. The experimental part has been carried out in a unit which simulates BF environment, operating under load up to a temperature of 1580 deg C. Sinter showed a high softening temperature (around 1400 deg C) but a relatively low meltdown ratio and poor high temperature permeability. An increase in sinter basicity has been seen to be detrimental to the fluidity of melted slag and iron in the BF, resulting in more melted slag and iron being blocked in the coke layer, thus decreasing the percent meltdown and increasing the gas resistance of the sample bed. For this reason it is important to lower the sinter basicity. On the other hand, an increase in Al2O3 (range from 0.9 % to 2.6%) or MgO lowered the slag melting point, thus favouring a reduction in high temperature gas resistance. Sinter presents better softening and melting behaviour than pellets or ore, but worse meltdown and high temperature gas resistance. It has been seen that a mixed burden containing 65 % sinter, 20 % lump ore, and 15 % pellets is slightly better than other compositions in terms of FT and ST, meltdown and high temperature gas resistance.
In an another study it has been found that the softening temperature comes down as the gangue content in the ore increases, due to the fact that gangue forms compounds with low melting point such as 2FeO·SiO2, FeO·SiO2·CaO, and Fe2O3·SiO2·CaO (Fig 5). The alkalis contained in gangue can also form compounds with a low melting point such as Na2SiO3, K2SiO3, and NaAlSi2O6. The softening temperature of the sinters produced at temperatures between 1300 deg and 1350 deg C depends on the composition and mineralogy of the sinter.
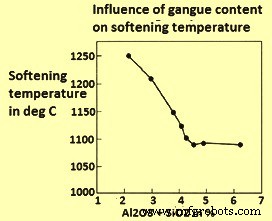
Fig 5 Influence of gangue material on softening temperature
The permeability resistance K of the sinter bed is generally evaluated by the sinter softening property test. When K is plotted against the bed temperature, integrating the curve obtained in the 1000 deg C to 1600 deg C interval, the KS bed resistance parameter when calculated, it has been found that a reduction in the SiO2 content and an increase in MgO in sinter improves both its permeability (lower KS) and the sinter softening property. The action of SiO2 is due to a decrease in the melt which fills the voids in the bed. The action of MgO is due to an increase in the melting point of CaO-FeO-SiO2 slag. The Al2O3 content has little effect on the sinter softening property.
In another study, it has been found that as the sinter is improved when the Al2O3 content is decreased from 1.8 % to 1.5 %, the sinter has better reduction and softening-melting in the BF. Also the permeability resistance index in the cohesive zone is improved. This may be due to the amount of melt having low melting point being little owing to the improved reduction efficiency and lower Al2O3 content.
The softening and melting behaviour of three lump hematite ores and a sinter has been determined in an outfit which operates under load. It has been found that the beds of lump ores contract much earlier than sinter by the formation of fayalite, with a low melting temperature component to be around 1175 deg C to 1205 deg C. No fayalite forms in sinter and at higher temperature melts which are generated appear to be more viscous, resulting in less bed deformation. There is not an appreciable difference for the softening and melting temperatures for sinter and for 80 % sinter and 20 % lump ore blend. With this blend as ferrous burden in the BF, the permeability remained in the normal operating range, the same that when the BF operate with 100 % sinter, with no indication of non-uniform gas flow conditions or abnormal cohesive zone issues and gas utilization efficiency even improved slightly.
An important property of melts is that they coalesce, transforming the uniformly packed bed of granules into sinter particles and very large channels in the bed. The coalescing behaviour of melts needs to have a favourable influence on the flame front properties in determining the permeability of the sinter bed.
Reactions in the process of sintering
During the sintering process, several chemical reactions between iron ores and fluxes are taking place at a specific maximum temperature, resulting in conversion of loose materials into a solid mass. These reactions are defined as sintering reactions and involve the formation of the melting phase followed by the assimilation of large particles into the melt.
Studies have been carried out regarding the sequence of formation of phases during iron ore sintering (Fig 6). These studies found that the sintering reactions occurred in the FF and consisted of reactions between a fraction of iron ore and the principal flux. This led to the formation of a liquid phase which formed the bonding phase. It has also been that the sintering reactions start within the layer of adhering fines where fine reactive ores and fluxes are in intimate contact. Hence, solid – solid reactions are the first reactions to occur, generating the primary melt. However, large particles are almost inactive during this first stage due to their large reaction area.
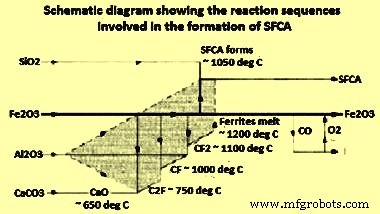
Fig 6 Sequence of formation of phases during iron ore sintering
The sintering reactions consist of melt formation and assimilation reactions (Fig 7). A relevant starting point was a pseudo-particle consisting of a large core particle (nucleus) and a coating layer of adhering fines and fluxes. Fig 7 (i) represent the basic structure of pseudo-particles formed during the granulation. The sintering reactions begin within the layer of adhering fines, where fine materials are in intimate contact. With the increase in temperature (at about 1100 deg C), calcium ferrites are the first product to form by solid-solid reactions between hematite and lime. At around 1200 deg C, calcium ferrites decompose and form the initial liquid melt, which can dissolve SiO2 and Al2O3. This stage of the sintering process is schematically represented in Fig 7 (ii). As the sintering process progresses, the liquid melt starts reacting with the nucleus particles, resulting in a dissolution of the nucleus particle and formation of more melt as shown in Fig 7 (iii). The assimilation reaction depends on the properties of both the initial melt and nucleus particle. The more reactive is the melt, the greater is its ability to dissolve the solid nucleus. Similarly, the greater is the reactivity of the solid nucleus, the more is the amount which gets assimilated.
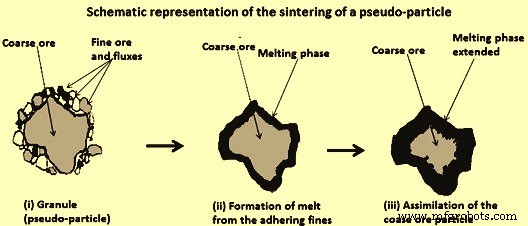
Fig 7 Schematic representation of the sintering of a pseudo-particle
In principle, the sintering reactions involve reactions of fine ores with fluxes resulting in the formation of a melting phase which is used during solid-liquid reactions for the assimilation of coarse ore. The melt which forms during sintering acts as the bonding phase.
During the sintering process, the formation of the melt occurs in the FF where the temperature is higher than 1100 deg C. Then, the melt solidifies to become the bonding phases which make up the majority of other phases within a sinter. The bonding phase is generally consists of the SFCA phase in association with iron oxides and silicates. SFCA is considered to be the most important bonding phase because of its great influence on the properties of sinter.
In the process of sintering the temperature of the sinter mix is increased to achieve its partial melting and to produce a molten material which, during cooling, crystallizes or solidifies into several mineral phases which agglomerate the structure as a whole. The energy for this process is supplied by burning of the coke breeze.
A study to determine the sequence of reactions in SFCA formation has been carried out using a combination of XRD (X-ray diffraction), DTA (differential thermal analysis), and EPMA (electron probe micro analyzer). The first ferrites formation reactions are solid-solid reactions which start in the temperature range of 750 deg C to 780 deg C and end at 1200 deg C, the melting temperature of these ferrites, following the sequence dicalcium ferrite (C2F) to calcium ferrite (CF) to calcium diferrite (CF2) (Fig 6) as per the following equations.
Fe2O3 + 2CaO =2CaO·Fe2O3 at 750 deg C to 780 deg C
2CaO·Fe2O3+Fe2O3 =2[CaO·Fe2O3] at 920 deg C to 1000 deg C
CaO·Fe2O3+Fe2O3 =CaO·2Fe2O3 at 1050 deg C to 1150 deg C
CaO plays an extremely important role during sintering as it combines easily with Fe oxides in the mix to produce calcium ferrites. The melt formation reaction starts at the point of contact between the ore fines and CaO. At the same time, the solid-solid SFCA formation reaction starts at around 1050 deg C and continues in a solid-liquid reaction above 1200 deg C. The presence of Al2O3 increases the stability of SFCA, and lowers the temperature at which these ferrites start to form. Above 1200 deg C, solid-liquid (solid-melt) reactions predominate, with the presence of a molten phase which reinforces the assimilation of material to form ferrite as per the following equation.
CaO·Fe2O3 + Al2O3 + SiO2 =CaO·SiO2·(Fe, Al)2O3
The sequence of SFCA formation reactions is shown in the schematic diagram (Fig 5). Al2O3 is highly reactive and enters the solid dissolution with the C2F, CF and CF2 phases, as indicated in the shaded region of Fig 5. In this study it has been also seen that SiO2 does not react with Fe2O3 or CaO and remains inert until SFCA start to form at temperatures higher than 1050 deg C.
Study has also been done on the formation of 2CaO·Fe2O3 at 1000 deg C from a stoichiometric mixture of Fe2O3 (Fe ore) and CaCO3 (lime stone). Fe2O3 is reduced to Fe3O4 and FeO before the calcination of limestone starts, as a function of the partial pressure of O2, which is determined according to the CO content in the CO+CO2 reducing mixture. The order which is found for the reaction rate of Fe oxide with CaO, for the formation of dicalcium ferrite is FeO -> Fe3O4 -> Fe2O3.
Throughout the process, the Fe oxide can simultaneously be reduced by CO produced in the partial combustion of coke-coal as per the following equation.
2 Fe2O3 + CO =Fe3O4 + FeO +CO2
Fe3O4 can oxidize to Fe2O3. FeO can oxidize to Fe3O4 or Fe2O3, and can initiate with outside energy, low melting point following slag formation reactions.
FeO + CaO =CaO·FeO at 1120 deg C
FeO + SiO2 =SiO2·FeO at 1180 deg C
FeO+CaO+SiO2 =CaO·SiO2·FeO at 1220 deg C
Silica from the iron ore can react with the molten ferrite as per the following equation to form calcium silicates and precipitate hematite or magnetite, depending on the pO2 in the reaction system, together with the silicate formed.
CaO·Fe2O3 + SiO2 =CaO·SiO2 + Fe2O3
The sequence of reactions shown above has been widely studied due to its importance in sintering. In one of the study calcium ferrite (CF) samples and CF + Al2O3 and CF + SiO2 samples have been sintered. It has been shown that the addition of Al2O3 is more effective to dissolve the hematite in CF, and the addition of SiO2 is more effective to raise the CF formation rate. CF2 and CF2 + Al2O3 (3 % to 9 %) + SiO2 (1 % to 7 %) samples have been sintered to prepare SFCA, monitoring the evolution of these processes by XRD. Al2O3 solubility in CF2 at 1250 deg C is 5 % -7 % and SiO2 solubility is 2 % to 4 %. Monoclinic structure CF2 changes to triclinic when it reacts with Al2O3 and SiO2 to form SFCA. The addition of SiO2 at 1200 deg C causes partial decomposition of CF2 into calcium silicates. As the Al2O3/SiO2 ratio increases, formation of hematite decreases and SFCA formation increases. The Fe3+ ion (radius 0.65 angstrom) in tetrahedral centres is replaced by smaller ions (Si4+, 0.40 angstrom and Al3+, 0.54 angstrom), in such a way that the unit cell volume tends to decrease as more Si4+ and Al3+ are added to the CF2.