Produksi dan Pemrosesan Baja Armor
Produksi dan Pemrosesan Baja Armor
Di lingkungan saat ini, ada upaya yang dipercepat untuk menghadirkan teknologi lapis baja ringan yang dapat mengalahkan proyektil penusuk lapis baja (AP) dengan bobot area yang berkurang. Sementara banyak dari upaya ini melibatkan penerapan logam dengan kepadatan lebih rendah seperti aluminium dan titanium, pemilihan paduan baja terus menjadi kompetitif untuk banyak aplikasi balistik dan struktural, karena kemampuannya untuk membuat komponen pelindung di area operasional komersial dan militer dengan peralatan dan personel yang tersedia. Ini adalah keuntungan utama dari solusi baja.
Baja adalah bahan armor dengan performa terbaik meskipun memiliki kepadatan tinggi karena sifatnya seperti ketangguhan, ketersediaan siap pakai, biaya rendah, kemampuan cast, dan kemampuan las, dll. Baja pelindung bukanlah baja biasa tetapi memiliki kekuatan tinggi yang dikombinasikan dengan kekerasan dan patah. kekerasan. Mereka digunakan untuk melindungi objek dari kerusakan proyektil atau tekanan selama pertempuran. Baja ini umumnya digunakan dalam bentuk pelat canai panas yang biasanya digunakan dalam pembuatan kendaraan lapis baja.
Sifat utama baja lapis baja seperti ketangguhan, kekerasan, kekuatan lelah yang baik, kemudahan fabrikasi dan penyambungan serta memiliki biaya yang relatif rendah menjadikan baja sebagai bahan yang populer untuk kendaraan lapis baja. Persyaratan penting dari baja ini adalah untuk menjaga integritas struktural bahkan pada suhu di bawah nol ketika terkena dampak peluru artileri yang terlalu serasi. Oleh karena itu, baja ini diharuskan memiliki kekuatan impak suhu rendah. Pertimbangan penting lainnya untuk pelat baja lapis baja adalah bahwa pelat tersebut harus sesuai dengan teknik fabrikasi dan konstruksi modern dan mudah dilas serta mampu diproduksi dalam berbagai bentuk.
Telah diketahui dengan baik bahwa komposisi kimia, austenisasi dan temperatur temper, dan ukuran butir baja mempengaruhi sifat mekanik baja dan karenanya kinerja balistiknya. Juga telah ditetapkan bahwa sifat mekanik dan kinerja balistik baja martensit dapat dioptimalkan dengan mengontrol komposisi kimia dan parameter perlakuan panas.
Baja lapis baja pada dasarnya adalah baja struktural paduan rendah kekuatan tinggi yang telah diperlakukan memiliki sifat ketahanan yang sangat tinggi terhadap penetrasi. Sifat baja ini biasanya diberikan oleh perlakuan panas biasanya dengan perlakuan termo mekanis. Telah diketahui bahwa ketahanan terhadap penetrasi baja dapat ditingkatkan dengan meningkatkan intensitas teksturnya yang dapat diperoleh dengan perlakuan termo-mekanis. Efektivitas massa baju besi meningkat dengan kekerasan material. Namun, armor yang sangat keras cenderung rapuh dan pecah saat dipukul.
Elemen paduan utama dari baja lapis baja adalah nikel (Ni), kromium (Cr), dan molibdenum (Mo). Kandungan fosfor (P) dan belerang (S) dari baja ini harus sangat rendah (lebih disukai kurang dari 0,015% dari setiap elemen). Juga ada nilai yang sangat rendah dari gas terlarut seperti nitrogen (N2), oksigen (O2), dan hidrogen (H2) dalam baja ini. Selanjutnya, baja harus menjadi baja yang sangat bersih dengan tingkat inklusi yang sangat rendah. Itu juga untuk bebas dari segregasi.
Armor baja dapat diklasifikasikan menjadi empat kelompok utama. Kelompok-kelompok ini adalah (i) baju besi homogen yang digulung (RHA), (ii) baju besi kekerasan tinggi (HHA), (iii) baju besi baja kekerasan variabel, dan (iv) baju besi berlubang. Dari keempat jenis ini, baja RHA biasanya dianggap sebagai bahan acuan. Baja RHA telah dianggap sebagai pelindung konvensional untuk kendaraan lapis baja ringan. Ini adalah baja paduan berkualitas tinggi yang digulung sebelum diberi perlakuan panas untuk memberikan kombinasi kekuatan dan ketangguhan yang optimal.
Baja Rolled Homogeneous Armor (RHA) tetap menjadi standar armor di sebagian besar tank. Biaya rendah, keandalan, ketersediaan infrastruktur produksi, utilitas bersamaan sebagai bahan struktural dan kemudahan fabrikasi telah memungkinkan baja ini untuk mempertahankan posisi utamanya. Baja amour ini terus digunakan dalam struktur mikro martensit temper setelah perlakuan panas yang melibatkan pengerasan untuk meningkatkan ketahanannya terhadap penetrasi oleh proyektil dan kemudian temper untuk membuatnya lebih keras dan oleh karena itu meningkatkan kemampuan menyerap energi terhadap proyektil yang terkena benturan.
Spesifikasi HHA memungkinkan teknologi pemrosesan berkelanjutan modern untuk digunakan secara efisien dan menawarkan kelas baru baja keras-tinggi yang ditempa otomatis. Baja pelindung kekerasan variabel juga dikenal sebagai baja pelindung kekerasan ganda (DHA) yang diproduksi dengan menggulung pelat depan kekerasan tinggi ke pelat belakang kekerasan rendah. Baja DHA roll-bonded rumit untuk diproduksi dan memiliki keterbatasan produksi yang diketahui. Studi telah dilakukan untuk memproduksi baja DHA dengan proses peleburan kembali terak elektro, tetapi memproduksi baja DHA terus menjadi sulit.
Ada beberapa upaya sedang dilakukan untuk mengembangkan baja monolitik ultra-high hardness armor (UHHA) dengan kekerasan 600 BHN (Brinell hardness number) atau lebih besar dan kemajuan signifikan dalam metalurgi baja telah dibuat ke arah ini. Ketahanan balistik baja yang ditingkatkan sebagai fungsi peningkatan kekerasan sudah mapan di komunitas balistik. Baja UHHA diharapkan dapat meningkatkan kekalahan peluru AP, mengurangi berat armor, dan menghilangkan kesulitan manufaktur yang melekat pada DHA.
Quenching dan tempering, didefinisikan sebagai kombinasi pemanasan dan pendinginan logam atau paduan, mengubah struktur mikro baja dan meningkatkan kekuatan, kekerasan dan ketangguhan bahan yang dirawat. Laju pendinginan selama pendinginan baja yang berada dalam kisaran austenitik harus sedemikian rupa sehingga mendinginkan baja di bawah suhu Ms (awal pembentukan martensit). Setelah seluruh struktur mikro baja diubah menjadi martensit, tempering martensit dilakukan. Selama proses temper, suhu baja dinaikkan ke suhu di mana struktur martensit baja ditempa. Dalam proses pendinginan dan temper selama penggulungan panas pelat, suhu penggulungan akhir dan laju pendinginan dan temper harus dikontrol untuk mendapatkan nilai kualitas baja yang optimal dengan kandungan paduan rendah. Produk yang dihasilkan dari baja paduan rendah yang dipadamkan dan ditempa menawarkan kepada perancang kendaraan lapis baja keunggulan kekuatan terhadap bobot dan sifat tahan aus yang biasanya tidak tersedia pada baja konvensional.
Proses produksi baja lapis baja
Teknologi yang digunakan dalam pembuatan pelat baja harus bersifat sangat tinggi, karena tuntutan baja kekuatan tinggi dan kekerasan tinggi mendikte kebutuhan akan salah satu rute proses yang paling ketat yang akan digunakan untuk produksi baja. piring. Pembuatan baja utama dari baja lapis baja dapat dilakukan di tungku oksigen dasar (BOF) atau di tungku busur listrik (EAF).
Sedangkan pada tungku oksigen dasar sebagian besar logam panas (besi cair dari tanur tinggi) dan scrap digunakan sebagai bahan baku pembuatan baja, tungku busur listrik dapat menggunakan scrap, besi reduksi langsung, dan logam panas berdasarkan ketersediaannya. Kualitas bahan baku yang digunakan untuk pembuatan baja primer perlu dikontrol. Dalam hal penggunaan logam panas selama pembuatan baja, diinginkan untuk melakukan de-sulfurisasi, de-fosforisasi, dan de-silikonisasi logam panas sesuai dengan persyaratan proses untuk memastikan rendahnya kadar belerang, fosfor, dan silikon di panas. logam. Penghapusan elemen-elemen ini dari logam panas membantu kualitas pembentukan terak selama proses pembuatan baja oksigen dasar. Memo yang digunakan untuk pembuatan baja harus bersih dan berdensitas tinggi. Juga, jumlah elemen gelandangan dalam memo harus sangat rendah.
Flowsheet dari proses untuk produksi dan pemrosesan baja lapis baja diberikan pada Gambar 1 dan Gambar 2. Gambar 1 memberikan proses yang digunakan hingga tahap produksi pelat sedangkan Gambar 2 memberikan proses penggulungan, pemrosesan termal, dan inspeksi piring.
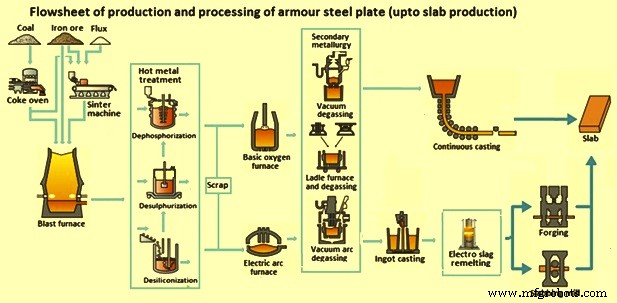
Gbr 1 Flowsheet produksi dan pemrosesan pelat baja lapis baja (hingga produksi pelat)
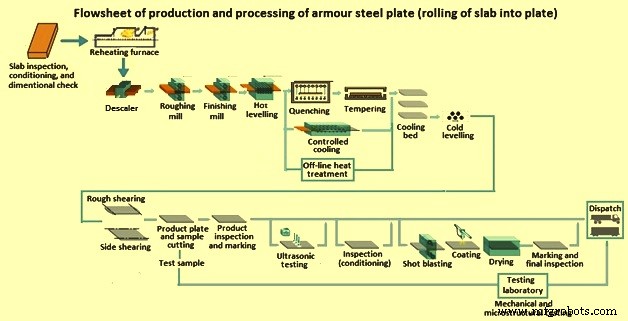
Gbr 2 Flowsheet produksi dan pemrosesan pelat baja lapis baja (penggulungan pelat menjadi pelat)
Pembuatan dan pengecoran baja lapis baja
Setelah baja cair dibuat di tungku oksigen dasar atau tungku busur listrik, baja tersebut diolah di unit pembuatan baja sekunder. Tujuan dari pembuatan baja sekunder meliputi (i) homogenisasi komposisi kimia dan suhu baja cair dalam sendok, (ii) deoksidasi atau pembunuhan yang berarti penghilangan oksigen, (iii) penyesuaian superheat yang berarti pemanasan atau pendinginan baja cair ke suhu yang sesuai untuk pengecoran kontinunya, (iv) penambahan paduan besi dan karbon dengan tujuan membuat penyesuaian kimia baja cair, (v) penghilangan gas baja secara vakum untuk menghilangkan gas hidrogen dan nitrogen, (vi) penghilangan senyawa bukan logam yang tidak diinginkan dengan cara mengapungkannya ke dalam terak, dan (vii) mengubah komposisi pengotor yang tersisa untuk memperbaiki struktur mikro baja. Pembuatan baja sekunder diperlukan untuk mencapai sifat mekanik yang diinginkan pada baja setelah penggulungan.
Selama produksi baja kualitas lapis baja, satu atau lebih proses pembuatan baja sekunder yang biasanya digunakan meliputi penghilangan gas vakum, pelepasan gas sendok dan tungku sendok, pelepasan gas busur vakum, dan pelelehan kembali terak elektro. Selama proses pembuatan baja sekunder juga pembilasan atau pengadukan baja cair bersama dengan injeksi bahan yang berbeda dilakukan di sendok untuk homogenisasi dan pemurnian baja cair. Pembuatan baja sekunder juga diperlukan untuk kelancaran pengecoran baja cair di mesin pengecoran kontinyu serta untuk produksi kualitas suara pelat.
Pengecoran baja berkelanjutan adalah proses dimana baja cair dipadatkan menjadi produk baja setengah jadi yaitu slab (dalam kasus baja lapis baja) untuk pengerolan selanjutnya di pabrik penggilingan. Operasi pengecoran kontinyu mengubah baja cair dari komposisi tertentu menjadi untaian pelat dengan ukuran tertentu melalui sekelompok operasi seperti operasi cetakan, zona pendinginan semprot, dan operasi zona pelurusan dll. Ketebalan pelat cor adalah untuk sedemikian rupa sehingga tingkat pengurangan minimum terjadi selama penggulungan pelat.
Peralatan utama mesin continuous casting adalah (i) turret ladle beserta sistem penimbangan turret dan manipulator penutup ladle, (ii) mobil tundish dan tundish beserta sistem penimbangan tundish, preheater dan pengering tundish, (iii) osilasi cetakan dan cetakan sepanjang dengan kontrol level cetakan dan pengaduk elektromagnetik, (iv) pendinginan sekunder yang terdiri dari pendinginan untai, penahanan untai dan pemandu, (v) unit penarikan dan pelurusan, (vi) dummy bar, parkir dummy bar dan unit gulung pemutus dummy bar, (vii) unit pemutus rol dan obor, (viii) sistem identifikasi produk, dan (ix) meja rol dan sistem pelepasan produk yang terdiri dari alas pendingin, meja rol, dan kisi pelepasan.
Untuk pengecoran baja lapis baja paduan rendah, tekanannya adalah pada produksi baja bersih. Juga, ada persyaratan yang lebih tinggi untuk struktur mikro dan homogenisasi komposisi produk cor. Komposisi kimia, kondisi pemadatan dan sifat aliran baja cair dalam cetakan mempengaruhi kualitas permukaan dan struktur bagian dalam produk cor. Penerapan teknik pengadukan elektromagnetik (EMS) mendorong pembentukan zona kristal yang sama pada untaian. Ini menyebabkan penyempurnaan struktur pemadatan, pengurangan kandungan inklusi dan peningkatan kualitas permukaan, sub permukaan dan struktur bagian dalam pelat tuang.
Pelat untuk baja lapis baja juga dapat diproduksi dengan mengikuti rute peleburan kembali terak elektro, dicor menjadi batangan yang lebar dan kemudian menempa batangan tersebut menjadi pelat. Karena selama pengecoran ingot, pemisahan karbon terjadi ke arah pemadatan saat pemadatan baja cair berlangsung, ada kebutuhan untuk proses peleburan kembali terak listrik. Namun, rute ini meningkatkan biaya produksi pelat. Rute produksi ini terutama cocok untuk kapasitas rendah. Selanjutnya, karena pelat dibuat melalui proses penempaan, pelat tersebut memiliki struktur bagian dalam yang kuat.
Mesin pengecoran kontinu pelat modern yang dilengkapi dengan semua jenis kontrol mulai dari menara ladle hingga pelepasan produk cor biasanya menghasilkan pelat yang sangat baik dengan praktis tanpa cacat permukaan dan bawah permukaan. Namun, karena pentingnya baja lapis baja, pelat setelah pendinginan dikenakan inspeksi visual, magnaflux dan ultrasonik untuk mengidentifikasi kemungkinan cacat permukaan, sub-permukaan, dan internal. Cacat internal pada pelat cor terus menerus dapat memiliki efek yang kuat baik pada kinerja baja selama pemrosesan termo-mekanis dan/atau sifat mekanik produk akhir. Oleh karena itu, penting untuk mengidentifikasi, mengukur dan mengkarakterisasi cacat. Karakterisasi cacat meliputi kepadatan, distribusi, jenis dan lokasi anomali.
Inspeksi membantu dalam pemisahan pelat cor menjadi tiga kategori yaitu (i) pelat utama yang dapat dikirim untuk digulung, (ii) pelat dengan cacat permukaan kecil yang dapat dihilangkan baik dengan penggoresan atau dengan penggilingan agar sesuai untuk penggulungan. , dan (iii) pelat dengan sub-permukaan yang tidak dapat diterima dan cacat internal berdiri ditolak untuk digulung dan dibuang untuk dilebur kembali.
Penggulungan pelat di pabrik pelat
Pelat setelah pemeriksaan dipanaskan dalam tungku pemanas ulang hingga suhu sekitar 1150 derajat C hingga 1200 derajat C yang sesuai untuk deformasi plastis baja dan karenanya untuk penggulungan baja di pabrik penggilingan. Jenis tungku pemanas ulang berjalan beam lebih disukai karena hemat energi dan memastikan pemanasan pelat yang seragam. Tungku pemanasan ulang diperlukan untuk memiliki semua fasilitas untuk pemulihan limbah panas. Itu juga harus dilengkapi dengan kontrol pembakaran yang diperlukan untuk mengontrol suhu pelat serta kontrol lain yang diperlukan untuk operasi yang efisien.
Pelat yang dipanaskan kemudian digulung dalam pabrik penggilingan pelat. Pabrik pelat biasanya merupakan pabrik penggulung pembalik empat tinggi dengan konfigurasi dudukan tunggal atau dengan konfigurasi dua dudukan. Dudukan penggulung biasanya memiliki gulungan edger yang terpasang untuk mengontrol lebar pelat. Pelat umumnya digulung hingga ketebalan yang ditentukan dalam dudukan penggulung terbalik (yaitu, berulang kali melewati pelat bolak-balik melalui dudukan gulungan) sambil secara bertahap mengurangi celah antara gulungan atas dan bawah secara bertahap, dan umumnya memerlukan sejumlah melewati bergulir. Tindakan melewatkan pelat melalui celah gulungan disebut lulus, dan jumlah pengurangan ketebalan pelat di setiap lintasan disebut pengurangan bergulir. Pengurangan ketebalan selama penggulungan didistribusikan ke beberapa lintasan penggulungan. Proses dimana jumlah lintasan dan pengurangan rolling di setiap lintasan dari ketebalan pelat ke ketebalan produk diputuskan adalah jadwal lintasan rolling. Suhu penggulungan akhir memengaruhi jumlah lintasan yang diperlukan karena sifat material, di mana material yang lebih dingin menjadi lebih keras.
Dalam kasus produk ketebalan normal (yaitu, pelat datar), ketebalan yang sama diperoleh di seluruh panjang dengan mengontrol penggilingan sehingga celah antara gulungan atas dan bawah tidak berubah selama rolling pass.
Suhu awal dan akhir penggulungan menentukan stabilitas proses, di mana material yang lebih dingin membutuhkan lebih banyak gaya penggulungan daripada yang lebih panas. Oleh karena itu, pelat tipis yang memiliki laju pendinginan lebih tinggi daripada pelat tebal dapat membuat proses penggulungan menjadi tidak stabil, terutama untuk pelat dengan ketebalan rendah yang penurunan suhunya tinggi.
Dudukan pabrik dan sistem pendingin pelat serta semua bagian pabrik hilir harus dirancang sedemikian rupa sehingga pelat berkekuatan tinggi dapat diproduksi dan diproses untuk mendapatkan produk akhir berkualitas tinggi
Sekrup ke bawah dan kontrol celah otomatis adalah bagian utama dari rolling mill untuk menyesuaikan celah gulungan sesuai dengan ketebalan yang ditetapkan. Masing-masing ukuran pelat memiliki perhitungan jadwal lintasannya sendiri termasuk celah guling, gaya gulung, dan modulus penggilingan yang sesuai.
Untuk penggilasan pelat tipis, pabrik pelat harus dilengkapi dengan fasilitas untuk kontrol bentuk otomatis, kontrol kerataan, dan kontrol pengukur. Penggulungan pelat tipis umumnya membutuhkan dua dudukan dengan dudukan akhir memberikan lintasan terakhir. Juga diperlukan n alat ukur pengukur online untuk pengukuran ketebalan.
Pelat yang digulung mengalami perataan dalam penyamarataan panas sebelum memasuki bagian pemrosesan termo dan perataan dingin setelah bagian pemrosesan termo. Kerataan pelat baja yang baik diinginkan karena selama proses pendinginan, kerataan mempengaruhi jarak tumbukan air dengan pelat baja dan mempengaruhi aliran air pada pelat baja. Fungsi dari hot leveler yang dipasang sebelum peralatan pendingin adalah untuk meratakan pelat baja sebelum didinginkan. Di sisi lain, penyamarata dingin yang dipasang setelah bagian pemrosesan termo dimaksudkan untuk meratakan pelat guna memperbaiki bentuk yang memburuk dengan pendinginan agar mudah dipindahkan ke proses selanjutnya.
Selama penggulungan baja lapis baja, suhu penggulungan akhir diatur pada nilai yang lebih rendah daripada dalam kasus pelat canai panas konvensional. Ini berarti terkadang waktu tunggu untuk penyesuaian suhu diperlukan selama proses penggulungan, dan waktu tunggu cenderung menjadi lebih lama dengan produk yang lebih tebal.
Bagian pemrosesan termo sangat penting dalam produksi dan pemrosesan baja lapis baja karena sifat akhir baja diperoleh selama pemrosesan pelat di bagian ini. Untuk memenuhi persyaratan selama produksi baja lapis baja, tiga pendekatan digunakan.
Pada pendekatan pertama, pemrosesan termo dilakukan secara off-line dari pabrik pelat, Dalam pendekatan ini, pelat dipanaskan sampai suhu yang diinginkan dalam kisaran austenisasi. Kontrol pemanasan penting untuk menghindari pertumbuhan butir. Setelah pelat mencapai struktur austenitik yang homogen, pelat dipadamkan dengan air pada laju pendinginan yang telah ditentukan untuk mendapatkan struktur baja martensit. Baja yang dipadamkan kemudian ditempa pada suhu rendah untuk mencapai sifat yang diinginkan.
Pada pendekatan kedua, baja yang digulung segera setelah penggulungan dikenai pendinginan kontrol yang dipercepat. Dalam hal ini struktur martensit dihindari, dan struktur bainitik berbutir sangat halus adalah tujuannya. Dalam pendekatan ini kekerasan yang sangat tinggi pada baja tidak dapat dicapai tetapi baja mendapatkan kekuatan tinggi ditambah dengan ketangguhan yang baik.
Pada pendekatan ketiga, operasi quenching dan tempering dilakukan secara on line segera setelah rolling. Dalam pendekatan ini, pemanasan pelat dihilangkan, tetapi dalam pendekatan ini, laju penggulungan pelat di pabrik dan waktu pendinginan dan temper harus sesuai, atau jika tidak, satu operasi harus menunggu operasi lainnya selesai. . Juga, kontrol yang memadai dengan penggunaan pirometer yang murah hati harus disediakan untuk kontrol parameter pemrosesan termo. Selanjutnya, bagian pemrosesan termo harus terkait erat dengan operasi penggulungan melalui sistem kontrol untuk kontrol yang efektif dari sifat-sifat pelat baja.
Pinch roll selama operasi pendinginan dan temper memiliki fungsi menahan pelat baja di antaranya, meningkatkan pendinginan/pemanasan yang seragam dengan menekan deformasi pelat selama pendinginan/pemanasan, memperbaiki bentuk pelat, dan mengamankan zona pendinginan. Dalam kasus pendinginan pelat baja, suhu pendinginan akhir dan waktu pendinginan sangat bervariasi tergantung pada ukuran dan bahan yang dituju. Oleh karena itu, perlu untuk menyesuaikan panjang zona pendinginan peralatan pendingin. Gulungan jepit menentukan aliran air pendingin ke hilir zona pendinginan, mencegah pendinginan yang tidak seragam karena air yang tertahan di pelat baja di luar zona pendinginan, sehingga memisahkan zona pendinginan dari zona non-pendingin.
Unit pendingin air perlu dirancang dengan baik karena dipengaruhi oleh kurva didih air. Kapasitas pendinginan air dalam kasus pendinginan pelat baja pada suhu tinggi menunjukkan perilaku karakteristik seperti yang diungkapkan oleh apa yang dikenal sebagai kurva didih (ditunjukkan pada Gambar 3). Di daerah suhu tinggi, ada lapisan uap uap di antara pelat baja dan air, menyebabkan keadaan yang disebut sebagai film mendidih dan, meskipun suhu tinggi di daerah tersebut, kapasitas pendinginan menjadi sedikit lebih rendah. Saat suhu pelat baja turun, kontak air dengan pelat baja dimulai dan, saat suhu pelat baja turun lebih jauh, area kontak air dengan pelat baja meluas dan keadaan pendinginan memasuki daerah didih transisi di mana kapasitas pendinginan meningkat. Saat suhu pelat semakin turun, keadaan pendinginan masuk ke daerah didih nukleat di mana gelembung yang dihasilkan memainkan peran utama. Dalam pendinginan pelat baja, pendinginan di daerah didih transisi sangat penting. Di wilayah ini, ketika kapasitas pendinginan meningkat seiring dengan penurunan suhu pelat, distribusi suhu yang tidak merata di dalam pelat baja yang dikembangkan pada pendinginan sebelumnya diperbesar dan, suhu pendinginan akhir juga bervariasi untuk setiap pelat baja.
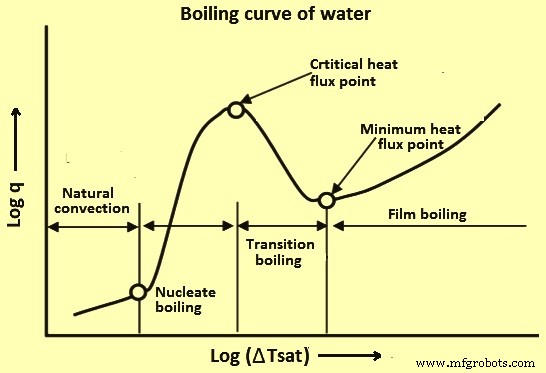
Gbr 3 Kurva didih air
Unit pendingin air perlu dirancang dengan baik karena dipengaruhi oleh kurva didih air. Fungsi yang dibutuhkan untuk unit pendingin air sangat beragam untuk memiliki kemampuan pendinginan yang cepat. Oleh karena itu, unit harus dilengkapi dengan banyak nozel semprot karena memerlukan laju aliran air yang tinggi untuk pendinginan cepat yang seragam pada pelat lebar. Juga, di bawah kondisi operasi dan tergantung pada kualitas pelat baja yang diinginkan, suhu pendinginan akhir (suhu Mf) harus diatur di suatu tempat di wilayah didih transisi.
Setelah pelat mengalami pemrosesan termo yang diperlukan untuk mencapai sifat kekuatan, kekerasan, dan ketangguhan yang diinginkan, pelat baja diluruskan lagi dalam pelurus dan kemudian aktivitas finishing seperti geser dan pemotongan, pemotongan sampel, pengujian dan inspeksi. dan jika diperlukan peledakan tembakan dan pelapisan dan pewarnaan dilakukan seperti yang ditunjukkan pada lembar alir. Pelat harus menjalani pemeriksaan akhir sebelum dikirim.
Selama pengujian semua pengujian yang diperlukan sesuai standar harus dilakukan untuk memastikan bahwa pelat sesuai dengan nilai yang ditentukan dalam standar sehubungan dengan dimensi, toleransi dimensi, struktur mikro, kekuatan, kekerasan, dan ketangguhan. Laboratorium rolling mill harus dilengkapi dengan semua fasilitas pengujian dan inspeksi yang diperlukan sehingga pengujian dan inspeksi pelat yang digulung dapat dilakukan.