Memahami Pembuatan Besi Tungku Ledakan dengan Injeksi Batubara Serbuk
Memahami Pembuatan Besi Tungku Ledakan dengan Injeksi Batubara Serbuk
Injeksi pulverized coal di blast furnace (BF) awalnya didorong oleh harga minyak yang tinggi tetapi sekarang penggunaan pulverized coal injection (PCI) telah menjadi praktik standar dalam operasi BF karena memenuhi persyaratan pengurangan biaya bahan baku, polusi dan juga memenuhi kebutuhan untuk memperpanjang umur oven kokas yang sudah tua. Injeksi pulverized coal ke dalam BF menghasilkan (i) peningkatan produktivitas BF, yaitu jumlah logam panas (HM) yang dihasilkan per hari oleh BF, (ii) mengurangi konsumsi coking coal yang lebih mahal. dengan mengganti kokas dengan kokas lunak atau batubara termal yang lebih murah, (iii) membantu menjaga stabilitas tungku, (iv) meningkatkan konsistensi kualitas HM dan mengurangi kandungan silikon (Si), dan (v) mengurangi emisi gas rumah kaca. Selain keuntungan ini, penggunaan PCI di BF telah terbukti menjadi alat yang ampuh di tangan operator tungku untuk menyesuaikan kondisi termal tungku jauh lebih cepat daripada yang mungkin dilakukan dengan menyesuaikan muatan beban dari atas.
Batubara bubuk pada dasarnya memiliki dua peran dalam pengoperasian BF. Ini tidak hanya menyediakan bagian dari panas yang dibutuhkan untuk mereduksi bijih besi, tetapi juga beberapa gas pereduksi. Untuk memahami produksi HM dalam BF dengan injeksi batu bara bubuk, perlu dipahami apa yang terjadi di dalam BF serta reaksi kimia dan pentingnya permeabilitas dalam tungku dan bagaimana bahan baku dapat mempengaruhi parameter ini.
BF pada dasarnya adalah tungku unggun yang bergerak berlawanan arah dengan padatan (bijih besi, kokas dan fluks), dan kemudian cairan cair, berjalan menuruni poros. Batubara bubuk dan ledakan udara panas yang diperkaya oksigen (O2) disuntikkan pada tingkat tuyere di dekat dasarnya. Gas-gas yang terbentuk oleh berbagai reaksi yang terjadi bergerak ke atas poros tungku, mengurangi bijih besi saat turun.
Muatan BF terdiri dari (i) bahan baku bantalan besi (benjolan bijih besi, pelet, dan sinter) dan fluks (batugamping, dolomit, dan kuarsa), dan (ii) kokas. Bahan muatan ini diisi secara alternatif di bagian atas tungku. Bahan setelah diisi dikeringkan dan dipanaskan oleh gas yang meninggalkan tungku.
Saat muatan bergerak ke bawah tungku, ia dipanaskan dan, pada suhu sekitar 500 derajat C, reduksi tidak langsung bijih oleh karbon monoksida (CO) dan hidrogen (H2) dalam gas naik dimulai. Transformasi oksida besi yang lebih tinggi menjadi oksida besi (FeO) dimulai di zona ini. Saat muatan turun lebih jauh dan dipanaskan sampai tingkat suhu sekitar 900 derajat C hingga 950 derajat C, reduksi langsung oksida besi oleh kokas padat terjadi. Bijih direduksi oleh CO dan H2, dan karbon dioksida (CO2) yang terbentuk segera direduksi oleh kokas kembali menjadi CO. Efek bersihnya adalah reduksi bijih oleh kokas. Reaktivitas kokas terhadap CO2 merupakan parameter penting karena menentukan kisaran suhu di mana transisi dari reduksi tidak langsung ke reduksi langsung terjadi.
Di bagian bawah tungku terdapat daerah yang dikenal sebagai zona kohesif. Di sini, terak mulai terbentuk sekitar 1100 derajat C. Awalnya relatif kental, dan mengelilingi partikel oksida besi, mencegah reduksi lebih lanjut. Ketika suhu meningkat ke tingkat sekitar 1400 derajat C hingga 1450 derajat C, ia meleleh dan reduksi berlanjut. Wilayah ini sangat penting dalam hal permeabilitas beban.
Zona berikutnya di BF dikenal sebagai zona cair atau coke aktif. Di zona ini, suhu meningkat menjadi sekitar 1500 derajat C, proses pencairan bijih besi dan terak terus berlanjut. Ada pergerakan substansial di wilayah ini dan kokas mengalir darinya ke raceway. Raceway adalah bagian terpanas dari BF, di mana suhu bisa mencapai hingga 2200 derajat C. Hal ini dibuat ketika ledakan udara panas disuntikkan melalui tuyeres ke dalam tungku. Batubara bubuk disuntikkan dengan ledakan udara panas langsung ke raceway. Pembakaran dan gasifikasi batubara, dan kokas terjadi, menghasilkan baik gas pereduksi (CO dan H2) dan panas yang dibutuhkan untuk melelehkan bijih besi dan terak dan untuk mendorong reaksi endotermik.
Semburan udara panas diperkaya dengan oksigen (O2) untuk mempertahankan suhu nyala yang diinginkan dan untuk meningkatkan efisiensi pembakaran. Sebuah BF memiliki banyak tuyer (jumlah tuyer tergantung pada diameter perapian tungku), masing-masing dengan raceway sendiri, diatur secara simetris di sekelilingnya. Kedalaman setiap raceway biasanya berkisar antara 1 meter (m) hingga 2 m, tergantung pada energi kinetik dari semburan udara panas.
Bahan yang tidak terbakar meninggalkan raceway dan bergerak ke atas tungku ke daerah bosh dan poros. Logam cair dan terak melewati 'deadman' (tempat tidur kokas yang stagnan) ke perapian tungku di mana mereka dikumpulkan dan dikeluarkan secara berkala melalui taphole. Terak kemudian dipisahkan dari besi cair. Beberapa tungku memiliki tapholes terpisah untuk terak dan besi. Diperlukan waktu sekitar 6 jam (h) hingga 8 jam agar bahan mentah turun ke perapian tungku, meskipun kokas dapat bertahan selama berhari-hari, atau bahkan berminggu-minggu, di dalam orang mati. Besi cair, disebut sebagai HM diangkut ke fasilitas pembuatan baja. Persyaratan kualitas HM untuk pembuatan baja adalah kualitas HM yang konsisten dan suhu yang setinggi mungkin.
Gas panas yang meninggalkan bagian atas tungku dikenal sebagai gas BF atas. Ini didinginkan, dibersihkan, dan digunakan di pabrik baja sebagai bahan bakar gas dengan sebagian besar digunakan untuk pemanasan kompor ledakan panas. Gambar 1 menunjukkan penampang BF yang menunjukkan zona yang berbeda beserta suhunya.
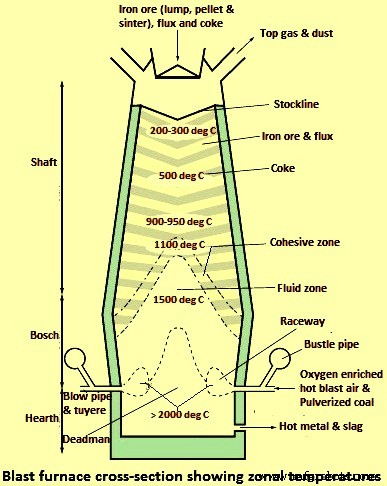
Gambar 1 Penampang BF menunjukkan zona yang berbeda beserta suhunya
Reaksi kimia dalam BF
BF dapat dianggap sebagai tungku penukar panas dan pertukaran massa arus balik karena panas dipindahkan dari gas naik ke beban BF dan O2 dari beban turun ke gas. Sifat reaksi yang berlawanan dengan arus membuat keseluruhan proses menjadi proses yang sangat efisien. Reaksi kimia yang terjadi di dalam BF bersifat kompleks. Reaksi utama yang terjadi di dalam tungku dijelaskan di sini.
Reaksi kimia utama adalah reduksi muatan bijih besi menjadi besi metalik. Ini berarti penghilangan O2 dari oksida besi dari beban bijih melalui serangkaian reaksi kimia yang disebut sebagai reduksi gas atau reduksi tidak langsung. Reaksi-reaksi ini seperti yang diberikan di bawah ini.
3Fe2O3 + CO =2Fe3O4 + CO2 (dimulai pada sekitar 500 derajat C)
3Fe2O3 + H2 =2Fe3O4 + H2O
Fe3O4 + CO =3FeO + CO2 (berlangsung pada kisaran suhu 600 derajat C hingga 900 derajat C)
Fe3O4 + H2 =3FeO + H2O
FeO + CO =Fe + CO2 (terjadi pada kisaran suhu 900 derajat C hingga 1100 derajat C)
FeO + H2 =Fe + H2O
Reaksi di atas bersifat eksoterm dan menghasilkan panas. Pada saat yang sama ketika oksida besi mengalami reaksi ini, mereka juga mulai melunak dan meleleh. Pada suhu tinggi di dekat zona fluida, karbon (C) dari kokas mereduksi FeO untuk menghasilkan besi (Fe) dan CO. Reaksi ini, disebut sebagai 'reduksi langsung', sangat endotermik, dan panas yang mendorongnya disediakan oleh panas spesifik yang terkandung dalam gas raceway panas.
FeO + C =Fe + CO
Pembakaran dan gasifikasi batubara, dan kokas menghasilkan gas pereduksi (CO dan H2) yang mengalir ke atas tungku. Saat batubara dan kokas memasuki raceway, mereka dinyalakan oleh ledakan udara panas dan segera terbakar sesuai reaksi berikut untuk menghasilkan CO2 dan panas.
C + O2 =CO2
Karena reaksi berlangsung dengan adanya C berlebih pada suhu tinggi, CO2 direduksi dengan 'Boudouard atau reaksi kehilangan larutan' berikut menjadi CO yang merupakan reaksi endotermik.
CO2 + C =2CO
Selain itu, uap air (H2O) yang dihasilkan selama pembakaran berkurang sesuai dengan reaksi berikut yang lagi-lagi merupakan reaksi endoterm.
H2O + C =CO + H2
Injeksi batubara bantalan H2 menambah pengurangan tidak langsung. H2 merupakan gas pereduksi yang lebih efektif daripada C (reduksi langsung). Reaksi regenerasi H2 (H2O + C =CO + H2) kurang endotermik dan berlangsung lebih cepat daripada regenerasi CO (reaksi Boudouard). Kandungan H2 yang lebih tinggi dalam gas yang bergerak ke atas BF mendorong tingkat reduksi bijih besi yang lebih tinggi, dan karenanya meningkatkan produktivitas BF. Namun, konsentrasi H2 yang lebih tinggi juga dapat menyebabkan jumlah butiran halus kokas yang lebih tinggi di poros tungku.
Batu kapur dan dolomit turun ke dalam tungku dan tetap padat saat melewati reaksi kalsinasi berikut.
CaCO3 =CaO + CO2
(Ca,Mg)CO3 =(Ca,Mg)O + CO2
Reaksi-reaksi ini bersifat endotermik dan dimulai pada sekitar 870 derajat C. CaO (kalsium oksida) dan MgO (magnesium oksida) membantu menghilangkan belerang (S) dan pengotor asam dari beban bijih untuk membentuk terak cair. Ini juga dapat membantu menghilangkan S yang dilepaskan dari kokas dan batu bara.
Masalah proses
Pengoperasian BF yang stabil tergantung pada distribusi seragam aliran gas yang bergerak ke atas dan aliran HM dan terak yang tidak terhalang ke perapian BF. Oleh karena itu, pemeliharaan permeabilitas dalam tungku penting untuk operasi tungku yang stabil, dan oleh karena itu produktivitas BF. Sebagian besar masalah teknis yang terkait dengan peningkatan laju injeksi batubara merupakan respons terhadap persyaratan permeabilitas. Beberapa masalah yang pada dasarnya terkait dengan tingkat PCI yang tinggi ditunjukkan pada Gambar 2.
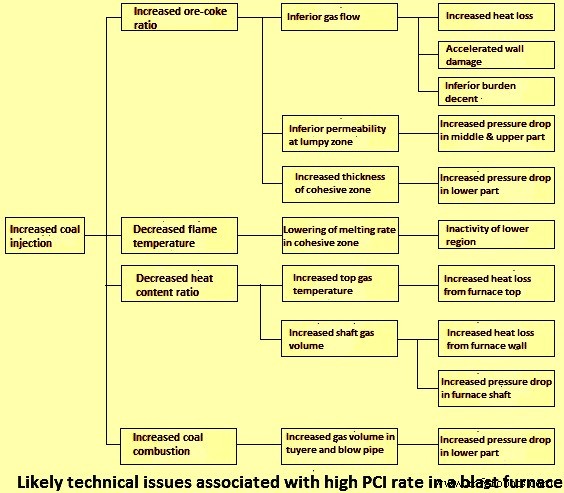
Gbr 2 Masalah teknis yang terkait dengan tingkat PCI yang tinggi dalam BF
Permeabilitas dalam tungku dipengaruhi oleh sifat-sifat beban bijih, kokas, dan batubara. Denda yang dihasilkan dari bahan-bahan ini dapat menumpuk, menghalangi aliran gas dan cairan. Arang yang tidak terbakar dari batu bara dan bubuk kokas, misalnya, dapat menumpuk di sarang burung walet, zona yang relatif padat antara raceway dan deadman, dan di sekitar bagian bawah zona kohesif. Hal ini dapat mengakibatkan fluktuasi aliran gas dan operasi yang tidak stabil. Aliran gas perifer dapat terjadi yang menyebabkan peningkatan beban panas pada dinding tungku, terutama di bagian bawah tungku. Hal ini dapat mempersingkat masa pakai lapisan refraktori tungku, sehingga mempercepat kebutuhan perbaikan modal awal.
Efisiensi proses BF tergantung pada laju penghilangan O2 dari beban bijih. Semakin banyak gas menghilangkan O2 dari beban bijih, semakin efisien prosesnya. Oleh karena itu, kontak yang erat antara gas dan beban bijih adalah penting. Untuk optimasi kontak ini, permeabilitas lapisan bijih harus setinggi mungkin. Rasio gas yang mengalir melalui beban bijih dan jumlah O2 yang akan dikeluarkan dari beban juga harus seimbang.
Permeabilitas lapisan bijih sangat ditentukan oleh jumlah butiran halus (kurang dari 5 mm) di dalamnya. Mayoritas denda biasanya dihasilkan oleh sinter, jika ada dalam beban yang dibebankan, atau dari bijih lump. Ada dua sumber butiran halus, yang (i) membentuk bagian dari muatan bijih besi, dan (ii) dihasilkan oleh degradasi bahan beban bijih selama pengangkutan dan pengisiannya, dan di dalam poros tungku.
Oleh karena itu penting untuk menyaring bahan beban untuk menghilangkan denda sebelum dibebankan ke BF. Ukuran yang disukai untuk bahan yang berbeda biasanya 5 mm sampai 30 mm untuk sinter, 8 mm sampai 16 mm untuk pelet dan 10 mm sampai 30 mm untuk bijih bijih besi benjolan. Sebagian besar BF yang beroperasi saat ini dengan kecepatan PCI tinggi menggunakan sebagian besar beban bijih yang disiapkan yang terdiri dari lebih dari 80% sinter dan/atau pelet.
Dalam kasus di mana butiran halus dihasilkan oleh degradasi bahan beban bijih selama pengangkutan dan pengisiannya, dan di dalam poros tungku, penting untuk mengontrol karakteristik degradasi bahan beban. Ada tes standar untuk menentukan ketahanan material beban besi terhadap degradasi fisik akibat benturan dan abrasi, dan untuk mengukur disintegrasi selama reduksi pada suhu rendah.
Beban bijih dengan reducibility tinggi lebih disukai. Ada metode standar yang tersedia untuk penentuan reducibility bahan yang merupakan beban bijih. Sangat disayangkan bahwa peningkatan reducibility dapat meningkatkan degradasi dan disintegrasi bahan bijih. Kandungan silika (SiO2) dan kalsium oksida (CaO) yang lebih rendah, dan kandungan alkali yang lebih tinggi meningkatkan kemampuan mereduksi tetapi juga meningkatkan disintegrasi.
Permeabilitas aliran gas berkurang segera setelah material beban mulai melunak dan mencair. Oleh karena itu, bahan beban harus mulai meleleh pada suhu yang relatif tinggi sehingga tidak memperlambat aliran gas saat masih tinggi di poros. Transisi cepat dari keadaan padat ke cair juga diinginkan. Sifat leleh ditentukan oleh komposisi terak. Pelelehan pelet dan bijih lump biasanya dimulai pada kisaran suhu 1000 derajat C hingga 1100 derajat C, sedangkan sinter dasar mulai meleleh pada suhu yang lebih tinggi.
Selanjutnya, kualitas bahan beban harus konsisten untuk memastikan operasi BF yang stabil. Juga, itu harus didistribusikan ke BF sedemikian rupa untuk mencapai operasi yang lancar dengan produktivitas tinggi.
Coke memiliki tiga fungsi utama dalam sebuah BF. Ini adalah (i) kimia, (ii) termal, dan (iii) fisik. Karena fungsi kimianya, ia memainkan peran sebagai agen pereduksi. Pembakarannya menghasilkan gas untuk mereduksi oksida besi, dan oksida lainnya seperti silika (SiO2). Ini juga memasok C untuk karburisasi HM. Karena fungsi termalnya, kokas dibakar di raceway yang menyediakan sumber panas untuk melelehkan besi dan terak, dan juga untuk mendorong proses endotermik. Karena fungsi fisiknya, kokas memberikan dukungan untuk beban besi pada matriks permeabel, di mana gas dan besi cair dan terak dapat mengalir.
Batubara berkontribusi pada dua fungsi pertama tetapi tidak pada fungsi 'fisik' ketiga. Di sini, kokas harus memastikan permeabilitas untuk gas tungku di wilayah di atas zona kohesif, di dalam zona kohesif, dan untuk gas dan produk cair di wilayah bosh dan perapian. Peranan kokas sangat penting terutama di zona kohesif dimana pelunakan dan pelelehan bijih besi dapat membentuk lapisan kedap air, dipisahkan oleh lapisan atau jendela kokas yang permeabel. Selanjutnya, di zona ini kokas membentuk kisi-kisi yang kuat yang menopang sebagian berat dari beban di atasnya. Karena fungsi fisik kokas, ada batasan jumlah batubara yang dapat disuntikkan.
Kualitas kokas yang tinggi dan konsisten diperlukan untuk mengurangi pembentukan butiran halus yang dapat menyebabkan permeabilitas yang buruk, pengoperasian BF yang tidak stabil, dengan hasil produktivitas yang lebih rendah. Tingkat di mana kokas terdegradasi dan menghasilkan butiran halus saat turun melalui tungku terutama dikendalikan oleh reaksi Boudouard, tegangan termal, tekanan mekanis dan akumulasi alkali, tergantung pada posisinya di dalam tungku dan juga pada kondisi operasional. Dengan demikian, sifat-sifat utama kokas berikut ini menarik.
- Kekuatan dingin (dalam BF) – Kekuatan dingin menentukan ketahanan terhadap kerusakan dan abrasi selama penanganan. Mekanisme penghancuran dan abrasi mendominasi pembentukan butiran halus di bagian atas atau poros tungku, dan mekanisme ini sering dikaitkan dengan kekuatan dingin kokas. Tersedia tes standar untuk menilai degradasi mekanis (kekuatan dingin) kokas.
- Kekuatan panas – Karena kekuatan panas dari kokas, ada retensi integritas struktural dalam gumpalan kokas ketika direaksikan dengan CO2 pada suhu tinggi. Reaksi kokas dengan CO2 (reaksi Boudouard) di jalur balap mendorong degradasinya dan produksi butiran halus. Selain itu, degradasi yang disebabkan oleh benturan dengan ledakan udara panas berkecepatan tinggi dapat terjadi. Coke dengan kekuatan panas yang lebih rendah dapat mengakibatkan raceway terdistorsi dan zona kohesif, dan akumulasi denda coke di deadman yang menyebabkan masalah permeabilitas. Oleh karena itu, kekuatan dan stabilitas struktur kokas setelah bereaksi dengan CO2 pada suhu tinggi merupakan parameter penting. Dua indeks digunakan untuk memberikan indikasi perilaku potensial kokas pada suhu tinggi. Ini adalah (i) Coke Reactivity Index (CRI) dan (ii) Coke Strength after Reaction (CSR). Ini ditentukan menggunakan tes standar.
- Komposisi kimia- Sehubungan dengan komposisi kimia, kandungan abu, S (yang mempengaruhi S dalam HM) dan alkali adalah penting. Alkali (dan oksida dasar lainnya seperti oksida besi) meningkatkan reaktivitas kokas terhadap CO2 karena efek katalitiknya, dan menurunkan ketahanan abrasinya. Jadi kokas lebih rentan terhadap degradasi. Abu dalam kokas biasanya memiliki efek buruk pada kinerja BF.
- Rata-rata ukuran dan distribusi ukuran – Bahan yang berukuran terlalu kecil harus disaring sebelum diisi untuk menghindari kemungkinan masalah permeabilitas. Distribusi ukuran berdampak langsung pada permeabilitas tungku, baik di area poros maupun bagian bawah tungku. Ukuran rata-rata rata-rata dari kokas yang diisi biasanya dalam kisaran 20 mm hingga 50 mm. Di bawah operasi BF yang stabil, sebagian besar butiran halus kokas dikonsumsi di dalam tungku oleh reaksi Boudouard, karburisasi HM, dan reaksi dengan terak, dengan hanya sedikit sisa gas BF teratas.
Kadar kokas di bawah 300 kilogram per ton HM (kg/tHM) telah menjadi praktik mutakhir di BF modern dengan PCI. Nilai terendah untuk kadar kokas yang dicapai adalah sekitar 240 kg/tHM. Penggunaan nut coke sudah menjadi hal yang umum, jumlahnya tergantung kondisi setempat. Coke kacang meningkatkan hasil C keseluruhan dari BF. Ini melindungi kokas kasar dari degradasi ukuran yang berlebihan karena lebih disukai digasifikasi di poros.
Emisi dan masalah lingkungan
Secara global, industri besi dan baja menyumbang bagian tertinggi dari emisi CO2 (sekitar 27%) dari sektor manufaktur. Ini karena produksinya yang intensif energi, ketergantungannya pada batu bara sebagai sumber energi utama, dan volume produksi baja yang besar. Sekitar 60% dari produksi baja global melalui rute BF dan pembuatan besi oleh BF adalah salah satu sumber utama emisi di dalam pabrik baja, karena sebagian besar konsumsi energi terkait dengan proses BF sekitar 2,4 giga kalori per ton ( Gkal/t) hingga 3,1 Gkal/t baja mentah, termasuk kompor sembur panas. Karena CO2 dikaitkan dengan perubahan iklim, pengurangannya menjadi perhatian penting. Di bawah ini dijelaskan jumlah, komposisi, dan nilai kalor (CV) gas BF teratas, emisi udara, dan emisi CO2 dan pengurangannya, serta secara singkat limbah cair dan padat.
Gas BF kotor panas meninggalkan bagian atas tungku, di bawah tekanan, dan melewati pabrik pembersih gas (GCP) di mana partikulat (terutama arang yang tidak terbakar, jelaga dan kokas halus) dan air dihilangkan, dan gas BF didinginkan. Jumlah debu yang diperlukan untuk dihilangkan meningkat dengan meningkatnya laju injeksi batubara. GCP modern adalah unit multi-langkah di mana partikel kasar pertama kali dihilangkan dengan pemisahan gravitasi (penangkap debu atau siklon), diikuti dengan penghilangan butiran halus oleh scrubber basah atau presipitator elektrostatik basah untuk mencapai kadar debu di bawah 10 mili gram per meter kubik (mg/ air mani). Di beberapa BF, penghilangan butiran halus menggunakan filter kantong udara juga dilakukan. GCP modern bahkan memungkinkan debu yang diekstraksi disortir ke dalam jenis yang berbeda agar dapat digunakan kembali secara efektif.
Gas BF teratas mengandung sekitar H2 – 4%, CO – 25%, dan CO2 – 20%, dengan sisanya sebagian besar adalah nitrogen (N2). Ini memiliki CV sekitar 810 kilo kalori per meter kubik (kkal/cum), yaitu sekitar 35% hingga 40% dari kandungan energi batubara dan kokas diekstraksi dari BF dalam gas BF. Gas BF yang telah dibersihkan digunakan di berbagai tempat di pabrik baja termasuk dalam pemanasan udara sembur di kompor sembur panas. CV gas BF mempengaruhi penggunaannya dalam proses hilir.
BF modern biasanya dioperasikan pada tekanan tinggi untuk meningkatkan produktivitas tungku. Di banyak BF, turbin pemulihan tekanan atas digunakan untuk menghasilkan listrik dari tekanan yang tersisa di gas atas. Output daya turbin pemulihan tekanan atas dapat mencakup sekitar 30% dari kebutuhan listrik untuk semua peralatan BF, termasuk blower untuk semburan udara. Jumlah, komposisi dan CV gas BF dipengaruhi oleh sifat-sifat batubara serta kondisi operasinya. Misalnya, batubara HV biasanya memiliki kandungan H2 yang lebih tinggi dan CV yang lebih rendah daripada yang LV, dan oleh karena itu dapat menghasilkan gas BF dengan kandungan H2 yang lebih tinggi dan CV yang lebih rendah. Penyuntikan batubara HV biasanya meningkatkan jumlah debu dalam gas BF dibandingkan dengan batubara LV. Jumlah debu halus dalam gas BF biasanya lebih tinggi ketika batubara VM (volatile matter) yang sangat tinggi disuntikkan. Peningkatan material karbon dalam debu halus diidentifikasi sebagai jelaga, yang berasal dari pembakaran tidak sempurna VM batubara.
Hanya sedikit informasi yang tersedia sehubungan dengan perubahan emisi udara saat batubara disuntikkan ke dalam BF. Injeksi batubara tidak menyebabkan peningkatan kandungan S pada gas BF ketika batubara dengan kandungan S sekitar 0,8% diinjeksikan ke dalam BF. Sebuah studi untuk inventaris siklus hidup untuk BF telah menunjukkan bahwa emisi SO2 dan NO2 sebenarnya masing-masing berkurang sekitar 22% dan 16%, ketika tingkat PCI meningkat dari 16 kg/tHM menjadi 116 kg/tHM.
Batasan kandungan klorin (Cl) untuk batubara (biasanya di bawah 0,05%) adalah karena sifat korosif dari senyawa klorin yang dihasilkan, khususnya asam klorida (HCl). Klorin, terbentuk di raceway saat batubara disuntikkan, bereaksi dengan gas alkali (dari batubara atau abu kokas) membentuk alkali klorida (NaCl dan KCl). Beberapa asam HCl dan sejumlah kecil senyawa Cl lainnya juga dihasilkan. Bagian dari asam HCl yang dihasilkan dihilangkan oleh batu kapur di tungku. Alkali klorida (juga dihasilkan dari bijih besi) dapat bersirkulasi di dalam poros yang menyebabkan disintegrasi sinter dan dengan demikian, meningkatkan kandungan butiran halus dan penurunan permeabilitas tungku. Senyawa Cl juga dapat menimbulkan korosi pada lapisan refraktori dan saluran pipa di GCP BF. Mereka dihilangkan dalam air cucian di scrubber.
Termodinamika dan metalurgi dari proses BF memusatkan elemen jejak yang berasal dari batu bara, kokas, dan bijih besi ke dalam aliran keluaran yang berbeda. Unsur-unsur volatil tinggi, seperti kadmium (Cd) dan merkuri (Hg), diserap pada debu halus dan meninggalkan gas atas BF. Mereka dihapus di GCP (sekitar 75% Cd dan 90% Hg). Cd dan Hg tidak pergi ke HM atau terak. Unsur-unsur yang kurang mudah menguap, seperti seng (Zn) dan tembaga (Cu), partisi antara logam cair dan terak. Mayoritas Zn dari semua sumber input larut ke dalam HM karena tekanan tinggi di BF, dengan sekitar 70% tertinggal di HM dan terak. Timbal (Pb) memiliki suhu penguapan yang lebih rendah daripada Zn, dan dapat terakumulasi dalam BF, sehingga menurunkan produktivitas. Sebagian besar timbal (Pb) berasal dari bijih besi (sinter, lump ore dan pellet), diikuti dengan kokas. Sebagian besar meninggalkan BF diserap pada partikel debu halus dari bahan beban dan kokas, dan dihilangkan di GCP di scrubber (lebih dari 80%). Pemindahannya ke HM dianggap tidak terlalu penting. Hanya sekitar 1% masing-masing Cd dan Pb, dan 5% Hg yang dipancarkan dalam bentuk gas logam.
Emisi CO2 dari BF dipengaruhi oleh sejumlah faktor. BF yang lebih kecil cenderung mengeluarkan lebih banyak CO2/tHM daripada BF yang besar karena efisiensinya yang lebih rendah. BF yang lebih besar biasanya lebih efisien karena kehilangan panas lebih rendah dan biasanya lebih ekonomis untuk memasang peralatan hemat energi. Kehilangan energi untuk BF yang efisien kurang dari 10% dari total input energi. Selain itu, kualitas bahan baku mempengaruhi konsumsi energi dan emisi CO2. Misalnya, batubara dengan abu yang lebih rendah menghasilkan jumlah terak yang lebih rendah daripada batubara dengan abu yang lebih tinggi, dan karenanya efisiensi termal yang lebih baik tercapai karena lebih sedikit energi yang dibutuhkan untuk melelehkan abu. Untuk setiap persentase peningkatan kadar abu dari batubara yang diinjeksi, dibutuhkan sekitar 1,5 kg/tHM kokas tambahan yang meningkatkan masukan C dan dengan demikian, emisi CO2.
Kualitas kokas mempengaruhi kuantitas zat pereduksi (kokas, dan batubara) yang dibutuhkan dalam BF dan oleh karena itu, emisi CO2. Peningkatan 1% abu kokas meningkatkan laju terak sebesar 10 kg/tHM menjadi 12 kg/tHM, dan kebutuhan energi untuk setiap 10 kg/tHM terak sekitar 15 Mcal/tHM. Kualitas kokas tergantung pada kualitas batubara yang digunakan dalam produksinya dan proses pembuatan kokasnya.
Kualitas bijih besi berbeda dalam komposisi kimia dan kandungan besinya, yang mempengaruhi energi yang dibutuhkan untuk reaksi reduksi untuk menghasilkan besi, dan untuk melelehkan bijih besi. Komposisi kimia gangue mempengaruhi jumlah batugamping atau kapur yang harus ditambahkan untuk mencapai kebasaan terak yang dibutuhkan. Secara total, faktor-faktor ini dapat membuat perbedaan sekitar 240 Mcal/t hingga 480 Mcal/t perbedaan dalam kebutuhan energi untuk BF. Namun, kualitas bijih besi memburuk karena menipisnya deposit berkualitas tinggi. Oleh karena itu, kebutuhan energi untuk pembuatan besi meningkat karena faktor ini.
PCI mengurangi emisi CO2 keseluruhan dari pabrik baja dibandingkan dengan operasi all-coke. Ini terutama karena PCI mengurangi kebutuhan akan kokas dan karenanya konsumsi energi dan emisi CO2 dari baterai oven kokas. Energi yang dihemat rata-rata sekitar 840 Mcal/t coke diganti. PCI juga dapat menurunkan konsumsi energi dalam BF.
Studi Life Cycle Assessment (LCA) mengevaluasi kinerja lingkungan produk dan material dari penambangan bahan mentah hingga akhir masa pakai dan pembuangan limbah. Fase awal LCA melibatkan melakukan inventarisasi siklus hidup, yang mengkuantifikasi material, energi, dan emisi yang terkait dengan sistem tertentu. Industri besi dan baja memiliki aliran energi dan material yang kompleks, baik di dalam maupun di luar pabrik baja. Banyak produk dapat dijual 'melewati pagar' dan beberapa dapat dikirim ke jarak jauh. Oleh karena itu, penggunaan energi produksi penuh dan emisi CO2 mungkin jauh lebih tinggi atau lebih rendah daripada yang disarankan oleh tapak lokasi. Misalnya, membeli kokas dan/atau listrik mengurangi emisi CO2 di lokasi tetapi meningkatkan emisi di tempat lain. Hasil LCA tergantung di mana batas sistem ditetapkan.
Asosiasi Baja Dunia (WSA) telah menggunakan pendekatan LCA untuk mengukur penggunaan sumber daya, energi dan emisi lingkungan yang terkait dengan produksi empat belas produk industri baja dari ekstraksi bahan mentah hingga gerbang pabrik baja ('cradle-to-gate' ). Inventaris siklus hidup mencakup rute tungku oksigen BF/dasar dan tungku busur listrik. Inventaris siklus hidup untuk BF telah menunjukkan sekitar 6,5% pengurangan CO2 ketika tingkat PCI ditingkatkan dari 16 kg/tHM menjadi 116 kg/tHM. Namun, ada batasan jumlah batu bara yang bisa disuntikkan. Sebuah penelitian menunjukkan bahwa laju maksimum batubara yang dapat diinjeksikan adalah sekitar 250 kg/tHM. Namun, menurut WSA, peningkatan injeksi batu bara di atas 180 kg/tHM tidak mengurangi jumlah kokas, dan batu bara tambahan hanya digasifikasi dan menghasilkan lebih banyak gas BF.
Dalam salah satu studi yang dilakukan dengan metodologi LCA, diperkirakan bahwa efek pengurangan CO2 dari PCI adalah 0,07 kg CO2 pada laju injeksi 0,1 kg/kg HM.
Berbagai penelitian LCA menunjukkan bahwa menyuntikkan zat pereduksi yang mengandung H2, seperti batu bara, dapat menurunkan emisi CO2 (dibandingkan dengan operasi semua kokas karena kandungan H2 kokas hanya sekitar 0,5%). Pengurangan CO2 lebih lanjut dapat dicapai dengan menurunkan input C (coke dan batubara). Langkah-langkah untuk mencapai hal ini dapat dibagi menjadi dua kelompok berikut.
- Mereka yang mempromosikan operasi BF efisiensi yang lebih tinggi. Ini termasuk suhu ledakan yang lebih tinggi, peningkatan efisiensi poros, dan suhu zona cadangan termal yang lebih rendah. Namun, langkah-langkah ini juga mengurangi pasokan gas BF atas ke proses hilir. Meminimalkan produksi gas BF teratas mengurangi emisi CO2 tetapi mungkin tidak dapat dilakukan di pabrik di mana pemanfaatan gas BF dalam proses hilir penting.
- Langkah-langkah yang mendorong penghematan energi dalam proses pembuatan besi, seperti pengurangan kehilangan panas BF, pengisian besi logam, laju terak yang lebih rendah, dan pengoperasian dengan rasio sinter yang lebih rendah atau sinter yang telah dikurangi sebelumnya.
Selanjutnya, mendaur ulang gas BF yang didekarbonisasi ke BF menurunkan emisi CO2. Teknologi ini, biasanya disebut daur ulang gas atas (TGR), pertama-tama menghilangkan CO2 dengan proses komersial seperti 'Selexol', sebelum memanaskan kembali dan menginjeksikan gas BF ke dalam poros tungku dan/atau melalui tuyeres. Ini membutuhkan pengoperasian tungku dengan ledakan O2 murni untuk menghindari akumulasi N2 karena daur ulang. CO2 yang ditangkap dapat disimpan di bawah tanah. Gas BF, yang terutama terdiri dari CO dan H2, mengurangi konsumsi C dan meningkatkan produktivitas BF. ULCOS (Ultra-Low CO2 Steelmaking), sebuah konsorsium dari 48 perusahaan dan organisasi Eropa, memelopori teknologi ini. Pengujian teknologi skala pilot selama periode enam minggu menghasilkan pengurangan emisi CO2 hingga 76%, asalkan CO2 yang ditangkap disimpan.
Air limbah dan produk sampingan
Produksi baja adalah proses intensif air, mengkonsumsi sekitar 180 cum hingga 200 cum air per ton baja. BF mengkonsumsi sekitar 14 cum hingga 17,5 cum air per ton HM, yang sebagian besar digunakan untuk tujuan pendinginan (untuk mendinginkan dinding dan tuyer BF), dan untuk memadamkan terak. Air selanjutnya digunakan di BF GCP. Air limbah yang dihasilkan dari proses ini diolah sebelum didaur ulang dengan lebih dari 90% air didaur ulang. Jumlah dan komposisi air limbah sebagian tergantung pada kualitas bahan baku BF. Misalnya, bahan baku dengan kandungan garam tinggi dapat membutuhkan volume air pencuci yang jauh lebih tinggi di scrubber gas BF teratas. Proses pengolahan air dapat menghilangkan Cd dan logam berat lainnya dalam air limbah sebelum didaur ulang atau dibuang.
Produksi besi dan baja terintegrasi menghasilkan sekitar 450 kg hingga 500 kg residu dan produk sampingan per ton baja mentah yang diproduksi. Of this, more than 375 kg/t is slag and around 60–65 kg/t is dust and sludge from flue gas cleaning and scale. Around 86 % of all residues and by-products can be recycled internally and externally, after treatment. The coarse dust removed from the BF top gas by dry separation can be recycled internally. The sludge containing the finer particles from the BF GCP is typically landfilled. In some plant it is also recycled through sinter plant.
Different forms of slag are produced depending on the method used to cool the liquid slag. These include air cooled slag, expanded or foamed slag, pelletized slag, and granulated slag. The majority of the slag can be sold, with only a small amount being used for landfilling (less than 10 %). Thus BF slag is considered to be a by-product rather than a waste. The slag can be utilized in cement production, road construction, as a building material, and for special purposes. The possible uses depend on the properties and form of the slag.
The composition of the slag depends on the quality of the BF raw materials. It is formed from the gangue material in the iron ore, and the ash from the coke and coal. It consists principally of silicates and alumino-silicates of Ca (calcium) and Mg (magnesium), together with other compounds of S, Fe (iron), Mn (manganese), and other trace elements.
The amount of slag generated increases with rising injection rates and increasing ash and S content of the reductants. S in the slag originates mainly from the coal. However, the S is effectively captured within the slag. It is only any S present on the surface which is potentially leachable. The trace elements also probably are captured within the slag.