Aspek Teoritis dari Proses Pengurangan Langsung
Aspek Teoretis Proses Reduksi Langsung
Dalam proses reduksi langsung bijih besi, besi logam padat (Fe) diperoleh langsung dari bijih besi padat tanpa membuat bijih atau logamnya mengalami fusi. Reduksi langsung dapat didefinisikan sebagai reduksi dalam keadaan padat pada potensial oksigen (O2) yang memungkinkan reduksi oksida besi, tetapi tidak untuk oksida lain (MnO, SiO2 dll.), ke elemen yang sesuai. Karena reduksi dalam keadaan padat, sangat kecil kemungkinan unsur-unsur ini larut (pada aktivitas termodinamika rendah) dalam besi tereduksi, sehingga oksida yang lebih stabil daripada besi pada dasarnya tetap tidak tereduksi. Reduksi langsung bijih besi juga terjadi di poros tanur sembur oleh gas yang naik.
Besi – sistem oksigen
Sistem besi-oksigen (Fe-O) mungkin merupakan salah satu sistem yang paling banyak dipelajari. Termodinamika sistem dipahami dengan baik dan banyak informasi tersedia tentang kinetika reduksi gas yang melibatkan oksida besi. Fasa padat yang stabil secara termodinamika yang terjadi antara 400 derajat C dan 1400 derajat C dalam sistem Fe-O, pada tekanan total I kg/cm persegi, ditunjukkan dalam diagram biner (Gambar 1). Diagram ini menunjukkan bahwa Fe membentuk dengan O2 tiga senyawa padat yang stabil yaitu (i) hematit – Fe2O3, (ii) magnetit – Fe3O4, dan wustit – FexO, di mana x sedikit lebih rendah dari 1. Fasa FeO non-stoikiometri ( wustite) tidak stabil di bawah 570 derajat C dan terurai menjadi campuran logam Fe dan Fe3O4. Jadi, pembacaan dari kanan ke kiri melintasi diagram fase pada suhu konstan, di bawah 570 derajat C urutan fase adalah Fe2O3 – Fe3O4 – Fe, sedangkan di atas 570 derajat C urutannya adalah Fe2O3 – Fe3O4 – FeO – Fe.
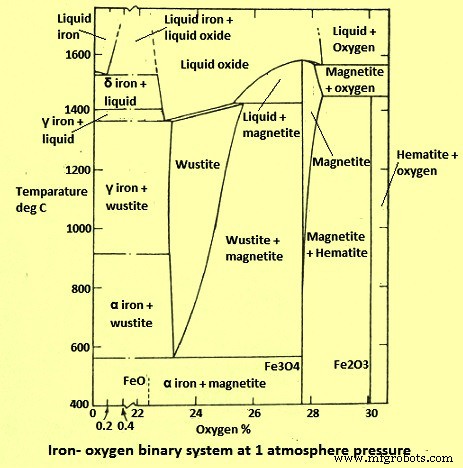
Gambar 1 diagram sistem biner Fe-O
Kelarutan O2 yang dapat diabaikan dalam besi alfa dan gamma padat adalah kurang dari 0,01% O2. Oleh karena itu, kandungan O2 tidak berpengaruh pada suhu transisi dari modifikasi Fe padat dan diabaikan dalam diagram.
Mempertimbangkan kesetimbangan reaksi, reduksi oksida Fe melibatkan satu atau lebih langkah berikut (i) hematit (Fe2O3) -> magnetit (Fe3O4), (ii) magnetit (Fe3O4) -> besi (Fe), (iii) magnetit ( Fe3O4) -> wustit (FeO), dan (iv) wustit (FeO) -> besi (Fe).
Wustit stabil hanya pada suhu yang lebih tinggi dari 570 derajat C. Kesetimbangan termodinamika untuk reaksi di atas terkenal dengan dua zat pereduksi gas utama yang digunakan yaitu hidrogen (H2) dan karbon monoksida (CO).
Besi – oksigen – sistem karbon
Kesetimbangan Fe dan Fe oksida dengan campuran gas CO dan CO2 (karbon di-oksida) dengan karbon padat (C) ditunjukkan pada Gambar 2.
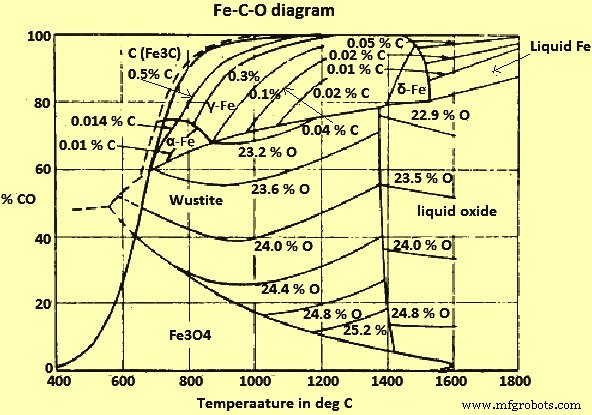
Gambar 2 diagram sistem Fe-CO-O
Dari Gambar 2 dapat disimpulkan bahwa, pada suhu di atas 710 derajat C dan pada tekanan total 1 kg/cm2 semua oksida Fe dapat direduksi oleh campuran gas CO/CO2 yang berada dalam kesetimbangan dengan C, dan dapat, karenanya, direduksi oleh C itu sendiri. Pada suhu yang lebih rendah hanya campuran yang sangat jenuh dengan C dan yang, oleh karena itu, menurut kesetimbangan Boudouard, bereaksi terhadap deposisi C memiliki aksi reduksi pada wustit.
Besi – hidrogen – sistem oksigen
Diagram kesetimbangan Fe dan Fe oksida dengan campuran gas H2 dan H2O (uap) ditunjukkan pada (Gbr 3).
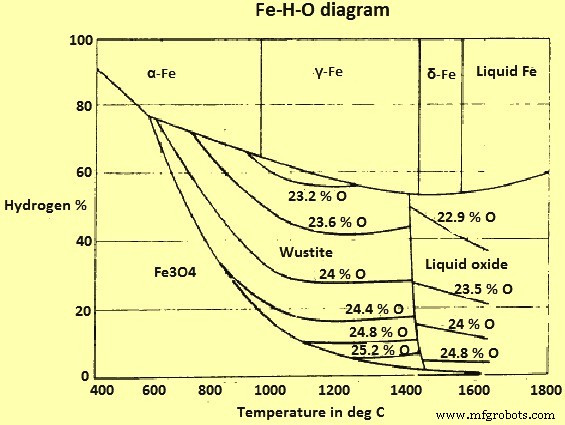
Gambar 3 diagram sistem Fe-H-O
Perbedaan utama antara sistem ini dan sistem Fe-O-C adalah tidak adanya 'garis jelaga' atau fenomena yang sesuai. Oleh karena itu, secara teori dimungkinkan untuk mereduksi hematit (dan magnetit) menjadi Fe dengan H2 pada suhu berapa pun.
Perbandingan antara reduksi oleh CO dan H2
Dari studi sistem Fe-C-O, dan Fe-H-O (Gambar 4), terlihat bahwa di atas 815 derajat C, H2 adalah zat pereduksi yang lebih efisien daripada CO (yaitu, rasio kesetimbangan H2/H2O lebih rendah daripada CO yang sesuai. /CO2 rasio), sementara itu berlawanan pada suhu yang lebih rendah. Namun, kesetimbangan ini hampir tidak tercapai dalam tungku industri, karena laju reduksi menjadi sangat lambat saat kesetimbangan didekati. Ketika kondisi sangat menyimpang dari kesetimbangan, laju reaksi masing-masing untuk reduksi dengan H2 dan CO berada dalam urutan terbalik dengan yang biasanya diharapkan dari pertimbangan kesetimbangan. Jadi, H2 sebenarnya adalah zat pereduksi yang lebih efisien untuk proses non-kesetimbangan yang dirancang untuk beroperasi pada suhu lebih rendah dari 815 derajat C dan CO lebih efisien pada suhu yang lebih tinggi.
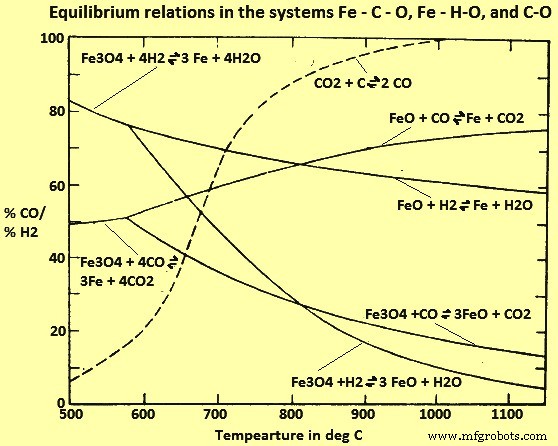
Gambar 4 Hubungan kesetimbangan pada sistem Fe-C-O, Fe-H-O, dan C-O
Studi tentang pengaruh komposisi gas campuran CO dan H2 pada suhu yang berbeda telah menunjukkan bahwa dengan meningkatnya kandungan H2 dari campuran gas pereduksi, laju reaksi meningkat. Hubungan ini ternyata sangat nonlinier.
Reduksi oksida Fe menjadi logam Fe dengan H2 bersifat endotermik dan sumber panas eksternal diperlukan untuk mempertahankan suhu yang diperlukan. Reaksi yang sesuai dengan CO adalah eksotermik dan di bawah kondisi yang dikontrol dengan tepat, reaksi tersebut dapat bertahan sendiri secara termal. Bahkan, mungkin diperlukan untuk mengencerkan CO dengan H2 atau gas penyerap panas lainnya untuk menghindari muatan yang terlalu panas. Beberapa proses telah dirancang untuk memanfaatkan keseimbangan termal CO – H2 dan menggunakan campuran gas-gas ini untuk meningkatkan jumlah reduksi yang diperoleh selama pemanasan bijih, dari suhu sekitar hingga suhu reaksi maksimum sekitar 1100 derajat C.
Gambar 4 menunjukkan bahwa untuk semua suhu dalam kisaran di mana reduksi gas dimungkinkan secara ekonomis, campuran gas kesetimbangan mengandung setidaknya 60% CO dan/atau H2. Ketika kesetimbangan tidak tercapai, konsentrasi gas-gas ini yang tidak bereaksi bahkan lebih tinggi dan sebagian besar lewat tanpa perubahan melalui tungku pereduksi. Agar proses tersebut menjadi ekonomis maka perlu adanya pemanfaatan gas yang tersisa setelah reduksi wustite menjadi logam Fe, untuk reduksi oksida Fe yang lebih tinggi menjadi wustit dan/atau untuk regenerasi campuran gas dan penghapusan produk reaksi gas.
Reaksi gas-padat dan reaksi padat-padat
Reaksi gas-padat memainkan peran utama dalam teknologi, dan mencakup bidang yang sangat luas termasuk ekstraksi logam dari bijihnya (reduksi oksida Fe, dll.). Sebuah fitur umum dari semua sistem reaksi gas-padat adalah bahwa proses keseluruhan dapat melibatkan beberapa langkah antara. Biasanya, langkah-langkah antara ini melibatkan (i) difusi gas (perpindahan massa) reaktan dan produk dari sebagian besar fase gas ke permukaan luar partikel padat yang bereaksi, (ii) difusi reaktan gas atau produk gas melalui pori-pori produk reaksi padat atau melalui pori-pori padatan yang bereaksi sebagian, (iii) adsorpsi reaktan gas pada dan desorpsi produk reaksi dari permukaan padat, dan (iv) reaksi kimia aktual antara gas yang teradsorpsi dan padatan.
Di bidang reaksi gas-padat, ada beberapa fenomena lain yang dapat mempengaruhi kemajuan reaksi dan kinerja tungku di mana reaksi gas-padat dilakukan. Fenomena lain ini termasuk perpindahan panas, perubahan struktur padat (seperti sintering) yang menyertai reaksi, dan aliran gas dan padatan melalui tungku di mana reaksi gas-padat berlangsung. Tingkat pengurangan dikendalikan oleh faktor-faktor ini tergantung pada proses yang digunakan.
Reaksi antara padatan dapat dibagi menjadi dua kelompok utama yaitu (i) padatan sejati – reaksi padatan yang berlangsung dalam keadaan padat antara dua partikel yang bersentuhan satu sama lain, atau melalui migrasi partikel dalam keadaan padat, (misalnya pembentukan besi karbida melalui reaksi antara oksida Fe dan C), dan (ii) reaksi antara reaktan padat, yang berlangsung melalui zat antara gas (misalnya reduksi oksida Fe dengan karbon pada tekanan 1 kg/cm²).
Reduksi oksida Fe dengan C padat juga dapat menjadi reaksi padat-padat yang sebenarnya, asalkan dilakukan pada tekanan absolut yang sangat rendah. Selama salah satu studi yang dilakukan oleh reaksi campuran bubuk halus grafit (C) dan bijih hematit di bawah vakum 0,0005 mm Hg (merkuri) ditemukan bahwa pada suhu hingga 900 derajat C, reaksi berlangsung sangat perlahan, dan dalam 18 jam hanya Fe3O4 dan FeO yang terbentuk, tetapi tidak ada Fe. Selama pengujian transformasi yang cukup besar diamati hanya pada suhu yang lebih tinggi. Disimpulkan selama penelitian bahwa laju reaksi ditentukan oleh difusi ion Fe dalam fase oksida. Pengurangan yang dibuat dalam penyelidikan lain adalah bahwa C berdifusi dalam oksida Fe, mungkin hanya menarik secara historis. Namun, studi ini telah menunjukkan bahwa laju reaksi jelas meningkat ketika tekanan gas di atas campuran bubuk meningkat. Dalam pengujian dengan jenis yang sama, di mana aliran N2 (nitrogen) dilewatkan melalui campuran C dan Fe oksida, terjadi penurunan laju reaksi yang nyata seiring dengan peningkatan aliran N2. Semua penyelidikan ini, apakah dilakukan dalam ruang hampa atau di bawah N2, dengan laju reduksi oksida Fe bubuk serupa dalam CO atau H2, membuktikan bahwa reaksi wujud padat langsung C dan bijih (yang kadang-kadang dianggap sebagai mekanisme aktual pengurangan langsung yang sebenarnya) tidak penting untuk kemajuan proses reduksi di tungku industri.
Struktur pori dari besi tereduksi
Uji reducibility pada beberapa bijih alam telah menunjukkan bahwa porositas partikel bijih besi adalah salah satu faktor terpenting yang mengendalikan reducibility. Reduksibilitas dinyatakan sebagai kebalikan dari waktu yang dibutuhkan untuk reduksi 90%, bervariasi langsung dengan porositas. Reduksibilitas relatif meningkat dengan peningkatan porositas seperti yang diberikan oleh persamaan “Reduksi relatif =(porositas x 0,75) + 8,0”.
Reduksi oksida Fe selalu menghasilkan produk reaksi berpori. Sifat oksida dan kondisi reduksi mempengaruhi struktur pori-pori besi tereduksi. Ini karena reduksi berlangsung dari permukaan partikel ke arah dalam. Volume yang menempati ruang yang ditentukan oleh permukaan wustit asli berkurang. Ini hanya dapat dicapai dengan mengembangkan porositas. Studi mikrograf elektron pemindaian porositas ini telah menunjukkan bahwa secara umum, reduksi H2 memberikan struktur pori yang lebih halus daripada yang diperoleh dengan reduksi CO. Juga, dari pemindaian mikrograf elektron, menjadi jelas bahwa struktur pori menjadi lebih kasar karena suhu reduksi H2 meningkat secara progresif dari 600 derajat C menjadi 1200 derajat C.
Luas permukaan pori awal oksida Fe mempengaruhi luas permukaan pori besi tereduksi yang dibentuk oleh reduksi gas. Penurunan luas permukaan pori awal oksida Fe mengurangi luas permukaan pori besi tereduksi. Luas permukaan pori besi yang direduksi dari bijih hematit dalam H2 yang diukur dengan teknik BET (Brunauer-Emmett-Teller) menunjukkan bahwa ia menurun dengan meningkatnya suhu reduksi.
Hubungan antara temperatur reduksi dan ukuran pori kritis rata-rata dan radius pori terkecil diperoleh dari distribusi ukuran pori. Ukuran pori telah ditemukan meningkat perlahan dengan suhu reduksi hingga 900 derajat C, tetapi telah meningkat pesat dengan peningkatan suhu lebih lanjut. Hasil ini sesuai dengan pengamatan permukaan rekahan dengan pemindaian mikroskop elektron, yang menunjukkan pengasaran yang berbeda dari struktur pori pada suhu reduksi di atas 900 derajat C.
Luas permukaan pori dari bijih hematit yang tereduksi juga dipengaruhi oleh temperatur reduksi dan komposisi gas. Luas permukaan pori yang diperoleh dari reduksi hematit dalam campuran gas CO/CO2 adalah sekitar dua pertiga dari luas permukaan untuk reduksi campuran gas H2/H2O. Ini konsisten dengan struktur pori yang lebih kasar dari besi tereduksi CO/CO2 yang diamati di bawah mikroskop.
Difusi gas dalam pori-pori besi tereduksi telah diukur. Fluks difusi pada media berpori terjadi melalui dua proses difusi yaitu (i) difusi Knudsen, tidak bergantung pada tekanan dan sebanding dengan T (suhu) terhadap pangkat 1/2, dan (ii) difusi molekuler, berbanding terbalik dengan tekanan dan sebanding dengan T kekuatan 3/2.
Struktur ideal pembatas diasumsikan memiliki pori-pori dengan ukuran seragam yang semuanya saling berhubungan dan berpotongan dengan sudut 45 derajat.
Difusivitas efektif bervariasi untuk media berpori tertentu dengan suhu dan tekanan dan berbeda untuk pasangan gas biner yang berbeda. Struktur pori menjadi lebih halus dengan penurunan suhu reduksi.
Mode pengurangan
Pengurangan partikel bijih besi alami atau pelet hematit yang disinter menghasilkan pembentukan lapisan produk. Fenomena terkenal ini menjadi subyek banyak penelitian. Dalam salah satu studi terbaru tentang pengurangan pelet hematit yang disinter oleh H2, telah diperhatikan bahwa ada contoh khas pembentukan lapisan di bagian yang dipoles dari pelet hematit yang tereduksi sebagian. Antarmuka yang relatif mulus antara lapisan biasanya muncul pada perbesaran rendah, meskipun penampilan seperti itu bisa menyesatkan.
Ini menunjukkan bahwa difusi gas cukup di lapisan wustite untuk memberikan beberapa reduksi internal di depan antarmuka Fe/FeO yang maju. Zona reduksi internal diperpanjang saat (i) suhu diturunkan, (ii) porositas dinaikkan, dan (iii) ukuran partikel menjadi lebih kecil.
Pengaruh ukuran partikel pada waktu yang dibutuhkan untuk mencapai persentase pengurangan tertentu tergantung pada mode reduksi dan karenanya pada jenis proses pengontrol laju. Pertimbangan mode reduksi oksida Fe berpori dengan reduksi gas telah menunjukkan tiga proses pengendalian laju pembatas yaitu (i) reduksi internal seragam, (ii) membatasi kontrol campuran, dan (iii) difusi dalam lapisan Fe berpori. Jika reduksi hanya dikendalikan oleh salah satu dari ini, maka waktu reduksi terkait dengan diameter partikel (spheroidal) dalam salah satu dari tiga cara yaitu (i) reduksi internal seragam yaitu waktu tidak tergantung pada diameter, (ii) membatasi kontrol campuran, dan (iii) difusi dalam besi berpori.
Proses pengontrolan laju menjadi relatif sederhana hanya jika (i) ada reduksi internal yang seragam, oleh karena itu diperlukan ukuran partikel yang kecil, atau (ii) kendali laju akhir dengan difusi gas dalam pori-pori lapisan besi mendominasi, karena ukuran partikel besar. Juga harus disadari bahwa dapat terjadi transisi dari satu proses pengontrolan laju pembatas ke proses lainnya saat reduksi berlangsung, tergantung pada suhu, komposisi gas, ukuran partikel dan jenis oksida. Reduksi oksida besi juga dapat menunjukkan beberapa perilaku yang tidak dapat dijelaskan dan tidak biasa.
Laju reduksi partikel bijih Fe berpori
Porositas dan struktur pori bijih memiliki efek yang nyata pada tingkat dan keseragaman reduksi internal. Dalam salah satu studi, pengaruh ukuran partikel pada laju reduksi bijih hematit untuk campuran 90% CO dan 10% C02, dan untuk H2 pada 1000 derajat C telah menunjukkan bahwa dengan bertambahnya ukuran partikel, reduksi internal dibatasi ke daerah terluar partikel, sehingga terjadi penurunan laju reduksi keseluruhan dengan bertambahnya ukuran partikel.
Pada tahap awal reduksi partikel hematit berpori, terjadi konversi cepat menjadi FeO diikuti oleh reduksi internal FeO menjadi Fe. Dalam kasus yang membatasi difusi gas yang hampir sempurna dalam pori-pori oksida Fe, reduksi internal mendominasi dan lajunya dikendalikan terutama oleh reaksi gas-padat pada dinding pori. Lapisan Fe, setebal beberapa atom diasumsikan menutupi dinding pori FeO. Laju reduksi diduga dikendalikan bersama oleh difusi cepat O2 melalui pelapisan lapisan Fe pada dinding pori dan oleh reaksi kimia H2 atau CO dengan O2 pada permukaan lapisan Fe yang sangat tipis ini.
Pengaruh ukuran partikel menunjukkan bahwa laju reduksi meningkat dengan menurunnya ukuran partikel. Mikrograf tipikal menunjukkan bahwa mode reduksi bervariasi dari satu butir ke butir lainnya di dalam partikel. Ini karena perbedaan lokal dalam porositas butir oksida. Karena variasi ukuran pori dan difusi gas yang lebih cepat dalam pori-pori yang lebih besar, sebagian besar reaksi terjadi pada dinding pori-pori yang lebih besar. Artinya, hanya sebagian kecil dari total luas permukaan pori yang diharapkan dapat digunakan untuk reaksi. Laju reduksi H2 pada 800 derajat C yang dicapai dengan berbagai jenis partikel bijih hematit meningkat secara non-linier dengan meningkatnya luas permukaan pori Fe (atau FeO) yang terbentuk. Hasil ini memperkuat fakta bahwa semakin besar luas permukaan pori, semakin kecil fraksi dari total dinding pori yang digunakan dalam reaksi.
Laju reduksi internal dalam campuran gas H2 – CO biasanya merupakan jumlah dari dua laju reduksi individu dengan H2 dan CO. Baik data reduksi dan deposisi C yang diamati menunjukkan bahwa, di bawah 1000 derajat C, reaksi gas mengarah ke air- kesetimbangan gas lambat.
Laju reduksi bijih besi (lump atau pellet)
Laju reduksi lump ore atau pelet bijih bersifat kompleks dalam aliran gas pereduksi dalam unggun yang dikemas, Kompleksitasnya karena laju reduksi keseluruhan dikendalikan oleh beberapa proses reaksi secara seri, seperti panas dan massa transfer melalui lapisan batas film gas, reaksi gas-padat dan difusi gas dalam lapisan produk berpori. Melalui analisis matematis, yang difasilitasi oleh perhitungan komputer, banyak persamaan telah diturunkan untuk menggambarkan laju reduksi partikel oksida besar untuk berbagai mode reduksi.
Dalam beberapa percobaan dengan pelet tunggal atau partikel bijih besi, perpindahan panas relatif cepat dan, dengan aliran gas berkecepatan cukup tinggi, hambatan perpindahan massa film gas cukup kecil untuk diabaikan. Oleh karena itu, terutama ada dua langkah reaksi utama secara seri yang mempengaruhi laju reduksi yaitu (i) reaksi gas-oksida, dan (ii) difusi gas dalam oksida berpori dan lapisan produk berpori. Efek relatif dari proses laju ini tergantung pada ukuran partikel, komposisi gas, suhu dan mode reduksi, dan mereka berubah dengan kemajuan reduksi.
Difusi gas pada lapisan Fe berpori
Dalam salah satu studi, percobaan reduksi searah telah dilakukan untuk menunjukkan efek difusi gas dalam pori-pori lapisan Fe. Sampel silinder panjang dibuat dari potongan besar bijih hematit benjolan dan dikemas di dalam tabung nikel yang pas. Setelah reduksi H2 selama waktu yang dibutuhkan, sampel dipartisi secara aksial dan dipoles, dan ditentukan ketebalan lapisan Fe. Hasil eksperimen menunjukkan bahwa, ketika ketebalan lapisan Fe tereduksi sekitar 1 mm, reduksi lebih lanjut berlangsung sesuai dengan hukum laju parabola, yang serupa dengan hasil kontrol difusi pori. Pengujian ini telah menunjukkan bahwa dengan bertambahnya ketebalan lapisan berpori Fe, laju reduksi akhirnya dikendalikan oleh difusi gas dalam pori-pori lapisan Fe.
Reduksi internal parsial yang mendahului bagian depan utama lapisan Fe dapat menyebabkan jebakan beberapa FeO di lapisan tereduksi. Situasi ini dapat menyebabkan lambatnya pembuangan O2 pada tahap akhir reduksi.
Ketika suhu reduksi menurun, struktur pori menjadi jauh lebih halus, mungkin dengan banyak saluran sempit dan kemacetan pada kapiler yang terhubung, ketika difusi Knudsen mendominasi, maka nilai rasio difusivitas molekul efektif/rata-rata efektif difusivitas Knudsen rendah. Karena struktur pori menjadi lebih kasar dengan meningkatnya suhu reduksi, sehingga memudahkan aliran gas melalui pori-pori, rasionya menjadi lebih tinggi.
Pengaruh komposisi gas terhadap waktu pencapaian reduksi 50%, 75%, 90%, dan 95% untuk pelet bijih hematit sinter dan pelet bijih magnetit tereduksi pada 900 derajat C dengan campuran H2-CO-CO2 (dengan rasio CO/CO2 sama dengan 9 untuk menekan deposisi jelaga), adalah bahwa ketika H2 digantikan oleh CO, waktu reduksi isotermal untuk mencapai persentase tertentu dari penyisihan O2 meningkat secara bertahap hingga sekitar 50% CO dan dengan penambahan CO lebih lanjut, ada peningkatan yang nyata dalam waktu pengurangan. Waktu reduksi untuk 100% (rasio CO/CO2 sama dengan 9), kira-kira 10 kali lebih lama daripada di H2 pada suhu yang sama. Difusivitas gas molekuler dalam sistem biner, seperti H2-H2O atau CO-CO2, yang diturunkan dari teori kinetik gas, adalah invarian untuk sistem dan pada dasarnya tidak bergantung pada komposisi gas. Namun dalam sistem terner dan multi komponen, masing-masing spesies memiliki difusivitas yang berbeda dan bervariasi dengan komposisi gas. Selanjutnya, persamaan laju untuk fluks difusi rumit.
Perilaku reduksi pelet bijih hematit dalam campuran H2-CO telah menunjukkan pola yang serupa dengan yang diamati pada H2 dan CO, yaitu laju reduksi di luar sekitar 50% penyisihan O2 dikendalikan oleh difusi gas dalam pori-pori Fe. lapisan.
Membatasi kontrol campuran pada kecepatan awal
Pada tahap awal reduksi, laju reduksi dikendalikan bersama oleh (i) difusi gas dalam pori-pori FeO (difusi solid state dalam FeO dapat diabaikan), dan (ii) reaksi pada dinding pori FeO . Ini menyiratkan lapisan Fe berpori tipis dan difusi gas yang cepat di dalamnya. Tergantung pada porositas FeO dan difusivitas gas di dalamnya, ada reduksi internal parsial di depan antarmuka Fe/FeO nominal. Reaksi H2 dengan FeO berpori biasanya terbatas pada mulut pori yang dekat dengan antarmuka nominal Fe/FeO.
Pengurangan internal sebagian
Tergantung pada komposisi gas, suhu, ukuran pelet dan tekanan gas total, ada kontrol laju campuran selama beberapa periode pengurangan dalam kerangka undang-undang laju pembatasan. Persamaan laju biasanya didasarkan pada asumsi bahwa reduksi gas pelet dikendalikan bersama-sama oleh difusi gas dengan arus berlawanan yang lambat melalui pori-pori antar partikel pelet, dan dengan reaksi kimia yang lambat dari gas dengan oksida Fe pada Fe oksida-/Fe antarmuka partikel.
Reaksi pergeseran air-gas
Reaksi perpindahan gas air memainkan peran penting dalam proses reduksi langsung yang menggunakan hidro-karbon yang direformasi sebagai pereduksi dalam reduksi oksida besi. Secara umum disepakati, dari perbedaan laju reduksi bijih besi oleh CO dan H2 dan efek nyata yang dimiliki oleh sejumlah kecil H2 yang terkandung dalam campuran CO/CO2 pada laju reduksi, bahwa H2 adalah komponen pereduksi yang sebenarnya. dalam campuran gas seperti itu. CO dianggap berfungsi terutama untuk mereduksi uap yang dihasilkan (H2O) kembali menjadi H2. Reaksi yang terjadi adalah (i) H2 + FeO =H2O + Fe, dan (ii) H2O + CO =H2 + CO2.
Subproses kedua dari reaksi ini dikenal sebagai reaksi pergeseran air-gas. Telah diketahui bahwa proses ini membutuhkan katalis. Dalam reduksi bijih besi semua produk (Fe3O4, FeO, dan Fe) dipertimbangkan sebagai katalis yang memungkinkan. Dari ini sangat aktif adalah Fe padat. Oleh karena itu, proses reduksi bijih besi dalam campuran CO/CO2 yang mengandung H2 harus dipahami, ketika logam Fe hadir, sebagai urutan reaksi. Sub-reaksi (i) reduksi yang tepat, terjadi di permukaan oksida Fe sedangkan sub-reaksi (ii), regenerasi H2 oleh reaksi air-gas, terjadi di permukaan Fe.
Pemisahan spasial dari dua sub-reaksi membutuhkan koneksi mereka dengan proses transportasi, yang berlangsung sebagai difusi gas atau difusi permukaan oleh salah satu peserta dalam reaksi. Kondisi optimal terjadi pada batas 3 fasa Fe/Fe oksida/gas.
Pembengkakan selama reduksi
Volume nyata bijih besi atau pelet biasanya meningkat selama reduksi. Ini disebut bengkak. Secara umum ada tiga jenis perilaku pembengkakan yang dapat dilihat. Ini dikenal sebagai (i) pembengkakan normal, (ii) pembengkakan katastropik di mana ada ekspansi volume tiba-tiba dengan konversi FeO menjadi Fe, Fe muncul dalam bentuk pertumbuhan filamen, yang dikenal sebagai kabel kumis Fe berserat, dan (iii) meledak ekspansi, perilaku khas bahan kaya Fe yang mengandung sejumlah kecil alkali. Jenis perilaku yang terakhir ini berbeda dengan pembengkakan katastropik (walaupun tidak kalah seriusnya) karena sebagian besar pemuaian terjadi sebelum munculnya Fe sebagai produk reaksi.
Dapat dikatakan bahwa baik lump ore maupun sinter tidak diketahui membengkak secara tidak normal atau menimbulkan bencana, sedangkan jenis pelet tertentu melakukannya, dan menimbulkan masalah operasional dengan mengurangi permeabilitas beban karena pelet yang membengkak secara tidak normal lunak, kenyal, dan cenderung hancur. .
Volume spesifik Fe oksida dan Fe yang berbeda seperti yang dilaporkan dalam literatur adalah 0,272 cc Fe2O3 per gram Fe (pada suhu kamar), 0,270 cc Fe3O4 per gram Fe, 0,231 cc FeO per gram Fe (23,5% O2) , dan 0,128 cc Fe per gram Fe. Oleh karena itu, volume diharapkan menurun selama setiap tahap reduksi. Namun, penyebab utama pembengkakan bijih Fe disebabkan oleh transformasi bijih hematit heksagonal menjadi bijih magnetit kubik dan gangguan kisi yang dihasilkan. Gangguan kisi menyebabkan pembentukan pori, di mana ada peningkatan yang cukup besar dalam volume nyata bijih Fe selama transformasi dari hematit menjadi magnetit.
Secara umum, selama pengurangan gas kaya CO, pembengkakan jauh lebih besar daripada di gas kaya H2. Alasan untuk perilaku ini adalah bahwa debu logam terjadi selama deposisi C dalam campuran gas yang mengandung CO. Namun, sulit untuk menjelaskan pembengkakan yang dapat terjadi selama reduksi campuran gas CO-CO2 ketika tidak ada deposisi C. Penyebab dan akibat dari pembengkakan atau penyusutan yang menyertai pengurangan belum terpecahkan.
Biasanya ada dua jenis pengotor dalam pelet bijih. Ini adalah (i) pengotor dengan efek menghambat pembengkakan, dan (ii) pengotor dengan efek peningkatan pembengkakan. Contoh yang pertama adalah silika (SiO2) sedangkan yang kedua adalah alkali (K2O, Na2O). Telah diperhatikan bahwa pelet Fe2O3 tingkat reagen yang mengandung SiO2 hingga 5% tidak membengkak ketika direduksi dalam campuran gas CO – CO2 dan juga sejumlah SiO2 diperlukan dalam pelet asam untuk mempertahankan kekuatan dan mencegah pembengkakan katastropik. Dalam kasus kedua, terlihat bahwa penambahan sedikit alkali Na2CO3 atau K2CO3 dalam kisaran 0,1% hingga 1% dapat mengakibatkan pembengkakan besar dalam H2 atau CO dari pelet bijih normal. Pengaruh basa menjadi lebih nyata dengan meningkatnya rasio kebasaan (CaO/SiO2) dalam pelet. Efek merugikan dapat dicegah dengan penambahan gangue asam berbutir halus untuk membentuk silikat alkali yang stabil.
Ada beberapa pengamatan yang kontradiktif tentang pengaruh pengotor dalam pelet bijih (misalnya kandungan kapur). Sejumlah kecil penambahan CaO (kurang dari 0,1%) ke pelet bijih hematit menyebabkan pembengkakan yang cukup besar selama reduksi dan ini menunjukkan bahwa CaO adalah penyebab pembengkakan katastropik. Di sisi lain, telah diperhatikan bahwa sekitar 1% penambahan CaO ke pelet bijih hematit menekan pembengkakan selama reduksi. Variasi dalam efek CaO yang diamati pada pengembangan ini dapat disebabkan oleh ada atau tidak adanya pengotor lain dalam bijih besi, seperti alkali.
Reduksi bijih hematit oleh C
Reaksi antara bijih hematit dan C sangat penting dalam pembuatan pelet bijih logam. Banyak minat baru telah dirangsang oleh pengembangan proses tanur putar yang menggunakan C padat sebagai reduktor dalam produksi besi tereduksi langsung (DRI). Secara umum diterima bahwa reduksi Fe oksida oleh C terjadi melalui intermediet gas CO dan CO2, kecuali di bawah vakum yang sangat tinggi di mana reaksi padat-padat yang sebenarnya adalah mekanisme yang dominan.
Mekanisme reaksi melalui zat antara gas yang berlangsung selama reduksi bijih hematit oleh C adalah melalui reaksi (i) C(s) + 0,5 O2 =CO(g), (ii) FexOy(s) + CO(g) =FexO (y-1) (s) + CO2(g), dan (iii) CO2(g) + C(s) =2CO(g).
Pembentukan awal CO merupakan langkah penting dalam laju reaksi keseluruhan. O2 dari udara yang terperangkap bersama dengan gas O2 yang dilepaskan oleh disosiasi Fe oksida bereaksi dengan C menghasilkan CO (reaksi pertama). Selain itu, beberapa CO juga dapat dibentuk melalui reduksi langsung sejati yang terjadi pada titik-titik kontak antara partikel oksida C dan Fe. Gas CO yang dihasilkan mudah bereaksi dengan partikel bijih hematit (reaksi kedua). Boudouard atau reaksi kehilangan larutan antara gas CO2 dan partikel C meregenerasi gas CO (reaksi ketiga) dan dengan demikian cenderung mengembalikan potensi reduksi fase gas yang terkandung dalam pori-pori sampel. Oksidasi jenis C tertentu dalam CO2 dikatalisis dengan adanya logam dan senyawa logam tertentu. Peningkatan laju proses telah diamati dengan penambahan Li2O (lithium oksida) dan efek penghambatan telah dilaporkan dengan penambahan FeS (ferrous sulfida). Logam Fe telah ditemukan menjadi katalis yang baik untuk gasifikasi grafit (C). Karena reaksi katalitik yang tidak dapat diprediksi dalam campuran ini, persamaan yang diturunkan melalui pemodelan matematika untuk menggambarkan laju reaksi secara keseluruhan memiliki nilai yang terbatas dan hanya dapat diterapkan pada sistem di mana reaksi tidak dikatalisis.
Pada suhu yang cukup tinggi (misalnya 1000 derajat C) laju reaksi oksida Fe (pada suhu lebih besar dari 570 derajat C dan urutannya adalah Fe2O3, Fe3O4, FeO, Fe) jauh lebih besar daripada reaksi Boudouard. Dengan kata lain keseluruhan proses menjadi dibatasi oleh ketersediaan gas CO menurut reaksi Boudouard. Thus at steady-state the composition of this gas-phase closely corresponds to the equilibrium gas-phase composition for FexOy/FexO(y-1).
Fe oxides reduction with hydrocarbons
Hydrocarbons can be used in two ways as a reducing agent for the production of DRI. These are (i) direct use of hydro-carbons or a mixture of gas containing hydro-carbons, and (ii) use of the reformed hydrocarbon products (CO, H2), by reforming within the reduction reactor (it has been found that auto-catalytic reforming of some hydro-carbons within the reducing furnace provided an access of macro and micro porosity which leads to more extensive reduction and also which leads to the deletion of the capital cost of gas reformer and processing.
There are a few studies using directly hydrocarbons or a mixture of gas containing hydrocarbons as reductant for direct reduction of iron ores. Two important points emerge from these studies. The first is that the rate of reduction with hydrocarbons is slow and the production of a high quality of DRI is troublesome and uneconomical. The second point is that these studies have been done under isothermal conditions in a thermo-gravimeter with single particle or powder compact, thus the results are of only theoretical value.
Theoretical importance of investigations with hydrocarbons – The kinetics of ferric oxide reduction by pure methane (CH4) has been studied in the three temperature ranges of (i) low temperature (500 deg C to 600 deg C), (ii) medium temperature (650 deg C to 750 deg C) and (iii) high temperature (800 deg C to 950 deg C). At the low temperature, the reduction proceeds only from Fe2O3 to Fe3O4. A prolonged holding of the sample in a stream of CH4 has not led to any process extension beyond this stage. The rate became appreciable at 650 deg C. In special experiments after the Fe3O4 composition has been reached, the sample has been reduced further by H2 and CH4. It has been shown that CH4 reduction in the low temperature range beyond the Fe3O4 stage occurs only if a sufficient quantity of metallic Fe has been built up. In this case the reducing agent has not been CH4, but its decomposition product, H2. C formed by CH4 decomposition takes almost no part in the reduction and gets accumulated in the sample.
In the medium temperature range the conversion of Fe3O4 to FeO takes place but at low rates. A sharp rise in reduction rate is observed on going from 750 deg C to 800 deg C. The process becomes very sensitive to temperature changes beyond 800 deg C, and accelerated considerably in the high temperature range, when metallic Fe appeared in the sample. The appearance of metallic Fe at the FeO to Fe stage, at comparatively high temperatures indicates a decisive role of metallic Fe as a catalyst for reforming CH4 by the reduction products (CO2, and H2O). In the absence of a catalyst, the decomposition of CH4 and its reforming by the reduction products (CO2, H2O) do not occur to any substantial extent and no C accumulation in the sample has been observed. When the Fe catalyst is present, CH4 dissociation into the elements takes place only at very late stages of reduction, when there is insufficient CO2 and water vapour to convert all the CH4 diffused into the sample. C build-up in the sample starts from that stage.
In the 2-stage production of DRI with CH4, it has been found that the complete decomposition of CH4 in the presence of the Fe bearing material occurs at temperatures of 850 deg C to 900 deg C, which is 400 deg C to 450 deg C lower than on an inert surface (e.g. fire clay), while the reaction rate, conversely, has been 10 times higher. The products of the first stage are a sooty Fe containing 30 % to 50 % C and technically pure H2.
In the second stage, the product of the first stage (sooty Fe with highly dispersed C in the pores of DRI and on the surface of the Fe particles) has been used as an active reducing agent and mixed with mill scale or concentrate. The mixture has been reduced in the temperature range 1050 deg C to 1100 deg C with a make-up reducing agent of H2 reformed natural gas. The results of industrial trials has shown that the use of sooty Fe instead of soot, petroleum coke and the other known carbonaceous reducing agents considerably intensified the Fe-oxide reduction process. As is well known, the direct reduction of Fe oxides with C is directly related to the rate of reaction between the C and CO2. The sooty Fe can have intensified the rate of Boudouard reaction.
The isothermal reduction of hematite ore pellets (with 10 % to 15 % porosity) in a thermo-balance with a mixture of CH4-H2 (containing 4.5 % CH4) within the temperature range 700 deg C to 1000 deg C has shown that the reduction is chemical – controlled initially and diffusion – controlled in the later stages. It has been shown that reduction in pure H2 is faster than in the CH4- H2 mixture. This difference is attributed to C deposition in the outer reduced layers of the pellet, causing resistance to gas diffusion when the reducing gas contained CH4. It has been shown that the excess residual C can be removed from the reduced iron at lower temperature by its hydrogenation.
In another study, it has also been demonstrated that it is possible to hydrogenate residual C in direct reduced products to CH4. The C formed as a result of the reduction of Fe oxide in a mixture of CH4 and H2 (containing 20 % CH4) reacted with steam (H2O) according to the water gas reaction to regenerate H2 and produce CO.
Pure ferric oxide briquettes were reduced at temperatures ranging from 800 deg C to 1050 deg C, in gas mixtures containing H2, CO, CH4, N2 and CO2, which has been obtained by partial oxidation of natural gas with air. The CH4 content of the reformed gas mixture was between 13 % and 16 %. The overall reduction rate again has been controlled initially by chemical reaction and the gaseous diffusion has been applicable during the latter stages. It has been shown that the hematite ore briquettes have swelled and considerable porosity has been was developed during reduction. The solid-state diffusion rates increased more rapidly with temperature than it did by interfacial or gaseous diffusion reaction rates. The reduction of porous (30 % porosity) Fe ore in CH4 has indicated that the reaction proceeded stepwise from Fe2O3 to Fe3O4, FeO and Fe. The Fe catalyzed the CH4 cracking reaction. Optimum conditions for CH4 utilization occurred at around 1000 deg C.
The above findings are not consistent with the earlier studies on the understanding of high-grade porous (around 30 %) or dense hematite ore reduction kinetics, which had shown that the rate of reduction can be considered to fall between 3 limiting cases, namely (i) uniform internal reduction, (ii) limiting mixed control, and (iii) diffusion in porous iron layer, respectively with the rate of reduction corresponding to, (i) chemical control, (ii) the overall chemical control and diffusion control, and (iii) diffusion control. The overall rate of reduction is not controlled by only one of these rate controlling mechanisms and can be changed from one limiting case to another during the course of reduction.
In one of the studies it has been found that the most important factors controlling the extent of reduction are (i) the temperature, (ii) the composition of gas, presence of unreacted hydrocarbons in the reducing gas, the ratio of H2/C in it, and reducing capacity, (iii) the ore particle size, and (iv) the residence time for reduction.
Reduction of Fe oxides with the products of CH4 reformed with H, O within the reduction furnace – In early 1981 a commercial process has been introduced, using gaseous mixtures containing upto around 30 % by volume of CH4 (e.g. coke oven gas), for the direct gaseous reduction of Fe ore in a counter current moving bed shaft furnace. The furnace contained a reduction zone, a cooling zone, and an intermediate reforming zone. A hot mixture of coke oven gas and steam has been fed to the intermediate zone and reduced Fe ore therein catalyzed the reforming of the CH4 to CO and H2. The reformed gas flows upward into the reduction zone for the reduction of Fe ore.